
Методическое пособие 631
.pdf
температуру и в силу этого, в п ротивоположность остальной части газового потока, является неэлектропроводимым. Он образует противоэлектрический и противотермический изолирующий слой между стенками сопла и потоком плазмы. С увеличением расстояния от центра токопроводящего канала температура понижается.
Сжатая дуга косвенного действия может иметь различную длину. Внутри сопла она сжата, однако при выходе за его пределы начинает постепенно расширяться до размеров, равных свободной дуге. При этом расширение происходит тем быстрее, чем сильнее сжат разряд и чем меньше расход газа. На расстоянии 25 - 30 мм от нижнего среза сопла сжатая дуга расширяется до свободных размеров. В большинстве случаев плазменную наплавку выполняют на постоянном токе прямой, значительно реже обратной полярности.
Разработанные способы плазменной наплавки с присадочной или электродной проволокой (рис. 2.11) позволяют обеспечивать минимальное проплавление основного металла (доля основного металла в первом наплавленном слое состав-
ляет 0,5 - 2,5 %).
Рис. 2.11. Схема плазменной наплавки с использованием
электродной (а) или присадочной (б) проволоки: 1– защитное сопло; 2 – плазмообразующее сопло; 3 – защитный газ;
4 - плазмообразующий газ; 5– электрод; 6 – источник питания;
7 – проволока; 8 – наплавляемое изделие
61
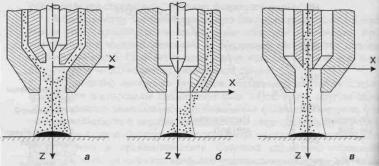
Из существующих способов плазменной наплавки наибольшее распространение в промышленности получила плаз- менно-порошковая наплавка, которая является наиболее универсальным среди других способов плазменной наплавки. Благодаря малому проплавлению основного металла требуемую твердость и заданный химический состав наплавленного металла обеспечивают уже на расстоянии 0,3 - 0,5 мм от поверхности сплавления, что позволяет ограничиться однослойной наплавкой там, где электродуговым способом необходимо наплавить 3 - 4 слоя.
При плазменно-порошковой наплавке присадкой служат гранулированные металлические порошки, которые подаются в плазмотрон транспортирующим газом с помощью специального питателя. Для наплавочных плазмотронов разработано три схемы ввода порошка в дугу (рис. 2.12):
-распределенный через кольцевую щель между соплами;
-локальный боковой через канал (каналы) в торце сопла;
-аксиальный через полый электрод.
Рис. 2.12. Схемы подвода порошка в дугу при плазменно-
порошковой наплавке: а – распределенный через кольцевую щель между соплами; б – локальный боковой через канал в торце сопла; в – аксиальный через полый электрод
В промышленных установках применяют два первых способа, последний, несмотря на преимущества с точки зрения использования порошка, не нашел практического применения
62
из-за малой надежности и низкой стойкости электрода, через отверстие в котором подается присадочный порошок.
2.3.3. Материалы для плазменной наплавки
Для плазменной наплавки применяют порошки сплавов на основе никеля, кобальта, железа и меди. Производят порошки преимущественно методом распыления струи жидкого металла инертным газом, что обеспечивает им отличные свароч- но-технологические свойства - хорошую сыпучесть, низкое содержание кислорода (0,02 - 0,10 %) и др. В небольших масштабах (для производства порошков тугоплавких материалов) используют термоцентробежное распыление. Порошок является универсальным наплавочным материалом, так как может быть получен практически из любого наплавочного сплава, независимо от прочности, твердости и других его свойств.
Следует отметить, что многие составы порошков, разработанных и рекомендованных для газопорошковой наплавки и плазменного напыления, можно успешно использовать и для плазменной наплавки.
Сплавы на основе никеля. Для плазменно-порошковой наплавки применяют никелевые сплавы системы легирования Ni- Сг-Si-В. Содержание хрома в этих сплавах может колебаться в пределах 1 – 29 %. Важными легирующими элементами являются бор и кремний, содержание которых обычно составляет 1
– 4 %. Присадки бора и кремния снижают температуру плавления хромоникелевых сплавов и обеспечивают способность к самофлюсованию. Одновременно эти элементы повышают твердость и износостойкость наплавленного металла. Углерод и железо содержатся в никелевых сплавах в небольших количествах (до 1 % углерода и до 4,5 % железа). Некоторые из сплавов содержат также в небольших количествах вольфрам, молибден, марганец, медь и другие легирующие элементы.
