
2873
.pdf31
Методы защиты металлических поверхностей от коррозии
Защита металла сводится к повышению коррозионной стойкости металлов и снижению коррозионной активности окружающей среды.
Метод ингибирования основан на добавлении в коррозионную среду специальных веществ, замедляющих коррозию (ингибиторы). Ингибиторами могут быть органические (амины, аминокислоты, сульфокислоты) и неорганические соединения (хроматы, бихроматы, нитраты), которые адсорбируются на поверхности металла, образуя оксидную пленку, предохраняющую металл от дальнейшего растворения, либо взаимодействуют с ионами металлов и образуют труднорастворимые продукты коррозии – карбонаты, фосфаты, силикаты на анодных участках.
Неметаллические покрытия (краски, лаки, эмали, полимерные пленки) механически защищают металлическую поверхность от коррозии. Кроме этого, многие краски содержат ингибиторы коррозии и обладают большим защитным действием против разрушения.
Промышленное значение имеют масляные, спиртовые, асфальтовые лаки и нитролаки. Лаки обладают высокими защитными свойствами в условиях атмосферной коррозии. Коррозионная стойкость спиртовых лаков мала. Нитролаки весьма стойки во влажной атмосфере, но токсичны, взрывоопасны и горючи. Эмалевые лаки эластичны, прочны, обладают хорошей стойкостью в холодной и горячей воде, в растворах солей. Из полимерных материалов имеют применение полихлорвиниловые и фенолоальдегидные пластмассы.
Для сушильных камер имеется определенный набор лакокрасочных покрытий, устойчивых в атмосфере лесосушильных камер (табл. 11).
Таблица 11 Лакокрасочные покрытия, устойчивые в атмосфере лесосушильных камер
Покрытие |
Срок службы покрытия, год |
Эмаль ФЛ-777 |
5,0 |
|
|
Шпатлевка ЗП-00-10 |
5,0 |
|
|
Лак ГФ-95 с алюминиевой пудрой |
3,0 |
|
|
Краска АКС-3 |
2,5 |
|
|
Лак КФ-95 с алюминиевой пудрой |
1,5 |
|
|
Эмаль ПхВ-14 |
1,0 |
|
|
Краска БТ-177 |
1,0 |
|
|
32
Оксидирование применяется для создания на поверхности металлических изделий защитных оксидных пленок.
Термический способ оксидирования стали при температуре 623…723 К называется воронением. Фосфатирование – это химический процесс, при котором на поверхности стали образуется пленка нерастворимых в воде фосфатных соединений марганца и железа. Эта пленка выдерживает температуру до 873 К и обладает электроизоляционными свойствами.
Для защиты от химической коррозии используют покрытие защищаемого металла металлическими покрытиями: хромом (термохромирование), алюминием (термоалютирование), кремнием (термосилицирование).
Для защиты от электрохимической коррозии используют гальванические покрытия, получаемые в процессе электролиза. Защищаемая металлическая поверхность играет роль катода. Она может покрываться за счет процесса восстановления хромом (хромирование), никелем (никелирование), железом (железнение), серебром (серебрение) и так далее. Этот процесс называют гальваностегией.
Протекторная защита заключается в том, что создается гальванический элемент из защищаемого металла и другого металла, обладающего более электроотрицательным потенциалом. Последний служит анодом и называется протектором. Протекторы должны располагаться на участках, наиболее подверженных коррозии. Для железных конструкций в качестве протектора применяют цинк, магниевые сплавы. Радиус действия протектора тем выше, чем больше электропроводимость агрессивной среды. Для морской воды он составляет 3-5 м.
Электрозащита, или катодная защита обеспечивается подключением защищаемой металлической конструкции к катоду внешнего источника постоянного тока. В качестве анода используется любой металлический лом, который подключают к положительному полюсу источника тока.
Для повышения коррозионной стойкости металлов используют метод легирования, при котором в состав сплава вводят металлы (хром, никель, титан, молибден, вольфрам), вызывающие пассивацию защищаемого металла. При химической коррозии в качестве легирующих агентов используют хром, алюминий, кремний. При электрохимической коррозии легирующими металлами являются хром, вольфрам, никель, титан, кобальт, молибден, ванадий и другие.
33
Реактивы и оборудование
1.U -образная трубка.
2.Набор электродов и пластин из различных видов стали.
3.Вольтметр.
4.Соединительные проводники.
5.Набор растворов кислот и солей.
6.Наждачная и фильтровальная бумага.
