
Методическое пособие 771
.pdf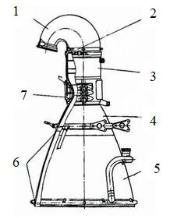
УДК 621.9.04
ТЕХНОЛОГИЯ ФОРМООБРАЗОВАНИЯ БЕСШОВНЫХ ГАЗОВОДОВ
А.К. Севостьянов1, А.А. Витковская2, О.Н. Кириллов3 1,2Магистранты гр. мТМ-11, Alex1235e@yandex.ru, nastya19960505@mail.ru
3Д-р техн. наук, профессор, kirillov.olli@yandex.ru
ФГБОУ ВО «Воронежский государственный технический университет»
В статье рассматриваются основные этапы технологии формообразования газовода на предприятии машиностроительного комплекса.
Ключевые слова: формообразование, газовод, заготовка, вытяжка, матрица, штамп.
Введение
С переходом отечественной космонавтики на эффективные двигатели замкнутой схемы в конструкции камеры сгорания появился газовод, подводящий горячие газы от турбонасосного агрегата (ТНА) к камере.
Газовод – это криволинейный диффузор со спрямляющей смесительной решеткой, который установлен перед блоком форсунок головки камеры сгорания. Он снабжен дополнительной спрямляющей сопловой решеткой в виде блока малоразмерных сопл, установленной за турбиной турбонасосного агрегата. На рис. 1 представлен газовод в составе камеры сгоранияракетного двигателя [1].
Рис. 1. Камера сгорания: 1 – газовод; 2 – форсуночная головка (блок форсунок); 3 – часть средняя; 4 – блок сопла верхний; 5 – блок сопла нижний; 6 – бандажи; 7 – газогенератор
Технология формообразования газовода
Газовод испытывает большие температурные и прочностные нагрузки, а его местоположение и конструкция затрудняют охлаждение. Высокая температура, значительные габариты и давление выдвигают на первый план
310
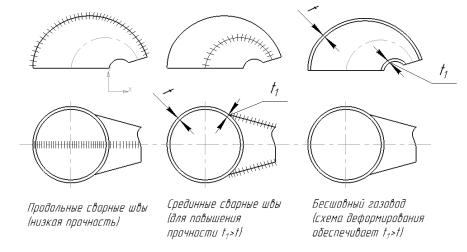
проблему достижения высокой прочности. Изготовление газовода традиционными методами (штамповка) не достигают требуемого результата. У малого радиуса данного изделия происходили разрушения. Вставка более утолщенного материала значительно усложняла технологию получения. Объем ручных работ по разделению, стыковке и подварке дефектов превзошел допускаемые пределы. Разделение газовода по среднему сечению с изготовлением обеих частей из материала разной толщины и автоматизацией изготовления сварного шва, решило вопрос прочности, но сделало конструкцию в несколько раз более тяжелой.
На ведущем предприятии была разработана,не имеющая аналогов, технология изготовления бесшовного газовода. Главным секретом данной технологии стала схема деформирования, которая утолщала стенку в самом напряженном месте. На рис. 2 показана схема эволюции создания газовода.
Рис. 2. Эволюция технологии газоводов (слева-направо): с боковыми сварными швами; со сварными швами и вставкой; бесшовный
Этапы создания и формообразования газовода
Изготовление газовода в АО КБХА базируется на технологии ведущего предприятия и подразделяется на несколько этапов:
1)Из заготовительного цеха деталь перемещают в штамповочный цех, где контролируют заготовку на марку материала, а также отсутствие глубоких трещин, забоин, раковин и так далее. Заготовкой для будущего изделия служит лист из нержавеющей стали, диаметром 970 мм, который показан на рис. 3;
2)После того, как заготовка была проверена на отсутствие дефектов, приступают к процессу вытяжки. Для этого проводят операцию настройки: устанавливают штамп на стол пресса, закрепляют и настраивают штамп, устанавливают пуансон в матрицу и верхние прижимы, протирают поверхности рабочих частей штампа, а после устанавливают деталь в матрицу. Далее происходит процесс вытяжки детали. Вытяжка происходит на гидравлическом листоштамповочномпрессе.
