
Технологическая оснастка. методические указания к выполнению лабораторных работ для студентов направления 15.03.01 «Машиностроение». Симонова Ю.Э
.pdfМИНИСТЕРСТВО НАУКИ И ВЫСШЕГО ОБРАЗОВАНИЯ РОССИЙСКОЙ ФЕДЕРАЦИИ
Федеральное государственное бюджетное образовательное учреждение высшего образования
«Воронежский государственный технический университет»
Кафедра автоматизированного оборудования машиностроительного производства
ТЕХНОЛОГИЧЕСКАЯ ОСНАСТКА
МЕТОДИЧЕСКИЕ УКАЗАНИЯ
к выполнению лабораторных работ для студентов направления 15.03.01 «Машиностроение»
(профиль «Технологии, оборудование и автоматизация машиностроительных производств»)
всех форм обучения
Воронеж 2021
1
УДК 621.9(07)
ББК 34.5-5я7
Составитель: Ю. Э. Симонова
Технологическая оснастка: методические указания к выполнению лабораторных работ для студентов направления 15.03.01 «Машиностроение» (профиль «Технологии, оборудование и автоматизация машиностроительных производств») всех форм обучения / ФГБОУ ВО «Воронежский государственный технический университет»; сост. Ю. Э. Симонова. – Воронеж: Изд-во ВГТУ, 2021. - 29 с.
В методических указаниях изложены требования и общие вопросы по выполнению лабораторных работ, приведены теоретические сведения, полезные не только для выполнения лабораторных работ, но и при подготовке к сдаче зачетов и экзаменов. Выполнение лабораторных работ дает возможность получения навыков для выбора технологического оснащения при обработке деталей машиностроительного производства с использованием государственных стандартов, учебной и справочной литературы.
Издание предназначено для студентов направления 15.03.01 «Машиностроение» (профиль «Технологии, оборудование и автоматизация машиностроительных производств») всех форм обучения всех форм обучения.
Методические указания подготовлены в электронном виде в файле ТОЛР.pdf.
Ил. 24. Табл. 2. Библиогр.: 5 назв.
УДК 621.9(07)
ББК 34.5-5я7
Рецензент ‒ С. Ю. Жачкин, д-р. техн. наук, проф. кафедры автоматизированного оборудования машиностроительного производства ВГТУ
Издается по решению редакционно-издательского совета Воронежского государственного технического университета
2
ЛАБОРАТОРНАЯ РАБОТА № 1
ИССЛЕДОВАНИЕ ВЛИЯНИЯ УСИЛИЯ ЗАЖИМА НА ТОЧНОСТЬ ОБРАБОТКИ ДЕТАЛЕЙ
Цель работы: ознакомление с зажимными механизмами приспособлений, определение влияния усилия зажима на точность обработки деталей.
Общие сведения о зажимных механизмах приспособлений
Зажимные устройства используются для обеспечения правильной установки и центрирования заготовки, выполняя функцию установочнозажимных устройств. К ним относятся самоцентрирующие патроны, цанговые зажимы и др. Силовые механизмы приспособлений делятся на простые и комбинированные, т.е. состоящие из двух-трех сблокированных простых. К простым механизмам относятся клиновые, винтовые, эксцентриковые, рычажные, рычажно-шарнирные и т.п. По числу ведомых звеньев механизмы делятся на однозвенные, двухзвенные и многозвенные (многоточечные). Каждый силовой механизм имеет ведущее звено, к которому прикладывается исходная сила, и одно или несколько ведомых звеньев (прижимных планок, плунжеров, кулачков), передающих обрабатываемой детали силы зажима. Многозвенные механизмы зажимают одну деталь в нескольких точках или несколько деталей в многоместном приспособлении одновременно и с равными силами. Особую группу многозвенных механизмов составляют самоцентрирующие патроны и оправки. По степени механизации зажимные механизмы делят: на ручные, требующие применения мускульной силы. При использовании ручных механизмов для зажима заготовок усилие зажима не должно превышать 147 Н. Ручные механизмы применяют в единичном и мелкосерийном производстве; механизированные, представляющие собой компоновку простых или комбинированных механизмов с механизированными приводами. Применяют их в серийном и массовом производстве; автоматизированные зажимные механизмы, которые приводятся в действие перемещающимися частями станков (столами, суппортами, шпинделями и др.), силами резания или центробежными силами вращающихся масс. Зажим и раскрепление