Экспериментальная часть Опыт 1. Защита стали и чугуна методом оксидирования
Для исследования коррозии стали и методов ее защиты от коррозии стальную пластину необходимо очистить наждачной бумагой и измерить электродный потенциал относительно электрода сравнения (каломельного электрода). Затем вытащить рабочий электрод из U-образной трубки, высушить фильтровальной бумагой и нагревать в пламени горелки до тех пор, пока на ней не образуются тончайшие слои оксидов, о чем свидетельствуют цвета побежалости на поверхности пластин. Довести температуру рабочего электрода до комнатной и после этого измерить потенциал электрода, покрытого оксидными пленками. Замеры электродных потенциалов не оксидированной и оксидированной пластины производить через 5 минут после помещения электродов в раствор электролита, данные занести в табл. 12.
Таблица 12
Значения ЭДС коррозионного элемента
Коррозионный |
Не оксидированная |
Оксидированная |
электролит |
пластина |
пластина |
|
|
|
|
|
|
|
|
|
|
|
|
Сделайте вывод об изменении ЭДС коррозионного элемента и назовите причину этого изменения. Напишите схемы коррозионных гальванических элементов и объясните их работу.

34
Опыт 2. Коррозия металлических поверхностей в кислой среде Наиболее активно коррозия металлических поверхностей происходит в
кислой среде. Например, одним из окислительных агентов в лесосушильных камерах является уксусная кислота, которая реагирует с металлическим материалом камер.
Для проведения эксперимента поместить в U-образную трубку 10 %-й раствор уксусной кислоты в таком количестве, чтобы электроды были погружены в электролит на 2…3 см. Измерить электродный потенциал взятого металла через 1, 5, 10 и 20 минут. Полученные данные внести в табл. 13 и сделать вывод о том, что происходит с металлической поверхностью в результате работы микрогальванических пар.
Таблица 13 Электродный потенциал сталей, используемых в лесопромышленном
комплексе
|
Продолжительность коррозии сталей |
|||||
Вид материала |
|
в уксусной кислоте |
|
|
||
|
1 |
5 |
|
10 |
|
20 |
Сталь Х3 |
|
|
|
|
|
|
Низколегированная сталь Х13 |
|
|
|
|
|
|
Нержавеющая сталь Х18Н9Т |
|
|
|
|
|
|
Напишите схему работы коррозионных гальванических элементов. В лабораторной работе вместо стали в схеме можно использовать железо, которое является основным компонентом стали.
Вопросы для самоконтроля:
1.Каковы виды и механизм коррозии металлов?
2.Каковы основные методы защиты от коррозии?
3.В чем измеряется скорость коррозии?
4.В чем заключается метод оксидирования?
Лабораторная работа № 6 ПОЛУЧЕНИЕ И РАСЧЕТ ТОЛЩИНЫ ГАЛЬВАНИЧЕСКОГО
ПОКРЫТИЯ
Цель работы:
1.Ознакомиться с методами нанесения и определение толщины гальванических покрытий.
2.Определить толщину гальванического покрытия гравиметрическим методом.
35
Теоретическая часть
Для защиты металлических изделий от коррозии, а также придания изделиям из металлических и неметаллических материалов защитнодекоративных или специальных (повышение твердости, износостойкости, антифрикционные свойства) свойств используют металлические покрытия.
Нанесение металлических покрытий проводят различными способами: электроосаждением ионов металла из раствора электролита (гальванические), погружением защищаемого изделия в расплавленный металл (горячие), насыщением поверхностных слоев металла при высоких температурах (термодиффузионные), распылением расплавленного металла (металлизационные) или горячей прокаткой металла и слоя коррозионностойкого металла (плакировочные).
Независимо от способа нанесения все металлические покрытия должны удовлетворять следующим основным требованиям: быть прочно сцепленными с основой и не отслаиваться при любых условиях эксплуатации; быть плотными, мелкокристаллическими, обеспечивающими коррозионную стойкость изделия; иметь минимальную пористость; удовлетворять специальным требованиям к покрытию: твердости, износостойкости, удельному электросопротивлению, оптическим свойствам, антифрикционным свойствам и др.
По механизму защиты металла от коррозии металлические покрытия подразделяются на катодные и анодные. К катодным относятся покрытия, потенциалы которых в данной среде имеют более положительное значение, чем потенциал основного металла. Катодными покрытиями по отношению к стали являются медные, никелевые, золотые, серебряные, палладиевые и др. Анодные покрытия имеют потенциал более отрицательный, чем потенциал защищаемого металла (цинковое покрытие для стали).
Катодные покрытия надежно защищают от коррозии только при отсутствии в них пор, трещин и других дефектов, т.е. при условии их сплошности. При повреждении катодного покрытия возникает коррозионный элемент, в котором основной металл служит анодом и растворяется, а материал покрытия – катодом, на котором идет процесс или восстановления водорода, или ионизации кислорода (рис. 7).
