
3597
.pdfПРАКТИЧЕСКАЯ РАБОТА №5
ОПРЕДЕЛЕНИЕ КИНЕМАТИЧЕСКИХ И ГЕОМЕТРИЧЕСКИХ ПАРАМЕТРОВ КАНАТНЫХ МЕХАНИЗМОВ
Цель работы: На основе кинематических и геометрических параметров определить рабочие характеристики лебедок.
В лесной промышленности широко применяются лебедки для привода канатных и канатно-блочных систем и механизмов. Лебедки бывают одноступенчатые и многоступенчатые, однобарабанные и многобарабанные, однонаправленные и реверсивные, прямонаправленные и разворотные.
Трелевочная лебедка состоит из двигателя, холостого трелевочного барабана, рабочего барабана, разворотного рабочего барабана, разворотного возвратного барабана, редуктора, коробки передач и электрогенератора.
Требуется: определить канатоемкость барабана; скорость движения каната; тяговое усилие барабана; производительность лебедки.
Количество витков каната, расположенных по длине барабана по горизонтали определяется:
iв = |
lб |
ϕ ,шт. |
(5.1) |
|
|||
|
dк |
|
|
где lб - длина барабана, м (принимается по |
согласованию с |
||
преподавателем); |
|
dк - диаметр каната, м, [1];
ϕ - коэффициент не плотности укладки витков на барабане, ϕ = 0, 7 −0,92 ; Количество рядов каната, расположенных по вертикали (с учетом запаса
2 dк между ребордой и верхним рядом навивки)
iр = |
(D1 |
−D2 )−4dк |
, шт. |
(5.2) |
|
2dк |
|||
|
|
|
|
|
где D1 - диаметр реборд барабана; мм. |
|
|
||
D2 - диаметр барабана, мм, D2 =300 −450 . |
|
|
||
Общее количество витков на барабане: |
|
|
||
i = iр iв , шт |
|
(5.3) |
Средняя длина одного витка каната, навиваемого на барабан:
21
lср = |
π(D1 +D2 |
−4dк ) |
|
|
|
|
, мм |
(5.4) |
|
2 |
|
Общая канатоемкость барабана определяется:
L = i lср , мм (5.5)
Скорость движения каната и тяговое усилие необходимо определять для первого и последнего рядов витков. При многорядной навивке каната на барабан скорость его движения неодинакова на разных рядах витков.
Для первого ряда:
νmin = |
π (D2 +dк ) nб |
,м/с |
(5.6) |
||
|
60 1000 |
||||
|
|
|
|
|
|
Для последнего ряда: |
|
π (D1 −4dк ) nб |
|
|
|
νmax = |
|
,м/с |
(5.7) |
||
|
60 1000 |
|
|||
|
|
|
|
|
Вследствие того, что канат навивается на барабан лебедки в несколько рядов, скорость движения каната всё время изменяется, а, следовательно, изменяется и величина тягового усилия.
Ρmax = Ν η , Кн |
(5.8) |
νmin
где Ν - мощность, расходуемая барабаном, кВт берется [1]; η - КПД передаточного механизма лебедки, η = 0,92 .
Производительность лебедки в смену на трелевке определяется:
Πсм = |
(Τ−tпз ) |
ϕ1 ϕ2 Qn |
(5.9) |
||||||||
|
l |
ср |
+ |
|
l |
ср |
+t |
+t |
|
||
|
|
|
|
|
|||||||
|
|
|
|
|
2 |
|
|||||
|
|
|
|
|
|
|
|
||||
|
|
νx |
|
ν |
1 |
|
|
||||
|
|
|
гр |
|
|
|
|||||
где t1 -время прицепки (сбора) пачки, мин. определяется по формуле: |
|
||||||||||
|
|
|
|
t1 = а0 Qn , мин |
(5.10) |
||||||
t2 - время отцепки пачки |
|
|
|
|
|
|
|
|
|
|
|
|
|
|
|
t2 =b0 +c0 Qn ,,мин, |
(5.11) |
где а0 =3,5, b0 =2,9, c0 =0,24коэффициенты, зависящие от среднего объема хлыста.
