
Учебное пособие 2013
.pdfЛЕКЦИЯ 1
Поэтому металлические конструкции зданий, опасных в пожарном отношении (склады с горючими или легковоспламеняющимися материалами, жилье и общественные здания), должны быть защищены огнестойкими покрытиями или облицованы бетоном, керамикой и др.
1.5. СПОСОБЫ СОЕДИНЕНИЯ ДЕТАЛЕЙ И УЗЛОВ В СТРОИТЕЛЬНЫХ МЕТАЛЛОКОНСТРУКЦИЯХ
При производстве строительных металлических конструкций применяют следующие виды соединения деталей и узлов:
1.Сварные;
2.Болтовые, в том числе фрикционные на высокопрочных болтах;
3.Клепаные;
4.Клеевые;
5.Комбинированные (клеесварные, клееклепаные, клееболтовые). Наибольший объем соединений в металлоконструкциях выполняют с по-
мощью сварки (более 90 %).
Это связано со следующими преимуществами сварных соединений перед клепаными и болтовыми.
1.Сварные соединения обладают более высокой прочностью, чем клепаные и болтовые. При изготовлении клепаных и болтовых соединений рабочее сечение конструкции уменьшается (ослабляется) отверстиями под болты и заклепки. Кроме того, эти отверстия являются концентраторами напряжений, что значительно снижает усталостную прочность этих соединений при знакопеременных нагрузках.
Прочность сварных соединений составляет 90—100 % прочности металла, из которого изготавливается конструкция, а прочность клепаных — 70—80 %.
2.Сварные соединения обеспечивают высокую герметичность изделий (поэтому сварка незаменима при изготовлении емкостей для хранения и транспортирования различных жидкостей и газов).
Для обеспечения герметичности клепаных или болтовых соединений требуется применение специальных клеев — герметиков.
3.Сварные соединения обладают меньшим весом, чем клепаные и болтовые, т. к. для клепаных и болтовых соединений требуется нахлестка соединяемых деталей или дополнительные накладки; выступающие головки болтов и заклепок, а также гайки еще больше увеличивают вес конструкции и повышают расход металла.
4.Сварные соединения обладают более высокой коррозионной стойкостью из-за отсутствия очагов коррозии в виде щелей, карманов и пазух, в которых накапливается грязь, пыль и влага.
5.При изготовлении сварных соединений достигается более высокая производительность с меньшими затратами труда.
11

СТРОИТЕЛЬНЫЕ МЕТАЛЛИЧЕСКИЕ КОНСТРУКЦИИ
Трудоемкость сварочных работ при производстве металлических конструкций в заводских условиях составляет в среднем 24—25 %, а при монтаже 16— 18 % от общей трудоемкости 1. Таким образом, 40—43 % всех трудовых затрат при изготовлении металлоконструкций приходится на сварочные работы.
Но сварные соединения обладают и рядом недостатков, связанных с самой природой сварочного процесса, при котором металл подвергается концентрированному местному нагреву до температур, превышающих точку плавления. К таким недостаткам относятся:
−наличие остаточных напряжений и деформаций сварных соединений вследствие неравномерного нагрева изделия в процессе сварки;
−образование дефектов в шве и околошовной зоне, которые зачастую возникают внутри металла и для их обнаружения требуются специальные методы контроля (рентгеновское просвечивание, ультразвуковой контроль и др.).
Современный инженер, работающий в строительной отрасли, где, как уже отмечалось, потребляется большое количество металла, особенно при производстве металлоконструкций, должен хорошо представлять себе технологию сварки, знать, какие факторы влияют на качество сварных соединений и определяют производительность этого процесса. Без этих знаний невозможно правильно и рационально организовать производство и обеспечить высокое качество строящихся объектов.
Контрольные вопросы
1.Какие факторы объединяют металлические конструкции в особый вид строительных конструкций?
2.Назовите восемь основных групп металлических конструкций.
3.Назовите основные достоинства металлических конструкций.
4.Перечислите недостатки металлических конструкций и способы уменьшения их негативных последствий.
5.Перечислите способы соединения деталей и узлов при производстве металлических конструкций.
6.Какие преимущества имеют сварные соединения перед клепаными и болтовыми?
7.Какие недостатки присущи сварным соединениям?