Из большого количества разработанных в настоящее время никелевых сплавов наибольшее распространение для
63

плазменной наплавки получили порошки самофлюсующихся Ni-Сг-Si-В-С-сплавов (табл. 2.9), известных под названием «Колмонои».
Таблица 2.9
Химический состав некоторых порошков сплавов на основе никеля и твердость наплавленного ими слоя
Марка |
|
Содержание элементов, % |
|
НRCэ |
|||
порошка |
С |
Сr |
Si |
Fе |
В |
||
|
|||||||
ПГ-СР2 |
0,3 |
13,5 |
2,5 |
<5 |
1,8 |
35-42 |
|
ПГ-СР3 |
0,5 |
15 |
3 |
<5 |
2,4 |
45-52 |
|
ПГ-СР4 |
0,8 |
16,5 |
3,7 |
<5 |
3,3 |
55-60 |
|
ПР-Н70Х17С4Р4 |
0,9 |
17 |
4 |
<5 |
3,5 |
55-60 |
Металл, наплавленный самофлюсующими никелевыми сплавами, обладает хорошей износостойкостью при комнатной и повышенных температурах, особенно в условиях трения металла по металлу, жаропрочностью и жаростойкостью. Он также стоек против коррозии в растворах некоторых кислот (уксусной, муравьиной, лимонной и т.п.), в каустической соде
идругих агрессивных средах.
Сувеличением содержания углерода, бора и кремния твердость наплавленного металла повышается, а его структура
изменяется от доэвтектической, состоящей из α -твердого раствора на основе никеля и сложной эвтектики, к заэвтектической, в которой наряду с этими структурными составляющими есть также бориды хрома, сложные карбиды и карбобориды.
Наплавленный металл с доэвтектической и эвтектической структурами предпочтительнее для работы в парах трения и при значительных ударных нагрузках, с заэвтектической структурой - при абразивном изнашивании.
Сплавы на основе кобальта (стеллиты) предназначены для наплавки деталей арматуры, клапанов и седел ДВС, инструмента для деформирования металла и др. Наплавленный металл отличает высокая износостойкость при нормальной и повышенной температурах, жаропрочность, жаростойкость, коррозионная стойкость во многих агрессивных средах.
64

В настоящее время известно более 60 марок стеллитов, однако для плазменно-порошковой наплавки наибольшее применение получили только некоторые из них (табл. 2.10).
Таблица 2.10
Химический состав некоторых порошков сплавов на основе кобальта и твердость наплавленного ими слоя
Марка порошка |
|
Содержание элементов, % |
НRCэ |
||||
С |
Сr |
Si |
Fе |
Прочие |
|||
|
|
||||||
ПР- |
1,2 |
30 |
2,2 |
<3 |
<3,0 Ni, 4,5 W |
38-44 |
|
К60Х30ВС(В3К) |
|||||||
ПР-К58Х30В5С |
1,5 |
30 |
1,7 |
<3 |
2,0 Ni, 4,5 W |
42-47 |
|
ПН-АН34 |
0,8 |
30 |
1,7 |
<3 |
6,0 Ni, 4,5 W, |
42-47 |
|
0,8 В |
|||||||
|
|
|
|
|
|
||
ПР- |
1,5 |
25 |
1 |
<3 |
20 Ni, 12 W |
42-45 |
|
К40Х25Н20В12 |
Хром придает сплавам жаростойкость, повышает твердость, прочность и жаропрочность, при его содержании более 34 % образуются кобальтохромовые интерметаллиды, приводящие к охрупчиванию сплавов. Повышению жаропрочности способствует также вольфрам. Его содержание колеблется в широких пределах (4 - 23 %) и зависит от назначения сплава.
Содержание углерода обычно не превышает 2,5 %. В стеллиты также вводят небольшие присадки (0,5 - 2,0 %) бора, ниобия и других элементов. Например, присадка бора придает наплавленному металлу повышенную твердость и износостойкость, а также стойкость против образования кристаллизационных трещин, но снижает коррозионную стойкость в растворах некоторых кислот. Жаростойкость наплавленного металла при легировании его бором практически не изменяется.
Структура наплавленного металла, который обычно содержит около 30 % хрома, зависит, главным образом, от содержания углерода и вольфрама. Применяемые для наплавки стеллиты являются доэвтектическими сплавами, структура которых состоит из твердого раствора и двойной эвтектики, с о- стоящей из карбидов Сг23С6 и твердого раствора, обогащенного кобальтом.
