
Учебное пособие 800555
.pdfмическая модель, имеет возможность многокоординатного перемещения в рабочей зоне и оператор, меняя положение формы, обеспечивает равномерное наращивание слоев металла. По завершении процесса и остывания в течение полуторадвух часов керамическую модель удаляют из металлического брикета и производят регламентные технологические операции механической и термической обработки.
На указанной установке RSP можно получать детали с максимальными габаритами 180×180×100 мм. при продолжительности одного технологического цикла 3-4 часа. То есть, в течение одной смены может быть получено 2-3 изделия.
Используя эту технологию, можно получать биметаллические композиции, формируя рабочую часть кокиля из специальной легированной стали, а корпус из обычной конструкционной стали или цветного металла с высокой теплопроводностью. Рассмотренная технология уже находится на уровне промышленного использования и успешно распространяется. Примеры деталей ракетных двигателей, полученных из сращенных из гранул никелевых сплавов заготовок по технологии Spray forming, приведены на рисунке 7.10.
Сплавы группы Al-Zn-Cu-Mg, которые давно относятся к высокопрочным, ограничены в улучшении своих прочностных характеристик эффектом макросегрегации, возникающей в отливке. Технология spray forming снимает эту проблему. Сплавы Al-Zn-Cu-Mg, полученные по новой технологии, подтверждают более высокую ударную вязкость и усталостную прочность, чем традиционно кованый алюминий.
Значительным ограничением в применении сплавов AlLi является анизотропия у деталей, получаемых из отлитых заготовок. Сплав, полученный по технологии spray forming с повышенным содержанием лития, имеет улучшенную изотропию, экспериментально показано отсутствие проблем с растрескиванием отливки и макросегрегацией. Такие заготовки отличаются содержанием кремния до 70%, что практически невозможно получить традициооным литьем из-за то-
130
тального охрупчивания из-за выпадения крупных зерен кремния при кристаллизации и высокого содержания в отлитом сплаве оксидов.
Также был получен сплав с содержание лития до 4%, плотностью 2,4 г/куб. см и с удельной жесткостью на 30% выше, чем у традиционных литых алюминиевых сплавов. Были получены сплавы группы Al-Cu-Mg-X с улучшенными по сравнению с литейными сплавами прочностными свойствами и характеристиками по износу при повышенных температурах. Самым значительным достоинством этой технологии стала возможность получения новых материалов с уникальными свойствами, а также различных функциональных покрытий.
Созданы композиционные материалы (MMC, metal matrix composite). В них матричная основа дополнена керамикой до 15% по объему, что обеспечило повышенную жесткость и износостойкость. Эти композиты получены при вдувании частиц керамики в распыленный поток металла в процессе его осаждения на матрицу по технологии spray forming. На основе алюминия получены сплавы с заданным коэффициентом термического расширения, постоянным в широком диапазоне температур, которые имеют большие перспективы применения в оборудовании для телекоммуникационных систем, аэрокосмической и оборонной промышленности.
Перспективы эта технология имеет и для получения новых конструкционных наноструктурированных материалов. Например, для дальнейшего развития отечественной технологии интенсивной пластической деформации (ИПД). Известно, что ИПД по схеме равноканального углового прессования (РКУП) позволяет получать наноструктурированные заготовки размерами до Ø85 и длиной до 300 мм, которые могут использоваться в машиностроении. При реализации технологической схемы РКУП заготовка неоднократно продавливается в специальной оснастке через два пересекающихся под углом 90 градусов канала с одинаковыми поперечными сечениями
131
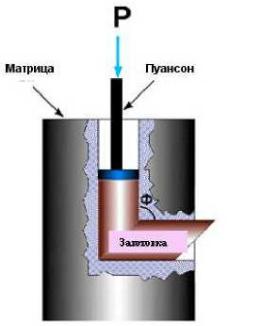
при комнатной или повышенной температурах, в зависимости от свойств деформируемого материала (рис. 7.13).
Наноструктурированность материала обеспечивают за счет очень малого размера зерен. Формируемые заготовки содержат в своей структуре большее количество границ зерен, которые играют определяющую роль в формировании их традиционно недостигаемых физико-механических свойств. При традиционных методах упрочнения пластическим деформированием (прокатке, волочении, ковке) повышение прочности материала приводит к уменьшению его пластичных свойств. Наноструктурированные же в процессе ИПД материалы имеют высокую прочность и пластичность.
Рис. 7.13. Схема процесса РКУП
132
При образовании наноструктур при ИПД очень важным является не только число технологических проходов, но и состояние исходной микроструктуры материала, равномерность распределения химических элементов, составляющих лигатуру сплава по всему объему исходного материала. Технология spray forming позволяет как раз получить подготовленный для ИПД материал.