1 В настоящее время монтаж отправочных марок (узлов, изготовленных в заводских условиях) на месте возведения объекта во многих случаях наряду со сваркой осуществляется с помощью болтовых соединений (т. н. фрикционные соединения на высокопрочных болтах). Это позволяет с меньшей трудоемкостью и высоким качеством производить соединения на открытом воздухе и больших высотах.
12
ЛЕКЦИЯ 2 ФИЗИЧЕСКИЕ ОСНОВЫ СВАРКИ МЕТАЛЛОВ
2.1. ОБРАЗОВАНИЕ СОЕДИНЕНИЙ ПРИ СВАРКЕ МЕТАЛЛОВ
Болтовые и клепаные соединения являются разъемными, т. е. если удалить болты или заклепки, то соединенные детали можно разъединить без их разрушения. Связь между деталями в таких соединениях обеспечивает механическое сцепление, детали зафиксированы относительно друг друга силами трения, нагрузка воспринимается в основном только болтами или заклепками. То есть, как уже было отмечено, сечение металла соединяемых деталей в этом случае используется нерационально.
При сварке, в отличие от клепаных и болтовых конструкций, соединение деталей происходит на атомном уровне. Рассмотрим этот вопрос более подробно.
Известно, что всякое твердое или жидкое тело представляет собой систему атомов, ионов или молекул, связанных между собой внутренними силами (связями). Эти связи в зависимости от природы вещества (строения атомов и молекул) подразделяются на несколько типов:
−ковалентная,
−ионная,
−металлическая,
−молекулярная.
Первые три типа связей являются химическими межатомными связями, обусловленными электрическим, магнитным и гравитационным взаимодействием атомов вещества. Нехарактерные для металлов наиболее слабые межмолекулярные (ван-дер-ваальсовы) силы наблюдаются при сварке пластмасс и в клеевых соединениях.
2.1.1. Металлические связи
Металлы и их сплавы представляют собой кристаллические тела, в которых атомы располагаются в строго определенном порядке и на определенном расстоянии друг от друга. Это расстояние, называемое параметром кристалли-
ческой решетки, очень мало и в зависимости от типа решетки колеблется в пределах 3-5 Ǻ (Ǻ — ангстрем 1 Ǻ = 10-10м = 10-8 см). Оно настолько мало, что
внешние электронные орбиты соседних атомов перекрывают друг друга, в результате чего валентные электроны свободно переходят от одного атома к другому. То есть в металлических кристаллах внешние электроны не принадлежат определенному атому, они коллективизированы и слабо связаны с ядрами атомов. Поэтому металлы обладают высокой электропроводностью, и уже при не-
13
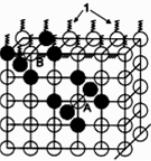
ФИЗИЧЕСКИЕ ОСНОВЫ СВАРКИ МЕТАЛЛОВ
большой разности потенциалов в различных точках в металле возникает направленное движение электронов — электрический ток.
Атомы, расположенные в глубине кристаллического тела, окружены большим, чем поверхностные атомы, количеством соседей. Поэтому все связи у
них использованы и взаимоуравновешены. |
|
Например, в кубической решетке атом |
|
«А» окружен 6-ю ближайшими соседями, а |
|
поверхностный атом «В» — только 5-ю (на |
|
рис. 2.1. соседние атомы закрашены). По- |
|
этому поверхностные атомы имеют сво- |
|
бодные незанятые связи, т. е. имеют «из- |
|
лишек» энергии, которая называется сво- |
|
бодной поверхностной энергией. Поверх- |
|
ность металлического тела стремится пога- |
Рис. 2.1. Кубическая решетка атома: |
сить этот излишек путем адсорбции раз- |
А — атом внутри кристаллического |
личных газов или образования связей с по- |
тела; В — атом на поверхности тела; |
верхностными атомами другого твердого |
1 — незанятые связи |
или жидкого тела. |
поверхностных атомов |
2.1.2. Факторы, препятствующие образованию сварного соединения металлов в реальных условиях
Для соединения двух твердых тел, в результате которого создается общее монолитное тело, необходимо установить между поверхностными атомами соединяемых тел непосредственную связь. Иными словами, надо поверхностные атомы сблизить на расстояния, сопоставимые с параметрами решетки, т. е. на
0
3—5 A. При этом произойдет перекрытие электронных оболочек поверхностных атомов соединяемых тел и валентные электроны будут свободно перемещаться из одного металлического тела в другое и наоборот, т. е. произойдет коллективизация валентных электронов соединяемых тел. Граница раздела между ними исчезнет и образуется одно монолитное тело. Такое соединение было бы идеальным с точки зрения прочности, химической однородности и отсутствия внутренних напряжений.
