
4887
.pdf31
ЛАБОРАТОРНАЯ РАБОТА № 6
ИССЛЕДОВАНИЕ ТОЧНОСТИ СРАБАТЫВАНИЯ ПРЕДОХРАНИТЕЛЬНЫХ МУФТ
1. Цель работы
Оценка точности срабатывания предохранительных муфт и выявление путей ее повышения
2. Общие сведения и расчетные зависимости
Предохранительные муфты предназначены для защиты деталей машин от перегрузок. Они срабатывают, когда вращающий момент превышает некоторую установленную величину ТМ. Обычно величину ТМ назначают несколько большей номинального момента, например на 25 % (для исключения слишком частых срабатываний). Для снижения инерционных усилий от вращающихся масс привода предохранительные муфты устанавливают по возможности ближе
кисточнику перегрузок.
Косновным типам предохранительных муфт относятся: фрикционные,
кулачковые, шариковые и муфты с разрушающимися элементами. Наи-
большее распространение получили фрикционные дисковые предохранительные муфты, у которых усилие на поверхностях трения осуществляется винтовыми или тарельчатыми пружинами.
Как правило, фрикционные муфты используют при кратковременных перегрузках, поскольку при продолжительном скольжении мощность, расходуемая на трение, вызывает интенсивное выделение тепла и износ рабочих поверхностей.
Срабатывание муфты – сложный динамический процесс, и максималь-
ная нагрузка деталей машин зависит от регулировочного момента муфты ТМ, скорости нарастания нагрузки, жесткости системы и моментов инерции масс. Точность ограничения нагрузки муфтой – одна из важнейших ее характеристик,
оцениваемая коэффициентом точности срабатывания КТ:
КТ = ТMmax/ТMmin, |
(6.1) |
где ТМmax и ТМmin – соответственно наибольший и наименьший крутящие моменты, при которых возможно срабатывание муфты, Нм.
Чем ближе КТ к единице, тем надежнее работает муфта, тем выше ее качество.
Для дисковой фрикционной предохранительной муфты (рис. 6.1), у ко-
торой рабочими поверхностями являются плоские (боковые) поверхности дисков, расчетное значение крутящего момента ТМ (Нм) определяется по формуле:
ТМ = Fпрf0 · 0,5Dсрz, |
(6.2) |
где Fпр – осевое усилие пружины, Н; f0 – коэффициент трения;
Dср – средний диаметр рабочих поверхностей, м; z – число трущихся поверхностей: z = m + n – 1,
(m – число ведущих дисков; n – число ведомых дисков).

32
Рис. 6.1. Схема дисковой фрикционной муфты: Q – сила включения, Н;
Rср – средний радиус рабочих поверхностей, м; R и r – радиусы рабочих поверхностей, м
Для конусной фрикционной предохранительной муфты (рис. 6.2), у ко-
торой рабочие поверхности имеют коническую форму, расчетное значение крутящего момента ТМ (Нм) определяется по формуле:
ТМ = Fпрf0 · 0,5Dсрsinα, |
(6.3) |
где Dср – средний диаметр контакта фрикционных поверхностей, м;– половина угла конуса, град.
Рис. 6.2. Схема конусной фрикционной муфты: α – угол наклона конуса, град;
Rср – средний радиус рабочих поверхностей, м; b – ширина поверхности трения, м
Из анализа (6.2) и (6.3) видно, что точность срабатывания муфты определяется стабильностью коэффициента трения на рабочих поверхностях. На фактическое значение коэффициента трения f0 оказывают влияние такие факторы,

33
как состояние и температура поверхностей трения, скорость скольжения, удельное давление на поверхностях трения и др.
3. Оборудование и приборы
Экспериментальная установка ДМ 40.
Набор предохранительных муфт. Штангенциркуль. Тарировочное приспособление, включающее рычаг и грузы. Индикатор часового типа (или осциллограф с усилителем).
3.1. Описание экспериментальной установки ДМ 40
Установка (рис. 6.3) состоит из электродвигателя 6, клиноременной передачи 30, натяжение которой осуществляется роликом 1, одноступенчатого зубчатого цилиндрического редуктора 18 (шестерня 29 и колесо 20), ведомый вал 21 установлен на подшипниках, смонтированных внутри колеса 20. Нагрузка ведомого вала 21 осуществляется колодочным тормозом 17.
