
1842
.pdf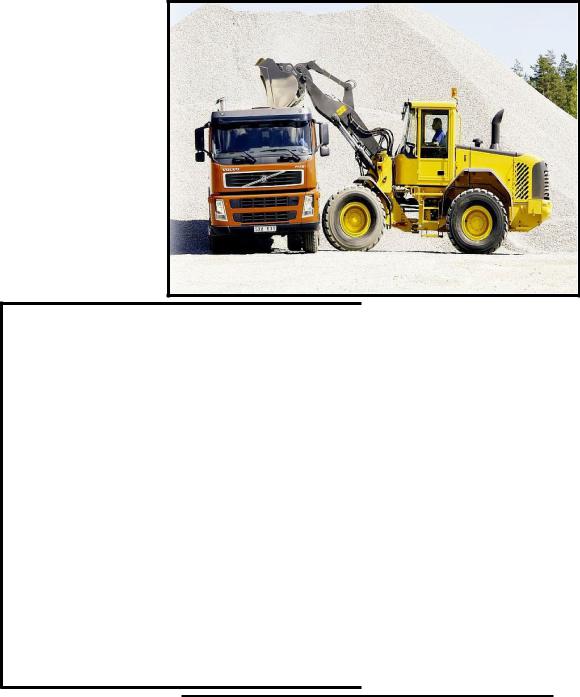
ОСНОВЫ ТЕХНОЛОГИИ ПРОИЗВОДСТВА И РЕМОНТА ТРАНСПОРТНЫХ И ТРАНСПОРТНО-ТЕХНОЛОГИЧЕСКИХ
МАШИН И ОБОРУДОВАНИЯ.
ТЕХНОЛОГИЯ И ОРГАНИЗАЦИЯ ВОССТАНОВЛЕНИЯ ДЕТАЛЕЙ И СБОРОЧНЫХ ЕДИНИЦ
Методические указания к лабораторным работам
Омск 2011
20
Министерство образования и науки Российской Федерации
ФГБОУ ВПО «Сибирская государственная автомобильно-дорожная академия (СибАДИ)»
Кафедра «Эксплуатация и сервис транспортных и технологических машин и комплексов в строительстве»
ОСНОВЫ ТЕХНОЛОГИИ ПРОИЗВОДСТВА И РЕМОНТА ТРАНСПОРТНЫХ
И ТРАНСПОРТНО-ТЕХНОЛОГИЧЕСКИХ МАШИН И ОБОРУДОВАНИЯ.
ТЕХНОЛОГИЯ И ОРГАНИЗАЦИЯ ВОССТАНОВЛЕНИЯ ДЕТАЛЕЙ И СБОРОЧНЫХ ЕДИНИЦ
Методические указания к лабораторным работам
Составители: С.В. Мельник, А.И. Злобин, Л.А. Шапошникова
Омск
СибАДИ
2011
21
УДК 621.86:629.113.004.5 ББК 39.91
Рецензент д-р техн.наук, проф. Н.С. Галдин
Работа одобрена НМСС факультета «НСТ» в качестве методических указаний по выполнению лабораторных работ для студентов направлений подготов-
ки бакалавров 190100, 190600; специальностей 190205, 190603, 190500, 190109.
Основы технологии производства и ремонта транспортных и транс- портно-технологических машин и оборудования. Технология и организация восстановления деталей и сборочных единиц: методические указания к лабо-
раторным работам / сост.: С. В. Мельник, А. И. Злобин, Л.А. Шапошникова. – Омск: СибАДИ, 2011.– 48 с.
В лабораторном практикуме изложена методика выполнения лабораторных работ, порядок их выполнения.
Лабораторные работы выполняются по дисциплинам: «Основы технологии производства и ремонта транспортных и транспортно-технологических машин и оборудования. Технология и организация восстановления деталей и сборочных единиц»; «Технология машиностроения, производство и ремонт подъемнотранспортных, строительных и дорожных машин»; «Технология и организация восстановления деталей и сборочных единиц при сервисном сопровождении»; «Основы технологии производства и ремонта транспортных и транспортнотехнологических машин и оборудования. Технологические процессы технического обслуживания и ремонта ТиТТМО».
