
- •Important Comments
- •Legal Principles
- •Copyright
- •Personnel Qualification
- •Intended Use
- •Symbols
- •Font Conventions
- •Number Notation
- •Scope
- •Important Comments for Starting up
- •Abbreviation
- •The WAGO-I/O-SYSTEM 750
- •Technical Data
- •Manufacturing Number
- •Storage, Assembly and Transport
- •Mechanical Setup
- •Installation Position
- •Total Expansion
- •Assembly onto Carrier Rail
- •Carrier rail properties
- •WAGO DIN Rail
- •Spacing
- •Plugging and Removal of the Components
- •Assembly Sequence
- •Internal Bus / Data Contacts
- •Power Contacts
- •Wire connection
- •Power Supply
- •Isolation
- •System Supply
- •Connection
- •Alignment
- •Field Supply
- •Connection
- •Fusing
- •Supplementary power supply regulations
- •Supply example
- •Power Supply Unit
- •Grounding
- •Grounding the DIN Rail
- •Framework Assembly
- •Insulated Assembly
- •Grounding Function
- •Grounding Protection
- •Shielding (Screening)
- •General
- •Bus Conductors
- •Signal Conductors
- •WAGO Shield (Screen) Connecting System
- •Assembly Guidelines / Standards
- •Fieldbus Controller
- •Fieldbus Controller 750-841
- •Description
- •Hardware
- •View
- •Device Supply
- •Fieldbus Connection
- •Display Elements
- •Configuration and Programming Interface
- •Operating Mode Switch
- •Hardware Address (MAC-ID)
- •Operating System
- •Start-up
- •PLC Cycle
- •Process Image
- •Example of a Process Input Image
- •Example of a Process Output Image
- •Fieldbus specific Process Data Architecture for MODBUS/TCP
- •Digital Input Modules
- •Digital Output Modules
- •Analog Input Modules
- •Analog Output Modules
- •Specialty Modules
- •Data Exchange
- •Memory Areas
- •Addressing
- •Addressing the I/O Modules
- •Address Range
- •Absolute Addresses
- •Data Exchange between MODBUS TCP Master and I/O Modules
- •Data Exchange between Ethernet IP Master and I/O Modules
- •Data Exchange between PLC Functionality (CPU) and I/O Modules
- •Data Exchange between Master and PLC Functionality (CPU)
- •Example MODBUS TCP Master and PLC functionality (CPU)
- •Comparison of MODBUS TCP Addresses and IEC 61131-3 Addresses
- •Starting up an ETHERNET TCP/IP fieldbus node
- •Connecting PC and Fieldbus Node
- •Determining IP Addresses
- •Allocating the IP Address to the Fieldbus Node
- •Testing the Function of the Fieldbus Node
- •Deactivating the BootP Protocol
- •Programming the PFC with WAGO-I/O-PRO CAA
- •WAGO-I/O-PRO CAA library elements for ETHERNET
- •IEC 61131-3-Program transfer
- •Transmission via the Serial Interface
- •Transmission by the Fieldbus
- •Information on the web-based management system
- •LED Display
- •Blink code
- •Fieldbus status
- •Node status
- •Fault Message via Blink Code from the I/O-LED
- •Supply voltage status
- •Fault behavior
- •Fieldbus failure
- •Internal bus fault
- •Technical Data
- •I/O Modules
- •General
- •Digital Input Modules
- •Digital Output Modules
- •Analog Intput Modules
- •Analog Output Modules
- •Counter Modules
- •ETHERNET
