
Лекции / Лекция 6
.pdf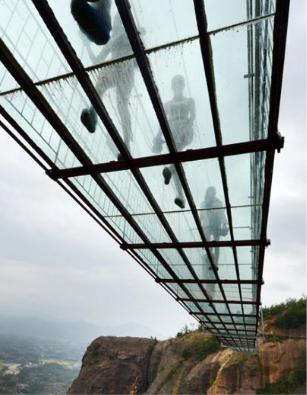
«Пою перед тобой в восторге похвалу ‒ не камням дорогим, не злату, но стеклу…» (М.В. Ломоносов)
Лекция №6
СТРОИТЕЛЬНОЕ СТЕКЛО ИЗ МИНЕРАЛЬНЫХ РАСПЛАВОВ
1.ОБЩИЕ СВЕДЕНИЯ
2.СЫРЬЕ И ОСНОВЫ ПРОИЗВОДСТВА СИЛИКАТНОГО СТЕКЛА
3.КАЧЕСТВЕННЫЕ ХАРАКТЕРИСТИКИ ОСНОВНЫХ ИЗДЕЛИЙ ИЗ СТЕКЛА
5.РАЗНОВИДНОСТИ ЛИСТОВОГО СТЕКЛА
6.СВЕТОПРОЗРАЧНЫЕ ИЗДЕЛИЯ И КОНСТРУКЦИИ
6.СТЕКЛО В АРХИТЕКТУРНО-ХУДОЖЕСТВЕННОМ ОФОРМЛЕНИИ
7.СТЕКЛОКРИСТАЛЛИЧЕСКИЕ МАТЕРИАЛЫ И ИЗДЕЛИЯ
1. Общие сведения
Стекло – это аморфное вещество, получаемое путём переохлаждения расплава независимо от его химического состава и температурной области затвердевания и обладающее в результате постепенного увеличения вязкости механическими свойствами твёрдого тела. Причём процесс перехода из жидкого состояния в стеклообразное должен быть обратимым. Процесс превращения стеклообразующего расплава в твёрдое состояние происходит постепенно, путём нарастания вязкости в широком интервале температур, минуя кристаллическую фазу (СТБ 2054 и ГОСТ 32539). Образование в стекле кристаллов является пороком и приводит к потере прочности, прозрачности и рассеянию света.
Стекло, как строительный материал имеет многовековую историю. Оно было и продолжает оставаться самым востребованным строительным материалом. +
1
П р и м е ч а н и е – 1. Стекло известно человечеству с доисторических времен:
как природный материал:
вулканического происхождения – обсидиан, получившего название по имени воина Обсидиана, который привез такой камень из Эфиопии в Рим,
и метеоритного происхождения – тектиты (от греч. расплавленный);
либо как искусственное стекло – силикатное, боратное, боросиликатное и др.
Искусственное стекло было изобретено за несколько тысяч лет до н. э. Считается, что стеклоделие, как самостоятельное ремесло, сложилось уже в середине II тыс. до н. э., в эпоху поздней бронзы.
2. Стекло иногда называют еще «переохлажденной жидкостью», не успевшей при остывании перейти в кристаллическое состояние. Однако не следует отождествлять понятия «переохлажденная жидкость» с понятием «твердое тело». Стекло – это, безусловно, твердое тело, но аморфного строения. Стеклообразное состояние вещества – это состояние вещества с аморфным строением, обладающее способностью в результате постепенного увеличения вязкости приобретать механические свойства твердого тела. Переход из твердого стеклообразного состояния в расплав и наоборот характеризуется температурным интервалом. Обратимость этого перехода и является отличительной особенностью стеклообразного состояния от других аморфных тел.
В строительстве используются как органические стекла «плексиглас» (полиметилметакрилат, полистирол, поликарбонат), так и неорганические – из минеральных расплавов. Но минеральные расплавы в зависимости от скорости охлаждения и ряда других условий могут затвердевать как в аморфном (стеклообразном), так и кристаллическом состоянии. Разница лишь в том, что если одни расплавы (силикатные) для получения стекла можно охлаждать часами, то для получения, например, металлических стёкол скорость охлаждения должна быть порядка ста градусов в секунду (106 град/сек.). При таких гигантских скоростях охлаждения атомы не успевают выстроиться в строгом порядке, как это происходит в кристаллах, и расплав затвердевает, не кристаллизуясь. В результате формируются твёрдые аморфные стеклообразные вещества с внутренней структурой аналогичной жидкости, и стеклообразное состояние является лишь частным случаем аморфного.
