
Учебное пособие 1511
.pdf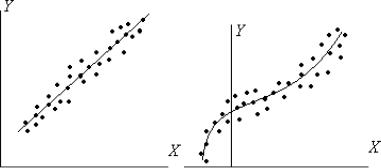
Форма и расположение кластера точек на диаграмме разброса определяют различные варианты корреляции парных данных. Наиболее часто встречающиеся из них приведены на рис. 23.7.
а б Рис. 23.7. Виды корреляционного поля
Визуально, по внешнему виду корреляционного поля можно оценить структуру функциональной зависимости Y(X). Если корреляционное поле – вытянутый эллипс то связь линейная (рис.23.7., а). Чем уже эллипс, тем теснее связь. Если корреляционное поле представляет собой неправильную фигуру, то можно предположить, что зависимость нелинейная (рис.23.7, б). Если корреляционное поле – круг, с равномерной плотностью распределения точек, то можно сказать, что связи между переменными нет.
Диаграмма разброса является удобным и простым инструментом для выявления взаимосвязи парных данных. Однако сильная взаимосвязь не обязательно означает, что одна переменная напрямую связана с другой переменной. В частности, может быть третья переменная, которая влияет на исследуемые парные данные и которая в итоге «кластеризует» точки на диаграмме разброса.
8. Диаграмма Исикавы
Диаграмма Исикавы (Ишикавы) или причинно-следственная диаграмма (иногда ее называют диаграмма «рыбья кость») – применяется с целью графического отображения взаимосвязи между решаемой проблемой и причинами, влияющими на ее возникновение. Как правило, данный инструмент качества используют совместно с методом «мозгового штурма», т.к. он позволяет быстро отсортировать по ключевым категориям причины проблем, найденных с помощью «мозгового штурма».
Диаграмма Исикавы дает возможность выявить ключевые параметры процессов, влияющие на характеристики изделий, установить причины проблем процесса или факторы, влияющие на возникновение дефекта в изделии. В том случае, когда над решением проблемы работает группа специалистов, причинно-следственная диаграмма помогает группе достичь общего понимания проблемы. Также, с помощью диаграммы Исикавы можно понять, каких данных, сведений или знаний о проблеме недостает для ее решения и тем самым сократить область принятия необоснованных решений.
21
Когда строится диаграмма Исикавы, причины проблем распределяют по ключевым категориям. В качестве таких категорий выступают – человек, методы работы (действий), механизмы, материал, контроль и окружающая среда. Все причины, связанные с исследуемой проблемой детализируются в рамках этих категорий:
Причины, связанные с человеком включают в себя факторы, обусловленные состоянием и возможностями человека. Например, это квалификация человека, его физическое состояние, опыт и пр.
Причины, связанные с методом работы заключают в себе то, каким образом, выполняется работа, а также все, что связано с производительностью
иточностью выполняемых операций процесса или действий.
Причины, связанные с механизмами – это все факторы, которые обусловлены оборудованием, машинами, приспособлениями, используемыми при выполнении действий. Например, состояние инструмента, состояние приспособлений и т.п.
Причины, связанные с материалом – это все факторы, которые определяют свойства материала в процессе выполнения работы. Например, теплопроводность материала, вязкость или твердость материала.
Причины, связанные с контролем – это все факторы, влияющие на достоверное распознавание ошибки выполнения действий.
Причины, связанные с внешней средой – это все факторы, определяющие воздействие внешней среды на выполнение действий. Например, температура, освещенность, влажность и т.п.
Пример. Диаграмма Исикавы построена для определения причин неравномерной толщины покрытия, наносимого гальваническим способом на металлические детали (рис. 23.8). Исследуемая проблема – неравномерность толщины покрытия. Причины распределяются по пяти ключевым категориям – человек, метод, материал, механизмы, контроль. Наиболее значимые причины выделены красным цветом.
Диаграмма Исикавы обладает следующими преимуществами: позволяет графически отобразить взаимосвязь исследуемой проблемы и причин, влияющих на эту проблему; дает возможность провестисодержательный анализ цепочки взаимосвязанных причин, воздействующих на проблему; удобна и проста для применения и понимания персоналом. Для работы с диаграммой Исикавы не требуется высокая квалификация сотрудников, и нет необходимости проводитьдлительное обучение.