Рис. 6.3. Установка ДМ40
Рычаги тормоза 17 соединены штангой 12 с обоймой 16, сидящей на подшипниках ведомого вала, что позволяет тормозной системе свободно качаться вокруг оси вала. Тормоз снабжен гидравлическим демпфером 7.
34
Штанга через призму 9 опирается на измерительную пружину 8, прогиб которой измеряется индикатором 3. Балансировочная система тормоза 17 может быть зафиксирована при помощи винтового устройства 2.
На ведомом валу 21 наклеены тензодатчики 19, выводы которых вынесены на торец вала. Токосъемник 10 соединен с ведомым валом компенсирующей муфтой 11. Исследуемые муфты 26, представляющие отдельные быстросъемные узлы, одеваются на выступающий конец ведомого вала 21 и закрепляются в осевом направлении. При этом ведущая полумуфта соединяется с колесом 20 через подушку 28. Каждая конструкция муфты позволяет производить регулировку силы сжатия полумуфты и ее замер путем определения длины предварительно протарированной пружины 27.
Все узлы установки смонтированы на станине 15. На станине установлен защитный кожух 31 с пультом управления 5. Выступающий конец муфты закрыт прозрачным откидывающимся колпачком 4.
Установка подключается к сети при помощи шнура 13 и имеет болт заземления 14.
Тарировочное приспособление состоит из рычага 23 и подвески с четырьмя грузами 24. Приспособление одевается на ведомый вал и закрепляется винтом 22.
3.2. Техническая характеристика испытываемых муфт
Дисковая фрикционная предохранительная муфта:
средний диаметр ( диаметр трения) – Dср = 65 мм; пара трения – сталь – азбофрикционный материал; коэффициент трения – f0 = 0.3;
количество трущихся поверхностей – z = 5.
Конусная фрикционная предохранительная муфта:
средний диаметр контакта фрикционных поверхностей – Dср = 65 мм; длина образующей контакта – 20 мм; половина угла конуса – = 200; пара трения – сталь – текстолит;
коэффициент трения – f0 = 0.2.
Номинальный момент срабатывания муфт – 10 Нм.
Номинальная скорость вращения вала муфт – 12 рад/с (115 мин-1). Способ нагружения – колодочным тормозом.
Замер крутящего момента на муфте – при помощи индикатора часового типа (или электротензометрический).
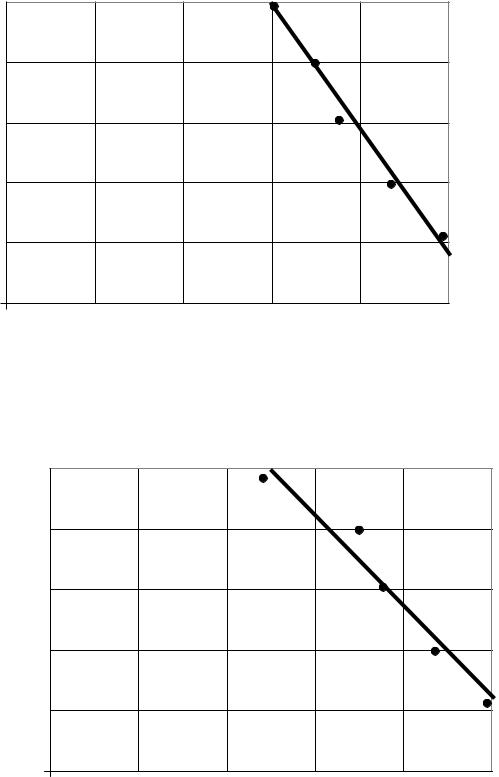
35
Н500
400
300
200
100
0
0 |
10 |
20 |
30 |
40 |
50 |
|
|
|
|
|
мм |
Рис. 6.4. Тарировочный график пружины фрикционной конусной муфты
Н500
400
300
200
100
0
|
|
|
|
|
мм |
0 |
10 |
20 |
30 |
40 |
50 |
Рис. 6.5. Тарировочный график пружины фрикционной дисковой муфты
36
Замер силы пружины муфты – по длине пружины с помощью тарировочного графика.
