
Каталитический крекинг
.pdfСПБГУАП группа 4736 https://new.guap.ru/i03/contacts
К А Т А Л И Т И Ч Е С К И Й К Р Е К И Н Г
Процесс каталитического крекинга -основной процессом, направленным на углубление переработки нефти. Цель процесса - получение высококачественного компонента автобензина с октановым числом* 85-93(ИМ).
При каталитическом крекинге образуется значительное количество газа, богатого пропан-пропиленовой и бутан-бутиленовой фракциями (сырье для производства различных высокооктановых эфиров, алкилатов и других ценных компонентов моторного топлива). Установки каталитического крекинга являются также поставщиком сырья для химической промышленности: из газойлей крекинга получают сажевое сырье и нафталин, тяжелый газойль может служить сырьем для производства высококачественного игольчатого кокса.
За длительный период своего развития, каталитический крекинг значительно совершенствовался как в способах контакта сырья и катализатора, так и в отношении применяемых катализаторов. Эти усовершенствования влекли за собой радикальные изменения технологии процесса в целом, позволившие увеличить выход целевого продукта – компонента автобензина от 30-40 до 50-70% мас. максимально.
Достигнутый прогресс обеспечил вовлечение в переработку все более тяжелого сырья: если на первой стадии развития крекингу подвергали керосино-газойлевые фракции, а затем – вакуумные газойли, то за последние 20 лет все возрастает число установок, использующих в качестве сырья нефтяные остатки: мазуты, деасфальтизаты и их смеси с вакуумными дистиллятами.
Химические основы каталитического крекинга.
Каталитический крекинг – типичный пример гетерогенного катализа. Реакции протекают на границе двух фаз: твердой(катализатор) и паровой или жидкой (сырье); в этой связи решающее значение имеют структура и поверхность катализатора.
Алюмосиликатные катализаторы обладают очень пористой и развитой поверхностью, что в существенной степени объясняет их активность. Кроме того, между строением этих катализаторов и углеводородов существует геометрическое подобие. Следует отметить аналогию в поведении алюмосиликатов, хлористого алюминия и кислотных катализаторов (серной кислоты, фосфорной кислоты, фтористого водорода ). Во всех случаях ускоряемые ими реакции связаны с переносом водорода.
При каталитическом крекинге протекают реакции деструкции, алкилирования, изомеризации, ароматизации, полимеризации, гидрогенизации и деалкилирования углеводородов. Некоторые из них являются первичными, но большинство – вторичными.
Наиболее распространенной теорией механизма каталитического крекинга является карбоний-ионная, предложенная Уитмором (карбоний-ион – положительно заряженный углеводородный ион).
Карбоний-ионный механизм каталитического крекинга исходит из кислотного характера алюмосиликатного катализатора, имеющего условную формулу nAl2O3 · mSiO2 · xH2O. На поверхности катализатора имеются каталитические центры двух
СПБГУАП группа 4736 https://new.guap.ru/i03/contacts
видов: протонные, где каталитическая функция принадлежит протонам (кислоты Бренстеда), и апротонные (кислоты Льюиса), где координационно ненасыщенный атом алюминия служит акцептором электронов.
В результате контакта углеводородного сырья с катализатором и взаимодействия с его протонами образуются карбоний-ионы, отвечающие эмпирической формуле Cn H+2n+1 для парафинов и для моноциклических нафтенов.
Наиболее легко образуются карбоний-ионы, когда с катализатором взаимодействуют олефины, - протон катализатора присоединяется к молекуле олефина:
RCH = CH2 + H+ →RC+H – CH3
*- Октановое число: в бензиновом двигателе внутреннего сгорания сжигание топлива включается с помощью свечей зажигания. В постоянно создаваемых внутри камеры сгорания условиях высокого давления и температуры жизненно важно предотвратить преждевременное возгорание топлива. Октановое число измеряет устойчивость топлива к спонтанному
возгоранию. Чем выше октановое число, тем больше устойчивость топлива к возгоранию
Склонность карбоний-ионов к изомеризации при последующем разрыве по β-связи приводит к образованию к образованию легких изопарафинов и олефинов, присутствующих в значительных концентрациях в газах и легких бензиновых фракциях каталитического крекинга.