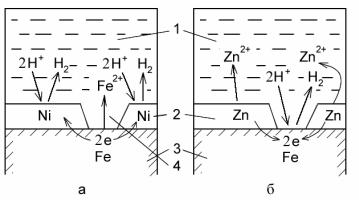
36
Рис. 7. Схема коррозии металла в кислом растворе при нарушении металлических покрытий: а – катодного, б – анодного;
1– раствор, 2 – покрытие, 3 – основной металл, 4 – дефект в покрытии
Анодное покрытие, даже при его повреждении, продолжает защищать металл изделия (рис. 7, б).
Гальванические покрытия
Гальванические покрытия – это покрытия изделий из металлических и неметаллических материалов, получаемые в процессе электролитического осаждения металла на их поверхности, т.е. электролиза. Хромирование и никелирование фурнитуры в мебельной промышленности, в лесном и автомобильном хозяйствах, в лесоинженерном деле проводят с помощью электролиза, получая противокоррозионные гальванические покрытия для защиты оборудования, механизмов и транспорта от коррозионных разрушений.
Электролиз представляет собой процесс раздельного окисления и восстановления на электродах, протекающий под действием постоянного электрического тока. Электролитические процессы осуществляются в электролизерах или электролитических ваннах. Изделие, на которое необходимо нанести слой защитного металлического покрытия, подключают к катоду, а анодом является графитовый электрод или электрод из того металла, который служит покрытием. Катодная и анодная пластины помещаются в соответствующий раствор электролита, содержащий ионы металла, служащего защитным покрытием.
Например, при нанесении цинкового покрытия на изделие из стали протекают следующие процессы по схеме:
37
Диссоциации электролита ZnSO4 Zn2+ + SO42– Миграция катионов (Zn2+) к катоду, а анионов (SO42–) к аноду
КАТОД (-): |
|
|
АНОД графитовый (+): |
Zn2+ |
|
|
SO42– |
на катоде – реакция восстановления |
на аноде – реакция окисления воды |
||
2 Zn2+ + 2e = Zn0 |
|
|
2H2O – 4e = O2 + 4H+ |
металл (Zn)осаждается на поверхности электрода |
|
|
|
Суммарный процесс электролиза выражается следующим уравнением: |
|||
электролиз |
|
0 |
+O2 +2H2 SO4 . |
ZnSO4 +2H2O →Zn |
|
Законы М. Фарадея, установленные в 1833 г. позволяют рассчитывать массу осаждаемого металла, время электролиза и необходимую силу.
|
I закон Фарадея |
|
|
|
Масса выделяющегося на электроде вещества пропорциональна |
||
количеству электричества, протекающего через электролизер. |
|
||
|
m = K I t = K Q , |
(15) |
|
где |
m – масса вещества на электроде, г; |
I – сила тока, А; t – время протекания |
|
тока |
через электролизер, с; Q = |
I t – количество |
электричества; |
K – электрохимический эквивалент, равный отношению химического эквивалента к числу Фарадея (F ≈ 96500 Кл/моль).
II закон Фарадея
Для выделения на электроде 1 моль любого вещества необходимо затратить одно и то же количество электричества, равное F=96500 Кл/моль
– постоянная Фарадея.
Обобщенный вид первого и второго законов Фарадея выглядит так:
m = |
Э |
I t . |
(16) |
|
F |
||||
|
|
|
Определение толщины покрытия
Толщина гальванопокрытия во многих случаях является решающим признаком качества покрытия, технические и экономические требования к которому установлены ГОСТ 9.302-88. Следует учитывать, что толщина покрытия на изделиях, особенно профилированных, неодинакова в различных точках поверхности, поэтому необходимо измерение не только средней толщины покрытия, но и минимальной толщины на определенных участках детали.
Методы контроля толщины покрытий по степени воздействия на объект подразделяют на две группы: разрушающие и неразрушающие.
38
Разрушающие методы контроля толщины покрытий приводят к разрушению целостности не только покрытия, но и самого изделия. Они делятся на химические и физические. К химическим методам относят метод стравливания, методы капли и струи, кулонометрический метод.
Метод стравливания является наиболее простым и удобным и позволяет определять среднюю толщину нанесенного покрытия по изменению массы при растворении покрытия в травильном электролите, который не действует на металл основы.
В методе капли травильный раствор (HCl, H2SO4) наносят по каплям на поверхность покрытия из капельницы с внутренним диаметром капилляра 1,5-2,0 мм и выдерживают в течение определенных промежутков времени до полного растворения покрытия. Метод капли позволяет определять локальную толщину покрытия на любом участке поверхности изделия, однако имеет высокую относительную погрешность до ±30 %.
Методы струи определяют толщину однослойных и многослойных покрытий на поверхности площадью не менее 0,3 мкм. Методы основаны на растворении покрытия под действием струи электролита, вытекающей с определенной скоростью.
