
4886
.pdfМинистерство образования и науки Российской Федерации Федеральное государственное бюджетное образовательное учреждение высшего образования
«Воронежский государственный лесотехнический университет имени Г.Ф. Морозова»
ДЕТАЛИ МАШИН
методические указания к лабораторным работам для студентов по направлению подготовки бакалавра
15.03.02 - «Технологические машины и оборудование»
ВОРОНЕЖ 2015
- 2 -
УДК 621.81+621.86
Детали машин [Текст]: методические указания к лабораторным работам для студентов по направлению подготовки бакалавра 15.03.02 - «Технологические машины и оборудование»/ В. В. Ткачев, Р. Г. Боровиков, П. Н. Щеблыкин; М- во образования и науки РФ, ФГБОУ ВО «ВГЛТУ». – Воронеж, 2015. – 44 с.
Печатается по решению учебно-методической комиссии по направлению «Технологические машины и оборудование» ФГБОУ ВО «ВГЛТУ» (протокол № 4 от 28 мая 2015 г.)
Рецензент: заведующий кафедрой эксплуатации машинно-тракторного парка ФГБОУ ВПО «Воронежский государственный аграрный университет имени императора Петра I», д-р техн. наук, Е.В. Пухов
Виталий Викторович Ткачев Роман Геннадьевич Боровиков Павел Николаевич Щеблыкин
ДЕТАЛИ МАШИН
методические указания к лабораторным работам для студентов по направлению подготовки бакалавра
15.03.02 - «Технологические машины и оборудование»
- 3 -
ЛАБОРАТОРНАЯ РАБОТА № 1
ИЗУЧЕНИЕ РЕЗЬБОВЫХ КРЕПЕЖНЫХ ИЗДЕЛИЙ
1. Цель работы
Ознакомление с резьбовыми соединениями, измерение и расчет их параметров, выбор по ГОСТу.
2. Общие сведения
Резьбовыми соединениями называются разъемные соединения, неподвижность которых обеспечивается за счет крепежных изделий, имеющих резьбу.
Резьбы – это выступы, образованные на основной поверхности детали и расположенные по винтовой линии с постоянным шагом.
По форме поверхности различают цилиндрические и конические резьбы. Наибольшее распространение получила цилиндрическая резьба.
Резьба, нанесенная на наружную поверхность детали, называется наружной, а на внутреннюю – внутренней.
Профиль резьбы – контур сечения резьбы в плоскости, которая проходит через ось основной поверхности. По форме профиля резьбы делятся на треугольные, прямоугольные, круглые и трапецеидальные. По направлению винтовой линии – на правую и левую резьбы. По числу заходов – на однозаходную и многозаходную (двух и более заходов) резьбы. Все крепежные резьбы однозаходные.
Геометрические параметры цилиндрической резьбы (рис. 1.1):
d – наружный диаметр резьбы – диаметр цилиндра, описанного вокруг вершин наружной резьбы (винта), мм;
d1 – внутренний диаметр резьбы – диаметр цилиндра, описанного вокруг вершин внутренней резьбы, мм;
d2 – средний диаметр резьбы – диаметр воображаемого цилиндра, на поверхности которого ширина витков и ширина впадин резьбы совпадает, мм;
p – шаг – расстояние между параллельными сторонами профиля двух соседних витков, измеренное вдоль оси, мм;
n – число заходов; p1 – ход резьбы, мм;
p1 p n |
(1.1) |
Н1 = h – рабочая высота профиля, на которой происходит соприкосновение витков винта и гайки, мм;
α – угол профиля; γ – угол подъема линии:
tg |
p1 |
|
p n |
(1.2) |
d 2 |
d 2 |
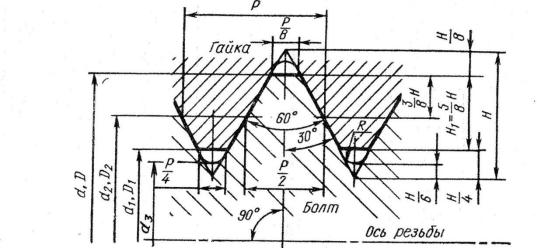
- 4 -
d - наружный диаметр наружной резьбы (болта); D - наружный диаметр внутренней резьбы (гайки); d2 – средний диаметр болта;
D2 – средний диаметр гайки; d1 - внутренний диаметр болта; D1- внутренний диаметр гайки;
d3 - внутренний диаметр болта под впадины; P – шаг резьбы;
H – высота исходного треугольника;
R – номинальный радиус закругления впадин болта; Н1 – рабочая высота профиля.
