
Сварка специальных сталей и сплавов. методические указания к выполнению лабораторных работ для студентов направления подготовки 15.03.01 «Машиностроение». Чумарный В.П
.pdf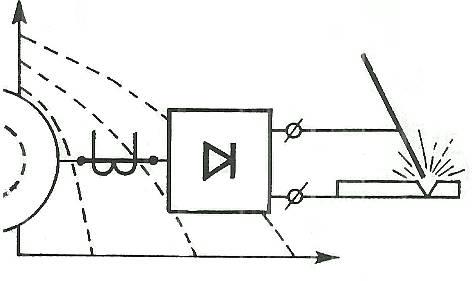
МИНИСТЕРСТВО НАУКИ И ВЫСШЕГО ОБРАЗОВАНИЯ РОССИЙСКОЙ ФЕДЕРАЦИИ
Федеральное государственное бюджетное образовательное учреждение высшего образования «Воронежский государственный технический университет»
Кафедра технологии сварочного производства и диагностики
СВАРКА СПЕЦИАЛЬНЫХ СТАЛЕЙ И СПЛАВОВ
МЕТОДИЧЕСКИЕ УКАЗАНИЯ
к выполнению лабораторных работ № 1-4 для студентов направления подготовки 15.03.01 «Машиностроение»
(профиль «Оборудование и технология сварочного производства») очной и заочной форм обучения
Воронеж 2020
1
УДК 621.791(07)
ББК 34.641я7
Составитель канд. техн. наук В. П. Чумарный
Сварка специальных сталей и сплавов: методические указания к выполнению лабораторных работ № 1-4 для студентов направления подготовки 15.03.01 «Машиностроение» (профиль «Оборудование и технология сварочного производства») очной и заочной форм обучения / ФГБОУ ВО «Воронежский государственный технический университет»; сост. В. П. Чумарный. Воронеж: Изд-во ВГТУ, 2020. - 26 с.
Лабораторные работы позволяют глубже изучить особенности сварки высоколегированных сталей по сравнению с низкоуглеродистыми сталями. Особое внимание уделено влиянию физических свойств сплавов и сталей на свариваемость и особенности структурных превращений при сварке.
Ввиду того, что лабораторные работы выполняются параллельно с прохождением теоретического курса, в первой части и в каждой работе приводятся основные теоретические сведения, которые необходимы студентам для понимания сущности работы.
Методические указания подготовлены в электронном виде и содержатся в файле МУ ССС.pdf.
Предназначены для студентов 3-4 курсов.
Ил. 8. Библиогр.: 6 назв.
УДК 621.791(07)
ББК 34.641я7
Рецензент - В. Р. Петренко, д-р техн. наук, проф. кафедры автоматизированного оборудования машиностроительного производства ВГТУ
Издается по решению редакционно-издательского совета Воронежского государственного технического университета
2
КЛАССИФИКАЦИЯ И ОСНОВНЫЕ ОСОБЕННОСТИ СВАРИВАЕМОСТИ ВЫСОКОЛЕГИРОВАННЫХ СТАЛЕЙ И СПЛАВОВ
К высоколегированным относятся стали на основе железа, легированные одним или несколькими элементами в количестве 10÷55%. Стали, легированные никелем и другими элементами свыше 55%, относятся к сплавам. Высоколегированные сплавы и стали обладают повышенными механическими свойствами: жаропрочностью, жаростойкостью и коррозионной стойкостью в агрессивных средах. В ряде случаев эти стали используются как хладостойкие.
Высоколегированные сплавы и стали широко применяются в химической, энергетической, нефтяной и других отраслях промышленности. При этом в машиностроении применяются более 1500 марок высоколегированных сталей и сплавов.
Высоколегированные сплавы и стали классифицируются по различным признакам.
По свойствам эти материалы делят:
-коррозионно-стойкие – стали, которые сопротивляются коррозии в воде, кислотах, солях, почве;
-жаропрочные – стал сохраняющие свои свойства при повышенных температурах;
-жаростойкие - стали, работающие при температурах вплоть до
1200°С.