Qn - средний объем трелюемой пачки, м3 принимаем из справочной литературы [1];
22
ϕ1 - коэффициент использования рабочего времени, ϕ1 = 0,81−0,85; ϕ2 - коэффициент использования тягового усилия лебедки, ϕ2 = 0, 75 −0,8 ; Τ - продолжительность рабочей смены, Τ = 400 −480мин;
tпз - время на подготовительно-заключительные работы, tпз = 40 −50мин; lср - среднее расстояние трелевки, принимается по согласованию с
преподавателем, м;
νx - средняя скорость подачи прицепного оборудования к месту чеперовки, м/мин;
νгр - средняя скорость рабочего каната с пачкой, м/мин.
Отчет по практической работе №5 должен содержать:
1.Исходные данные к работе, согласно индивидуальному заданию
2.Расчет основных формул согласно индивидуальному заданию и построение графика.
3.Вывод о проделанной работе.
ПРАКТИЧЕСКАЯ РАБОТА №6
РАСЧЕТ ОСНОВНЫХ ЭЛЕМЕНТОВ ТЕХНОЛОГИЧЕСКОГО ОБОРУДОВАНИЯ ЛЕСОПОГРУЗЧИКОВ
Цель работы: Определить основные параметры технологического оборудования лесопогрузчика.
Площадь зева захвата определяется по той же формуле, что и для грейферных захватов. Расстояние между рычагами захвата выбирают из условия устойчивого положения груза на рычагах с учетом различной длины лесоматериалов с тем, чтобы центр тяжести груза находился между рычагами. При погрузке деревьев и хлыстов расстояние рекомендуется принимать в пределах от 2,0 до 3,0 м, при погрузке бревен - 1,5-2,5 м.
Подъем груза челюстным захватом происходит в два приема: первый - груз сдвигается при горизонтальном движении захвата и под него подводится нижняя челюсть, второй - нижняя челюсть, вращаясь, поднимается и захватывает части груза.
Момент, развиваемый гидроцилиндрами относительно оси вращения
23
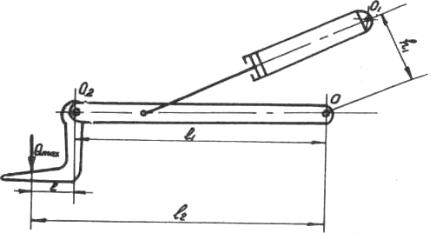
стрел ы (рис. 6. 1), определяется по формуле: |
|
М = n Pшт р η |
(6.1) |
где n - ч исло цили ндров, поднимающих стрелу; |
|
Pшт - усилие, развиваемое гидроцилиндром при |
работе штоковой |
полостью, Н;
h - плечо приложения силы гидроцилиндра, м;
η - коэф фициент полезного действия оси поворота, η = 0,99 .
Рисунок 6.1 Схема расчета гидроцилиндров подъема стрелы
челюстного погрузчика
Для определения силы тяж ести по днимаемого груза составляется сумма моментов относительно точки О и приравнивается к нулю:
∑Мо = М −qcl1 −Ql2 = 0 |
(6.2) |
||
Откуда |
|
|
|
Q = |
М −qcl1 |
(6.3) |
|
l2 |
|
||
где qc - сила тяжести стрелы с захватами и |
гидроц илиндрами поворота |
челюстей, Н. Данная ве личина оп ределяется по формуле представле нной ниже:
|
qc = Gц +Gк +Gв +Gзв +Gз +Gтр |
(6.4) |
|
где Gц - сила тяжести цепи, Gц =1300 −1400Н ; |
|
||
Gк - сила тяжести клыков захвата, Н; |
|
||
Gв |
- сила тяжести шлицевых валов, Gв =1400Н |
; |
|
Gзв |
- сила тяжести звездочки, Gзв |
=18 0 −200Н ; |
|
Gз |
- сила тяжести захвата, Gк +Gз |
=1 4800Н ; |
|
Gтр |
- сила тяжести труб стрелы, Gтр = 3000Н . |
|
l1 - длина стрелы, м;
l2 - длина стрелы плюс челюсть захвата, м
24
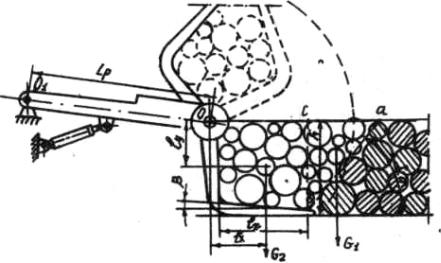
Общая си ла тяжести сдвигаемого груза, Н (рис. 6.2) складывается из силы тяжести части штабеля или призмы и си лы тяжести груза, находящегося над нижней челюстью, т.е.
