
Кузнецов А.Е., Градова Н.Б., Лушников С.В. и др. Прикладная экобиотехнология. Учебное пособие. В 2-х томах
.pdfПереработка органических отходов |
341 |
пространенным крупногабаритным аппаратом является аппарат с общим объемом около 100 м3, поскольку его еще можно перевезти по железной дороге. При большем объеме монтаж ферментера ведут на месте.
Материалы для ферментеров: легированная нержавеющая сталь. Обычные марки стали, черный чугун, эмалированный чугун не используются.
Верхняя крышка ферментера обычно приваривается (в отличие от химических аппаратов) – для обеспечения герметичности (фланцевые соединения не обеспечивают герметичности, так как прокладки пробиваются, особенно под давлением при стерилизации). В ферментере имеется люк (монтируется на болтах), через который можно пролезть внутрь для монтажа теплообменника, барботера, мешалки, чистки поверхностей внутри ферментера.
Порядок запуска ферментера в асептических условиях.
1.Осуществляют стерилизацию аппарата. Для этого заливают воду, подают пар либо в рубашку, либо в ферментер и пар в обвязку. Выдерживают несколько часов, затем опорожняют, продувают стерильным воздухом.
2.Загружают стерильную питательную среду (воду, источники углерода, макро- и микроэлементы).
3.Устанавливают рабочую температуру (26–55 °С) подачей холодной воды в рубашку.
4.Вносят стерильно посевной материал.
5.Начинают подавать чистый воздух (с температурой не выше 60–90 °C). При повышении температуры воздуха наблюдается повышенный брызгоунос (до 50% среды за ферментацию). Вариант возврата унесенных
питательных веществ не предусматривается из-за необходимости сохранения асептических условий.
Охлаждение ферментера. Выделение тепла в процессах биосинтеза и перемешивания приводит к нагреву ферментационной среды, поэтому, как правило, требуется охлаждение ферментера.
На большинстве ферментеров имеются рубашки. Если поверхности теплообмена не хватает, то монтируют дополнительные змеевики. Часто используют наружное орошение. Летом могут возникнуть проблемы с охлаждением, так как температура холодной воды (в месте водозабора) растет, разность температур по обе стороны теплообменной поверхности уменьшается и соответственно падает скорость теплоотвода, в связи с этим возможен перегрев ферментационной среды с превышением температуры выше оптимальной на 8–10 °С. В таких случаях требуется захолаживание воды или использование в качестве хладоагента рассола CaCl2. Затраты на охлаждение ферментера в этом случае резко повышаются.
В технологической схеме должны быть предусмотрены резервуары для промежуточных потоков – стерильных сред и ферментированной среды. Объем и количество резервуаров рассчитываются исходя из технологического потока и допустимых сроков хранения среды в резервуаре.
Если культуральную жидкость нужно долго хранить в промежуточных емкостях, то ее захолаживают (до 10 С), чтобы не развивалась посторонняя микрофлора.
Если по какой-либо причине наблюдается низкая активность продуцента (низкая конечная концентрация продукта), то такая ферментация является бра-
342 |
Глава 3 |
кованной. В этом случае приходится все содержимое ферментера сливать в трап и далее на очистные сооружения. Обычно доля таких ферментаций – не более нескольких процентов.
Чистка и мойка оборудования. Можно осуществлять чистку и мойку паром, однако это не совсем удобный метод – поверхности сложно очистить. Чаще используется мойка с химическими средствами. Они должны быть избирательными, инертными к материалу оборудования. Часто для мойки используется щелочь, сода с концентрацией 10–15%, затем оборудование и коммуникации промываются водой. Отработанный раствор при необходимости стерилизуется. В технологической схеме должна быть предусмотрена возможность чистки, мойки и дезинфекции всех аппаратов и трубопроводов.
