
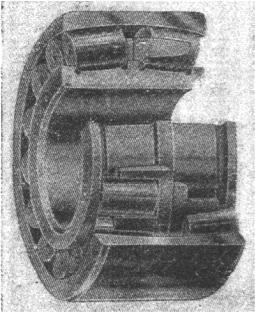
1
Федеральное агентство по образованию Государственное образовательное учреждение высшего профессионального образования «Воронежская государственная лесотехническая академия»
ДЕТАЛИ МАШИН И ОСНОВЫ КОНСТРУИРОВАНИЯ
Методические указания к выполнению лабораторных работ для студентов специальностей
250403 – Технология деревообработки,
250401 – Лесоинженерное дело Часть 2
Воронеж 2009
2
УДК 621.81
Детали машин и основы конструирования [Текст] : методические указания к выполнению лабораторных работ для студентов специальностей 250403 – Технология деревообработки, 250401 – Лесоинженерное дело. Ч. 2 / В. С. Быков, Г. Н. Вахнина, В. В. Ткачев, В. В. Стасюк, П. Н. Щеблыкин ; Фед. агентство по образованию, ГОУ ВПО «ВГЛТА». – Воронеж, 2009. – 32 с.
Печатается по решению учебно-методического совета ГОУ ВПО «ВГЛТА» (протокол № 9 от 21 мая 2008 г.)
Рецензент канд. техн. наук, доц. А. М. Гиевский
3
ЛАБОРАТОРНАЯ РАБОТА № 1
ИЗУЧЕНИЕ ПОДШИПНИКОВ КАЧЕНИЯ И УПЛОТНЕНИЙ ПОДШИПНИКОВЫХ УЗЛОВ
1. Цель работы
Ознакомление с различными типами подшипников качения, системой их условных обозначений (маркировкой),
а также с основными типами уплотнений подшипниковых узлов.
2. Общие сведения
Подшипники качения – это опоры вращающихся или касающихся деталей, использующие элементы качения (шарики или ролики) и работающие на основе трения качения. Они состоят из наружного кольца, внутреннего кольца, между которыми расположены тела качения. Для предохранения тел качения от соприкосновения между собой их отделяют друг от друга сепаратором, который существенно уменьшает потери на трение.
Преимущества подшипников качения по сравнению с подшипниками скольжения:
-малый коэффициент трения: f = 0,0015…0,006;
-незначительный расход смазки;
-малое сопротивление при разгоне, малый статический момент трения;
-меньшие габариты в длину;
-большая надежность при заедании;
-простота монтажа, демонтажа и обслуживания;
-снижение стоимости производства за счет массового изготовления стандартных типов подшипников.
Недостатки подшипников качения:
-ограниченная способность восприятия ударных и динамических нагрузок;
-ограничение срока службы подшипников усталостным выкрашиванием поверхностей тел качения;
-большие габариты по диаметру при больших нагрузках.
Подшипники качения классифицируют по следующим признакам.
По форме тел качения их подразделяют на шариковые и роликовые (рис. 1.1, рис. 1.2). Роликовые, в свою очередь, делятся по форме роликов на подшипники с короткими цилиндрическими роликами, коническими, бочкообразными, игольчатыми и витыми роликами.
По направлению действия воспринимаемых сил (нагрузок) разделяют на радиальные (воспринимающие преимущественно радиальные нагрузки, действующие перпендикулярно оси вращения подшипника); радиальноупорные (воспринимающие одновременно действующие радиальные и осевые
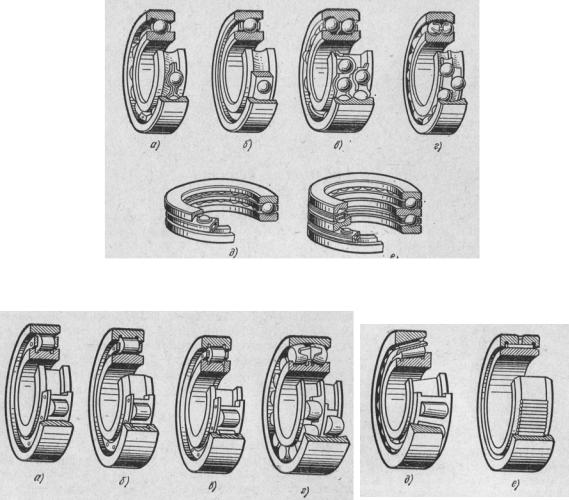
4
нагрузки); упорно-радиальные (воспринимающие одновременно действующие осевые и радиальные нагрузки); упорные (воспринимающие осевые нагрузки).
По способности самоустановки подшипники качения бывают самоустанавливающиеся и несамоустанавливающиеся.
По числу рядов тел качения (расположенные по ширине) их делят на однорядные, двухрядные, четырехрядные и многорядные.
Рис. 1.1. Основные типы шарикоподшипников
Рис. 1.2. Основные типы роликоподшипников
Основными характеристиками подшипников являются грузоподъемность, быстроходность, масса, габариты, потери энергии.
Для маркировки, указаний на чертежах и в спецификациях, применения в технической литературе и т.п. стандартные подшипники имеют условные обозначения. Условные обозначения подшипников составляют из цифр, значения которых определяют местом, занимаемым в обозначении. Две первые цифры, считая справа, обозначают внутренний диаметр подшипника (для подшипников с внутренним диаметром от 20 до 495 мм эти цифры соответствуют внутреннему диаметру, деленному на 5). Третья цифра справа
5
совместно с седьмой обозначает серию подшипников всех диаметров (кроме малых до 9 мм):
-особо легкая серия – 1;
-легкая серия – 2;
-средняя серия – 3;
-тяжелая серия – 4;
-легкая широкая серия – 5;
-средняя широкая – 6 и т.д.
Четвертая цифра справа обозначает тип подшипника, т.е. какую нагрузку подшипник может воспринимать:
0– радиальный шариковый;
1– радиальный шариковый сферический;
2– радиальный с короткими цилиндрическими роликами;
3– радиальный роликовый двухрядный сферический;
4– радиальный роликовый с длинными игольчатыми роликами;
5– радиальный роликовый с витыми роликами;
6– радиально-упорный шариковый;
7– радиально-упорный роликовый конический;
8– упорный шариковый;
9– упорный роликовый.
Пятая или пятая и шестая цифры, вводимые не для всех подшипников, обозначают конструктивные особенности подшипников, например, наличие стопорной канавки на наружном кольце, наличие встроенных уплотнений и т.п.
