
Основные механические свойства металлических материалов и методы их оценки. Орлов А.С., Рубцова Е.Г
.pdfФедеральное агентство по образованию
Государственное образовательное учреждение высшего профессионального образования
Воронежский государственный архитектурно-строительный университет
ОСНОВНЫЕ МЕХАНИЧЕСКИЕ СВОЙСТВА МЕТАЛЛИЧЕСКИХ МАТЕРИАЛОВ
И МЕТОДЫ ИХ ОЦЕНКИ
Методические указания к выполнению лабораторных работ по курсу «Материаловедение»
для студентов, обучающихся по направлению 190200 «Транспортные машины и транспортно-технологические комплексы» всех форм обучения
Воронеж 2010
УДК 669.01 (075.8) ББК 34.2
Составители А.С. Орлов, Е.Г. Рубцова, И.Ю. Зиброва
Основные механические свойства металлических материалов и методы их оценки: метод. указания к выполнению лабораторных работ по
дисциплине «Материаловедение» для студ. направл. 190200 / Воронеж. гос. арх.-строит. ун-т; сост.: А.С. Орлов, Е.Г. Рубцова, И.Ю. Зиброва.- Воронеж, 2010.- 32 с.
Дается описание наиболее распространенных способов механических испытаний металлических материалов и приводятся количественные характеристики механических свойств, которые могут быть определены при этих испытаниях. Дана последовательность выполнения лабораторных работ раздела «Механические свойства» курса «Материаловедение»: цель работы, краткие теоретические сведения, порядок проведения испытаний, описание применяемых приборов и порядок оформления отчетов. Приведены справочные данные из нормативной литературы.
Предназначены для студентов, обучающихся по направлению подготовки дипломированных специалистов 190200 «Транспортные машины и транспортно-технологические комплексы» всех форм обучения.
Ил. 8. Табл. 6. Библиограф.: 8 назв.
УДК 669.01 (075.8) ББК 34.2
Печатается по решению редакционно-издательского совета Воронежского государственного архитектурно-строительного университета
Рецензент – Н.А. Барченкова, к.т.н., доц. кафедры строительной механики Воронежского государственного архитектурно-строительного университета
2
ВВЕДЕНИЕ
Свойство – это количественная или качественная характеристика материала, определяющая его общность или различие с другими материалами.
Металлы и сплавы характеризуются комплексом физических, химических, механических и технологических свойств.
Физические свойства металлов и сплавов важны для самолетострое-
ния, автомобилестроения, строительства, медицины и часто являются основными характеристиками, по которым определяют возможность использования того или иного металла или сплава:
блеск – способность поверхности металла или сплава направленно отражать световой поток;
плотность – масса единицы объема металла или сплава;
температура плавления – температура, при которой металл или сплав целиком переходит в жидкое состояние;
электрические свойства – электрическая проводимость и электрическое сопротивление;
магнитные свойства – магнитная проницаемость, коэрцитивная сила, намагниченность и т.д.
Химические свойства металлов и сплавов определяют их способ-
ность сопротивляться воздействию окружающей среды.
Жаростойкость характеризует способность материала противостоять химической коррозии, развивающейся в атмосфере сухих газов при высоких температурах.
Коррозионная стойкость – это способность металла противостоять электрохимической коррозии, которая развивается при наличии жидкой среды на поверхности металла и ее электрохимической неоднородности.
Технологические свойства металлов и сплавов характеризуют спо-
собность металлов и сплавов обрабатываться различными методами и позволяют определить, насколько экономически эффективно можно изготовить изделие.
Ковкость – способность металла и сплава обрабатываться путем пластического деформирования.
Свариваемость – способность металла и сплава образовывать неразъемное соединение, свойства которого близки к свойствам основного металла (сплава).
Обрабатываемость резанием – поведение металла и сплава под воздействием режущего инструмента.
Жидкотекучесть – способность расплавленного металла и сплава заполнять литейную форму.
Механические свойства характеризуют сопротивление материала деформации, разрушению или особенность его поведения в процессе разрушения.
3
Упругость – свойство материалов восстанавливать первоначальные размеры и объем после снятия нагрузки. Упругость характеризуется пределом пропорциональности и пределом упругости.
Прочность – свойство материалов воспринимать, не разрушаясь, различного рода нагрузки. Прочность характеризуется пределом текучести и пределом прочности (временным сопротивлением).
