
- •TABLE OF CONTENTS
- •Important comments
- •Legal principles
- •Copyright
- •Personnel qualification
- •Intended use
- •Scope
- •Symbols
- •Font conventions
- •Number notation
- •Abbreviation
- •The WAGO-I/O-SYSTEM 750
- •System Description
- •General
- •Coupler/Controller (1)
- •I/O Modules (2)
- •End Module (3)
- •Installation
- •Safty notes
- •Mechanical Installation
- •Electrical Installation
- •Wire Connection
- •Change fuse
- •Power supply
- •System supply voltage
- •Supply Voltage Field Side
- •Manufacturing Number
- •Technical Data
- •Fieldbus coupler / controller
- •Fieldbus coupler 750-342
- •Description
- •Hardware
- •View
- •Device supply
- •Fieldbus connection
- •Display elements
- •Configuration interface
- •Operating system
- •Process image
- •Example of a process input image
- •Example of a process output image
- •Process data architecture for MODBUS/TCP
- •Data exchange
- •Memory areas
- •Addressing
- •Data exchange between MODBUS master and I/O modules
- •Starting up ETHERNET TCP/IP fieldbus nodes
- •Connecting PC and fieldbus node
- •Determining IP addresses
- •Allocating the IP address to the fieldbus node
- •Testing the function of the fieldbus node
- •Reading out the information as HTML pages
- •LED Display
- •Blink code
- •Fieldbus status
- •Node status
- •Fault behavior
- •Fieldbus failure
- •Internal bus fault
- •Technical Data
- •Fieldbus controller 750-842
- •Description
- •Hardware
- •View
- •Device supply
- •Fieldbus connection
- •Display elements
- •Configuration and programming interface
- •Operating mode switch
- •Operating system
- •Start-up
- •PLC cycle
- •Process image
- •Example of a process input image
- •Example of a process output image
- •Process data architecture for MODBUS/TCP
- •Data exchange
- •Memory areas
- •Addressing
- •Data exchange between master and I/O modules
- •Data exchange between PLC functionality (CPU) and I/O modules
- •Data exchange between master and PLC functionality (CPU)
- •Common access of MODBUS master and PLC functionality to outputs
- •Address review
- •Starting up ETHERNET TCP/IP fieldbus nodes
- •Connecting PC and fieldbus node
- •Determining IP addresses
- •Allocating the IP address to the fieldbus node
- •Testing the function of the fieldbus node
- •Viewing the HTML pages
- •Programming the PFC with WAGO-I/O-PRO 32
- •LED Display
- •Blink code
- •Fieldbus status
- •Node status
- •Supply voltage status
- •Fault behavior
- •Fieldbus failure
- •Internal bus fault
- •Technical Data
- •I/O modules
- •I/O modules-Review
- •Digital Inputs
- •Digital Outputs
- •Analog Inputs
- •Analog Outputs
- •Supply and End modules
- •Terminal blocks for encoder and resolvers
- •Special terminal blocks
- •ETHERNET
- •Network architecture – Principles and Regulations
- •Transmission media
- •Network topologies
- •Coupler modules
- •Important terms
- •Network communication
- •Channel access method
- •Communication protocols
- •ETHERNET
- •IP-Protocol
- •TCP protocol
- •ICMP
- •Application protocols
- •MODBUS/TCP
- •Bootstrap Protocol (BootP)
- •HyperText Transfer Protocol (HTTP)
- •Common MODBUS functions
- •Use of the MODBUS functions
- •Description of the MODBUS functions
- •Function code FC1 (Read Coils)
- •Function code FC2 (Read Discrete Inputs)
- •Function code FC3 (Read multiple registers)
- •Function code FC4 (Read input registers)
- •Function code FC5 (Write Coil)
- •Function code FC6 (Write single register)
- •Function code FC7 (Read Exception Status)
- •Function code FC16 (Write multiple registers)
- •Function code FC11 (Get comm event counter)
- •Function code FC23 (Read/Write multiple registers)
- •Watchdog (Fieldbus failure)
- •Diagnostic function
- •Configuration function
- •Firmware information
- •General Registers
- •Special PFC Register (only for controller 750-842)
- •Application examples
- •Test of MODBUS protocol and fieldbus nodes
- •Visualization and control using SCADA software
- •Application in Explosive Environments
- •Foreword
- •Protective measures
- •Classification meeting CENELEC and IEC
- •Divisions
- •Explosion protection group
- •Unit categories
- •Temperature classes
- •Types of ignition protection
- •Classifications meeting the NEC 500
- •Divisions
- •Explosion protection groups
- •Temperature classes
- •Identification
- •For Europe
- •For America
- •Installation regulations
- •Glossary
- •Literature list
- •Index

Fieldbus coupler 750-342 • 41
LED Display
3.1.7LED Display
The coupler possesses several LED’s for displaying the coupler operating status and the complete node status.