- •General
- •Network Architecture – Principles and Regulations
- •Transmission Media
- •Network Topologies
- •Coupler Modules
- •Important Terms
- •Network Communication
- •Protocol layer model
- •Communication Protocols
- •ETHERNET
- •Channel access method
- •IP-Protocol
- •IP Multicast
- •TCP Protocol
- •Application Protocols
- •MODBUS
- •Ethernet/IP
- •BootP (Bootstrap Protocol)
- •HTTP (HyperText Transfer Protocol)
- •DHCP (Dynamic Host Configuration Protocol)
- •DNS (Domain Name Systems)
- •SNTP-Client (Simple Network Time Protocol)
- •FTP-Server (File Transfer Protocol)
- •SNMP V1 (Simple Network Management Protocol)
- •Configuration of SNMP
- •Description of MIB II
- •IpNetToMediaTable
- •Traps
- •SMTP (Simple Mail Transfer Protocol)
- •MODBUS Functions
- •General
- •Use of the MODBUS Functions
- •Description of the MODBUS Functions
- •Function Code FC1 (Read Coils)
- •Function Code FC2 (Read Input Discretes)
- •Function Code FC3 (Read multiple registers)
- •Function code FC4 (Read input registers)
- •Function Code FC5 (Write Coil)
- •Function Code FC6 (Write single register)
- •Function Code FC11 (Get comm event counter)
- •Function Code FC15 (Force Multiple Coils)
- •Function Code FC16 (Write multiple registers)
- •Function Code FC22 (Mask Write Register)
- •Function Code FC23 (Read/Write multiple registers)
- •MODBUS Register Mapping
- •Internal Variables
- •Description of the internal variables
- •Watchdog (Fieldbus failure)
- •Watchdog Register:
- •Diagnostic Functions
- •Configuration Functions
- •Firmware Information
- •Constant Registers
- •Ethernet/IP (Ethernet/Industrial Protocol)
- •General
- •Characteristics of the Ethernet/IP Protocol Software
- •Object model
- •General
- •Classes
- •CIP Common Classes
- •Static Assembly Instances
- •Application examples
- •Test of MODBUS protocol and fieldbus nodes
- •Visualization and control using SCADA software
- •Use in Hazardous Environments
- •Foreword
- •Protective measures
- •Classification meeting CENELEC and IEC
- •Divisions
- •Explosion protection group
- •Unit categories
- •Temperature classes
- •Types of ignition protection
- •Classifications meeting the NEC 500
- •Divisions
- •Explosion protection groups
- •Temperature classes
- •Identification
- •For Europe
- •For America
- •Installation regulations
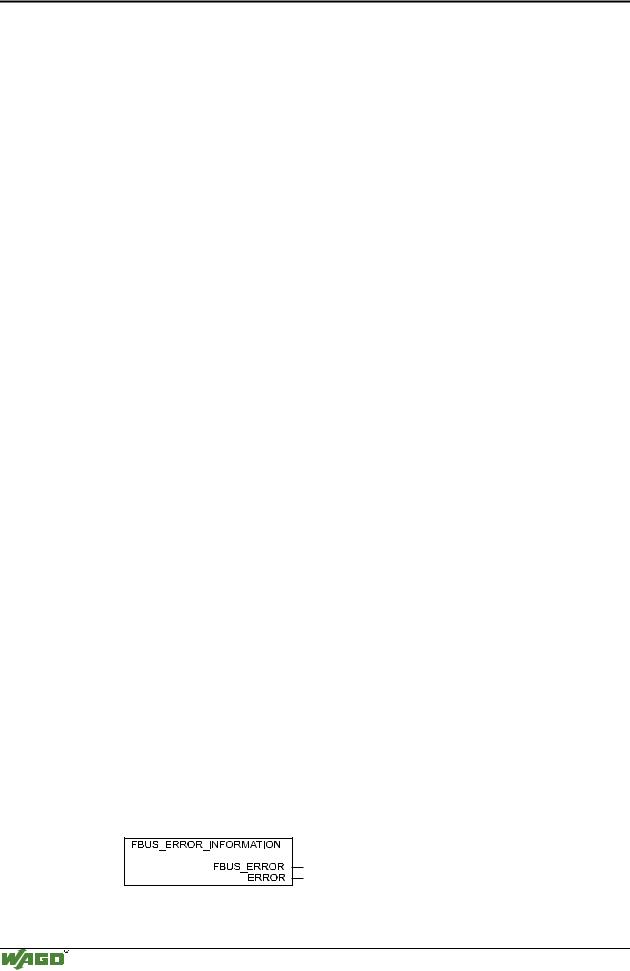
100 • Fieldbus Controller 750-841
Fault behavior
3.1.8.5 ‘USR‘-LED
The state of the ‘USR‘ LED is programmable with WAGO-I/O-PRO CAA. Functions in the program library ”Visual.lib“ can be used to control the LED state. One of the many possible uses of this LED is to indicate the RUN/STOP state of your controller.
3.1.8.6 Supply voltage status
The two green LED’s in the controller supply section, display the status of the supply voltage. The left LED (A) indicates the status of the 24 V supply for the controller. The right LED (B or C) displays the status of the field side supply (i.e., the power jumper contacts).
