
4826
.pdf
|
|
|
|
|
|
|
|
Расчёт скорости |
|
|
31 |
||
|
|
|
|
|
|
Расчёт скорости |
|
Расчёт скорости |
|||||
|
|
|
|
|
|
|
подачи по |
|
|
||||
|
|
|
|
|
|
подачи по |
|
|
подачи по заданной |
|
|||
|
|
|
|
|
|
|
работоспособности |
|
|
||||
|
|
|
|
|
|
мощности резания |
|
|
шероховатости |
|
|||
Например, |
в |
отношении |
|
|
инструмента |
|
|
||||||
|
|
|
|
|
|
||||||||
|
|
|
|
|
|
|
|
||||||
|
|
|
|
|
|
|
|
||||||
модуля |
для |
расчета |
величин |
|
|
|
|
|
|
|
|
||
|
|
|
Прогнозирование |
|
|
Расчёт мощности |
|
||||||
мощности резания и скорости |
|
Расчёт сил резания |
|
качества |
|
|
резания |
|
|||||
|
|
|
обработки |
|
|
|
|
||||||
подачи |
(который |
обычно |
|
|
|
|
|
|
|
|
|||
Рис. 9.12. Интерфейс модуля для выбора режима |
|||||||||||||
используют |
для |
вычисления |
|||||||||||
|
|
|
резания |
|
|
||||||||
величин |
мощности |
привода |
|
|
|
|
|
|
|
|
главного движения и скорости подачи, а также можно применить для определения загрузки установленных на станках двигателей) использовали
исходные данные: U – скорость движения подачи, |
м/мин; |
fп - площадь |
|||||||
поперечного сечения срезаемого слоя, мм2; а |
– |
общий |
поправочный |
||||||
|
|
|
|
|
попр |
|
|
|
|
множитель; aср – средняя толщина срезаемого слоя, мм. |
|
|
|||||||
|
|
Табл. 9.4. Исходные данные расчёта мощности резания |
|
|
|||||
|
№ |
Входные величины |
Расчётные зависимости |
|
Выходные данные |
|
|||
|
1 |
U |
V 1C fп |
U |
|
|
|
|
|
|
2 |
fп |
60 |
|
|
N К V1С , Вт |
|
||
|
3 |
апопр. |
K Ктабл. апопр |
|
|
|
|
||
|
|
|
|
|
|
|
|
||
|
4 |
аср. |
КТ f (aср) |
|
|
|
|
||
|
|
|
|
|
|
|
|
|
|
Рис.9.13. Пользовательский интерфейс модуля для определения величины мощности резания
Интерфейс модуля для расчета мощности резания представлен на рис. 9.13.
В отношении модуля для расчета величин сил резания, который вычисляет касательную силу Fx, нормальную Fz, боковую Fy, силу Fs, действующую по направлению подачи, и силу Fn, действующую нормально к подаче (эти данные можно применить при проектировании режущего инструмента, механизма подачи, дереворежущего станка), использовались исходные данные, приведенные в табл.9.5.
Табл. 9.5. Исходные данные для расчёта сил резания
№ |
Входные величины |
Расчётные зависимости |
Выходные данные |
|||
1 |
N |
|
|
|
|
|
2 |
Z |
|
|
|
|
|
3 |
i |
Zp |
l |
Fxц N /Vср |
||
4 |
Vср. |
|
|
Fx(p.x.)=2Fxu |
||
f (Z ) |
||||||
|
||||||
5 |
l |
|
Fxср.=Fx(p.x.) /iZр |
|||
|
|
|
||||
7 |
aср |
m f (aср, ар) f ( ) |
Fzcp Fxcp m |
|||
8 |
|
Fzц Fxц m |
||||
|
|
|
||||
9 |
aр |
|
|
|
|

|
|
|
|
|
|
|
|
|
|
|
|
|
|
|
|
|
|
|
|
32 |
N – мощность резания, Вт; Z – число |
|
|
|
|
|
|
|
|
|
|
||||||||||
режущих элементов инструмента, шт.; |
|
|
|
|
|
|
|
|
|
|
||||||||||
i – число установленных инструментов, |
|
|
|
|
|
|
|
|
|
|
||||||||||
шт.; - угол резания, град; aр – рабочий |
|
|
|
|
|
|
|
|
|
|
||||||||||
кинематический задний угол, град. |
|
|
|
|
|
|
|
|
|
|
|
|||||||||
Интерфейс |
модуля |
расчёта |
сил |
|
|
|
|
|
|
|
|
|
|
|||||||
резания представлен на рис. 9.14. По |
|
|
|
|
|
|
|
|
|
|
||||||||||
данной программе можно также: |
|
|
|
|
|
|
|
|
|
|
||||||||||
прогнозировать |
качество |
|
станочной |
|
|
|
|
|
|
|
|
|
|
|||||||
обработки |
резанием |