Следовательно, для каждого аморфного стеклообразного вещества есть два состояния:
при более высоких температурах они ведут себя как жидкости (пластичны);
при температурах ниже, так называемой, температуры стеклования (tg) (для силикатных стёкол tg составляет 400…600°С) – как твёрдые и хрупкие тела. Ниже температуры стеклования стекло становится хрупким.
Все стекла имеют искусственную аморфную стеклообразную структуру, но
вместе с тем при определённых условиях охлаждения могут иметь и кристаллическую или смешанную (аморфно-кристаллическую) структуру. Характерным признаком стеклообразного состояния вещества является также отсутствие чётко выраженной точки плавления. Их переход в расплавленное состояние происходит в интервале температур, т. е. при нагревании они размягчаются и постепенно переходят в жидкое состояние, при охлаждении – наоборот. Кроме того, стекло не является веществом с
2
определённым химическим составом и не может быть выражено химической формулой. Чаще всего его состав условно выражают суммой оксидов, входящих в шихту.
В отличие от кристаллических веществ, стёкла изотропны, прозрачны и чрезвычайно хрупкие. Прочность стекла при ударном изгибе составляет всего 0,2 МПа, а на сжатие, например, у оконного стекла − около 1000 МПа. Тем не менее, свойства стёкол можно изменять термической, химической и механической обработкой.
П р и м е ч а н и е – Стекло всегда ценили за два прекрасных качества: прозрачность и низкую теплопроводность. Чего стеклу не хватало, так это – прочности. Выражение – «хрупкое, как стекло» издавна вошло в поговорку – и не без основания.
И, тем не менее, возможности для повышения прочности стекла – есть. Считается, например, что истинная (теоретическая) прочность стекла ≈ в 200 раз больше, чем реальная (фактическая). Например, фактическая прочность обычного оконного стекла при растяжении и изгибе составляет лишь 30…90 МПа, а теоретическая может достигать 8…10 тыс. МПа.
Дело в том, что хрупкость стекла не является результатом его молекулярной структуры, а вызывается наличием поверхностных микротрещин, т. е. технологией изготовления. Другими словами – причиной низкой фактической прочности стекла служат микродефекты поверхности, внутренние напряжения, возникающие при охлаждении, и другие причины, которые могут быть устранены с развитием науки и технологий. Уже в настоящее время в лабораторных условиях получают тянутые стеклянные волокна прочностью более 7 тыс. МПа, а также пуленепробиваемые и другие стекла.
Способность веществ к стеклообразованию зависит также от их химического состава. Веществами (оксидами), расплавы которых при охлаждении способны переходить в стеклообразное состояние, являются кремнезём (SiO2), фосфорный ангидрид (P2O5), борный ангидрид (B2O3) и др. Называют их стеклообразующими, а стекла, образованные ими, – соответственно силикатное, фосфатное, боросиликатное (СТБ ЕН 1748-1), алюмосиликатное и др. Однако наиболее ярко эта способность выражена у кремнезёма (SiО2) и соединений на его основе – силикатов. Поэтому в промышленных масштабах наибольшее применение находит силикатное стекло (натрий- кальций-силикатное), основными компонентами которого являются диоксид кремния
иоксиды натрия и кальция.
Пр и м е ч а н и е – 1. Стекло разлагается в недрах земли через миллион лет.
2.При разрушении стекла трещина движется со скоростью около 5 тыс. км/час.
3.Самое толстое силикатное стекло, изготовленное человеком, имеет толщину 26 см (экран аквариума в г. Сиднее размером 7х4 м)
4.Стекло – одно из немногих материалов, которое может быть переработано, не теряя качества, на 100%.
5.Разрабатываются новые технологии получения стекла. Например, ученые создали сверхпрочное стекло, которое по прочности не уступает стали. В составе такого стекла до 50% оксида алюминия и другие компоненты.
2. Сырье и основы производства силикатного стекла
Сырьём для производства силикатного стекла (СТБ 2416) служат кремнезём
SiO2 (69…74%), оксиды кальция CaO (5…14%), натрия Na2O (10…16%), магния MgО
3
(0…6%), алюминия Al2O3 (0…3%) и в небольших количествах другие (вспомогательные) компоненты (0…5%). К ним относят осветлители (способствуют удалению из стекломассы газовых пузырьков), обесцвечиватели (устраняют сине-зеленые или желто-зеленые оттенки), глушители (придают стеклу светорассеивающие свойства или делают его непрозрачным), красители (окрашивают стекло в тот или иной цвет) и др.