Следует отметить, что это деление сталей несколько условно, т.к. есть стали, способные работать при всех указанных условиях, а также и как хладостойкие.
По системам легирования стали делятся на хромистые, хромоникелевые, хромомарганцевые, хромоникельмарганцевые и др.
В качестве легирующих элементов в сталях и сплавах, кроме никеля и хрома, как правило, используются углерод, кремний, ванадий, молибден, титан, алюминий, бор и др.
По структуре при оценке свариваемости специальные стали подразделяют на следующие классы:
-мартенситные - Х5, Х5ВФ, 2Х13, 1Х13М3 и др.;
-мартенситно-ферритные- 1Х12В2МФ, 1Х13, 1Х12ВММФ и др.;
-ферритные0Х13, Х14, Х17, Х25 и др.;
-аустенитно-мартенситные - Х16Р6, Х15М9Ю, 2Х17Н2 и др.;
-аустенитно-ферритные - 0Х20Н14С2, 1Х21Н5Т, Х23Н13 и др.;
-аустенитные - 00Х18Н10, 0Х18Н10Т, 0Х18Н5Г11БАФ и др. Аустенитные сплавы имеют стабильную аустенитную структуру
(ХН35ВТ, 0Х16Н40М5Д3ТЗЮ, ХН60В и др.) и при сварке не претерпевают структурных превращений.
По системе упрочнения различают следующие группы специальных сталей:
3
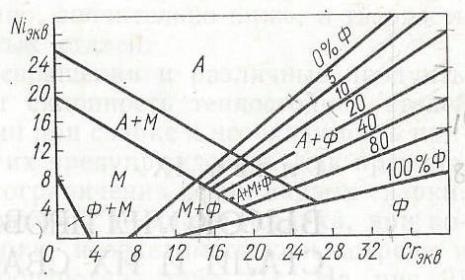
-карбидное - содержание углерода в стали 0,2÷1,0%, при этом образуются карбиды железа, хрома, никеля типов Me23C6 , Me6C, MeC ;
-интерметаллидное – стали, легированные титаном и алюминием, которые образуют мелкодисперсные интерметаллиды типа Ni3 Ti, Al и др.
-боридное – стали на основе боридов железа, хрома, углерода, молибдена.
Следует отметить, что в разной степени в каждой стали имеют место все эти виды упрочнения.
Ввиду многообразия марок важно определить, к какому структурному классу относится сталь, а затем по диаграммам проследить возможные изменения при сварке.
Структура сталей и сплавов определяется соотношением эквивалентного содержания ферритообразующих (Cr , Mo, Si , Ti, Al, W , Nb )
иаустенитообразующих (Ni, Co , C, N , Cu , Mn, B) элементов. Для определения структуры стали пользуются диаграммой Шеффлера (рис.1).
Рис. 1. Структурная диаграмма Шеффлера
На этой диаграмме по вертикальной оси откладывается суммарное содержание в стали аустенитообразующих элементов, которое приводится к эквивалентному действию никеля. По горизонтальной оси диаграммы отложен эквивалент хрома, который характеризует суммарное влияние содержания ферритообразующих элементов. Для подсчёта эквивалентного содержания никеля и хрома применяются эмпирические формулы, основанные на опытных данных. Например:
%NiЭКВ Ti 30 C 0,5 Mn 12 N
%CrЭКВ Cr Mo 1,5 Si 0,5 Nb 4 Ti 3,5 Al 0,8 W 1,5 V
Следует иметь в виду, что эта диаграмма составлена на основании опытных данных, применительно к скорости охлаждения, характерной для обычных режимов сварки, и даёт приближённое представление о структуре
4
стали, а формулы для расчёта эквивалентного содержания никеля и хрома могут уточняться по мере накопления экспериментальных данных.
Общими отличительными признаками высоколегированных сталей по сравнению с углеродистыми сталями являются:
-большой коэффициент линейного расширения (примерно в 1,5 раза больше, чем у углеродистых сталей);
-пониженный коэффициент теплопроводности (в 2 раза меньше, чем у углеродистых сталей);
-высокое удельное сопротивление (в 5 раз больше, чем у углеродистых сталей).