Таким образом, наиболее активными углеводородами в условиях контакта с алюмосиликатными являются непредельные.
Полимеризация олефинов начинается при комнатной температуре; с повышением температуры возникает обратная реакция деполимеризации, равновесие которой при температурах промышленного процесса сдвигается в сторону разложения. Высокая активность непредельных углеводородов, на несколько порядков превышающая таковую при термическом крекинге, в первую очередь объясняется их высокой адсорбируемостью на катализаторе.
Парафиновые углеводороды в присутствии катализатора подвергаются крекингу значительно быстрее, чем при термическом крекинге, причем особенно легко происходит распад высокомолекулярных углеводородов. Специфичными особенностями каталитического крекинга парафинов являются:
Тенденция к расщеплению молекул в нескольких местах, благодаря чему получаются углеводороды с низкой молекулярной массой. Газообразные углеводороды в основном сосоят из трех и более атомов углерода (главным образом, пропан, пропилен, бутан, бутилены), а содержание метана и этана незначительно;
Повышенное содержание ароматических углеводородов в жидких продуктах;
Значительное содержание изопарафинов, что является результатом полимеризации, изомеризации, гидрирования олефинов.
Олефиновые углеводороды подвергаются каталитическому крекингу легче, чем парафиновые. Если каталитический распад парафинов примерно в 10 раз быстрее, чем термический, то олефины распадаются каталитически в 1 000 – 10 000 раз быстрее, причем скорость крекинга нарастает с увеличением молекулярной массы.
Реакции изомеризации протекают достаточно легко. Образующиеся изоолефиновые углеводороды насыщаются водородом с образованием изопарафинов. Одновременно
СПБГУАП группа 4736 https://new.guap.ru/i03/contacts
получаются значительные количества ароматических углеводородов и высокомолекулярных соединений.
Нафтеновые углеводороды при 500º С подвергаются каталитическому крекингу примерно в 500 – 4000 раз быстрее, чем термическому, и скорость крекинга определяется молекулярной массой, но не строением нафтенового углеводорода. Так, в условиях, при которых циклогексан подвергается крекингу на 7%, алкилированные пергидрофенантрены превращаются на 80%. Крекинг идет очень глубоко, причем распадаются и кольца, и боковые алкильные цепи. Характерно отметить, что при крекинге нафтенов образование ароматических углеводородов связано с образованием предельных алифатических соединений, что является результатом сопряженного дегидрирования.
Ароматические углеводороды. Гомологи бензола при 500º С подвергаются крекингу тем легче, чем разветвленнее боковая цепь:
Углеводород |
Степень |
|
превращения,% |
C6H5CH3 |
1 |
C6H5CH2CH3 |
11 |
н-C6H5C3H7 |
43,5 |
изо-С6Н5С3Н7 |
83,5 |
перв-н- |
13,9 |
С6Н5С4Н9 |
|
втор- |
49,2 |
С6Н5С4Н9 |
|
трет- |
80,4 |
С6Н5С4Н9 |
|
В результате разложения моноалкилированных бензолов образуется бензол, а также углеводорды С3 и С4.
Порядок расположения углеводородов по их стабильности при каталитическом крекинге следующий: олефины < ароматические углеводороды с тремя и большим числом заместителей < нафтены < полиметилированные ароматические углеводороды < парафины < конденсированные ароматические углеводороды.
Относительные скорости каталитического крекинга во всех случаях выше скоростей термического крекинга. При 500º С каталитическому крекингу подвергаются быстрее:
парафины – в 6 – 60 раз;
нафтены – в 1000 раз;
олефины – более чем в 100 – 10 000 раз;
ароматические углеводороды – более чем в 10 000 раз.
Газ каталитического крекинга весьма постоянен по составу; он всегда содержит в значительных количествах водород и углеводороды С3 и С4.
Последних обычно в 2-3 раза больше, чем при термическом крекинге, но водорода меньше, так как он присоединяется к ненасыщенным молекулам. Коксообразование

СПБГУАП группа 4736 https://new.guap.ru/i03/contacts
велико, если присутствуют циклоолефины, диолефины и ненасыщенные жирноароматические углеводороды, например стирол.