Промышленность изготовляет подшипники качения пяти классов точности: 0; 6; 5; 4; 2. Обозначения даны в порядке повышения точности, определяемой допусками на изготовление элементов, а так же нормами плавности вращения. Класс точности указывается слева от условного обозначения подшипников через тире (например, 6-207).
Примеры обозначения подшипников:
-шариковые однорядные с внутренним диаметром 50 мм: легкой серии
–210; средней – 310; тяжелой – 410;
-радиально-упорные роликовые подшипники с внутренним диаметром 80 мм: легкой серии – 7216; легкой широкой – 7516; средней – 7316; средней широкой – 7616.
Подшипники качения в целях предохранения от загрязнений извне и для предотвращения вытекания из них смазки снабжают уплотняющими устройствами. Предотвращение уменьшения смазки важно с точки зрения уменьшения расхода смазки, загрязнения пола и предохранения от попадания смазки в механизмы, которые должны работать всухую: сухие фрикционные передачи, муфты, тормоза, электродвигатели и т.д.
Уплотнения подшипниковых узлов делятся на следующие основные
типы:
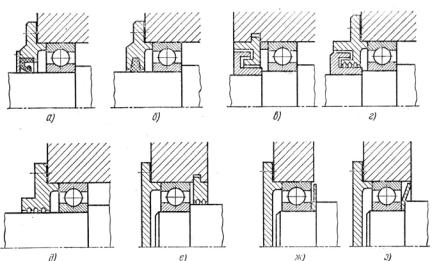
6
-контактные (манжетные (рис. 1.3, а), войлочные (рис. 1.3, б)и т.п.), применяемые при низких и средних скоростях. Основное достоинство этих уплотнений – простота и дешевизна изготовления; недостаток – трение на поверхности контакта;
-лабиринтные (рис. 1.3, в, г) и щелевые (рис. 1.3, д, е), применяемые в неограниченном диапазоне скоростей, осуществляющие защиту благодаря сопротивлению протекания жидкости или газа через узкие щели. Они практически не имеют изнашивающихся деталей и не требовательны в эксплуатации;
-центробежные (рис. 1.3, ж, з), применяемые при средних и высоких скоростях и основанные на отбрасывании центробежными силами смазки и загрязняющих веществ, попадающих на вращающиеся защитные диски;
-комбинированные, сочетающие уплотнения, основанные на двух и более из указанных типов.
Рис. 1.3. Основные типы уплотнений
3.Порядок выполнения работы
3.1.Ознакомиться с устройством и характеристиками основных типов подшипников качения [1, 2].
3.2.Изучить систему условных обозначений подшипников качения.
3.3.Изучить указанные преподавателем подшипники качения разных типов, записать номера подшипников и расшифровать их полное наименование.
3.4.Указанные преподавателем три подшипника качения замерить, определить тип и восстановить их маркировку, сравнив затем с ГОСТом.
3.5.Ознакомиться с основными типами уплотнений подшипниковых
узлов.
7
4.Оформление отчета
4.1.Титульный лист по образцу. Цель работы. Общие сведения.
4.2.Эскизы основных типов подшипников качения [2].
4.3.Эскизы основных типов уплотнений подшипниковых узлов [2, 4].
4.4.Расшифровка условных обозначений подшипников качения согласно таблице 1.1.
|
|
|
|
|
Таблица 1.1 |
|
|
|
|
|
|
Обозначение |
Внутренний |
Внешний |
Ширина |
|
Тип |
подшипника |
диаметр |
диаметр |
подшипника |
Серия |
подшипника |
качения |
d, мм |
D, мм |
В, мм |
|
качения |
|
|
|
|
|
|
4.5. Составленные условные обозначения измеренных подшипников качения свести в таблицу 1.2.
|
|
|
|
|
Таблица 1.2 |
|
|
|
|
|
|
|
|
Тип |
Внутрен- |
Внешний |
Ширина |
Предпо- |
|
Обозначе- |
подшипника |
ний |
диаметр |
подшип- |
лагаемое |
|
ние по |
качения |
диаметр |
D, мм |
ника |
обозначение |
|
ГОСТу |
|
d, мм |
|
В, мм |
|
|
|
|
|
|
|
|
|
|
4.6.Вывод по закрепленной за лабораторной работой теме.
5.Контрольные вопросы
5.1.Подшипники качения и их конструкция, основные характеристики.
5.2.Преимущества и недостатки подшипников качения по сравнению
сподшипниками скольжения.
5.3.Классификация подшипников качения:
а) по форме тел качения; б) по направлению воспринимаемых нагрузок;
в) по числу рядов тел качения; г) по самоустанавливаемости.
5.4.Как маркируют подшипники качения (с примерами обозначения)?
5.5.Назначение уплотнений подшипниковых узлов, основные типы.
8
ЛАБОРАТОРНАЯ РАБОТА № 2
ИССЛЕДОВАНИЕ ТОЧНОСТИ СРАБАТЫВАНИЯ ПРЕДОХРАНИТЕЛЬНЫХ МУФТ
1. Цель работы
Оценка точности срабатывания предохранительных муфт и выявление путей ее повышения.
2. Общие сведения и расчетные зависимости
Предохранительные муфты предназначены для защиты деталей машин от перегрузок [1, 2]. Они срабатывают, когда вращающий момент превышает некоторую установленную величину ТМ. Обычно величину ТМ назначают несколько большей номинального момента, например на 25 % (для исключения слишком частых срабатываний). Для снижения инерционных усилий от вращающихся масс привода предохранительные муфты устанавливают по возможности ближе к источнику перегрузок.
К основным типам предохранительных муфт относятся: фрикционные,
кулачковые, шариковые и муфты с разрушающимися элементами.
Наибольшее распространение получили фрикционные дисковые предохранительные муфты, у которых усилие на поверхностях трения осуществляется винтовыми или тарельчатыми пружинами.
Как правило, фрикционные муфты используют при кратковременных перегрузках, поскольку при продолжительном скольжении мощность, расходуемая на трение, вызывает интенсивное выделение тепла и износ рабочих поверхностей.
Срабатывание муфты – сложный динамический процесс, и максимальная нагрузка деталей машин зависит от регулировочного момента муфты ТМ, скорости нарастания нагрузки, жесткости системы и моментов инерции масс. Точность ограничения нагрузки муфтой – одна из важнейших ее характеристик, оцениваемая коэффициентом точности срабатывания КТ:
КТ = ТMmax/ТMmin, |
(2.1) |
где ТМmax и ТМmin – наибольший и наименьший крутящие моменты, при которых возможно срабатывание муфты, Нм.