по |
исходным |
|
|
|
|
|
|
|
|
|
|
|||||||
условиям |
обработки; |
|
вычислять |
|
Рис. 9.14. Пользовательский интерфейс |
|||||||||||||||
наибольшую |
допустимую |
величину |
|
|||||||||||||||||
|
модуля для расчета величин сил резания |
|||||||||||||||||||
скорости |
подачи, |
|
исходя |
из |
|
|
|
|
|
|
|
|
|
|
||||||
максимальной работоспособности режущего инструмента; рассчитывать |
||||||||||||||||||||
наибольшую допустимую величину скорости подачи по условию полного |
||||||||||||||||||||
использования заданной мощности движения главного привода; определять |
||||||||||||||||||||
наибольшую допустимую величину скорости подачи для получения в |
||||||||||||||||||||
дальнейшем необходимого уровня качества обработки. |
|
|
|
|
|
|
||||||||||||||
Современные инженерные методики расчета резания древесины |
||||||||||||||||||||
базируются на результатах экспериментальных исследований. В качестве |
||||||||||||||||||||
основных справочных материалов используют результаты наиболее полных |
||||||||||||||||||||
авторитетных работ по конкретным процессам резания. Различие между |
||||||||||||||||||||
условиями расчета и условиями базового эксперимента учитывают путем |
||||||||||||||||||||
применения системы экспериментально установленных значений |
||||||||||||||||||||
поправочных множителей. |
|
|
|
|
|
|
|
|
|
|
|
|
|
|
||||||
Значения поправочных множителей найдены по результатам |
||||||||||||||||||||
экспериментов. Варьированием на ЭВМ с помощью разработанных |
||||||||||||||||||||
алгоритмов и программы расчета интенсивных режимов деления древесины |
||||||||||||||||||||
для |
удобства |
пользователей |
впервые |
|
разработаны |
номограммы |
для |
|||||||||||||
определения основных режимов резания древесины мягких лиственных |
||||||||||||||||||||
пород. Одна из номограмм приведена на рис. 9.16. |
|
|
|
|
|
|
|
|||||||||||||
Исследованы |
основные |
|
|
|
|
|
|
|
|
|
|
|
|
|||||||
факторы, |
|
определяющие |
|
Шероховатость поверхности, Rm, мкм |
|
|
|
|
|
|
|
|
|
|
||||||
эффективность |
проведения |
|
900 |
|
|
|
|
|
|
|
|
|
||||||||
|
750 |
|
|
|
|
|
|
|
|
|
||||||||||
технологического |
процесса |
|
|
|
|
|
|
|
|
|
|
|||||||||
|
600 |
|
|
|
|
|
|
|
|
|
||||||||||
деления |
древесины |
|
и |
|
его |
|
450 |
|
|
|
|
|
|
|
|
|
||||
оптимизации |
с |
применением |
|
300 |
|
|
|
|
|
|
|
|
|
|||||||
|
150 |
|
|
|
|
|
|
|
|
|
||||||||||
|
|
|
|
|
|
|
|
|
|
|
|
|
|
|
|
|
|
|
||
ЭВМ |
в |
целях |
минимизации |
|
0 |
|
|
|
|
|
|
|
|
|
||||||
|
|
|
|
|
|
|
|
|
|
|
|
|
|
|
|
|
|
|
|
|
энергоемкости |
процессов |
|
|
|
0 |
0,3 |
0,6 |
0,9 |
1,2 |
1,5 |
1,8 |
|
||||||||
|
|
|
|
|
|
|
|
|
|
|
|
|||||||||
резания |
и |
относительного |
|
|
|
|
|
Подача на зуб, Uz, мм |
|
|
|
|||||||||
|
|
|
|
|
|
|
|
|
|
|
|
|||||||||
объема |
образования |
|
отходов |
|
|
|
|
С разводом |
|
С плющением |
|
|
||||||||
древесины. |
|
Установлены |
|
Рис. 9.15. Графики зависимости показателя |
|
|||||||||||||||
допустимые |
значения |
подачи |
|
шероховатости обработанной поверхности от |
||||||||||||||||
на |
|
зуб, |
|
отвечающие |
|
|
|
|
подачи на зуб |
|
|
|
|

33
оптимальным режимам резания мягкой лиственной древесины (рис. 9.15). |
||||||||
|
|
Скорость подачи, м/мин |
|
|
||||
|
|
|
|
