
Производственная и пожарная автоматика / Shishov - Tekhnologii promishlennoy avtomatizatsii 2007
.pdf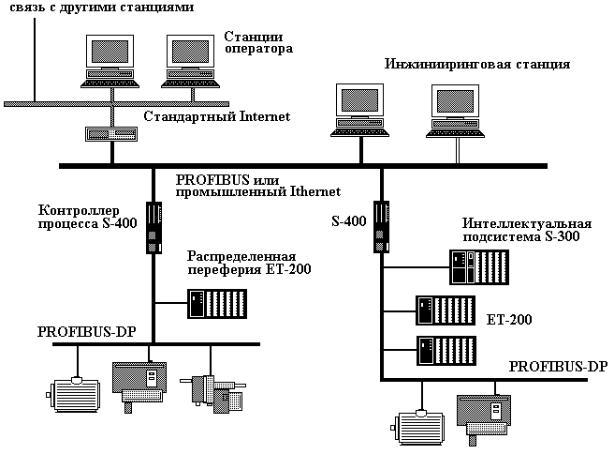
Р и с. 2.6. Аппаратные и сетевые компоненты системы SIMATIC PCS 7
Станции распределенного ввода/вывода ЕТ 200М/X/iS подключаются к системе управления через шину PROFIBUS-DP. Станции позволяют включать и отключать модули без остановки всей системы управления и завода в целом. Для управления оборудованием, расположенным в зонах повышенной опасности, в станциях могут применяться модули с входами и выходами искробезопасного исполнения (Ex-модули).
SIMATIC PCS 7 оснащена системой проектирования ES, позволяющей решать широкий круг задач проектирования человеко-машинного интерфейса, систем управления на основе программируемых логических контроллеров, систем распределенного ввода/вывода. Система проектирования содержит готовые стандартные библиотеки, снабжена функциональными блоками тестирования, мощными средствами редактирования и копирования, что значительно повышает эффективность разработки систем управления процессами. Наличие единой системы организации хранения и обработки данных позволяет использовать в SIMATIC PCS 7 широкий спектр средств проектирования: STEP 7, SCL, CFC, DocPro, опции I&C (например, SFC), технологическая иерархия и ассистент импорта-экспорта, WinCC.
Подсистемы визуализации и обслуживания реализуются на базе персональных компьютеров. Настройка всей системы осуществляется централизованно при помощи ПК-ориентированного программного обеспечения, в основе
24
работы которого лежит общая для всей системы база данных. Визуализация и контроль процесса осуществляются при помощи средств, имеющих одинаковую пользовательскую оболочку.
Рабочие станции системы SIMATIC PCS 7 спроектированы с учетом специальных требований, предъявляемых к системам управления процессами. Базовым программным обеспечением рабочих станций является пакет WinCC (Windows Control Center). Основной пакет WinCC поддерживается управляющими системными опциями. Управляющие системные функции обеспечивают защиту доступа к системе с помощью считывателя пластиковых карт, синхронизацию по времени суток с помощью DCF 77 и GPS, вывод на изображение процесса изображений с видеокамеры, архивацию данных, иерархическое отображение процессов и т.д. В системе могут быть использованы рабочие станции различного исполнения (SIMATIC PC промышленного исполнения, персональные компьютеры).
Вцентральных диспетчерских пунктах, как правило, применяются системы
сархитектурой типа «клиент/сервер», реализуемые на базе персональных компьютеров. В качестве операционных систем применяются версии Windows NT фирмы Microsoft. В дополнение к этому предлагаются новые системы визуализации и обслуживания, работающие под управлением операционной системы
Unix.
Всостав SIMATIC PCS 7 включен пакет программ BATCH flexible, который позволяет достаточно просто и с минимальными затратами осуществлять пакетное управление процессом. SIMATIC PCS 7 позволяет осуществлять гибкое управление любыми процессами и непрерывными, и пакетноориентированными. Во всех способах представления программ, пользователи получили дополнительную поддержку по созданию рецептов управления пакетными процессами.
Для хранения значений переменных процесса, сообщений и другой информации служит реляционная база данных, содержание которой может циклически или в зависимости от определенных событий в системе архивироваться для долгосрочного хранения и записываться на внешние носители данных. Кроме того, все эти данные могут импортироваться в другие приложения посредством стандартных интерфейсов фирмы Microsoft.