Перспективным методов внедрения наноматериалов является подшихтовка ультрадисперсных порошков в распыливаемый расплав матричного металла сплава. Этот метод позволяет создавать новые сплавы с равнораспределенным включением в объемную структуру металла наночастиц любых металлов, включая редкоземельные, а также оксидов и др. по желанию.
Процесс распыливания металла и получения порошка - атомизация (англ. atomization - распыление) варьируется в зависимости от исходного металла. В состав атомайзера входят: плавильная камера, где в вакууме или инертной среде производят расплав металла; распылительную камеру, где струю расплавленного металла, вытекающую из плавильной камеры, разбивают на мелкие капли с помощью высокоскоростного потока аргона, воздуха или водяного пара в зависимости от исходного металла и требований по форме отдельных частиц порошка.
Конструкция атомайзеров обеспечивает получение металла в слитках при сливе в изложницу, либо в виде порошка, либо в виде spray forming-заготовки. Заготовки в виде слитков используют для последующей обработки давлением прокатом или ковкой, а также при проведении необходимых технологических исследований.
Обладание такой техникой, кроме возможности проводить широкий круг научно-исследовательских и опытнотехнологических работ в области разработки перспективных технологий и материалов, также снижает зависимость от поставщиков специальных металлических порошков, так как по-
133
зволяет получать в достаточном количестве порошки для решения своих задач, а также снабжать расходными материалами AF-машины для послойного синтеза сложных изделий без последующей механической обработки [4].
Вопросы для самоконтроля
1.Приведите основные понятия и опишите виды аддитивного производства.
2.Расскажите сущность метода стереолитографии при получении литейных моделей.
3.Приведите примеры использования других аддитивных технологий в литейном производстве.
4.Дайте технологическую классификацию аддитивных методов синтеза литейных форм.
5.Для какой цели используются аддитивные технологии
Quick-Cast?
6.В чем заключается построение модели путем послойного склеивания ПВХ-пленки на 3D-принтерах?
7.Опишите порядок производства песчаных литейных форм с использованием AF-технологии.
8.Приведите примеры аддитивной технологии в порошковая металлургия для заготовительного производства наукоемких лопаточных машин.
9.Какие могут быть получены композиционные материалы с помощью технологии spray forming?
10.Каким образом реализуется возможность создания уникальных сплавов с равномерным включением в объемную структуру металла наночастиц различных материалов?
11.Опишите метод равноканального углового прессования и его возможности по наноструктурированию материалов.
134
8.СИНТЕЗ ТЕХНОЛОГИЧЕСКОЙ ОСНАСТКИ
8.1.Использование АМ-технологий для изготовления
оснастки
Серийное производство подразделяют на крупно-, средне- и мелкосерийное. Последнее часто бывает производством многономенклатурным, программа выпуска которого измеряется всего десятками или сотнями изделий одного наименования. Подобных изделий, имеющих сложную геометрическую форму, получаемых из специальных труднообрабатываемых материалов очень много в авиационной, космической промышленности, энергетическом машиностроении и других добывающих отраслях [8].
Особенно в этих областях возник интерес к АМтехнологиям как к возможности прямо выращивать металлические изделия в качестве традиционной товарной продукции. Креативной мотивацией в этом случае являлось не получение экзотики необычайных свойств, а реальная техникоэкономическая целесообразность. В ряде случаев при объективных расчетах реальных затрат на подготовку производства аддитивные технологии оказываются менее затратными традиционных.
Перспективным направлением использования АМтехнологий является быстрое получение технологической оснастки: приспособлений и инструментов для серийного производства. Например, изготовление модульных сменных элементов для термопласт-автоматов (рис. 8.1).
Современное серийное производство характеризуется быстрой сменой выпускаемой продукции. При этом часто сменяются не базовые детали, определяющие функциональные характеристики изделий, а модные потребительские свойства: декоративные панели, элементы декора, которые обычно изготавливаемые литьем, в том числе - и на термо- пласт-автоматах. Поэтому в большинстве случаев нет необхо-
135
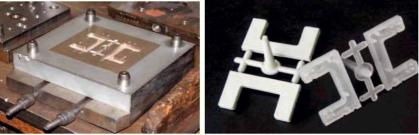
димости использовать дорогостоящую формовочную оснастку, которая работоспособна и сотни тысяч технологических циклов. С помощью АМ-технологий можно быстро получить пресс-форму из легкого сплава с меньшим ресурсом.