Пластичность – свойство материала под действием внешних нагрузок изменять, не разрушаясь, свою форму и размеры и сохранять остаточные деформации после снятия этих нагрузок. Пластичность характеризуется относительным удлинением и сужением образца при механических испытаниях.
Вязкость – свойство материалов необратимо поглощать энергию при их пластическом деформировании. Вязкость непосредственно не измеряется, но косвенным показателем ее является ударная вязкость.
Хрупкость – способность твердых тел разрушаться при механических воздействиях без заметной пластической деформации.
Твердость – это свойство металлов и сплавов оказывать сопротивление местной пластической деформации или хрупкому разрушению в поверхностном слое при контактном приложении нагрузки.
Износостойкость – свойство материала оказывать сопротивление изнашиванию в условиях трения.
Выносливость – свойство противостоять усталости. Усталость - процессы постепенного накопления повреждений в материале под действием циклических нагрузок, приводящие к изменению его свойств, образованию трещин, их развитию и разрушению. Критерии выносливости: циклическая прочность (физический или ограниченный предел выносливости) и циклическая долговечность (число циклов, которые выдерживает материал до образования усталостной трещины определенной протяженности или до усталостного разрушения при заданном напряжении).
Жаропрочность – способность материала длительное время сопротивляться деформированию и разрушению, когда рабочие температуры деталей превышают 0,3 tпл. Критериями жаропрочности являются предел ползучести, предел длительной прочности, сопротивление релаксации.
Ползучесть представляет собой медленное нарастание пластической деформации под действием напряжений, меньших предела текучести.
Механические свойства количественно определяют по результатам механических испытаний, при которых материалы подвергают воздействию внешних сил (нагрузок). Механические испытания – определение механических свойств материалов и изделий на образцах в строго регламентированных условиях (скорость, среда, температура, время, схема приложения механической нагрузки и др.).
Классификацию механических испытаний проводят по следующим признакам:
а) способу и времени действия нагрузки (статические, динамические, циклические);
4
б) типу и схеме приложения нагрузки (на растяжение, сжатие, изгиб, кручение);
в) температуре, при которой проводят испытания (при нормальной, пониженной или повышенной температуре).
Методы механических испытаний регламентированы государственными стандартами.
Нагрузка вызывает в твердом теле напряжение и деформацию. Напряжение – величина нагрузки, отнесенная к единице площади по-
перечного сечения испытуемого образца. Различают истинные напряжения и условные. Истинное напряжение определяется делением действующей в определенный момент нагрузки на площадь, которую образец имеет в этот момент. Истинные напряжения в повседневной практике не определяют, а пользуются условными, считая, что поперечное сечение образца остается неизменным, хотя на самом деле в процессе растяжения, например, она уменьшалась.
Деформация – изменение формы и размеров твердого тела под влиянием приложенных внешних сил.
В лабораторных работах данных методических указаний дается описание наиболее распространенных механических испытаний металлических материалов, и приводятся количественные характеристики механических свойств, которые могут быть определены при этих испытаниях.
ЛАБОРАТОРНАЯ РАБОТА № 1
ИСПЫТАНИЯ НА СТАТИЧЕСКОЕ РАСТЯЖЕНИЕ
1.1.Цель работы
Изучение и освоение методики и оборудования для проведения испытаний на статическое растяжение, изучение основных количественных характеристик механических свойств, определяемых при испытаниях на статическое растяжение, и экспериментальное их определение для стальных образцов.
1.2.Оборудование, приборы и материалы
Машина разрывная Р-5, образцы стальные цилиндрические, штангенциркуль, чертилка или кернер.
1.3.Основные термины и определения
Рабочая длина образца l – часть образца с постоянной площадью поперечного сечения между его головками или участками для захвата (рис. 1.1).
5
Начальная расчетная длина образца lo – участок рабочей длины образ-
ца между нанесенными метками до испытания, на которое определяется удлинение (рис. 1.1).
Конечная расчетная длина образца lk – длина расчетной части после разрыва образца.
Начальный диаметр образца do – диаметр рабочей части цилиндрического образца до испытания (рис. 1.1).
Диаметр образца после разрыва dк – минимальный диаметр рабочей части цилиндрического образца после разрыва.
Начальная площадь поперечного сечения образца Fo – площадь попе-
речного сечения рабочей части образца до испытания.
Площадь поперечного сечения образца после разрыва Fк – минимальная площадь поперечного сечения рабочей части образца после разрыва.
Предел пропорциональности пц – напряжение, которое материал образца выдерживает без отклонения от закона Гука.