Чемближе КТ кединице, темнадежнееработаетмуфта, темвышееекачество.
Для дисковой фрикционной предохранительной муфты (рис. 2.1), у
которой рабочими поверхностями являются плоские (боковые) поверхности дисков, расчетное значение крутящего момента ТМ (Нм) определяется по формуле:
ТМ = Fпрf0 · 0,5Dсрz, |
(2.2) |

9
где Fпр – осевое усилие пружины, Н; f0 – коэффициент трения;
Dср – средний диаметр рабочих поверхностей, м; z – число трущихся поверхностей: z = m + n – 1,
(m – число ведущих дисков; n – число ведомых дисков).
Рис. 2.1. Схема дисковой фрикционной муфты: Q – сила включения, Н;
Rср – средний радиус рабочих поверхностей, м; R и r – радиусы рабочих поверхностей, м.
Для конусной фрикционной предохранительной муфты (рис. 2.2), у
которой рабочие поверхности имеют коническую форму, расчетное значение крутящего момента ТМ (Нм) определяется по формуле:
ТМ = Fпрf0 · 0,5Dсрsinα, |
(2.3) |
где Dср – средний диаметр контакта фрикционных поверхностей, м; α – половина угла конуса, град.
Рис. 2.2. Схема конусной фрикционной муфты: α – угол наклона конуса, град;
Rср – средний радиус рабочих поверхностей, м; b – ширина поверхности трения, м.
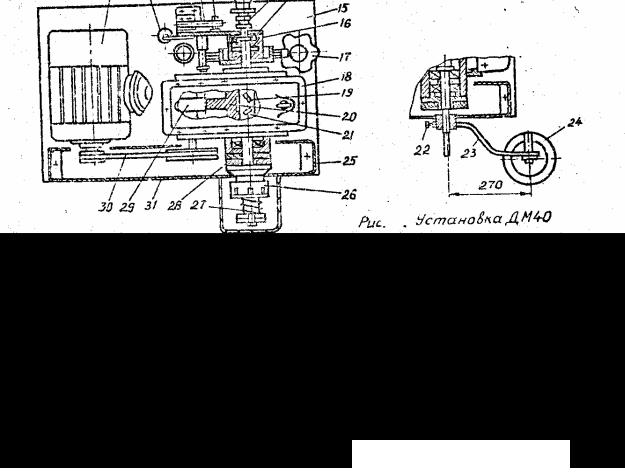
10
Из анализа (2.2) и (2.3) видно, что точность срабатывания муфты определяется стабильностью коэффициента трения на рабочих поверхностях. На фактическое значение коэффициента трения f0 оказывают влияние такие факторы, как состояние и температура поверхностей трения, скорость скольжения, удельное давление на поверхностях трения и др.
3. Оборудование и приборы
Экспериментальная установка ДМ 40.
Набор предохранительных муфт. Штангенциркуль. Тарировочное приспособление, включающее рычаг и грузы. Индикатор часового типа (или осциллограф с усилителем).
3.1. Описание экспериментальной установки ДМ 40
Установка (рис. 2.3) состоит из электродвигателя 6, клиноременной передачи 30, натяжение которой осуществляется роликом 1, одноступенчатого зубчатого цилиндрического редуктора 18 (шестерня 29 и колесо 20), ведомый вал 21 установлен на подшипниках, смонтированных внутри колеса 20. Нагрузка ведомого вала 21 осуществляется колодочным тормозом 17.
Рис. 2.3. Установка ДМ40
11
Рычаги тормоза 17 соединены штангой 12 с обоймой 16, сидящей на подшипниках ведомого вала, что позволяет тормозной системе свободно качаться вокруг оси вала. Тормоз снабжен гидравлическим демпфером 7.
Штанга через призму 9 опирается на измерительную пружину 8, прогиб которой измеряется индикатором 3. Балансировочная система тормоза 17 может быть зафиксирована при помощи винтового устройства 2.
На ведомом валу 21 наклеены тензодатчики 19, выводы которых вынесены на торецвала. Токосъемник10 соединенсведомымваломкомпенсирующеймуфтой11. Исследуемые муфты 26, представляющие отдельные быстросъемные узлы, одеваются на выступающий конец ведомого вала 21 и закрепляются в осевом направлении. При этом ведущая полумуфта соединяется с колесом 20 через подушку 28. Каждая конструкция муфты позволяет производить регулировку
силы сжатия полумуфты и ее замер |
путем определения |
длины |
предварительно протарированной пружины 27. |
|
|
Все узлы установки смонтированы |
на станине 15. На |
станине |
установлен защитный кожух 31 с пультом управления 5. Выступающий конец муфты закрыт прозрачным откидывающимся колпачком 4.
Установка подключается к сети при помощи шнура 13 и имеет болт заземления 14.
Тарировочное приспособление состоит из рычага 23 и подвески с четырьмя грузами 24. Приспособление одевается на ведомый вал и закрепляется винтом 22.
3.2. Техническая характеристика испытываемых муфт
Дисковая фрикционная предохранительная муфта:
средний диаметр (≈ диаметр трения) – Dср = 65 мм; пара трения – сталь – азбофрикционный материал; коэффициент трения – f0 = 0,3;
количество трущихся поверхностей – z = 5.
Конусная фрикционная предохранительная муфта:
средний диаметр контакта фрикционных поверхностей – Dср = 65 мм; длина образующей контакта – 20 мм; половина угла конуса - α = 20º; пара трения – сталь – текстолит;
коэффициент трения – f0 = 0,2.
Номинальный момент срабатывания муфт – 10 Нм. Номинальная скорость вращения вала муфт – 12 рад/с (115 мин-1). Способ нагружения – колодочным тормозом.
Замер крутящего момента на муфте – при помощи индикатора часового типа (или электротензометрический).
