
Учебное пособие 1555
.pdf4.Какие показатели относят к показателям, характеризующим точность обработки изделия?
5.Какие показатели относят к показателям, характеризующим геометрическую точность станка?
6.Какие показатели относят к дополнительным показателям точности
станка?
7.Столько классов точности станков выделяют? Как их обозначают?
8.Какие требования установлены по отношению к испытанию станков на точность?
9.Какие требования установлены по отношению к методампроверки?
10.Какие проверки проводят при испытаниях токарного станка?
ПРАКТИЧЕСКАЯ РАБОТА № 13 КОНТРОЛЬ КОНСТРУКТИВНЫХ ЧАСТЕЙ ТОКАРНОГО РЕЗЦА,
ОЦЕНКА СООТВЕТСТВИЯ ПО РЕЗУЛЬТАТАМ ИЗМЕРЕНИЙ
Теоретическаячасть
1. Общиесведения
При обработке заготовок на токарных станках используют резцы, которые классифицируются по нескольким признакам (рис. 13.1):
а) по конструкции режущей части:
−цельные (рис. 13.1, 1),
−с припаянной пластинкой из твёрдого сплава (рис.13.1, 2.),
−с механическим креплением режущейпластинки (рис.13.1, 3); б) по форме головки резца:
−прямые (рис. 13.1, 4),
−отогнутые (рис.13.1, 5.),
−оттянутые (рис.13.1, 6.);
в) по направлению подачи (рис. 13.1, 7):
−правые,
−левые;
г) по виду выполняемой работы:
−проходные для обтачивания гладких цилиндрических и конических поверхностей (рис. 13.1: 8, 9, 10),
−подрезные для обтачивания плоских торцовых поверхностей(рис. 13.1, 11),
− расточные для растачивания сквозных |
(рис. 13.1, |
12.1) иглухих (рис. |
|
13., 12.2) отверстий, |
|
|
|
− отрезные для разрезания заготовок на части и для протачивания |
|||
кольцевых канавок (рис. 13.1, 6), |
|
|
|
− галтельные |
для обтачивания |
переходных |
поверхностей |
между ступенями валов по радиусам (рис. 13.1,13), − резьбовые наружные (рис. 13 . 1.14) и внутренние (рис. 13.1, 15).
21
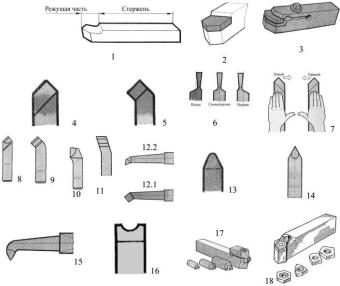
−фасонные для обтачивания фасонных поверхностей (рис. 13.1, 16); д) по роду режущего материала:
−из быстрорежущей стали,
−с пластинками из твёрдого сплава,
−с пластинками из минералокерамики,
−с кристаллами алмазов и эльбора (рис.13.1, 17).
д) по роду режущего материала:
−из быстрорежущей стали,
−с пластинками из твёрдого сплава,
−с пластинками из минералокерамики,
−с кристаллами алмазов и эльбора (рисунок 1, 17).
Рис. 13.1. Типы токарных резцов
В настоящее время в промышленности находят широкое применение резцы с многогранными неперетачиваемыми пластинкамитвёрдого сплава (рис. 13.1, 18).
2. Части,элементыигеометриятокарногопроходногорезца
Токарный проходный резец состоит из двух частей (рис. 13.1, 1): режущей части (головки) и державки (стержня).
Режущая часть резца (рис. 13.2) имеет следующие элементы: переднюю поверхность, по которой сходит стружка;
−главную заднюю поверхность, обращённую к поверхности резания на заготовке;
−вспомогательную заднюю поверхность, обращённую к обработанной поверхности заготовки;
−главное режущее лезвие (кромку), которым является линия пересечения передней и главной задней поверхностей;
−вспомогательное режущее лезвие (кромку), которым является линия пересечения передней и вспомогательной задней поверхностей;
22

− вершину резца, которой является точка пересечения главного и вспомогательного режущих лезвий.
Рис. 13.2. Элементы режущей части прямого проходного резца
Чтобы резец мог осуществлять работу резания, его поверхности затачивают под определёнными углами (рис. 13.3). Для определениявеличины углов резца (рис. 13.4) вводят две координатные плоскости (основную и плоскость резания) и две секущие плоскости (главную и вспомогательную). Вспомогательная секущая плоскость условно не показана.