22

Рис. 23.8. Диаграмма Исикавы
К недостаткам данного инструмента качества можно отнести сложность правильного определения взаимосвязи исследуемой проблемы и причин в случае, если исследуемая проблема является комплексной, т.е. является составной частью более сложной проблемы. Другим недостатком может являться ограниченное пространство для построения и прорисовывания на бумаге всей цепочки причин рассматриваемой проблемы. Но данный недостаток может быть преодолен, если диаграмма Исикавы строится с применением программных средств.
Задания для практической работы
Практическая работа. Оформление результатов оценки соответствия технологического процесса требованиям нормативных документов и технических условий
Задание 1. Гистограммы.
Изучите теоретический материал, представленный в методических указаниях. Составьте таблицу: Виды гистограмм по форме таблицы 23.4. Оформите схему на листе формата А4 с указанием фамилии, имени, отчества, группы.
Таблица 23.4
Форма таблицы «Виды гистограмм»
|
Графическое представление |
Описание |
Несоответствия, вы- |
|
№ |
явленные при анализе |
|||
гистограммы |
гистограммы |
|||
|
||||
|
|
|||
|
|
|
гистограммы |
|
|
|
|
|
|
|
|
|
|
Задание 2. Сильные и слабые стороны инструментов качества. Изучите теоретический материал, представленный в методических указаниях. Составьте схему: Сильные и слабые стороны инструментов качества. Оформите схему на листе формата А4 с указанием фамилии, имени, отчества, группы.
23
Задание 3. Диаграмма Исикавы.
Обучающиеся делятся на группы по 3-4 человека и строят причинноследственную диаграмму для продукции, услуги, изделия, процесса или группы процессов по их собственному выбору. Из всех выбранных факторов выделяются наиболее значимые. В выводах обосновывается выбор факторов и построение диаграммы. Оформите диаграмму на листе формата А4 с указанием фамилий, имен, отчеств, группы.
Примерные варианты процессов:
1.Изучение дисциплины в рамках обучения по специальности.
2.Перевозка пассажиров городским автотранспортом.
3.Доставка посылок почтой России.
4.Посещение поликлиники.
5.Получение кредита в банке.
6.Пассажирские авиаперевозки.
7.Приготовление супа
Представьте на проверку преподавателю отчет о результатах работы. Ответьте на контрольные вопросы.
Контрольные вопросы
1.Назовите основные инструменты контроля качества.
2.Для чего используют контрольный листок? Каков порядок его построения?
3.Для чего используют гистограмму? Каков порядок ее построения?
4.Для чего используется метод стратификации?
5.Для чего используется диаграмма Парето? Каков порядок ее построения?
6.Для чего используется диаграмма рассеивания? Каков порядок ее построения?
7.Для чего используется диаграмма Исикавы? Каков порядок ее построения?
ПРАКТИЧЕСКАЯ РАБОТА № 24 ЗАПОЛНЕНИЕ ОПЕРАЦИОННОЙ КАРТЫ КОНТРОЛЯ НА
ОСНОВАНИИ ТРЕБОВАНИЙ ЧЕРТЕЖА К ИЗГОТОВЛЕНИЮ ДЕТАЛИ
Теоретическая часть
1.Общие положения
Техническую документацию контроля разделяют на три вида:
1.Технологическая документация;
2.Сопроводительная документация;
3.Накопительная документация.
24
Под технологической документацией понимают операционные карты и ведомости операций.
Операционные карты и ведомости операций используют для описания технологических операций и технологических процессов технического контроля. В составе комплекса ЕСТД разработан ГОСТ 3.1502-85 « ЕСТД. Формы и правила оформления документов на технический контроль».
Операционные карты предназначены для описания технологических операций технического контроля с указанием содержания и последовательности переходов. Под переходом понимают элементарную часть технологической операции. Операционные карты, как правило, разрабатывают для сложных операций с большим числом переходов. Они используются в крупносерийном и массовом производстве. В их указывают контролируемые параметры, данные о применяемых средствах технологического оснащения и норм времени.
