
204
.pdf3
Федеральное агентство по образованию Государственное образовательное учреждение высшего профессионального образования
Воронежская государственная лесотехническая академия
Основы технологии производства и ремонта автомобилей
Разработка технологического процесса сборки изделий
для студентов всех форм обучения по специальности 190601 – Автомобили и автомобильное хозяйство, 150405 – Машины и оборудование лесного комплекса
Воронеж 2006
4
УДК Станчев, Д.И. Основы технологии произврдства и ремонта автомобилей. Раз-
работка технологического процесса сборки изделия [Текст] : методические указания для студентов всех форм обучения по специальности 190601 – Автомобили и автомобильное хозяйство, 150405 – Машины и оборудование лесного комплекса
/ Д.И. Станчев, Г.А. Сухочев, В.Н. Бухтояров ; Фед. Агенство по образованию, Гос. образовательное учреждение высш. проф. образования – Воронеж. гос. лесотехн. акад. Воронеж, 2006. – 15 с.
Печатается по решению редакционно-издательского совета ВГЛТА
Рецензент док. техн. наук, доц. ВГТУ А.В. Кузовкин
5
1 ЦЕЛЬ РАБОТЫ
1.На основании изучения устройства и особенностей эксплуатации заданного узла (сборочной единицы) или изделия в целом, студенту необходимо освоить последовательность разработки технологического процесса сборки этого узла.
2.Освоить методику составления технологической схемы сборки и оформления технологической документации в соответствии с ЕСТД.
3.Разработать технологическую последовательность сборки, подобрать необходимое оборудование, инструмент и оснастку.
2 ОБЩИЕ ПОЛОЖЕНИЯ
Сборка изделий является завершающей стадией изготовления изделия, которая отличается высокой трудоемкостью − сборочные операции составляют 20 ... 40 % от общей трудоемкости изготовления изделия.
Качество сборки зависит не только от точности сборки, но и от методов организации сборочного процесса, чистоты собираемых деталей, оснащения рабочих мест, контроля в процессе сборки и испытания собранных узлов, агрегатов автомобиля. Сборку автомобиля, как сложной машины, расчленяют на узловую и общую. Начинают сборку с базовой детали, базового узла или агрегата в зависимости от того, что собирается – узел, агрегат или машина. Под базовым сборочным элементом понимают деталь (узел, агрегат), являющуюся исходной для начала процесса сборки. Узел – соединение базовой детали с несколькими деталями, которое может быть собрано обособленно от других деталей. Узел может быть собран из отдельных деталей и деталей, предварительно соединенных до постановки в узел. Например, в сборку узла поршень – шатун входит шатун с предварительно (до сборки узла) запрессованной втулкой. Поэтому помимо узловой сборки различают еще подсборку, т. е. простейшее соединение деталей, называемое «подузел». В результате соединения базового узла с несколькими узлами и деталями получаем агрегат. Например, базовый агрегат – рама с монтированными другими агрегатами, узлами и деталями – образует готовое изделие – автомобиль.
Одним из основных этапов проектирования, в большой степени определяющих эффективность технологических процессов сборки, является анализ технологичности конструкции. В соответствии со стандартами ЕСТПП требования к технологичности сборочной единицы разбиты на 3 группы:
1)требования к составу сборочной единицы;
2)требования к конструкции соединения составных частей;
3)требования к точности и методу сборки.