В результате следует отметить самые существенные особенности каталитического крекинга: 1) избирательное протекание процесса с малым образованием С1 и С2- содержащих осколков; 2) ясно выраженную изомеризацию углеродного скелета и кратных связей в молекулах олефинов; 3) значительное насыщение С=С-связей (особенно у изомеризованных олефинов с высокой молекулярной массой); 4) большое количество ароматических и изопарафиновых углеводородов; 5) большее, чем при термическом крекинге коксообразование; 6) значительные выходы бензина с высоким октановым числом(80-81 ММ).
В таблице сопоставлены данные по продуктам термического и каталитического крекинга.
Сопоставление продуктов реакций при термическом и каталитическом крекинге
Исходные углеводороды |
Термический крекинг |
Каталитический крекинг |
Парафиновые |
Главный продукт – |
Главный продукт – |
|
парафины С2 с большой |
парафины от С3 до С6, мало |
|
примесью С1 и С3, много |
нормальных олефинов выше |
|
нормальных олефинов от С3 |
С4; алифатические |
|
до С5; мало алифатических |
углеводороды главным |
|
углеводородов изостроения |
образом изостроения |
Нормальные олефиновые |
Кратная связь перемещается |
Кратная связь перемещается |
|
медленно; скелетная |
быстро; скелетная |
|
изомеризация происходит в |
изомеризация происходит в |
|
малой степени |
значительной степени |
Изоолефиновые |
Перераспределение |
Перераспределение |
|
водорода идет медленно и |
водорода - избирательно |
|
не избирательно для |
для третичных изоолефинов. |
|
третичных изоолефинов. |
Крекируются со значительно |
|
Крекируются примерно с |
большей скоростью, чем |
|
такой же скоростью, как |
соответствующие парафины |
|
парафины |
|
Нафтеновые |
Крекируются с меньшей |
Крекируются быстрее, чем |
|
скоростью, чем парафины |
нормальные парафины с |
|
|
соответствующим числом |
|
|
атомов С |
Алкилароматические(с |
Крекируется боковая |
Крекируется боковая |
цепями С1-С2) |
алкильная цепь |
алкильная цепь |
|
|
непосредственно у кольца |
Алкилароматические(с С3 |
Крекируются с меньшей |
Крекируются с большей |
и более длинными цепями) |
скоростью, чем парафины |
скоростью, чем парафины |
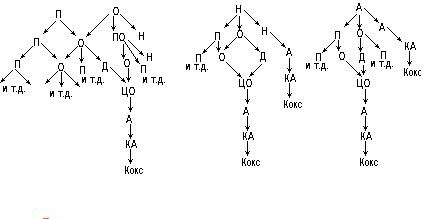
СПБГУАП группа 4736 https://new.guap.ru/i03/contacts
Общая схема реакций крекинга углеводородов.
Реакции крекинга углеводородов всех классов, которые встречаются в исходном сырье, могут быть представлены следующей схемой:
где П – парафиновые углеводороды; О – олефины; Н – нафтеновые углеводороды; А – ароматические углеводороды; ПО – полимеризованные олефины; ЦО – циклические олефины; Д – диены; КА – конденсированные ароматические углеводороды
Схема показывает, что коксообразование является вторичной реакцией – результатом крекинга ароматических углеводородов, образующихся на различных стадиях процесса.
Крекинг сложных углеводородов может затрагивать какую-либо часть молекулы, независимо от других ее частей.
Обычно одним из лучших критериев интенсивности побочных реакций является отношение выходов бензина и кокса. Высокое отношение указывает на преобладание желательных реакций. Низкое отношение выходов бензина и кокса указывает на интенсивное протекание нежелательных побочных реакций. К желательным реакциям относятся изомеризация, гидрирование, циклизация и ароматизация (неглубокая) олефинов; эти реакции ведут к высокому выходу парафиновых углеводородов изостроения и ароматических углеводородов, выкипающих в пределах температур кипения бензина, и высокому отношению изо- и нормальных парафиновых углеводородов. Нежелательные реакции (крекинг, дегидрогенизация и полимеризация олефинов, алкилирование и конденсация ароматических углеводородов) приводят к высоким выходам водорода и кокса, низкому выходу олефинов и к получению сравнительно тяжелых газойлей, при этом выход бензина и его октановое число снижаются.