Ведомости операций предназначены для операционного описания технологических операций технического контроля в технологической последовательности с указанием переходов. Их разрабатывают в том случае, если технологический процесс содержит большое число операций технического контроля, а сами операции состоят из двух – трёх несложных переходов.
Ведомости операций и операционные карты должны применяться совместно с маршрутной картой или заменяющими ее картами технологического процесса или картой типового (группового) технологического процесса в зависимости от того, разрабатывается комплект документов на единичный или типовой (групповой) технологический процесс.
В зависимости от сложности изделия и объема контролируемых параметров операции технического контроля могут входить в самостоятельный технологический процесс технического контроля, так и быть составными частями технологических процессов, специализированных по методам обработки, оформления и сборки.
Наименование операций технического контроля следует применять по классификатору технологических операций машиностроения и приборостроения.
Операции технического контроля могут быть описаны в маршрутном или маршрутно-операционном описании (в единичном и мелкосерийном производстве) либо в операционном описании (в крупно-серийном и массовом производстве).
Для разработки технологической документации на испытания в составе ЕСТД разработан ГОСТ 3.150784 «ЕСТД. Правила оформления документов на испытания». Их разрабатывают в форме маршрутных карт.
Совместно с операционными картами, ведомостями операций, и маршрутными картами могут применяться карты эскизов, на которых помещаются графическое изображение зоны изделия, подлежащие контроля или испытаниям, таблицы контролируемых параметров, схемы и т.п.
25
При разработке технологических документов используют унифицированные и машинно-ориентированные формы, обеспечивающие возможность обработки содержащейся в них информации с применением средств вычислительной техники.
Сопроводительная документация сопровождает каждое изделие или партию изделий на протяжении всего технологического процесса. К сопроводительным документам относят технологический паспорт, технологическую бирку и сопроводительный ярлык.
Технологический паспорт предназначен для указания содержания выполняемых при изготовлении изделия операций и проставления подписей исполнителей и контролирующих лиц. Документ используется для учёта и анализа результатов контроля при изготовлении особо ответственных изделий.
Технологический паспорт оформляется также на специфические технологические процессы, например, когда время выполнения отдельных операций или между их выполнением регламентировано. Этот документ после приемки и сдачи изделия хранится в ОТК весь период, рассчитанный на эксплуатацию изделия. В технологический паспорт могут входить вспомогательные документы: карты измерений и испытаний. Их используют для регистрации результатов измерения контролируемых параметров при изготовлении изделий и регистрации условий, режимов и контролируемых параметров при проведении испытаний. На картах проставляются даты выполнения и подписи исполнителей.
Технологическая бирка является разновидностью паспорта и оформляется на несколько изделий одного типа.
Сопроводительный ярлык является разновидностью технологической бирки при изготовлении большой партии.
На ряде предприятий к сопроводительным документам относят рабочие карты (рабочие наряды, сменные задания). В этих документах оформляются сведения, указывающие общее количество контролируемых объектов и результаты проверки их качества.
Накопительные документы используются для дальнейшего анализа и обобщения результатов контроля и получения сводных карт (отчётов) по контролю. К таким документам относятся: акты (извещения) о браке, рекламационные карточки и журналы контроля технологического процесса и др.
Акты о браке оформляются контролерами БТК. Он является основным первичным документом для учета и анализа брака. Браком считается продукция, которая по своему качеству не соответствует нормативнотехнической документации. На основании актов составляются сменные или ежедневные сводки по браку. Они позволяют более углубленно изучать причины брака с целью разработки эффективных мероприятий по его устранению.
26
Рекламационные карты заполняются после анализа причин отказов продукции. Она может быть полезной при последующем обобщении и сопоставлении с данными контроля по другим рекламациям. В журналы контроля заносится текущая информация о контроле качества материалов и полуфабрикатов, состоянии технологических операций и процессов и результатах приемочного контроля готовой продукции.
Накопительная документация позволяет получить историю качества по выпуску продукции данного типа с целью управления процессом изготовления продукции и прогнозирования её качества. Для систематизации сведений о браке продукции и автоматизации учёта результатов контроля вводятся классификаторы. Они представляют собой шифры из набора цифр и букв. С помощью шифра фиксируют виды и причины брака, а также их виновников.