ETHERNET |
01 |
02 |
status |
|
voltage supply |
|
|||
ON |
A |
|
|
|
|
-power jumper contacts |
|
||
|
|
|
||
|
|
C |
|
|
LINK |
B |
|
-system |
|
|
D |
|
||
TxD/RxD |
24V 0V |
|
|
|
ERROR |
|
|
|
|
I/O |
+ |
+ |
|
|
|
|
|
||
Fig. 3-15: Display elements 750-342 |
G012901e |
A differentiation is made between the two groups of LEDs.
The first group = fieldbus contains the solid color LEDs having the designation ON (green), LINK (green), TxD/RxD (green) and ERROR (red) indicating the operating status of the communication via ETHERNET.
The second group = internal bus consists of the three-color I/O LED (red/green/orange). This LED is used to display the status of the internal bus and i. e. the status of the fieldbus node.
LEDs located on the right-hand side in the coupler feed section, show the status of the supply voltage.
3.1.7.1Blink code
A blink code displays detailed fault messages. A fault is cyclically displayed using up to 3 different blink sequences.
•The first blink sequence (approx. 10 Hz) indicates the fault display.
•After a pause a second blink sequence appears (approx. 1 Hz). The number of blink impulses gives the fault code.
•The third blink sequence (approx. 1 Hz) appears following a further pause. The number of blink pulses indicates the fault argument.
Modular I/O System
ETHERNET TCP/IP
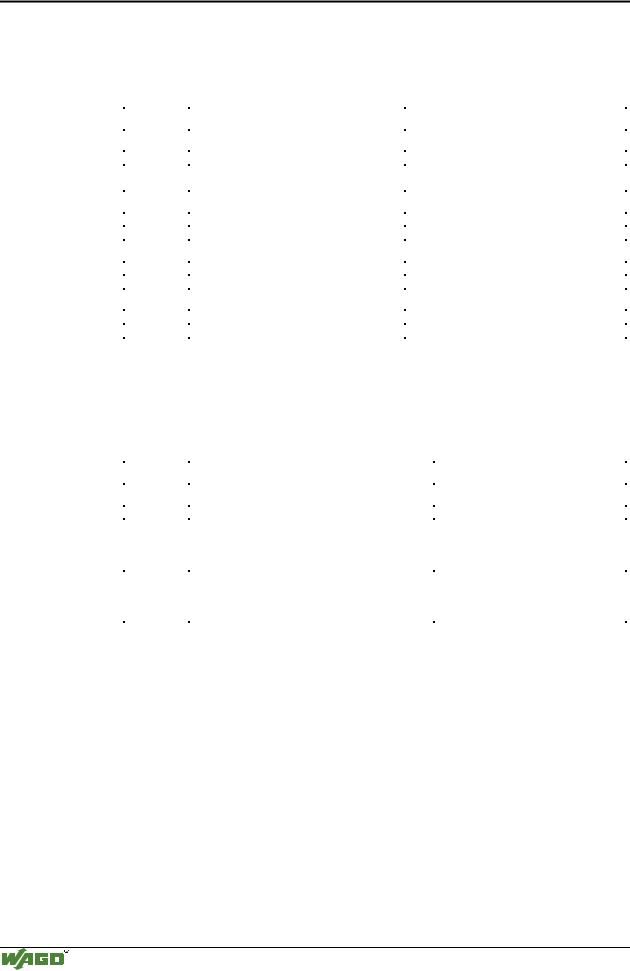
42 • Fieldbus coupler 750-342
LED Display
3.1.7.2Fieldbus status
The operating status of the communication via ETHERNET is signalled by means of the top LED group (ON, LINK, TxD/RxD and ERROR).
LED |
Meaning |
Trouble shooting |
|
|
|
ON |
|
|
|
|
|
green |
Fieldbus initialization is correct |
|
OFF |
Fieldbus initialization is not correct, |
Check the supply voltage (24V and 0V), |
|
no function or self-test |
check the IP configuration |
LINK |
|
|
|
|
|
green |
Link to a physical network exists |
|
OFF |
No link to a physical network |
Check the fieldbus connection. |
TxD/RxD |
|
|
|
|
|
green |
Data exchange taking place |
|
OFF |
No data exchange |
|
ERROR |
|
|
|
|
|
red |
Error on the fieldbus |
|
OFF |
No error on the fieldbus, normal operation |
|
3.1.7.3Node status
The operating status of the communication via the internal bus is signalled via the bottom I/O LED.
