
4282
.pdf
11
РАСЧЕТ
1) Расход воды
По рис. 1. ориентировочный расход воды при осадке h=3 см и крупности гравия до 40 мм составляет 173 л. С учетом корректировки на использование мелкого песка воды потребуется
1) Определение водоцементного отношения Водоцементное отношение определяется из формулы 1
|
В |
|
0,55 Rц |
|
|
|
|
|
0,55х250 |
0,51 |
|||
|
Ц |
|
0,5х0,55Rц |
|
|
R28 |
|
0,5х0,55х250 200 |
|||||
|
|
|
|
|
|
||||||||
3) расход цемента |
|
|
|
|
|
|
|
|
|
|
|||
|
|
|
ЦВ : |
|
|
В |
|
183 : 0,51 |
357,5 |
|
|||
|
|
|
|
|
Ц |
|
|||||||
|
|
|
|
|
|
|
|
|
кг |
|
|||
|
|
|
|
|
|
|
|
|
|
|
|
|
|
4) Определение пустотности гравия по формуле 3 |
|
||||||||||||
|
|
|
|
|
|
|
ρ |
|
|
|
|
|
|
|
|
|
Vк |
1 |
|
нк |
1 |
1,70 |
0,41 |
|
|||
|
|
|
|
ρк |
2,90 |
|
|||||||
|
|
|
|
|
|
|
|
|
|
|
5) Определение соотношения между песком и гравием по формуле 2
ρ
Х |
V |
нп |
α |
0,411,55 |
х1,51 0,57 |
У |
к |
ρ |
1,70 |
|
|
|
|
нк |
|
|
Здесь =0,51, определен по табл. 1 интерполированием.
6) Плотность смеси заполнителей определяется по формуле 4
|
|
Х ρ |
п |
ρ |
к |
|
|
|
|
|
ρ |
|
У |
|
|
|
0,57 х2,70 |
2,90 |
|
||
|
|
|
|
|
|
|||||
|
см |
|
Х |
|
1 |
|
0,57 |
1 |
2,83 |
|
|
|
|
|
|
|
|||||
|
|
|
У |
|
|
|
|
|
кг/л |
|
|
|
|
|
|
|
|
|
|
7) Расход заполнителей на 1 м3 бетонной смеси по формуле 5
Расход абсолютно сухого гравия по формуле 6
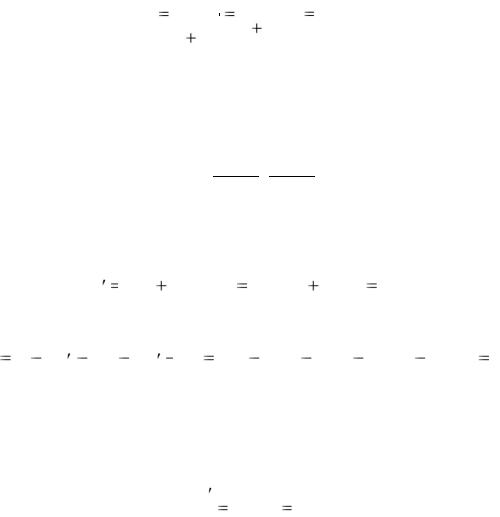
|
|
|
|
|
12 |
|
|
Г |
|
Р |
1991 |
1268 |
|||
|
|
|
|
|
|
||
1 |
|
Х |
|
1 0,57 |
|||
|
|
|
|||||
|
|
У |
|
|
кг |
||
|
|
|
|
|
9)Расход абсолютно сухого песка
10)Номинальный состав бетона по весу
11)Расход песка с учетом влажности по формуле 8
12)Расход гравия с учетом влажности по формуле 9
|
Г |
Г( 1 |
0,01Wк ) |
1268( 1 |
0,02 ) |
1293кг |
|||||||||
13) |
Расход воды для производственного состава бетона |
||||||||||||||
В В ( П П ) |
( Г |
Г ) |
183 |
(744 |
|
723) |
( 1293 1268) 137л |
||||||||
14) |
Производственный состав бетона |
|
|
|
|
||||||||||
|
|
|
|
|
|
|
|
||||||||
При этом составе бетона водоцементное отношение равно |
|||||||||||||||
|
|
|
|
В |
137 |
|
|
0,38 |
|
||||||
|
|
|
|
|
|
|
|
|
|
|
|
|
|||
|
|
|
|
|
|
|
|
|
|
|
|
|
Ц357,5
ВЫВОД: производственный расход материалов на 1 м3 бетона составляет: цемента М 250 – 357,5 кг, песка – 744 кг, гравия – 1293 кг, воды – 137 л.
