
Методическое пособие 200
.pdf7)прочитать число твердости по соответствующей шкале индикатора;
8)оформить результаты измерения твердости в виде
табл. 2.
|
|
|
|
|
|
|
Таблица 2 |
|
|
Результаты измерения твердости |
|
|
|
||||
|
|
|
|
|
|
|
|
|
Материал |
Вид |
Нагрузка, |
Шкала |
Твердость HR |
||||
образца |
индентора |
|
кг |
измерений |
|
|
|
|
|
|
Р0 |
Р1 |
Р |
|
1 |
2 |
средняя |
|
|
|
|
|
|
|
|
|
Испытание на растяжение. Испытания проводятся на разрывной испытательной машине. Для испытания на растяжение применяют цилиндрические или плоские образцы. На рабочей части образцов не должно быть следов механической обработки, забоин и других дефектов; образцы должны быть без кривизны и закалочных трещин. Перед испытанием измеряют поперечное сечение образцов. Точность измерения – до 0,01 мм. Измеряют не менее, чем в трех местах по длине рабочей части образца (в середине и по краям). Затем проводят испытание на растяжение.
Полученные данные заносят в табл. 3, по ним вычисляют площадь поперечного сечения образца F0.
Относительное удлинение δ и относительное сужение Ψ рассчитываются по формуле:
|
lk |
l0 |
100% и |
|
F0 Fk |
100% |
(9) |
|
|
|
|||||
|
|
l0 |
|
F0 |
|
Индекс k означает конечные, после испытаний, значения соответствующих величин.
Основой для расчетов силовых параметров при испытаниях на растяжение является первичная (машинная) кривая в координатах «усилие-удлинение» (рис.5). По вертикальной оси
19
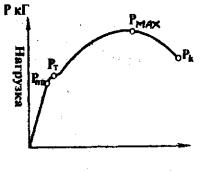
отложены величины нагрузок P, H, а по горизонтальной оси - величины абсолютных удлинений образца l, мм.
Рис. 5. Диаграмма растяжения мягкой стали
Вначале, до точки Рпц идет прямая линия. Это значит, что удлинения пропорциональны нагрузкам, прилагаемым к образцу. Нагрузка, соответствующая точке Рпц называется нагрузкой предела пропорциональности. До предела пропорциональности в металле возникают только упругие деформации. Если нагрузку удалить, то образец возвратится в первоначальное состояние и никаких остающихся удлинений в образце обнаружено не будет.
При дальнейшем повышении нагрузки прямолинейность нарушается и прямая переходит в кривую, то есть происходит нарушение пропорциональности между напряжением и удлинением, и в образце начинают возникать остаточные удлинения.
При повышении нагрузки выше Рпц кривая может переходить в горизонтальную или почти горизонтальную линию, что указывает на то, что в этот момент удлинение образца увеличивается без возрастания нагрузки. Материал как бы течет, поэтому нагрузка, соответствующая горизонтальному участку на кривой, называется нагрузкой Рт, соответствующей пределу текучести (физическому).
Если при растяжении образца не образуется горизонтальной площадки, то за нагрузку предела текучести принимают ту
20

нагрузку, которая вызывает остаточное удлинение, равное 0,2% расчетной длины образца, и обозначают через Р0,2 нагрузку, соответствующую пределу текучести условному.
После предела текучести нагрузка начинает увеличиваться до максимума в точке Pmax. Наибольшая нагрузка Pmax соответствует пределу прочности (временному сопротивлению).
Дальше в образце начинает образовываться шейка (местное уменьшение сечения образца), нагрузка в связи с этим понижается; наконец, при нагрузке, соответствующей точке Pk, происходит разрыв образца.
Определение нагрузки предела текучести. Для определения нагрузки Р0,2 условного предела текучести надо провести прямую ОА (рис. 6), совпадающую с прямолинейным участком кривой растяжения. Через точку О провести ось ординат ОР. От точки О вправо надо отложить участок ОВ, величина которого равна величине заданного остаточного удлинения, то есть 0,2 % от начальной расчетной длины образца (l0), увеличенного до масштаба диаграммы растяжения (например, в 100 раз, если диаграмма получена с масштабом 100:1). Из точки В надо провести прямую ВС, параллельную прямой ОА. Точка D пересечения прямой ВС с кривой растяжения определит высоту ординаты, то есть нагрузку Р0,2, соответствующую условному пределу текучести.
Рис. 6. Определение по диаграмме растяжения нагрузки предела текучести
21

Предел текучести (условный) σ0,2, Па, определяют по формуле:
0,2 |
|
Р0,2 |
(10) |
|
F0 |
||||
|
|
|
Определение предела прочности. Определение предела прочности при растяжении, σb, Па, определяют по формуле:
b |
|
Pmax |
(11) |
|
F0 |
||||
|
|
|
Определение истинного разрушающего напряжения. Расчет истинного разрушающего напряжения проводят по формуле:
Sk |
Pk |
(12) |
|
Fk |
|||
|
|
Все полученные значения механических параметров заносят в табл. 3. Расчетные значения заносят в табл. 4
Таблица 3
l0, |
lk,мм |
δ, % |
d0, мм |
dk, мм |
|
F0, |
Fk, |
|
Ψ, |
|
мм |
|
|
|
|
|
мм |
мм |
|
% |
|
|
|
|
|
|
|
|
|
|
|
|
|
|
|
|
|
|
|
|
Таблица 4 |
||
σ0,2, МПа |
|
σb, МПа |
|
Sk, МПа |
|
|||||
|
|
|
|
|
|
|
|
|
|
|
Задание
1.Изучите схему испытания и величину твердости по Ро-
квеллу.
