
4327
.pdf11
При стандартных размерах образца и прохождении через него 2000 см3 воздуха формула 2.2 примет вид
K = |
509 ,5 |
. |
(2.3) |
|
|||
|
F p t |
|
Для большей достоверности полученных результатов испытания провести не менее чем на трех образцах, для каждого из трех замесов. Результат определяется для каждого замеса.
2.8 Определение прочности
Показатели, характеризующие предел прочности при сжатии, растяжении, изгибе и срезе могут быть получены как для влажных, так и для сухих формовочных смесей. Для каждого метода испытаний используются специально подготовленные образцы и машины для испытаний.
Используемая нами испытательная машина модели 04116А (рис. 2.4) предназначена для определения предела прочности формовочных и стержневых смесей при сжатии, срезе и изгибе. Предел прочности на сжатие во влажном состоянии определяют на стандартном цилиндрическом образце диаметром 50±0.2 мм и высотой 50±0,8 мм, изготовленном в разъемной гильзе 13 на копре (рис. 2.2) аналогично образцу для определения газопроницаемости.
Испытуемый образец устанавливается на тарелку 12 и поджимается подвижным упором 10 до касания с диском 11. При этом образец не должен выступать за контуры посадочного места на тарелке и прижимного диска подвижного упора более, чем на 0,5 мм. Включить шнур питания машины в сеть переменного тока с напряжением 220 В, предварительно убедившись в подключении машины к контуру заземления.
На лицевой панели электронного блока 4 органы управления установить в исходное положение:
-тумблер "сеть" 9 - Вкл.;
-тумблер "Д" 8-двигатель компрессора - Вкл.;
-переключатель вида испытания "сжатие-изгиб" 7 в положение
сжатия;
-тумблер "И-С" 5 - измерения-сброс в положение "С". После чего на
индикаторе 6 появятся нули. Вращением подвижного упора поджать образец с усилием, не превышающим 10 Н до появления на индикаторе последней значащей цифры.
Переключением тумблера ""И-С" в положение "И" включить режим испытания. При этом включается двигатель компрессора 1, который нагнетает воздух в ёмкость, служащую для сглаживания пульсации давления. Далее воз-
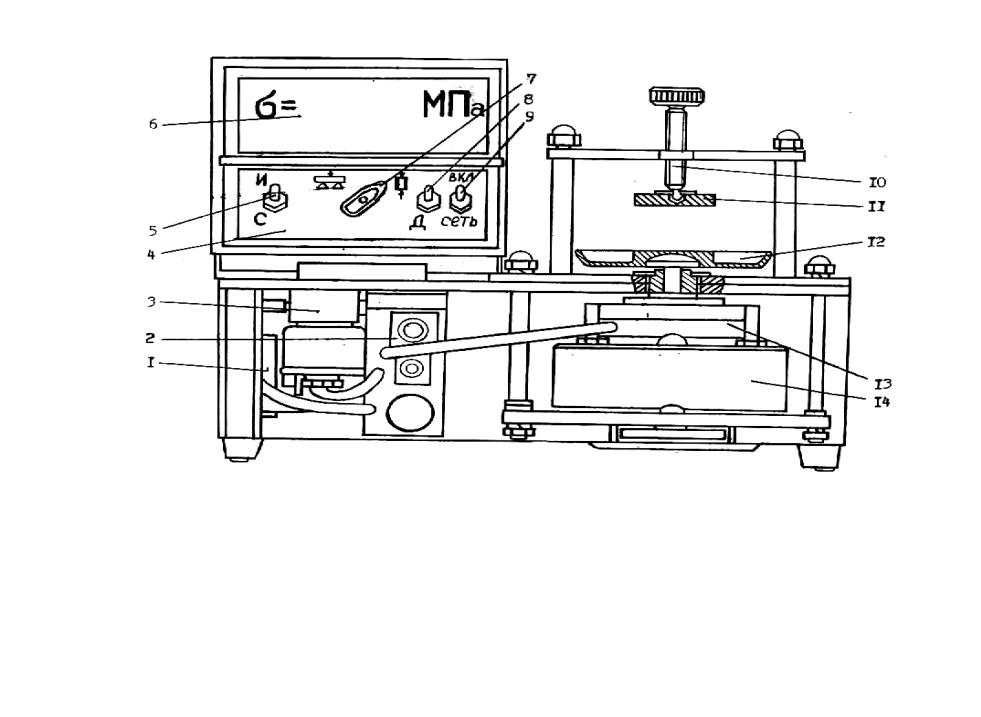
12
Рис. 2.4 Испытательная машина для определения предела прочности формовочной смеси:
1 - компрессор; 2 - дроссель; 3 - электропневмоклапан; 4 - электронный блок; 5 – тумблер ”И-С”; 6 - индикатор; 7 - переключатель; 8 – тумблер ”Д”; 9 - тумблер”сеть”; 10 - упор; 11 - диск; 12 - тарелка; 13 -
силовозбудитель; 14 - датчик
13
дух через дроссель 2 подается в рабочую камеру мембранного пневматического силовозбудителя 13. Пневмосистема содержит также регулятор скорости нарастания разрушающего усилия. Нарастание нагрузки, происходит автоматически. После разрушения образца воздух из рабочей полости силовозбудителя стравливается в атмосферу, двигатель компрессора отключается, нагнетание прекращается, а на цифровом индикаторе зафиксируется значение предела прочности при сжатии в МПа. Это число будет сохраняться до тех пор, пока тумблер "И-С" не будет переключен в положение "С" - сброс.