Контрольные вопросы
1.Порядок расчета состава тяжелого бетона.
2.Что такое номинальный и производственный состав тяжелого бетона?
3.Что называется бетоном?
4.Чем отличается бетон от строительного раствора?
5.Область применения бетона в строительстве.
6.Сущность железобетона.
13
Лабораторная работа № 2
Тема: Испытание тяжелого бетона Цель работы: получение в лабораторных условиях бетонной смеси, тре-
буемой подвижности и заданной марки бетона.
Экспериментальная часть.
Объем замеса – 7 л, что несколько превышает объем 2-х стандартных образцов, которые будут изготовлены в процессе выполнения этой лабораторной работы. Чтобы получить необходимое количество материалов для замеса, нуж-
но производственный расход составляющих на 1 м3 бетона умножить на 0,014.
Замес изготавливают в следующем порядке:
1) отвешивают необходимое количество песка и высыпают на боек (под-
дон), отвешивают цемент, добавляют его к песку и перемешивают до получения однородной смеси;
2)добавляют требуемое количество крупного заполнителя и всю смесь перемешивают до тех пор, пока крупный заполнитель не будет равномерно распределен по всему объему;
3)отмеривают требуемое количество воды и выливают ее в смесь не-
большими порциями при одновременном перемешивании. Затем энергично перемешивают смесь до получения однородной массы.
Подбор бетонной смеси требуемой подвижности Подвижность бетонной смеси зависит от количества цементного теста, от
зернового состава мелкого и крупного заполнителей, формы и характера по-
верхности их зерен, от соотношения заполнителей, от вида цемента, содержа-
ния воды в смеси и других факторов. Практически регулировать подвижность бетонной смеси можно только количеством цементного теста, т.к. в противном случае меняется состав бетона, а в следствие этого и его физико-механические свойства.
Например, если увеличить содержание воды, то изменится водоцементное отношение, а следовательно, и марка бетона.
14
Показателем подвижности бетонной смеси является осадка бетонной смеси, освобожденной от стандартного конуса.
Стандартный конус из листовой стали высотой 300 мм, диаметром в ниж-
нем основании 200 мм и верхнем 100 мм смачивается водой, устанавливается на боек и прижимается к дну его. Бетонную смесь укладывают в конус в три приема слоем по 10 см, при этом каждый слой 25 раз штыкуют стержнем диа-
метром 12 мм. Затем излишки бетона снимают с верхней горловины конуса.
Конус осторожно поднимают вертикально вверх и устанавливают рядом с бе-
тонной смесью.
Измеряют осадку конуса с точностью до 0.5 см (рис. 2.)
Если осадка конуса окажется меньше требуемой, добавляют в смесь оп-
ределенный процент воды и цемента (5–10 % от первоначального содержания).
Бетонную смесь вновь тщательно перемешивают и определяют осадку конуса.
Цемент и воду добавляют до тех пор, пока осадка конуса не достигнет требуе-
мого значения.
Если осадка конуса окажется больше требуемой, то это означает перерасход цемента. В бетонную смесь нужно добавлять песок и цемент и повторять эксперимент до достижения необходимой консистенции.
По техническим условиям бетон подразделяется четыре вида:
1) жесткий с осадкой конуса 0, идет на подготовку под полы, фундамен-
ты;
2) малоподвижный с осадкой конуса 1–3 см, идет на изготовление желе-
зобетонных конструкций с редко расположенной арматурой;
3) подвижный с осадкой конуса 4–15 см, идет на изготовление железобе-
тонных конструкций среде и сильно насыщенных арматурой, тонкостенных конструкций;
4) литой с осадкой конуса свыше 15 см, идет на изготовление конструк-
ций подводного бетонирования.

