
- •РОЗДІЛ4
- •4.2. Розділення пластин та підкладок
- •4.2.1. Скрайбування алмазним різцем
- ••Друга стадія розділення скрайбованих пластин та підкладок проводиться шляхом розламування по послаблених рисками
- •4.2.2. Скрайбування алмазним диском
- •Таблиця 4.1. Порівняльна характеристика методів
- •4.3. Монтаж кристалів та плат.
- •4.3.1. Клеєві з’єднання
- •4.3.2. Паяння склом.
- •4.3.3. Паяння металевим сплавом
- •М’які припої знижують інтервал температур роботи МСХ.
- ••4.4. Приєднання зовнішніх виводів.
- •Рис 4.2. Схема монтажу безкорпусних транзисторів з кульковими виводами:
- ••4.4.1. Паяння мікропаяльником
- •4.4.2. Термокомпресійне зварювання
- •Термокомпресійне зварювання має багато різновидів, які можна класифікувати за деякими ознаками:
- ••За способом з’єднання класифікуються двома способами: встик (з утворенням кульки) або внаклад.
- ••При зварюванні інструментом «пташиний клюв» один і той же пристрій подає дріт, приєднує
- •• 4.4.3 Ультразвукове зварювання
- •4.4.6. Зварювання розщепленим електродом
- ••4.5. Герметизація мікросхем
- ••При безкорпусній герметизації кристала або плати виготовляється необхідна система зовнішніх видів, до яких
- ••Мас-спектрометричний метод полягає в тому, що способом мас- спекрометрії виявляється гелій, попередньо введений

РОЗДІЛ4
СКЛАДАННЯ МІКРОСХЕМ
4.1. Методи та етапи складання
Складання та захист інтегральних мікросхем – це частина загального технологічного процесу виготовлення ІМС, в результаті здійснення якого отримують готову конструкцію ІМС.
Процес складання ІМС умовно можна поділити на наступні етапи:
-розділення пластин та підкладок зі сформованими активними та пасивними елементами на кристали (НІМС) та плати (ГІМС);
-монтаж на плату кристалів ІМС та навісних елементів (при складанні ГІМС);
-монтаж кристалів або плат на основу корпусу, приєднання виводів;
-герметизація ІМС
Для монтажу кристалів використовують два основних методи:
-прямого монтаж;
-перевернутого кристалу.
Приєднання виводів здійснюється різними способами, які можна також об’єднати в 2 методи:
-гнучкий (дротяний) монтаж;
-жорсткий (бездротяний) монтаж.
1

4.2. Розділення пластин та підкладок
Основними методами розділення пластин та підкладок є наступні:
-скрайбування алмазним різцем з послідуючим розламуванням;
-розділення за допомогою алмазного диску;
-розділення за допомогою лазерного променя (лазерне скрайбування).
Для вказаних методів загальною особливістю цих методів є наступне:
-необхідність точно орієнтувати лінію розрізування між площинками, які займають окремі структури;
-забезпечення цілісності сформованих елементів після розрізання за рахунок зведення до мінімуму механічних напружень за лінією розрізання;
-збереження орієнтації розділених кристалів та забезпечення відтворюємості розмірів та форми;
-одержання мінімальної ширини лінії розділення.
2

