
- •В. А. Валетов, Ю. П. Кузьмин, А. А. Орлова, С. Д. Третьяков
- •Технология приборостроения
- •Оглавление
- •Введение
- •Глава 1. Отработка конструкций деталей
- •на технологичность
- •1.1. Общие понятия и определения
- •1.2. Обеспечение технологичности
- •Глава 2. Точность изготовления деталей приборов
- •и методы ее обеспечения
- •2.1. Метод пробных ходов и промеров
- •2.2. Метод автоматического получения размеров на настроенных станках
- •2.3. Систематические погрешности обработки
- •2.3.1. Погрешности, возникающие вследствие неточности, износа
- •и деформации станков
- •2.3.2. Погрешности, связанные с неточностью и износом режущего инструмента
- •2.3.3. Погрешности, обусловленные упругими деформациями технологической системы под влиянием нагрева
- •2.3.4. Погрешности теоретической схемы обработки
- •2.3.5 . Погрешности, вызываемые упругими деформациями заготовки
- •2.4. Случайные погрешности обработки
- •2.4.1. Законы рассеяния (распределения) размеров
- •2.4.2. Составляющие общего рассеяния размеров деталей
- •2.5. Суммарные погрешности изготовления деталей
- •2.6 Практическое применение законов распределения размеров
- •для анализа точности обработки
- •2.7 Технологические размерные цепи
- •Глава 3. Оптимизация характеристик поверхностного слоя изделий приборостроения
- •3.1. Микрогеометрия и ее оптимизация
- •3.2.Технологические остаточные напряжения
- •3.3. Нанесение покрытий на поверхности изделий
- •3.3.1. Современные технологии нанесения покрытий
- •3.3.1.1. Газодинамический метод
- •3.3.1.2. Импульсно плазменная технология нанесения покрытий
- •3.3.1.3. Нанесение покрытий с помощью вращающихся валков
- •3.3.1.4. Технология нанесения порошковых полимерных покрытий
- •Глава 4. Принципы и особенности базирования
- •при использовании современного оборудования
- •4.1. Классификация баз по различным признакам
- •4.2. Разновидности технологических баз
- •4.3. Назначение технологических баз
- •4.4. Принцип совмещения (единства) баз
- •4.5. Принцип постоянства баз
- •Глава 5. Современные методы проектирования техпроцессов и оформления технологической документации
- •5.1. Методы проектирования
- •5.1.1. Современные САПР ТП
- •5.1.2. Система «TechCard»
- •5.1.3. Система «T-FLEX Технология
- •5.1.4. Система «САПР ТП ВЕРТИКАЛЬ»
- •5.1.5. САПР ТП TechnologiCS
- •5.1.6. Система «МАС ПТП»
- •5.1.7. Система "ТИС-Адрес"
- •5.2. Оформление технологической документации
- •Глава 6. Основы технологии сборки элементов точной механики
- •6.1. Селективная сборка или метод групповой взаимозаменяемости
- •6.2. Основной принцип адаптивно-селективной сборочной технологии
- •6.3. Определение и оптимизация границ групп допусков
- •6.4. Реализация АСС
- •Глава 7. Применение RP-технологий в производстве элементов, приборов и систем.