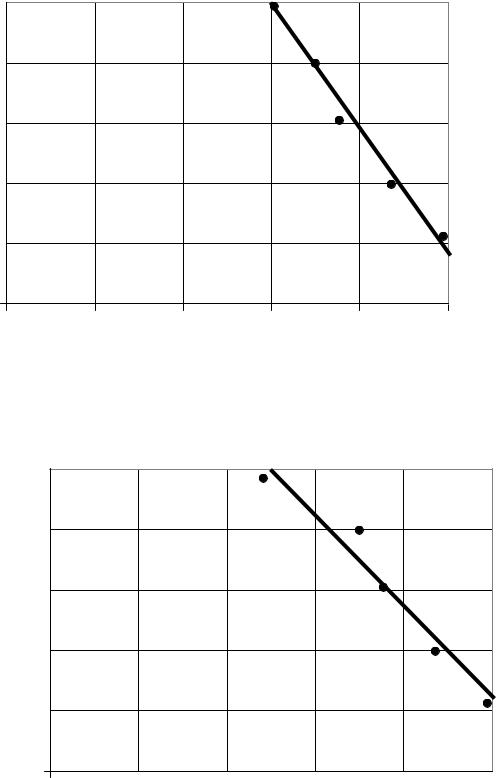
12
Н500
400
300
200
100
0
0 |
10 |
20 |
30 |
40 мм50 |
Рис. 2.4. Тарировочный график пружины фрикционной конусной муфты
Н500
400
300
200
100
0
0 |
10 |
20 |
30 |
40 |
мм |
50 |
Рис. 2.5. Тарировочный график пружины фрикционной дисковой муфты
13
Замер силы пружины муфты – по длине пружины с помощью тарировочного графика.
Привод – от электродвигателя 4А71В. 6 исп. 100, мощностью Рдв = 1,55 кВт, частота вращения вала электродвигателя nдв = 940 мин –1.
Габаритные размеры – 635х570х410 мм. Масса – 130 кг.
4. Порядок выполнения работы
(ознакомиться с правилами по технике безопасности, приведенными в конце лабораторной работы)
4.1.Разобрать и собрать каждую муфту, изучить конструкцию, отметить число трущихся поверхностей.
4.2.Рычаг тарировочного приспособления установить на ведомый вал установки. Ведомый вал зафиксировать колодочным тормозом, чтобы не проворачивался. Поочередно навешивая грузы, определить соотношение величины создаваемого на валу крутящего момента и показаний на индикаторе (динамометрическом кольце). Построить тарировочный график.
4.3.Для заданного преподавателем наибольшего в серии опытов ТМ вычислить расчетное значение Fпр (формула 2.2 и 2.3) и округлить его.
4.4.Наметить серию из 3…5 опытов с разным усилием пружины,
составляющим, например, 100, 80, 60, 40 процентов от Fпр и по тарировочному графику найти соответствующие длины пружины (рис. 2.4, 2.5).
4.5.Муфту в сборе установить на ведомый вал, обеспечив точное вхождение штифтов в отверстия резинового диска.
4.6.Установить требуемую для данного опыта длину пружины.
4.7.Закрыв щиток, включить электродвигатель. Создать перегрузку тормозом, замкнув колодки до полной остановки тормозного шкива; зафиксировать показания индикатора. Снять перегрузку, опустив колодки. Повторить необходимое число раз опыт, создавая и снимая перегрузку.
4.8.Выключить электродвигатель.
4.9.Провести опыт по п. 6, 7, 8 для другого значения длины пружины.
4.10.По экспериментальным данным вычислить коэффициент точности срабатывания для каждого усилия пружины (формула 2.1). Определить значения коэффициентов трения для каждого опыта, зависимости (2.2) и (2.3).
5.Оформление отчета
5.1.Титульный лист по образцу. Цель работы. Общие сведения.
5.2.Описание и схема (рис. 2.3) экспериментальной установки ДМ 40.
5.3.Техническая характеристика испытываемых муфт.
5.4.Тарировочный график по данным тарировки грузами.
14
5.5. Расчеты осевого усилия пружины, крутящих моментов, коэффициента точности срабатывания муфт, итоги которых свести в табл. 2.1.
Таблица 2.1
Осевое |
Длина |
Показания |
Крутящий |
Коэффи- |
Коэффи- |
усилие |
пружины, |
динамомет- |
момент |
циент |
циент |
пружины |
мм |
рического |
ТМ, Нм |
трения |
точности |
Fпр, Н |
|
кольца |
|
f0 |
срабатывания |
|
|
|
|
|
муфты КТ |
0,4Fпр |
|
|
|
|
|
|
|
|
|
|
|
0,6Fпр |
|
|
|
|
|
|
|
|
|
|
|
0,8Fпр |
|
|
|
|
|
|
|
|
|
|
|
Fпр |
|
|
|
|
|
|
|
|
|
|
|
5.6. Вывод по закрепленной за лабораторной работой теме с обоснованием результатов расчетов и испытаний.
6. Контрольные вопросы
6.1. Назначение предохранительных муфт. Принцип работы фрикционных предохранительных муфт.
6.2.Какое влияние на точность срабатывания исследованных муфт оказало изменение давления на поверхностях трения (изменение усилия пружины)?
6.3.Как изменялся коэффициент трения в зависимости от давления на поверхностях трения?
6.4.При каком давлении коэффициент трения наиболее стабильный?
6.5.Какие имеются конструктивные решения, повышающие точность срабатывания предохранительных муфт?
ПРАВИЛА по технике безопасности во время работы на установке
для исследования предохранительных муфт
1.Использовать средства защиты от поражения электрическим током (резиновый коврик).
2.Испытания производить только при наличии защитного кожуха на
муфте.
3.При смене муфт установка должна быть отключена от электросети.
4.Не останавливать установку руками или какими-либо предметами.
15
5. При обнаружении неисправности в работе установки отключить ее от электросети и сообщить преподавателю или учебному мастеру.
ЛАБОРАТОРНАЯ РАБОТА № 3
ИСПЫТАНИЕ ПОДШИПНИКОВ КАЧЕНИЯ
1. Цель работы
Определение момента трения в подшипнике, условно приведенного к валу коэффициента трения, и зависимости этих величин от нагрузки, частоты вращения и уровня масла в подшипнике.
2. Общие сведения
Из различных видов опор валов и вращающихся осей наибольшее распространение в настоящее время получили подшипники качения [1, 3]. Они имеют низкий коэффициент трения (f=0,0015÷0,006), просты в эксплуатации и не требуют большого расхода смазки. Коэффициент полезного действия одной пары подшипников в среднем равен 0,99.
Однако при проектировании сложных механизмов с большим количеством опор необходимо учитывать потери на трение в подшипниках. Эти потери зависят от нагрузки, количества смазки и других факторов.
Сопротивление вращению подшипников складывается из:
-трения между телами качения и кольцами;
-трения тел качения о сепаратор и сепаратора о кольца;
-сопротивления масла;
-трения в уплотнениях.