В реальных же условиях получить такое идеальное соединение невозможно по двум причинам.
Во-первых, как уже было сказано, поверхностные атомы имеют свободные связи, т. е. обладают свободной энергией, поэтому активно взаимодействуют с окружающей средой. На поверхности твердого тела образуются химические соединения (оксиды, нитриды) и адсорбционные пленки влаги, масел и т. п. (рис. 2.2). Толщина слоя продуктов взаимодействия поверхностных атомов достигает десятков, сотен тысяч ангстрем (104—105 Ǻ) и, следовательно,
14
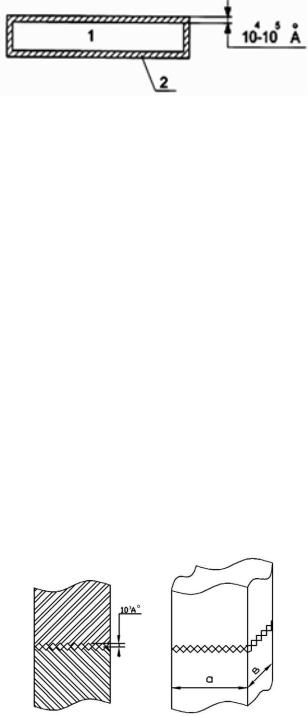
ЛЕКЦИЯ 2
является фактором, препятствующим взаимодействию поверхностных атомов соединяемых тел и образованию неразъемного соединения.
Рис. 2.2. Взаимодействие металлического тела с окружающей средой: 1 — металл, 2 — продукты взаимодействия металла с окружающей средой (оксиды МеО, нитриды МеN, ржавчина и др.)
Во-вторых, поверхность реальных твердых металлических тел представляет собой чередующиеся микровыступы и микровпадины, высота и глубина которых зависит от способов обработки этой поверхности. Даже на поверхности, обработанной по высшему классу точности, высота неровностей превышает
0
1000 A, т. е. в 200—300 раз превышает параметр кристаллической решетки (расстояние, при котором возникают металлические связи). И хотя при сближении реальных тел на их поверхности могут образоваться точки соприкосновения, где возможно межатомное взаимодействие, площадь соприкосновения тел в этих точках составляет всего 0,001—0,01 долю теоретической площади тел в зоне соприкосновения (рис. 2.3), т. е. суммарная площадь соприкосновения реальных тел
∑S = (0,001−0,01)аb ,
где а и b — размеры поперечного сечения соединяемых тел.
Рис. 2.3. Контакт реальных поверхностей твердого тела
Поэтому суммарная величина сил межатомного взаимодействия на поверхности соединяемых тел будет очень мала по сравнению с силами связи внутри тела и прочность такого соединения будет ничтожна, даже если соеди-
15
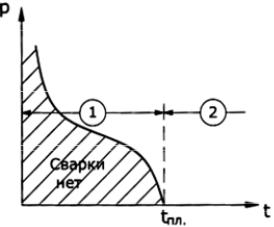
ФИЗИЧЕСКИЕ ОСНОВЫ СВАРКИ МЕТАЛЛОВ
няемые поверхности идеально очищены от адсорбированных веществ и продуктов химического взаимодействия.
Таким образом, для получения качественного неразъемного соединения металлических тел в реальных условиях необходимо решить две задачи:
1)получить чистую поверхность, свободную от оксидов, нитридов и адсорбированных пленок;
2)обеспечить взаимодействие атомов на соединяемых поверхностях не в отдельных точках, а по всей площади соединения. В реальных условиях эти задачи решаются путем применения различных способов очистки свариваемых поверхностей (механическая обработка, химическое травление) и путем защиты зоны соединения от взаимодействия с окружающей средой в процессе сварки (применение флюсов, защитных газов, вакуума и др.). А обеспечение контакта соединяемых деталей по всей площади соединения достигается сдавливанием свариваемых деталей или нагревом металла в зоне соединения до пластического или жидкого состояния.