По стадиям процесс каталитического крекинга можно представить следующим образом:
1.поступление сырья на поверхность катализатора(внешняя диффузия);
2.диффузия(внутренняя) молекул сырья в поры катализатора;
3.хемосорбция молекул сырья на активных центрах катализатора;
4.химическая реакция на катализаторе;
5.десорбция продуктов крекинга и непрореагировавшего сырья с поверхности и диффузия из пор катализатора;
6.удаление продуктов крекинга и неразложившегося сырья из зоны реакции.
СПБГУАП группа 4736 https://new.guap.ru/i03/contacts
Характер протекающих реакций определяет химический состав получаемых продуктов: бензин содержит много изопарафиновых и ароматических углеводородов; отсюда его высокое октановое число. Газ получается «тяжелый», с высоким содержанием изобутана и олефинов С3-С4 и весьма низким содержанием метана и этана; газойлевые фракции богаты полициклическими ароматическими углеводородами.
Учет химических превращений, происходящих при каталитическом крекинге, сложен и требует знания углеводородного состава исходных и конечных продуктов.
Лимитирующей стадией каталитического крекинга является химическая реакция на поверхности – в кинетической области протекания реакции. В случае применения цеолитсодержащих катализаторов, имеющих разветвленную пористую структуру, скорость процесса может лимитироваться диффузией реагирующих молекул в порах катализатора( внутри диффузионная область). Каталитический крекинг углеводородов является необратимой реакцией первого порядка.
В процессе каталитического крекинга образуются высокомолекулярные соединения, которые отлагаются на поверхности катализатора, приводя к его дезактивации. Кокс на катализаторе крекинга состоит из агломератов с псевдографитовой структурой и многоядерных, ароматических углеводородов. Повышение глубины конверсии сырья, температуры реакции и длительности контакта катализатора с сырьем способствует увеличению соотношения углерод:водород в коксе.
Катализаторы каталитического крекинга.
Реакции каталитического крекинга протекают на поверхности катализатора. Направление реакций зависит от свойств последнего, качества сырья и условий процесса. В результате крекинга на поверхности катализатора отлагается кокс, поэтому важной особенностью каталитического крекинга является необходимость непрерывной регенерации катализатора (выжигание кокса).
Для крекинга применяются алюмосиликатные катализаторы. Это искусственно полученные твердые высокопористые вещества с сильно развитой внутренней поверхностью.
В настоящее время наибольшее развитие получили системы каталитического крекинга «флюид»(ККФ), то есть с «кипящим» слоем катализатора, использующие микросферический целиотсодержащий катализатор.
Современные катализаторы крекинга содержат в своем составе 3-20% мас. цеолита, равномерно распределенного в матрице. Преобладающей формой цеолитсодержащего катализатора являются микросфероиды со средним диаметром частиц около 60 мкм для установок ККФ и шарики диаметром 3-4 мм – для установок с движущимся слоем.
Цеолиты, используемые в составе катализаторов, должны иметь высокую активность и селективность в крекинге нефтяных фракций, стабильность при высокотемпературных воздействиях в среде воздуха и водяного пара, необходимые размеры входных окон в полости структуры. Таким требованиям в наибольшей степени соответствуют цеолиты типа Х и Y в редкоземельной обменной форме или в ультрастабильной форме, и поэтому
СПБГУАП группа 4736 https://new.guap.ru/i03/contacts
они находят преимущественное применение при синтезе катализаторов крекинга. Цеолиты представляют собой алюмосиликаты с трехмерной кристаллической структурой следующей общей формулы: Me2/nO·Al2O3·xSiO2·yH2O, где n – валентность катиона Me ;
x– мольное отношение SiO2/Al2O3 ; y – число молей воды.