Требования к составу сборочной единицы:
–сборочная единица должна расчленяться на рациональное число составных частей;
–конструкция сборочной единицы должна обеспечивать возможность компоновки из стандартных и унифицированных частей;
–сборка изделия не должна обусловливать применение сложных специальных средств технологического оснащения;
6
–виды используемых соединений, их конструкции и месторасположение должны соответствовать требованиям его механизации и автоматизации сборочных работ;
–в конструкции сборочной единицы и ее составных частей, имеющих массу более 20 кг, должны предусматриваться конструктивные элементы для удобного захвата грузоподъемными средствами, используемыми в процессе сборки, разборки и транспортирования;
–конструкция сборочной единицы должна предусматривать базовую составную часть, которая является основой для расположения остальных составных частей;
–компоновка конструкции сборочной единицы должна позволять производить сборку при неизменном базировании составных частей;
–в конструкции базовой составной части необходимо предусматривать возможность использования конструктивных сборочных баз в качестве технологических и измерительных;
–компоновка сборочной единицы должна обеспечивать общую сборку без промежуточной разборки и повторных сборок составных частей;
–компоновка составных частей сборочной единицы должна обеспечивать удобный доступ к местам, требующим контроля, регулировки и проведения других работ, регламентированных технологией подготовки изделия к функционированию и техническому обслуживанию;
–компоновка сборочной единицы должна предусматривать рациональное расположение такелажных узлов, монтажных опор и других устройств для обеспечения транспортабельности изделия.
Требования к конструкции соединений составных частей:
–количество поверхностей и мест соединений составных частей в общем случае должно быть наименьшим;
–места соединений составных частей должны быть доступны для механизации сборочных работ и контроля качества соединений;
–соединение составных частей не должно требовать сложной и необоснованно точной обработки сопрягаемых поверхностей;
–конструкции соединений составных частей не должны требовать дополнительной обработки в процессе сборки.
Требования к точности и методу сборки:
–точность расположения составных частей должна быть обоснована и взаимосвязана с точностью изготовления составных частей;
–выбор места сборки для данного объема выпуска и типа производства должен производиться на основании расчета и анализа размерных цепей;
–расчет размерных цепей следует производить, используя методы мак- симума-минимума – метод полной взаимозаменяемости или, основанный на теории вероятностей, метод неполной взаимозаменяемости.
В зависимости от типа производства используются также другие методы достижения точности замыкающего звена: метод групповой взаимозаменяемости; метод регулирования; метод пригонки.
Метод полной взаимозаменяемости экономично применять в крупносе-
7
рийном и массовом производстве. Основан метод на расчете размерных цепей на максимум-минимум. Метод прост и обеспечивает стопроцентную взаимозаменяемость. Недостаток метода – уменьшение допусков на составляющие звенья, что приводит к увеличению себестоимости изготовления и трудоемкости.
Метод неполной взаимозаменяемости заключается в том, что допуски на размеры деталей, составляющие размерную цепь, преднамеренно расширяют для удешевления производства. В основе метода лежит положение теории вероятности, согласно которому крайние значения погрешностей, составляющих звеньев размерной цепи встречаются значительно реже, чем средние значения. Такая сборка целесообразна в серийном и массовом производствах при многозвенных цепях.
Метод групповой взаимозаменяемости применяют при сборке соединений высокой точности, когда точность сборки практически недостижима методом полной взаимозаменяемости (например, шарикоподшипники). В этом случае детали изготовляют по расширенным допускам и сортируют в зависимости от размеров на группы так, чтобы при соединении деталей, входящих в группу, было обеспечено достижение установленного конструктором допуска замыкающего звена.
Недостатками данной сборки являются: дополнительные затраты на сортировку деталей по группам и на организацию хранения и учета деталей; усложнение работы планово-диспетчерской службы.
Сборка методом групповой взаимозаменяемости применяется в массовом и крупносерийном производствах при сборке соединений, обеспечение точности которых другими методами потребует больших затрат.
Сборка методом пригонки трудоемка и применяется в единичном и мелкосерийном производствах.
Метод регулирования имеет преимущество перед методом пригонки, так как не требует дополнительных затрат и применяется в мелко- и среднесерийном производствах.
Разновидностью метода компенсации погрешностей является способ сборки плоскостных соединений с применением компенсирующих прокладок (шайб).
Особое внимание следует уделять при сборке размерным цепям, составляющими звеньями которых являются разные геометрические параметры, так как решение этих цепей проверяет на совместимость допуски, установленные на основе различных нормативных источников.