Испытания проводятся на трех образцах для какого из трех замесов, результаты усредняются.
2.9 Содержание отчета
2.9.1Дать краткую информацию о формовочных и стержневых материалах.
2.9.2Изложить общие вопросы приготовления формовочных смесей и
принципа их разделения по характеру использования.
2.9.3Привести общие сведения о свойствах формовочных смесей и их влияния на качество отливки.
2.9.4Описать приборы и методики определения влажности, газопроницаемости и прочности.
2.9.5Результаты исследований представить в табл. 2.2.
2.9.6Построить графики зависимости газопроницаемости и предела
прочности на сжатие от влажности формовочной смеси.
2.9.7 Сделать заключение о качестве испытанных формовочных смесей и возможности их использования для изготовления форм. При отклонениях полученных показателей от рекомендуемых (см. табл. 2.1) объяснить причины отклонений и дать рекомендации по приближению показателей к нормативным.
2.10 Контрольные вопросы
2.10.1Назовите материалы, входящие в формовочную и стержневую
смесь.
2.10.2Какие бывают смеси по характеру использования?
2.10.3Изложите технологию приготовления формовочных смесей.
2.10.4Перечислите свойства формовочных смесей и дайте им краткую
характеристику.
2.10.5 Изложите методику определения влажности, газопроницаемости и прочности.
2.10.6 Объясните устройство и принцип работы приборов для определения влажности, газопроницаемости и прочности.
14
2.10.7 Дайте анализ влияния влажности, состава основных материалов и добавок на свойства формовочных смесей.
2.10.8 Перечислите возможные виды брака в отливках, получаемые из-за низкого качества смесей, назовите причины их появления и дайте рекомендации по их устранению.
Таблица 2.2
Результаты испытаний
№ |
|
|
Величины показателей при определении |
|
||||
за- |
№ |
|
влажности |
|
газопроницаемос |
предела |
||
масса об- |
|
время |
давление |
коэфф. га- |
||||
меса |
образца |
|
прочности |
|||||
|
|
разца |
влажность |
прохож- |
воздуха |
зопрони- |
при |
|
|
|
после |
W,% |
дения |
р, мм |
цаемости |
сжатии |
|
|
|
высу- |
|
воздуха, |
вод.стол- |
К |
σсж, МПа |
|
|
|
шивания, |
|
t, мин |
ба |
|
||
|
|
|
|
|
||||
|
|
m2, г |
|
|
|
|
|
|
|
|
|
|
|
|
|
|
|
|
1 |
|
|
|
|
|
|
|
1 |
2 |
|
|
|
|
|
|
|
3 |
|
|
|
|
|
|
|
|
|
|
|
|
|
|
|
|
|
|
средняя |
|
|
|
|
|
|
|
|
величина |
|
|
|
|
|
|
|
|
1 |
|
|
|
|
|
|
|
|
2 |
|
|
|
|
|
|
|
2 |
3 |
|
|
|
|
|
|
|
средняя |
|
|
|
|
|
|
|
|
|
|
|
|
|
|
|
|
|
|
величина |
|
|
|
|
|
|
|
|
|
|
|
|
|
|
|
|
|
1 |
|
|
|
|
|
|
|
|
2 |
|
|
|
|
|
|
|
3 |
3 |
|
|
|
|
|
|
|
средняя |
|
|
|
|
|
|
|
|
|
|
|
|
|
|
|
|
|
|
величина |
|
|
|
|
|
|
|
|
|
|
|
|
|
|
|
|
|
|
3 ЛАБОРАТОРНАЯ РАБОТА № 2 |
|
|
ПОЛУЧЕНИЕ ОТЛИВОК В ПЕСЧАНОЙ ФОРМЕ И В КОКИЛЕ
3.1 Цель работы
3.1.1Изучить состав модельного комплекта.