- •Предисловие
- •7.1 Основные технологии быстрого получения прототипов изделий
- •7.1.1 Стереолитография
- •7.1.2. Технологии с использованием тепловых процессов
- •7.1.2.1. Технология SLS
- •7.1.2.2 LOM - технология
- •7.1.2.3 FDM - технология
- •7.1.3 Трехмерная печать (3D Printers)
- •7.1.3.1. Genisys (Stratasys)
- •7.1.3.2. Z 402 (Z Corporation)
- •7.1.3.3. Actua 2100 (3D Systems)
- •7.1.4 Практическое применение RP - технологий
- •7.1.4.1. QuickCast. Литье по выжигаемым стереолитографическим моделям
- •7.1.4.2 Литье в эластичные силиконовые формы в вакууме
- •7.1.4.3. Промежуточная оснастка
- •7.1.4.4 RP - технологии с использованием листовых материалов
- •7.2 Проектирование и изготовление - единый процесс создания изделий
- •7.2.1 Предисловие
- •7.2.2. Проектирование изделия - изготовление изделия - быстрое усовершенствование изделия
- •7.2.3. Последовательность создания изделия
- •7.2.4. Критические факторы успеха и стратегии конкуренции
- •7.2.5 Ключевой фактор - время
- •7.2.6 Одновременное проектирование - конкурентоспособное проектирование
- •7.2.6.1 Классические ступени проектирования изделий
- •7.2.6.2. Требования к новым методам проектирования изделий
- •7.2.6.3. Принцип одновременности инженеринга
- •7.2.7. Модели
- •7.2.7.1. Классификация моделей
- •7.2.7.2. Влияние моделей на ускорение процесса проектирования изделий
- •7.2.7.3. Мотивация через модели
- •7.2.8. Создание моделей с помощью RP - технологий, как элемент одновременного инженеринга
- •7.2.8.1. RP - модели как гарантия обязательной базы данных
- •7.2.8.2. Определения: быстрое прототипирование, быстрое изготовление, быстрое производство
- •7.2.8.3. Взаимосвязь RP - моделей и фаз проектирования изделий
- •Глава 8.Основы технологии изготовления и сборки элементов радиоэлектронной аппаратуры
- •8.1. Электронные и микроэлектронные элементы
- •8.1.1 Типы полупроводниковых структур
- •Рис. 8.1. Схема классификации полупроводниковых структур
- •Немагнитные полупроводниковые структуры в свою очередь делятся на элементы, химические соединения, твердые растворы.
- •8.1.1.1. Кремний и его применение
- •8.1.2. Дискретные электрорадиоэлементы
- •8.1.2.1 Резисторы
- •8.1.2.2. Конденсаторы
- •8.1.2.3. Катушки индуктивности
- •8.1.2.4. Трансформаторы
- •8.1.2.5. Диоды
- •8.1.2.5.1. Светодиоды
- •8.1.2.6. Транзисторы
- •8.1.2.6.1. Пластиковые транзисторы
- •8.1.3. Технология изготовления тонкопленочных интегральных микросхем
- •8.1.3.1. Классификация и назначение интегральных микросхем
- •Рис. 8.33. Современная интегральная микросхема
- •8.1.3.1.1. Классификация интегральных микросхем
- •По степени интеграции. Названия микросхем в зависимости от степени интеграции (в скобках указано количество элементов для цифровых схем):
- •По технологии изготовления.
- •По виду обрабатываемого сигнала
- •Аналоговые (входные и выходные сигналы изменяются по закону непрерывной функции в диапазоне от положительного до отрицательного напряжения питания)
- •8.1.3.1.2 Назначение интегральных микросхем
- •8.1.3.2. Материалы для изготовления тонкопленочных и толстопленочных интегральных схем
- •8.1.3.2.1.Напыление частицами
- •8.1.3.2.2. Физико-химические способы получения пленочных покрытий
- •8.1.4. Технология изготовления полупроводниковых интегральных микросхем
- •8.1.4.1.1. Подготовка поверхности
- •8.1.4.1.2. Нанесение фотослоя
- •8.1.4.1.3. Совмещение и экспонирование
- •8.1.4.1.4. Проявление
- •8.1.4.1.5.Травление
- •8.1.5 Электрический монтаж кристаллов интегральных микросхем на коммутационных платах
- •8.1.5.1. Проволочный монтаж
- •8.1.5.2. Ленточный монтаж