6.2 Программно-технический комплекс фирмы ОМРОН
Универсальность, эффективность и скорость являются жизненно важными факторами конкурентоспособности в машиностроении. Системы управления компании Omron в полной мере обеспечивают заказчику эти конкурентные преимущества. Качество, надежность и внедрение современных технологий являются неотъемлемым качеством всех систем управления компании Omron.
Основными аппаратными программируемыми средствами автоматизации компании являются:
• серия компактных программируемых логических контроллеров CPM1 и
CPM2;
25
•серия модульных программируемых логических контроллеров CJ1;
•серия программируемых логических контроллеров для монтажа в стойке
CS1 .
Устройства рассчитаны на удовлетворение растущих потребностей в скорости обработки и прозрачности сетей. Они обеспечивают совместимость при обмене данными в модулях, между модулями и главными компьютерами, а также между оборудованием и удаленными станциями. Кроме того, поддерживающее программное обеспечение компании Omron помогает использовать всю мощь и гибкость этих систем управления. Изделия компании Omron поддерживают широкий диапазон сетей, включая сеть Compobus/S, открытые промышленные шины DeviceNet и Profibus, шина MC-High motion, простая в эксплуата-
ции шина Controller Link и, конечно, Industrial Ethernet.
Протокол FINS (Интеллектуальная сетевая служба масштаба предприятия) представляет собой независимый от типа сети протокол связи компании Omron, поддерживаемый программируемыми логическими контроллерами, терминалами HMI и программным пакетом. Он обеспечивает непосредственный доступ к программам, параметрам конфигурации и всем остальным данным, допускающим чтение или запись. Протокол FINS обеспечивает доступ к любому элементу с помощью модема, а также по сетям Ethernet, Controller Link
иDeviceNet с использованием одной и той же команды, т.е., этот протокол не зависит от типа сети.
Модули ввода/вывода DeviceNet (DRT2) – это ведомые модули ввода/вывода обеспечивающие встроенные функции диагностики и технического обслуживания. Такие встроенные функциональные возможности обеспечивают пользователя подробными данными диагностики и технического обслуживания без какого-либо дополнительного программирования контроллеров, позволяя свести к минимуму затраты на техническое обслуживание, на поиск и устранение неисправностей.
Пакет автоматизации CX содержит программные средства настройки, программирования, запуска, наблюдения и обслуживания для всех контроллеров Omron при абсолютной совместимости передачи данных. Требуемые для работы программные средства всегда можно расширить путем добавления дополнительных программных компонентов.
Программы визуализации пакета CX-Automation Suite компании Omron содержат ряд инструментов для визуализации работы оборудования, технологических процессов или продукции.
Программа CX-Server lite обеспечивает связь систем управления Omron с программами из пакета Microsoft Office. Использование стандартных шаблонов, входящих в состав программы CX-Server lite, позволяет считывать и просматривать производственные данные в программе Microsoft Excel без дополнительного программирования.
CX-Server lite обладает следующими функциональными возможностя-
ми:
•повышение наглядности представления производственной информации через стандартное офисное программное обеспечение;
26
•удобный доступ ко всем переменным программируемого логического контроллера и, как следствие, ко всей информации об оборудовании, технологическом процессе или производстве;
•для программирования требуется только опыт работы с программами Microsoft, что снижает стоимость обучения и исключает необходимость привлечения специалистов;
•автоматизация трудоемкой подготовки производственных и технологических отчетов;
•создание единой программы визуализации HMI с помощью стандартного программного обеспечения Microsoft и использование интерфейса OPC для подключения к системе управления.
Впрограмме CX-Server OPC используется стандартный промышленный интерфейс обмена данными OPC, обеспечивающий удобство обмена данными с системами управления Omron.
Функциональные возможности CX-Server OPC достаточно широки:
•диспетчерское управление и доступ к данным;
•работа с технологическими программам;
•отображение и протоколирование аварийных сигналов и ошибок;
•язык программирования сценариев на основе программ Microsoft;
•простая связь с базами данных уровня предприятия;
•простота в эксплуатации;
•разработка и использование многоязычных приложений.
Программа CX-Supervisor обеспечивает функции по визуализации процессов. Она сочетает в себе простоту эксплуатации с мощным набором функций и возможностей.
6.3 Программно-технический комплекс ТЕКРОН® промышленной группы Текон
ПТК "ТЕКРОН" – многоуровневая иерархическая информационноизмерительная и управляющая система распределённого типа созданная для аппаратных и программных средств российской группы компаний «ТЕКОН».