311
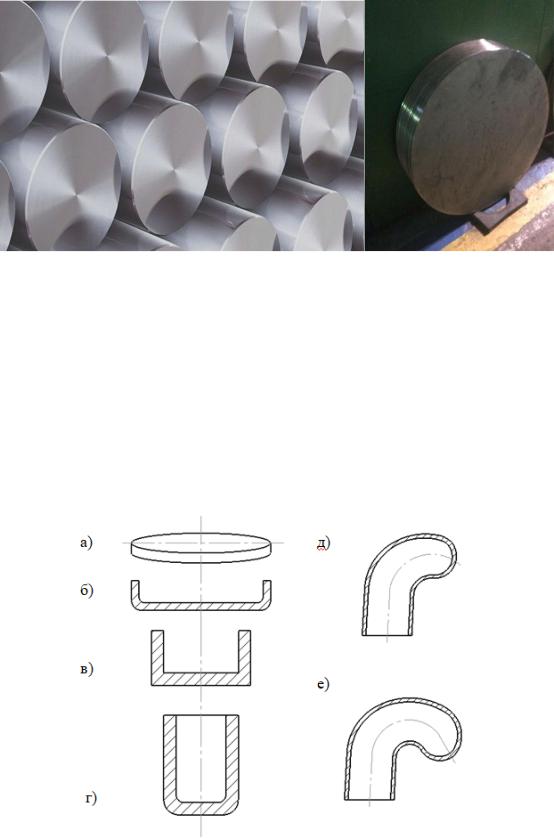
Рис.3. Заготовки для газоводов
Пресс применяется для выполнения операций по вытяжке, горячей и холодной формовке при изготовлении изделий типа днищ, сосудов, резервуаров, котлов и других подобных изделий[2]. Усилие вытяжки для газовода составляет 180 т.с.;
3) После вытяжки деталь промывают, обрабатывают на токарном и фрезерном станках, маркируют, термообрабатывают в печи и формуют. Так повторяют до тех пор, пока заготовка не примет нужную конфигурацию формы. На рис. 4 представлена схема формообразования газовода.
Рис. 4. Формообразование газовода: а) заготовка; б), в), г), д) 1-4 этапы вытяжки; е) полученная заготовка
312
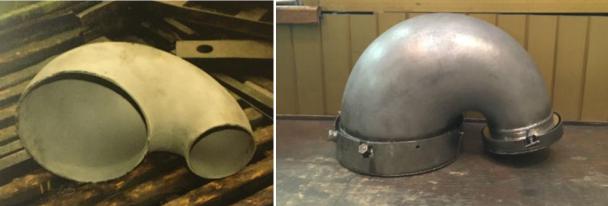
4)Как только деталь приняла нужную форму, ее обрабатывают на токарных и фрезерных станках, зачищают заусенцы и острые кромки, обдувают поверхности газовода мокрым песком, чтобы удалить окалину, подвергают пассивации, проводят каппилярный и рентген контроли, наносят покрытие и сушат ее на воздухе.
5)После того, как деталь проконтролируют, ее доставляют в механосборочный цех, вместе с блоком форсунок, фланцем, наконечниками и штуцерами, изготовленными в других механосборочных цехах.
6)Далее газовод комплектуют с вышеперечисленными изделиями, проводят токарные, сварочные, фрезерные, испытательные и другие операции,
ив конечном итоге устанавливают на камеру сгорания.
Окончательный вариант газовода после формообразования и механообработки, а также полностью скомплектованный газовод с другими сборочными единицами представлены на рис. 5.
Рис. 5. Бесшовный газовод и скомплектованный газовод с блоком форсунок, фланцем, наконечниками и штуцерами
Таким образом, применение данной технологииформообразования, позволяет решить задачу получения бесшовного газовода, что позволяет получать изделия с заданными техническими характеристиками иускорить производственный процесс изготовления ракетного двигателя.
