
- •Инструментальные стали
- •К инструментальным относят стали, применяемые для обработки материалов резанием и давлением.
- •Классификация инструментальных сталей
- •По структуре в равновесном состоянии стали подразделяют на следующие группы:
- •Стали для режущего инструмента
- •Легированные стали.
- •Быстрорежущие стали
- •V образует карбид VC с твердостью НV 2700…2800. Максимальный эффект от введения в
- •Обработка быстрорежущих сталей включает горячую деформацию для устранения карбидной неоднородности сфероидизирующий изотермически отжиг
- •Закалка инструмента из быстрорежущей стали обычно проводится с аустенизацией в соляных ваннах (во
- •Диаграмма изотермического распада аустенита быстрорежущих сталей характеризуется двумя С-кривыми, соответствующими перлитному и бейнитному
- •Отпуск быстрорежущих сталей проводится для снижения объема остаточного аустенита до 1% и на
- •Влияние температуры отпуска на твердость стали Р6М5. Снижение твердости до 4000С связано с
- •В результате выделения карбидов из аустенита Мн повышается до
- •Штамповые стали
- •Стали с умеренным сопротивлением пластической деформации –
- •Стали с высоким сопротивлением пластической деформации.
- •Штамповые стали для горячего деформирования.
- •Термообработка этих сталей включает закалку на мартенсит и высокий отпуск.
- •Стали для измерительных инструментов
- •Низкотемпературный отпуск практически не меняет количества остаточного аустенита. Для уменьшения его содержания применяют
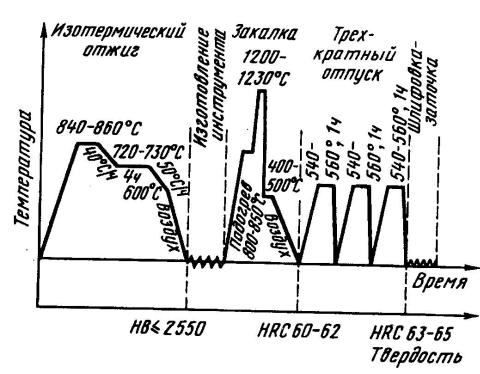
Обработка быстрорежущих сталей включает горячую деформацию для устранения карбидной неоднородности сфероидизирующий изотермически отжиг (смягчающая термообработка на НВ 250…300) перед изготовлением инструмента и окончательную термическую обработку: закалку с отпуском готового инструмента на HRC 63…68
Режим смягчающего отжига: аустенизация при 840…8600С, охлаждение со скоростью 30…400С/час до 720…7500С, выдержка не менее 4 ч, охлаждение со скоростью 40…500С/ч до 6000С и далее на воздухе.
11
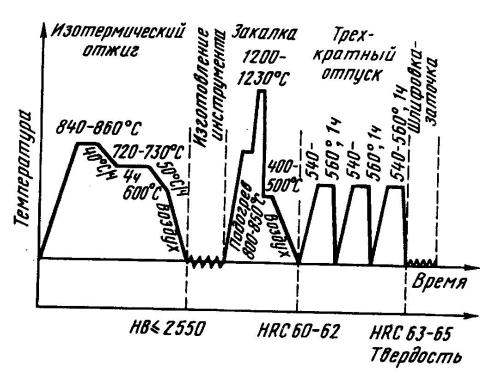
Закалка инструмента из быстрорежущей стали обычно проводится с аустенизацией в соляных ваннах (во избежание обезуглероживания). Нагрев под закалку вследствие низкой теплопроводности сталей проводят с предварительным подогревом при температуре 800…8500С (для выравнивания температуры).
Для сложного крупногабаритного инструмента сечением более 30 мм делают дополнительный подогрев при 400…5000С, иногда еще и при 1000…11000С.
Температура аустенизации выбирается высокой, чтобы перевести W в твердый раствор: Т=1200…12500С. После аустенизации сталь имеет структуру аустенит+Ме6С+VC.