|
|
|
G = G1 +G2 |
|
|
|
(6.5) |
||
где |
|
|
|
|
|
|
|
|
|
|
|
G1 = 0 ,5 ctgαo h2 lср |
kп |
γ |
|
(6.6) |
|||
|
|
|
|
|
|
|
g |
|
|
|
|
|
G2 |
= h lr lср |
kп |
γ |
|
|
(6.7) |
|
|
|
|
|
|
g |
|
|
|
где |
αo - |
угол естественного |
откоса |
для круглых лесоматериалов, для |
|||||
деревь ев |
и |
хлыстов |
αo = 50 ÷650 |
(0,87 ÷1,13 рад) , |
для |
бревен |
|||
αo = 35 ÷450 (0,6 ÷ 0,75рад) ; |
|
|
|
|
|
|
|
||
h - высота штабеля, призмы или слоя, м; |
|
|
|
|
|||||
lср |
- длина нижней челюсти, м; |
|
|
|
|
|
Рисунок 6.2 Схема расчета челюстного захвата
lr - горизонтальн ая проекция нижней челюсти, м; |
|
kп - коэффициент полнодревесности штабеля, м; |
|
γ - плотность древесины, т/м3. |
|
Усилие на штоках гидро цилиндров поворота захвата можно |
найти, |
составив сумм у моментов относительно точки О2 и приравняв ее к нулю: |
|
∑Мо 2 =Qmax − Pшт Rзв ηзв |
(6.8) |
отсюда |
|
25
Pшт = |
Qmax l |
(6.9) |
|
Rзв ηзв |
|||
|
|
где Rзв - радиус звездочки механизма поворота, м;
ηзв - коэффициент полезного действия цепного механизма поворота,
ηзв 0,87
Наибольший момент, развиваемый приводом челюсти при сжатии пачки, равен:
Mкр = n1 Pшт Rзв |
(6.10) |
где n1 - число цилиндров поворота.
Давление масла в цилиндре поворота челюсти определяется по следующее зависимости:
Pм |
= |
Pшт.пов |
(6.11) |
|
Sв ηц |
||||
|
|
|
Отчет по практической работе №6 должен содержать:
1.Исходные данные к работе, согласно индивидуальному заданию
2.Расчет основных формул согласно индивидуальному заданию.
3.Вывод о проделанной работе.