При анализе причин брака принимают во внимание следующиепринципы:
Сначала формируются предположение (версия), которая затем уточняется путём проведения определённой исследовательской работы;
Область поиска причин дефектности сужают, переходя от общего к частному;
Устанавливаются отрицательно действующие на качество факторы и определяются характеризующие их параметры, которые нужно контролировать;
Анализ причин дефектности должен быть направлен на выявление причино-следственных связей;
Определяют наиболее существенные причины брака или отказа и результаты исследования изображают в виде диаграмм или графиков;
Если трудно выявить отдельные причины брака, которые могут быть зависимы от нескольких факторов, используют методы статистического анализа.
При изучении и анализе брака или отказов сварных изделий можно выявить три группы причин:
1.Конструктивные причины. Они являются следствием несовершенства методов расчёта, недостаточным учётом реальных условий эксплуатации и ошибками в проектировании изделия и технологической подготовке производства.
2.Производственные причины. Они являются следствием отклонений в производственных процессах изготовления изделий. Производственные причины, как и дефекты, можно разделить на металлургические и технологические причины.
Металлургические причины связаны с металлургическими факторами производства отливок и их последующей обработки для получения свариваемых деталей.
Технологические причины связаны с: неудовлетворительной подготовкой
поверхности; низким качеством сборки; нарушением технологии сварки;
27
низкой квалификацией сварщиков; неисправностью оборудования; неблагоприятными производственными условиями.
3.Эксплутационные причины. Они связаны с нарушением условий эксплуатации изделий.
2. Технический контроль
Процесс технического контроля разрабатывают как совокупность взаимосвязанных операций технического контроля для отдельных групп и типов материалов, заготовок, полуфабрикатов, деталей и сборочных единиц, а также для отдельных видов технического контроля и производств.
Операции контроля разрабатывают для входного, операционного и приемочного контроля изделий. Операции контроля назначаютпосле тех этапов обработки, где вероятно повышенное количество брака, перед сложными и дорогостоящими операциями, после законченного цикла, а также в конце обработки детали.
При разработке процессов и операций контроля должны выполняться следующие требования:
1)контроль должен предотвращать пропуск дефектных материалов, полуфабрикатов, заготовок, деталей и сборочных единиц на последующие этапы изготовления, испытания, ремонта и потребления;
2)контроль должен соответствовать требованиям действующей на предприятии системы менеджмента качества;
3)контроль должен соответствовать требованиям промышленной безопасности, пожаро- и взрывобезопасности, промышленной санитарии и правилам защиты окружающей среды;
4)проектирование технического контроля осуществляют с учетом характеристик технологического процесса изготовления изделия с обеспечением необходимой взаимосвязи и взаимодействия между ними;
5)при проектировании технического контроля должны обеспечиваться: достоверная оценка качества продукции и снижение потерь от брака; повышение производительности труда; снижение трудоемкости контроля; возможное совмещение операций изготовления с операциями технического контроля; сбор и обработка информации для контроля, прогнозирования и регулирования технологических процессов обработки; оптимизация технического контроля по установленным технико-экономическим критериям;
6)при проектировании операций технического контроля следует обеспечивать единство измерительных баз с конструкторскими и технологическими;
7)уровень механизации и автоматизации контроля должен соответствовать требованиям технологии изготовления изделия, а также условиям и типу производства.
Основные этапы разработки процессов технического контроляи задачи, решаемые на каждом этапе, представлены в таблице 24.1.