С ростом нагрузки момент трения растет по линейной зависимости. При полном отсутствии смазки момент трения повышен и длительная работа подшипников невозможна. При увеличении подачи масла момент вначале остается постоянным, а потом начинает возрастать.
3. Установка для испытаний
Установка для испытания подшипников качения представлена на рис. 3.1. Установка состоит из корпуса 1, на котором смонтированы вал 17 с испытательными головками и силоизмерительным устройством привода устройства для измерения момента трения.
Вал17 установлен вдвухшарикоподшипниковыхопорах16 иприводитсяво вращение электродвигателем 29 через 3-ступенчатую клиноременную передачу 19. Натяжение ремня осуществляется винтовым натяжным устройством 30, поворачивающим подмоторную плиту с электродвигателем вокруг оси. Клиноременная передача находится в кожухе 18 с крышкой 20. Для натяжения ремня и доступа к клеммовой коробке в корпусе имеются окна, закрытые

16
крышками 28 и 31. Испытуемая головка устанавливается на конце вала, имеющем шариковыйфиксатор7.
Наружные кольца двух средних испытуемых подшипников 5 находятся в общей обойме 13, а наружные кольца двух крайних испытуемых подшипников 6
– в корпусе головки 14, охватывающей обойму средних подшипников с зазором. Нагружение осуществляется с помощью винта 11 корпуса 12, который связан с корпусом головки. При этом подшипники обоймы поджимаются к
втулке 15, сидящей на валу, а подшипники корпуса отжимаются от нее. Силоизмерительное устройство состоит из динамометрической скобы
21 и индикатора 22. Тарировочный график динамометрической пружины представлен на рис. 3.2.
.
Рис. 3.1 Установка для испытания
На испытуемой головке имеется смазочное устройство для смазки подшипников, состоящее из цилиндра 8 с поршнем 9. Передвижением поршня можно изменять уровень масла в подшипниках.
Для определения начала стабильной работы подшипников предусмотрен термометр 10, определяющий температуру масла.
Возникающий в подшипниках момент трения стремится увлечь корпус и с ним обойму двух средних подшипников. Закрепленный на корпусе

17
головки маятник с грузом 4 будет удерживать корпус от вращения и отклоняться на некоторый угол в зависимости от величины момента.
Стрелка 26, закрепленная на маятнике, по шкале 27 показывает величину возникающего момента трения (Нм) в подшипниках.
Для уравновешивания головки служит груз 23, перемещающийся на резьбе по штанге 24. Для ограничения поворота головки при пуске электродвигателя имеются ограничительные упоры 25.
На установке предусмотрено измерение момента трения с помощью тензодатчиков сопротивления, наклеенных на измерительную пружину 32 с выводом на три клеммы 39, расположенные на панели 35. Для этого необходимо ввести в зацепление с измерительной пружиной нажимную втулку 2, расположенную на конце маятника, и с помощью маховика 3 зафиксировать ее.
Питание электродвигателя А02-11-1 мощностью Рдв = 0,6 кВт при частоте вращения nдв = 1350 об/мин осуществляется от сети 3-фазного переменного тока напряжением 380 В. Шнур 36 служит для подключения установки к сети. Автоматический выключатель типа АК63-3М защищает электрооборудование от токов короткого замыкания и перегрузки.
Рукояткой 34 автоматического выключателя подается напряжение на силовые цепи и цепи управления. Пуск электродвигателя осуществляется нажатием кнопки 33 (черного цвета) с надписью «пуск», остановка нажатием кнопки 38 (красного цвета) с надписью «стоп». Данные, которые имеют подшипники качения, предназначенные для испытания, приведены в табл. 3.1.
500 |
|
|
|
|
|
|
f,мм |
|
|
|
|
|
|
2,2 |
|
|
|
|
|
|
400 |
|
|
|
|
|
|
1,5 |
|
|
|
|
|
|
300 |
|
|
|
|
|
|
1,0 |
|
|
|
|
|
|
200 |
|
|
|
|
|
|
0,5 |
|
|
|
|
|
|
100 |
|
|
|
|
|
|
0 |
|
|
|
|
|
|
0 |
0 |
2500 |
5000 |
7500 |
10000 |
F, Н |
|
10 |
20 |
30 |
40 |
50 |
|
|
|
Рис. 3.2 Тарировочный график |
|
18
4. Расчетные зависимости
Суммарный момент трения ТТ (Нм) выражают через условный коэффициент трения fпр, приведенный к посадочному диаметру вала d (м):
ТТ = Fr · fпр · 0,5d, |
(3.1) |
где Fr – радиальная нагрузка на подшипник, Н.
В установке усилие на динамометрической скобе F (Н) создает на
каждом из подшипников радиальную нагрузку Fr (Н): |
|
|
|
|
|||||
|
|
Fr = F/2. |
|
|
|
|
(3.2) |
||
|
|
|
|
|
|
|
Таблица 3.1 |
||
|
|
|
|
|
|
|
|
|
|
|
|
|
Условн |
|
|
|
Грузоподъемнос |
||
|
|
|
ое |
d, |
D, |
В, |
тьН |
|
|
Наименование подшипника |
|
обознач |
мм |
мм |
мм |
динами |
статиче |
|
|
|
|
|
ение |
|
|
|
ческая, |
ская, С0 |
|
|
|
|
|
|
|
|
С |
|
|
Шарикоподшипник |
|
208 |
40 |
80 |
18 |
25600 |
13900 |
|
|
радиальный однорядный легкой |
|
|
|
|
|
|
|
|
|
серии |
|
|
|
|
|
|
|
|
|
Шарикоподшипник |
|
308 |
40 |
90 |
23 |
31900 |
22700 |
|
|
радиальный |
однорядный |
|
|
|
|
|
|
|
|
средней серии |
|
|
|
|
|
|
|
|
|
Шарикоподшипник |
|
1208 |
40 |
80 |
18 |
15100 |
8720 |
|
|
радиальный |
сферический |
|
|
|
|
|
|
|
|
двухрядный легкой серии |
|
|
|
|
|
|
|
|
|
Роликоподшипник |
конический |
|
7208 |
40 |
80 |
20 |
42400 |
32700 |
|
легкой серии |
|
|
|
|
|
|
|
|
|
Момент трения, получаемый на всех четырех подшипниках: |
|
|
|||||||
|
ТТ = 4Fr · fпр · 0,5d. |
|
|
|
(3.3) |
|
|||
Подставив (3.2) в (3.3), получаем: |
|
|
|
|
|
|
|||
|
ТТ = F · fпр · d. |
|
|
|
(3.4) |
|
|||
Из формулы (3.4) можно определить условный, приведенный к валу |
|||||||||
коэффициент трения fпр: |
fпр = TТ/ Fd. |
|
|
|
(3.5) |
|
|||
|
|
|
|
|
|
5. Порядок выполнения работы
(ознакомиться с правилами по технике безопасности во время работы на установке ДМ-28, приведенными в конце лабораторной работы)
19
5.1.Установить на вал предназначенную для испытаний головку с подшипниками (по указанию преподавателя). Проверить надежность фиксации головки.