2.Изучите устройство прибора типа Роквелла, а также выбор нагрузки и индентора.
22
3.Подготовьте образцы и проведите испытания на твер-
дость.
4.Изучите методику определения по диаграмме растяжения нагрузки предела текучести, предела прочности и истинного разрушающего напряжения.
5.Проведите испытание на растяжение образца стали.
6.Определите относительное удлинение и относительное сужение образца, рассчитайте нагрузку предела текучести, предел прочности и истинное разрушающее напряжение.
7.По результатам испытаний заполните таблицы и напишите отчет по работе.
Контрольные вопросы
1.В чем заключается принцип измерения твердости?
2.Как измеряется твердость по методу Роквелла?
3.Методика измерения твердости и выбор индентора и нагрузки по шкалам А, В, С.
4.Как проводятся испытания на растяжение?
5.Как определить нагрузку предела текучести?
6.Как определить предел прочности и истинное разрушающее напряжение?
7.Как определить относительное сужение и относительное удлинение образца?
Лабораторная работа №4
ВЛИЯНИЕ ТЕРМИЧЕСКОЙ ОБРАБОТКИ НА СТРУКТУРУ И СВОЙСТВА МЕТАЛЛОВ
ЦЕЛЬ РАБОТЫ Изучить возможности влияния различных режимов тер-
мической обработки на структуру и свойства металлов.
23
КРАТКИЕ ТЕОРЕТИЧЕСКИЕ СВЕДЕНИЯ Цель любого процесса термической обработки заключа-
ется в том, чтобы нагревом до определенной температуры и последующим охлаждением вызвать желаемое строение металла. Основными факторами воздействия при термической обработке являются температура и время.
Если в сплавах при нагреве имеет место фазовое превращение (полиморфное превращение, растворение второй фазы и т.д.), то нагрев выше некоторой критической температуры вызывает изменение в строении сплава. При последующем охлаждении произойдет обратное превращение. Если охлаждение происходит достаточно медленно, то превращение совершается в полной мере, фазовый состав будет соответствовать равновесному состоянию (отжиг). Если охлаждение быстрое, то зафиксируется состояние сплава, характерное для высоких температур (закалка).
Во многих случаях закалка фиксирует не состояние сплава при высокой температуре, а некоторую стадию структурного превращения, при которой в сплаве не достигается еще равновесное состояние.
И в том, и в другом случае сплав нагревается выше температуры фазового превращения и окончательное строение приобретает в результате превращения при последующем охлаждении.
Термической обработкой называют комплекс технологических операций нагрева материала до определенных температур, выдержки при этих температурах и охлаждения с различными скоростями с целью изменения структуры и свойств. Упрочнению термической обработкой в машиностроении подвергается до 40 % стали, потребляемой этой отраслью. Выбор материала и вида его термической обработки с целью получения максимальных технико-экономических показателей является наиболее важным и сложным звеном в процессе конструирования и изготовления изделия, определяющим его надежность и долговечность. Основными операциями термической
24
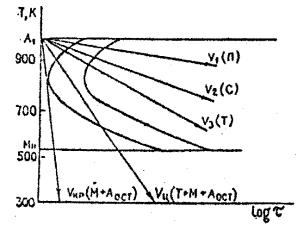
обработки, различно изменяющими структуру и свойства стали, и назначаемыми в зависимости от требований, предъявляемых к полуфабрикатам и изделиям, являются отжиг, нормализация, закалка и отпуск.
Общее описание процессов отжига, закалки и нормализации можно сделать при наложении кривых охлаждения на диаграмму изотермического распада аустенита. Первым (общим) этапом всех этих процессов является нагрев для получения структуры аустенита выше критических температур A1 -A3. Далее следует выдержка при этих температурах для выравнивания температуры и завершения образования аустенита и охлаждение до комнатных температур. В процессе охлаждения происходит превращение переохлажденного аустенита, причем строение и свойства стали зависят от скорости охлаждения
(рис. 7).
Рис. 7. Влияние скорости охлаждения на превращение аустенита в стали
При отжиге сталь после нагрева выше критической точки медленно охлаждается вместе с печью со скоростью V1 , обеспечивающей получение в углеродистой стали наиболее равновесной структуры - перлита. Для проведения полного отжига доэвтектоидную сталь нагревают до температур, на 20-400 вы-
25
ше точки А3 и охлаждают вместе с печью. Структура после охлаждения – феррит и перлит.
Для заэвтектоидных сталей полный отжиг с нагревом выше Аcm не используют. Для них применяют отжиг с нагревом до 740-7800С и последующим медленным охлаждением. Структура после охлаждения – зернистый перлит.