Внастоящее время известно 34 природных и около 100 разновидностей синтетических цеолитов, однако практическое применение имеют пока несколько типов.
Основой структуры всех цеолитов является тетраэдр, состоящий из четырех анионов кислорода O2- , которые окружают значительно меньший по размерам ион Si4+ или Al3+. Тетраэдры с ионами кремния электрически нейтральны, а тетраэдры с ионами алюминия имеют заряд –1, который в цеолитах нейтрализуется положительным зарядом катиона, например Na+.
Современные катализаторы крекинга характеризуются низким содержанием остаточного натрия (Na2O) – 0,2-0,5%, высокой насыпной плотностью – 800-1000 кг/м3, прочностью на истирание(индекс прочности по Девисону составляет 2 -8%) и однородным гранулометрическим составом.
Зарубежные фирмы располагают широким ассортиментом промышленных катализаторов, различающихся по целевому назначению, уровню активности и селективности. Ведущими фирмами-производителями катализаторов являются: ГрейсДэвисон, Энгельгард, Акзо-Нобель (таблица на стр. №7). Значительными производителями катализаторов являются в настоящее время Китай и Япония.
Среди отечественных катализаторов крекинга наибольшее распространение распространение получили системы КМЦР, Микроцеокар-8, Микроцеакар-5. содержание Al2O3 в современных катализаторах составляет 30-45%. Это обусловлено тем, что высококремнеземная матрица повышает термопаровую стабильность и в определенной степени – устойчивость к отравлению тяжелыми металлами.
Одной из определяющих эксплуатационных характеристик катализаторов крекинга является их регенерируемость. Цеолитсодержащие катализаторы имеют несколько лучшие регенерационные характеристики, чем аморфные алюмосиликаты. Применение в цеолитсодержащих катализаторах редкоземельного цеолита улучшает регенерацию вследствие катализирующего действия ионов редкоземельных элементов на горение кокса.
Цеолитсодержащие катализаторы крекинга отличаются существенно более высокой активностью, чем
Характеристика некоторых зарубежных катализаторов крекинга нефтяных фракций
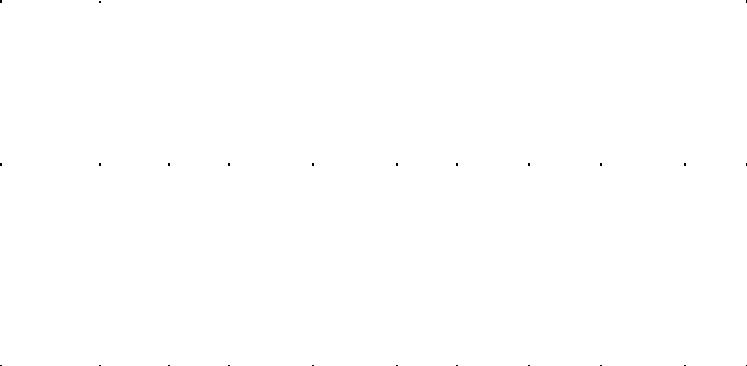
СПБГУАП группа 4736 https://new.guap.ru/i03/contacts
Показатель |
Фирма-производитель и марка катализатора |
|
|
||||||
|
|
Грейс-Девисон |
|
|
|
Акзо- |
|||
|
|
|
|
|
|
||||
|
|
|
|
|
|
|
|
Нобель |
|
|
Криста |
Футур |
Дистимак |
Бриллиан |
ГОАЛ |
Омника |
Ультим |
Адванс- |
Кобра |
|
лл-242 |
а-140 |
с-203 |
т-242 |
-32 |
т-320 |
а-447 |
937 |
|
Содержание |
|
||||||||
|
|
|
|
|
|
|
|
|
|
%мас : |
|
|
|
|
|
|
|
|
|
|
|
|
|
|
|
|
|
|
|
Al2O3 |
49 |
42 |
47 |
49 |
43 |
49 |
47 |
43,5 |
44,4 |
|
|
|
|
|
|
|
|
|
|
Na2O3 |
0,25 |
0,25 |
0,30 |
0,25 |
0,25 |
0,20 |
0,30 |
― |
― |
|
|
|
|
|
|
|
|
|
|
Re2O3 |
2,7 |
2,7 |
2,4 |
2,7 |
3,5 |
1,8 |
1,8 |
2,32 |
1,97 |
|
|
|
|
|
|
|
|
|
|
Индекс |
5 |
5 |
5 |
5 |
5 |
5 |
5 |
― |
― |
Девисона |
|
|
|
|
|
|
|
|
|
Удельная |
300 |
275 |
270 |
300 |
280 |
210 |
320 |
99 |
134 |
плотность, |
|
|
|
|
|
|
|
|
|
м2/г |
|
|
|
|
|
|
|
|
|
Насыпная |
0,70 |
0,70 |
0,72 |
0,71 |
0,73 |