3.2.1.2. Выделение и концентрирование биомассы и белковых веществ
При переработке жидких отходов в кормовые продукты глубинным культивированием биомассу одноклеточных организмов отделяют от ферментированной среды (бесклеточной, культуральной жидкости) и концентрируют различными методами или сгущают и сушат вместе с остатками субстрата и продуктами жизнедеятельности. При гетерофазном глубинном культивировании биомассу выделяют совместно с твердой фазой.
Для выделения клеток микроорганизмов из жидкой среды могут использоваться различные методы (см. разд. 1.8).
Декантация (седиментация), гравитационное уплотнение. В отличие от процессов биологической очистки сточных вод, в которых активный ил осаждается во вторичных отстойниках или на стадии предварительного уплотнения активного ила, в технологиях микробиологического синтеза эти способы применяются редко из-за низкой производительности, поскольку плотность микроорганизмов близка к плотности среды культивирования. Иногда для ускорения осаждения биомассы в среду добавляют коагулянты и флокулянты, способствующие образованию крупных флокул микроорганизмов и их осаждению. Сгущению активного ила, предназначенного для использования в качестве кормовой добавки, способствует введение минеральных веществ с коагулирующими свойствами, кормовых дрожжей р. Candida, биофлокулянтов, получаемых модификацией активного ила. Добавление дрожжей благоприятствует агрегированию хлопьев и увеличению скорости их осаждения. Аналогичный вариант, но с добавками активного ила, возможен и при выделении дрожжей из отработанной культуральной жидкости. Плотный осадок образуется при высоких концентрациях минерального коагулянта при совместном отстаивании суспензии активного ила и дрожжей в гравитационном поле.
Декантация и уплотнение позволяют уменьшить объем суспензии микроорганизмов, что приводит к снижению затрат на последующих стадиях переработки. Осадок после отстаивания можно направить в сепаратор для дополнительного сгущения микробной биомассы, а сгущенную биомассу подать в сушилку.
Переработка органических отходов |
343 |
Фильтрация. Используется достаточно широко на конечной стадии сгущения для выделения крупных мицелиальных форм микроорганизмов, дрож- жей-сахаромицетов. Применяются барабанные и ленточные прессы (при фильтрации кормового продукта, содержащего твердую фазу), фильтр-прессы, нутч-фильтры (при малом объеме жидкости). Фильтрация с намывным слоем возможна для выделения микроорганизмов совместно с остатками твердой фазы субстрата после гетерофазного культивирования. В качестве намывного слоя выступает твердая фаза переработанного субстрата. Перед фильтрацией суспензии микробных клеток возможно добавление древесных опилок несмолистых пород деревьев, древесной муки, диатомита, цеолитов, других присадочных материалов – инертных легкофильтрующихся веществ, которые создают крупнопористую структуру осадка. Этот прием улучшает фильтруемость и одновременно может быть использован для балансирования кормовых свойств получаемых продуктов.
Бактериальные микроорганизмы имеют малые размеры и для них обычные фильтры непригодны. В этом случае можно использовать микрофильтрацию и ультрафильтрацию.
Во всех методах фильтрации проблемой является быстрое забивание фильтров и мембран, что приводит к резкому падению (в десятки раз) их производительности. Приходится прикладывать большие усилия для поддержания удовлетворительных рабочих характеристик фильтров, многократно увеличивать площадь фильтрующей поверхности и габариты установок. Для повышения скорости фильтрации в суспензию микроорганизмов добавляют коагулянты или флокулянты, нагревают ее. Попадание в суспензию смолистых, слизистых и коллоидных примесей, масел и жиров ухудшает фильтруемость суспензии.
