
- •Технология термической обработки
- •Стальной листовой прокат тонколистовой - с толщиной 0,2…3,9 мм и Толстолистовой - толщиной
- •Технология термической обработки тонколистового проката регулирует конечную структуру и свойства стали с целью
- •Технологию термической обработки тонкой ленты для глубокой и особо сложной вытяжки:
- •Рекристаллизационный отжиг выполняют в колпаковых печах с защитной атмосферой. Нагрев рулонов ведется со
- •Технология термической обработки толстолистовой стали включает операции отжига-нормализации с высоким отпуском или без
- •Наиболее перспективно применение термической обработки с использованием тепла горячей прокатки.
- •Технология термической обработки проволоки и ленты. Патентирование
- •Проволока должна иметь следующие свойства:
- •ПТО катанки. Микроструктура катанки должна представлять собой сорбитообразный пластинчатый перлит. Сорбитизированную структуру получают
- •Окончательная термообработка проволоки включает
- •Патентирование предусматривает обработку проволоки в нитку и проводится в непрерывно действующих установках.
- •На практике обычно температура изотермической выдержки поддерживается в интервале 420-540°С.
- •ОТО в виде закалки и отпуска применяется для высоколегированных сталей. Это чаще всего
- •Технология термической обработки деталей подшипников
- •В зависимости от условий работы деталей подшипников предусмотрено 3 варианта термической обработки:
- •Химический состав подшипниковых сталей
- •Маршрутная технология получения деталей подшипников
- •Технология ПТО подшипниковых сталей заключается в сфероидизирующем отжиге с образованием структуры зернистого перлита.
- •Параметры сфероидизирующего отжига:
- •Технология ОТО деталей подшипников включает закалку с низким отпуском, данная термическая обработка формирует
- •Закалочная среда выбирается в зависимости от марки стали, массы и формы деталей. Для
- •Заключительной операцией в ОТО является низкий отпуск, который формирует свойства готовых деталей подшипников.
- •Заключительной операцией в ОТО является низкий отпуск, который формирует свойства готовых деталей подшипников.
- •Контроль качества ТО деталей подшипников включает:

Окончательная термообработка проволоки включает
рекристаллизационный отжиг, патентирование или закалку и отпуск. В игольной проволоке из стали У7А - зернистый перлит образуется при ускоренном охлаждении до 500-550 °С с температуры конца горячей деформации.
Рекристаллизационный отжиг это основной вид термообработки для проволоки из высокоуглеродистых сталей. Мотки проволоки отжигают в колпаковых или роликовых печах.
Параметры отжига определяются маркой стали и находятся по температуре в пределах 670-700°С, с выдержкой 3-6 ч для колпаковых печей (отжиг в мотках) или в проходных, где выдержка определяется диаметром проволоки.
11
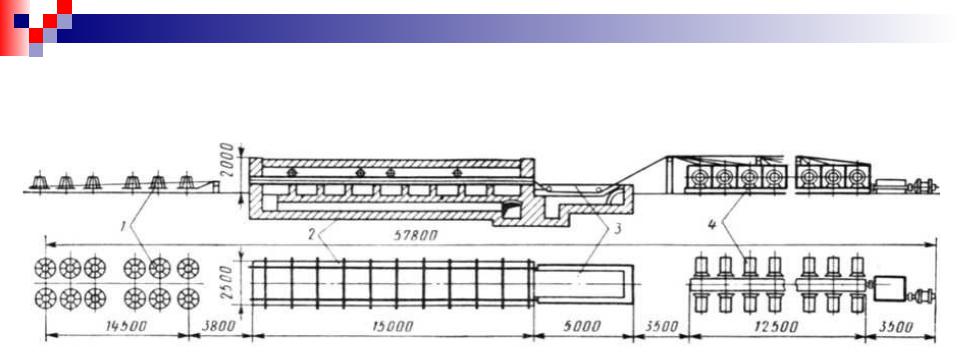
Патентирование предусматривает обработку проволоки в нитку и проводится в непрерывно действующих установках.
Схема установки для непрерывного патентирования проволоки
Нагрев ведется в протяжных трубчатых печах до температуры выше точки Ас3 на 80-100 °С, что обеспечивает однородность аустенита и
оптимальный для волочения размер зерна 2-3 балл.
Для переохлаждения аустенита и изотермической выдержки используют электродные соляные ванны (65-75% NaNO3 и 35-25%
KNO3), которые обеспечивают превращение переохлажденного
аустенита в тонкопластинчатый перлит (сорбит) с толщиной пластин 10-40 нм и феррита с размером зерна 60-200 нм. Такая структура позволяет проводить волочение с суммарными обжатиями12 90-99%.