0,72 |
0,72 |
0,87 |
0,94 |
плотность, |
|
|
|
|
|
|
|
|
|
г/мл |
|
|
|
|
|
|
|
|
|
Микроакт |
79 |
78 |
76 |
79 |
79 |
77 |
78 |
69 |
72 |
аморфные алюмосиликаты(на 2-3 порядка), а также большей селективностью по выходу бензина при одновременном снижении выхода газа и кокса. Причины столь необычной селективности заложены в самой природе цеолитов, обладающих высоким адсорбционным потенциалом ультратонких пор, специфическим набором кислотных центров, проявляющих весьма высокую склонность к осуществлению новых реакций протолиза С-С, С-Н - связей и Н-переноса от молекул исходного сырья к промежуточным соединениям карбоний-ионного типа.
Цеолитсодержащие катализаторы проявляют меньшую восприимчивость к отравлению тяжелыми металлами, обычно присутствующими в сырье крекинга. «Эффективные» металлы характеризуют ту долю осажденных на катализаторе тяжелых металлов, которая обусловливает образование кокса и водорода. Содержание «эффективных» металлов определяется как произведение ванадиевого эквивалента(4Ni+V) на активную долю металла, определяемую по графической зависимости. Для цеолитсодержащих катализаторов содержание «эффективных» металлов заметно влияет на образование дополнительного кокса, однако это влияние проявляется меньше, чем для аморфного катализатора.
Особое значение имеет использование металлостойких катализаторов при переработке остаточного сырья. В этом случае наиболее эффективны катализаторы на базе широкопористых матриц с небольшой удельной поверхностью, «улавливающих» тяжелые металлы. Такие катализаторы обладают высокой активностью при содержании в равновесном катализаторе до 10-12 тыс.мг/кг металлов.
Наряду с этими катализаторами используют специальные пассиваторы металлов, которые в виде небольших добавок подаются вместе с сырьем. В настоящее время пассиваторы получили широкое распространение на промышленных установках ККФ. Сущность пассивации заключается в переводе металлов, осадившихся на катализаторе, в
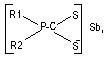
СПБГУАП группа 4736 https://new.guap.ru/i03/contacts
неактивное (пассивное) состояние, например, в результате образования соединения типа шпинели.
Никель чаще всего пассивируют соединениями сурьмы типа:
где R – органические радикалы.
Пассивирующий агент вводят в сырье в виде водоили маслорастворимой добавки. Содержание сурьмы на катализаторе при работе на остаточном сырье и концентрации металлов на катализаторе 9000-15 000мг/кг должно составлять 900-1500 мг/кг.
Помимо сурьмы в качестве пассиваторов можно использовать добавки, содержащие оксиды кальция и магния, не обладающие каталитической активностью, адсорбируют в 6-10 раз больше ванадия, чем обычный катализатор крекинга. Известны также жидкие добавки на основе олова, которые на 30% снижают отрицатальное воздействие ванадия на выход бензина и на 50% - на выход водорода и кокса. На большинстве установок крекинга США и Западной Европы, перерабатывающих остаточное сырье, применяются указанные пассиваторы металлов.
Катализаторы дожига оксида углерода.
