
[SHipinsky_V.G.]_Oborudovanie_i_osnastka_upakovoch(z-lib.org)
.pdf
применяться термоконтактная, лучевая или ультразвуковая сварка, а также сварка горячим воздухом или токами высокой частоты. Сборка туб завершается навинчиванием на горловину головки колпачков (бушонов) и после этого готовые изделия подаются на тубонаполнительные автоматы.
Автоматическая линия по производству бесшовных пластмассовых туб, в частности, состоит:
из установки 1 (рис.17.2) экструзионного формования цилиндрической трубки и резки ее на мерные заготовки корпуса;
установки 2 формования полиэтиленовой головки и сварки ее с заготовкой корпуса;
установки 3 внутреннего лакирования тубы с туннельной сушильной камерой 4;
устройства 5 многокрасочного декоративного оформления наружной поверхности туб с туннельной сушильной камерой 6;
автомата 7 навинчивания колпачков на горловину тут и их укладки в технологические кассеты-накопители или транспортную тару;
Рис.17.2. Схема автоматической линии по производству бесшовных пластмассовых туб
а также транспортирующей системы 8, связывающей между собой все устройства линии и обеспечивающей их работу в едином технологическом цикле с производительностью от 80 до 120 туб в минуту.
Автоматизированная линия по производству ламинатных туб,
работающая с производительностью 65 – 70 туб в минуту, содержит два устройства размотки 1 и 2 (рис.17.3), на которые устанавливаются рулоны декорированной ламинатной ленты, а также сварочное устройство 3, обеспечивающее соединение концов рулонов без приостановки производственного процесса.
Рис.17.3. Схема автоматической линии по производству ламинатных туб
11

Далее через направляющие ролики 4 лента подается в рукавообразователь 5 и оправку 6, где сворачивается в трубку с точным совмещением кромок внахлест. Затем в зоне нахлеста края ленты соединяются между собой непрерывным сварным швом под воздействием тока высокой частоты сварочной головки 7 и обжимных роликов 8. В следующем устройстве 9 полученная трубка разрезается на заготовки 10 в соответствии с их заданной длиной. Требуемая точность резки обеспечивается фотоэлементом, реагирующим на метки, нанесенные на поверхность при полиграфическом оформлении ленты. Затем заготовки корпусов туб на станции 11 поворачиваются в плане на 90о и укладываются на ленточный конвейер 12, служащий промежуточным накопителем и обеспечивающий подачу корпусов в сборочный автомат 13. Здесь поштучно подаваемые головки туб вместе с корпусами насаживаются на оправку и на ней свариваются между собой по периметру плеча головки токами высокой частоты. При этом в ламинатных тубах на головку в области плеча дополнительно приваривается штампованная из того же ламината внешняя или внутренняя кольцевая вставка (рондель), повышающая диффузионную плотность тубы в этой зоне. В следующем устройстве 14 линии, поштучно подаваемые колпачки навинчиваются (напрессовываются) на горловину тубы и готовые изделия следующим устройством 15 укладываются в транспортную или технологическую тару 16, в которой затем и доставляются на тубонаполнительные автоматы или склад.
Такие автоматические линии для производства ламинатных туб, имеющие свои характерные конструктивные особенности, выпускаются несколькими зарубежными фирмами.
Рис.17.4. Автоматическая линия модели B·GLS-III
фирмы «Boom Industry» (Китай) для производства ламинатных туб
В частности, высокотехнологичная автоматическая линия (рис.17.4) модели B·GLS-III фирмы «Boom Industry» (Китай), работающая в комплексе с литьевым автоматом модели B·ZT-III, изготавливающим головки туб, имеет следующую техническую характеристику:
Производительность, штук/мин. ……………………………… 150; Диаметр туб, мм:
минимальный ……………………………………….. 12,7; максимальный ………………………………………. 60,0;
Потребляемая мощность, кВт ………………………………… 20,7; Габаритные размеры, мм:
12
длина ………………………………………………... 4810, ширина ……………………………………………...... 850, высота ………………………………………………..1700;
Масса, кг………………………………………………………… 2500.
17.4. Изготовление колпачков (бушонов) для туб
Укупоривающие колпачки (бушоны) для всех типов туб изготавливаются методом литья под давлением из полиэтилена высокой плотности, полипропилена или полистирола с их разнообразной цветовой окраской. Изготовление, как правило, производится в многоместных формах на специализированных литьевых автоматах.
17.5. Оборудование для наполнения и закрытия туб
Оборудование для наполнения и закрытия туб можно классифицировать по следующим признакам:
по степени автоматизации – на машины с ручным, полуавтоматическим и автоматическим управлением;
по принципу перемещения объектов обработки – на двухпозиционные, а также на карусельные и конвейерные одно- и многопоточные;
по виду наполняемых туб – на машины для металлических туб, для пластмассовых и ламинатных туб, для комбинированных туб (двухъемкостных, полутуб (туба-флакон), туб с комбинированным заполнением и др.), а также на универсальные;
по выполняемым процессам – на наполняюще-закрывающие машины и комплексно-автоматизированные линии, обеспечивающие изготовление, наполнение и закрытие туб.