На практике обычно температура изотермической выдержки поддерживается в интервале 420-540°С.
Минимально необходимое время пребывания проволоки в ванне изотермической выдержки для углеродистых сталей составляет около 15 с. В промышленных условиях эта выдержка определяется экспериментально в зависимости от марки стали и диаметра проволоки.
Для легированных сталей наиболее эффективно применение ступенчатого патентирования: 950 °С, выдержка 10 мин, охлаждение в ванне до 320 °С, перенос в ванну с температурой около 600 °С, выдержка 5-7 с.
13

ОТО в виде закалки и отпуска применяется для высоколегированных сталей. Это чаще всего стали аустенитного или ферритного класса.
Закалка выполняется с нагревом до температур 1000-1050°С с охлаждением в воде. С целью уменьшения окисления и обезуглероживания применяются высокотемпературные соляные ванны (расплав солей BaCl2, KCl, NaCl). При выборе режима
термообработки необходимо учитывать химический состав стали и диаметр проволоки (катанки).
После закалки стали имеют структуру стабильного аустенита или феррита, которые имеют высокую пластичность. Поэтому волочение проволоки из этих сталей проводится после закалки.
Отпуск проволоки ведется при температурах 450-620 °С после волочения. Такая технологическая схема является разновидностью термомеханической обработки и позволяет получить на проволоке высокие уровни прочности при сохранении значительных величин вязкости и пластичности.
14

Технология термической обработки деталей подшипников
В машиностроении используется около 11000 типоразмеров подшипников качения с наружным диаметром 2…3000 мм и массой от долей грамма до 6 т. Подшипники работают в интервале температур от −150 до +700 °С со скоростью до 300000 об/мин.
Условия работы подшипников и материалы для их изготовления.
Детали подшипников испытывают многократно повторяющиеся контактные, ударные нагрузки, износ, воздействие коррозионной среды и высоких температур.
Основные виды дефектов, возникающих при работе - это контактно-усталостное выкрашивание, смятие, износ, заклинивание, трещины, коррозия. Поэтому материалы для изготовления подшипников должны иметь: высокое сопротивление пластической деформации, стойкость против усталостного разрушения, износостойкость, достаточную вязкость, стабильность размеров.
15

В зависимости от условий работы деталей подшипников предусмотрено 3 варианта термической обработки:
1. Детали подшипников работают без высоких ударных нагрузок. Они изготавливаются из заэвтектоидных легированных сталей типа ШХ15. Термическое упрочнение обеспечивает высокую твердость по всему сечению деталей;
2. Детали подшипников, испытывающие при эксплуатации значительные ударные нагрузки и высокие контактные напряжения (подшипники прокатных станов, буровых установок). Данные изделия изготавливаются из низкоуглеродистых легированных сталей (18ХГТ, 20Х2Н4А) с повышением твердости, износостойкости поверхности путем цементации и последующей термической обработки;
3. Детали крупногабаритных подшипников, работающие в условиях ударного нагружения (подшипники букс железнодорожных вагонов). Данные изделия изготавливаются из стали ШХ4, эта сталь относится к заэвтектоидным хромистым сталям с регламентированной прокаливаемостью. Упрочняющая термическая обработка стали ШХ4 состоит из объемно-поверхностной закалки с отпуском.
16
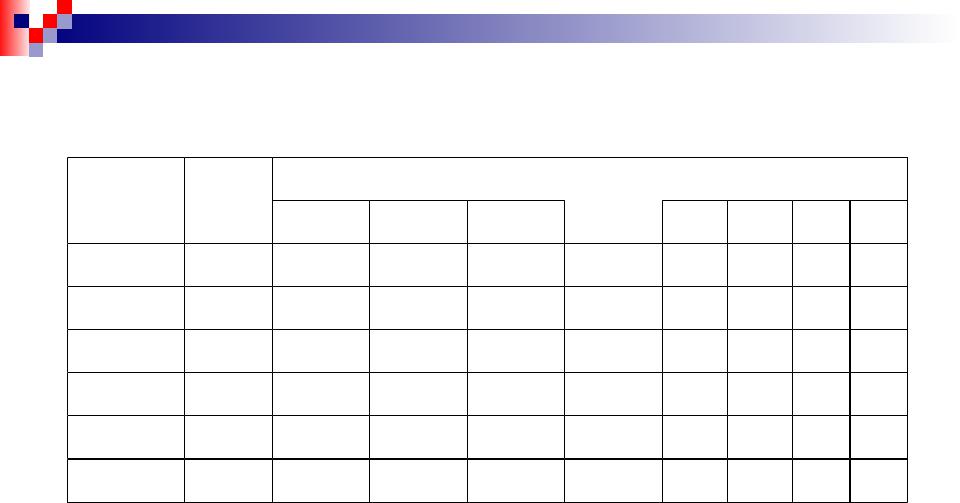
Химический состав подшипниковых сталей
Марка |
ГОСТ |
|
|
Содержание элементов, % |
|
|
|
||
|
|
|
|
|
|
|
|||
|
|
С |
Si |
Mn |
Cr |
P |
S |
Ni |
Cu |
ШХ15 |
801-78 0,96-1,05 |
0,17-0,37 |
0,20-0,40 |
1,30-1,65 |
0,027 |
0,020 |
0,30 |
0,25 |
|
ШХ15СГ |
801-78 |
0,95-1,05 |
0,40-0,65 |
0,90-1,20 |
1,30-1,65 |
0,027 |
0,020 |
0,30 |
0,25 |
ШХ20СГ |
801-78 |
0,90-1,00 |
0,55-0,85 |
1,40-1,70 |
1,40-1,70 |
0,027 |
0,020 |
0,30 |
0,25 |
18ХГТ |
4543-71 |
0,17-0,23 |
0,17-0,37 |
0,8-1,1 |
1,0-1,3 |
0,035 |
0,30 |
0,30 |
- |
|
|||||||||
20Х2Н4А |
4543-71 |
0,15-0,22 |
0,17-0,37 |
0,3-0,6 |
1,25-1,75 |
0,025 |
0,020 |
- |
0,30 |
|
|||||||||
ШХ4 |
801-78 |
0,95-1,05 |
0,15-0,30 |
0,15-0,30 |
0,35-0,50 |
0,027 |
0,020 |
0,30 |
0,25 |
17