Металлографический метод основан на измерении толщины однослойных и многослойных покрытий на поперечном шлифе с помощью металлографического микроскопа при увеличениях до 1000 раз для покрытий толщиной менее 20 мкм и до 200 раз для покрытий толщиной более 20 мкм. Разновидностью металлографического метода является оптический, основанный на измерении при помощи металлографического микроскопа длины уступа, образованного краем покрытия с основным металлом. Метод применим для измерения покрытий толщиной 1-40 мкм с коэффициентом отражения не менее 0,3. Погрешность метода ±10 %.
Из неразрушающих методов контроля наибольшее распространение получили электромагнитные методы, метод измерения масс, метод прямого измерения.
Электромагнитные методы основаны на изменении силы отрыва постоянного магнита от контролируемой поверхности в зависимости от толщины покрытия (магнитоотрывной); регистрации изменений напряжённости магнитного поля в цепи электромагнита постоянного тока в
39
зависимости от толщины покрытия (магнитостатический); определении магнитного сопротивления участка цепи соответствующего изменению толщины покрытия (магнитоиндукционный).
Метод прямого измерения заключается в измерении размеров детали до и после нанесения покрытия с помощью микрометра или оптиметра.
Гравиметрический метод предусматривает непосредственное взвешивание и измерение покрываемой поверхности образца или изделия до и после электроосаждения. Средняя толщина покрытия представляет собой отношение объема нанесенного покрытия к площади поверхности покрытого изделия. Из-за трудностей измерения площади поверхности покрываемых изделий гравиметрический метод применяют для определения средней толщины гальванопокрытия на небольших деталях простого профиля.
Реактивы и оборудование
1.Электролизер.
2.Металлические электроды (медные, цинковые пластины).
3.Внешний источник тока.
4.Потенциометр или амперметр.
5.Соединительные проводники.
6.Набор растворов электролитов.
7.Аналитические весы.
Экспериментальная часть
Порядок выполнения работы
В данной работе для получения медного гальванического покрытия используется установка, представленная на рис. 8. Перед сбором установки необходимо определить массу катодной пластины m1, и ее площадь S, записать в табл. 14. Для этого катодную пластину отсоединяют и взвешивают на аналитических весах. Площадь катодной пластины определяют геометрически. Затем собирают установку, для чего в электролизер наливают раствор соли меди (CuSO4) с концентрацией 0,1 моль/л объемом 300-400 мл. В раствор помещают исследуемые металлические пластины таким образом, чтобы они были максимально покрыты раствором электролита. Одна из пластин служит катодом (К) и будет покрыта металлом, ионы которого присутствуют в растворе, а также тем металлом, из которого сделана анодная пластина (А). Электроды необходимо соединить проводниками с источником постоянного
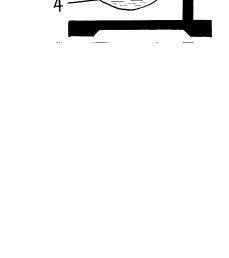
40
тока, последовательно соединив с амперметром. Составленную схему установки необходимо показать преподавателю или лаборанту.
Рис. 8. Схема установки для электролитического нанесения покрытий:
1 – электролизер;
2 – электроды (металлические пластины);
3 – штатив;
4 – раствор электролита;
5 – амперметр;
6 – внешний источник тока
Силу тока и время проведения электролиза определяет преподаватель, так, чтобы время электролиза составило не менее 30 мин. После этого включают источник тока и засекают время электролиза. В течение времени осуществления электролиза студенты наблюдают за явлениями, происходящими на электродах, и записывают уравнения электрохимических процессов на электродах. После этого проводят расчет теоретических значений массы m3, и толщины покрытия, пользуясь законом Фарадея и уравнением (16). Результаты расчетов записывают в табл. 14.
Таблица 14 Результаты определения толщины гальванического покрытия
гравиметрическим методом
Материал катодной пластины |
Состав раствора для нанесения покрытия |
Сила тока, А |
Время электролиза, мин |
Масса катодной пластины, г |
Толщинапокрытия, см |
Погрешность, % |
|||
|
|
|
|
|
|||||
Без |
Эксперим., |
Теоретич., |
|
|
|||||
покрытия, |
после |
по закону |
|
|
|||||
m1 |
нанесения |
Фарадея, |
Эксперим. |
Теоретич. |
|||||
|
покрытия, |
m3 |
|
|
|||||
|
m2 |
|
|
|
|||||
|
|
|
|
|
|
|
|
|
|
|
|
|
|
|
|
|
|
|
|
|
|
|
|
|
|
|
|
|
|
|
|
|
|
|
|
|
|
|
|
По истечении времени электролиза источник тока отключают, катодную пластину извлекают, промывают дистиллированной водой, аккуратно высушивают фильтровальной бумагой и оставляют на 5 мин до полного