Рис. 1.1. Геометрические параметры метрической резьбы
Для соединения деталей применяют болты, винты, шпильки и гайки (рис.
1.2).
Болт представляет собой стержень с резьбой для гайки на одном конце и головкой на другом (рис. 1.2, а).
Винт – это стержень с головкой на одном конце и резьбой на другом, которой он непосредственно вкручивается в соединяемые детали (рис. 1.2, б).
Шпилька – стержень с резьбой на обоих концах, одним концом она ввинчивается в соединяемые детали, а на другой конец навинчивается гайка (рис. 1.2, в).
Гайка – деталь с резьбовым отверстием, которая навинчивается на болт или шпильку.
Винты и шпильки надо применять в тех случаях, когда постановка болта невозможна. При частом монтаже и демонтаже деталей следует соединять их болтами или шпильками.
Для уменьшения смятия под гайку или головку винта ставят подкладную шайбу. Кроме подкладных шайб используют предохранители от самоотвинчивания (гаечные замки), так как отсутствие таковых может привести к аварии. Применяют три основных способа стопорения (рис. 1.3):
– повышают и стабилизируют трение в резьбе за счет постановки пружинной шайбы, контргайки и др. элементов (рис. 1.3, а, б);
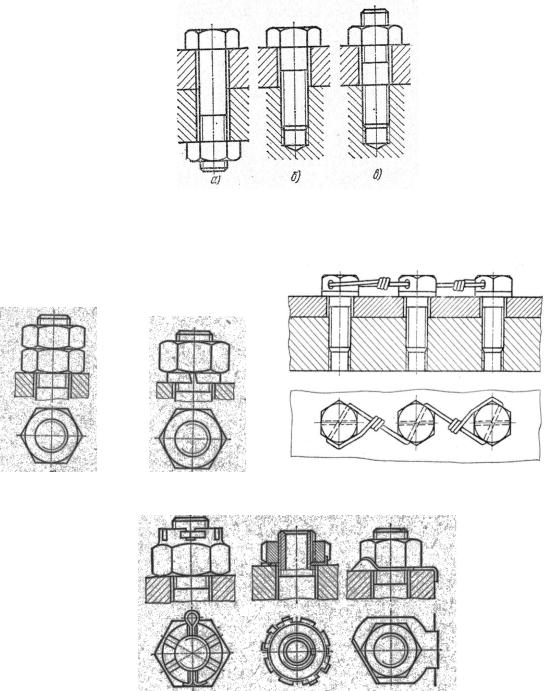
-5 -
–прошивают группу винтов проволокой (рис. 1.3, в);
–гайку жестко крепят с деталью с помощью шплинта, специальной шайбы или планки (рис. 1.3, г, д, е).
Рис. 1.2. Основные типы резьбовых соединений: а) болт; б) винт; в) шпилька
а) |
б) |
в) |
г) |
д) |
е) |
Рис. 1.3. Способы стопорения гаек.
3.Мерительный инструмент
3.1.Штангенциркуль, линейка.
-6 -
4.Порядок выполнения работы
4.1.Ознакомиться с общими сведениями о резьбовых соединениях.
4.2.Измерить наружный диаметр резьбы винта (болта) d (мм) и длину нарезной его части L (мм).