Литература
1.Режим доступа: http://allpatents.ru/patent/2186236.html
2.Режим доступа: https://stanok-kpo.ru/spravochnik/kpo-sovetskoe- rossiyskoe-importnoe-spravochnaya-informatsiya/p4644.html
313
УДК 621.791.722
УНИКАЛЬНОЕ СВАРОЧНОЕ ОБОРУДОВАНИЕ, ПРИМЕНЯЕМОЕ В МАШИНОСТРОЕНИИ
А.К. Севостьянов1, А.А. Витковская2, О.Н. Кириллов3 1,2Магистранты гр. мТМ-11, Alex1235e@yandex.ru, nastya19960505@mail.ru
3Д-р техн. наук, профессор, kirillov.olli@yandex.ru
ФГБОУ ВО «Воронежский государственный технический университет»
Встатье рассматриваются использование электронно-лучевой сварки на примере установки СУЭЛС, а также ее применение в АО КБХА.
Ключевые слова: сварка,АО КБХА,электронно-лучевая сварка, ЭЛС, СУЭЛС, луч.
Внастоящее время в машиностроении наиболее широкое применение
получили конструкционные материалы на основе металлов, которые имеют высокую температуру плавления, а также высокоактивных металлов (вольфрам, молибден и другие). Это потребовало создание способа их обработки с помощью источника тепла с высокой плотностью энергии и защиты от внешних воздействий с помощью вакуума. Таким условиям соответствует электронно-лучевая обработка.
Электронно-лучевая сварка (ЭЛС) – вид сварки, базирующийся на применении электронного луча, сформированного с помощью электронной пушки.
С помощью такой технологии обрабатывают металлы, диэлектрики, органические соединения, композиты. Можно выполнять операции на образцах в несколько микрон. При использовании ЭЛС в крупных металлоконструкциях шов получается наиболее качественным, с глубоким проплавом.
ЭЛС допускается использовать для получения высококачественных швов, для металлических конструкций, с глубоким проплавом металла. [1].
Данная технология отличается чистотой процесса, возможностью ее автоматизации и воздействует на материал путем использования электронных и ионных лучей и с помощью плазменной дуги. Чистота процесса заключается в том, что проходит он в вакуумной камере при глубоком вакууме [2].
В КБХА, в качестве такого оборудования применяется установка электронно-лучевойсварки (СУЭЛС). Она представлена на рис. 1.
Принцип действия установки СУЭЛС.
Установка состоит из герметического корпуса, электронной пушки, электронопроводов, вытягивающей и ускоряющей систем, системы фокусировки луча (магнитные линзы), предметного столика, манипулятора, вакуумной камеры (P=10-5Па), вакуумных насосов, генераторов и прочих элементов [2].
314
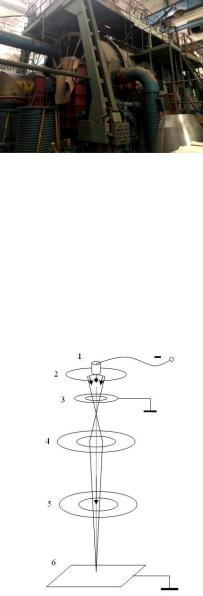
Рис. 1. СУЭЛС
Сущность процесса заключается в следующем: от горячего источника электронов – катода, электронный луч через ускоряющие, фокусирующие и управляющие системы попадает на поверхность обрабатываемой детали. Попадая на него электроны, расплавляют материал либо разрушают его. Это зависит от плотности тока в луче, температуры и ускоряющего движения. Главным элементом СУЭЛС является электронная пушка, которая показана на рис. 2.
Рис. 2. Электронная пушка. 1 — катод, 2 — электрод, 3 — анод, 4 — электромагнитная линза, 5 — отклоняющая катушка, 6 — свариваемое изделие
Она состоит из катода 1, анода 3, герметического корпуса, электрода 2, системы фокусировки луча (магнитной линзы) 4, отклоняющей катушки 5. При подключении электрического тока и нагреве катода, между ним и анодом возникает электронный поток, для регулирования потока электронов при одной и той же силе тока предназначен управляющий электрод 2 [2].