4.2.1. Скрайбування алмазним різцем
Цей процес розділення виконують у дві стадії.
На першій стадії спочатку за допомогою алмазного різця наносяться подряпини. Для цього пластину розміщують на вакуумний притиск, орієнтують її в горизонтальній площині. Далі переміщенням алмазного різця під відповідним тиском наносять риски на поверхню пластини у двох взаємно-перпендикулярних напрямках. Вздовж риски у деякій товщині матеріалу з’являються механічні напруження та виникають деформації та мікротріщини. Вони і послаблюють міцність пластини. Риски мають ширину 20-40 мкм та глибину 10-15 мкм. Так, наприклад, при скрайбуванні кремнієвих пластин товщиною 200 мкм різець треба притискати з силою 0,4-0,6 Н, а при товщині 300-400 мкм – 0,8-1,2 Н, для сіталових підкладок F =1,5-2,5 Н.
Слід відмітити, що в установках для скрайбування, як правило, переміщують не різець, а столик з пластиною або підкладкою. Швидкість скрайбування складає – 20÷75 мм/с.
В якості ріжучого інструменту використовують різці у вигляді тригранної або чотиригранної піраміди із натурального або синтетичного алмазу. Ріжучим елементом таких різців є ребра піраміди, які використовують послідовно.
3
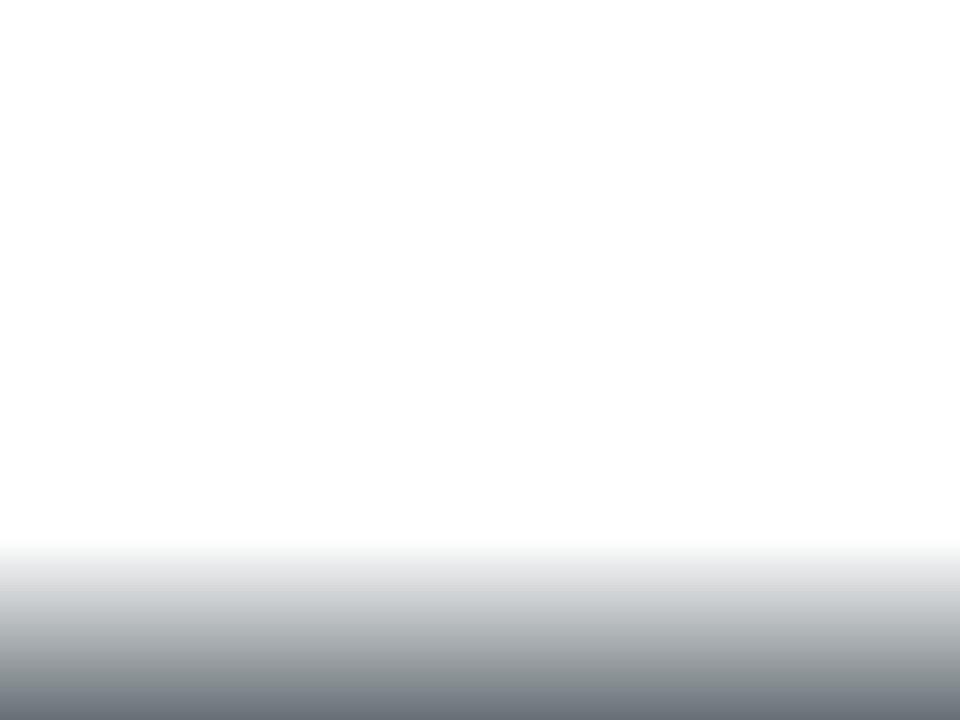
•Друга стадія розділення скрайбованих пластин та підкладок проводиться шляхом розламування по послаблених рисками місцях вручну, за допомогою
резинових валиків або машинним способом за допомогою напівсфери.
•Розламування валиком здійснюється шляхом переміщення валика по пластині, яка знаходиться на опорі. Для збереження взаємного розміщення кристалів (плат) під та над пластиною та валиком наносять еластичну прозору тонку плівку (з поліетилену або фторопласту). Пластини та підкладки спочатку розділяють на полоси, потім при розвороті їх на 90° - на окремі кристали.
•При другому способі пластина розміщується на напівсфері. Потім вона обтискається по сферичній поверхні за допомогою еластичної мембрани, яка має властивість добре розтягуватись. Тиск на мембрану здійснюється гідравлічним методом або стисненим повітрям. При цьому методі кристали або пластини розділяються зразу за двома напрямками. Зменшується кількість зломів, подряпин, зламаних кристалів, брак складає 2%.
•Обидва наведені вище методи мають такі недоліки:
•- великий розклад геометричних розмірів кристалів;
•- залежність якості розділення від співвідношення розмірів кристалів та товщини пластини;
•- поява браку за рахунок непередбачених тріщин, відколів.
4

4.2.2. Скрайбування алмазним диском
В якості інструмента для розділення пластин та підкладок цим методом використовують диск з зовнішньою ріжучою кромкою у вигляді леза з алмазним шаром. Розрізання проводиться у напівавтоматичному режимі при переміщенні пластин під диском, який обертається. Цей метод дозволяє розділяти пластини великого діаметру, великої товщини та високої твердості (мінімальний розмір кристалу 3 х3мм). Брак складає 0,5%.
4.2.3. Розділення лазерним променем
Розділення кристалів за допомогою лазерного променя відноситься до безконтактних способів. При цьому методі відсутня механічна дія на кристал.
Розділення пластин здійснюється двома способами:
-попереднє нанесення рисок (лазерне скарбування) з послідуючим розламуванням;
-наскрізне проходження лазерного променя по всій товщині пластин (лазерне розрізання). У першому випадку йде випаровування матеріалу, а в другому плавлення.
Застосування лазерного скрайбування дозволяє істотно підвищити продуктивність процесу порівняно з скрайбуванням алмазним різцем.
При цьому метод є можливість розділяти пластини, на яких нанесені шари оксидів, нітридів, металів, а велика глибина риски дозволяє підвищити вихід придатних виробів (99,5%). Кристал має практично вертикальну оплавлену бокову поверхню без гострих виступів.
Недоліком цього методу є забруднення пластин продуктами випаровування і розплаву, температурний вплив на напівпровідникові мікросхеми, а також висока вартість та складність управління обладнанням.
5
Для розділення пластин можливі також інші методи, наприклад, хімічне наскрізне травлення попередньо маскованої пластини.