5.2.Снять заднюю крышку на установке, перебросить ремень на шкивы, соответствующие частоте вращения, равной n = 970 мин-1.
5.3.Убедившись, что масла в подшипнике нет, включить электродвигатель и дать поработать 2…5 мин, создав нагрузку F = 2000…3000 Н.
5.4 Включив электродвигатель, создать винтом нагружения ряд нагрузок на подшипники: 2500; 5000; 7500; 10000 Н, используя тарировочный график и индикатор динамометра. На каждой ступени нагружения включать установку и по шкале замерять момент трения.
5.5.Произвести испытания по п.п. 5.3 – 5.4 при частоте вращения вала
1880 мин-1 и 2860 мин-1.
5.6.Следующее испытание произвести с заполнением подшипника маслом до центра нижнего шарика при тех же нагрузках и тех же скоростях.
5.7.Заполнить подшипник до погружения в масло нижней части внутреннего и в той же последовательности произвести испытания.
Испытания в пунктах 5.6 - 5.7 проводить по возможности при установившейся (постоянной) температуре масла.
5.8.Результаты испытаний занести в табл. 3.2.
5.9.По формуле (3.5) вычислить условный коэффициент трения и тоже занести в табл. 3.2.
6.0.Используя данные табл. 3.2, построить графики зависимости момента трения от нагрузки и частоты вращения и графики зависимости приведенного коэффициента трения от нагрузки и частоты вращения при различных уровнях смазки.
6.Оформление отчета
6.1.Титульный лист по образцу. Цель работы. Общие сведения.
6.2.Описание и схема установки (рис. 3.1).
6.3.Расчетные зависимости.
6.4.Результаты испытаний свести в таблицу 3.2.
6.5.Графики зависимостей ТТ = φ(F) и fпр = φ(F) при различном уровне масла в подшипнике.
6.6.Вывод по закрепленной на лабораторной работе теме с обоснованием полученных результатов.
7.Контрольные вопросы
7.1.Как изменяется момент трения с изменением нагрузки и частоты
вращения?

20
7.2.Как изменяется условный коэффициент трения с изменением нагрузки и частоты вращения?
7.3.Как влияет на момент трения и на условный коэффициент трения заполнение подшипника маслом?
и условное |
2860 об/мин |
пр |
Нм f |
||
полное(подшипникназвание обозначение) |
об=1880n /мин n = |
Т |
|
|
, |
|
|
Т |
|
|
Т |
|
|
пр |
|
|
f |
|
|
, Нм |
Испытуемый |
=970nоб/мин |
Т |
Т |
||
|
|
пр |
|
|
f |
|
|
, Нм |
|
|
Т |
|
|
Нагруз ка F, Н |
|
|
Таблица 3.2
По внутреннему кольцу
Поцентрунижнегошарика
Без смазки
По внутреннему кольцу
Поцентрунижнегошарика
Без смазки
По внутреннему кольцу
Поцентрунижнегошарика
Без смазки
По внутреннему кольцу
Поцентрунижнегошарика
Без смазки
По внутреннему кольцу
Поцентрунижнегошарика
Без смазки
По внутреннему кольцу
Поцентрунижнегошарика
Без смазки
2500 |
5000 |
7500 |
10000 |
ПРАВИЛА по технике безопасности во время работы на установке ДМ-28
1.Использовать средства защиты от поражения электрическим током (резиновый коврик).
2.Следить за надежной фиксацией испытуемого блока подшипников.
3.Нагрузку на корпус блока подшипников качения производить только
при полной остановке установки.
21
4.Изменение частоты вращения вала блока подшипников (переустановку ремня на шкивах) производить при полной остановке вала и отключенной от электросети установке (настенным выключателем АП-50).
5.При обнаружении неисправностей в работе установки испытание прекратить, отключить установку от электросети и сообщить преподавателю или учебному мастеру.
ЛАБОРАТОРНАЯ РАБОТА № 4
ИЗУЧЕНИЕ ПОСАДОК ДЕТАЛЕЙ МАШИН
1. Цель работы
Ознакомление с рекомендациями по выбору посадок зубчатых колес, шкивов ременных передач, звездочек цепных передач и подшипников качения.
2.Общие сведения
Вмашинах и механизмах соединяемые между собой детали должны иметь в зависимости от условий работы различную свободу относительного перемещения, определяемую степенью сопротивления их взаимного смещения. Например, соединение зубчатого колеса с валом должно обеспечить неподвижность, а соединение подшипника скольжения с валом – свободное вращение. Выполнение указанных требований осуществляется применением той или иной посадки [2, 4]. Посадки разделяют на три группы:
-с зазором (для подвижных соединений, рис. 4.1, а, б, в);
-с натягом (для неподвижных соединений, рис. 4.1, г, д);
-переходные (возможна подвижность при приложении небольшого усилия, рис. 4.1 е, ж).
Приведём понятия по терминологии единой системы допусков и посадок. Вал – термин, применяемый для обозначения наружных (охватываемых) элементов деталей. Отверстие – термин, применяемый для
обозначения внутренних (охватывающих) элементов деталей.
Номинальный размер – основной размер, который определяется расчетом на прочность или по конструктивным соображениям, он служит началом отсчета отклонений. Номинальные размеры округляются в соответствии с нормальным рядом чисел по ГОСТу.
Действительный размер – это размер, полученный в результате измерения с допустимой погрешностью.
Предельными размерами называют максимальное и минимальное значения размера, между которыми должен находиться действительный размер детали. Большее из них – наибольший предельный размер, меньшее – наименьший предельный размер.
Отклонение размера – алгебраическая разность между действительным размером и его номинальным значением.