3.1.2Освоить технологию изготовления песчаной формы.
3.1.3Изучить устройство и технологию литья в кокиль.
3.1.4Ознакомиться с составами огнеупорных покрытий (красок) и технологией их нанесения.
15
3.1.5Освоить технологию заливки литейных форм.
3.1.6Сравнить качество отливок, достоинства и недостатки обоих
способов литья.
3.2 Оборудование и материалы
3.2.1Модельный комплект.
3.2.2Опоки.
3.2.3Лабораторный смеситель (бегуны).
3.2.4Материалы для приготовления формовочной и стержневой смесей.
3.2.5Формовочный инструмент и приспособления.
3.2.6Кокиль.
3.2.7Материалы для приготовления огнеупорных покрытий (красок).
3.2.8Пульверизатор.
3.2.9Термошкаф для нагрева кокиля и сушки стержней.
3.2.10Плавильная, муфельная печь.
3.2.11Разливочный ковш.
3.3 Общая характеристика литейного производства
Продукцией литейного производства являются чаще всего сложные (фасонные) заготовки, называемые отливками. Отливки получают заливкой расплавленного металла в литейную форму, внутренняя рабочая полость которой имеет конфигурацию отливки.
После затвердевания и охлаждения отливку извлекают из литейной формы. При этом форму разрушают (песчаная форма) или разбирают на части для повторного использования (кокиль).
Отливки получают литьем в песчаную литейную форму, в оболочковую литейную форму, по выплавляемым моделям, в кокиль, под давлением, центробежным литьем и другими способами.
Наиболее универсальным, но менее точным является способ литья в песчаную форму. Специальными способами литья получают отливки повышенной точности, с малой шероховатостью поверхности и минимальными припусками на механическую обработку.
Выбор способа литья зависит от технологических возможностей и технико-экономических показателей.
3.4. Модельный комплект Модельный комплект - это совокупность технологической оснастки и
приспособлений, необходимых для образования в форме полости, соответствующей контурам отливки. В модельный комплект входят: литейная модель, модельные или подмодельные плиты, стержневые ящики, модели элементов литниковой системы, шаблоны, кондукторы и другие приспособления.
16
Опоки, штыри и скобы для их скрепления откосятся к вспомогательной оснастке.
Литейная модель (рис . 3.1) - приспособление, при помощи которого в литейной форме получают полости с формой и размерами, близкими к отливке. Они могут быть разъемными, неразъемными, с отъемными частями и др. В зависимости от требуемого количества отливок, их размеров и сложности для изготовления моделей обычно используют древесину, металлы, гипс, пластмассы и другие материалы. Особенности изготовления моделей см. в работе № 3.
Модельная плита представляет собой металлическую плиту, на которой укрепляется одна или несколько моделей с литниковой системой и выпорами, а также размещаются штифты для установки опок. Модельные плиты чаще бывают с моделями и элементами литниковой системы, закрепленными на них.
Подмодельные плиты - как правило гладкие или с элементами, позволяющими фиксировать модели и опоки.
Стержневые ящики (рис. 3.2)- приспособления для изготовления стержней. Они бывают цельные, вытряхные, разъемные и др.
Кондукторы применяют для сборки стержней, а также для удобства их установки в формы.