Предел упругости 0,05 – напряжение, при котором остаточное удлинение достигает 0,05% от первоначальной длины образца.
Предел текучести физический т – наименьшее напряжение, при ко-
тором образец деформируется без увеличения нагрузки.
Предел текучести условный 0,2 – напряжение, при котором пластическая деформация образца достигает 0,2 % от рабочей длины образца l.
Предел прочности (временное сопротивление) в – напряжение, соот-
ветствующее наибольшему усилию Рmax, предшествующему разрыву образца.
Истинное сопротивление разрыву Sи- напряжение, определяемое от-
ношением усилия в момент разрыва к минимальной площади поперечного сечения образца после разрыва Fк.
Относительное удлинение - отношение приращения расчетной длины
образца (lk - lo) после разрушения к начальной расчетной длине lo, выраженное в процентах.
Относительное сужение - отношение разности Fo и минимальной Fк площади поперечного сечения образца после разрушения к начальной пло-
щади поперечного сечения образца Fo, выраженное в процентах.
1.4.Краткие теоретические сведения
Нагрузка на образец при статических испытаниях возрастает медленно и плавно или остается постоянной в течение длительного времени. К статическим испытаниям металлов и сплавов относятся испытания на растяжение, сжатие, изгиб и кручение.
Методы испытаний на растяжение черных и цветных металлов и изделий из них регламентируется ГОСТ 1497-84. Испытание на растяжение является наиболее универсальным по сравнению с другими видами испытаний,
6

так как оно позволяет определять механические свойства материала на всех стадиях его деформации (от упругой деформации до разрушения).
Размеры и типы образцов установлены ГОСТ 1497-84. Испытания на растяжение проводят на образцах с гладкими зажимными головками (плоскими или цилиндрическими) (рис. 1.1), используя клиновые зажимные приспособления. Подготовка образцов к испытанию начинается с их контроля (осмотр внешнего вида, оценка шероховатости их поверхности и измерение размеров). Образцы с механическими повреждениями, заусенцами, неправильной маркировкой, а также с размерами, превышающими допустимые, к испытанию не допускаются.
Rz 80 D
1 |
lo |
r |
D |
o |
1,25 |
|
d |
|
r1 |
l |
h2 h1 |
|
||
|
L |
|
Рис. 1.1. Цилиндрический образец
Испытание образцов осуществляют на серийно выпускаемых испытательных (разрывных) машинах, которые имеют три основных узла: механизм нагружения, механизм силоизмерения и устройство для автоматической записи диаграммы растяжения – диаграммный аппарат.
Установив образец на машине и выбрав зазоры, медленно и плавно нагружают образец до момента его разрыва. Параллельно с этим записывается диаграмма растяжения, показывающая зависимость между нагрузкой, действующей на образец, и вызываемой ею изменением длины образца. На рис. 1.2 показана диаграмма растяжения образца из стали. По оси ординат отло-
жена нагрузка Р, Н, по оси абсцисс – удлинение образца l, мм.
На диаграмме отмечено несколько характерных участков: упругой деформации до точки В; равномерной пластической деформации от В до D и сосредоточенной пластической деформации от D до Е. Прямолинейный уча-
сток сохраняется до точки А или нагрузки Рпц, что соответствует пределу
пропорциональности пц, который определяют по формуле
пц Pпц , МПа, (1.1)
Fo
где Рпц – усилие, превышение которого вызывает появление остаточной деформации;
Fo – начальная площадь поперечного сечения образца.
7

Р, Н
D
Е
С
В
А
max |
E |
Р |
P |
|
|
|
|
|
пц |
|
уп |
|
т |
Р |
|
Р |
|
Р |
|
|
|
||
|
|
|
||
|
|
|
|
|
l, мм
Рис. 1.2. Диаграмма растяжения образца
Тангенс угла наклона прямолинейного участка характеризует модуль упругости первого рода Е.
На небольшом участке от А до В нарушается линейная зависимость между Р и l из-за упругих несовершенств материала, связанных с дефекта-
ми решетки. Точке В соответствует усилие Рупр, при котором остаточная деформация станет равной 0,05 % от начальной расчетной длины образца. Ордината точки В служит для определения предела упругости:
0,05 |
Pупр |
, МПа, |
(1.2) |
|
|||
|
Fo |
|
Предел пропорциональности и предел упругости определяют упругие свойства материала.