2.1.3. Классификация способов сварки
Исторически сложилось так, что первые неразъемные соединения человек научился получать, вводя в зону соединения тепловую энергию. Поэтому в русском языке процесс получения неразъемного соединения металлов получил название «сварка». Хотя считается, что соединение за счет межатомного взаимодействия можно получить путем механического сжатия соединяемых деталей без подвода тепла в зону сварки, но, если глубоко рассмотреть этот процесс, не трудно прийти к выводу, что при смятии выступов и течении металла в зоне сварки часть механической энергии сжатия переходит в тепловую.
С повышением температуры металла в зоне соединения усилия, необходимые для обеспечения хорошего контакта по свариваемым поверхностям, уменьшаются и при переходе металла в зоне соединения в жидкое состояние эти усилия становятся равными нулю
(рис. 2.4).
При этом расплавленные участки соединяемых деталей под действием сил Ван-дер-Ваальса сливаются в общий объем подобно тому, как две капли жидкости при сближении объединяются в одну каплю. При последующем охлаждении в результате кристаллизации расплавленного металла образуется монолитное соединение за счет химического взаимодействия атомов соединяемых тел.
16
ЛЕКЦИЯ 2
Таким образом, сварка представляет собой процесс образования неразъемного соединения двух или более твердых тел за счет химического взаимодействия атомов соединяемых тел.
Все способы сварки в зависимости от состояния металла в зоне соединения делятся на две группы (см. рис. 2.4):
1)сварка в твердой фазе (сварка давлением). Температура металла в зоне сварки не превышает температуру плавления металла (на рис. 2.4 это соответствует зоне 1).
2)сварка в жидкой фазе (сварка плавлением); металл в зоне сварки нагревается выше температуры плавления. Таким образом, при сварке плавлением необходимо применять источник тепла, обеспечивающий концентрированный нагрев металла в зоне сварки до температуры выше tпл. (зона 2).
2.2. ЭЛЕКТРОДУГОВАЯ СВАРКА
При изготовлении и монтаже строительных металлических конструкций наибольший объем сварочных работ выполняется с помощью электродуговой сварки.
При электродуговой сварке в качестве источника тепла применяется электрическая дуга, которая представляет собой один из видов устойчивого электрического разряда через газовый промежуток. При этом через газовый промежуток между двумя электродами, подсоединенными к источнику электроэнергии, протекает электрический ток.
В обычном состоянии газовые молекулы электрически нейтральны. Для того чтобы газ стал электропроводным, необходимо, чтобы в нем находились электрически заряженные частицы — электроны и ионизированные молекулы или атомы — ионы. В процессе горения дуги с поверхности отрицательного электрода (катода) под действием электрического поля и разогрева его поверхности вылетают электроны. Процесс выхода электронов с поверхности катода называется эмиссией электронов.
Электроны разгоняются электрическим полем, приобретая значительную кинетическую энергию. Сталкиваясь с атомами и молекулами газа, находящимися в дуговом промежутке, электроны, если они получили достаточную скорость (энергию), могут из нейтральных атомов или молекул выбить электрон. При этом нейтральная частица становится положительно заряженным ионом (рис. 2.5). Этот процесс называется ионизацией газа:
А + е ↔ А+ + 2е.
Положительно заряженные частицы движутся в сторону отрицательного электрода (катода), а отрицательно заряженные — в сторону положительного электрода (анода).
При столкновении электрона с положительным ионом или с поверхностью анода выделяется тепловая энергия Q, которую электрон получил при отрыве
17
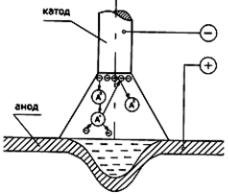
ФИЗИЧЕСКИЕ ОСНОВЫ СВАРКИ МЕТАЛЛОВ
от катода и при разгоне в электрическом поле (протекает процесс деионизации), положительно заряженный ион превращается в нейтральный атом
(рис. 2.5):
А+ + е → А + Q.