Привод – от электродвигателя 4А71В. 6 исп. 100, мощностью Рдв = 1,55 кВт, частота вращения вала электродвигателя nдв = 940 мин –1.
4.Порядок выполнения работы
4.1.Разобрать и собрать каждую муфту, изучить конструкцию, отметить число трущихся поверхностей.
4.2.Рычаг тарировочного приспособления установить на ведомый вал установки. Ведомый вал зафиксировать колодочным тормозом, чтобы не проворачивался. Поочередно навешивая грузы, определить соотношение величины создаваемого на валу крутящего момента и показаний на индикаторе (динамометрическом кольце). Построить тарировочный график.
4.3.Для заданного преподавателем наибольшего в серии опытов ТМ вычислить расчетное значение Fпр (формула 6.2 и 6.3) и округлить его.
4.4.Наметить серию из 3…5 опытов с разным усилием пружины, состав-
ляющим, например, 100, 80, 60, 40… процентов от Fпр и по тарировочному графику найти соответствующие длины пружины (рис. 6.4, рис. 6.5).
4.5.Муфту в сборе установить на ведомый вал, обеспечив точное вхождение штифтов в отверстия резинового диска.
4.6.Установить требуемую для данного опыта длину пружины.
4.7.Закрыв щиток, включить электродвигатель. Создать перегрузку тормозом, замкнув колодки до полной остановки тормозного шкива; зафиксировать показания индикатора. Снять перегрузку, опустив колодки. Повторить необходимое число раз опыт, создавая и снимая перегрузку.
4.8.Выключить электродвигатель.
4.9.Провести опыт по п. 6, 7, 8 для другого значения длины пружины.
4.10.По экспериментальным данным вычислить коэффициент точности срабатывания для каждого усилия пружины (формула 6.1). Определить значения коэффициентов трения для каждого опыта, зависимости (6.2) и (6.3).
5.Оформление отчета
5.1.Титульный лист по образцу. Цель работы. Общие сведения.
5.2. Описание и схема (рис. 6.3) экспериментальной установки ДМ 40.
5.3.Техническая характеристика испытываемых муфт.
5.4.Тарировочный график по данным тарировки грузами.
5.5.Расчеты осевого усилия пружины, крутящих моментов, коэффициента точности срабатывания муфт, итоги которых свести в табл. 6.1.
37
|
|
|
|
|
Таблица 6.1 |
|
Осевое |
Длина |
Показания |
Крутящий |
Коэффи- |
|
Коэффи- |
усилие |
пружины, |
динамомет- |
момент |
циент |
|
циент |
пружины |
мм |
рического |
ТМ, Нм |
трения |
|
точности |
Fпр, Н |
|
кольца |
|
f0 |
|
срабатывания |
|
|
|
|
|
|
муфты КТ |
0,4Fпр |
|
|
|
|
|
|
|
|
|
|
|
|
|
0,6Fпр |
|
|
|
|
|
|
|
|
|
|
|
|
|
0,8Fпр |
|
|
|
|
|
|
|
|
|
|
|
|
|
Fпр |
|
|
|
|
|
|
|
|
|
|
|
|
|
5.6. Вывод по закрепленной на лабораторной работе теме с обоснованием результатов расчетов и испытаний.
6.Контрольные вопросы
6.1.Назначение предохранительных муфт. Принцип работы фрикционных предохранительных муфт.
6.2.Какое влияние на точность срабатывания исследованных муфт оказало изменение давления на поверхностях трения (изменение усилия пружины)?
6.3.Как изменялся коэффициент трения в зависимости от давления на поверхностях трения?
6.4.При каком давлении коэффициент трения наиболее стабильный?
6.5.Какие имеются конструктивные решения, повышающие точность срабатывания предохранительных муфт?
ПРАВИЛА по технике безопасности во время работы на установке
для исследования предохранительных муфт
1.Использовать средства защиты от поражения электрическим током (резиновый коврик).
2.Испытания производить только при наличии защитного кожуха на
муфте.
3.При смене муфт установка должна быть отключена от электросети.
4.Не останавливать установку руками или какими-либо предметами.
5.При обнаружении неисправности в работе установки отключить ее от электросети и сообщить преподавателю или учебному мастеру.
