
- •TABLE OF CONTENTS
- •Important Comments
- •Legal Principles
- •Copyright
- •Personnel Qualification
- •Intended Use
- •Symbols
- •Font Conventions
- •Number Notation
- •Scope
- •Abbreviation
- •The WAGO-I/O-SYSTEM 750
- •System Description
- •Technical Data
- •Manufacturing Number
- •Storage, Consignment and Transport
- •Mechanical Setup
- •Installation Position
- •Total Expansion
- •Assembly onto Carrier Rail
- •Carrier rail properties
- •WAGO DIN Rail
- •Spacing
- •Plugging and Removal of the Components
- •Assembly Sequence
- •Internal Bus / Data Contacts
- •Power Contacts
- •Wire connection
- •Power Supply
- •Isolation
- •System Supply
- •Connection
- •Alignment
- •Field Supply
- •Connection
- •Fusing
- •Supplementary power supply regulations
- •Supply example
- •Power Supply Unit
- •Grounding
- •Grounding the DIN Rail
- •Framework Assembly
- •Insulated Assembly
- •Function Earth
- •Protective Earth
- •Shielding (screening)
- •General
- •Bus Conductors
- •Signal Conductors
- •WAGO Shield (Screen) Connecting System
- •Assembly Guidelines / Norms
- •Fieldbus Coupler/Controller
- •Fieldbus Coupler 750-306
- •Description
- •Hardware
- •View
- •Device Supply
- •Fieldbus Connection
- •Display Elements
- •Configuration Interface
- •Hardware Address (MAC ID)
- •Setting the Baud Rate
- •Operating System
- •Process Image
- •Data Exchange
- •Communication Interfaces
- •Memory Areas
- •Addressing
- •Fieldbus Specific
- •Configuration Software
- •Starting up DeviceNet Fieldbus Nodes
- •Connecting the PC and Fieldbus Node
- •Setting the MAC ID and Baud Rate
- •Configuration with Static Assembly
- •LED Display
- •Node Status
- •Blink Code
- •Fault Message via the Blink Code of the I/O LED
- •Supply Voltage Status
- •Technical Data
- •Fieldbus Controller 750-806
- •Description
- •Hardware
- •View
- •Device Supply
- •Fieldbus Connection
- •Display Elements
- •Configuration and Programming Interface
- •Operating Mode Switch
- •Hardware Address (MAC ID)
- •Setting the Baud Rate
- •Operating System
- •Start-up
- •PLC Cycle
- •Process Image
- •Data Exchange
- •Communication Interfaces
- •Memory Areas
- •Addressing
- •Fieldbus Specific
- •Absolute Addressing
- •Calculate Addresses
- •Address Range for I/O Module Data
- •Address Range for Fieldbus Variables
- •Address Range for Flags
- •Example for Absolute Addresses
- •Programming the PFC with WAGO-I/O-PRO 32
- •WAGO-I/O-PRO 32 Library Elements
- •IEC 61131-3 Program Transfer
- •Transmission via the Serial Interface
- •Transmission via the Fieldbus
- •Special DeviceNet Features of the Controller
- •Connection via the UCMM port
- •Offline Connection Set
- •DeviceNet Shutdown
- •Dynamic Assembly
- •Change MAC ID by SW
- •Heartbeat
- •Bit-Strobe
- •Configuration Software
- •Starting-up DeviceNet Fieldbus Nodes
- •Connecting the PC and Fieldbus Node
- •Setting the MAC ID and Baud Rate
- •Configuration with Static and Dynamic Assembly
- •LED Display
- •Node Status
- •Blink Code
- •Fault Message via the Blink Code of the I/O LED
- •Supply Voltage Status
- •Technical Data
- •I/O modules
- •DeviceNet
- •Description
- •Network Architecture
- •Transmission Media
- •Type of Cable
- •Cable Types
- •Maximum Bus Length
- •Cabling
- •Network Topology
- •Network Grounding
- •Interface Modules
- •Network Communication