В результате этих процессов дуговой промежуток разогревается до 5000—6000 оС. При этом столб дуги выделяет лучистую энергию, растет кинетическая энергия молекул газа и возрастает число их соударений друг с другом. В результате воздействия лучистой энергии на нейтральные молекулы происходит фотоионизация.
Ионизация газа за счет увеличения кинетической энергии молекул и частоты их соударений при высокой температуре называется термической ионизацией.
Для того чтобы из нейтральной молекулы газа выбить электрон, необходимо затратить определенную работу — работу ионизации. Чем менее прочно связан электрон с ядром атома, тем меньшая работа требуется для его отрыва. Минимальная работа, необходимая для отрыва электрона от атома, измеряется потенциалом ионизации в вольтах.
В табл. 2 даны величины потенциалов ионизации некоторых элементов, присутствующих в столбе сварочной дуги.
Таблица 2
Элемент |
Cs |
K |
Na |
Ca |
Fe |
C |
H |
O |
N |
Ar |
He |
ионизации, В |
3,88 |
4,3 |
5,11 |
6,11 |
7,83 |
11,22 |
13,5 |
13,6 |
14,5 |
15,7 |
24,5 |
Потенциал |
|
|
|
|
|
|
|
|
|
|
|
|
|
|
|
|
|
|
|
|
|
|
|
2.3. ВИДЫ СВАРОЧНЫХ ДУГ
Для сварки металлов плавлением дуговой разряд применяется в следующих вариантах.
2.3.1. Дуги прямого и косвенного действия
При сварке дугой косвенного действия (рис. 2.6) нагрев осуществляется дугой (1), горящей между двумя электродами (2) и (3), подключенными к различным полюсам источника электрической энергии (4) (источник питания ду-
18
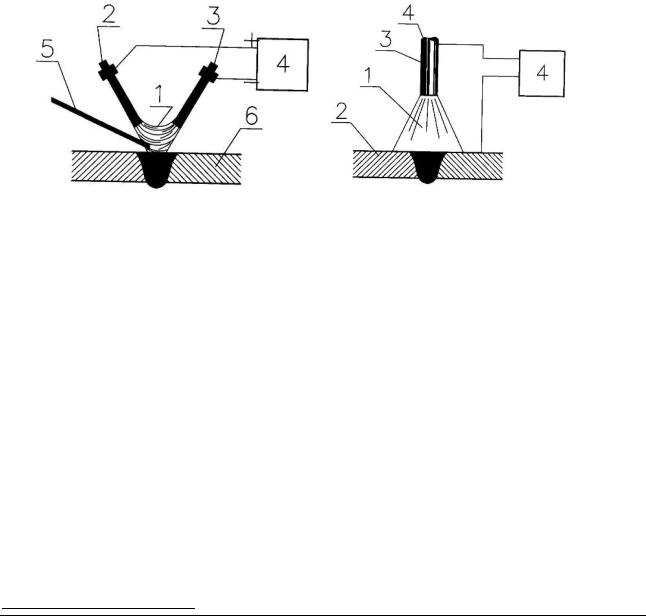
ЛЕКЦИЯ 2
ги), а свариваемое изделие (6) в электрическую цепь не включено. Сварка может выполняться как без добавочного присадочного металла, так и с применением присадки (5). Этот способ применяется очень редко.
При сварке дугой прямого действия свариваемое изделие (2) включено в цепь дуги (1) и является одним из его полюсов, вторым полюсом служит стержень (3), называемый электродом (рис. 2.7). Питание дуги может осуществляться как переменным, так и постоянным током. Если при сварке на постоянном токе электрод подключен к отрицательному полюсу источника питания дуги, то дуга называется дугой прямой полярности. Если электрод подключен к положительному полюсу, а свариваемое изделие — к отрицательному, то дуга называется дугой обратной полярности.
Рис. 2.6 |
Рис. 2.7 |
При сварке на прямой полярности электронов осуществляется с небольшой площади торца электрода, нагретого до высокой температуры (близкой к температуре кипения металла электрода). Это обеспечивает выход (эмиссию) большого количества электронов и устойчивое горение дуги.
При сварке на обратной полярности, когда катодом является свариваемая деталь (минус на изделии), выход электронов происходит с поверхности более холодной, чем электрод сварочной ванны. Поэтому дуга горит менее устойчиво и требует для питания более высокого электрического напряжения.