4.3.Подсчитать количество витков резьбы винта (болта) Z.
4.4.Измерить размер под ключ головки винта (болта) D (мм).
4.5.Измерить размер под ключ гайки D1 (мм) и ее высоту H (мм).
4.6.Подсчитать количество витков резьбы гайки Z1.
4.7.Определить шаг резьбы винта (болта)
p = L/Z (мм). |
(1.3) |
4.8. Вычислить рабочую высоту профиля резьбы винта (болта) |
|
h = 0,54·p (мм). |
(1.4) |
4.9. Вычислить внутренний диаметр резьбы винта (болта) |
|
d1 = d – 2·h (мм). |
(1.5) |
4.10. Определить средний диаметр резьбы винта (болта) |
|
d2 = d – 0,325·p (мм). |
(1.6) |
4.11. Вычислить площадь поперечного сечения винта (болта) |
|
S = π · d12/ 4 (мм2). |
(1.7) |
4.12. Рассчитать угол подъема резьбы винта (болта) |
|
tgγ = p/(π·d2) → γ = arctg p/(π·d2). |
(1.8) |
4.13.Для контроля правильности измерения размеров и определения параметров резьбы измерить шаг и профиль резьбы с помощью резьбомера.
4.14.Определить тип винта (болта) и гайки по ГОСТу и записать их условные обозначения [4].
4.15.Провести проверку прочности напряженного болтового соединения по исходным данным табл. 1.1 согласно указанному преподавателем варианту.
Условие прочности для болтового соединения [1], установленного без
зазора, определяется для расчетного напряжения на растяжение σр (МПа) по формуле:
σр = 1,3 Fр/ (π·d12/4) ≤ [σр], |
(1.9) |
где Fр – расчетная нагрузка на один болт, Н; |
|
d1 – внутренний диаметр резьбы винта (болта), мм, |
|
[σр] – допускаемое напряжение на растяжение, МПа. |
|
Расчетная нагрузка на болт рассчитывается: |
|
Fр = [1,3 К · (1 – Х) + Х] F, |
(1.10) |
где К – коэффициент запаса; |
|
Х – коэффициент внешней нагрузки; |
|
F – нагрузка, приходящаяся на один болт, Н. |
|
Допускаемое напряжение на растяжение находится по формуле: |
|
[σр] = σm/[n], |
(1.11) |
где σm – предел текучести материала, МПа; |
|
[n] – коэффициент запаса прочности. |
|
- 7 -
Таблица 1.1
Исходные данные вариантов заданий
№ |
|
|
|
|
|
|
σm, |
|
вариан- |
d, мм |
р, мм |
Материал |
F, Н |
Х |
К |
МПа |
[n] |
та |
|
|
|
|
|
|
|
|
1 |
10 |
1,5 |
Сталь 3 |
2000 |
0,3 |
1,35 |
190 |
3,5 |
2 |
12 |
1,75 |
Сталь 5 |
3500 |
0,4 |
1,3 |
200 |
2,5 |
3 |
16 |
2,5 |
Сталь 3 |
2500 |
0,35 |
1,25 |
190 |
3,0 |
4 |
20 |
2,5 |
Сталь 5 |
4500 |
0,4 |
1,3 |
200 |
2,0 |
5 |
24 |
3,0 |
Сталь 5 |
7000 |
0,35 |
1,25 |
200 |
2,0 |
5.Оформление отчета
5.1.Титульный лист по образцу. Цель работы. Общие сведения.