заготовки при их использовании происходят без участия рабочего. Автоматизированные зажимные механизмы применяют в крупносерийном и массовом производстве. Главной задачей при разработке любого приспособления является установление типа и размеров зажимного устройства, а также определение силы, развиваемой приводом. Задача решается путем построения схемы закрепления деталей в приспособлении и определения: а) места приложения и направления сил зажима; б) величины сил резания и их моментов, действующих на обрабатываемую деталь, а при необходимости – инерционных и центробежных сил, возникающих при обработке; в) величины усилий зажима при решении задачи статики на
3
равновесие твердого тела, находящееся под действием всех приложенных к нему сил; г) требуемой величины сил зажима путем умножения найденного значения сил зажима на коэффициент запаса K. Коэффициент запаса K рассчитывается применительно к конкретным условиям обработки по формуле
К= К1 ∙К 2∙К3∙К4 ∙К5∙К6 |
(1.1) |
где K0 = 1,5 – гарантированный запас для всех случаев; |
K1 – |
коэффициент, учитывающий состояние поверхности заготовки. Для черновой заготовки K1 = 1,2, для чистовой заготовки K1 = 1,0; K 2 – коэффициент, учитывающий увеличение сил резания от прогрессирующего затупления инструмента: K2 = 1,0–1,9; K3 – коэффициент, учитывающий увеличение силы резания при прерывистом резании. При работе с ударами K3 = 1,2; K 4 – коэффициент, учитывающий постоянство силы зажима, развиваемой силовым приводом приспособления: K4 = 1 для механизированных силовых приводов (пневматических, гидравлических и т. д.); K4 = 1,3 для ручного привода; K5 – характеризует зажимные механизмы с ручным приводом. При удобном положении рукоятки зажима и малом диапазоне угла ее отклонения K5 = 1,0; при большом диапазоне угла отклонения рукоятки (более 90) или неудобном расположении рукояток K5 = 1,2; K6 – коэффициент, учитываемый только при наличии крутящих моментов, стремящихся повернуть обрабатываемую деталь. K6 = 1,0, если обрабатываемая деталь установлена базовой плоскостью на опоры с ограниченной поверхностью контакта; K6 = 1,5, если обрабатываемая деталь установлена на планки или другие элементы с большой поверхностью контакта. Силу, развиваемую силовым приводом, можно определить по формуле
Q = KW / i, |
(1.2) |
где i – передаточное отношение зажимного механизма, которое зависит от его конструкции и размеров.
Влияние усилия зажима на погрешность формы деталей При закреплении нежестких деталей типа колец возникают погрешности
формы цилиндрической поверхности заготовки, что влияет на точность обработки деталей. В зажимных устройствах (патронах) с обычными (узкими) кулачками наибольшие прогибы колец возникают в местах приложения сил, а наибольшие выпучивания – в сечениях симметрии между кулачками. При наличии широких кулачков деформация колец снижается.
Методика расчета деформации тонкостенных колец при закреплении радиальными силами применима при отношении толщины стенки кольца к среднему радиусу (h / r ≤ 0,2) и при условии, что кольцо полностью перекрыто кулачками или длина участков кольца, выступающих за кулачками, не превышает
4
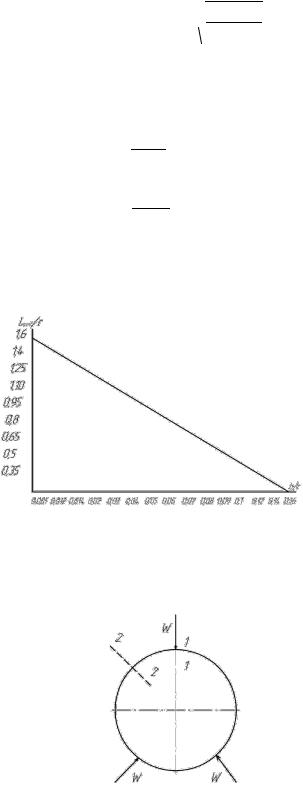
lпред = 1,3rn−1 (n2 r−1)h
где n – число кулачков;
r и h – средний радиус и толщина стенки кольца соответственно, мм:
r= D+d
4
h= D− d
2
(1.3)
(1.4)
(1.5)
На рисунке представлена номограмма, позволяющая быстро найти lпред при известных n, r и h /r.
Рис. 1.1. Номограмма для определения lпред
На рис. 2 представлена схема закрепления тонкостенного кольца в трехкулачковом патроне.
Рис. 1.2. Схема закрепления кольца в трехкулачковом патроне
Наибольший прогиб кольца в сечении рассчитывается по формуле
δ1−1 |
= 0.016 |
Wr3 |
(1.6) |
|
EI |
||||
|
|
|
||
|
5 |
|
|
где W – сила зажима от кулачка (для удобства расчета суммарная сила зажима отнесена к одному кулачку);
r = (D + d)/4 – радиус нейтральной окружности кольца; Е – модуль упругости материала кольца;
I – момент инерции поперечного сечения кольца относительно нейтральной оси:
I = |
bh3 |
(1.7) |
12 |
где b – высота кольца.