Шаблоны служат для проверки размеров форм и стержней.
3.5Требования к формовочным и стержневым смесям Качество отливок зависит от правильности выбора состава формовочных
истержневых смесей, которые должны обладать следующими свойствами: пластичностью, податливостью, хорошей газопроницаемостью, минимальной газотворной способностью, огнеупорностью, прочностью, противопригарностью, легкой выбиваемостью (особенно для стержневых смесей).
Для заливки алюминиевого сплава рекомендуется следующий состав и свойства формовочной смеси: содержание глины – 8…12%, влажность – 4…5%,
газопроницаемость – 25…80 ед., прочность на сжатие сырого образца - 0,03…0,05 МПа.
Стержневые смеси должны обладать еще более высокими свойствами. Например, газопроницаемость должна быть от 45 до 100 ед. в зависимости от сложности стержня. В таких случаях для изготовления стержней используют высококачественные кварцевые пески и связующие. Улучшить свойства стержней можно также сушкой, что часто используется.
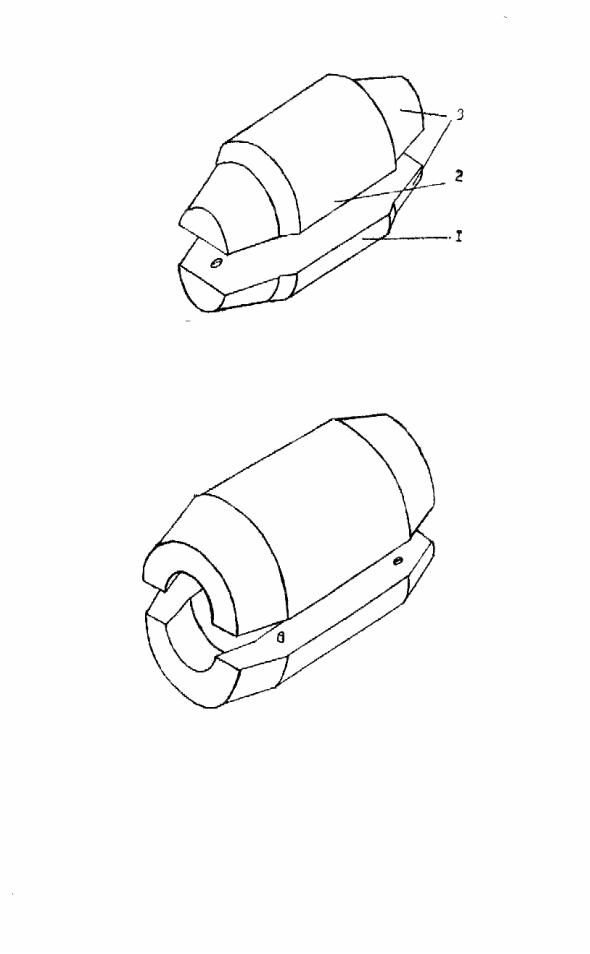
17
Рис. 3.1 Литейная модель (разъемная): 1,2 – нижняя и верхняя части модели; 3 – знаки
Рис. 3.2 Стержневой ящик (разъемный)
18
3.6 Порядок изготовления песчаной формы
3.6.1Разобрать стержневой ящик, очистить и посыпать припылом из графитового порошка его рабочую поверхность. Скрепить половинки ящика хомутом, поставить вертикально на подмодельную плиту и заполнить смесью, уплотняя ее трамбовкой. Разобрать ящик, вынуть стержень и положить его на 20…30 мин для сушки в сушильный шкаф при температуре 120…150 °С.
3.6.2На очищенную подмодельнуо плиту положить перевернутую на 180° нижнюю опоку, установить нижнюю половину модели детали (разъемом вниз), расположить сбоку модели питатели и посыпать внутреннюю поверхность в опоке тонким разделительным слоем сухого песка. Затем засыпать послойно формовочную смесь, периодически уплотняя
ее.Излишек смеси после уплотнения срезать линейкой вровень с кромками опоки.