LED |
Meaning |
Trouble shooting |
A |
|
|
green |
Operating voltage for the system exists. |
|
OFF |
No operating voltage for the system. |
Check the supply voltage (24V and 0V). |
B or C |
|
|
green |
Operating voltage for the power jumper contacts |
|
|
exists. |
|
OFF |
No operating voltage for the the power jumper |
Check the supply voltage (24V and 0V). |
|
contacts. |
|
3.1.9 Fault behavior
3.1.9.1 Fieldbus failure
When a Modbus TCP fieldbus failure occurs (e.g., the Ethernet cable is removed or broke), the outputs that are controlled by the fieldbus port remain in their current state by default. If this behavior is undesirable, a fieldbus watchdog timer can be programmed to monitor Fieldbus communications. The watchdog monitors the data transfer between the master controls and the PFC. In the event of a watchdog timeout (i.e., there is a Fieldbus failure), the PFC can be programmed to control the state of the outputs, based on your application needs. In the case of fault free communications, the watchdog timer will not timeout, since after each successful data transfer the watchdog timer is reset.
Monitoring the watchdog time in the PFC is done by using the function block 'FBUS_ERROR_INFORMATION' in the control program. This function is part of the “mod_com.lib” library.
Fig. 3-16: Function block for determining a fieldbus failure |
g012926x |
WAGO-I/O-SYSTEM 750
ETHERNET TCP/IP
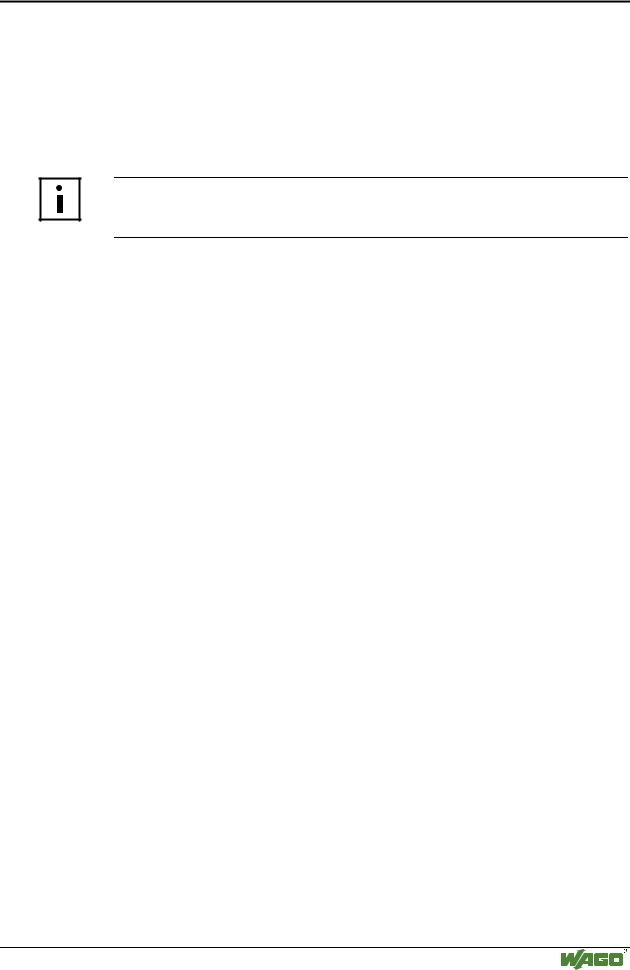
Fieldbus Controller 750-841 • 101
Fault behavior
'FBUS_ERROR' (BOOL) = FALSE = no fault
|
= TRUE = fieldbus failure |
|
'ERROR' (WORD) |
= 0 |
= no fault |
|
= 1 |
= fieldbus failure |
More information
For detailed information to the Watchdog register see the Chapters "MODBUS Functions"; "Watchdog (Fieldbus failure)" and "Watchdog Register".
3.1.9.2 Internal bus fault
When an internal bus fault occurs (e.g., an I/O module is removed), all output modules turn off. Additionally, the "I/O" LED blinks red and generates a fault message. This message is decoded from the blink code, in the form of a fault code and fault argument.
Once the internal bus fault is fixed, the controller is restarted by cycling its power. At this point the transfer of the process data resumes and the outputs are updated.
WAGO-I/O-SYSTEM 750 ETHERNET TCP/IP