Основными трудностями при сварке специальных сталей являются:
-обеспечение стойкости против образования трещин в шве и в околошовной зоне;
-обеспечение коррозионной стойкости;
-сохранение требуемых свойств в условиях эксплуатации;
-получение плотных швов.
ОСОБЕННОСТИ СТРУКТУРНЫХ ПРЕВРАЩЕНИЙ ВЫСОКОЛЕГИРОВАННЫХ ХРОМИСТЫХ СТАЛЕЙ
К этой группе относятся мартенситные, мартенситно-ферритные и ферритные стали с высоким содержанием хрома.
При содержании хрома более 12% на поверхности стали образуется плотная и достаточно прочная окисная пленка, которая защищает металл от коррозии и окисления при высоких температурах. При наличии других легирующих элементов (молибден, ниобий, ванадий) происходят превращения по мартенситному типу и образуются дисперсные интерметаллидные фазы, что обеспечивает высокую прочность и жаропрочность этих сталей.
Хром относится к легирующим элементам, стабилизирующим в железных сплавах - фазу и уменьшающим область существования - фазы.
Офазовом и структурном состояниях сплавов, системы «железо-хром»,
сразным содержанием хрома, имеющим в своем составе углерод и другие легирующие элементы, можно судить по диаграммам изображёнными на рис.1 и 2.
5

Рис. 2. Диаграмма состояния сплавов «железо-хром»
Хромистые стали, претерпевающие превращения, т.е. находящиеся в пределах концентрации существования - фазы, относятся к мартенситным сталям. В связи с наличием полиморфного превращения эти стали термически обрабатываемы. Чем выше в стали содержание углерода, тем более высокую прочность можно получить после закалки и нормализации, а стали с содержанием углерода менее 0,05% практически не закаливаются и являются ферритными.
При повышении углерода более 0,3% при отжиге образуются карбиды хрома, типа Cr23C6 . При этом твердый раствор существенно обедняется хромом и снижается коррозионная стойкость сталей.
Дополнительное повышение жаропрочности высокохромистых мартенситных сталей достигается введением карбидообразующих элементов - вольфрама, ванадия, молибдена. Эти элементы увеличивают дисперсность карбидной фазы и образуют интерметаллидные фазы Fe2 W,Mo высокодисперсной формы, что увеличивает прочность и жаропрочность. Однако эти легирующие элементы сужают - область, т.е. способствуют увеличению количества феррита, что снижает жаропрочность. Для повышения устойчивости - фазы и уменьшения количества феррита в эти стали вводят никель, который уменьшает критическую скорость охлаждения и снижает температуру мартенситного распада, что обеспечивает повышение прочности.
Стали, содержащие 17% хрома, относятся к ферритно–мартенситным сталям и обладают высокой коррозионной стойкостью. Однофазное - состояние сохраняется при содержании в стали углерода до 0,04%. Нагрев и закалка этих сталей до температур до 1200°С не вызывают перекристаллизации. Однако при более высоком содержании углерода в стали при нагреве может иметь место превращение и после охлаждения может образоваться мартенсит.
6
Основной особенностью этих сталей является их высокая склонность к росту ферритного зерна при нагреве. Оптимальной термообработкой данных сталей, является, отжиг при температуре 760÷780°С. Повышение коррозионной стойкости ферритно-мартенситных сталей достигается легированием хромом до 25÷28%. Эти стали являются чисто ферритными даже при содержании углерода до 0,1%. Такое фазовое состояние резко снижает ударную вязкость и повышает температуру перехода в хрупкое состояние, выше комнатной.
Склонность к росту зерна при нагреве и уменьшение пластичности и вязкости после переохлаждения, требует проведения всех операций деформирования при температуре выше 100° С. Некоторое уменьшение склонности к росту зерна в ферритно-мартенситных сталях, достигается при легировании никелем и азотом, когда образуются небольшие количества - фазы. Стали этой группы обладают повышенной склонностью к 475градусной хрупкости и межкристаллитной коррозии при нагреве до температуры не выше 850°С.