Программно-технический комплекс "ТЕКРОН" предназначен для применения в автоматизированных системах управления технологическими процессами, систем телемеханики, систем коммерческого учёта энергоресуров и т.д., обеспечивающих:
•измерение, оперативный контроль технологических параметров, управление технологическим оборудованием, автоматическое управление и регулирование технологических процессов, выполнение противоаварийных защит и блокировок технологических процессов, архивирование значений параметров и событий;
•коммерческий учет и диспетчеризацию добываемого, транспортируемого, перерабатываемого и распределяемого природного газа и его компонентов, а
27
также оперативный контроль и архивирование текущих, суммарных и усредненных значений их технических параметров;
•коммерческий учет и диспетчеризацию отпускаемой или потребляемой тепловой энергии и теплоносителя в открытых и закрытых водяных и паровых системах теплоснабжения и системах теплопотребления, подключённых по зависимой или независимой схеме присоединения к тепловой сети, и оперативный контроль, архивирование текущих, суммарных и усредненных значений теплофизических параметров теплоносителей;
•коммерческий учёт производимой, распределяемой и потребляемой электроэнергии (активной и реактивной составляющей электроэнергии) и режимных параметров электрической сети, а также оперативный контроль, архивирование текущих, суммарных и усредненных значений параметров энергоснабжения/энергопотребления;
•телеизмерение и телесигнализацию технологических параметров, оперативный контроль и архивирование их текущих, суммарных и усредненных значений, дистанционное управление и регулирование (телеуправление, телерегулирование) исполнительными механизмами.
ПТК относится к средствам измерений электрических величин по ГОСТ 22261.
Базовые программные модули, определяющие функциональную область применения ПТК:
•ТЕКРОН®-Р – с применением модуля управления и регулирования;
•ТЕКРОН®-Г – с применением модуля коммерческого учета газа;
•ТЕКРОН®-Т – с применением модуля коммерческого учета тепла;
•ТЕКРОН®-Э – с применением модуля коммерческого учета электроэнер-
гии;
•ТЕКРОН®-ТМ – с применением модуля телемеханики.
По архитектуре ПТК “ТЕКРОН” – многоуровневая иерархическая ин- формационно-измерительная и управляющая система распределенного типа, включающая в свой состав контроллеры ТЕКОН и модульную интегрированную SCADA КРУГ-2000. Архитектура ПТК в общем виде состоит из верхнего и нижнего уровней.
На нижнем уровне ПТК могут применяться следующие технические средства:
•программируемые логические контроллеры (ПЛК);
•контроллеры многофункциональные МФК3000;
•контроллеры многофункциональные МФК;
•системы интеллектуальных модулей ТЕКОНИК®;
•контроллеры многофункциональные ТКМ410;
•контроллеры многофункциональные ТКМ700,
•барьеры искрозащиты серии TCC Ex.
Контроллеры и интеллектуальные модули выполняют функции автоматического сбора (по аналоговым и цифровым измерительным каналам), хранения и обработки измеряемых параметров, автоматического регулирования, технологических защит и блокировок, а также реализуют вычислительные алго-
28
ритмы, в том числе вычисление количественных и качественных показателей энергоносителей.
Также на нижнем уровне могут использоваться коммуникационные контроллеры на базе процессорных модулей Р06 ТЕКОНИК® или им аналогичных, предназначенные для автоматического сбора (обмена), хранения и первичной обработки измеряемых параметров от внешних устройств и средств измерений по стандартным интерфейсам RS-232, RS-485, Ethernet, а также для реализации вычислительных алгоритмов, в том числе вычисление количественных и качественных показателей энергоносителей.
На верхнем уровне ПТК применяются технические средства выполненные на базе IBM PC совместимых компьютеров промышленного или офисного исполнения под управлением операционных систем совместимых с SCADA КРУГ-2000, а также сетевое оборудование для объединения всех технических средств локальной вычислительной сетью Ethernet. В качестве устройств верхнего уровня, в общем случае, могут использоваться:
•выделенные серверы оперативной и (или) архивной базы данных (Серверы ОБД и АБД), предназначенные для сбора, регистрации, заданной математической обработки, в том числе для реализации алгоритмов вычисления количественных и качественных показателей энергоносителей, документирования и архивирования информации, поступающей с ПЛК нижнего уровня;
•автоматизированные рабочие места (АРМ) оперативно-диспетчерского и управленческого персонала, которые в общем случае могут быть выполнены с использованием архитектуры "клиент-сервер" (АРМ-клиенты) и предназначены для визуализации оперативной и архивной информации о технологическом процессе с серверов ОБД и АБД, а также для формирования оперативного дистанционного воздействия на объект управления;
•серверы "Web-Контроля", предназначенные для передачи информации с ПТК сторонним пользователям посредством сети Internet;
•станции инжиниринга, предназначенные для осуществления наладочных
исервисных работ по обслуживанию абонентов нижнего и верхнего уровней ПТК;
•серверы точного времени, предназначенные для поддержания единого астрономического времени абонентов нижнего и верхнего уровней ПТК, с его коррекцией по сигналу точного времени, получаемого со спутника (по GPSприемнику);
•COM-серверы для связи с другими подсистемами АСУ ТП;
•табло коллективного пользования для отображения информации.