При производстве автомобилей сборка машин производится исключительно из новых деталей, имеющих номинальные размеры, сборка в авторемонтном производстве осуществляется из деталей с номинальными и ремонтными размерами и с допустимым износом. Известно, что сборка автомобилей на автозаводах осуществляется при полной взаимозаменяемости деталей, причем для сборки основных сопряжений двигателя применяется метод группового – селективного – подбора. В авторемонтном производстве полная взаимозаменяемость сохраняется только для деталей, восстановленных под номинальные размеры, или новых с номинальными размерами. Для деталей
8
ремонтных размеров взаимозаменяемость сохраняется лишь в пределах данного ремонтного размера. Детали же с допустимыми износами вовсе утрачивают взаимозаменяемость, так как не обеспечивают начальных посадок сопряжений. По всем этим причинам сборка в авторемонтном производстве осуществляется с использованием метода подгонки или селективной подборки. При этом, однако, необходимо заметить, что метод подгонки в современном ремонтном производстве имеет наибольшее применение.
Собственно сборочные работы содержат набор отдельных операций по соединению деталей и сборочных единиц в изделие:
−сборки резьбовых соединений; сборка неподвижных соединений с гарантированным натягом;
−сборка подвижных соединений с гарантированным зазором, сборка соединений с подшипниками;
−сборка зубчатых передач и других типовых механизмов, имеющих место в изготавливаемом соединении.
Технология сборки содержит также операции по испытаниям, обкатке и регулировке наиболее ответственных узлов, которые выполняются по специально разработанному регламенту.
Завершающей и важнейшей операцией технологии сборки является контрольная, которая проверяет качество не только окончательно изготовленного изделия, но и промежуточные, наиболее ответственные операции по всему технологическому циклу. В качестве контрольных операций часто используются различные виды параметрических испытаний.
3 ИСХОДНЫЕ ДАННЫЕ И УСЛОВИЯ ДЛЯ ВЫПОЛЕНИЯ РАБОТЫ
3.1Сборочный чертеж объекта сборки изделия или сборочной единицы сложного изделия и его спецификации. Наименование сборочной единицы выдается преподавателем на основе табл. 1 прил. А.
3.2Натурный образец аналога объекта сборки.
3.3Руководящие материалы по оформлению технологической докумен-
тации.
4 ПОСЛЕДОВАТЕЛЬНОСТЬ РАБОТЫ
4.1 Анализ исходных материалов Изучаются:
−назначение объекта сборки;
−принцип его работы и особенности эксплуатации;
−состав объекта сборки;
−технические требования, предъявляемые к сборке;
−уровень технологичности объекта сборки;
−годовой объем выпуска.
Этот анализ проводится по имеющемуся сборочному чертежу со спецификацией аналога изделия с уточнениями по натурному образцу.
9
4.2 Изучение аналога объекта сборки При рассмотрении данного вопроса:
−устанавливается наименование и количество сборочных единиц изделия;
−выявляется базовая сборочная единица, с которой целесообразно начинать процесс сборки;
−выявляется наименование и количество отдельных деталей для соединения сборочных единиц;
−выбирается метод сборки для заданной программы выпуска;
−уточняется перечень слесарно-сборочных работ при соединении сборочных единиц низшего порядка в изделие (слесарно-пригоночные, механические или термические при выполнении неподвижных соединений, окрасочные, сварочно-монтажные, регулировочные и др.);
−уточняются промежуточные контрольные операции.
4.3 Составление технологической схемы сборки Технологическая схема сборки показывает последовательность соедине-
ния деталей и сборочных единиц низшего порядка в изделие с указанием основных видов работ, используемых при этом. Схема сборки составляется в соответствия с ГОСТ 23887-79. Пример оформления технологической схемы сборки цилиндра пневматического (рис. 1) приведен в приложении.
4.4 Разработка технологического процесса сборки Эта часть работы приводится в следующей последовательности:
−разделение общей технологии сборки на отдельные операции (установы и переходы);
−подбор технологического оборудования, инструмента, специальных приспособления и стендов, контрольно-измерительных средств, необходимых для выполнения каждой операции (см. прил. Б).