65

Стали и сплавы на основе железа (табл. 2.11). Порошки ПГ-С1 и ПГ -АН1 - это высокоуглеродистые и высокохромистые сплавы с карбидным или карбоборидным упрочнением. Эти сплавы весьма стойки в условиях интенсивного абразивного изнашивания, однако склонны к образованию трещин при наплавке. Они предназначены для наплавки рабочих органов почвообрабатывающих машин и землеройной техники, дисков и седел арматуры для пульпопроводов, деталей металлургического оборудования и т.п.
Таблица 2.11
Химический состав некоторых порошков сталей и сплавов на основе железа и твердость наплавленного ими слоя
Марка |
|
Содержание элементов, % |
НRCэ |
||||
порошка |
С |
Сr |
Si |
Мn |
Прочие |
||
|
|||||||
ПГ-С1 |
3 |
29 |
3,5 |
1,2 |
4 Ni |
50-55 |
|
ПГ-АН1 |
2,4 |
29 |
2 |
1 |
1,4 В |
54-58 |
|
ПГ-АН2 |
2,2 |
18 |
0,5 |
0,8 |
8 V, 3 Мо, 1,4 |
44-52 |
|
|
|
|
|
|
Ni |
|
|
ПР-10Р6М5 |
1 |
4 |
0,5 |
0,5 |
1,9 V, 5 Мо, |
58-64 |
|
6,5 W |
|||||||
|
|
|
|
|
|
||
ПР- |
2,1 |
5,9 |
1,4 |
0,8 |
7,8 V, 0,4 Мо, |
54-60 |
|
220Х6Ф8ВМС |
|
|
|
|
1 W |
|
Металл, наплавленный порошком ПН-АН2, по износостойкости не уступает металлу, наплавленному порошком ПГС1, но он более пластичен и не склонен к образованию трещин, что обусловлено особенностями его структуры, состоящей из аустенитно-мартенситной основы, карбидной эвтектики, расположенной по границам зерен, но не образующей замкнутого скелета, и мелких, равномерно распределенных первичных карбидов. Его коррозионная стойкость выше, чем у хромистых сталей типа 20Х13. Порошок ПН-АН2 применяют для наплавки шнеков экструдеров и термопластов, деталей арматуры для систем гидротранспорта сыпучих материалов, рабочих органов почвообрабатывающих машин и т.п.
Порошки 4, 5 (табл. 2.11) предназначены для наплавки заготовок режущего инструмента, штампов, технологической
66

оснастки.
Сплавы на основе меди (табл. 2.12) служат для наплавки деталей пар трения, а также для восстановления деталей судовой арматуры из цветных сплавов. Наплавку порошками медных сплавов выполняют на обратной полярности, что особенно важно при наличии в их составе алюминия.
Таблица 2.12
Химический состав некоторых порошков сплавов на основе меди
Марка |
|
|
Содержание элементов, % |
|||
порошка |
Si |
Мn |
Fе |
Ni |
Прочие |
|
ПР-БрКМц 3-1 |
3 |
1,3 |
- |
- |
- |
|
ПР-БрОН 8,5-3 |
0,2 |
- |
- |
3 |
8,5 Sn |
|
ПР-БрАЖНМц |
<0,2 |
1,4 |
4 |
4,8 |
8,5 Аl |
|
8,5-4-5-1,5 |
||||||
|
|
|
|
|
||
ПР-МН40 |
- |
1,1 |
1,5 |
41 |
8,5 Аl, 0,3 Тi |
При плазменной наплавке бронз ПР-БрКМц3-1, ПР- БрАЖНМц8,5-4-5-1,5 и ПР-БрАЖНМц8,5-1,5-5-1,5 на стальные детали практически не наблюдается так называемое проникновение медного сплава в основной металл.
При наплавке оловянных бронз с целью исключения таких проникновении необходимо наплавлять промежуточный слой из упомянутых выше бронз.
2.4. Индукционная наплавка
Сущность индукционной наплавки заключается в том, что наплавляемую деталь помещают в электромагнитное поле индуктора, который питается переменным током высокой частоты (ТВЧ); в массе металла детали или компактной присадки индуктируются вторичные переменные токи той же частоты, распределяющиеся в поверхностном слое металла и нагревающие этот слой. На рис. 2.13 показаны приблизительные картины магнитных полей двух проводников, с прямоугольным сечением, для случая одинаково направленных (рис. 2.13, а, разность фаз равна нулю) и встречно направленных (рис. 2.13, б, разность фаз равна 180°) токов. Из рисунка видно, что наи-
67

большая напряженность поля в системе с однонаправленными токами наблюдается у внешних поверхностей проводников, а в системе с противоположно направленными токами у внутренних поверхностей. Очевидно, что главная часть электромагнитной энергии, поглощаемой проводником, поступает в него из зоны сильного поля, в связи с чем, там будет расположена и зона с наибольшей плотностью тока (рис. 2.13 - глубина зачерненного слоя пропорциональна плотности тока). Распределение тока по глубине подчиняется закономерностям поверхностного эффекта и состоит в концентрации тока в определенных зонах поверхности проводников в результате суммарного взаимодействия электромагнитных полей всех проводников с током, входящим в рассматриваемую систему.