Режим работы ПТК – круглосуточный с остановами на техническое обслуживание во время остановок технологического оборудования.
Основные технические характеристики, общие для всех модификаций
ПТК:
•общее количество аналоговых и дискретных измерительных/управляющих каналов – до 30 000;
•период обновления информации на верхнем уровне ПТК – от 1с;
29
•периодичность опроса сигналов, обеспечивающая требования по точности фиксации событий и значений аналоговых сигналов по отношению к системному времени ПТК (в зависимости от динамических свойств параметра) для дискретных пассивных – 0,03 - 0,5с, для дискретных инициативных – 10 мс, для аналоговых – 0,02 - 0,2с, для аналоговых температурных параметров – 0,25
-2с;
•время выдачи управляющего воздействия по каналам технологических защит (ТЗ) после обнаружения аварийной ситуации (для ТЗ, не имеющих выдержки времени) не более 0,1 - 0,2 с;
•время прохождения команды от момента нажатия операторомтехнологом кнопки виртуального блока управления до появления сигнала на выходных цепях ПТК, не более – 1 с;
•задержка от момента выдачи оператором команды дистанционного управления до отображения на мониторе результатов выполнения команды без учета времени отработки команды объектом управления не более 1,5 с;
•количество формируемых трендов до 50 000, дискретность записи в тренды – от 1 секунды и выше;
•количество регистрируемых в ПТК оперативных сообщений (событий) до 21 000 за одни сутки, архивных – ограничено только ёмкостью дискового накопителя.
Дискретность регистрируемых сообщений (событий) – от 10 мс.
7. ЦИФРОВЫЕ ПРОМЫШЛЕННЫЕ СЕТИ
7.1. Требования к ЦПС
Проводящееся ранее рассмотрение тенденций развития современных промышленных систем позволило сделать вывод о том, что одним из основных компонентов развитых систем АСУ ТП является цифровая промышленная сеть (ЦПС).
Промышленная сеть – это среда передачи данных, которая должна отвечать множеству разнообразных, а зачастую противоречивых требований. Промышленная сеть – это набор стандартных протоколов обмена данными, позволяющая связать воедино оборудование различных производителей, а также обеспечить взаимодействие нижнего и верхнего уровней АСУ. Наконец, промышленная сеть – это образ мысли инженера, определяющий конфигурацию и принципы построения системы. От этого будут зависеть не только затраты на создание системы, но и срок ее жизни, ее способность к развитию.
Попробуем сформулировать лишь некоторые основные требования, которые можно предъявить к «идеальной» промышленной сети:
1.высокая производительность;
2.предсказуемость времени доставки информации;
3.помехоустойчивость;
30
4.доступность и простота организации физического канала передачи
данных;
5.максимальный сервис для приложений верхнего уровня;
6.минимальная стоимость устройств аппаратной реализации, особенно на уровне контроллеров;
7.возможность получения «распределенного интеллекта», путем представления максимального доступа к каналу нескольким ведущим узлам;
8.управляемость и самовосстановление в случае возникновения нештатных ситуаций.
Как видно, в получившемся списке одно требование может противоречить другому. Подобные противоречия приходится обходить постоянно на всех уровнях проектирования, начиная с того, какой формат пакета передачи данных выбрать: тот, который позволит осуществлять расширенное управление сетью и удаленную загрузку, или тот, который обеспечит максимально быструю работу
сбольшим числом дискретных сигналов, заканчивая решением проблемы, что лучше: применить не самое современное, но проверенное годами решение, или применить кажущееся блестящим и современным решение, которое почему-то оказывается дороже и еще до сих пор не применяется на предприятииконкуренте.