Склонность сталей к межкристаллитной коррозии по границам зерён объясняется образованием при нагреве по границам зерён карбидов хрома и обеднением этих участков хромом. Склонность к межкристаллитной коррозии устраняется введением в сталь титана в количестве в 5 раз больше, чем содержание углерода, для образования карбидов титана и предотвращения образования карбидов хрома по границам зерён. Рассмотренные особенности структурных превращений при нагреве и охлаждении высокохромистых сталей, а также их низкая теплопроводность, по сравнению с углеродистыми сталями, при сварке вызывает ряд трудностей.
ОСОБЕННОСТИ СТРУКТУРНЫХ ПРЕВРАЩЕНИЙ ВЫСОКОЛЕГИРОВАННЫХ ХРОМОНИКЕЛЕВЫХ СТАЛЕЙ
К этой группе сталей относятся сплавы на основе железа с высоким содержанием никеля и хрома. Как известно, никель существенно расширяет температурную и концентрационную область существования - фазы, снижает критическую скорость охлаждения при закалке. При содержании в стали никеля более 8% и хрома более 18%, критическая скорость снижается настолько, что даже при медленном охлаждении при комнатной температуре сохраняется переохлажденный аустенит.
Однако в реальных условиях при наличии в сталях углерода и других легирующих элементов фазовое состояние может быть более сложным и зависит от условий эксплуатации.
Свойства хромоникелевых сталей, их коррозионная стойкость, жаропрочность, хладостойкость и свариваемость зависят от их химического состава.
7
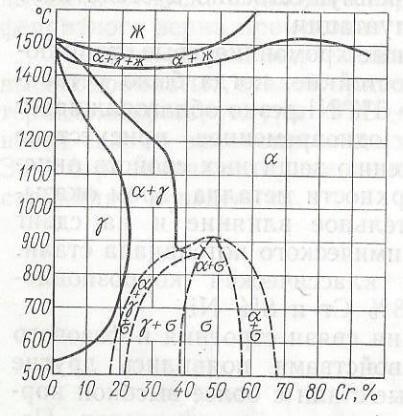
На рис.3 приведена диаграмма «железо-хром» при содержании никеля 8%.Из диаграммы следует, что тройные сплавы Fe Ni Cr при содержании 8% никеля и 20% хрома при нагреве претерпевают превращение.
Рис. 3. Диаграмма состояния сплава «железо-хром» при содержании 8% никеля
При содержании более 22% хрома чистой -фазы не образуется, а только смесь . Максимальное содержание хрома, при котором можно осуществить нагрев до чистого -состояния, возрастает с увеличением содержания никеля.
Следовательно, полностью аустенитная структура может быть поучена, если температура начала мартенситного превращения лежит ниже комнатной и полностью мартенситная структура, если эта температура лежит выше комнатной.
Большое влияние на понижение температуры мартенситного превращения оказывают и другие легирующие элементы (углерод, марганец, кремний). При этом температура мартенситного превращения может смещаться в область отрицательных температур до -100°С. Следовательно, переохлажденный до комнатной температуры аустенит может претерпевать при определенных условиях, например, охлаждение при закалке до пониженных температур или холодная пластическая деформация, мартенситное превращение.
8
Следует отметить, что в сталях со значительным содержанием хрома при нагреве возможны две схемы фазовых превращений. Для сталей в концентрационной области замкнутой петли - фазы (рис.3), нагрев в интервале температур существования одной - фазы не вызывает структурных превращений. При нагреве этих сталей до более высоких температур может образоваться область. Такая - фаза представляет собой высокотемпературный - феррит. При охлаждении таких сталей при высоких температурах происходит обратное превращение и сталь становится ферритно-аустенитной. Количество феррита зависит от содержания аустенито- и ферритообразующих элементов и может быть определено по диаграмме Шеффлера (рис.1). Являясь более хрупкой составляющей по сравнению с аустенитом, феррит снижает вязкость стали, снижает жаропрочность и деформируемость. Количество феррита в основном определяется соотношением содержания хрома и никеля. В сталях типа 18-8 может содержаться феррита до 25%, стали типа 25-20 являются полностью аустенитными.