Кремнезёмистым компонентом в составе сырьевой смеси (шихты) является кварцевый песок с максимальным содержанием кремнезёма SiO2 и минимальным содержанием окрашивающих оксидов. Оксид натрия вводится в виде технической кальцинированной соды (Na2CO3) или сульфата натрия (природного Na2SO4). Сода, сульфат натрия понижают температуру варки стекла и ускоряют процесс стеклообразования.
При варке смеси чистого песка и соды (SiO2 + Na2CO3) образуется полупрозрачная стеклообразная (сиропообразная) масса Na2SiO3, называемая натриевым жидким стеклом (силикат-глыба), способная растворяться в воде под действием давления пара 3…5 атм. Используя вместо соды карбонат калия (поташ) К2СО3, получают калиевое жидкое стекло. Называются такие продукты – растворимое стекло, жидкое стекло или силикатный клей и относят их к группе воздушных вяжущих веществ. Благодаря введению в шихту CaO (стабилизатор) в виде известняка CaCO3 или доломита CaCO3·MgCO3, стекло становится нерастворимым в воде. Следовательно, трёхкомпонентная шихта – песок, сода и известняк являются базовой смесью для производства обычного силикатного стекла.
П р и м е ч а н и е – Силикатное стекло – неорганическое стекло, основным компонентом которого является оксид кремния. Натрий-кальций-силикатное стекло – силикатное стекло, характеризующими компонентами которого являются оксиды натрия и кальция (ГОСТ 32539).
С целью улучшения технических характеристик стекла в его состав вводят другие компоненты. Например, для повышения скорости стекловарения и термостойкости стекла вводят оксид бора, прочности и химической стойкости – оксиды алюминия, для получения окрашенных или цветных стёкол – перекись марганца, оксид хрома и др. При введении оксидов свинца образуются стекла с высоким показателем преломления света – хрусталь. Сырьём для производства других стеклообразных минеральных расплавов (каменных, шлаковых) служат, соответственно, базальты, диабазы, базальто-доломиты, доменные металлургические и другие шлаки.
Современное стекольное производство состоит из следующих основных операций: подготовка сырья; приготовление шихты; стекловарение; формование изделий (выработка) и их отжиг. Для получения стекла указанные вещества очищают от примесей, размалывают, дозируют по массе, и готовят в смесителе шихту. Затем шихту расплавляют при температуре 1400…1500°С в ванных печах непрерывного или периодического действия. Расплавление шихты называется варкой стекла. Процесс варки
4
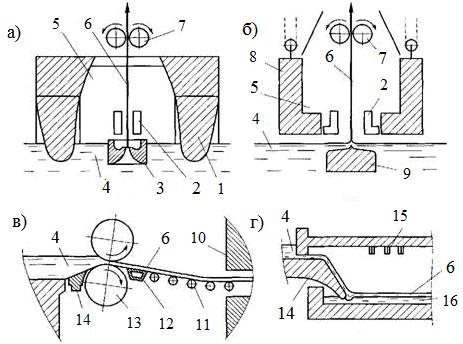
стекла делится на три стадии: провар шихты, осветление и студка (осторожное охлаждение или тепловая обработка). Варку стекла ведут по особому для каждого вида стекла режиму. После расплавления масса выдерживается при той же температуре до полного отделения всех примесей. Примеси, как правило, собираются на поверхности стекломассы в виде пены. В это время происходит также и обесцвечивание стекломассы путём введения специальных добавок, а также удаление пузырьков воздуха и газа. Переработка стекломассы в изделия осуществляется при температуре 1000…1100°С и называется выработкой.
По структуре материалы и изделия из стекла могут быть плотного, пористого, ячеистого, волокнистого, зернистого и других строений. По назначению стекло подразделяется на техническое, строительное и бытовое. Строительное стекло – на конструкционное, отделочное, теплоизоляционное, звукоизоляционное и др.
Наиболее массовым видом продукции строительного стекла является листовое стекло. Листовое прозрачное натрий-кальций-силикатное стекло (далее – силикатное) является основным видом продукции стекольных заводов и представляет собой плоские листы, у которых длина и ширина значительно превосходят толщину (ГОСТ 111 и ГОСТ Р 54170). Выработка листового стекла (далее – стекла) осуществляется вертикальным вытягиванием ленты (тянутое стекло), флоат-способом (флоат-стекло) и горизонтальным прокатом (рис. 6.1).