LED |
Meaning |
Trouble shooting |
|
|
|
I/O |
|
|
|
|
|
Green |
Fieldbus coupler operating perfectly |
|
Red |
a) During startup of fieldbus coupler: |
|
|
Internal bus being initialized, |
|
|
Startup displayed by LED flashing fast for approx. |
|
|
1-2 seconds |
|
Red |
b) After startup of fieldbus coupler: |
|
|
Errors, which occur, are indicated by three conse- |
Evaluate the fault message (fault code and |
|
cutive flashing sequences. There is a short pause |
fault argument). |
|
between each sequential flash. |
|
The coupler starts up after switching on the supply voltage. The "I/O" LED blinks. The "I/O" LED has a steady light following a fault free run-up.
In the case of a fault the "I/O" LED continues blinking. The fault is cyclically displayed by the blink code.
Modular I/O System
ETHERNET TCP/IP
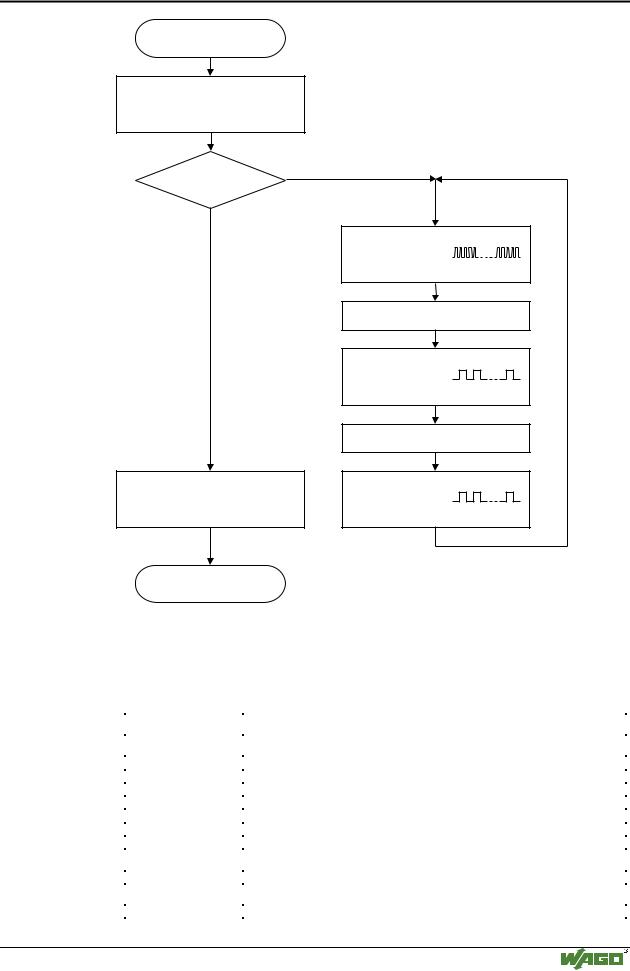
Fieldbus coupler 750-342 • 43
LED Display
Switching on the power supply
Coupler/Controller starts up
“I/O”-LED is blinking
No
Test o.k.?
Yes
“I/O”-LED is shining
ready for operation
“I/O” LED
1st flash sequence
(Introduction of the error indication)
1st break
“I/O” LED
2nd flash sequence
Error code
(Number of flash cycles)
2nd break
“I/O” LED
3rd flash sequence
Error argument
(Number of flash cycles)
Fig. 3-16: Signalling of the LED for indication of the node status |
g012911e |
After clearing a fault, restart the coupler by cycling the power.