15
Рис. 2. Измерение осадки бетонной смеси:
1 – стандартный конус; 2 – бетонная смесь; 3 – рейка; 4 – линейка;
5 – дно бочка По окончании эксперимента необходимо классифицировать полученную
бетонную смесь по ее подвижности и, в случае необходимости, уточнить производственный состав бетона и расход материалов.
Изготовление опытных образцов Укладку бетонной смеси в формы производят не позднее 45 мин с момен-
та затворения. Требуется изготовить 4 стандартных образца в виде куба с раз-
мером ребра 150 мм. Для этого стальные формы смазывают машинным маслом и бетонную смесь насыпают в гнезда формы с некоторым избытком. Вибриру-
ют до момента прекращения оседания смеси и появления на поверхности це-
ментного молока. После чего верхнюю поверхность образца заглаживают вро-
вень с краями формы и маркируют.
Образцы хранят в формах. Укрытых влажной тканью не менее одних суток, затем их вынимают из формы и помещают во влажную среду, где они на-
ходятся до испытания. Время хранения в общей сложности должно составить
28 суток.
16
Бетоны имеют широкий диапазон свойств в зависимости от производст-
венного назначения. Бетоны разделяют на конструкционные - для изготовления бетонных и железобетонных внутренних и наружных конструкций промыш-
ленных и гражданских зданий и инженерных сооружений (колонны, балки,
плиты и др.); гидротехнические – для строительства плотин, шлюзов, облицов-
ки каналов и других гидротехнических сооружений; дорожные – для строи-
тельства дорожных и аэродромных оснований и покрытий; специальные – для использования при устройстве жароупорных покрытий, кислотоупорных изде-
лий и т.п.
Каждой разновидности бетона присущи свои особенности: гидротехни-
ческий должен быть предельно плотным, водонепроницаемым, морозостойким,
стойким против коррозии, тогда как бетон для жилищного строительства, тем более ограждающих конструкций (стен, перекрытий), должен быть малотепло-
проводным, поддерживать и сохранять хорошую звукоизоляцию, а бетоны до-
рожные должны быть не только морозостойкими, но и устойчивыми к динами-
ческим воздействиям транспортных нагрузок, к истираемости и износу под ко-
лесами автомобилей в сложных климатических условиях.
Требования к бетонам в процессе эксплуатации обуславливает точный расчет и дозировку всех составляющих бетонной смеси при изготовлении.
Контрольные вопросы
1.Классификация бетонов по объемной массе.
2.Классификация бетонов по назначению.
3.Ячеистые бетоны.
4.Специальные бетоны.
5.Область применения бетонов в строительстве.
6.Как определить подвижность бетонной смеси?
7.Классификация бетонов по осадке конуса.
8.Расскажите о ходе выполнения работы.
17
Лабораторная работа № 3
Тема: Испытание извести Цель работы: определение скорости и температуры гашения извести.
Сырьем для производства воздушной извести служат плотные известня-
ки, ракушечники, мел, доломитизированные породы при условии, что содержание глинистых примесей в них не превышает 6 %. Сырье обжигают при темпе-
ратуре 1000–1200 оС до полного удаления углекислого газа. Обжиг известняка проводят в шахтных речах, которые надежны в эксплуатации, позволяют использовать местные виды топлива и требуют меньшего его расхода. После обжига получают комовую известь или известь – кипелку.
Известняки при обжиге разлагаются на известь СаО и углекислый газ СО2, который полностью удаляется. Реакция разложения известняка обратимая:
Если комовую известь измельчить, то получится молотая негашеная известь. Более распространена в строительстве известь гашеная, получаемая путемзатворения водой негашеной извести
При выделении теплоты часть воды превращается в пар, под воздействием которого комовая известь превращается в тончайшие частицы гидратной извести размером в несколько микрон с высокой удельной поверхностью.
Гашение извести в условиях стройплощадки производится в творильных ящиках с сеткой для сцеживания разжиженного известкового теста (известко-
вого молока) в гасильную яму, где оно выдерживается длительное время. В за-
водских условиях известь гасится в специальных барабанных гасителях.
Известь классифицируется по скорости гашения и максимальной температуре гашения.