|
|
|
|
0,31 |
|
|
15 |
|
|
|
|
|
мм |
|
10 |
2 0 |
|
|
|
|
зуб, |
|
|
|
|
25 |
|
|
|
|
|
|
|
|
|
|
|
|
0,21 |
|
|
5 |
|
30 |
35 |
|
|
|
на |
|
|
|
|
|
|
|
||
|
|
3 |
|
40 |
45 |
|
0,11 |
|
|
|
|
|
|
50 55 |
Подача |
||
|
|
|
|
|
|
|
||
|
|
|
|
|
|
|
|
0,01 |
. |
181 |
|
|
|
|
|
|
|
шт |
|
|
|
|
|
|
|
|
156 |
|
|
1500 |
|
|
|
||
пилы, |
|
|
|
|
|
|||
131 |
|
1000 |
2000 |
|
4500 |
|
||
|
|
|
|
|||||
106 |
|
|
|
|
|
|
|
|
зубьев |
|
|
3000 |
6000 |
|
|||
|
|
|
|
|||||
81 |
|
|
|
|
|
|
||
|
|
|
|
|
|
|
||
56 |
|
|
|
|
|
|
|
|
Число |
|
|
|
|
|
|
|
|
31 |
|
|
|
|
|
|
|
|
6 |
|
|
|
|
|
|
|
|
|
|
|
|
|
|
|
|
|
|
|
|
Частота вращения, об/мин |
|
||||
Рис. 9.16. Номограмма для определения режимов пиления круглыми пилами |
По предлагаемым номограммам легко определить величины основных технологических параметров режимов проведения процессов деления и формообразования древесины мягких лиственных пород: показана оптимальная область по выбору скорости резания и рациональной скорости подачи при цилиндрическом фрезеровании, а также интенсивного режима деления древесины круглыми пилами.
Установлено, что оптимальная зона режимов при продольном делении древесины круглыми пилами и режущими дисками составляет от 0,3 до 1 мм. Практика показала неэффективность пил с зубьями одинакового профиля (с учетом оптимальных величин параметров инструментов для деления древесины различной плотности). Значительно большей производительности при той же потребляемой мощности можно добиться при использовании пил с комбинированными зубчатыми венцами с подрезающими зубьями.
Контрольные вопросы
1.Какова «объемная» формула расчета силы резания?
2.Из каких модулей состоит структурная схема программы расчета режима резания?
3.Что значит назначить рациональный режим резания древесины и древесных материалов?

34
4.Зависит ли шероховатость обработанной поверхности древесины от подачи на зуб?
5.Опишите как изменяется шероховатость обработанной поверхности для заданного процесса резания от скорости подачи, отметить какой из факторов оказывает наибольшее влияние на силу резания: порода древесины; влажность; толщина стружки; угловые характеристики инструмента; степень затупления инструмента?
Практическая работа №4
Исследование процесса обрабатываемости резанием древесины различных пород
Цель работы: изучить процесс пиления древесины различных пород на ленточном станке «Wood–Mizer» и дать оценку обрабатываемости древесины.
Теоретические положения и указания к выполнению
На процессе разрушения связей между частицами древесины сказывается концентрация напряжений в материале в зоне контакта режущей кромки и образца. Характер и величина концентрации возникающих напряжений предопределяется формой (профилем) и состоянием режущей кромки резца. Существенное влияние на характер разрушения материала оказывает также анизотропия древесины – ее волокнисто-слоистое строение. Наиболее ощутимо влияние волокон при продольном резании и резании в поперечном направлении в плоскости, перпендикулярной к волокнам. В обоих случаях разрушение древесины в значительной мере предопределяется направлением волокон. При резании же в поперечном направлении в плоскости, параллельной волокнам, в большей степени сказывается направление слоев древесины.