Выдержка при температуре аустенизации не должна быть больше,
чем это необходимо для растворения карбидов, т.к. возможен рост |
|
зерен. |
12 |
|
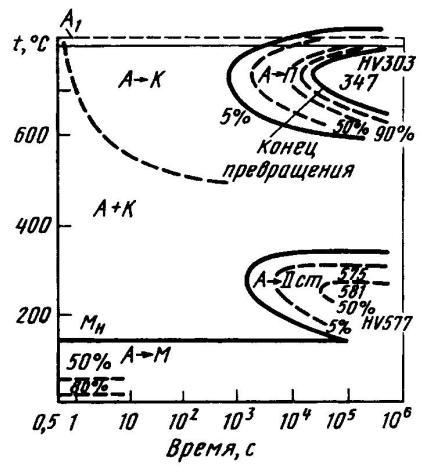
Диаграмма изотермического распада аустенита быстрорежущих сталей характеризуется двумя С-кривыми, соответствующими перлитному и бейнитному превращениям. Аустенит устойчив в области перлитного превращения, поэтому закалку можно проводить на воздухе. Но при температурах 800…5500С даже при небольших выдержках происходит выделение специальных карбидов типа Ме6С (пунктирная
линия), что приводит к обеднению твердого раствора легирующими
элементами и к снижению красностойкости. Поэтому охлаждение при закалке проводят либо в масле, либо в горячей среде с выдержкой при 400…5000С. Такая выдержка не вызывает выделения карбидов, распада аустенита и не влияет на температуру мартенситного превращения. Ступенчатая закалка позволяет выровнять
температуру по сечению инструмента и избежать коробления.
13
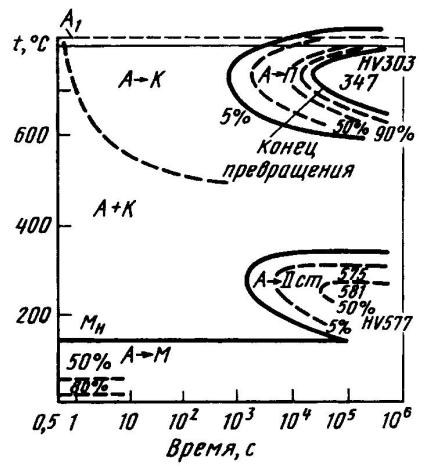
Температура мартенситного превращения составляет (Мн=150…2000С). При охлаждении
до комнатной температуры остается нераспавшимся 20…25% аустенита.
После закалки фазовый состав быстрорежущих сталей: М + (20… 30%) Аост. + (7…15%) нерастворившиеся карбиды.
14
Отпуск быстрорежущих сталей проводится для снижения объема остаточного аустенита до 1% и на вторичное твердение за счет выделения VC.
В зависимости от температуры отпуска происходит выделение следующих карбидов:
1)при Т=300…4500С выделяется легированный цементит Ме3С; 2)при Т=400…4250С – CrXCY;
3)при Т=525…6500С – VC+(W, Mo)2C. При этом пока не выделится VC, (W, Mo)2C не выделяется;
4)при Т=650…7500С – Cr7C3 (отсюда при 6200С происходит
потеря красностойкости);
5)при Т=750…8000С – Cr23C6.
15
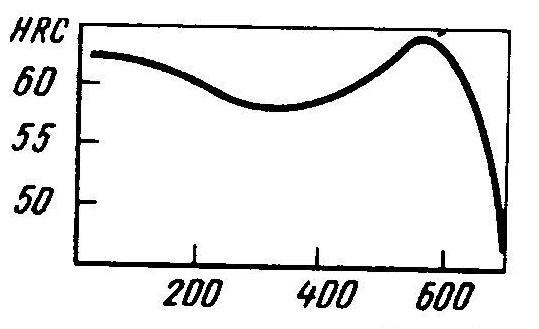
Влияние температуры отпуска на твердость стали Р6М5. Снижение твердости до 4000С связано с образованием карбидов цементитного типа. Максимальная твердость достигается при температуре 540…5600С, что связано с появлением карбидов МеС. и Ме2С. Резкое уменьшение твердости при более высоких
температурах связано с выделением карбидов Ме6С и Ме23С6.