ФГБОУ ВПО «СибАДИ», 2011
22
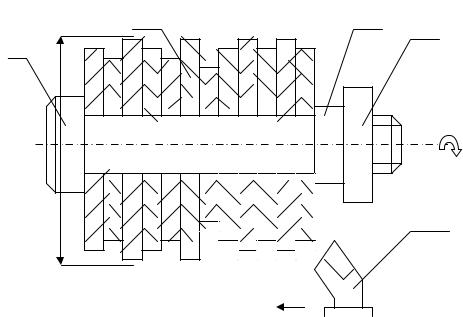
|
Лабораторная работа № 1 |
|
ОПРЕДЕЛЕНИЕ ЖЕСТКОСТИ И ПОДАТЛИВОСТИ ТОКАРНОГО |
||
СТАНКА ДИНАМИЧЕСКИМ МЕТОДОМ |
||
Цель работы – практическое освоение динамического метода опре- |
||
деления жесткости и податливости токарного станка в производственных |
||
условиях. |
|
|
|
Методические указания |
|
Для определения жесткости и податливости системы «шпиндель – |
||
задняя бабка – суппорт токарного станка» динамическим методом произ- |
||
водим обточку за один проход стальных колец различного диаметра, уста- |
||
новленных на жесткой центровой оправке (рис.1.1). |
4 |
|
2 |
3 |
|
1 |
|
|
|
|
n |
Di |
|
5 |
|
|
|
|
S |
|
Рис.1.1. Схема обработки колец при определении жесткости станка: |
||
1 – оправка; 2 – комплект колец; 3 – втулка; 4 – гайка; 5 – резец |
|
Обработку комплекта колец производим за один проход установленного на размер резца. При этом толщина снимаемой стружки с каждого кольца будет различной, поэтому изменяется усилие резания, а следовательно, и упругое отжатие резца при переходе от обработанного кольца к следующему. Таким образом, диаметры колец отличаются как до обработки (прил.1), так и после нее будут несколько отличаться друг от друга.
Произведя замеры диаметров колец до и после обтачивания, можно для каждой соседней пары колец определить уточнение
23
i |
|
i |
, |
(1.1) |
|
|
|||||
|
|
|
i |
|
|
|
|
|
|
где i = Di – Di+1 − разность диаметров соседних колец до обточки;i = di – di+1 – разность диаметров соседних колец после обточки; i – порядковый номер кольца.
Затем определяем среднее значение уточнения
n
i
|
i 1 |
, |
(1.2) |
|
|||
|
n |
|
|
где n – количество пар соседних колец, установленных на оправке, |
|||
для 20 колец n будет равно 19. |
|
||
Определив уточнение, находим жесткость |
токарного станка (j), как |
||
системы «шпиндель - задняя бабка - суппорт» (Н/мм) по формуле: |
|||
j 10 'CpS0.75 , |
(1.3) |
где ─ коэффициент, характеризующий отношение Py / Pz и зависящий от угла заточки резца, состояния режущей кромки, режимов резания, твердости обрабатываемого материала и других факторов (прил.2); Cp – коэффициент, зависящий от угла резания и механических свойств обрабатываемого материала (прил.3); S – продольная подача резца (мм /об); - среднее значение уточнения.
Величина, обратная жесткости, называется податливостью технологической системы ( ) «шпиндель - задняя бабка - суппорт» (мкм/Н):
= 1/ j 1000, |
(1.4) |
где j- жесткость системы, Н/мм.
Значение податливости токарных станков нормальной точности лежит в пределах 0,0334…0,0550 мкм/Н.
Порядок выполнения работы
1.Осуществить наладку токарного станка, установить оправку с комплектом колец из стали с пределом прочности 650 МПа, (диаметры
колец до обработки приведены в прил. 1). Закрепить проходной резец в резцедержателе, установить режимы точения: глубина резания по наименьшему кольцу t=0,25 мм: подача S=0,26 мм/об: скорость резания V=60 м/мин.