После электронной пушки, все процессы формирования луча происходят в электронопроводе. Электродный пучок попадает туда под воздействием ускоряющего электрического потенциала вытягивающей системы. Далее поток электронов поступает в ускоряющую систему, где поля ускоряющего потенциала (3х ступенчатые) разгоняют электроны до заданной энергии ускорения. На рис. 3 (а, б, в) показаны основные процессы получения луча [2].
315
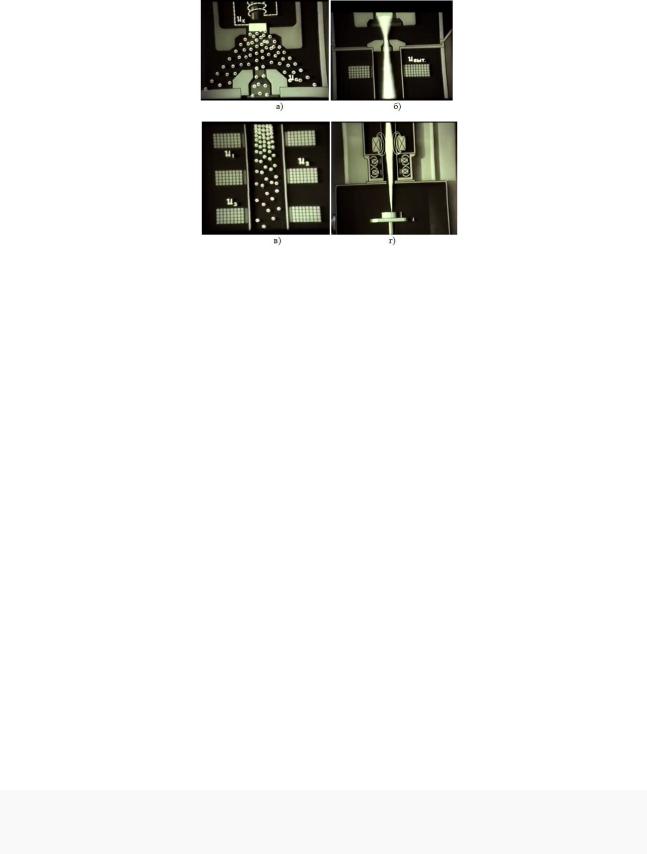
Для того чтобы сфокусировать ускоренный пучок энергии используется система фокусировки луча, представляющее магнитное поле. Оно создается кольцевыми электромагнитами. Это показано на рис. 3 (г) [2].
Рис. 3. Формирование луча: а) электронная пушка, с возникающим электронным потоком. Uк – катод, Uа – анод; б) электронопровод с вытягивающей системой (Uвыт.); в) ускоряющая система из трех ступеней (U1, U2; U3); г) система фокусировки луча
Для перемещения луча в пространстве существует три способа: электромагнитный (отклоняющееся электромагнитное поле перемещает электронный луч в пространстве) и механический (при неподвижном луче перемещают предметный столик) и при помощи манипулятора [2].
Откачивающая система в СУЭЛС состоит из насосов предварительной откачки и насосов глубокого вакуума [2].
На данной установке выполняется не только обычная сварка изделий, но также возможен прожиг отверстий, кольцевая сварка, круговая рельефная сварка и прямолинейная сварка. Также возможна электронно-лучевая плавка электронными лучами.
ЭЛС имеет следующие преимущества:
-сваривание за один проход металлов, толщиной от 0,2 до 150 мм;
-используется в 10 раз меньше энергии, чем для дуговой сварки
-металл, который подвергся плавлению, не насыщается газами.
Таким образом, применение электронно-лучевой установки СУЭЛС позволит достичь высокого качества и точности при изготовлении перспективных изделий машиностроения.
Литература
1.РД 24.949.04-90. Сварка электронно-лучевая изделий тяжелого машиностроения. Тех. тр. НПО ЦНИИТМАШ, Мин. тяж. маш. СССР, М.: 1990. 16 с.