Наибольшее выпучивание в сечении 2–2 можно подсчитать по формуле
δ2−2 |
= −0.014 |
Wr3 |
|
(1.8) |
|||
EI |
|||||||
|
|
|
|
||||
Силу зажима от одного кулачка W можно определить из условия |
|||||||
равновесия кольца: |
|
|
|
|
|
|
|
|
kМрез = Wf D/2 |
(1.9) |
|||||
Отсюда |
|
|
|
|
|
|
|
|
W = |
2kM рез |
|
(1.10) |
|||
|
fD |
||||||
|
|
|
где W– суммарная сила зажима, отнесенная к одному кулачку; k – коэффициент запаса;
Мрез – момент резания;
f – коэффициент трения между кольцом и кулачками: f = 0,16–0,18;
D – наружный диаметр кольца. При закреплении тонкостенного кольца двумя призмами возникают погрешности формы, зависящие от силы прижима и угла призм.
На рисунке представлена схема закрепления тонкостенного кольца двумя призмами с углом α = 90о. Перемещения в сечениях 2–2, 3–3, 4–4 определяются следующим образом:
δ2−2= 0.006 |
|
Wr |
3 |
|
- прогиб |
(1.11) |
|||
|
EI |
|
|||||||
δ3−3= 0.004 |
Wr |
3 |
|
– прогиб |
(1.12) |
||||
EI |
|
|
|||||||
δ4− 4= − 0.012 |
Wr |
3 |
– выпучивание |
(1.13) |
|||||
EI |
|
6
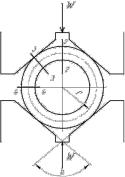
Рис. 1.3. Схема закрепления кольца в призму
Сила зажима детали в призмах определяется по формуле
W = kMрез sinα / (fD) |
(1.14) |
где k – коэффициент запаса; Мрез – момент резания; α – угол призмы; f – коэффициент трения между кольцом и двумя самоцентрирующими призмами: f = 0,16–0,18; D – наружный диаметр кольца.
Порядок выполнения работы
1.У выданных преподавателем тонкостенных колец определить наружный диаметр D, внутренний диаметр d и высоту h.
2.Пользуясь формулой, определить усилие зажима W от кулачков при растачивании кольца, закрепленного в трехкулачковом патроне, при следующих значениях момента резания: а) М = 0,15 Нм; б) М = 0,2 Нм; в) М = 0,25 Нм.
3.Определить наибольший прогиб и выпучивание кольца для каждого полученного усилия зажима W по формулам. Данные занести в табл. 1.1
|
|
|
|
|
|
|
|
|
Таблица 1.1 |
|
|
|
|
|
|
Результаты измерений |
|||
|
|
|
|
|
|
|
|
|
|
№ |
D, |
d |
h |
Mрез |
Перемещение, мкм |
|
Возможность |
||
де |
м |
, |
, |
, Нм |
|
|
|
|
закрепления |
та |
м |
м |
м |
|
|
|
|
|
|
ли |
|
м |
м |
|
|
|
|
|
|
|
|
|
|
|
|
|
|
|
|
|
|
|
|
|
теоретическое |
практическое |
|
||
|
|
|
|
|
1–1 |
2–2 |
1–1 |
2–2 |
|
|
|
|
|
|
|
|
|
|
|
4. Для получения необходимого усилия зажима при различных моментах резания определить исходную силу Q, прикладываемую к рукоятке динамометрического ключа. Уравнение сил механизма патрона в общем виде
7
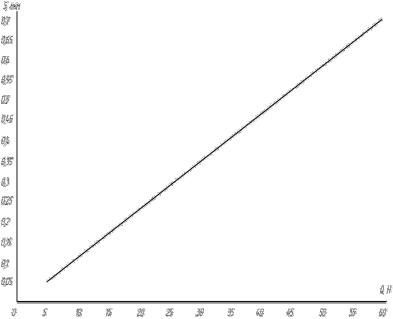
W = Qηпi1i2i3 |
(1.15) |
где i1, i2, i3 – передаточные отношения сил рычажных и центрирующего клиноплунжерного механизмов. В нашем случае i1 = 16,4; i2 = 0,89; i3 = 6,65.
КПД патрона определяется по формуле
ηп= ηкз ηк ηпп |
(1.16) |
где ηп – КПД патрона; ηкз = 0,96 – КПД конического зацепления; ηк = 0,153
– КПД клиновой пары «спираль–рейка кулачка»; ηпп = 0,81 – КПД поступательной пары «кулачок–направляющие корпуса патрона».
5. По тарировочному графику определить показания индикатора динамометрического ключа для полученной исходной силы Q.