Центрифугирование и сепарация широко используются на биотехнологических предприятиях на первом этапе концентрирования микроорганизмов, если ферментационная среда не содержит остатков твердой фазы, абразивных примесей. Достоинства этого способа: простота, экономичность, возможность автоматизации. Недостаток – частая остановка центрифуг и сепараторов для мойки из-за наличия в суспензии частиц песка, остатков твердой фазы субстрата и т. п. Крупные микроорганизмы (дрожжи) отделяются легко, бактерии – сложнее. Для их отделения необходимо увеличивать число оборотов, диаметр ротора, что ведет к резкому увеличению затрат энергии. В промышленности для сгущения биомассы микроорганизмов наибольшее распространение получили тарельчатые сепараторы. Варианты организации сепарации: одноступенчатая, многоступенчатая (обычно двухступенчатая). Между ступенями сепарации возможен нагрев сепарируемой жидкости с биомассой. Это приводит к уменьшению вязкости среды и, следовательно, к большей производительности сепаратора, а также к увеличению степени отмывки клеток микроорганизмов от остаточных примесей, например капелек жира. После одноступенчатой сепарации концентрация микроорганизмов повышается с 1–2 до 3–6%. После двухступенчатой – до 15%.
В ходе сепарации небольшая часть микроорганизмов может уноситься с потоком осветленной культуральной жидкости. Потери дрожжей после сепарации
344 |
Глава 3 |
в результате уноса обычно не превышают 1–2% от всего количества биомассы. Бактерии хуже сепарируются из-за своих размеров, что приводит к повышенному уносу биомассы с потоком осветленной культуральной жидкости со стадии сепарации. В этом случае, если в схеме не предусмотрен рецикл отработанной культуральной жидкости на ферментацию, необходимы дополнительные сепараторы для ее доочистки.
Флотация. Используется на первой стадии сгущения биомассы. Достоинства флотационного сгущения – простота аппаратурного оформления, незначительная продолжительность процесса, удовлетворительные показатели сгущения суспензии (степень сгущения 3–5). Разделение идет в односекционных или многосекционных флотаторах. Флотация может происходить в ферментере при образовании пены. Пена содержит повышенную концентрацию микроорганизмов. Содержание биомассы в пенном слое достигает 30–100 г/л (по сухим веществам).
Флотаторы используются в производстве дрожжей на гидролизатах древесины. В этом производстве конечная концентрация дрожжей в ферментационной среде невысока (не более 8–10 г/л). При невысокой концентрации биомассы на первой стадии выделения более рационально использовать флотационный метод, а не сепарацию. Как правило, отделение или концентрирование микроорганизмов не достигается только флотацией. Обычно после флотации предусмотрена сепарация.
Бактериальные микроорганизмы плохо флотируют, дрожжи – лучше. Для повышения флотируемости частиц и клеток в среду можно вводить дополнительные реагенты (ПАВ и др.).
В промышленности наиболее широко применяют способ напорной флотации (см. рис. 1.94). Постферментационную среду с микроорганизмами насыщают под давлением 0,25–0,65 МПа воздухом в сатураторе в течение нескольких минут. При снижении давления до атмосферного во флотационной камере начинают выделяться мельчайшие пузырьки воздуха, которые флотируют содержащиеся в воде частицы. Образовавшийся пенный слой сфлотированной биомассы механически удаляется из камеры в приемник суспензии.
Недостаток флотации – высокий вынос нефлотированных клеток микроорганизмов (0,5–1,5 г/л) и потери биомассы.
Электрофлотация, при которой пузырьки газа образуются в результате электролиза воды, также может быть использована для сгущения микробной биомассы. При обработке суспензии бактерий электрофлотацией степень сгущения составляет 3–5 при исходной концентрации 0,6–1,0% абсолютно сухих веществ, а энергозатраты – около 1–2 кВт·ч на 1 м3 исходной суспензии. Наибольшее влияние на процесс электрофлотации оказывает плотность тока.
Коагуляция и флокуляция применяются для улучшения седиментационных, фильтрационных и флотационных характеристик клеток микроорганизмов. Возможны реагентные (химические), безреагентные (физические) и комплексные (химические и физические) методы обработки.