Рис. 6.1. Схема формование листового стекла: а, б соответственно лодочный и безлодочный способы вертикального вытягивания ленты стекла; в горизонтальный прокат; г флоат-процесс;
1 ограждающий мост; 2 холодильник; 3 шамотная лодочка; 4 стекломасса; 5 камера формования; 6 лента стекла; 7 вытягивающие валки; 8 шамотные экраны; 9 шамотное погружаемое тело; 10 печь для отжига; 11 валки роликового конвейера; 12 охлаждаемая плита; 13 охлаждаемые прокатывающие валки; 14 приемный лоток; 15 нагреватели; 16 расплав олова
5
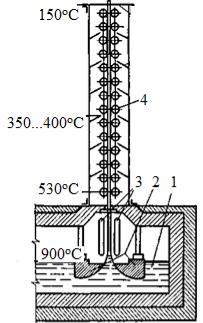
В зависимости от качества поверхности листовое стекло выпускается неполированным и полированным. Неполированное стекло формуют на машинах вертикального или горизонтального вытягивания ленты из вязкой стекломассы, либо горизонтальным прокатом. Полированным называют прозрачное стекло, обе поверхности которого отшлифованы и отполированы для придания им плоскостности и параллельности с целью обеспечения чёткого неискажённого изображения при просмотре сквозь него или при отражении. Микронеровности на поверхности полированного стекла не превышают 0,01 мкм. Получают либо путём механической шлифовки и полировки сырого прокатного или тянутого стекла, либо полирования ленты стекла в процессе её формирования на поверхности расплавленного металла (СТБ 2417).
П р и м е ч а н и е – Формование стекла – это процесс превращения расплавленного стекла (стекломассы) в твердое изделие заданной геометрической формы. При этом стекло из состояния вязкой жидкости в результате ее охлаждения и твердения переходит сначала в пластичное, а затем в твердое хрупкое состояние. Формование стекла осуществляется в интервале определенных температур.
При вертикальном способе производства вязкая стекломасса из стекловаренной печи постепенно оттягивается специальными машинами в виде непрерывной ленты (СТБ 2418). По виду узла формования различают «лодочное» и «безлодочное» вытягивание ленты стекла. Лодочный способ заключается в том, что лента стекла вытягивается через щель специального шамотного поплавка (лодочку), погруженного на некоторую глубину в расплавленную стекломассу (рис. 6.2).
Рис.6.2. Схема процесса формования стекла лодочным способом:
1 расплав стекломассы, 2 шамотная лодочка, 3 холодильники, 4 тянущие валки
6
Толщина стекла при этом регулируется путём изменения скорости вытягивания ленты. Однако качество стекла при таких способах производства получается недостаточно высоким, имеет оптические искажения. Для устранения имеющихся дефектов и повышения его качества стекло приходится подвергать дополнительной обработке (шлифовке, полировке), что усложняет и удорожает процесс производства. Выпускается тянутое стекло трех видов: новоантичное (плоское стекло ручной выработки с особой структурой поверхности), для ремонта (с допустимым наличием дефектов) и с минимальным наличием видимых дефектов.
Стекло с более высокими качественными показателями получают флоатспособом (разработан в 1959 г. фирмой Pilkington) и называют флоат-стеклом. Флоатстекло (float-glass) получило своё название от английского глагола «to float» (плавать). Сущность такого способа производства (т. н. термического формования) листового стекла состоит в том, что регулируемое количество стекломассы в виде плоской ленты поступает из стекловаренной печи в ванну на зеркальную поверхность расплавленного металла (олова), находящегося в защитной атмосфере из азота и водорода. Поскольку стеклянная масса имеет значительно меньшую плотность и более высокую вязкость относительно расплава металла, то она не смешивается и образует верхний слой, который продвигаясь по расплаву металла, превращается в ленту стекла с огненно-полированными поверхностями (рис. 6.3). В результате контакта нижней поверхности ленты стекла с идеально гладкой поверхностью расплавленного металла и огневой полировки ее верхней поверхности (под действием сил поверхностного натяжения) достигается исключительное качество поверхностей такого стекла – оно как бы полируется, становится абсолютно ровным и с малыми оптическими искажениями.