22
Верхнее предельное отклонение – алгебраическая разность между наибольшим предельным размером и номинальным. Нижнее предельное отклонение – разность между наименьшим предельным размером и
номинальным. |
|
|
|
|
Допуском размера |
называют разность между наибольшим и |
|||
наименьшим |
предельными |
размерами. |
Допуск диаметра |
отверстия |
δD = Dmax − Dmin , |
допуск диаметра вала δd |
= d max − d min , где Dmax |
и Dmin – |
наиболее и наименее допустимые диаметры отверстий; dmax и dmin – наиболее и наименее допустимые диаметры вала. Поле допуска – совокупность всех возможных отклонений в пределах допуска.
Зазор – разность действительных размеров отверстия и вала, если размер отверстия больше размера вала. Натяг – разность размеров вала и отверстия до сборки, если размер вала больше размера отверстия.
Различают посадки в системе отверстия – это такие посадки, при которых наименьший предельный размер отверстия равен номинальному (нижнее отклонение равно нулю), и посадки в системе вала, у которых наибольший предельный размер вала равен номинальному (верхнее отклонение равно нулю). Например, в системе отверстия: отверстие 50+0,5,
вал 50 +−00,,0301 ; в системе вала: отверстие 50+−00,,0502 , вал 50-0,02. Всегда верхнее отклонение записывается выше, нижнее – ниже номинального размера, справа от него. В нашей стране в основном принята система отверстия.

23
Рис. 4.1. Схемы образования посадок:
а, б, в – посадки с зазором; г, д – посадки с натягом; е, ж – переходные посадки;
наим и наиб – наименьший и наибольший зазоры (натяги).
Для краткости на чертежах размеры и положенные поля допуска, определяющие характер соединения, обозначают буквой латинского алфавита
– прописной (заглавной) А, В, С…Z для отверстий и строчной (малой) а, в, с…z для валов (табл. 4.1).
|
|
|
Таблица 4.1 |
|
|
|
|
Основное |
|
Переходные |
|
отклонени |
Посадки с зазором |
посадки |
Посадки с натягом |
е |
|
|
P, R, S, T, U, V, X, Y, Z |
Отверстие |
A, B, C, D, E, F, G, H |
Js, K, M, N |
|
|
|
|
p, r, t, u, v, x, y, z |
Вал |
a, b, c, d, e, f, g, h |
Js, k, m, n |
На чертежах предельное отклонение указывается следующим образом: - условными обозначениями, например отверстие 50Н7, вал 55q6;
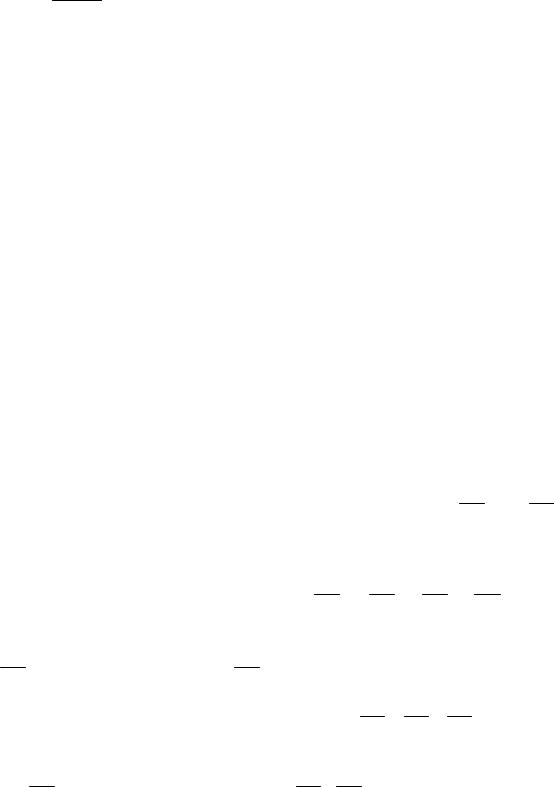
24
-числовыми значениями в мм, например отверстие 50+0,05 , вал
50−−0,0320,059;
-комбинированным способом, например отверстие 18Н7+0,018, вал
12е8 −−00,,032059 .
На сборочных чертежах посадки указывают в виде дроби, в числителе –
для отверстия, в знаменателе – для валов. Например, 50 |
Н7 |
. |
|
|
|
|
|
|||||||||||||||
|
|
|
|
|
|
|||||||||||||||||
|
|
|
|
|
|
|
|
|
|
|
|
|
|
|
|
g6 |
|
|
|
|
|
|
|
Цифра справа от буквенного обозначения посадки характеризует |
|||||||||||||||||||||
степень точности (степень качества) соединения, или квалитет (табл. 4.2) |
|
|||||||||||||||||||||
|
|
|
|
|
|
|
|
|
|
|
|
|
|
|
|
|
|
|
Таблица 4.2 |
|||
|
|
|
|
|
|
|
|
|
|
|
|
|
|
|
|
|
|
|
|
|
|
|
|
|
Точные |
|
|
|
|
|
Средние |
|
|
|
|
|
|
Грубые |
|
||||||
01 |
1 |
|
2 |
|
3 |
4 |
5 |
6 |
7 |
8 |
9 |
10 |
11 |
12 |
|
13 |
|
14 |
|
15 |
16 |
17 |
В машинах и механизмах общего назначения обычно применяют средние квалитеты.
3. Рекомендации по выбору посадок
3.1. Посадки зубчатых и червячных колес
Посадка зубчатых и червячных колес на вал, как правило, выполняется в системе отверстия. При выборе типа посадки учитывают условия работы и величину передаваемой нагрузки.
Для неподвижных соединений колес с валом, которые требуют периодической разборки, применяют переходные посадки Нn67 и Hk67
(первая – для небольших нагрузок, вторая – для средних, при мощности двигателя до 5 кВт). Для зубчатых и червячных редукторов общего
назначения обычно используют посадки Нr67 , Hs67 , Hp67 , mH76 . Для цилиндрических зубчатых и червячных колес наиболее употребляема посадка Hp67 , для конических колес mH76 . Для подвижных блоков шестерен
коробок передач по шпонкам применяют посадки Нh67 , Hf 67 , He87 . Посадку зубчатого вала на ступицу червячного колеса осуществляют при сплошной нагрузке по Hp67 , при умеренных толчках по Hr67 , Нn67 .

25
3.2. Посадка шкивов и звездочек
Рекомендуемые посадки шкивов ременных передач и звездочек цепных передач – переходные: при спокойной нагрузке Нк67 , при умеренных толчках
mН76 , Hn67 (если шкивы и звездочки установлены на шпонках).