При снижении или увеличении pH, под воздействием повышенной температуры или химических веществ (электролитов-коагулянтов, флокулянтов, ПАВ) свойства поверхности клеток модифицируются, они агрегируют, обра-
Переработка органических отходов |
345 |
зуют хлопья, флокулы. Медленное и равномерное перемешивание суспензии увеличивает объем, массу и способность к слипанию образующихся агрегатов. Такие агрегаты легче осаждаются и отделяются от воды, удельное сопротивление их при фильтрации ниже, флотируемость повышается. Дальше их либо отфильтровывают, либо осаждают или сепарируют, либо флотируют и отделяют другими методами.
При получении кормового и тем более пищевого продукта на основе микробной биомассы реагентная обработка не должна ингибировать рост микроорганизмов при введении в ферментер, добавляемые реагенты должны действовать эффективно в небольших количествах, быть нетоксичными или легко отмываться от клеток.
Седиментационные характеристики, сепарируемость микробной суспензии и способность к обезвоживанию можно существенно улучшить предварительным нагревом до 65–85 °С и термореагентной обработкой, при которых происходит денатурация белковых веществ и клеточных структур.
Коагуляция используется и в случаях, когда целевой продукт – внеклеточные метаболиты, а не клетки микроорганизмов. Тепловая коагуляция применяется, например, в технологии получения белка из клеточного сока растений. Недостаток тепловой коагуляции – при высокой температуре может наблюдаться лизис (плазмолиз) клеток, что приводит к потере биологически активных веществ.
Вакуум-выпарка используется на конечных стадиях концентрирования продукта. Режимы вакуум-выпарки выбирают такие, чтобы сгустить продукт, удалить воду, сохранив качество продукта, а иногда и жизнеспособность клеток (в производстве пекарских дрожжей, различных биопрепаратов на основе живых клеток микроорганизмов). Поэтому температура упаривания должна быть не выше 90 °С, а если требуется сохранить жизнеспособность микроорганизмов, то еще меньше и соответственно при использовании более глубокого вакуума. Содержание сухих веществ в упаренной после вакуум-выпарки суспензии составляет 20–30%.
На крупнотоннажных предприятиях распространены многокорпусные вы- куум-выпарные установки (ВВУ) с 2–4 ступенями с разным давлением и температурой. В этом случае более рационально используется тепло, необходимое для испарения влаги. Пар используется с давлением 0,4–0,6 МПа. По ходу ступеней интервал температур упариваемой жидкости меняется от 90–100 до 50–60 °С. Ниже 50 °С вакуум-выпарка экономически невыгодна.
Проблемой вакуум-выпарки является налипание органических веществ на стенки камеры, поэтому ВВУ приходится регулярно чистить (1 раз в месяц). Для этого используется промывка горячим раствором 4–6% NaOH или 4–6% раствором HNO3 в течение около 12 ч, что приводит к усилению коррозии поверхностей, дополнительным затратам, увеличивает объем жидких стоков.
Конечный этап концентрирования кормового продукта – сушка. Главное, что определяет условия сушки – это сохранение кормовых качеств продукта, его усвояемости и биологической ценности.
Сушка вальцеванием имеет низкую производительность, для нее характерно налипание продукта на барабаны, до 15% потерь продукта, однако использова-
346 |
Глава 3 |
ние ее целесообразно при получении продукта с твердой фазой (после твердофазной или глубинной гетерофазной ферментации).
Лиофильная сушка используется для сушки термолабильных продуктов и получения живых клеток (процесс длительный и плохо автоматизированный).
Распылительная сушилка имеет высокую производительность, большую скорость испарения. Частицы высушиваемого материала не перегреваются, так как время контакта материала с теплоносителем невелико, что приводит к меньшим потерям продукта по сравнению, например, с вальцовой сушилкой. Используются распылительные сушилки либо с форсункой, либо с быстро вращающимся диском. Недостаток форсунок – быстрое засорение и эрозия поверхности (ямки)
вместе, куда попадает струя продукта из-за неидеального распыления форсункой. Диск также эродируется, что приводит к неравномерному распылению.