- •8.1.5.3. Монтаж с помощью жестких объемных выводов
- •8.1.5.4. Микросварка
- •8.1.5.5. Изготовление системы объемных выводов
- •8.2.1. Основные характеристики печатных плат
- •8.2.1.1. Материалы, используемые для изготовления печатных плат
- •8.2.1.2. Точность печатных плат
- •8.2.1.3. Отверстия печатных плат
- •8.2.1.4. Толщина печатных плат
- •8.2.2. Типы печатных плат
- •8.2.2.1. Односторонние печатные платы
- •8.2.2.2. Двухсторонние печатные платы
- •8.2.2.3. Многослойные печатные платы
- •8.2.2.4. Гибкие печатные платы
- •8.2.2.5. Рельефные печатные платы
- •8.2.2.5.1. Технологии изготовления рельефных печатных плат
- •8.2.3. Технологические процессы изготовления печатных плат
- •8.2.3.1. Основные методы изготовления печатных плат
- •8.2.3.2. Аддитивная технология
- •8.2.3.3. Комбинированный позитивный метод
- •8.2.3.4. Тентинг-метод
- •8.2.3.5. Струйная печать как способ изготовления электронных плат
- •8.2.3.6. Технологии настоящего и будущего
- •8.2.4. Сборка и монтаж печатных плат
- •8.2.5. Методы контроля печатных плат
- •8.2.5.1. Система контроля качества печатных плат Aplite 3
- •Рис. 8.67. Интерфейс Системы Aplite 3
- •8.2.5.2. Электрический контроль печатных плат
- •8.3. Современное оборудование для изготовления радиоэлектронной аппаратуры
- •9.1. Основные понятия
- •9.2. Материалы для нанотехнологий
- •9.2.1. Фуллерены
- •9.2.2. Нанотрубки
- •9.2.3. Ультрадисперсные наноматериалы
- •9.3. Оборудование для нанотехнологий
- •9.4. Развитие нанотехнологий
- •9.4.1. Новейшие достижения
- •9.4.2. Перспективы развития
- •9.4.3. Проблемы и опасности
- •Литература
- •КАФЕДРА ТЕХНОЛОГИИ ПРИБОРОСТРОЕНИЯ
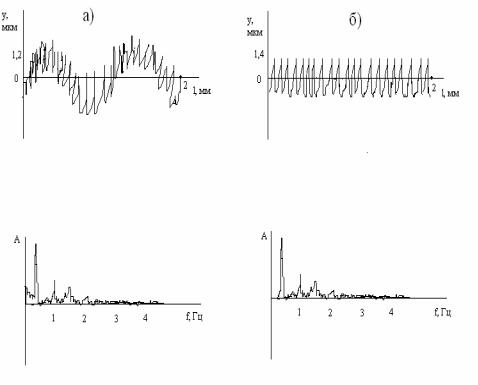
Рис. 3.5 Непараметрические критерии оценки профиля точеной поверхности с учетом (а) и без учета (б) волнистости
Этот профиль получен путем обратного Фурье - преобразования амплитудного спектра после удаления гармоник, содержащих информацию об отклонениях формы и волнистости.
3.2.Технологические остаточные напряжения
Не менее важной характеристикой поверхностного слоя деталей являются технологические остаточные напряжения [11]. Они возникают вследствие пластических деформаций кристаллических решеток материала заготовки в процессе ее механической или термической обработки. Играют роль и величина, и знак, и глубина залеганий, и характер распределения этих напряжений по глубине поверхностного слоя. Физическую сущность возникновения остаточных напряжений можно проиллюстрировать схемами, изображенными на рис.3.6.
56
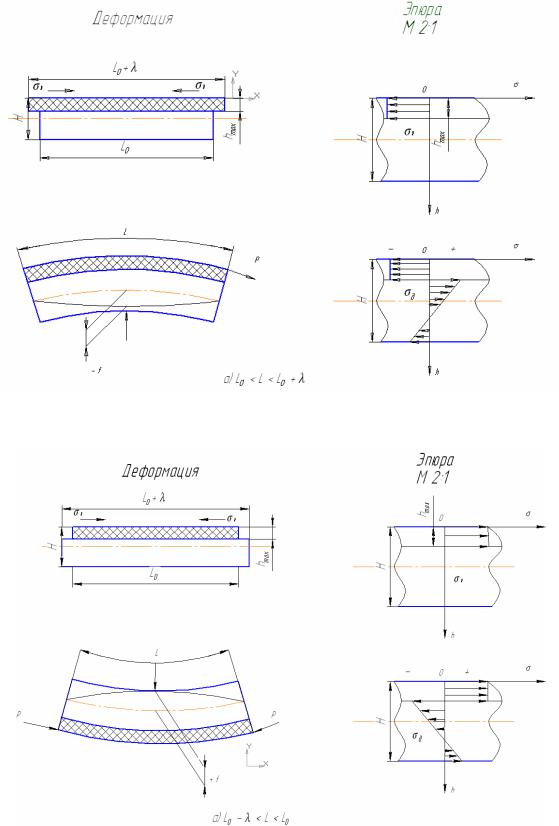
а)
б)
Рис. 3.6. Упрощенная схема деформации упругого призматического тела малой жесткости, при наличии остаточных напряжений в поверхностном слое: а) - сжатия; б) - растяжения
57
В процессе обработки заготовки ее поверхностный слой может, как уплотняться (рис.3.6, б), так и разуплотняться. (рис. 3.6, а). На схемах рис. 3.6. показаны гипертрофированные, чисто условные результаты этих воздействий, и, для наглядности, эти уплотненные и разуплотненные слои показаны условно отделенными от материала заготовок, не подвергнутого пластическим деформациям. Так как в реальных условиях никакого отделения деформированного слоя нет, то под воздействием деформаций в поверхностном слое произойдут деформации всего образца в соответствующих направлениях с перераспределением напряжений в поверхностном слое по всему поперечному сечению образца. Внесенные в поверхностный слой напряжения и результаты их перераспределения показаны справа от образцов. В общем случае возможны следующие результаты воздействия остаточных напряжений.