5.2. Данные измерений и подсчетов, результаты которых свести в табл. 1.2.
|
|
|
|
|
|
|
|
|
|
|
|
|
|
|
|
Таблица 1.2 |
||
|
Наружный |
|
Кол-во |
|
|
|
|
|
|
|
|
Длина |
Размер |
|
||||
Детали |
|
диаметр |
|
витков |
|
|
|
Высота |
|
|
нарезной |
|
под |
|
||||
|
|
резьбы |
|
резьбы |
|
|
|
|
|
|
|
|
части |
ключ |
|
|||
Винт |
|
|
|
|
|
|
|
|
|
|
|
|
|
|
|
|
|
|
(болт) |
d = |
мм |
Z = |
|
|
|
|
* |
|
|
L = |
мм |
D = |
мм |
|
|||
Гайка |
|
|
* |
Z1 = |
|
|
Н = |
мм |
|
|
* |
|
D1 = |
мм |
|
|||
5.3. Результаты расчетов параметров для винта (болта) свести в табл. 1.3. |
||||||||||||||||||
|
|
|
|
|
|
|
|
|
|
|
|
|
|
|
|
Таблица 1.3 |
||
Шаг |
|
Рабочая |
|
Внутренний |
|
Средний |
|
Угол |
Площадь |
|
||||||||
резьбы |
|
высота |
|
диаметр |
|
|
диаметр |
|
подъема |
поперечного |
|
|||||||
|
|
профиля |
|
резьбы |
|
|
резьбы |
|
резьбы |
сечения |
|
|||||||
|
|
резьбы |
|
|
|
|
|
|
|
|
|
|
|
|
|
|
|
|
р = мм |
h = |
мм |
D1 = |
мм |
d2 = |
мм |
γ = |
º |
S = |
мм2 |
|
5.4. Расчет прочности болтового соединения согласно варианту, исходные данные выписать в виде табл. 1.4.
|
|
|
|
|
|
Таблица 1.4 |
|
d, мм |
р, мм |
F, Н |
Х |
К |
σm, МПа |
[n] |
|
|
|
|
|
|
|
|
|
6.Контрольные вопросы
6.1.Что собой представляют резьбовые соединения?
6.2.Различие между болтом, винтом, шпилькой.
6.3.Основные способы стопорения.
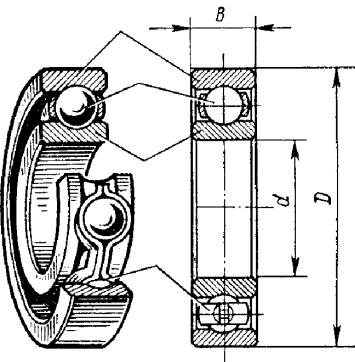
- 8 -
ЛАБОРАТОРНАЯ РАБОТА № 2
ИЗУЧЕНИЕ ПОДШИПНИКОВ КАЧЕНИЯ И УПЛОТНЕНИЙ ПОДШИПНИКОВЫХ УЗЛОВ
1. Цель работы
Ознакомление с различными типами подшипников качения, системой их условных обозначений (маркировкой), а также с основными типами уплотнений подшипниковых узлов.
2. Общие сведения
Подшипники качения – это опоры валов или осей, содержание элементы качения и работающие на основе трения качения.
В большинстве конструкций подшипник качения состоит из наружного кольца 1, внутреннего кольца 2, тел качения 3 и сепаратора 4 (рис.2.1).
1
3
2
4
Рис. 2.1. Схема подшипника качения
Сепаратор предохраняет тела качения от соприкосновения друг с другом, способствует равномерному распределению нагрузки между ними и вследствие этого уменьшает потери на трение.
Преимущества подшипников качения (по сравнению с подшипниками скольжения):
малый коэффициент трения: f = 0,0015…0,006; незначительный расход смазки;

- 9 -
малое сопротивление при разгоне; меньшие габариты в длину;
большая надежность при заедании; простота обслуживания; снижение стоимости производства за счет массового изготовления.
Недостатки подшипников качения:
плохое восприятие ударных и вибрационных нагрузок; малый срок службы при больших частотах вращения вала; большие габариты по диаметру.
Подшипники качения классифицируют по следующим признакам.
По форме тел качения их подразделяют на шариковые и роликовые. Роликовые по форме роликов делятся на цилиндрические (рис. 2.2, а), ко-
нические (рис. 2.2, б), бочкообразные (рис. 2.2, в), игольчатые (рис. 2.2, г) и витые (рис. 2.2, д).