При движении резца передняя его грань, располагающаяся наклонно к плоскости резания, отгибает стружку, деформируя ее в различных направлениях и различными способами. Характер отгиба стружки зависит от ряда факторов: угла наклона передней грани к плоскости резания, состояния передней грани (ее шероховатости), направления волокон и слоев древесины. Стружкообразование, таким образом – сложный процесс, определяемый не только взаимодействием резца и образца, но и многими другими сопутствующими факторами. Виды и характер образования стружек в зависимости от сопутствующих стружкообразованию условий резания лучше всего проследить по отдельным стадиям самого процесса стружкообразования – его кинограмме.
Первая, начальная стадия стружкообразования одинакова для всех видов резания и не зависит от анизотропии древесины. Для этой стадии начального внедрения резца в древесину характерно упруго-пластическое ее деформирование. Проследим развитие отдельных фаз этой стадии. При этом
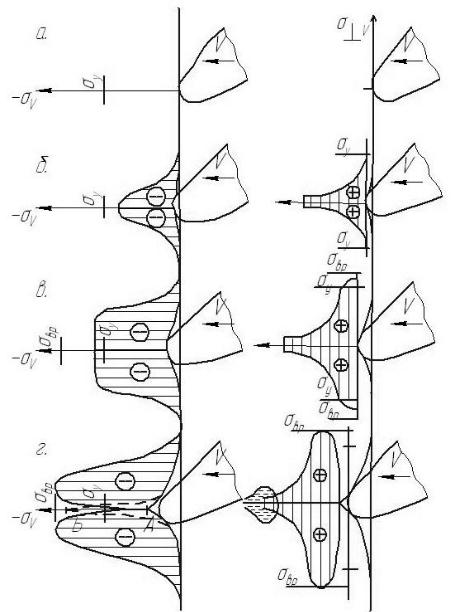
35
рассмотрим развитие нормальных напряжений в материале образца в двух направлениях: в направлении движения резца V и в направлении,
перпендикулярном ему и режущей кромке V .
Начинается стадия с касания резца и материала образца. В этой фазе (фаза а, рис. 10.1) напряжений в материале от воздействия резца еще нет.
Рисунок 10.1. Диаграмма нормальных напряжений отдельных фаз внедрения резца в древесину: а – в период касания; б – при упругом деформировании; в – при упругопластическом деформировании; г – при разрушении поверхностного слоя материала
Вторая фаза б характеризуется появлением нормальных напряжений сжатия V и нормальных напряжений растяжения V и вызванных этими
напряжениями упругих деформаций. Развитие упругих деформаций происходит до тех пор, пока не будет пройден предел упругости как в
36
направлении вектора скорости, так и в направлении, перпендикулярном ему. Таким образом, фаза б завершается достижением пределов упругости. Очевидно, что величина деформации материала образца может быть различной в зависимости от профиля и состояния режущей кромки резца, положения волокон древесины и других факторов, определяющих условия резания. Здесь мы не рассматриваем касательные напряжения и их влияние на деформирование материала образца, поскольку их роль в деформировании обычно не столь велика. Так как касательные напряжения, являются в какойто мере функцией нормальных напряжений, то, следовательно, имея эпюру нормальных напряжений, мы имеем картину распределения касательных напряжений.
Уже самое общее представление процесса воздействия резца на материал образца в начальной его стадии свидетельствует о наличии двухосного и фактически сложного напряженного состояния древесины в зоне ее контакта с резцом. При значительной длине режущей кромки, что практически имеет место в действительности при простых видах резания, рассматриваемое напряженное состояние можно считать плоским (в отличие от сложных видов резания, например пиления).
Третья фаза в — фаза развития упруго-пластических деформаций. Появляются они при превышении фактических напряжений в материале предела упругости. Для этой фазы характерно появление площадок пластичности (рис. 10.1), которые увеличиваются в размерах с ростом напряжений в материале. Это явление объясняется тем, что происходит перераспределение напряжений и, соответственно, деформаций; уменьшается доля упругих и возрастает доля пластических напряжений и деформаций. Однако разрушения в материале образца еще не происходят, поскольку напряжения в нем еще не достигли предела прочности. Как только напряжения достигнут предела прочности, произойдет разрушение (разрыв) частиц материала. В материале образца перед резцом появляется трещина. Эта, так называемая опережающая трещина возникает в некоторой точке А (рис. 10.1), в которой прежде всего будет превышен предел прочности. Появление трещины перед режущей кромкой является логическим завершающим этапом развития напряжений в материале в зоне взаимодействия резца и образца. Опережающая трещина появляется при любом направлении волокон древесины. Направление же ее развития определяется направлением волокон древесины.