На количество феррита оказывает влияние содержание и состояние углерода в стали. Как известно, углерод расширяет - область. Однако если он связан в карбиды (хрома и др. элементов), а не растворен в аустените он теряет своё значение как аустенизатор и сталь может перейти в область аустенитно-ферритную. Чтобы избежать этого следует обеспечить растворение карбидов путём выбора условий нагрева и охлаждения.
Отрицательное влияние на свойства хромоникелевых сталей оказывает σ - фаза, которая образуется из α – фазы при длительных нагревах в интервале температур 600 - 900 °С. В этих сталях σ - фаза представляет собой сложное интерметаллидное соединение на базе хрома и железа и значительно увеличивает хрупкость стали.
Следует отметить, что сварные конструкции из аустенитных сталей могут обладать сочетанием нескольких свойств: жаропрочности, хладостойкости и коррозионной стойкости, что связано с особенностями аустенитной структуры и высокой степенью легирования.
Основным условием получения высокой хладостойкости аустенитных сталей является сохранение стабильного аустенитного состояния при пониженных температурах и деформациях.
В этих сталях температура мартенситного превращения лежит ниже -100°С. Карбидообразующие элементы титан, молибден и др. могут обеднять твердый раствор углеродом и сталь при пониженных температурах может перейти в нестабильное аустенитное состояние. Для предотвращения этого применяют термическую обработку (отпуск) на гомогенный аустенит.
Пластическая деформация при пониженных температурах также может вызвать превращение аустенита в мартенсит.
Поэтому хладостойкие стали должны иметь определенный запас аустенитности при отрицательной температуре с учетом такого влияния пластической деформации.
9
Следует иметь в виду, что мелкозернистые стали являются более хладостойкими, по сравнению с крупнозернистыми. Объяснить это можно рассредоточением примесей в объеме стали.
В зависимости от способа обеспечения жаропрочности сталей следует учитывать и особенности их термической обработки. Для сталей, где используется только повышенная жаропрочность (типа 08Х18Н10) применяется закалка на аустенит.
Для сталей с карбидным (типа 10Х14Н4В2М) и интерметаллидным (типа 09Х14Н19ВБР) упрочнением аустенитной основы применяется закалка, старение. При этом закалка обеспечивает растворение углерода и легирующих элементов, а старение – выделение их в дисперсной форме карбидов или интерметаллидов. Старение следует проводить при температурах близких к температурам эксплуатации, во избежание потери жаропрочности при работе изделия.
Высокое содержание никеля и хрома в аустенитных сталях делает их стойкими против химической коррозии. Однако при нагреве данных сталей наблюдается выделение из твердого раствора по границам зерён карбидов хрома, что приводит к увеличению склонности к электрохимической коррозии. Выделение карбидов по границам зерён снижает коррозионную стойкость и повышает хрупкость сталей. Поэтому в этих сталях при повышенных температурах развивается склонность к межкристаллитной коррозии (МКК). Особенно интенсивно процесс МКК протекает в интервале температур 450-850°С. При нагреве выше 900°С, ускоряется диффузионное перемещение атомов хрома к границам зерён, что повышает стойкость стали против МКК. Поэтому оптимальной термообработкой для повышения коррозионной стойкости стали является закалка на гомогенный аустенит.
Повышение стойкости против МКК достигается ограничением содержания в стали углерода и тем самым сведению к минимуму процесса карбидообразования (например: стали 00Х18Н10, 000Х17Н13М2 и др.). Однако получение таких низкоуглеродистых сталей значительно удорожает их стоимость. Поэтому для предотвращения образования карбидов хрома в сталь вводят элементы (титан, ниобий и др.), дающие стойкие карбиды титана и ниобия (например: стали 12Х18Н10Т, 08Х18Н12Б). Карбиды титана и ниобия связывают углерод и при охлаждении располагаются в самих зёрнах, а не по границам. При этом хром остается в свободном состоянии и обеспечивает коррозионную стойкость стали.
10