При нормализации сталь нагревают до температур на 30500С выше линии GSE; охлаждение производится на спокойном воздухе со скоростью V2, обеспечивающей в углеродистой стали получение структуры сорбита.
При охлаждении в масле со скоростью V3 получается структура троостита. Критическая скорость охлаждения - это минимальная скорость, при которой не происходит распада аустенита на феррит и цементит. Охлаждение со скоростью выше критической реализуется при использовании в качестве охлаждающей среды воды и обеспечивает в углеродистой стали получение наиболее неравновесной структуры - мартенсита.
Указанные выше структуры: перлит, сорбит и троостит - являются продуктами распада переохлажденного аустенита в области перлитного превращения, представляют собой ферри- то-цементитные смеси пластинчатого строения и отличаются друг от друга по структуре только степенью дисперсности. Однако это различие вызывает существенное изменение свойств: по мере увеличения дисперсности в ряде перлит -сорбит - троостит пластичность стали уменьшается, а твердость ее возрастает.
Мартенситное превращение Мартенситное превращение протекает при быстром охла-
ждении (Vкр) углеродистой стали с температуры выше А1, например, в воде, когда подавлен диффузионный распад аустенита на смесь двух фаз (феррита и карбида), резко отличающихся по составу от исходного аустенита. Концентрация углерода в мартенсите такая же, как и в исходном аустените, следовательно, в отличие от перлитного превращения мартенситное превращение – бездиффузионное. Это превращение характеризуется некоторыми особенностями.
26
1.Превращение аустенита в мартенсит может протекать только при непрерывном охлаждении.
2.Превращение аустенита в мартенсит никогда не идет до конца, даже при при охлаждении ниже точки Мк; всегда в закаленной стали кроме мартенсита, остается небольшое количества остаточного аустенита, что объясняется увеличением объема и фазовым наклепом аустенита.
3.Превращение аустенита в мартенсит протекает с огромной скоростью.
4.При превращении аустенита в мартенсит возникают большие внутренние напряжения, которые вызывают деформацию, а иногда появление трещин в закаленных изделиях.
5.Мартенсит имеет игольчатое строение.
Превращение аустенита в мартенсит при охлаждении начинается с определенной для каждой марки стали температу-
ры Мн.
При закалке на мартенсит резко возрастает твердость стали. Например, твердость эвтектоидной стали в отожженном состоянии равна ~ 18 HRC, а в закаленном - ~ 65 HRC. высокая твердость сталей, закаленных на мартенсит, обусловлена, главным образом, возникновением сильных искажений в решетке пересыщенного -раствора за счет внедренных атомов углерода. Другими причинами упрочнения являются: фазовый наклеп – деформация решетки из-за увеличения объема при мартенситном превращении, образование внутри кристаллов мартенсита множества двойниковых пластин, тормозящих движение дислокаций, закрепление дислокаций атмосферами из атомов углерода, а также дисперсными частицами карбида, успевающими выделиться из мартенсита в период закалочного охлаждения ниже температуры Мн.
Закалка стали Полная закалка с нагревом до температуры, обеспечива-
ющей получение структуры однородного аустенита, применяется только для доэвтектоидных и эвтектоидных сталей. Структура после закалки этих сталей будет состоять из мелко-
27
игольчатого мартенсита и остаточного аустенита. При нагреве доэвтектоидных сталей до температуры выше А1 , но ниже А3 (неполная закалка) структура стали будет состоять из аустенита
иферрита. При последующем охлаждении со скоростью выше критической феррит в структуре сохранится, а аустенит превратиться в мартенсит. Наличие феррита ведет к снижению твердости стали и одновременно не увеличивает пластичность
иударную вязкость стали (брак по недогреву). Перегрев стали, т.е. нагрев на 150-2000С выше А3, способствует росту аустенитного зерна. После охлаждения структура стали будет состоять из крупноигольчатого мартенсита и остаточного аустенита, обладающего пониженной ударной вязкостью (брак по перегреву).
Заэвтектоидные стали закаливают с температур, превышающих точку А1 на 35-60 оС (неполная закалка). При закалке с температур в интервале А1 – Аcm в заэвтектоидных сталях наряду с мартенситом имеется остаточный аустенит и вторичный цементит, который повышает износостойкость инструмен-
та. Нагрев до температур выше Аcm вреден, так как твердость при этом не возрастает, но зато укрупняется аустенитное зерно, усиливается обезуглероживание поверхности и растут закалочные напряжения.
Режим охлаждения должен давать необходимую глубину прокаливаемости и не приводить к возникновению сильных закалочных напряжений.
Закалочные напряжения складываются из термических и структурных напряжений. Термические напряжения возникают в результате перепада температур по сечению образца, т.к. наружные и внутренние слои образца сжимаются на разную величину. Мартенситное превращение связано с увеличением объема на несколько процентов. А поскольку из-за перепада температур оно происходит не одновременно в разных точках сечения изделия, возникают структурные напряжения.
Чем выше температура нагрева под закалку и скорость охлаждения, тем больше перепад температур, что ведет к росту термических и структурных напряжений.
28