28
Таблица 24.1 Порядок разработки процессов и операций технического контроля
|
Этап разработки процессов |
Задачи, решаемые на этапе |
|
|
|
||
1. Подбор и анализ исходных материалов |
Ознакомление с изделием, требованиями к |
||
|
для разработки процессов контроля. |
изготовлению, испытаниям, ремонту и |
|
|
Подбор и анализ справочной ин- |
эксплуатации. |
|
формации, необходимой для раз-работки |
|
||
|
процесса контроля. |
|
|
|
2. Выбор объектов и видов контроля |
Оценка возможности и стабильности |
|
|
|
|
технологического процесса изготовления, |
|
|
|
испытания и ремонта. Определение |
|
|
|
номенклатуры объектов контроля. Установление |
|
|
|
видов контроля по его объектам. Определение |
|
|
|
технических требований на операции контроля. |
|
|
|
|
|
3. Выбор действующего типового, |
Отнесение объекта контроля к действующему |
|
группового процесса контроля или поиск |
типовому, групповому или единичному |
||
аналога единичного процесса контроля |
процессу контроля с учетом количественной |
||
|
|
|
оценки групп изделий. |
|
|
|
|
|
|
|
Определение состава и последовательности |
|
|
|
технологических операций контроля, |
|
|
|
обеспечивающих своевременное выявление и |
|
4. Составление технологического |
устранение дефектов и получение информации |
|
|
маршрута процесса контроля |
для оперативного регулирования и |
|
|
|
|
прогнозирования технологического процесса. |
|
|
|
Предварительное определение состава |
|
|
|
контрольного оборудования. |
5. Разработка технологических операций |
Выбор контролируемых параметров |
||
технического контроляВыбор методов и |
(признаков). Выбор схем контроля, определение |
||
средств контроля. Определение объема |
контрольных точек объектов, измерительныхбаз. |
||
|
(плана) контроля. Разработка |
|
|
|
последовательности переходов |
|
|
|
технического контроля. |
|
|
|
|
|
|
|
6. Нормирование процессов контроля |
Установление исходных данных, необходимых |
|
|
Расчет и нормирование затрат |
для расчетов норм времени и расхода |
|
|
|
|
материалов. |
|
|
|
|
|
7. Расчет технико-экономической |
Выбор оптимального варианта процесса |
|
|
эффективности процесса контроля |
технического контроля. |
|
|
|
|
|
8. |
Оформление |
технологических |
Заполнение технологических документов. |
документов на технический контроль |
Нормоконтроль технологической документации. |
||
|
|
|
Согласование технологической документации с |
|
|
|
заинтересованными подразделениями и ее |
|
|
|
утверждение. |
|
|
|
Установление порядка оформления результатов |
9. Разработка документации результатов |
контроля и необходимого состава форм |
||
|
контроля |
документов. Разработка технологических |
|
|
|
|
паспортов, карт измерения, журналов кон-троля. |
|
|
|
29 |
Процессы технического контроля содержат в среднем 26...30 операций (по числу технологических операций плюс операция входного контроля) для объектов 1-й категории, 15...18 операций – для объектов 2-й категории, 6...10 операций – для объектов 3-й категории. Категории указаны в классификаторе деталей, обрабатываемых резанием. В общем виде маршрут технического контроля содержит:
1. Входной контроль марки материала, геометрических и физических параметров, внешнего вида объекта.
Входной контроль проводят на предприятиях с целью предотвращения запуска в производство продукции поставщиков, не соответствующей установленным требованиям конструкторской и нормативной документации, договоров на поставку и протоколов разрешения. Входной контроль осуществляют по параметрам (требованиям) и методами, установленными в нормативной документации на продукцию, в договорах на поставку и протоколах разрешения.
Задачами входного контроля являются:
–проверка наличия сопроводительной документации на продукцию, удостоверяющей качество и комплектность продукции;
–контроль соответствия качества и комплектности продукции требованиям конструкторской и технологической документации и применения
еев соответствии с протоколами разрешения;
–накопление статистических данных о фактическом уровне качества получаемой продукции и разработка на этой основе предложений по повышению качества и, при необходимости, пересмотра требований нормативной документации на продукцию;
–периодический контроль за соблюдением правил и сроков хранения продукции поставщиков.
Входной контроль необходимо проводить в специально отведенном помещении (участке), оборудованном необходимыми средствами контроля, а также отвечающем требованиям безопасности труда. Входной контроль проводят кладовщик, контролер соотвествующей квалификации.
Порядок проведения входного контроля:
1)проверить сопроводительные документы, удостоверяющие качество продукции, и зарегистрировать продукцию в журналах учета результатов входного контроля;
2)проконтролировать отбор складскими работниками выборок или проб, проверить комплектность, упаковку, маркировку, внешний вид и заполнить акт отбора выборок или проб;
3)провести контроль качества продукции по технологическомупроцессу входного контроля или передать в соответствующее подразделение выборки или пробы для испытаний (анализов).
30