Рис. 8.1. Вставка длятермопласт-автомата и отливкиизABS-пластика
Даже для традиционного литейного производства АМтехнологии предоставляют совершенно новые возможности. Так, новая пресс-форма может быть выращена вместе с каналами охлаждения произвольной оптимальной конфигурации, что невыполнимо при использовании традиционных методах механической обработки. АМ-машины POM, Omtomec и Fabrisonic успешно используют для изготовления пресс-форм
смедными охлаждающими сердечниками и с наиболее оптимальной системой охлаждения, конфигурация которой соответствует геометрии формируемого изделия (рис. 8.2). Иначе говоря, каналы охлаждения формируются в толще формы именно как это технологически необходимо, а не исходя из возможностей традиционных методов формообразования. Внедрение литейных форм с равномерным или регулируемым охлаждением позволяет сократить время обязательного нахождения отливки в форме не менее, чем на 30%. Для АМтехнологии это не замена традиционной обработке на станках
сЧПУ, а новые возможности для сокращения затрат и ускорения технологической подготовки многономенклатурного производства.
136
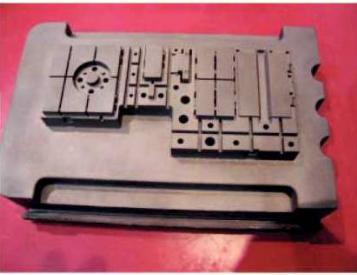
Поддерживание эффективности серийного производства напрямую зависит от своевременного изготовления специальных приспособлений (зажимных элементов, калибров, шаблонов, кондукторов, фиксаторов и т. д.). В этом случае использование АМтехнологий экономически оправдано, так как затраты на технологическую подготовку конкретного изделия напрямую зависят от реального объема производства, а это в рыночных условиях достоверно очень трудно спрогнозировать.
Рис. 8.2. Выращенная пресс-форма
Поэтому очень часто приходится выбирать: получить ли партию деталей на АМ-машине, или создавать традиционные средства технологического оснащения. И при этом постоянно опасаться срочных внесений изменений в технологическую документацию, доработки или переделки оснастки, или, что еще хуже: продукция не пошла на рынке и т. п. Ведь основа рыночного успеха пред-
приятия - постоянное обновление выпускаемой продукции. 137
Конкуренция производителей заставляет в новых разработках, улучшать не только технические характеристики, но и постоянно совершенствовать эстетические и эргономические параметры, использовать новые материалы и технологические процессы. Быстрое изменение требований к потребительским свойствам компенсируется более сложной оснасткой.
Текущие расходы на подготовку производства растут при приближении срока выпуска изделия: в рамках конструк- торско-технологической отработки по результатам испытаний опытных образцов и новой оснастки проводятся уточнения конструкции деталей и средств технологического оснащения (устранение недочетов дизайна, ошибки проектирования и др.). Срыв сроков выпуска продукции ведёт к поражению в конкурентной борьбе. Уменьшить сроки подготовки производства и её стоимость можно только применением современных технологий процессы, например - технологий послойного синтеза.
8.2. Организация производства оснастки по технологии послойного синтеза
Изготовление опытных образцов (моделей, макетов) и их экспертиза (испытание) на этапе разработки эскизного проекта определяет дальнейшую разработку изделия, так как необходимо понять правильность выбранных конструктивнотехнологических решений и получить предварительный отзыв потребителя об изделии до начала серийного производства.
На этапе эскизного проекта проводится обсуждение основных показателей эффективности производства изделий – заданный уровень качества и себестоимость изготовления. Современные возможности абстрактной визуализации проектной формы продолжают совершенствоваться, но пока не могут сравниться по объективности с точной физической мо-
138
делью создаваемого нового изделия. Она в определяющей степени участвует в совместном решении конструктора изделия с конструктором оснастки оперативно на начальных этапах разработки оптимизировать конструкцию с точки зрения её технологичности, стоимости конструкторскотехнологического проекта литьевой формы, её апробирования, отработки. Конечная цель - исключение лишних издержек при выпуске продукции.
Перед началом производства изделия тщательно проверяют и конструкцию, и возможность достижения заданных функциональных характеристик литейной оснастки (собираемость, воспроизводимость размеров и др.), проводятся контрольно-технологические параметрические испытания на различных материалах.
Прочные и термостойкие полимеры, металлические и керамические материалы, используемые в технологии послойного синтеза, позволяют проводить такие испытания, по результатам которых корректируется компьютерная модель. Испытания, при необходимости, повторяются, не требуя изготовления дорогостоящей оснастки с экономией времени и затрат на доработки пресс-форм.
Технологии послойного синтеза позволяют получать небольшие партии деталей, свойства которых с большой достоверностью соответствуют характеристикам деталей, полученных в поточном производстве по традиционным технологиям переработки пластмасс. Такой подход получил название Rapid Manufacturing - быстрое производство, в котором для изготовления небольших установочных партий наукоёмких изделий применяют недолговечную оснастку, недорогую и нетрудоем-
кую [4].
Как пример - эластичные силиконовые формы, срок службы которых составляет не более 50 отливок. Основная область их использования - получение опытных образцов и небольших установочных партий пластмассовых деталей любой группы сложности, реплика деталей и выплавляемых мо-
139