2.Электронно-лучевые сварочные установки (ЭЛО. Р. 1). Гос. ком. СССР
по народн. образ. Киевнаучфильм. Украина, 1990 г. / Видеофильм. Режим доступа: https://www.youtube.com/watch?v=XxEEgHaMW8g
316
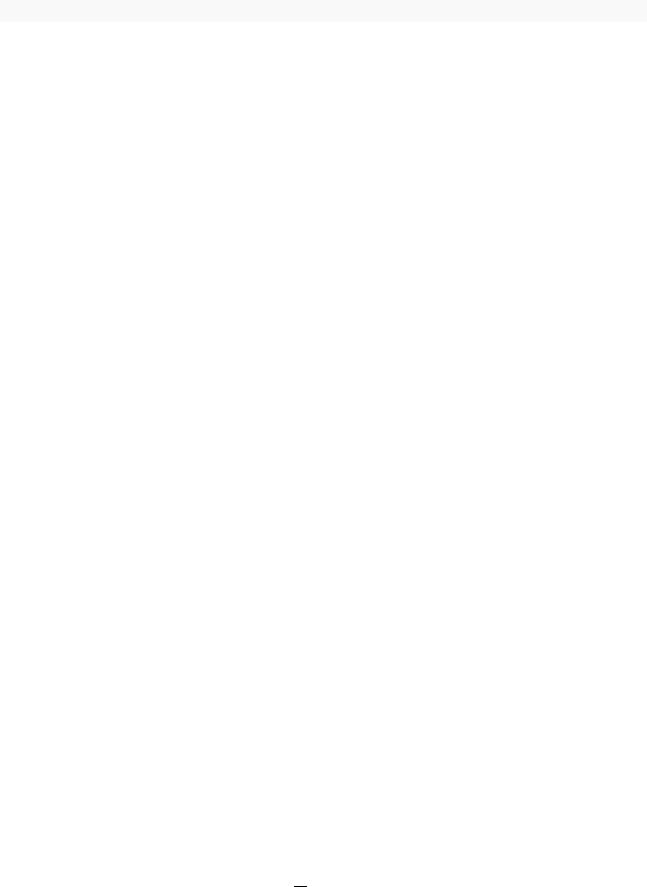
УДК 519.7
ФОРМИРОВАНИЕ ТЕСТОВ КОНТРОЛЯ КОНЕЧНЫХ АВТОМАТОВ НА ОСНОВЕ МЕТОДА ИДЕАЛЬНОЙ ТОЧКИ
И.А. Никифоров1, Г.В. Петрухнова2 1Студент гр. иВМ-161, ivan_nik89@mail.ru
2Канд. техн. наук, доцент, gvpetruhnova@mail.ru
ФГБОУ ВО «Воронежский государственный технический университет»
Рассматривается подход к тестированию конечного автомата посредством псевдослучайных контролирующих тестов. Для нахождения близкого к оптимальному набора входных параметров для построения псевдослучайного теста используется метод нахождения максимума входной энтропии.
Ключевые слова: дискретное устройство, конечный автомат, контролирующий тест, длина псевдослучайного теста, максимум энтропии.
Для проверки корректности работы дискретных устройств строятся различные диагностические и контролирующие тесты. Рассмотрим построение контролирующих тестов, которые предполагают подачу последовательности воздействий на входы устройства, последующий анализ выходных реакций и вывод о исправности проверяемого устройства.
Синтез теста на основе псевдослучайных последовательностей дает возможность не изучать детально структуру устройства и рассмотреть конечный автомат (КА). Для сокращения длины псевдослучайного теста будем максимизировать выходную энтропию КА [1].
Первичные входы КА являются независимыми и имеют различные вероятности поступления логической единицы. В результате формируется вектор весов ( ) и выходная последовательность ( ) , где i = 1,N; N – длина теста. Реакцию КА на тест смоделируем бинарной матрицей:
Y=( |
) |
где yij – значение, зафиксированное в j-той контролируемой точкой после подачи i-того входного набора; ( ) – реакция КА (выходной набор) на i-тое тестовое воздействие.