2. Диаметры колец до обтачивания Di занести в таблицу 1.1.(в соответствии с вариантом, прил.1)
24
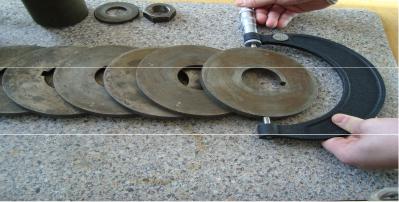
Таблица 1.1. |
|
Определение уточнения |
|
|
|||
|
|
|
|
|
|
|
|
Номер |
|
|
|
Размеры колец |
|
Уточ- |
|
кольца |
|
Di |
|
i=Di-Di+1 |
di |
i=di - di+1 |
нение |
|
|
|
|
|
|
|
i |
|
|
|
|
|
|
|
|
|
|
|
|
|
|
|
|
|
|
|
|
|
|
|
|
|
|
|
|
|
|
|
|
3.Произвести обтачивание колец за один проход.
4.Измерить диаметры колец после обтачивания (di) и результаты занести в табл. 1.1.
Рис.1.2. Измерение диаметра колец с помощью микрометра
5.Вычислить разницу соседних колец до обтачивания ( i), а также после обтачивания ( i),результаты расчетов занести в табл. 1.1.
6.Определить уточнение для каждой соседней пары колец ( i), а затем рассчитать среднее значение уточнения ( ), результаты занести в табл. 1.1.
7.Вычислить жесткость (j) и податливость ( ) станка.
8.Проанализировать полученные результаты, сделать выводы о точности токарной обработки на данном станке.
9.Составить отчет.
Контрольные вопросы
1.Что называется жесткостью и податливостью системы?
2.От каких факторов зависит величина радиальной составляющей силы резания?
3.В каких единицах измеряется жесткость и податливость?
4.Почему данный метод называется «динамический»?
25
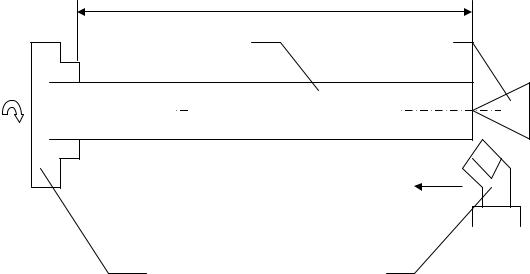
Лабораторная работа № 2
ОЦЕНКА ВЛИЯНИЯ ЖЕСТКОСТИ СИСТЕМЫ СПИД НА ТОЧНОСТЬ ОБРАБОТКИ ДЕТАЛЕЙ
Цель работы – изучение методики аналитической и экспериментальной оценки погрешностей обработки, вызываемых упругими деформациями технологической системы под влиянием силы резания.
Методические указания
Для оценки точности получаемого размера при токарной обработке детали можно определить погрешность формы в продольном сечении от упругих деформаций системы СПИД опытным путем и аналитическим.
Для определения погрешности опытным путем произведем обтачивание длинномерной заготовки за один проход в размер Dн. При этом заготовка закрепляется в трехкулачковом патроне и поджимается конусом задней бабки станка (рис. 2.1).
L=1000 мм
1 4
n
Dн
S
2 |
3 |
|
Рис. 2.1. Схема токарной обработки длинномерного вала: 1−вал; 2– токарный патрон; 3 −резец; 4 – задняя бабка
26
Поле проточки произведем замеры диаметра вала через каждые 100 мм, начиная от начала обработки заготовки. На каждом измеряемом участке определяем погрешность обработки (отклонение от номинального размера), мм:
Di =Di – Dн , |
(2.1) |
где Di – диаметр вала в i-м сечении; Dн – номинальный диаметр вала. По полученным данным определим погрешность обработки по ра-
диусу в этих же сечениях (мм):
yi = Di / 2, |
(2.2) |
где Di – погрешность обработки в i-м сечении.