Другие конструкции сушилок: струйного типа, с инертным псевдоожиженным носителем не получили широкого распространения в производстве кормовых продуктов.
После сушки продукт должен содержать не более 8–10% влаги. В этом случае он может длительно храниться без существенного ухудшения качества.
Товарная форма кормового продукта в виде порошка (после распылительной сушилки) не всегда удобна (порошок пылит, животные плохо его поедают), поэтому продукт может дополнительно гранулироваться.
Для получения гранул порошок увлажняется, паста поступает в гранулятор, проходит через фильтры, разрезается и затем заново подсушивается. Грануляция может также происходить при сушке в кипящем слое.
Если все клетки микроорганизмов необходимо инактивировать, то часто используются плазмолиз и пастеризация (перед сушкой). При плазмолизе клетки отмирают и лизируют. Температура плазмолиза 60–80 °С, продолжительность обработки – десятки минут. Если в технологической схеме предусмотрена вакуум-выпарка, то плазмолиз обычно не нужен, так как клетки отмирают непосредственно в ВВУ.
Пастеризацией инактивируют вегетативные клетки микроорганизмов при 70–90 °С. Для инактивирования спор среду сначала обрабатывают при температуре 85–90 °C. После чего ее выдерживают при температуре роста микроорганизмов до прорастания неинактивированных спор и вновь нагревают.
Фасовка и упаковка. При фасовке необходимо обеспечить минимальный контакт обслуживающего персонала с продуктом. В случае пылящего продукта используют вытяжку с циклонными сепараторами, с помощью которых пыль продукта собирается в бункеры и возвращается на упаковку. Сухой продукт фасуют в количестве до 25–30 кг в 2- или 3-слойные мешки из бумаги, полиэтилена, в банки, просто навалом. Жидкий продукт разливают в цистерны, бидоны, другие емкости.
Продукт с влажностью 70–80% и живыми микроорганизмами выпускается
ввиде пасты, прессованных брикетов в меньшей расфасовке, которые хранятся при низких температурах.
Иногда в кормовой продукт перед выпаркой, сушкой или упаковкой вносят дополнительные компоненты: питательные добавки, стабилизаторы, антиокис-

Переработка органических отходов |
347 |
лители, компоненты, предохраняющие слеживаемость препарата, различные твердые наполнители и носители и т. д. Это необходимо для стандартизации продукта, обеспечения оптимальной кормовой ценности и других потребительских характеристик, необходимых технологических свойств при его скармливании.
Примеры схем выделения:
глубинное культивирование на жидких средах а) содержание биомассы в конце ферментации невысокое (0,5–1%):
флотация сепарация вакуум-выпарка сушка б) содержание биомассы в конце ферментации высокое (1,5–2,5%):
сепарация I сепарация II вакуум-выпарка сушка
глубинное гетерофазное культивирование фильтрация пастеризация сушка
или вакуум-выпарка сушка
Флотацией, фильтрацией и сепарацией удаляется б;ольшая часть воды из концентрируемой суспензии микроорганизмов при существенно меньших энерго- и теплозатратах, чем при вакуум-выпарке и сушке. Иногда возможен возврат части образующихся фильтрата или фугата на стадию подготовки питательной среды или ферментации. В этом случае уменьшаются объемы потребляемой воды и жидких стоков.
На небольших установках для экономии капитальных затрат после сепарации продукт могут сразу подавать на распылительную сушку, либо вместо сепарации используется схема вакуум-выпарка – распылительная сушка.
Такие методы выделения, как ионный обмен, экстракция, электродиализ, осаждение, ультрафильтрация, хроматография, используемые при выделении и очистке биологически активных веществ, при получении кормового белка, применяются редко. Они высокозатратны и целесообразны лишь при получении продуктов пищевого назначения: белков, аминокислот, витаминов.