При этом надо учитывать заданный годовой объем производства.
4.5. Оформление технологической документации Разработка технологии завершается оформлением технологической до-
кументации. Оформляются:
−маршрутная карта (МК) в соответствии с ГОСТ 3.1118-82, форма 2;
−операционные карты (ОК) в соответствии с ГОСТ 3.1407-86 на 1...2 операции (по указанию преподавателя).
5 СОДЕРЖАНИЕ ОТЧЕТА
5.1Исходные данные и их анализ
5.2Схема сборки заданного изделия
5.3Описание технологических особенностей сборки изделия
5.4Технологический маршрут сборки заданного изделия
5.5Технологическая документация.
10
6 КОНТРОЛЬНЫЕ ВОПРОСЫ
6.1Какие операции составляет технологический процесс оборки из-
делия?
6.2Как выбирается базовая деталь при сборке сборочной единицы?
6.3Как зависит метод сборки изделия от серийности производства?
6.4Как влияет допуск на размер замыкающего элемента сборочной единицы на метод сборки?
6.5Какие средства механизации применяются в сборочных операциях?
6.6Укажите основные правила составления схемы сборки.
6.7Приведите примеры базовых деталей.
7 БИБЛИОГРАФИЧЕСКИЙ СПИСОК
Основная литература
1.Колесов, И.М. Основы технологии машиностроения [Текст]: учебник / И.М. Колесов под. ред. Ю.М. Соломенцева. – 2-е изд. испр. – М.: Высш. шк., 1999. – 591 с.
2.Сухочев, Г.А. Разработка технологического процесса изготовления детали [Текст]: учеб. пособие / Г.А. Сухочев, К.А. Яковлев; ВГЛТА. – Воронеж, 2002. – 68с.
3.Технология машиностроения. В 2 кн. Кн.1. Основы технологии машиностроения [Текст]: учеб. пособ. для вузов / Э.Л. Жуков, И.И. Козарь, С.Л. Мурашкин [и др]; под ред. С.Л. Мурашкина – М.: Высш. шк., 2003. – 278 с.
Дополнительная литература
1.Амиров, Ю.Д. Технологичность конструкции изделия [Текст]: Справочник / Ю.Д. Амиров, Т.К. Алферова, П.Н. Волков; Под общ. ред. Ю.Д. Амирова. – 2-е изд., перераб. и доп. – М.: Машиностроение, 1990. – 768 с.
2.Общетехнический справочник [Текст] / Под общ. ред. Е.А. Скороходова – М.: Машиностроение, 1991. - 496 с.
3.Андреев, Г.Н. Проектирование технологической оснастки машиностроительного производства [Текст]: учеб. пособие для машиностроительных вузов / Г.Н. Андреев, В.Ю. Новиков, А.Г. Схиртладзе. Под ред. Ю.М. Соломенцева. – 2-е изд., испр. – М.: Высш. шк., 1999. – 415 с.
4.Справочник технолога-машиностроителя [Текст]. В 2 т. / А.М. Дальский, А.Г. Суслов, А.Г. Косилова. – М: Машиностроение, 2003. – 912 с.
5.Машиностроение. Энциклопедия [Текст] : в 40 т. Раздел III. Технология производства машин. Т. III-5. Технология сборки в машиностроении / отв. ред. П.Н. Белянин ; ред. тома : В.В. Павлов, А.А. Гусев. – М: Машиностроение, 2001. – 640 с.