То, что опережающая трещина появляется всегда в зоне режущей кромки, можно утверждать с уверенностью, но где она появляется — выше или ниже наиболее выступающей в направлении движения резца его точки
— это пока установить не представляется возможным. Тем более, как указывалось ранее, профиль режущей кромки резца, обычно принимаемый плавно скругленным по дуге окружности, в действительности может иметь значительное количество неопределенно расположенных выступов, вызывающих местные концентрации напряжений различной интенсивности в
37
материале образца. Поэтому нельзя заранее установить точную зону раздела древесины по отношению к режущей кромке резца. Но, как только трещина появилась, она сама становится чрезвычайно сильным концентратором напряжений. Далее трещина может развиваться выше, ниже или пойти вообще произвольно в зависимости от направления волокон и слоев древесины.
Развитие трещины, очевидно, будет наблюдаться до тех пор, пока суммарные напряжения в точке ее образования не станут меньше предела прочности (точка Б, рис. 10.1). Скорость разрушения материала древесины при образовании опережающей трещины весьма высока и, видимо, сравнима со скоростью распространения упругой деформации. Стадия внедрения резца в материал, таким образом, завершается появлением опережающей трещины.
При дальнейшем движении резца стружка, скользя по передней его грани, начнет изгибаться. К отгибу ее принуждает именно передняя грань резца. Очевидным является и то, что отгиб стружки сопровождается приложением к ней соответствующей силы. Это — сумма сил нормального давления и сил трения передней грани резца. Воздействующее на стружку давление заставляет менять ее положение в пространстве и вызывает появление в материале стружки напряжений сдвига, изгиба, растяжения и сжатия. Составляющие сил трения, совпадающие с направлением движения стружки, вызывают напряжения, сжимающие стружку в продольном направлении.
Вследствие сложного напряженного состояния в стружке неизбежно появляются касательные напряжения, действующие во всех направлениях, но преимущественно в направлении движения резца и нормально к плоскости резания. Величина касательных напряжений зависит от угла отгиба стружки, равного углу резания , толщины стружки, структурной характеристики материала по сечению действия напряжений.
Итак, на обрабатываемость резанием древесины различных пород, кроме свойств самой древесины, огромное влияние оказывают следующие факторы: кинетостатика резания (силовое взаимодействие резца и древесины), геометрия и микрогеометрия резца, острота главной и вспомогательной. Нагрев древесины вызывает ее деструкцию, выделение агрессивных по отношению к инструментальным материалам веществ и, возможно, к водородному, окислительному и другим видам химического изнашивания.
Характеристикой агрессивности продуктов деструкции может служить в первом приближении показатель рН кислотности древесины различных пород. Практически для всех пород рН ≤ 7, т.е. дереворежущий инструмент работает в кислой среде. В таблице приведены усредненные численные значения параметров наиболее распространенных древесинных пород. Различия условий произрастания, расположения образца по длине и радиусу ствола и другие причины определяют разброс свойств в пределах одной породы, оцениваемой коэффициентом вариации v.
38
Показатели механических свойств, полученные по стандартным методикам испытаний, характеризуют древесину как конструкционный материал. Для описания процессов резания необходимо иметь дополнительно методы испытаний, результаты которых могли бы более точно отразить специфику разрушения древесины резцом.