Таким образом, можно считать, что промышленная сеть – один большой компромисс. И от того, как расставлены акценты в этом компромиссе, зависит успешность решения задач, стоящих перед сетевой архитектурой.
К промышленным сетям вполне применимы результаты теоретических изысканий в области коммуникационных сетей общего назначения, поэтому при их рассмотрении становятся вполне понятными постоянные ссылки на Модель взаимодействия открытых систем (Open System Interconnection model – OSI), принятую Международной организацией по стандартизации (ISO).
Модель OSI призвана разграничить и формализовать функции, выполняемые различными уровнями аппаратного и программного обеспечения сетевой структуры. Данная модель определяет семь уровней сервиса, предоставляемого сетью (таблица 2.1).
Т а б л и ц а 2.1.
Уровни модели взаимодействия открытых систем
7 |
Application |
Прикладной уровень |
|
|
|
б |
Presentation |
Уровень представления |
|
|
|
5 |
Session |
Уровень сессий |
|
|
|
4 |
Transport |
Транспортный уровень |
|
|
|
3 |
Network |
Сетевой уровень |
|
|
|
2 |
Data Link |
Канальный уровень |
|
|
|
|
|
|
31
1 |
Physical |
Физический уровень |
|
|
|
|
|
|
На физическом уровне определяются физические характеристики канала связи и параметры сигналов.
Канальный уровень формирует основную единицу передаваемых данных – пакет и отвечает за дисциплину доступа устройства к каналу связи (Medium Access Control) и установление логического соединения (Logical Link
Control).
Сетевой уровень отвечает за адресацию и доставку пакета по оптимальному маршруту.
Транспортный уровень разбирается с содержимым пакетов, формирует ответы на запросы или организует запросы, необходимые для уровня сессий.
Уровень сессий оперирует сообщениями и координирует взаимодействие между участниками сети.
Уровень представления занимается преобразованием форматов данных, если это необходимо.
Прикладной уровень – это набор интерфейсов, доступных программе пользователя.
На практике большинство промышленных сетей ограничивается только тремя из них, а именно физическим, канальным и прикладным. Наиболее «продвинутые» сети решают основную часть аппаратно, оставляя программную прослойку только на седьмом уровне.
7.2 Стандартные ЦПС
Рассмотрим несколько стандартов ЦПС, широко распространенных в различных приложениях современных АСУ ТП.
AS-интерфейс (Actuator/Sensor Interface). Это открытый международ-
ный стандарт EN 50 295. Появился в 1993 году. Поддерживается консорциумом ведущих производителей средств АСУТП, в числе которых фирмы Siemens, Pepperl+Fuchs и другие. Относится к классу ЦПС оконечных устройств, осуществляя непосредственную интеграцию датчиков и исполнительных механизмов в систему автоматизации. Позволяет полностью исключить из АСУ ТП аналоговые линии связи, кроссировочные шкафы и другое вспомогательное оборудование.
Отличительными чертами AS-интерфейса являются следующие основные характеристики:
•топология – произвольная («шина», «звезда», «дерево», «кольцо»);
•число ведущих устройств (master) – 1;
•число ведомых устройств (slave) – до 31;
•метод доступа – последовательный опрос;
•максимальное время опроса 5 - 10 мс.
32
•кабель используется как для обмена данными, так и для подачи напряжения питания на датчики/исполнительные механизмы;
•простой и экономичный монтаж соединений;
•малое время реакции: ведущему устройству требуется не более 5 мс для циклического обмена данными с 31 узлом сети;
•при использовании стандартных AS-i модулей на кабеле может находиться до 124 исполнительных механизмов/датчиков;
•если используются AS-i модули с расширенным режимом адресации, с одним ведущим устройством могут работать до 186 исполнительных механизмов и 248 датчиков;
•установка адресов устройств – автоматическая или ручным сервисным прибором;
•кабель – неэкранированный двух проводной с сечением 2х1,5 мм2 или специальный плоский;
•максимальная суммарная протяженность линий связи сегмента сети, об-
служиваемого одним ведущим устройством, – 300м (с использованием повторителей);
• электропитание напряжением 30 В постоянного тока.
Для развертывания сегмента AS-сети необходимо следующее оборудование (рис. 2.7):
•кабель;
•источник электропитания;
•ведомые устройства для подключения датчиков и исполнительных механизмов;
•ведущее устройство;
•повторители (при необходимости);
•сервисный прибор для адресации и диагностирования.
33