ПРАКТИЧЕСКАЯ РАБОТА №7 РАСЧЕТ ОСНОВНЫХ ЭЛЕМЕНТОВ ПРОДОЛЬНЫХ
ТРАНСПОРТЕРОВ Цель работы: Произвести расчет основных элементов продольных
транспортеров
К основным параметрам транспортеров относятся: длина и высота транспортера, скорость и тип тягового органа. Скорость тягового органа можно найти из формулы определения производительности транспортера:
ϑ = |
Пч l |
|
|
, м/с |
(7.1) |
|
3600 |
φ φ |
2 |
V |
|||
|
|
1 |
|
|
|
где Пч – часовая производительность, принимается значение по технической характеристики [1];
l – размер груза в направлении его движения, м;
φ1 - коэффициент использования рабочего времени, φ1 = 0,85 ;
26
φ2 |
– коэффициент заполнение тягового органа |
|
||||||
|
φ = |
l |
|
|
|
|
|
(7.2) |
|
i +l |
|
|
|
|
|
||
|
2 |
|
|
|
|
|
|
|
i – расстояние между рабочими торцами бревен и досок, м; |
|
|||||||
|
i = 0,1l |
|
|
|
|
|
(7.3) |
|
V |
- средний объем единицы продукции, м3 определяется по следующей |
|||||||
зависимости: |
|
|
|
|
|
|
|
|
|
V = |
πd |
2 |
l |
(7.4) |
|||
|
4 |
|
|
|||||
|
|
|
|
|
|
|
|
|
d – диаметр бревна, м. |
|
|
|
|
|
|
|
|
Общая длина продольного транспортера определяется по формуле: |
||||||||
|
L = Lн + Lз + Lр + Lд |
(7.5) |
||||||
где Lн - горизонтальная проекция наклонных участков транспортера, м; |
||||||||
Lз |
- длина загрузочной части транспортера, Lз =10 ÷12 м; |
|
||||||
Lд |
- длина части транспортера, занятая приводной станцией и натяжным |
|||||||
устройством, Lд = 2 ÷5 м; |
|
|
|
|
|
|
|
|
Lр |
- длина разгрузочной части транспортера, м. Определяется по |
|||||||
следующей зависимости: |
|
|
|
|
|
|
|
|
|
Lр = Lф = nмL +a(nм −1) +b( |
nшт |
-1) |
(7.6) |
||||
|
|
|||||||
|
|
|
10 |
|
|
|||
где Lф - фронт штабелей, м; |
|
|
|
|
|
|
|
|
nм |
– число штабелей, nм =10 −120 шт; |
|
||||||
L - длина бревна, м; |
|
|
|
|
|
|
|
|
a – расстояние между штабелями от 1,5 до 2 м; |
|
|||||||
b – расстояние между группами штабелей от 3 до 5 м; |
|
|||||||
nшт – число групп штабелей от 10 до 80. |
|
|||||||
Тяговое усилие определяется по следующей зависимости: |
|
|||||||
|
Pтяг = Pн +(gт Lp μ +n G) К |
(7.7) |
||||||
где Pн - монтажное натяжение тягового устройства Pн = 2000 ÷3000Н ; |
||||||||
gт – сила тяжести одного погонного метра тягового |
устройства, в |
|||||||
пределах от 240 до 420Н; |
|
|
|
|
|
|
|
n - число роликов под нижней ветвью транспортера, n =30 −50 шт;
27
μ |
– |
коэффициент |
трения скольжения |
траверс |
по направляющей, |
μ = 0, 2 −0,3 ; |
|
|
|
|
|
G |
- |
сила тяжести |
единицы материала, |
которое |
можно узнать из |
следующего выражения: |
|
|
|
||
|
|
|
G =V g |
|
(7.8) |
где V - объем единицы продукции, м3; g - ускорение свободного падения, м/с2.
k – коэффициент характеризующий угол наклона транспортера – 0,8-1,1. Необходимая мощность электромотора привода можно найти по
формуле: |
|
|
|
N = |
n1 Pтяг ϑ |
(7.9) |
|
η |
|||
|
|
где ϑ - окружная скорость ведущей звездочки, ϑ = 0,1−0, 4м/ с; η - коэффициент полезного действия двигателя, η = 0,93 ;
n1 - поправочный коэффициент, n1 =1,1÷1,3. Длину секций транспортера можно найти:
l = |
lp |
|
|
(7.10) |
||
с |
||||||
i |
|
|||||
Количество двигателей секций транспортера |
|
|||||
C = |
|
N |
|
(7.11) |
||
Nуст |
||||||
|
|
|||||
где N уст - установочная мощность транспортера, |
Nуст =1,5N |
Отчет по практической работе №7 должен содержать:
1.Исходные данные к работе, согласно индивидуальному заданию
2.Расчет основных формул согласно индивидуальному заданию.
3.Вывод о проделанной работе.
ПРАКТИЧЕСКАЯ РАБОТА №8
РАСЧЕТ УПРАВЛЯЮЩИХ ПАРАМЕТРОВ КРУГЛОПИЛЬНЫХ СТАНКОВ ДЛЯ РАСПИЛОВКИ ДРЕВЕСИНЫ
Цель работы: произвести расчет основных параметров круглопильных станков при заданных характеристиках предмета труда т параметрах рабочих
28
органов. Выбрать двигатель привода механизма пиления раскряжевочной установки.