Процесс окисления кокса при регенерации катализаторов крекинга представляет собой совокупность последовательных реакций образования и распада углерод-кислородных комплексов с выделением продуктов окисления. Количество образующихся продуктов окисления, а количество выделяющегося тепла в регенераторе зависит от многих факторов, из которых определяющими являются состав коксовых отложений и глубина окисления СО в СО2. Первичная реакция окисления коксовых отложений (распада поверхностных углерод-кислородных комплексов) дает практически постоянное соотношение СО2 /СО≈1,0. Однако образующийся СО может реагировать с избытком кислорода, превращаясь в СО2 с выделением дополнительного количества тепла.
Лучшие результаты дает способ регенерации с использованием каталитического дожига СО в присутствии специальных катализаторов. В качестве таких катализаторов используют металлы-окислители (предпочтительно металлы платиновой группы), которые либо вводят в состав катализаторов, либо применяют в виде твердых добавок, либо в виде жидких добавок, подаваемых вместе с сырьем.
Совершенствование процесса промотированного окисления СО ведется в направлении использования различных окислителей и способов их введения в зону регенерации.
При использовании в качестве окислителя оксидов Cu, Cr, V, Mn, Ti, Fe, Bi, Sn в количестве порядка 1% от катализатора в установке крекинга объемное соотношение СО2/СО в газах регенерации повышается с 1 до 4. Однако в результате значительного содержания в системе активного металла снижается селективность катализатора крекинга по коксу и повышается выход газа и кокса. Значительно эффективнее металлы платиновой группы.
СПБГУАП группа 4736 https://new.guap.ru/i03/contacts
Активный компонент может входить в состав катализатора крекинга, а также может быть нанесен на твердый неорганический носитель и применяться в виде добавки к основному катализатору. Наиболее перспективно использование промоторов окисления в виде отдельных добавок, так как введение твердого промотора в систему независимо от катализатора позволяет с максимальной гибкостью управлять процессом окисления СО в регенераторе. В качестве носителей таких промоторов используют оксиды Al, Si, Ti, Zn, Mg, их смеси, глины, аморфные и кристаллические алюмосиликаты. Окислительная активность промотора проявляется сразу же после его загрузки в реактор; полное окисление СО достигается через 8-10 минут после поступления промотора в систему.
Катализаторы связывания оксидов серы и азота.
При каталитическом крекинге сырья с высоким содержанием серы и азота возникает проблема улавливания из дымовых газов оксидов серы (SOx) и азота (NOx).
Содержание серы в коксе может меняться от 0,4 до 4,4% мас. В среднем 5% мас. серы сырья переходит в кокс и выбрасывается с дымовыми газами регенерации катализатора в виде SOx . Чем больше серы в сырье, тем больше ее в коксе.
При крекинге малосернистого сырья (до 1%мас. серы) содержание SOx в дымовых газах не превосходит 500 мл/м3, но с повышением содержания серы до 1,65% мас. может превышать 2 000мл/м3.
Из технологических приемов, используемых на установках ККФ, снижению выбросов SOx способствуют: уменьшение содержания серы в сырье, снижение глубины превращения, доли рисайкла, повышение расхода пара на отпарку, подачи воздуха в регенератор, температуры регенерации, введение промотора дожига СО. Наиболее экономичным способом очистки дымовых газов от SOx считается использование бифункциональных катализаторов или добавок. Оксиды ряда металлов образуют с SOx стойкие сульфаты, которые в реакторе восстанавливаются до исходного оксида металла и сероводорода, сероводород уходит из реактора с продуктами реакции и отделяется с сухим газом. Рациональнее же бифункциональных катализаторов использовать каталитически неактивные добавки – они не так закоксовываются, и количество добавки можно регулировать независимо от догрузки катализатора. Стоимость очистки с добавками в несколько раз меньше, чем скрубберная очистка или гидроочистка сырья.
При горении кокса в регенераторе от 20 до 90% содержащегося нем азота превращается в NOx и выбрасывается с дымовыми газами. При этом выбросы с установок ККФ в США от общего количества выбросов NOx , на НПЗ составляют: на установках, оборудованных котлами дожига СО – 13%, на остальных – 3%. В странах ЕС выбросы NOx с 1980 г. по 1995 г. снижены на 40%.
Основные факторы, влияющие на процесс каталитического крекинга.
Качество сырья.