16
В результате выделения карбидов из аустенита Мн повышается до
3000С и при последующей закалке происходит частичное мартенситное превращение. Полное превращение остаточного аустенита в мартенсит возможно после нескольких циклов нагрева и охлаждения.
Выделение мелкодисперсных карбидов (W, Mo)2C из остаточного
аустенита вносит значительный вклад в дисперсионное твердение. Многократный (2-4 ступени) отпуск с промежуточными закалками
обеспечивает также отпуск мартенсита, образовавшегося при предшествующей закалке.
После многократного отпуска структура представлена специальными карбидами – 20…25%, остаточным аустенитом – 1… 2% и отпущенным мартенситом (остальное, в т.ч. 3…4% неотпущенного).
17
Штамповые стали
Применяются для изготовления инструмента, предназначенного
для изменения формы материала деформированием. Штамповые стали делят на стали для холодного
деформирования и стали для горячего деформирования. Штамповые стали легируют Cr, W, Mo, V, Si, иногда Ni, Mn, Co, Ti. Увеличение содержания легирующих элементов благоприятно
влияет на прокаливаемость и на склонность к дисперсионному твердению.
Стали для холодного деформирования.
Х12, Х12ВМ, 8Х4В2С2МФ, 7ХГНМ.
Эти стали должны иметь высокую твердость, износостойкость и повышенную вязкость. При больших скоростях деформирования штампы разогреваются до 3000С и необходима теплостойкость.
По свойствам штамповые легированные стали для холодного деформирования делят на:
стали с умеренным сопротивлением пластической деформации; стали с высоким сопротивлением пластической деформации.
18
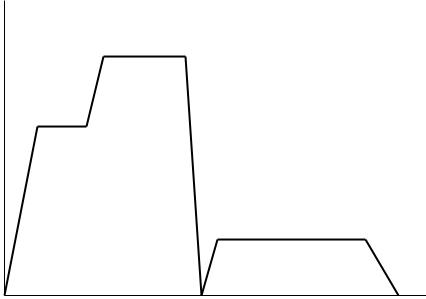
Стали с умеренным сопротивлением пластической деформации –
термообрабатывают на первичную твердость (Х12, Х6ВФ4). Термическая обработка этих сталей заключается в закалке от высоких температур (950…10500С) и низком отпуске (150…2500С – 1,5…2,5 ч). Вследствие пониженной теплопроводности нагрев под закалку осуществляют с предварительным подогревом при 650… 7000С. После закалки структура представляет собой мартенсит, карбиды цементитного типа или типа Ме23С6.
950…10500С
650…7000С
150…2500С
19
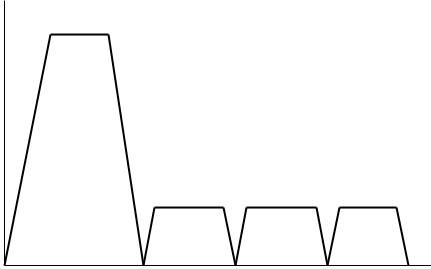
Стали с высоким сопротивлением пластической деформации.
6Х4М2ФС, 8Х4В2С2МФ.
Штамповые стали, легированные Mo, W и V упрочняются за счет дисперсионного (вторичного) твердения. Термическая обработка таких сталей состоит из закалки с более высоких температур для повышения легированности аустенита (1110…11300С) и многократном (3…4 стадии продолжительностью по 1…1,5 ч) высоком отпуске при 490…5300С. В результате отпуска происходит выделение мелкодисперсных карбидов и образование мартенсита из остаточного аустенита.
1110…11300С |
490… |
5300С |
20