Определение размеров круглой пилы, потребной мощности двигателя и производительности балансирного станка. Подача под пилу производится транспортером с коническими роликами. Расчет круглопильных станков для поперечной и продольной распиловки начинается с определения диаметра пильного диска:
D = d +2(dmax +a +e + f ) ,м |
(8.1) |
где d - диаметр шкива, см, d = 40 ÷60см;
a - запас на неровность обрабатываемой древесины, м;
dmax |
- максимальный диаметр хлыста, |
бревна, |
кряжа или толщина |
заготовки, м; |
|
|
|
e - запас на затачивание пилы, e = 0,02 ÷0, 03м; |
|
||
f |
- запас на размещения ограждения |
ремня, |
f = 0,02 ÷0,04м. Если |
ограждение не мешает процессу пиления, то f = 0.
Круглые пилы выпускаются диаметром до 1,6 м. Для распиловки балансов и рудничной стойки используют пилы диаметром от 1-1,25м, для раскряжевки хлыстов и разделки дров 1,5-1,6м. Хлысты и бревна диаметром более 0,6 м распиливаются двумя круглыми пилами или одной круглой пилой и второй с цепным аппаратом, находящимися в одной плоскости.
Толщина пил определяется в зависимости от диаметра пильного диска:
при D ≤1,0м толщина пилы |
S = |
D |
,мм |
(8.2) |
|||
250 |
|||||||
при D ≤1, 0 ÷1, 2м толщина пилы |
S = |
D |
|
||||
|
|
,мм |
(8.3) |
||||
275 |
|||||||
при D ≤1, 0м толщина пилы |
S = |
D |
,мм |
(8.4) |
|||
300 |
|
||||||
Ширина пропила с учетом развода зубьев: |
|
|
|
||||
в = S +1, мм ,мм |
|
|
(8.5) |
||||
Производительность станка зависит от длительности цикла: |
|
||||||
t/ = (t1 +t2 )n +t3 |
|
|
(8.6) |
где: t/ - общее время, затрачиваемое на распиливание кряжа на несколько
29

частей;
t1 - время на один пропил; определяется
t1 = Lϑн.ср
t2 - время на подъем и опускание пилы; n - число пропилов, шт.;
t3 - время на загрузку и подачу кряжа под пилу. L - путь надвигания L = d = 25см.
ϑн.ср - средняя скорость надвигания, определяется по формуле:
ϑн.ср = |
PVп |
|
, м/с |
k b H |
|
||
|
ср |
(8.7)
(8.8)
где: P - усиление надвигания, кг;
Vп - скорость подачи кряжа, м/с;
k - коэффициент удельного сопротивления надвиганию;
Hср - средняя высота пропила, которая определяется по зависимости:
Hср = 0,8dср |
(8.9) |
где dср - диаметр поперечного сечения дерева по месту пиления, м.
В круглых пилах шаг зубьев определяется в зависимости от толщины
пилы:
для пил поперечной распиловки t = (6 ÷15)S
Высота зуба определяется по следующим зависимостям: для пил поперечного пиления: h = (0,7 ÷1,0)
Допустимое значение скорости подачи определяется по следующей зависимости:
|
|
Npt0,15ηp |
1,2 |
(8.10) |
||||
U = |
|
|
|
|
|
|
||
8,5*106 a a a a a b0,5 H V 0,15 |
||||||||
|
|
|
||||||
|
|
n w |
p t c |
|
ср |
|
|
|
где Np - мощность, потребляемая при пилении; |
|
|
||||||
|
Np = |
k b H ϑн.ср |
|
(8.11) |
||||
|
|
η |
|
|
|
|||
|
|
|
|
|
|
|
||
k - величина удельной работы резания, |
Дж/м3 ее следует определять по |
|||||||
формуле: |
|
|
|
|
|
|
|
|
|
k = kо an aw ap at ac |
|
(8.12) |
30