Рис. 1.4. Тарировочный график динамометрического ключа
6.Зажать кольцо в трехкулачковый патрон с исходной силой Q и измерить значение прогибов и выпучиваний (перемещений) в сечениях 1–1, 2–2 по показаниям стрелки индикатора. Повторить опыт три раза для каждого найденного усилия зажима. Данные занести в таблицу
7.Пользуясь формулой, определить усилие зажима W от призмы при растачивании кольца, закрепленного в призмах самоцентрирующего механизма, при следующих значениях момента резания: а) Мрез = 0,3 Нм; б) Мрез = 0,4 Нм; в) Мрез = 0,5 Нм.
8.Определить прогибы δ2–2, δ3–3 и выпучивание δ4–4 для каждого полученного усилия зажима W по формулам.
8
|
|
|
|
|
|
|
|
|
Таблица 1.2 |
|
|
|
|
|
|
|
|
|
|
№ |
D, |
d |
h |
Mрез |
Перемещение, мкм |
|
|
Возможность |
|
де |
м |
, |
, |
, Нм |
|
|
|
|
закрепления |
та |
м |
м |
м |
|
|
|
|
|
|
ли |
|
м |
м |
|
|
|
|
|
|
|
|
|
|
|
|
|
|
|
|
|
|
|
|
|
теоретическое |
практическое |
|
||
|
|
|
|
|
1–1 |
2–2 |
1–1 |
2–2 |
|
|
|
|
|
|
|
|
|
|
|
В табл. 1.2 прогиб следует представлять в виде положительной, а выпучивание кольца – в виде отрицательной величины. Значение модуля нормальной упругости для колец, изготовленных из стали 45 ГОСТ 1050–88, Е
=2,1*105 МПа.
9.Определить исходную силу Q, прикладываемую к рукоятке динамометрического ключа, для получения необходимого усилия зажима при различных моментах резания. Сила зажима, развиваемая винтовым механизмом:
W =Q |
l |
|
|
(1.17) |
r tg(α +ϕ |
пр |
) |
||
|
ср |
|
|
где l = 160 мм – длина рукоятки ключа; rср = 20 мм – средний радиус резьбы;
α = 2–4о – угол подъема резьбы; φпр – приведенный угол трения для метрической резьбы (φпр = 60).
10. Зажать кольцо в призмах и измерить значения прогибов и выпучиваний в сечениях 2–2, 3–3, 4–4. Повторить опыт три раза для каждого найденного усилия зажима. Данные занести в таблицу.
12. Определить возможность закрепления колец для полученных усилий зажима, если допустимая погрешность формы не превышает 0,00001 м. При закреплении в трехкулачковом патроне погрешность формы заготовки
∆ф = (|δ1| + |δ2|),
а при закреплении в призмах
∆ф = (|δ2| + |δ4|).
9
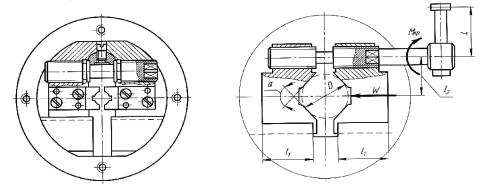
ЛАБОРАТОРНАЯ РАБОТА № 2
ТЕХНИЧЕСКОЕ ОСНАЩЕНИЕ СТАНДАРТНЫМИ ПРИСПОСОБЛЕНИЯМИ ТОКАРНЫХ СТАНКОВ
Цель работы: ознакомиться с различными видами конструкций и принципами работы стандартных приспособлений, применяемых для установки и закрепления заготовок инструмента на токарно-винторезном станке;
Общие теоретические сведения
На токарных станках большинство обрабатываемых деталей, в зависимости от формы и размеров, устанавливают либо в центрах, либо в патроне. Один центр расположен в шпинделе передней бабки, а второй – в пиноле задней бабки. Патрон устанавливают и закрепляют на конце шпинделя передней бабки токарного станка. Кулачковые патроны применяют для установки и зажима различных типов заготовок, обрабатываемых на токарных станках. В зависимости от количества кулачков патроны подразделяют на двух-, трех- и четырехкулачковые. Патроны двух- и трехкулачковые являются самоцентрирующими, а четырехкулачковые изготавливают в основном с независимым перемещением кулачков, но бывают и самоцентрирующие. Различают два основных типа универсальных двухкулачковых патронов – патроны с ручным зажимом, расположенным сбоку (для черновых работ) и патроны с центральным винтом (длячистовых работ). На рисунке 1,а представлен универсальный двухкулачковый патрон с ручным винтовым зажимом, находящимся с боку и служащий для перемещения кулачков при зажиме и разжиме небольших заготовок инструмента. На рисунке 1,б показана расчетная схема для определения силы и момента, действующих на патрон. Такую конструкцию патрона применяют для обработки заготовок инструмента на предварительных (черновых) операциях, так как боковое расположение винта может вызывать некоторый перекос перемещаемых кулачков.
а) б)
Рис. 2.1. Универсальный двухкулачковый самоцентрирующий патрон с ручным винтовым зажимом: а) конструктивная схема; б) расчетная схема
10