- •Objects, Classes, Instances and Attributes
- •Module Characteristics
- •Communication Model
- •Message Groups
- •Message Types
- •I/O Messaging
- •Explicit Messaging
- •I/O Messaging Connections
- •Process data and Diagnostic Status
- •Process Image
- •Assembly Instances
- •Configuration / Parametering with the Object Model
- •EDS Files
- •Object Model
- •Identity Class (0x01):
- •Message Router (0x02):
- •DeviceNet Object (0x03):
- •Assembly Object (0x04):
- •Connection Object (0x05):
- •Acknowledge Handler Object (0x2B):
- •Coupler configuration object (0x64):
- •Discrete Output Point Object (0x66):
- •Analog Input Point Object (0x67):
- •Analog Output Point Object (0x68):
- •Supplement to the Object Model for Controller 750-806
- •Bit-Strobe
- •Dynamic Assembly
- •New Classes for the PFC Fieldbus Variables
- •Class 160 (0xA0) Input PLC Fieldbus Variable USINT
- •Class 161 (0xA1) Input Fieldbus Variable USINT
- •Class 162 (0xA2) Input Fieldbus Variable USINT
- •Class 163 (0xA3) Output Fieldbus Variable USINT
- •Class 164 (0xA4) Output Fieldbus Variable USINT
- •Class 165 (0xA5) Output Fieldbus Variable USINT
- •Class 166 (0xA6) Input Fieldbus Variable UINT
- •Class 167 (0xA7) Input Fieldbus Variable UINT
- •Class 168 (0xA8) Output Fieldbus Variable UINT
- •Class 169 (0xA9) Output Fieldbus Variable UINT
- •Class 170 (0xAA) Input Fieldbus Variable UDINT
- •Class 171 (0xAB) Input Fieldbus Variable UDINT
- •Class 172 (0xAC) Output Fieldbus Variable UDINT
- •Class 173 (0xAD) Output Fieldbus Variable UDINT
- •Class 100 (0x64) - Attribute 44/100/101
- •Identity Class 1 (0x01)
- •Connection Object (0x05)
- •Additional Assembly Instances 10 and 11
- •Application in Explosive Environments
- •Foreword
- •Protective Measures
- •Classification Meeting CENELEC and IEC
- •Divisions
- •Explosion Protection Group
- •Unit Categories
- •Temperature Classes
- •Types of Ignition Protection
- •Classifications Meeting the NEC 500
- •Divisions
- •Explosion Protection Groups
- •Temperature Classes
- •Identification
- •For Europe
- •For America
- •Installation Regulations
- •Glossary
- •Literature List
- •Index
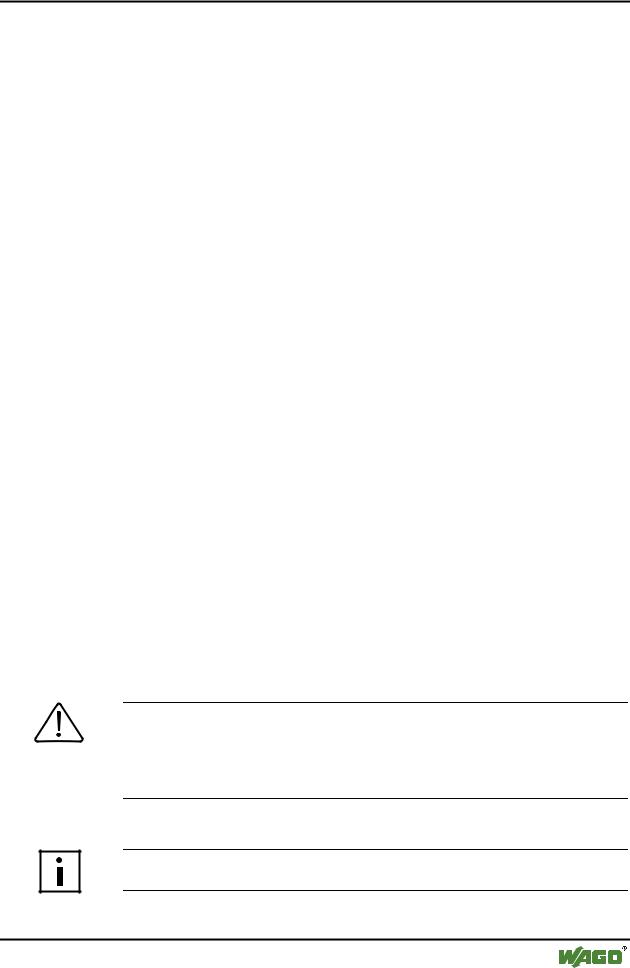
Feldbus-Koppler/-Controller • 85
Fieldbus Controller 750-806
3.2.7 Special DeviceNet Features of the Controller
3.2.7.1 Connection via the UCMM port
In contrast to the fieldbus Coupler 750-306 as a Group 2 Only Server, the DeviceNet Controller supports the dynamic connection via the UCMM port (Unconnected Message Manager Port).
For the Controller, the simultaneous set-up of 5 explicit and 5 dynamic I/O connections, i.e. the connection with 5 subscribers, is possible.
3.2.7.2 Offline Connection Set
Due to the Offline Connection Set, the fieldbus node can be addressed via the network when this node has been switched off because of a double MAC ID and is in a Communication Fault status. After being addressed, the MAC ID of the fieldbus Controller can be changed using the software.
3.2.7.3 DeviceNet Shutdown
The Device Shutdown allows the fieldbus node to log out from a control in a defined manner if the node is switched off due to internal faults. This function can be used in a targeted way in DeviceNet networks subject to very high safety requirements, such as e.g. in the chemical industry or in semi-conductor production.