Таблиця 4.1. Порівняльна характеристика методів
скрайбування та розділення пластин та підкладок
Параметр |
|
Метод розділення |
Лазерне |
|
|
|
Скрайбування |
Розрізання |
|
|
|
алмазним |
алмазним |
скрайбування |
|
|
різцем |
диском |
|
Ширина лінії, мкм |
20-40 |
35-40 |
20-25 |
|
Глибина різа, мкм |
10-15 |
10-400 |
50-170 |
|
Напрямок |
руху |
Односторонній |
Можливий |
Можливий |
інструмент |
|
|
двосторонній |
двосторонній |
Тип інструмента |
Алмазний |
Алмазний |
Лазерний |
|
|
|
різець |
диск |
промінь |
max |
вихід |
98% |
99,5% |
99,5% |
годинних ел., % |
|
|
|
|
Обробляємий |
|
Si, сітал |
Любий |
Любий |
матеріал |
|
|
|
|
Кваліфікація |
|
Висока |
Середня |
Люба |
персоналу |
|
|
|
|
6

4.3. Монтаж кристалів та плат.
•Після розділення пластини на кристали проводять їх монтаж
та закріплення всередині корпусу шляхом паяння чи приклеювання.
Метод закріплення залежить від вибору матеріалу яким це здійснюється – клей, скло, компаунд, припой та ін.
Матеріал приєднання повинен забезпечувати ефективний відвод тепла, мати приблизно однаковий температурний коефіцієнт розширення (ТКР) кристала та корпуса в робочому діапазоні температур, стійкість до динамічних дій в умовах вібрацій та ударів. У випадку напівпровідникових ІМС, як правило, матеріал повинен проводити електричний струм.
Процес приєднання можна умовно розділити на три стадії:
-підготовка місця з’єднання та нанесення з’єднуючого матеріалу;
-орієнтовна установка кристалу або плати;
-власне саме приєднання, яке в загальному випадку виконується під тиском та з нагрівом.
•Як матеріали використовується клей, скло і металевий припій.
Розглянемо основні типи з’єднань.
7

4.3.1. Клеєві з’єднання
Клеєві з’єднання використовуються для мікросхем пониженої потужності. Такі з’єднання відрізняються простотою процесу, достатньою механічною міцністю та надійністю низькою температурою затвердіння..
При цьому поверхні, які склеюються, повинні бути знежирені та висушені. Приєднання проводиться шляхом насадки на краплю рідкого клею абр підсушений шар клею.
Широке застосування одержали клеї марок ВК-2, ВК-4, ВК-8, ВК-9 та компаунди на основі епоксидної смоли ЕД-6.
Використання епоксидних компаундів обумовлено тим, що епоксидні смоли мають мінімальну цифру при затвердінні, чудову адгезію до різних матеріалів, не виділяють побочних продуктів, хімічно стабільні. Діапазони робочих температур (-60÷+150º С, короткочасно до 450ºС).
Товщина шару клею складає 0,05 - 0,1мм. При склеюванні більшість клеїв допускають варіювання температури та часу, причому при підвищенні температури час затвердіння клею швидко зменшується. Режим холодного затвердіння здійснюється при кімнатній температурі, але потребує довгої витримки (48 годин), тому приклеювання, як правило, здійснюють з підігрівом (60-120ºС). Клеєві з’єднання є ефективними у тому випадку, коли виготовляються ремонтопридатні гібридні ІМС, можливий демонтаж кристалів з метою їх заміни.
• |
8 |

4.3.2. Паяння склом.
Пайку склом в основному використовують для закріплення керамічних, полікорових, сіталових підкладок. Це пов’язано з тим, що найкраща адгезія скла та міцність представляють собою суміш оксидів (сітал, полікор, кераміка 22ХС) або металами, які мають на поверхні «прочный» шар окису.
•Технологія пайки склом зводиться до нанесення суспензії (пасти) скляного порошку в деіонізованій воді на очищену поверхню, подальшим стисненням деталей, які з’єднуються, послідуючим просушуванням та оплавленням в печі.
•Пайка склом дозволяє досягти доброго узгодження з’єднаних матеріалів по ТКР, так як змінюючи добавки, можна змінити склад скла.
9

4.3.3. Паяння металевим сплавом
Паяння металевим сплавом на металевий корпус забезпечує високу електропровідність з’єднання, механічну міцність, добре узгодження по ТКР.
Дана операція використовується на спеціальних автоматичних установках. Пання в мікроелектроніці застосовують нечасто, оскільки цей процес пов’язаний з нагріванням з’єднувальних матеріалів, що негативно впливає на параметри МСХ.
•Існують низько- та високотемпературні припої.
•Для поліпшення змочування з’єднувальних матеріалів припоєм використовується флюси на основі каніфолі (марок ФКСп, ФПЕт, ФКТС) і на основі хлористого цинку. Але флюси дуже забруднюють поверхню мікросхеми, тому їх використовують рідко, а спаювання проводять у відновлювальному середовищі (водень) чи інертному (аргон, гелій, криптон) середовищі.
•В якості приєднувального шару можуть бути використані такі припої:
•Au(80%) + Sn(20%) tпл=280ºС
•Pb(92%) + Sn(5,5%) + Ag(2,5%) tпл=300ºС
•Припой вводиться у місце з’єднання у вигляді фольгованих дисків або наноситься у вигляді пасти трафаретним способом. При використанні цих припоїв кристали на установочній площині повинні мати шар металу (металізація Ag, Au або нікель з підшаром Cr). Відповідно, площина під кристал
на підкладці повинна мати покриття із Ni або золота. Це робиться для високого
10
змочування поверхні припою.