Для определения погрешности от упругих деформаций в каждом сечении вала при токарной обработке аналитическим путем рассчитаем сначала податливость системы СПИД, i, через 100 мм при каждом положении резца, мкм/Н:
i = супп + шп( |
L x |
)2 + з.б( |
x |
)2 + |
109(L x) |
2 x2 |
, |
(2.3) |
L |
|
3EI L |
|
|||||
|
|
L |
|
|
|
где супп – податливость суппорта станка; шп. – податливость шпинделя станка; з.б– податливость задней бабки станка; L – длина заготовки, мм; x
–расстояние от торца заготовки до точки приложения силы резания, мм; E
–модуль упругости системы, Па,
E = 2,1 1011; I – момент инерции сечения вала, мм4, I = d4 / 64; d – диаметр детали после обработки, мм.
Для облегчения вычисления податливости в каждом сечении вала, значения коэффициентов при различных соотношениях х и L приведены в прил. 4. Также примем, что податливости суппорта, шпинделя и задней бабки станка будут условно равны.
Тогда
супп = шп = з.б = / 3. |
(2.4) |
Затем определим аналитическим методом погрешность обработки вала от упругих деформаций в каждом сечении вала:
yi = Pу i, |
(2.5) |
где Py – радиальная составляющая силы резания Н,
27
Py = 10 Cp t S0,75 |
, |
значения коэффициентов и Сp приведены в прил.2 и 3, а глубина резания t и подача S определяются заданием;
Проанализируем полученные результаты по эксперименту и аналитическому расчету и сделаем выводы о зависимости точности обработки вала от податливости системы СПИД. Для наглядности анализа построим графики зависимостей y = f (x).
Порядок выполнения работы
1. Осуществить наладку токарного станка. Установить заготовку из стали с пределом прочности 650 МПа, длиной L=1000 мм, назначить режимы резания: S=0,21 мм/об; t до 1 мм; V=60 м/мин
и проточить за один проход для получения вала с номинальным диаметром
Dн.
Таблица 2.1. Варианты номинальных диаметров валов
Номиналь- |
|
|
Варианты |
|
|
|
|
|
|
|
|
|
|
|
|
ный |
|
|
|
|
|
|
|
диаметр |
1 |
2 |
|
3 |
4 |
5 |
6 |
(мм) |
|
|
|
|
|
|
|
Dн |
31,18 |
31,20 |
|
31,10 |
31,15 |
31,17 |
31,13 |
|
|
|
|
|
|
|
|
2. Измерить диаметр вала, Di, через каждые 100 мм и результаты занести в табл. 2.2 в результаты эксперимента.
Таблица 2.2 Определение погрешности от упругих деформаций
Расст. от на- |
Результаты эксперимента |
Результаты расчета |
||
чала заготов- |
Di м) |
yi мм |
i,(мкм/Н) |
yi (мм) |
ки до |
|
|
|
|
измеряемого |
|
|
|
|
участка |
|
|
|
|
X, мм |
|
|
|
|
|
|
|
|
|
3. Рассчитать погрешность обработки по радиусу yi в каждом сечении и результат занести в табл. 2.2.
28
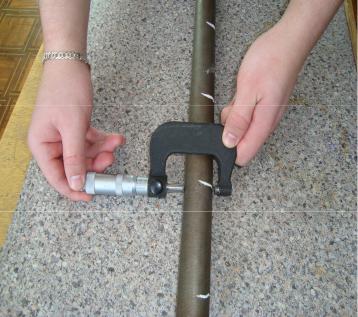
Рис.2.1. Измерение диаметра вала по сечениям
4.Определить расчетным путем по формуле (2.3) податливость системы в каждом сечении вала i и результаты занести в табл. 2.2.
5.По формуле (2.5) рассчитать погрешность обработки вала и занести в табл. 2.2.
6.Построить графики изменения погрешности обработки от упругих деформаций по длине обрабатываемого вала.
7.Проанализировать полученные результаты, сделать выводы о точности обработки и предложить варианты повышения точности при токарной обработке валов.
8.Составить отчет.
Контрольные вопросы
1.Какую заготовку вала называют «нежесткой»?
2.Как повлияет на форму длинномерной заготовки увеличенное значение податливости задней бабки станка?
3.В какой точке длинномерной заготовки максимальная податливость?
4.Какими технологическими способами можно повысить точность токарной обработки валов?
29