Основной плоскостью называется плоскость, параллельная направлениям продольной и поперечной подач.
Плоскостью резания называется плоскость, проходящая касательно к поверхности резания через главное режущее лезвие резца.
Главной секущей плоскостью называется плоскость, проходящая через произвольную точку главного режущего лезвия перпендикулярно к проекции главного режущего лезвия на основную плоскость.
Вспомогательной секущей плоскостью называется плоскость, проходящая через произвольную точку вспомогательного режущего лезвия перпендикулярно к проекции вспомогательного режущего лезвия на основную плоскость.
Рис. 13.3. Геометрические параметры режущей части прямогопроходного резца
23

Рис. 13.4. Координатные и секущие плоскости
В главной секущей плоскость измеряют передний угол γ и главный задний угол α.
Во вспомогательной секущей плоскость измеряют вспомогательный задний
угол α1.
Передним углом γ называется угол между передней поверхностью резца и плоскостью, перпендикулярной к плоскости резания, проведённой через главное режущее лезвие резца.
Главным задним углом α называется угол между передней и главной задней поверхностями резца.
Вспомогательным задним углом α1, называется угол между передней и вспомогательной задней поверхностями резца.
Углом заострения β называется угол между передней и главной задней поверхностями резца.
Углом резания δ называется угол между передней поверхностью резца и плоскостью резания.
Между углами существуют следующие зависимости: α+β+γ=90о; α+β=δ; β=90о–(α+γ).
Углы α, β, γ выбирают так, чтобы уменьшить до возможных пределов сопротивление металла резанию, но вместе с тем необходимо обеспечить достаточную прочность резца.
Абсолютная величина углов γ, α, α1 влияет на шероховатость обработанной поверхности, величину силы резания и т.д.
Кроме рассмотренных углов различают у резца углы в плане. Главный и вспомогательный углы а плане ψ и ψ1 измеряют между направлениям подачи и проекцией главного или вспомогательного режущих лезвий на основную плоскость. Угол при вершине резца ε в плане – угол между проекциями режущих лезвий (главного и вспомогательного) на основную плоскость.
Угол наклона главного режущего лезвия λ (угол между главным режущим лезвием и линией, проходящей через вершину резца параллельно основной плоскости) измеряется в плоскости, проходящей через главное режущее лезвие перпендикулярно к основной плоскости. Угол λ влияет на направление схода стружки (рис. 13.5).
24

3. Прибориизмерениегеометрическихпараметроврезцов
Сечение тела резца измеряют штангенциркулем или измерительной линейкой, а углы резца – универсальным и настольным угломерами. Самым распространённым угломером является универсальный угломер ЛМТ (рисунок 6), который предназначен для измерения основных углов резца 2 – переднего γ, главного заднего α, вспомогательного заднего α1, главного и вспомогательного в плане ψ и ψ1, наклона главного режущего лезвия λ.
Рис. 13.5. Угол наклона главного режущего лезвия
Рис. 13.6. Универсальный угломер ЛМТ:
а– общий вид; б – схема измерения угла γ; в – заднего угла α;
ги д – углов ψ и ψ1
Универсальный угломер (рис. 13.7) состоит из плиты 1, вертикальной стойки 6, на которой перемещается устройство, состоящее из блока 11, трёх шкал с измерительными ножами. Шкальное устройство устанавливается и перемещается
25

на стойке 6 по шпоночному пазу и при необходимости (после ослабления фиксатора 12) может поворачиваться вокруг оси стойки и устанавливаться в любом положении по высоте. Измерительные ножи шкальных устройств снабжены винтами (14), позволяющими фиксировать требуемое положение.
Верхняя плоскость плиты угломера снабжена направляющейлинейкой 15. На рис. 13.7 иллюстрируются способы измерения углов токарного проходного правого резца с отогнутой головкой.
Для измерения переднего угла γ измерительный нож 3 шкалы 4 настраивается перпендикулярно главному режущему лезвию резца и прижимается до соприкосновения с передней поверхностью резца. Совмещение измерительного ножа с гранью резца должно быть плотным без просвета. При этом указатель 5 измерительного ножа показывает значение γ.
Измерение задних углов α и α 1 производится с помощью изме-рительного ножа 10, который плотно прижимается к главной или вспомогательной задним поверхностям резца. Определение значения угла производится аналогично переднему.