Ордината точки С, соответствующей течению материала при пластическом деформировании, служит для определения физического предела теку-
чести т: |
Pт |
|
|
|
т |
, МПа, |
(1.3) |
||
F |
||||
|
o |
|
|
где Рт - усилие при текучести.
Физический предел текучести определяют по диаграмме растяжений, когда на ней имеется горизонтальный участок (площадка текучести). Такой участок характерен только для малоуглеродистых сталей и латуней. Для остальных сплавов определяют условный предел текучести, который равен
напряжению Р0,2, при котором остаточное удлинение образца составляет
0,2 %:
8
0,2 |
P0,2 |
, МПа, |
(1.4) |
|
|||
|
Fo |
|
Выбранная пластическая деформация 0,2 % достаточно точно характе-
ризует переход от упругих деформаций к пластическим, а напряжение 0,2 несложно определить при испытаниях независимо от того, имеется или нет площадка текучести на диаграмме растяжения.
Пластическое деформирование выше точки С идет при возрастающей нагрузке, так как металл в процессе деформирования упрочняется. Упрочне-
ние металла при деформировании называется наклепом. До точки Д удлине-
ние происходит равномерно по всей длине рабочей части рабочей части образца. Цилиндрическая форма образца сохраняется, хотя диаметр его уменьшается по мере удлинения. Ордината точки Д соответствует максимальному
усилию Ртах и служит для определения предела прочности или временно-
го сопротивления:
в |
Pmax , МПа, |
(1.5) |
|
Fo |
|
Наклеп металла увеличивается до момента разрыва образца, хотя рас-
тягивающая нагрузка при этом уменьшается от Ртах до РЕ (см. рис. 1.2). Это объясняется появлением в образце местного утонения – шейки, в которой в основном сосредотачивается пластическая деформация. Несмотря на уменьшение нагрузки, растягивающие напряжения в шейке повышаются до тех пор, пока образец не разорвется. В точке Е определяют истинное сопротив-
ление разрыву Sи – напряжение, определяемое отношением усилия в момент разрыва РЕ к минимальной площади поперечного сечения образца после разрыва Fк:
Sи |
PE |
, МПа. |
(1.6) |
F |
|||
|
к |
|
|
Напряжения 0,05, т и в - стандартные характеристики прочно-
сти.
Пластичность материала характеризуется относительным удлинением и относительным сужением.
Относительное удлинение определяется по формуле:
lк lo 100% |
l |
100%. |
(1.7) |
l |
l |
|
|
o |
o |
|
|
Относительное сужение:
Fo Fк 100%. |
(1.8) |
Fo
На рис. 1.3. представлены типовые диаграммы растяжения различных материалов.
9
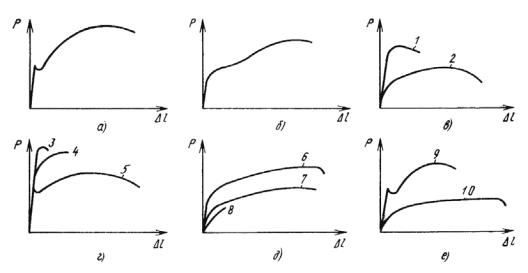
Рис. 1.3. Типовые диаграммы растяжения различных металлов:
а) - углеродистая сталь; б) – аустенитная сталь; в) – медь холоднодеформированная (1) и рекристаллизационная (2); г) – углеродистая закаленная сталь (3), улучшенная (4) и отожженная (5); д) – высокопрочный чугун (6), ферритный ковкий чугун (7), серый чугун (8); е) – высокоуглеродистая сталь (9), алюминий (10)
1.5.Порядок проведения испытаний
1.Ознакомиться с устройством машины для испытаний на растяжение (Р-5) и принципом работы на ней.
2.Получить и подготовить образцы для испытания, замерить диаметр. Вычислить площадь поперечного сечения образца и определить на-
чальную расчетную длину (lo).
3. Произвести испытание образцов.
4. Зафиксировать максимальную нагрузку, достигнутую в процессе испытания.
5. Сложив разорванные части, замерить конечную расчетную длину образца. Рассчитать относительное удлинение.
6. Замерить диаметр образца в месте разрыва. Рассчитать относительное сужение.
7. Рассчитать предел прочности и истинное сопротивление разрыву.
8. Занести все результаты измерений и расчета характеристик в протокол испытаний в виде табл. 1.1.
1.6.Содержание отчета
1.Название, цель работы.
2.Краткие сведения об основных характеристиках прочности и пластичности металлических материалов.
3.Эскиз образца.
10