Рис. 2.13. Схема магнитного поля и распределения тока при эффекте близости: а - одинаково направленные токи, б - встречно направленные токи
Используя данное явление, можно подбором соответствующей формы индуктора концентрировать нагрев в определенных частях поверхности обрабатываемой детали. Например, если индуктор представляет собой кольцо; охватывающее нагреваемую деталь, то в детали индуктируется ток, путь которого имеет также кольцевую форму. Ток концентрируется в полосе, по ширине мало отличающейся от ширины индуктора.
68
Эффект близости проявляется тем сильнее, чем меньше расстояние между проводниками и чем сильнее проявляется поверхностный эффект, т.е. чем больше отношение толщины проводника к глубине проникновения тока.
Чем выше частота тока, тем меньше нагреваемый слой металла. Для стальных деталей преимущественный нагрев ТВЧ поверхностных слоев металла сохраняется вплоть до точки Кюри (температуре, при которой магнитная проницаемость металла остается практически неизменной - 768 °С). После того как металл нагреется выше точки Кюри, глубина проникновения индуктированных токов увеличивается в 10 - 20 раз (в зависимости от частоты), благодаря чему распределение температуры в нагреваемом металле становится более равномерным. Металл детали или компактной присадки нагревается до плавления и соединяется между собой. Для предохранения от окисления улучшения сплавления основного и наплавленного металлов применяют флюсы.
Следует заметить, что в наиболее распространенных способах индукционной наплавки в качестве присадочного материала применяют не компактные материалы, а шихту, состоящую из металлических порошков и флюсовых добавок. Металлические гранулы изолированы друг от друга частицами флюса, вследствие чего электропроводность порошкового слоя и выделение в нем энергии малы. По этой причине нагрев и расплавление порошковой шихты идет в основном за счет теплопередачи от нагреваемого ТВЧ основного металла.
2.4.1. Технология индукционной наплавки
Индукционный нагрев ТВЧ в настоящее время применяют в следующих основных вариантах наплавки:
-армирование расплавленного поверхностного слоя основного металла тугоплавкой и труднорастворимой присадкой;
-заливка жидкого присадочного металла на подогретый основной металл;
69
-расплавление брикетированного или монолитного материала на основном металле;
-погружение подогретой детали в форму-тигель с расплавленным сплавом;
-центробежная наплавка деталей цилиндрической формы;
-расплавление порошковой шихты, нанесенной на наплав-
ляемую поверхность детали.
Армирование поверхности основного металла тугоплавкой и труднорастворимой присадкой. При использовании это-
го способа в качестве присадки применяют зерновой релит (карбид вольфрама) или крупку измельченных металлокерамических сплавов. Присадку вместе с флюсом (борная кислота) наносят на наплавляемую поверхность детали. Затем деталь вводят в индуктор, в котором поверхностный слои разогревается до температуры плавления и оплавляется. Зерна присадочного материала при этом не расплавляются и погружаются
воплавленный поверхностный слой. Закрепление зерен релита
вматрице происходит за счет их частичного растворения и
смачивания расплавом.
Армированный поверхностный слой представляет собой литую стальную матрицу с вплавленными в нее зернами тугоплавкого компонента. Как показывают исследования, тугоплавкие частицы практически не изменяют при таком способе наплавки свою структуру и твердость.
Как и большинство других способов индукционной наплавки, этот способ отличается простотой и обеспечивает высокие эксплуатационные свойства наплавленных деталей. Он нашел применение для упрочнения шарошек буровых долот.
Заливка жидкого присадочного металла на подогретый основной металл. Наплавляемую поверхность детали 1 (рис. 2.14) покрывают слоем флюса и помещают в индуктор 2, поверхность которого защищена огнеупорным составом 3. После нагрева детали до нужной температуры включают напряжение и снизу к индуктору подводят медное водоохлаждаемое кольцо
70