3.2.7.4 Dynamic Assembly
An Assembly Object is used to group data (e.g. I/O data) to form blocks to be sent as a single message. The static Assembly allows the user to access permanently pre-programmed Assembly Instances in the fieldbus Controller. The dynamic Assembly, on the other hand, offers the possibility to set up Assembly Instances in which process data from various application objects can be configured as required.
In addition to the I/O data transmission, the dynamic assembly can also be used for a targeted selection of data which are to be transmitted explicitly via the fieldbus, or those which are explicitly not to be transmitted via the fieldbus.
Attention
To set the pysical outputs with the PFC either use the dynamic assembly or the instance 11 of the static assemblies. With this, you do not enter the physical outputs into the mapping in order to prevent the output data from being transmitted and temporary overwritten by the fieldbus.
Further information
You can find more details in chapter 5.6.2.2.2 "Dynamic Assembly".
WAGO-I/O-SYSTEM 750
DeviceNet
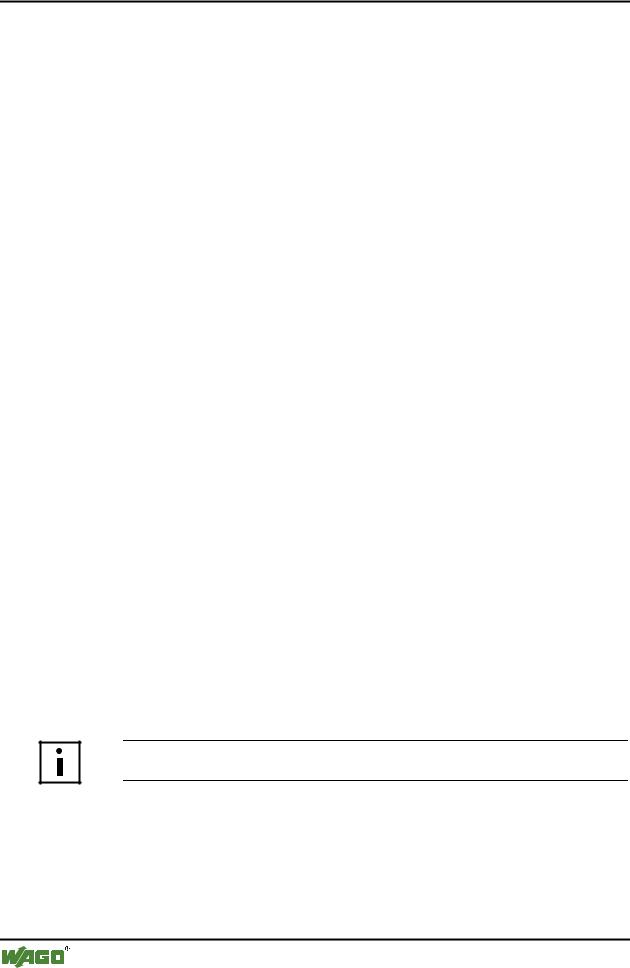
86 • Feldbus Coupler/Controller
Fieldbus Controller 750-806
3.2.7.5 Change MAC ID by SW
The MAC ID of the Controller can be changed via the network using the software (e.g. WAGO NETCON, RS NetWorx). For this purpose, the node address is stored in non-volatile memory. Should the address set at the DIP switch differ from the one set via the network using the software, the I/O LED changes its colour to orange.
To reset the software default address, the invalid address 64 is entered in class 3, instance 1, attribute 1.
Subsequently, the Controller has its MAC ID that is set at the DIP switch.
3.2.7.6 Heartbeat
The heartbeat function permits a node to cyclically transmit a so-called heartbeat message and, in this manner, to signal its communication ability to all members in the network.
If a responsible heartbeat consumer does not receive a message within a predefined time (Heartbeat Consuming Time), this is registered as a heartbeat fault. The relationship between producer and consumer of a Heartbeatmessage can be configured by entries in the object directory, so the time between two Heartbeat messages can be entered in Class 0x01, Instance 1, Attribut ID 10 (0x0A).
3.2.7.7 Bit-Strobe
The bit strobe I/O connection is always a 1 to n multicast connection.
In other words, a master can reach with its message all slaves supporting the bit strobe command. The transfer takes place at the same time. In this manner it is possible to synchronize the slaves.
The length of this master message is limited to 8 bytes. Each node address in the net is assigned a bit within the 8 data bytes. The reaction of the slave which bit is set is specific to the application. The reaction has to be defined and it has to be known by the PLC. With its answer, each slave can return 8 bytes of data. The order of the answers depends on the reaction time of the single slave and, in addition, it depends on the particular node address. If all slaves would reply to the Bit-Strobe command at the same time, the order of sending on the CAN bus would be determined by the node address (bit arbitration).
Further information
You can find more details in chapter 5.6.2.2.1 "Bit-Strobe".
WAGO-I/O-SYSTEM 750
DeviceNet