Для измерения главного ψ и вспомогательного ψ1 углов в плане резец устанавливается на плите 1 до соприкосновения с направляющей линейкой 15, а шкальное устройство поворачивается на стойке в требуемое положение до соприкосновения измерительного ножа 13 в первом случае с главным, а во втором со вспомогательным режущим лезвием. Отсчёт значений углов производится с помощью указателя 8 на шкале 9. После измерения главного и вспомогательного углов в плане ψ и ψ1 можно определить угол при вершине ε по следующей зависимости:
s = 180oC − († + †1).
Для измерения угла наклона главного режущего лезвия λ шкала 4 поворачивается на стойке в требуемое положение до соприкосновения с вершиной резца. При повороте измерительного ножа 3 до соприкосновения с главным режущим лезвием указатель 5 фиксирует значение угла λ.
Рис. 13.7. Универсальный угломер ЛМТ:
26
а – измерение углов γ, α, α1, λ; б – измерение углов ψ и ψ1
После измерения вышеуказанных углов значения остальных углов
подсчитывают по формулам: |
δ=90о–γ, |
β=90о–(α+γ) |
при γ>0о |
||
при γ<0о |
δ=90о+γ, |
β=90о–α+γ |
при γ=0о |
δ=90о, |
β=90о–α |
Приборы и инструменты: |
штангенциркуль |
(0+160 мм); угломер |
универсальный ЛМТ; комплект токарных резцов.
Заданиядляпрактическойработы
Практическая работа. Контроль конструктивных частей токарного резца, оценка соответствия по результатам измерений
Работа выполняется в группах по 2 человек.
Лабораторная работа производится в следующей последовательности.
1.Изучить измерительные приборы.
2.Произвести измерения конструктивных элементов токарного резца и занести в таблицу результатов работы (таблица 13.1).
|
|
|
|
|
Результаты работы |
|
|
Таблица 13.1 |
|||
|
|
|
|
|
|
|
|
||||
Наименование и тип резца |
Металл режущей части |
|
|
|
|
Углы резца в градусах |
|
|
|||
Основные размеры BxHxL |
Передний угол γ |
Задний главный угол α |
Задний вспомогательный угол α1 |
Угол заострения β |
Угол резания δ |
Главный угол в плане ψ |
Вспомогательныйугол в плане ψ1 |
Угол при вершине ε |
Угол наклона главной режущей кромкм λ |
||
|
|
|
|
|
|
|
|
|
|
|
|
3.Произвести измерения геометрических параметров токарного резца и занести в таблицу результатов работы (таблица 13.1).
4.Выполнить эскиз измеряемого резца с приведением его конструктивных и геометрических параметров.
5.Оформить отчет
Содержаниеотчета:
1)название работы;
2)цели;
3)таблица с результатами работы;
4)4)эскиз замеряемого резца;
5)результаты измерений, оформленные в виде таблицы 13.1;
6)основные выводы.
6.Представьте на проверку преподавателю отчет о выполнении работы.
Ответьте на контрольные вопросы.
Контрольные вопросы
1.Какие признаки используются при классификации резцов?
2.Как квалифицируют резцы по конструкции режущей части?
3.Как квалифицируют резцы по форме головки резца?
27

4.Как квалифицируют резцы по направлению подачи?
5.Как квалифицируют резцы по виду выполняемой работы?
6.Как квалифицируют резцы по роду режущего инструмента?
7.Из каких частей состоит резец?
8.Перечислите элементы режущей части проходного резца.
9.Какие исходные плоскости вводят для измерения главных и вспомогательных углов резца?
10.Перечислите главные углы резца.
ПРАКТИЧЕСКАЯ РАБОТА № 14 ОЦЕНКА ТЕХНИЧЕСКОГО СОСТОЯНИЯ ТЕХНОЛОГИЧЕСКОЙ
ОСНАСТКИ
Теоретическая часть
1. Общие сведения
Средства технологического оснащения – совокупность орудий производства, необходимых для осуществления технологического процесса (рис. 14.1).
Рис. 14.1. Средства технологического оснащения
Технологическое оборудование – средства технологического оснащения, в которых для выполнения определенной части технологического процесса размещаются материалы или заготовки, средства воздействия на них, а также технологическая оснастка.
Технологическая оснастка – средства технологического оснащения, дополняющие технологическое оборудование для выполнения определенной части технологического процесса (примерами технологической оснастки являются приспособления, пресс-формы, режущие инструменты, калибры и т.д.).