3.1.7.4Fault message via blink code from the I/O-LED
Fault argument |
Fault description |
|
|
Fault code 1: Hardware and Configuration fault |
|
|
|
0 |
EEPROM check sum fault / check sum fault in the parameter area of the flash memory |
1 |
Overflow of the internal buffer memory for the inline code |
2 |
Unknown data type |
3 |
Module type of the flash program memory could not be determined / is incorrect |
4 |
Fault when writing in the FLASH memory |
5 |
Fault when deleting the FLASH memory |
6 |
Changed I/O module configuration determined after AUTORESET |
Fault code 2: Fault in programmed configuration |
|
|
|
0 |
Incorrect table entry |
Fault code 3: Internal bus command fault |
|
|
|
0 |
No error argument is put out. |
Modular I/O System
ETHERNET TCP/IP
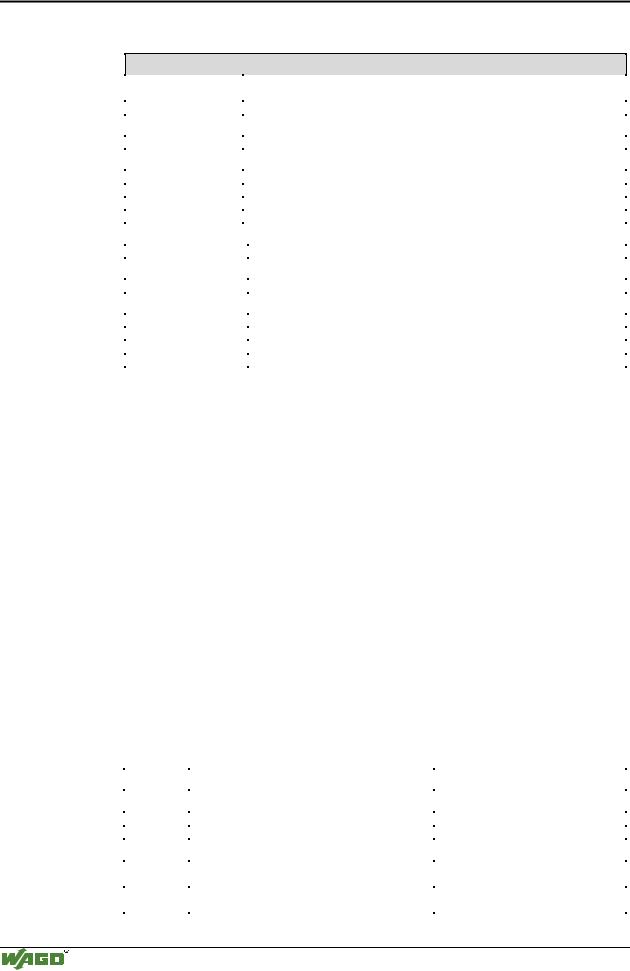
44 • Fieldbus coupler 750-342 LED Display
Fault code 4: Internal bus data fault
0 |
Data fault on internal bus or |
|
|
Internal bus interruption on coupler |
|
n* (n>0) |
Internal bus interrupted after I/O module n |
|
Fault code 5: Fault during register communication |
||
|
|
|
n* |
Internal bus fault during register communication after I/O module n |
|
Fault code 6: Fieldbus specific error |
||
|
|
|
1 |
No reply from the BootP server |
|
2 |
ETHERNET controller not recognized |
|
3 |
Invalid MACID |
|
4 |
TCP/IP initialization error |
|
Fault code 7: I/O module is not supported |
||
|
|
|
n* |
|
I/O module at position n is not supported |
Fault code 8: not used |
|
|
|
|
|
0 |
|
Fault code 8 is not used. |
Fault code 9: CPU-TRAP error |
||
|
|
|
1 |
|
Illegal Opcode |
2 |
|
Stack overflow |
3 |
|
Stack underflow |
4 |
|
NMI |
* The number of blink pulses (n) indicates the position of the I/O module. I/O modules without data are not counted (i.e. supply modules without diagnostics).
Example for a fault message
Fault: The 13th I/O module has been removed.
1.The "I/O" LED starts the fault display with the first blink sequence (approx. 10 Hz).
2.The second blink phase (approx. 1 Hz) follows the first pause. The "I/O" LED blinks four times and thus signals the fault code 4 (internal bus data fault).
3.The third blink sequence follows the second pause. The "I/O ERR" LED
blinks twelve times. The fault argument 12 means that the internal bus is interrupted after the 12th I/O module. Supply voltage status
There are two green LED’s in the coupler supply section to display the supply voltage. The left LED (A) indicates the 24 V supply for the coupler. The right hand LED (C) signals the supply to the field side, i.e. the power jumper contacts.
LED |
Meaning |
Trouble shooting |
|
|
|
A |
|
|
|
|
|
green |
Operating voltage for the system exists. |
|
OFF |
No operating voltage for the system. |
Check the supply voltage (24V and 0V). |
C |
|
|
|
|
|
green |
Operating voltage for the power jumper contacts |
|
|
exists. |
|
OFF |
No operating voltage for the the power jumper con- |
Check the supply voltage (24V and 0V). |
|
tacts. |
|
Modular I/O System
ETHERNET TCP/IP