
- •Important Comments
- •Legal Principles
- •Copyright
- •Personnel Qualification
- •Intended Use
- •Symbols
- •Font Conventions
- •Number Notation
- •Scope
- •Important Comments for Starting up
- •Abbreviation
- •The WAGO-I/O-SYSTEM 750
- •Technical Data
- •Manufacturing Number
- •Storage, Assembly and Transport
- •Mechanical Setup
- •Installation Position
- •Total Expansion
- •Assembly onto Carrier Rail
- •Carrier rail properties
- •WAGO DIN Rail
- •Spacing
- •Plugging and Removal of the Components
- •Assembly Sequence
- •Internal Bus / Data Contacts
- •Power Contacts
- •Wire connection
- •Power Supply
- •Isolation
- •System Supply
- •Connection
- •Alignment
- •Field Supply
- •Connection
- •Fusing
- •Supplementary power supply regulations
- •Supply example
- •Power Supply Unit
- •Grounding
- •Grounding the DIN Rail
- •Framework Assembly
- •Insulated Assembly
- •Grounding Function
- •Grounding Protection
- •Shielding (Screening)
- •General
- •Bus Conductors
- •Signal Conductors
- •WAGO Shield (Screen) Connecting System
- •Assembly Guidelines / Standards
- •Fieldbus Controller
- •Fieldbus Controller 750-841
- •Description
- •Hardware
- •View
- •Device Supply
- •Fieldbus Connection
- •Display Elements
- •Configuration and Programming Interface
- •Operating Mode Switch
- •Hardware Address (MAC-ID)
- •Operating System
- •Start-up
- •PLC Cycle
- •Process Image
- •Example of a Process Input Image
- •Example of a Process Output Image
- •Fieldbus specific Process Data Architecture for MODBUS/TCP
- •Digital Input Modules
- •Digital Output Modules
- •Analog Input Modules
- •Analog Output Modules
- •Specialty Modules
- •Data Exchange
- •Memory Areas
- •Addressing
- •Addressing the I/O Modules
- •Address Range
- •Absolute Addresses
- •Data Exchange between MODBUS TCP Master and I/O Modules
- •Data Exchange between Ethernet IP Master and I/O Modules
- •Data Exchange between PLC Functionality (CPU) and I/O Modules
- •Data Exchange between Master and PLC Functionality (CPU)
- •Example MODBUS TCP Master and PLC functionality (CPU)
- •Comparison of MODBUS TCP Addresses and IEC 61131-3 Addresses
- •Starting up an ETHERNET TCP/IP fieldbus node
- •Connecting PC and Fieldbus Node
- •Determining IP Addresses
- •Allocating the IP Address to the Fieldbus Node
- •Testing the Function of the Fieldbus Node
- •Deactivating the BootP Protocol
- •Programming the PFC with WAGO-I/O-PRO CAA
- •WAGO-I/O-PRO CAA library elements for ETHERNET
- •IEC 61131-3-Program transfer
- •Transmission via the Serial Interface
- •Transmission by the Fieldbus
- •Information on the web-based management system
- •LED Display
- •Blink code
- •Fieldbus status
- •Node status
- •Fault Message via Blink Code from the I/O-LED
- •Supply voltage status
- •Fault behavior
- •Fieldbus failure
- •Internal bus fault
- •Technical Data
- •I/O Modules
- •General
- •Digital Input Modules
- •Digital Output Modules
- •Analog Intput Modules
- •Analog Output Modules
- •Counter Modules
- •ETHERNET
- •General
- •Network Architecture – Principles and Regulations
- •Transmission Media
- •Network Topologies
- •Coupler Modules
- •Important Terms
- •Network Communication
- •Protocol layer model
- •Communication Protocols
- •ETHERNET
- •Channel access method
- •IP-Protocol
- •IP Multicast
- •TCP Protocol
- •Application Protocols
- •MODBUS
- •Ethernet/IP
- •BootP (Bootstrap Protocol)
- •HTTP (HyperText Transfer Protocol)
- •DHCP (Dynamic Host Configuration Protocol)
- •DNS (Domain Name Systems)
- •SNTP-Client (Simple Network Time Protocol)
- •FTP-Server (File Transfer Protocol)
- •SNMP V1 (Simple Network Management Protocol)
- •Configuration of SNMP
- •Description of MIB II
- •IpNetToMediaTable
- •Traps
- •SMTP (Simple Mail Transfer Protocol)
- •MODBUS Functions
- •General
- •Use of the MODBUS Functions
- •Description of the MODBUS Functions
- •Function Code FC1 (Read Coils)