3.2.1.3. Технико-химический контроль и обеспечение качества продукции
Технико-химический контроль – это работа, связанная с выполнением физических, физико-химических, химических, микробиологических методов анализа по месту по всей технологической линии в цеховых и заводских условиях.
Содержание технико-химического контроля на производстве определяется нормативно-технической документацией и регламентом завода. Нормативнотехническая документация определяет показатели и состав любого вещества сырья, полупродуктов, продуктов. Различают:
ГОСТы (государственные стандарты) на вещества;
ОСТы (отраслевые стандарты); ТУ (технические условия) – временные документы, действующие до
разработки и утверждения ОСТа и ГОСТа.

348 |
Глава 3 |
Регламент завода утверждается уполномоченным ведомством и носит обязательный характер в ходе технологического процесса.
На рис. 3.8 приведена схема технико-химического контроля типичного биотехнологического производства при получении кормовой биомассы микроорганизмов.
Рис. 3.8. Технико-химический контроль при получении кормовой биомассы микроорганизмов: х – химический контроль; – микробиологический контроль
Необходимо проконтролировать:
На стадиях приготовления питательной среды и подготовки воздуха.
1)Состав, концентрация субстрата S. На предприятиях этот показатель не всегда контролируется.
2)Химический состав солей, наличие вредных примесей (если предполагается их наличие).
3)Примеси в воде (например, жесткость воды).
4)Качество воздуха – качество очистки от пыли и микроорганизмов, отсутствие загрязнений после компрессора.
Вферментере.
Химические показатели
5)Концентрация субстрата – достаточно ли его в ферментационной среде или следует прекращать процесс.
6)Концентрация фосфора, азота, питательных солей.
7)Концентрация продуктов метаболизма.
Микробиологические показатели
8)Концентрация микроорганизмов.
9)Состояние культуры – количество живых и мертвых клеток, количество почкующихся, спорулирующих клеток.
10) Концентрация сопутствующей микрофлоры и ее состав.
Контроль этих показателей важен для наблюдения за стерильностью процесса и получения качественного продукта.

Переработка органических отходов |
349 |
Физико-химические параметры
11)Температура, рН, давление, расход питательной среды и воздуха, рО2 и другие параметры ферментационной среды.
12)Поток отходящих газов из ферментера, их состав. Важны соотношение между О2 и СО2, концентрация летучих продуктов метаболизма, концен-
трация микроорганизмов (продуцентов и сопутствующих).
Стадии выделения.
13)Состав и концентрация культуральной жидкости, концентрация микроорганизмов.
14)Коэффициент сгущения – отношение концентрации биомассы или другого целевого продукта к их концентрации в исходной постферментационной жидкости.
Сушка.
15)Влажность целевого продукта после сушилки.
16)Содержание микроорганизмов и белка в газовоздушных выбросах.
Готовый продукт.
17)Все показатели, указанные в нормативно-технической документации:
–содержание основного вещества и примесей (особенно тяжелых металлов, металломагнитных примесей, зольность продукта и др.);
–содержание продуцента и загрязняющей микрофлоры, спор, токсинов;
–отсутствие живых клеток микроорганизмов, или наоборот – титр живых клеток.
Сточные воды.
БПК, ХПК, содержание аммонийного и нитратного азота, фосфора, наличие санитарно-показательной микрофлоры.
Для качества кормового продукта важно:
минимальное содержание посторонней микрофлоры;
максимальное содержание протеина и оптимальный состав незаменимых аминокислот;
минимальное содержание вредных примесей.
Из технологических мер для уменьшения содержания посторонней микрофлоры эффективны следующие:
поддержание асептических условий;
использование как можно более простых сред; наличие витаминов, аминокислот, других органических примесей увеличивает содержание сопутствующей микрофлоры; в субстрате не должно быть много мертвых клеток микроорганизмов, которые могут служить источниками факторов роста;
использование высоких скоростей разбавления (D, для проточной ферментации); культуральные штаммы выращивают при D 0,2–0,25 ч–1; удельная скорость роста дикой микрофлоры обычно ниже (0,1–0,15 ч–1), она не удерживается в ферментере при D > 0,2 ч–1;
обеспечение кислородом процесса, т. е. использование ферментеров с высокими массообменными характеристиками; если концентрация
1 В одноступенчатом реакторе в проточных условиях D = v/V, в хемостатном режиме D = μ.