1.Если величина остаточных напряжений превысит предел прочности материала, а изделие обладает высокой жесткостью, то в поверхностном слое возникнут трещины вследствие его разрыва.
2.Если изделие представляет собой мало жесткую конструкцию, то произойдет его деформация, величина которой может намного превысить допуск на точность формы или взаимного расположения поверхностей.
3.Если остаточные напряжения ниже предела прочности материала, а изделие представляет собой жесткую конструкцию, то видимых изменений не произойдет. Однако, если эксплуатационные нагрузки совпадут со знаком остаточных напряжений, то изделие разрушится при нагрузках ниже запланированных, что чрезвычайно опасно. Из сказанного выше следует, что измерение и неразрушающий контроль технологических остаточных напряжений является важнейшей метрологической проблемой.
Исследования показали, что технологические остаточные напряжения технологически управляемы. Это означает, что и величина, и знак, и распределение остаточных напряжений по глубине поверхностного слоя зависят от видов и режимов обработки заготовок. Варьируя параметры обработки и последовательность методов обработки заготовок, можно в конечном итоге получить благоприятные величину и распределение остаточных напряжений в поверхностном слое. Чрезвычайно информативным критерием оценки остаточных напряжений является интеграл от эпюры их распределения по глубине. Этот критерий назван деформирующей способностью технологических остаточных напряжений и обозначен буквой "q". На рисунках 3.7 и 3.8 показаны эпюры распределения остаточных напряжений, полученных при различных видах и режимах обработки, что наглядно демонстрирует их технологическую управляемость.
58
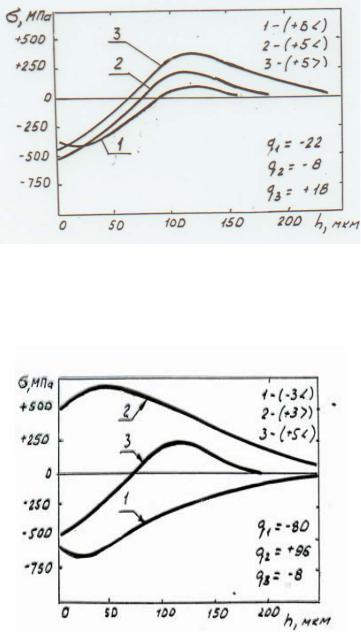
Рис. 3.7. Влияние режимов шлифования на σ(h) и q: 1 – ν = 10 м/с,
S = 0,3 м/с, P = 100 Н; 2 - ν = 20 м/с, S = 0,2 м/с, P = 150 Н; 3 - ν = 40 м/с, S = 0,1 м/с, P = 200 Н.
Рис. 3.8. Распределение σ (h) в стали 20Х13 после: 1 – фрезерование на станке FOREST; 2 – шлифования (ручного) на станке ЛШ-95; 3 – шлифования лентой на станке METABO
3.3. Нанесение покрытий на поверхности изделий
Одним из важнейших технологических методов управления характеристиками поверхностного слоя изделий является нанесение покрытий на функциональные поверхности изделий. Это целая отрасль технологической науки и практики, и здесь излагаются только основные принципы и краткое описание наиболее употребительных технологий нанесения покрытий [6]. Целью нанесения покрытий является улучшение свойств поверхности изделий в функциональном и (или) декоративном смысле. Основными видами функциональных покрытий являются: защита от коррозии, защита от износа, улучшение оптических свойств и трибологических характеристик. Во многих
59
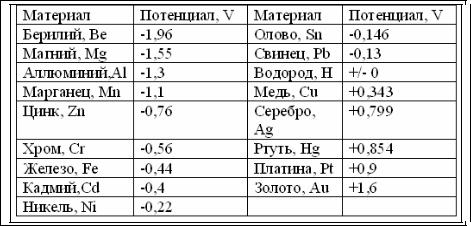
случаях покрытия совмещают функциональные и декоративные свойства. В качестве материалов покрытий используются как металлы, так и неметаллы. Последние в свою очередь, могут быть как органическими, так и неорганическими. Наиболее распространенными "механизмами" нанесения покрытий являются:
-процессы трения различных тел и сред друг о друга; -адгезионные и когезионные процессы; -химические и электрохимические процессы; -диффузионные процессы; -термические процессы.