- •Function Code FC2 (Read Input Discretes)
- •Function Code FC3 (Read multiple registers)
- •Function code FC4 (Read input registers)
- •Function Code FC5 (Write Coil)
- •Function Code FC6 (Write single register)
- •Function Code FC11 (Get comm event counter)
- •Function Code FC15 (Force Multiple Coils)
- •Function Code FC16 (Write multiple registers)
- •Function Code FC22 (Mask Write Register)
- •Function Code FC23 (Read/Write multiple registers)
- •MODBUS Register Mapping
- •Internal Variables
- •Description of the internal variables
- •Watchdog (Fieldbus failure)
- •Watchdog Register:
- •Diagnostic Functions
- •Configuration Functions
- •Firmware Information
- •Constant Registers
- •Ethernet/IP (Ethernet/Industrial Protocol)
- •General
- •Characteristics of the Ethernet/IP Protocol Software
- •Object model
- •General
- •Classes
- •CIP Common Classes
- •Static Assembly Instances
- •Application examples
- •Test of MODBUS protocol and fieldbus nodes
- •Visualization and control using SCADA software
- •Use in Hazardous Environments
- •Foreword
- •Protective measures
- •Classification meeting CENELEC and IEC
- •Divisions
- •Explosion protection group
- •Unit categories
- •Temperature classes
- •Types of ignition protection
- •Classifications meeting the NEC 500
- •Divisions
- •Explosion protection groups
- •Temperature classes
- •Identification
- •For Europe
- •For America
- •Installation regulations
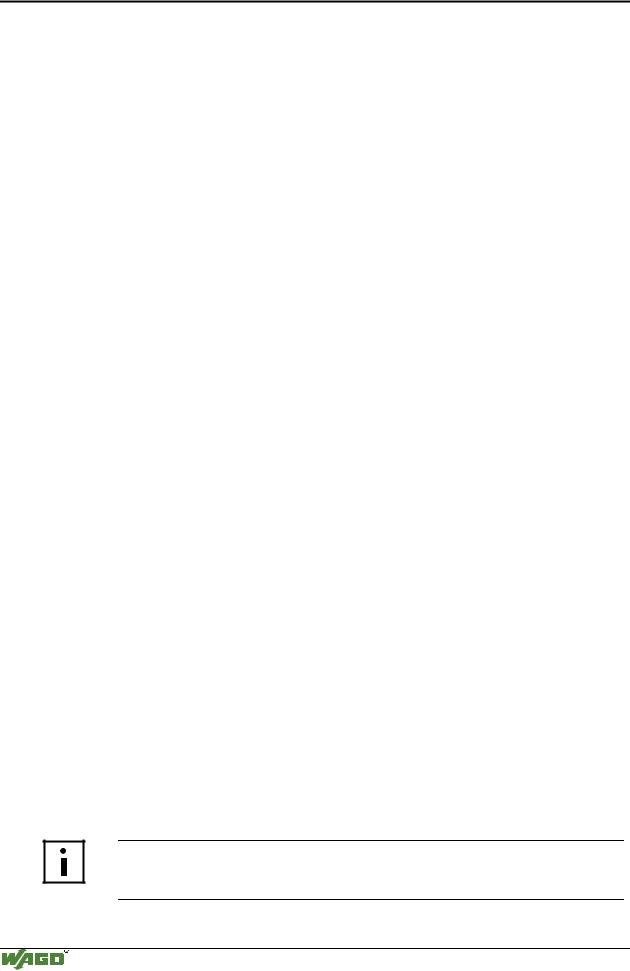
202 • Use in Hazardous Environments
Classification meeting CENELEC and IEC
9.3.5 Types of ignition protection
Ignition protection defines the special measures to be taken for electrical components in order to prevent the ignition of surrounding explosive atmospheres. For this reason a differentiation is made between the following types of ignition protection:
Identifi- |
CENELEC |
IEC |
Explanation |
Application |
|
cation |
standard |
standard |
|
|
|
EEx o |
EN 50 015 |
IEC 79-6 |
Oil encapsulation |
Zone 1 + 2 |
|
|
|
|
|
|
|
EEx p |
EN 50 016 |
IEC 79-2 |
Overpressure |
Zone 1 + 2 |
|
|
|
|
encapsulation |
|
|
EEx q |
EN 50 017 |
IEC 79-5 |
Sand encapsulation |
Zone 1 + 2 |
|
|
|
|
|
|
|
EEx d |
EN 50 018 |
IEC 79-1 |
Pressure resistant |
Zone 1 + 2 |
|
|
|
|
encapsulation |
|
|
EEx e |
EN 50 019 |
IEC 79-7 |
Increased safety |
Zone 1 |
+ 2 |
|
|
|
|
|
|
EEx m |
EN 50 028 |
IEC 79-18 |
Cast encapsulation |
Zone 1 |
+ 2 |
|
|
|
|
|
|
EEx i |
EN 50 020 (unit) |
IEC 79-11 |
Intrinsic safety |
Zone 0 |
+ 1 + 2 |
|
EN 50 039 (system) |
|
|
|
|
EEx n |
EN 50 021 |
IEC 79-15 |
Electrical components |
Zone 2 |
|
|
|
|
for zone 2 (see below) |
|
|
Ignition protection “n" describes exclusively the use of explosion protected electrical components in zone 2. This zone encompasses areas where explosive atmospheres can only be expected to occur rarely or short-term. It represents the transition between the area of zone 1, which requires an explosion protection and safe area in which for instance welding is allowed at any time.
Regulations covering these electrical components are being prepared on a world-wide scale. The standard EN 50 021 allows electrical component manufacturers to obtain certificates from the corresponding authorities for instance KEMA in the Netherlands or the PTB in Germany, certifying that the tested components meet the above mentioned standards draft.
Type “n” ignition protection additionally requires electrical components to be marked with the following extended identification:
•A – non spark generating (function modules without relay /without switches)
•AC – spark generating, contacts protected by seals (function modules with relays / without switches)
•L – limited energy (function modules with switch)
Further information
For more detailed information please refer to the national and/or international standards, directives and regulations!
WAGO-I/O-SYSTEM 750 ETHERNET TCP/IP