Для получения стекла необходимой толщины происходит либо растягивание ленты стекла (для малых толщин) с помощью специальных устройств (роликов, топроллеров), либо ограничение растекания (для больших толщин). Охлаждение сформированной ленты стекла осуществляется через футеровку ванны дополнительными холодильными установками различных конструкций. После охлаждения и выхода из флоат-ванны лента стекла подается в печь отжига для устранения остаточных напряжений путем регулируемого охлаждения (по заданному режиму) от температуры формования до температуры резки (≈60°С). Отжиг позволяет предотвратить образование временных напряжений, и ослабить остаточные напряжения до величины, безопасной с точки зрения прочности изделий. После отжига лента стекла разрезается на необходимые размеры (СТБ EN 572-8), маркируется, упаковывается и складируется.
П р и м е ч а н и е – Резка стекла считается нормальной, если соблюдаются следующие условия:
рез по стеклу должен быть ровный;
наносится при равномерной, постоянной скорости движения стеклореза и постоянном давлении ролика на стекло;
7
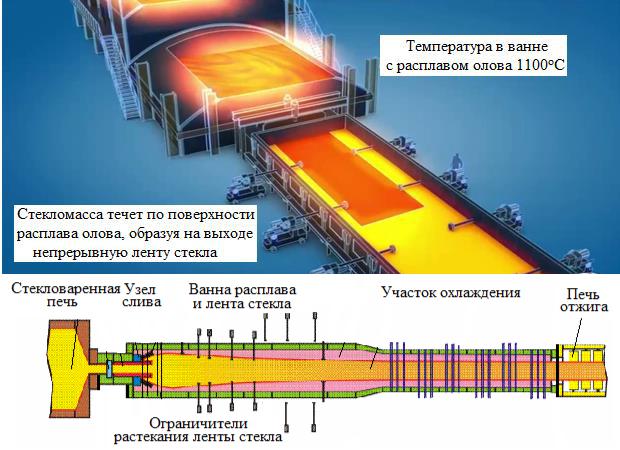
наклон стеклореза при его движении не должен изменяться;
резка должна производиться стеклорезом, смоченным в керосин, при этом не должна образовываться стеклянная стружка и пыль;
стекло должно разламываться по линии реза без образования сколов и т. п.
Рис. 6.3. Схема производства флоат-стекла
Флоат-стекло выпускается толщиной от 2 до 25 мм, но может быть меньше 2 мм и больше 25 мм, а размеры в длину и ширину – 5100…6000 х 3210 мм (свободных размеров) и по спецификации потребителя (твёрдых размеров). Оно может быть прозрачным, окрашенным или иметь специально нанесённое покрытие. Продолжительность цикла с момента формования ленты до упаковки готового стекла составляет около 2-х часов. В Республике Беларусь производителем флоат-стекла является ОАО «Гомельстекло» (две технологические лини с общим выпуском
35…45 млн. м2 в год).
П р и м е ч а н и е – На разработку и практическое внедрение уже запатентованного фло- ат-способа производства листового стекла (еще в 1902 г.) фирме Pilkington из 500 сотрудников (из них 250 с учеными степенями) потребовалось более 7 лет. Затраты фирмы были настолько высоки, что практически привели ее к разорению. Однако новый способ, получивший название «флоатспособ» (плавающее стекло), оказался перспективным и рентабельным. За короткое время (10…15 лет) этот способ практически полностью заменил механические конвейеры по обработке стекла и стал доминирующим в мире. Ширина ленты стекла может составлять до 4 м при толщине до 50 мм. Скорость выработки – от 600 до 1300 м/час.
8
Флоат-ванна имеет длину 45…55 м, ширину по длине от 7 до 4 м. Глубина слоя расплавленного олова изменяется по длине от 100 до 40 мм. Масса олова в ванне – 120…150 т. Невозвратные потери олова со стеклом составляют 4…5 т в год.
При горизонтальном способе проката стекломасса сливается на гладкую поверхность и прокатывается валками с гладкой или узорчатой поверхностью. Таким способом получают крупноразмерное цветное и бесцветное утолщенное стекло, а также армированное, узорчатое и волнистое.
3. Качественные характеристики основных изделий из стекла
Листовое стекло является в основном базовым продуктом для производства стекла функционального назначения. Основными качественными показателями таких стёкол являются внешний вид, оптические и спектрофотометрические характеристики (светопропускание, светоотражение, поглощение энергии и др.), плотность, прочность, твёрдость, коэффициент линейного расширения и др. (СТБ 2416, ГОСТ 111, 32361, 32539 и 33004).