3.3. Посадки подшипников качения
Посадки подшипников качения в корпус и на вал производятся в зависимости от режима работы в табл. 4.3.
|
|
Таблица 4.3 |
|
|
|
|
|
Посадка |
Режим работы |
Рекомендуемая |
|
|
|
посадка |
|
В корпус |
Легкий или нормальный |
Js7 |
|
На вал |
Легкий или нормальный |
js6, k6 |
|
В корпус |
Нормальный или тяжелый |
H7, K6 |
|
|
|
|
|
На вал |
Нормальный или тяжелый |
k6, m6 |
|
|
|
|
|
4. Соединения с натягом (прессовые соединения)
В последнее время для передачи момента со ступицы детали на вал все чаще стали применять соединения с натягом (без шпонок и шлицевых соединений), т.е. прессовые соединения (рис. 4.2).
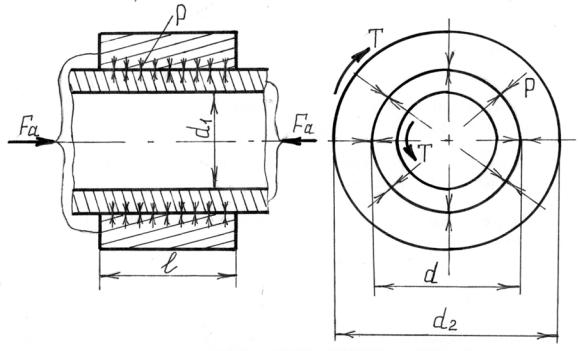
26
Рис. 4.2. Схема прессового соединения:
Р– давление на поверхность контакта, МПа;
Т– вращающий момент, Нмм; Fа – осевая сила, Н;
d – диаметр соединения, мм; l – длина сопряжения, мм; d1 – диаметр вала, мм; d2 – диаметр ступицы, мм.
Исходными данными являются: вращающий момент на ступице Т, Нмм; диаметр соединения d, мм; диаметр отверстия пустотелого вала d1, мм (для сплошного вала d1 = 0); диаметр (условный) ступицы d2, мм; длина
сопряжения l, мм.
Выбор посадок осуществляют в следующем порядке. Определяют среднее контактное давление р, МПа
р = |
2Тk |
, |
|
(4.1) |
||
|
||||||
|
|
πd2lf |
|
|
||
где k – коэффициент запаса сцепления (муфты соединительные k = 3, |
||||||
шкивы ременных передач k = 4, звездочки цепных передач k = 3,5, |
||||||
зубчатые колеса k = 4,5); |
|
|
|
|
|
|
f – коэффициент трения (табл.4.4). |
|
|
||||
|
|
|
|
|
Таблица 4.4 |
|
|
|
|
|
|
|
|
Материал соединяемых деталей |
|
|
Сборка |
|
|
|
|
|
Прессованием |
|
Нагревом |
|
|
Сталь-чугун |
|
0,08 |
|
0,14 |
|
|
Сталь-сталь |
|
0,08 |
|
0,14 |
|
27
Сталь-бронза, латунь |
|
|
|
|
|
|
|
0,05 |
|
|
0,07 |
|
|
||||
Чугун-бронза, латунь |
|
|
|
|
|
|
|
0,05 |
|
|
0,07 |
|
|
||||
Находят деформацию деталей δ, мм: |
|
|
|
|
|
|
|
|
|
||||||||
|
|
|
C |
1 |
|
C |
2 |
|
, |
|
|
|
|
(4.2) |
|
||
|
|
|
|
|
+ |
|
|
|
|
|
|
|
|||||
|
|
|
|
|
|
|
|
|
|
||||||||
|
|
|
δ = рd |
E1 |
E2 |
|
|
|
|
|
|
||||||
|
|
|
|
|
|
|
|
|
|
|
|
|
|||||
где С1 и С2 – коэффициенты жесткости соединяемых деталей: |
|
|
|||||||||||||||
C |
= |
1 + (d1 / d)2 |
−μ1; |
|
|
|
C |
|
= |
1 + (d / d2 )2 |
+μ |
|
. |
(4.3) |
|||
|
|
|
|
|
|
|
|||||||||||
1 |
|
1 −(d1 / d)2 |
|
|
|
|
|
2 |
1 −(d / d2 )2 |
|
2 |
|
|
|
Вприведенных формулах:
Е– модуль упругости: для стали – 2,1.105МПа; для чугуна – 0,5.105МПа;
для бронзы и латуни – 105МПа;
μ– коэффициент Пуассона: для стали – 0,3; чугуна – 0,25;
бронзы и латуни – 0,35.
Затем производят проверку на обмятие микронеровностей:
|
|
u = 5,5 (Rа1 + Rа2), |
|
|
|
(4.4) |
|||||
где u – поправка на обмятие, мм; |
|
|
|
|
|
|
|
|
|||
Rа1 и Rа2 – средние арифметические отклонения профиля |
|||||||||||
поверхностей (шероховатость) по табл. 4.5, мм. |
|
|
|
Таблица 4.5 |
|||||||
|
|
|
|
|
|
|
|
||||
|
|
|
|
|
|
|
|
|
|
|
|
Интервалы |
|
Отверстие |
|
|
|
Вал |
|
|
|
|
|
|
|
|
Квалитет |
|
|
|
|
|
|||
размеров, мм |
6, 7 |
|
8 |
9 |
6, 7 |
|
8 |
|
9 |
|
|
|
|
|
Шероховатость Ra, мкм |
|
|
|
|
|
|||
Св. 18 до 50 |
0,8 |
|
1,6 |
3,2 |
0,8 |
|
0,8 |
|
1,6 |
|
|
Св. 50 до 120 |
1,6 |
|
1,6 |
3,2 |
0,8 |
|
1,6 |
|
|
1,6 |
|
Св. 120 до 500 |
1,6 |
|
3,2 |
3,2 |
1,6 |
|
3,2 |
|
|
3,2 |
|
Проводят проверку на температурную деформацию (обычно при
подборе посадки зубчатых венцов червячных передач, которые нагреваются
при работе передачи до высоких температур): |
|
|
δt = d106 [(t2 - 20°) α2 - |
(t1 - 20°) α1], |
(4.5) |
где α – температурный коэффициент линейного расширения:
для стали – 12.10-6; для чугуна – 10.10-6; для бронзы, латуни – 19.10-6; t1 и t2 – средние объемные температуры соответственно обода
центра и венца колеса.