18
Скорость гашения – это время в минутах от момента затворения негаше-
ной извести до момента, соответствующего началу снижения температуры. По этому фактору известь подразделяется на:
1)быстрогасящуюся со скоростью гашения до 8 мин;
2)среднегасящуюся со скоростью гашения от 8 мин до 25 мин;
3)медленногасящуюся со скоростью гашения свыше 25 мин;
По максимальной температуре гашения известь подразделяется на:
1)высокоэкзотермическую (температура гашения свыше 70 оС);
2)низкоэкзотермическую (температуру гашения до 70 оС).
Вяжущие свойства извести проявляются в основном из-за того, что на воздухе происходит реакция
Са(ОН)2+СО2=СаСО3+Н2О
Так как карбонат кальция (СаСО3) не является водостойким соединением,
то изделия на основе извести применяются в конструкциях, не подвергающихся увлажнению.
Методика выполнения работы
Негашеную известь измельчают в порошок, отвешивают 10 г и высыпают
вхимический стакан (1).
Встакан, заранее помещенный в термос (2), осторожно влияют 20 см3 воды. Стакан закрывают пробкой (3) с термометром (4) так, чтобы он был погру-
жен в известковое тесто (5) (рис. 3.) и замечается время.
Через каждые 30 с отмечаются показания термометра и заносятся в табл.
4.
Таблица 4
Журнал замеров
Время |
0 |
0,5 |
1 |
1,5 |
2 |
2,5 |
3 |
3,5 |
4 |
4,5 |
5 |
И |
|
|
мин |
мин |
мин |
мин |
мин |
мин |
мин |
мин |
мин |
мин |
т.д. |
|
|
|
|
|
|
|
|
|
|
|
|
|
Температура |
|
|
|
|
|
|
|
|
|
|
|
|
|
|
|
|
|
|
|
|
|
|
|
|
|

19
Рис. 3. Прибор для определения температуры и скорости гашения извести: 1 – химический стакан; 2 – термос, 3 – пробка, 4 – термометр,
5 – известковое тесто По табл. 4 строится график изменения температуры во времени и произ-
водится классификация извести по скорости и максимальной температуре гашения ее.
Контрольные вопросы
1.Классификация вяжущих веществ.
2.Расскажите о ходе выполнения работы.
3.Классификация извести по скорости гашения.
4.Классификация извести по максимальной температуре гашения.
5.Как используется известь в строительстве.
20
Лабораторная работа № 4
Тема: Испытание строительного гипса Цель работы: изучение свойств строительного гипса.
Гипсовые вяжущие вещества условно разделяют на строительный, формовочный и высокопрочный гипсы.
Гипс строительный является продуктом обжига тонкоизмельченного дву-
водного гипса или, реже, тонкого помола β – полуводного гипса. Гипс формо-
вочный состоит также из β – модификации полугидрата сульфата кальция, от-
личаясь от гипса строительного большей тонкостью помола. Гипс высокопроч-
ный является продуктом тонкого помола α – полугидрата, получаемого в ре-
зультате тепловой обработки в условиях, в которых вода из гипса выделяется в капельно-жидком состоянии.
Отличительной особенностью гипсовых вяжущих веществ является их низкий срок схватывания, что вызывает определенное неудобство при произ-
водстве строительных работ. По срокам схватывания они разделяются на быст-
ро-, нормально- и медленнотвердеющие. Для продления сроков схватывания в гипсовое тесто нередко вводят добавки-замедлители, например, каратиновый клей, сульфитно-дрожжевую бражку и др.
Вышеуказанные разновидности гипсовых веществ применяют для раз-
личных целей. Строительный и формовочный с большим успехом используют-
ся при производстве гипсовых перегородочных панелей, сухой штукатурки.
Гипсолитных деталей, вентиляционных коробов, огнезащитных и звукопогло-
щающих изделий. Широкое использование всех этих изделий обуславливается строительной влажностью воздуха не более 60 %. Так как увлажнение гипсово-
го изделия всегда увязано с понижением прочности и ростом необратимых пла-
стических деформаций. Высокопрочный гипс используют для изготовления де-
коративных и отделочных материалов, например, искусственного «мрамора»,
штукатурных растворов, устройства бесшовных полов и подготовки под лино-
леум.