Внешний вид и оптические искажения. Внешний вид листового стекла оцени-
вается по наличию и размерам видимых пороков: включений – газообразных (пузырь, мошка), кристаллических (камень), стекловидных (свиль, шлир), пороков формования (отпечатки валков, кованость, прилипшая крошка), механических повреждений (царапины, потёртости, сколы, выступы, отбитости, трещины, посечки) и другие (дросс, блюм).
Оптические искажения (в проходящем и отраженном свете) стекла устанавливаются визуально по распознаваемости или искажению изображений в виде системы черно-белых полос «зебра» или «кирпичная стена» и оцениваются минимальным (максимальным) углом между направлением наблюдения и плоскостью листа стекла, при котором не наблюдаются искажения (изменение формы полос экрана, их «размытие»).
В соответствии с оптическими искажениями и допускаемыми пороками листовое стекло подразделяют на марки М0, М1, М4, М7 (ГОСТ 111). Чем ниже цифра в марке стекла, тем выше его качество, т. е. самого высокого качества стекло марок М0 и М1.
Светотехнические показатели стекла связаны с характерными особенностями взаимодействия световых лучей со стеклом. Луч света при воздействии на стекло частично проходит через слой стекла, частично поглощается стеклом (0,5…3%) и частично отражается (8…9%). Поглощение света вызвано присутствием в стекле соеди- нений-красителей, вызывающих избирательное поглощение, т. е. поглощение лучей только определенной длины волны. Поглощенное излучение возвращается стеклом во внешнее и внутреннее пространство путем конвекции и вторичного теплового излучения.
9
Светопропускание стекла (прозрачность, т. е. способность пропускать световые лучи) характеризует собой отношение светового потока, проходящего сквозь стекло, к падающему световому потоку.
Светоотражение ‒ отношение светового потока, отраженного от стекла, к падающему световому потоку.
Отражение энергии – процент солнечной энергии, отражённой от стекла. Поглощение энергии – процент солнечной энергии, поглощённой панелью стек-
ла в остеклённой конструкции ограждения.
Светопропускаемость стекла, как и другие оптические свойства (светоотражение, отражение и поглощение энергии) оцениваются коэффициентами соответственно светопропускания, отражения и поглощения (абсорбции). Определяющими показателями всех остеклений являются коэффициенты светопропускания и общего пропускания солнечной энергии (ГОСТ 26302). Остальные показатели несут дополнительную информацию о свойствах остекления (СТБ ЕН 410). По коэффициенту прохождения видимого света через стекло определяется оптическая прозрачность.
Обычные силикатные стекла хорошо пропускают всю видимую (87…90%) и инфракрасную (ИК) (почти 80% от падающего потока) часть спектра и практически не пропускают ультрафиолетовые лучи. Минимальное значение коэффициента направленного светопропускания в зависимости от толщины стекла (2…25 мм) составляет соответственно 0,89…0,67. Теоретически, даже особо прозрачное, не поглощающее свет стекло, не может пропускать света более 92%, так как обе его поверхности отразят не менее 8% световых лучей. Высокая прозрачность листового стекла обусловлена тем, что стекло является однородной и однофазной средой. В нём отсутствуют границы раздела фаз, которые вызывают рассеяние света. Коэффициент эмиссии силикатного стекла составляет 0,837, показатель преломления – 1,5 (хрустального
–1,65) и коэффициент направленного отражения света – 0,08.
Пр и м е ч а н и е ‒ 1. Декларируемая характеристика пропускания видимого света даже т. н. сверхпрозрачного стекла составляет 91,5 % при толщине 2 мм.
2. Отражение света от поверхности стекла может быть снижено (называется просветлением стекла) или увеличено путем нанесения тонких пленок некоторых материалов, имеющих меньший (больший) коэффициент преломления, чем стекло. По методике нанесения и составу покрытия просветление бывает физическим (напыление) и химическим (травление).
Теплофизические свойства. Коэффициент теплопередачи характеризуется количеством тепла в ваттах (Вт), которое проходит через 1 м2 конструкции остекления при разности температур по обе стороны в один градус по шкале Кельвина (К) и измеряется в Вт/(м2∙К). Сопротивление теплопередаче (термическое сопротивление)
– величина, обратная коэффициенту теплопередачи, выражает собой отношение разности температур окружающей среды по обе стороны ограждающей конструкции к плотности теплового потока, измеряется в м2∙К/Вт. Теплопроводность листового стекла составляет 0,4…0,82 Вт/(м∙К), что почти в 10 раз меньше, чем у аналогичных
10