Приспособление – технологическая оснастка, предназначеннаядля установки или направления предмета труда или инструмента при выполнении технологической операции.
Инструмент – технологическая оснастка, предназначенная для воздействия на предмет труда с целью изменения или определенияего состояния.
28
По служебному назначению различают следующие типы технологической оснастки.
− Станочные приспособления для базирования и закрепления изготавливаемых деталей на обрабатывающих станках. Эти приспособления обычно получают наименования по группам станков, на которых они используются: токарные, шлифовальные, фрезерныеи др.
− Станочные приспособления для базирования и закрепления рабочего инструмента, которые чаще именуют вспомогательным инструментом. К их числу относят: оправки и патроны для режущего инструмента, резцедержатели для токарных станков и инструментальные державки для автоматов.
− Станочные устройства для направления и координирования режущего инструмента: габариты, копиры, направляющие втулки, используемые для режущего инструмента на расточных станках и станках сверлильной группы.
−Сборочные приспособления для базирования и закрепления собираемых изделий.
−Сборочные приспособления для соединения и закрепления присоединяемых деталей, для установки упругих деталей.
−Сборочный инструмент: оправки для установки и запрессовки деталей, отвертки для завинчивания деталей, вальцовочный и другой инструмент.
−Контрольные устройства, предназначенные для проверки параметров изготавливаемых изделий и рабочего инструмента.
−Устройства для хранения заготовок и изготавливаемых изделий:
стеллажи и магазины.
−Захватные устройства манипуляторов и промышленных роботов,
предназначенные для ориентирования, транспортирования и установки заготовок, деталей и собираемых изделий.
По степени специализации технологической оснастки различают:
−специальную, предназначенную для массового и крупносерийного производства,
−специализированную переналаживаемую и непереналаживаемую для серийного изготовления изделий,
−универсальную – для выполнения различных операций над разными изделиями.
−Специальная технологическая оснастка предназначена для выполнения определенных технологических операций и переходов по изготовлению и контролю конкретного изделия или изделий одного наименования и представляет собой неразборную непереналаживаемую конструкцию одноцелевого назначения.
Специализированная технологическая оснастка предназначена для
выполнения определенных технологических операций и переходов по изготовлению и контролю ряда (группы) изделий, обладающих конструктивнотехнологической общностью конфигураций, позволяющих использовать единые
базирующие устройства.
29
Универсальная технологическая оснастка предназначена для широкой номенклатуры изделий и выполнения ряда технологических операций и переходов по их изготовлению и контролю и представляет собой конструкцию многоцелевого назначения с едиными базирующими устройствами. К ним относятся тиски, патроны, делительные головки и поворотные столы.
По степени механизации и автоматизации приспособления подразделяют на: ручные, механизированные, полуавтоматические, автоматические.
Типы технологической оснастки отличаются по стоимости, производительности, выполняемым с их помощью технологических операций, по трудозатратам подготовительно-заключительного времени. Поэтому выбор того или иного типа должен осуществляться на основе выполнения экономических расчетов.
Технологическая оснастка – это средство технологического оснащения, дополняющее технологическое оборудование для выполнения части технологического процесса (ГОСТ 3.1109-82).
Технологическая оснастка – звено технологической системы, связывающее изготавливаемый или контролируемый объект или инструмент с оборудованием с целью достижения требуемого качества объекта, экономичности его изготовления, облегчения труда и его безопасности. Поставленная цель будет достигнута, если технологическая оснастка будет соответствовать своему служебному назначению, излагаемому в техническом задании.
В общем виде технологическая оснастка характеризуется следующими качественными показателями:
1.Требуемая точность базирования объекта или объектов.
2.Требуемое значение силы закрепления (силового замыкания)объекта.
3.Требуемая точность установки объекта или объектов.
4.Требуемая точность координирования рабочего инструмента.
5.Требуемая точность изменения относительного положения рабочего инструмента и изготавливаемого объекта производства.
6.Точность установки технологической оснастки на оборудовании.
7.Производительность выполнения операции с использованием технологической оснастки.
8.Требуемые затраты времени на замену изготавливаемых или контролируемых объектов производства.
9.Требуемые затраты времени на замену рабочего инструмента.
10.Экономичность.
11.Контроль.
12.Габаритные размеры технологической оснастки.
13.Масса технологической оснастки.
14.Удобство обслуживания.
15.Безопасность работы.
16.Степень механизации и автоматизации и т.д.
30