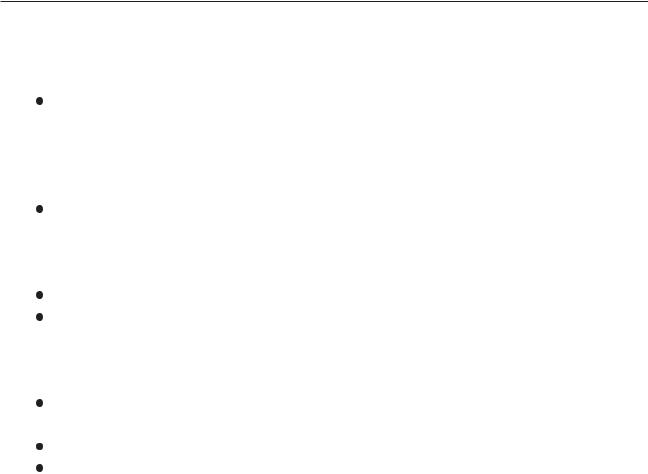
350 Глава 3
О2 в среде падает, то для достижения необходимой степени конверсии субстрата в биомассу необходимо уменьшать скорость разбавления, что приводит к увеличению численности посторонней микрофлоры;
при культивировании дрожжей ведение процесса в закисленной среде (pH 4,2–4,6); дрожжи при этом рН растут хорошо, а рост большинства бактерий угнетается.
Содержание протеина в биомассе дрожжей обычно составляет от 30 до 60%; в биомассе бактерий – до 80%. К падению содержания протеина приводят:
увеличение температуры ферментации, особенно в летнее время, когда из-за повышения температуры охлаждающей воды теплоотвод из ферментера затруднен (использование термофильных штаммов не устраняет проблему, так как они содержат меньше белка);
недостаточное обеспечение процесса биосинтеза кислородом;
переход на азотдефицитную среду; важно соотношение С : N и N : P (оптимальное соотношение N : P2O5 = 2–1,5 : 1).
Уменьшение содержания вредных примесей в продукте достигается: более тщательной предобработкой питательных субстратов;
использованием минеральных солей с низким содержанием примесей (но их стоимость более высокая);
промывкой биомассы на стадии выделения; снижением рецикла отработанной (бесклеточной) культуральной жид-
кости, что, однако, увеличивает количество сточных вод.
3.2.1.4. Принципы организации малоотходного производства
На приведенной на рис. 3.9 (стр. 348) технологической блок-схеме условного микробиологического производства показаны основные пути создания малоотходного производства (обозначены римскими цифрами) с получением продуктов А, Б, В, Г.
Источники отходов и загрязнений производства:
1.Охлаждающая вода и конденсат пара с теплообменников.
2.Промывные воды и растворы.
3.Побочные продукты культуральных жидкостей.
4.Газовоздушные выбросы (в основном из ферментеров, сушилок).
5.Стоки с ионообменных колонн, пермеаты или концентраты мембранного разделения, маточные растворы после кристаллизации и т. п.
6.Химикаты и растворители со стадий выделения.
7.Сточные воды.
8.Активный ил очистных сооружений.
9.Шламы с солеподготовительных отделений и отходы со стадии подго-
товки субстрата (лигнин в производстве на гидролизатах древесины).
Варианты утилизации и уменьшения отходов и стоков:
1. Создание замкнутого цикла водопотребления путем:
а) охлаждения оборотной воды с теплообменников в градирнях (или в холодильных агрегатах) и ее рецикла в производство (способ I);