2.3.2.Сварка дугой прямого действия неплавящимся
иплавящимся электродами
При сварке неплавящимся электродом 1 свариваемое изделие 2 включено в цепь дуги 1 и является одним из ее полюсов. Второй полюс подключается к неплавящемуся (угольному, графитовому или вольфрамовому) электроду 3 (рис. 2.8).
1 Изобретена русским изобретателем Н. Н. Бенардосом (1842—1905 гг.) в 1882 г. (сварка угольным электродом), усовершенствована американским инженером Александером в 1922 г. (аргоно-дуговая сварка вольфрамовым электродом).
19
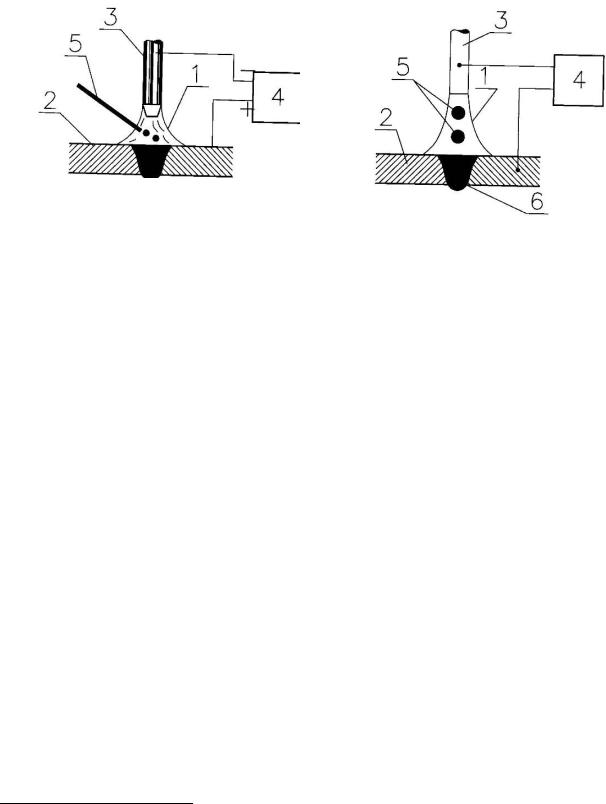
ФИЗИЧЕСКИЕ ОСНОВЫ СВАРКИ МЕТАЛЛОВ
Сварка плавящимся электродом1 — выполняется по такой же схеме, как и при сварке неплавящимся электродом (рис. 2.9).
Рис. 2.8:
1 — электрическая дуга прямого действия;
2 — свариваемое изделие; 3 — неплавящийся электрод; 4 — источник сварочного тока; Рис. 2.9
5 — присадочный металл
Изделие (2) включено в цепь источника питания (4) и является одним из полюсов дуги (1). Электрод (3) является металлическим, по химическому составу близким к свариваемому металлу, интенсивно расплавляется дугой. Расплавленные капли (5) электродного металла пролетая через дугу, стекают в сварочную ванну (6).
2.4. СПОСОБЫ ДУГОВОЙ СВАРКИ ПЛАВЯЩИМСЯ ЭЛЕКТРОДОМ
Для обеспечения устойчивого процесса дуговой сварки необходимо выполнять движение электрода в двух направлениях (рис. 2.10):
1)по мере плавления электрода для поддержания постоянства длины дуги подавать электрод в сторону дуги,со скоростью V (скорость подачи электрода);
2)для получения качественного сварного шва по линии соединения перемещать электрод вдоль стыка с определенной скоростью Vсв. (скорость сварки).
3)В зависимости от степени механизации этих двух элементов дуговую сварку плавящимся электродом подразделяют на следующие виды:
−ручную дуговую (РД);
−полуавтоматическую (ПА) (механизированную);
−автоматическую (А).
При ручной сварке перемещение электрода в обоих направлениях сварщик выполняет вручную. От стабильности скорости подачи электрода в зону дуги за-
1Изобретена русским инженером, нашим земляком, Н. Г. Славяновым (1854 — 1897 .)
в1888 г. В настоящее время широко применяется во всем мире и во всех отраслях экономики.
20