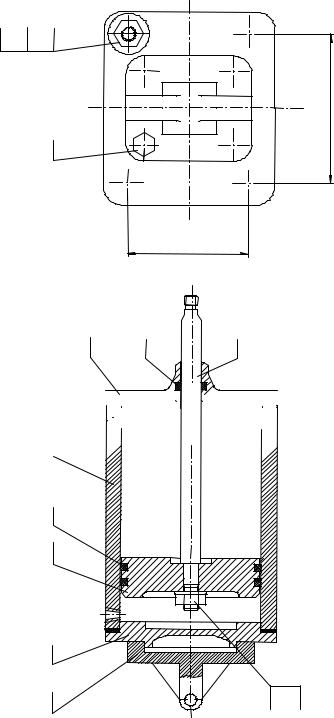
11
11 |
12 |
13 |
|
|
158 |
|
|
10 |
158
7 |
8 |
9 |
5 6
4 |
3 |
2 |
1 |
14 15 |
Рис. 1 Цилиндр пневматический тормозной системы автомобиля 1 – фланец; 2 – крышка задняя; 3 – поршень; 4 – кольцо; 5 – корпус; 6 - про-
кладка; 7 – крышка передняя; 8 – манжета; 9 – шток; 10 – болт; 11 – шпилька; 12 – гайка; 13 – шайба; 14 – гайка; 15 – шайба
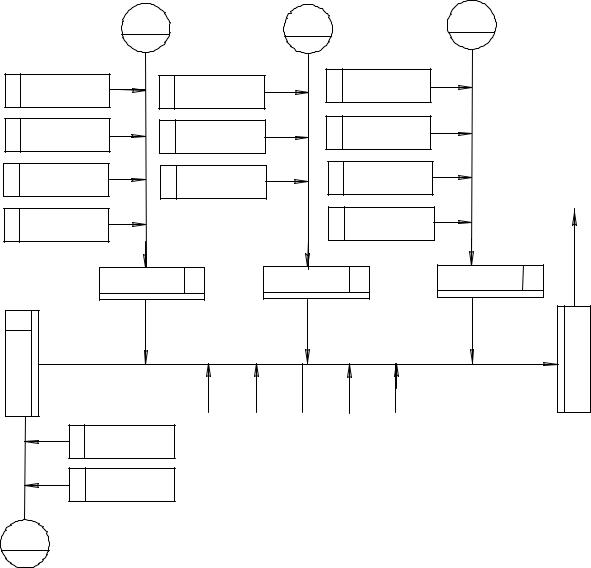
12
|
Сб. 2 |
|
|
Сб. 3 |
|
Сб. 4 |
|
|
|
|
|
|
|
||
3 |
Поршень |
|
Крышка |
2 |
Крышка |
|
|
7 |
задняя |
|
|
||||
передняя |
|
|
|||||
4 Кольцо |
8 Кольцо |
1 Фланец |
|
|
|||
9 |
Шток |
6 |
Прокладка |
10 |
Болт |
|
|
|
|
|
|
|
|
|
|
14 |
|
|
|
6 |
Прокладка |
|
Ок. |
Поршень |
|
|
|
и |
|||
|
|
|
|
|
|
|
|
|
|
|
Сб. |
Крышка |
Сб. |
Крышка |
Сб. |
|
Поршень |
|
2 |
передняя |
3 |
задняя |
4 |
Сб. 1
с |
Ст. |
|
Корпу |
|
|
|
11 |
Шпилька |
Ст. |
5 |
Корпус |
Сб. 1 |
|
|
К
Шпилька |
|
Гайка |
|
Шайба |
|
Гайка |
|
Шайба |
|
|
|
|
|
|
|
|
|
10 |
|
12 |
|
13 |
|
14 |
|
15 |
|
|
|
|
|
||||
|
|
|
|
|
|
|
Цилиндр пневматический
Рис. 2 Схема сборки цилиндра пневматического тормозной системы автомобиля
Пояснения к составлению технологической схемы сборки (см. рис. 2):
Наименование изделия (объекта сборки) указано в прямоугольнике с двумя утолщенными линиями (сверху и низу).
Наименования и номера сбоечных единиц указаны в прямоугольниках с одной утолщенной линией (внизу). Номер указывается в правой части прямоугольника.
Наименования и номер указаны, в прямоугольниках (без утолщенных линии). Номер указывается в левой части прямоугольника.
Технологическая последовательность общей сборки изделия из сборочных единиц показана горизонтальной линией со стрелкой.
Технологическая последовательность сборки сборочных единиц из деталей показана вертикальными линиями со стрелкой.