3.6.3Перевернуть заполненную нижнюю опоку на 180° и установить на нее верхнюю опоку. Установить верхнюю половину модели в гнезда нижней, зафиксировать модели шлакоуловителя, стояка и выпора, посыпать тонким слоем сухого песка и засыпать формовочной смесью, постепенно уплотняя
ее.Около стояка ланцетами изготовить литниковую чашу и извлечь модели стояка и выпора.
3.6.4Снять верхнюю опоку и повернуть ее на 180°, уложить рядом с нижней. Аккуратно вынуть половинки модели детали и модели элементов литниковой системы, предварительно освободив их от возможного прилипания. После чего очистить кисточкой полости формы от осыпавшейся формовочной смеси и, установив стержень на знаковые части, собрать форму.
Литейная форма в сборе (рис. 3.3) подготовлена к заливке.
3.7 Устройство кокиля
Кокиль (от франц. сoquille) - металлическая форма, заполняемая жидким металлом под действием гравитационных сил. В отличие от разовой песчаной формы кокиль используется многократно.
Кокиль обычно состоит из нескольких деталей, и чем сложнее форма отливки, тем больше их количество. Кокиль для получения цилиндрической втулки (рис. 3.4) состоит из нижнего основания 1, вертикального стакана 2, двух разъемных полуформ 4, формирующих упрощенную литниковую систему - выпор 8, стояк 6 и литниковую чашу 5. Закрепляющая втулка 4 фиксирует положение полуформ относительно стакана.
Для формирования отверстия при заливке цветных сплавов используют металлический стержень 7, опирающийся на знаковые конусы в нижнем основании и разъемных полуформах.

19
Рис.3.3Литейнаяформавсборе:
1 – подмодельная плита; 2, 3 – нижняя и верхняя опоки; 4 – знаковая формообразующая поверхность; 5 – литейная форма; 6 – стержень; 7 – выпор; 8 – литниковый стояк; 9 – литниковаячаша;10–шлакоуловитель;11–питатель
Рис.3.4 Кокиль:
1 – основание; 2 – стакан; 3 – закрепляющая втулка; 4 – разъемные формы; 5 – литниковаячаша;6–литниковыйстояк;7–стержень;8-выпор
20
3.8 Подготовка кокиля к заливке
Перед заливкой поверхности рабочей полости и разъемы тщательно очищают от следов загрязнений, ржавчины, проверяют легкость перемещения подвижных частей, точность центрирования, надежность крепления. Перед нанесением покрытия кокиль нагревают в термошкафе до 150…180 °С. Затем на поверхность рабочей полости и металлического стержня наносят слой огнеупорного покрытия. Составы огнеупорных покрытий приводятся в табл. 3.1.
Краски наносят обычно пульверизатором. Попадая на поверхность нагретого кокиля, вода испаряется, а огнеупорная составляющая ровным слоем покрывает поверхность. Толщина покрытия 0,3…0,8 мм. Огнеупорные покрытия выполняют две функции: защищают поверхность кокиля от нагрева и схватывания с отливкой и позволяют регулировать скорость охлаждения отливки, а значит и процесс ее затвердевания, т.е. влияют на микроструктуру полученной отливки. Перед заливкой расплавленного металла кокиль снова нагревают до рабочей температуры, зависящей от заливаемого металла, толщины стенок отливки, наличия ребер. Для заливки алюминиевого сплава в кокиль несложной формы с толщиной стенки более 8
ммбез ребер рекомендуется нагрев кокиля до 200…250°С.
3.9Заливка форм
Вкачестве плавильной печи для алюминиевого сплава можно использовать, муфельную печь с температурой нагрева 750…780 °С. После выемки ковша и удаления шлаков температура снижается на 20…30 °С и при заливке составляет 730…750 °С, что на 100…120 °С выше температуры плавления. Сначала жидкий металл надо залить в кокиль, т.к. он нагрет и быстро остывает, а затем в песчаную форму. Металл заливают до его появления из выпоров.
3.10 Выбивка отливок Кокиль по сравнению с песчаной формой обладает большей
теплопроводностью, поэтому расплав и отливка охлаждаются быстрее. Чтобы облегчить выбивку металлического стержня и уменьшить его обжатие, после того как отливка приобретает достаточную прочность, производят "подрыв" стержня, т.е. частично извлекают его из отливки.