38
ЛАБОРАТОРНАЯ РАБОТА № 7
ИЗУЧЕНИЕ МЕХАНИЧЕСКИХ ПРИВОДОВ
1. Цель работы
Ознакомление с назначением и конструкцией механических приводов и их узлов
2. Общие сведения
Механический привод – устройство, предназначенное для передачи мощности от источника движения к рабочим органам машины. При этом в большинстве случаев привод изменяет параметры движения (как правило, скорость уменьшает, а вращающий момент увеличивает).
В приводах находят применение передачи трением (ременные, фрикционные) и зацеплением (зубчатые, червячные, цепные, винтовые).
Ременную передачу обычно устанавливают между электродвигателем и редуктором (поскольку там наименьший крутящий момент, что необходимо для предотвращения существенного проскальзывания ремня).
По форме поперечного сечения ремни делят на плоские, круглые, клиновые и поликлиновые.
Наибольшее применение получили ременные передачи с ремнем клинового сечения. Клиновые ремни изготавливают семи стандартных сечений. Выбор сечения ремня производят в зависимости от передаваемой мощности и частоты вращения ведущего шкива.
Цепную передачу в приводах в большинстве случаев устанавливают между редуктором и рабочим органом машины (поскольку там наименьшая скорость, что необходимо для уменьшения износа цепи).
Для передачи движения в приводах применяют роликовые, втулочные и зубчатые цепи.
Широкое применение получили передачи с роликовой цепью. Цепи стандартизированы, выбор цепи производят по расчетной величине шага роликов.
Для соединения валов с неточно совмещенными осями применяют компенсирующие муфты, которые компенсируют небольшие радиальные, осевые, угловые или комбинированные смещения валов передач друг относительно друга.
Муфты для механических приводов подбирают по диаметру вала и расчетному вращающему моменту.
Приводы могут быть с постоянной и переменной скоростью. Для обеспечения изменения скорости вместо редуктора устанавливают коробку скоростей или вариатор.

39
Вариатор позволяет плавно (бесступенчато) изменять скорость рабочих органов машины.
Механический привод монтируется на плите или сварной раме, к которым предъявляются требования жесткости и точности взаимного расположения присоединительных поверхностей.
3. Описание конструкции приводов
На рис. 7.1 представлена кинематическая схема привода с червячным редуктором. Вращающий момент от электродвигателя 1 через клиноременную передачу 2 передаѐтся на ведущий вал редуктора 3. С выходного вала редуктора через соединительную муфту 4 момент передаѐтся на вал 5, на котором установлена ведущая звездочка транспортѐра (рабочий орган машины). Механический привод смонтирован на сварной раме. Для удобства монтажа и смены ремня, а также его натяжения предусмотрена возможность изменения межосевого расстояния, что достигается установкой двигателя 1 на салазках.
М |
|
|
5 |
1 |
4 |
3 |
2
Рис. 7.1. Схема привода с червячным редуктором
На рис. 7.2 представлена кинематическая схема привода с цилиндрическим зубчатым редуктором. От электродвигателя 1 вращающий момент передаѐтся через соединительную муфту 2 на входной вал редуктора 3. С выходного вала редуктора момент передаѐтся через цепную передачу 4 на приводной барабан конвейера 5 (рабочий орган машины).

40
3
4
1 2
5
М
Рис. 7.2. Схема привода с цилиндрическим редуктором
4.Порядок выполнения работы
4.1.Ознакомиться с типами редукторов, применѐнных в приводах, обратив внимание на число ступеней и расположение валов.
Вращая ведущие валы определить передаточные числа редукторов:
u1 = |
n1 |
, |
(7.1) |
|
n2 |
||||
|
|
|
где n1 – частота вращения входного вала редуктора, n2 – частота вращения выходного вала редуктора.
Пояснение: Необходимо заметить в каком положении находится выходной вал (например, по шпоночному пазу), затем следует вращать входной вал до тех пор, пока выходной сделает один полный оборот.
4.2. Изучить клиноременную передачу (рис. 7.1).
Определить сечение ремня, замерив размеры W, Т0 (табл. 7.1). Рассчитать передаточное число ременной передачи:
u2 = |
D2 |
, |
(7.2) |
D (1 ) |
|||
|
1 |
|
|
где D2 – диаметр ведомого шкива, D1 – диаметр ведущего шкива,
ε – коэффициент скольжения (0,01…0,02).