|
|
|
|
|
|
|
|
|
|
|
|
|
39 |
Табл. 10.1. Параметры, влияющие на обрабатываемость древесины резанием различных пород |
|
|
|
||||||||||
|
|
Коэффици- |
Cосна |
Ель |
Лист- |
Граб |
Дуб |
Клен |
Ясень |
Бук |
Берё- |
Липа |
Осина |
Параметры |
ент вариа- |
|
|
венни- |
|
|
|
|
|
за |
|
|
|
|
|
ции V, % |
|
|
ца |
|
|
|
|
|
|
|
|
1 |
|
2 |
3 |
4 |
5 |
6 |
7 |
8 |
9 |
10 |
11 |
12 |
13 |
Плотность кг/м |
|
30 |
500 |
450 |
660 |
800 |
690 |
690 |
680 |
670 |
630 |
420 |
440 |
|
|
|
|
|
|
|
|
|
|
|
|
|
|
Кислотность, рН |
|
- |
5,5 |
5,4 |
- |
- |
5,1 |
- |
7,0 |
6,9 |
6,0 |
- |
- |
|
|
|
|
|
|
|
|
|
|
|
|
|
|
Теплопроводность, , Вт/м°С |
- |
0,12 |
0,11 |
0,16 |
0,21 |
0,17 |
0,17 |
0,17 |
0,16 |
0,16 |
0,12 |
0,1 |
|
|
|
|
|
|
|
|
|
|
|
|
|
|
|
Модуль упругости |
Еi, МПа |
20 |
1230 |
1480 |
- |
- |
1460 |
- |
- |
- |
1640 |
- |
1420 |
|
|
|
|
|
|
|
|
|
|
|
|
|
|
|
Ео, МПа |
20 |
70 |
67 |
- |
- |
135 |
- |
- |
- |
68 |
- |
60 |
|
|
|
|
|
|
|
|
|
|
|
|
|
|
Предел прочности |
pi, МПа |
20 |
103 |
103 |
125 |
141 |
- |
- |
145 |
123 |
168 |
121 |
- |
|
|
|
|
|
|
|
|
|
|
|
|
|
|
|
po, МПа |
20 |
5,4 |
5,0 |
5,6 |
13,3 |
8,0 |
13,3 |
9,0 |
12,5 |
11,1 |
- |
- |
|
|
|
|
|
|
|
|
|
|
|
|
|
|
|
сж.i, МПа |
13 |
48,5 |
44,5 |
64,5 |
60,0 |
57,5 |
59,5 |
59,0 |
55,5 |
55,0 |
45,5 |
- |
|
|
|
|
|
|
|
|
|
|
|
|
|
|
|
сж.o, МПа |
13 |
5,2 |
- |
4,5 |
6,7 |
- |
- |
- |
6,2 |
- |
4,4 |
4,2 |
|
|
|
|
|
|
|
|
|
|
|
|
|
|
|
ск.i, МПа |
- |
7,5 |
6,9 |
9,9 |
15,6 |
10,2 |
12,4 |
13,9 |
11,6 |
9,3 |
6,3 |
6,1 |
|
|
|
|
|
|
|
|
|
|
|
|
|
|
|
ск.o, МПа |
- |
3,1 |
|
- |
- |
4,3 |
- |
- |
- |
3,9 |
- |
- |
|
|
|
|
|
|
|
|
|
|
|
|
|
|
Твердость радиальная, Hр, МПа |
17 |
23,5 |
17,7 |
28,4 |
75,5 |
54,9 |
54,5 |
57,9 |
42,7 |
36,3 |
16,7 |
16,9 |
|
|
|
|
|
|
|
|
|
|
|
|
|
|
|
Твердость торцовая, Hт, МПа |
17 |
28 |
28 |
42,6 |
88,8 |
66,2 |
74,6 |
78,5 |
59,8 |
45,6 |
25,5 |
27,3 |
|
|
|
|
|
|
|
|
|
|
|
|
|
|
|
Микротвердость ранней зоны |
|
|
|
|
|
|
|
|
|
|
|
|
|
|
|
|
|
|
|
|
|
|
|
|
|
|
|
H , МПа |
|
- |
20,6 |
18 |
20,1 |
73 |
52,4 |
- |
- |
57 |
- |
- |
16,1 |
|
|
|
|
|
|
|
|
|
|
|
|
|
|
Микротвердость поздней зоны |
|
|
|
|
|
|
|
|
|
|
|
|
|
|
|
|
|
|
|
|
|
|
|
|
|
|
|
H , МПа |
|
- |
112 |
111 |
134 |
79 |
93 |
- |
- |
- |
- |
- |
71 |
|
|
|
|
|
|
|
|
|
|
|
|
|
|
Коэффициент породы, Ап |
- |
1 |
0,9 |
1,1 |
1,2 |
1,55 |
1,5 |
1,75 |
1,4 |
1,3 |
0,6 |
0,7 |
40
Коб |
- |
1 |
1,14 |
- |
- |
0,58 |
- |
- |
0,7 |
0,74 |
1,22 |
1,19 |
|
|
|
|
|
|
|
|
|
|
|
|
|