Пусть качество теста контроля определяется энтропийными критериями:
∑( )
317
|
|
|
∑( |
) |
|
|
∑(( |
) ( |
) |
|
|
|
|
||||||
где pk – |
частота k-того выходного |
набора ( |
|
) ; qi – частота |
|||||
появления |
единичного сигнала |
в |
|
реакции КА (в выходном наборе |
|||||
( |
)) на входной набор; K – |
|
число контрольных точек; R = 2K [1]. |
Одним из способов оптимизации является использование метода Парето, который предполагает нахождение идеальной точки, в которой каждая из целевых функций достигает оптимального значения.
Максимальное значения критерия Н1 |
соответствует начальным условиям |
||||
pi=1/R, i=1,…,R. Максимальное значения критерия Н2 |
соответствует начальным |
||||
условиям qi=0.5, i=1,…,К. Вычислим |
|
|
|
|
|
|
|
|
x |
|
|
и определим значение целевой функции как |
|
|
|
||
|
|
|
|
|
|
√ |
( |
) |
( |
) |
|
где 1 и 2 – весовые коэффициенты, которые выбираются путем исследований. Решение многокритериальной задачи было сведено к решению однокритериальной. Для нахождения экстремума целевой функции использовался метод покоординатного спуска [2]. При исследованиях вводились одиночные ошибки в логику работы КА, запоминалась длина теста контроля, когда на каждый вход подавалась логическая единица с вероятностью 0,5. После чего вес каждого из входов переопределялся в результате решения задачи оптимизации. По окончании исследований анализировалась и запоминалась длина теста. Анализ экспериментальных данных, говорит о достаточно высокой эффективности предложенного алгоритма оптимизации. Алгоритм для синтеза тестов контроля также позволяет решать задачи контроля
уязвимости в моделируемом объекте.
Литература
1.Petrukhnova G.. The analysis of binary matrix symmetry properties in the tasks concerned with test control of digital devices/ G.. Petrukhnova // Journal of
Physics: Conference Series, 2019. С. 012051.
2.Васильев Ф.П. Численные методы решения экспериментальных задач / Ф.П. Васильев // М.: Наука, 1980. С. 552.
318
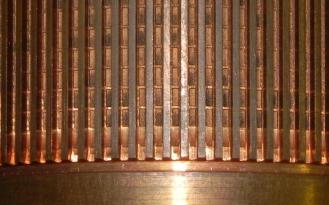
УДК 621.234.123
ЭКСПЕРИМЕНТАЛЬНОЕ ИССЛЕДОВАНИЕ КОМБИНИРОВАННЫХ ФИЗИКО-ТЕХНИЧЕСКИХ МЕТОДОВ УПРОЧНЕНИЯ МЕЖЛОПАТОЧНЫХ КАНАЛОВ ПЕРЕМЕННОГО СЕЧЕНИЯ
Г.А. Сухочев1, А.М. Некрылов2, Д.В. Силаев3 1Д-р техн. наук, профессор, suhotchev@mail.ru 2Аспирант кафедры ТМ, anekrylov@mail.ru
3Аспирант кафедры ТМ, luckymessages@yandex.ru
ФГБОУ ВО «Воронежский государственный технический университет»
Предложены пути снижения нежелательного наклепа, а также способ для упрочнения профильных поверхностей каналов деталей роторной группы, объединяющий процессы вибрационной и экструзионной обработки. Показан анализ эффективности предлагаемых решений.
Ключевые слова: комбинированная виброэкструзионная обработка, вибромашина, межлопаточные каналы, гранулированная рабочая среда, упрочнение обрабатываемых поверхностей.
Необходимость использования тех или иных операций с применением комбинированных процессов в общей технологии в процессе создания высокотехнологичной продукции определяется в зависимости от поставленной цели, а один и тот же способ обработки может использоваться для различных задач формообразования.
Например, размерная электрохимическая обработка, используемая для снятия заусенцев в труднодоступных местах, формирования искусственной шероховатости и дифференциального устранения разнотолщинности материала охлаждаемых оболочек (рис. 1), может применяться (после соответствующей адаптации) и для выравнивания микрогеометрии узкого межлопаточного канала переменного сечения роторных деталей, а также составных единиц турбонасосного агрегата.
Рис. 1. Фрагмент оребренной оболочки
319