Маршрутная технология получения деталей подшипников
(на примере изготовления колец подшипников):
1.Приготовление расплава, литье слитков на машинах непрерывного литья заготовок;
2.Горячая деформация свободной ковкой, штамповкой на горизон- тально-ковочных машинах, раскаткой;
3.ПТО с целью улучшения обрабатываемости резанием и подготовки структуры к ОТО;
4.Предварительная механическая обработка;
5.ОТО предварительно обработанных заготовок;
6.Окончательная механическая обработка (шлифование и доводка);
7.Отжиг для снятия напряжения;
8.Сборка и контроль качества.
18

Технология ПТО подшипниковых сталей заключается в сфероидизирующем отжиге с образованием структуры зернистого перлита. Сталь с такой структурой обеспечивает хорошую обрабатываемость резанием и высокое качество поверхности заготовок.
Структура зернистого перлита стали после отжига позволяет получить для ШХ15 и ШХ4 твердость НВ 179-207, для ШХ15СГ и ШХ20СГ - НВ 179217. При правильных температурно-временных параметрах отжига в структуре стали отсутствует карбидная сетка, а размеры карбидных частиц примерно одинаковы.
Если в результате горячей деформации подшипниковых сталей образовалась карбидная сетка, то рекомендуется для исправления этого дефекта провести отжиг нормализацию при температуре 900- 920 °С с выдержкой 30-40 мин, охлаждение со скоростью не менее 40-50 °С/ч. Такая скорость достигается охлаждением мелких поковок на воздухе, более крупных - обдувом воздуха или водовоздушной смесью.
19

Параметры сфероидизирующего отжига:
нагрев выше точки Ас1, но ниже Асm, выдержка при заданной
температуре в течение 45-60 мин, скорость охлаждения должна быть такой, чтобы превращение аустенита в зернистый перлит завершилось при температуре 600 °С.
Рекомендуется охлаждать со скоростью 15-20 °С/ч для садок массой более 3 т; 25-30 °С/ч для садок менее 0,5 т. Более быстрое охлаждение приводит к получению неоднородного крупнозернистого перлита с повышенной твердостью.
Заготовки для подшипников, изготовленные из низкоуглеродистых легированных цементуемых сталей, подвергают нормализации при температуре 900-920 °С и высокому отпуску при 640-660 °С. Твердость не превышает НВ 241, микроструктура - сорбитообразный перлит.
Контроль качества ПТО проводится проверкой твердости и микроструктуры заготовок.
20