По направлению действия воспринимаемых сил (нагрузок) подшиники разделяют на:
радиальные (воспринимающие преимущественно радиальные нагрузки, т.е. нагрузки, действующие перпендикулярно оси вращения подшипника);
радиально-упорные (воспринимающие одновременно действующие радиальные и осевые нагрузки, но радиальные в большей степени);
упорно-радиальные (воспринимающие одновременно действующие осевые и радиальные нагрузки, но осевые в большей степени);
упорные (воспринимающие осевые нагрузки, т.е. действующие вдоль геометрической оси вала).
По способности самоустановки подшипники качения бывают самоустанавливающиеся и несамоустанавливающиеся.
У самоустанавливающихся подшипников одно из колец может поворачиваться независимо от другого.
а) |
б) |
в) |
г) |
|
д) |
|
Рис. 2.2. Формы роликов |
|
По числу рядов тел качения (расположенные по ширине) их делят на однорядные, двухрядные, четырехрядные и многорядные.
Для маркировки, указаний на чертежах и в спецификациях, применения в технической литературе подшипники снабжают условные обозначения.
Основное условное обозначение подшипника может содержать до семи цифр. Цифры считают справа налево.
- 10 -
Первая и вторая цифры указывают внутренний диаметр подшипника. Эти цифры соответствуют частному от деления на 5 внутреннего диамет-
ра подшипника (при диметре от 20 до 495 мм).
Однако, если значение диаметра менее 20 мм., тогда обозначение соответствует следующим значения: «00» - 10 мм., «01» - 12 мм., «02» - 15 мм., «03» - 17 мм. Если же диаметр менее 10 мм, тогда в обозначении указывается фактическое значение диаметра.
Третья цифра обозначает серию подшипников по диаметру: особо легкая серия – 1; легкая серия – 2; средняя серия – 3; тяжелая серия – 4; легкая широкая серия – 5; средняя широкая – 6 и т. д.
Четвертая цифра указывает тип подшипника:
0– радиальный шариковый;
1– радиальный шариковый сферический;
2– радиальный с короткими цилиндрическими роликами;
3– радиальный роликовый двухрядный сферический;
4– радиальный роликовый с длинными игольчатыми роликами;
5– радиальный роликовый с витыми роликами;
6– радиально-упорный шариковый;
7– радиально-упорный роликовый конический;
8– упорный шариковый;
9 – упорный роликовый.
Пятая или пятая и шестая цифры, вводимые не для всех подшипников, обозначают конструктивные особенности подшипников, например, наличие стопорной канавки на наружном кольце, наличие встроенных уплотнений и т. п.
Седьмая цифра обозначает серию подшипника по ширине. Промышленность изготовляет подшипники качения пяти классов точно-
сти: 0; 6; 5; 4; 2. Обозначения даны в порядке повышения точности, определяемой допусками на изготовление, а также нормами плавности вращения. Класс точности указывается слева от обозначения подшипников через тире.
Нули, стоящие в условном обозначении левее последней цифры, не указывают.
Например, подшипник с условным обозначением 207 имеет внутренний диаметр 35 мм. (07х5=35 мм.), легкой серии по диаметру (цифра 2), радиальный шариковый (поскольку предполагается, что четвертая цифра 0).
Подшипники качения в целях предохранения от загрязнений извне и для предотвращения вытекания смазки снабжают уплотняющими устройствами.
Уплотнения подшипниковых узлов делятся на следующие основные типы:
–контактные (манжетные (рис. 2.3, а), войлочные (рис. 2.3, б), применяемые при низких и средних скоростях. Основное достоинство этих уплотнений – простота конструкции и дешевизна изготовления;
–лабиринтные (рис. 2.3, в, г) и щелевые (рис. 2.3, д, е), применяемые в неограниченном диапазоне скоростей, осуществляющие защиту благодаря со-