Из всех функциональных свойств, улучшаемых с помощью покрытий, можно считать антикоррозионную стойкость. Повышение этой стойкости осуществляется и с помощью разнообразных материалов покрытия, и с помощью различных технологий их нанесения. Так как одними из эффективнейших покрытий являются металлические покрытия, то для защиты от коррозии целесообразно учитывать так называемый электрохимический ряд напряжений металлов (см. таблицу 3.1).
Таблица. 3.1.
Практический смысл этого ряда в том, что в качестве материала покрытия нужно выбирать металл, являющийся анодом по отношению к защищаемому материалу. В противном случае под материалом покрытия-катода могут происходить невидимые анодные разрушения материала изделия. Единственным исключением является использование цинка для покрытия сплавов железа. Но там играют решающую роль диффузионные процессы, в результате которых происходит уплотнение покрытия. Наиболее распространенными методами нанесения металлических покрытий являются:
-химические технологии (без внешнего подвода электрического тока); это чаще всего покрытия медью и благородными металлами; -гальванические технологии (с подачей внешнего электрического тока); это омеднение, никелирование, хромирование и т.д.;
60
-механические технологии, например, плакирование - совместное прокатывание между валками покрываемого материала и материала покрытия; -термические технологии, например, погружение в расплав, покрытие сваркой и т.п.; -термомеханические технологии, например, плазменное напыление, покрытие взрывом и т.п.
Самыми распространенными органическими покрытиями являются лакокрасочные. Неорганические покрытия наносятся часто путем плазменного распыления, эмалирования, анодирования и т.п. Сущность химических технологий заключается в так называемом катодном превращении металлических ионов в электролите в металлические атомы. Для поддержания процесса необходимо обеспечивать соответствующую концентрацию электролита. Покрытия получаются плотные, гладкие и очень равномерные по толщине. Чаще всего таким способ наносят медь, никель, кобальт и благородные металлы. Гальванические технологии (отложения металла при пропускании электрического тока через электролит) делят на гальваностегию и гальванопластику. Первое - отложение тонких слоев со временем операции от нескольких минут до нескольких часов. Вторая - отложение слоев толщиной более 1 мм. Время операции может длиться несколько недель. Интенсивность процесса зависит и от концентрации электролита, и от температуры, и от соответствия форм анода и катода (заготовки). Качество покрытий сопоставимо с химическими, но уступает последним по равномерности толщины слоя. В качестве электролитов часто применяют водные растворы, реже - расплавы солей и металлов. В качестве функциональных покрытия используют цинк, кадмий, олово, медь, хром, серебро, золото, а в качестве декоративных покрытий в основном благородные металлы, медь, никель, хром и их комбинации. Механические технологии относятся к категории древних, однако плакирование и так называемая голтовка (вибрационное воздействие на покрываемые изделия, между которыми насыпан порошок материала покрытия). К наиболее распространенным термическим технологиям относятся покрытия сваркой и окунания в расплав. К числу достоинств этих технологий относятся простота, однако равномерность толщины слоя покрытия оставляет желать лучшего. Кроме того, температура плавления покрытия не должна превышать температуру плавления материала, покрываемого изделия. При использовании термомеханических технологий покрываемую поверхность рекомендуется иметь шероховатой, что обеспечивает лучшее схватывание покрытия с поверхностью изделия. Лакокрасочные покрытия и технологии их нанесения настолько распространены и хорошо известны, что не требуют дополнительных пояснений. Неорганические (неметаллические) покрытия в основном уступают по качеству металлическим покрытиям, но намного дешевле, и поэтому применяются довольно широко. Это в основном тонкие слои из оксидов, карбидов, нитридов, боридов, силицидов и т.д.
61