Машины с ручным управлением обеспечивают наполнение и закрытие туб с производительностью до 10 упаковок в минуту. Применяются они в условиях индивидуального и мелкосерийного производства, когда объемы производимого узкоспециализированного продукта невелики и покрываются возможностями ручного производства, а также в лабораторных условиях для экспериментальной отработки технологии упаковывания новой продукции в тубы различных исполнений. Обычно комплект такого оборудования состоит из двух машин, из которых одна обеспечивает фасование продукции в тубу, а вторая – ее герметичное закрытие плоским фальцевым или сварным швом, содержащим также и традиционную маркировку. Такие комплекты оборудования высокого качества поставляют, например, швейцарская фирма «Hahma» и польская фирма «Tubarex», а стоимость его составляет порядка 7 тысяч евро.
Полуавтоматическое же оборудование обеспечивает наполнение и закрытие туб с производительностью от 20 до 40 упаковок в минуту, а его начальный ценовой уровень составляет порядка 12 – 15 тысяч евро. Полуавтоматы, как правило, не комплектуются бункером автоматической подачи пустых туб и их в держатели машины вручную устанавливает оператор, упаковывающий продукцию.
Автоматическое оборудование, в свою очередь, работает с производительностью от 60 упаковок в минуту, а в высокопроизводительных
13
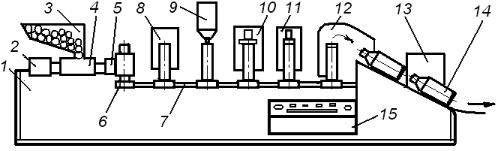
многопоточных автоматах она достигает 400 туб в минуту и более. Оборудование этого класса сильно отличается по стоимости, составляющей от 12 до 45 тысяч евро. При этом более дешевыми являются автоматы, специализированные на упаковывании в однотипные тубы, а более универсальные автоматы известных фирм, содержащие наборы комплектующих частей для их переналадки на различные типоразмеры туб, являются соответственно и более дорогими.
Данные автоматы содержат на общей станине ряд исполнительных устройств, расположенных в последовательности выполняемых операций и объединенных общим конвейером с гнездами для установки туб или карусельным транспортирующим столом. Различия в конструктивном исполнении автоматов, предназначенных для металлических туб или для пластмассовых и ламинатных туб, обусловлены в основном исполнением механизмов, обеспечивающих их закрытие после наполнения.
В частности, автомат для наполнения металлических туб модели
«АРЕНКОМАТИК 1000» фирмы «ARENCO» (Швеция) на станине 1 (рис.17.5) содержит питатель 2, которым тубы из кассеты 3 поштучно забираются и подаются в механизмы очистки 4 и довинчивания 5 колпачка, а затем устанавливаются вертикально в гнезда 6 шагового транспортера 7, работающего от привода с регулируемой скоростью движения.
Рис.17.5. Схема автомата для наполнения и закрытия металлических туб
На следующей же позиции автомата располагается механизм 8, который путем вращения относительно оси симметрии ориентирует тубу в гнезде по нанесенной на ее конце метке в заданное положение, контролируемое фотодатчиком, с фиксацией в этом положении. При перемещении транспортером 7 на следующий шаг эта туба располагается под дозатором 9, содержащим бак емкостью 90 дм3 и два дозатора, один из которых обеспечивает фасование в нее порции упаковываемой продукции объемом от 3,5 до 50 см3, а второй – от 25 до 300 см3. Дозатор оснащен также противокаплевым сдувателем и датчиком, блокирующим фасование продукции, при отсутствии в гнезде тубы. После наполнения закрываемый конец корпуса тубы должен оставаться свободным и чистым от фасуемого продукта.
Далее туба перемещается транспортером в фальцевальное устройство 10, сжимающее губками конец ее корпуса в плоское положение и несколько раз загибающее его. В зависимости от требуемой прочности применяется двойное, тройное, четверное и седлообразное фальцевание (загибание) конца металлической тубы. В следующем механизме 11 производится гладкое или с рифлением обжатие фальцевого соединения, после чего оно становится
14
плотным, герметичным и стабильным. Одновременно с обжатием на фальцевый шов клеймом наносится маркировка, содержащая информацию о месяце и дате изготовления продукта, а также номер партии.
На следующей позиции готовые упаковочные единицы механизмом 12 извлекаются из гнезд транспортера 7, разворачиваются в горизонтальное положение закрывающим швом вперед и через счетное устройство 13 выводятся из автомата на транспортер, перемещающий тубы 14 в следующий автомат, упаковывающий их в картонные пачки. Управление автоматом осуществляется от микропроцессора 15, содержащего индикаторы неполадок.
Автомат модели «АРЕНКОМАТИК 1000» имеет следующую техническую характеристику:
Производительность, туб/мин., не более…………………………. 100; Наполняемые тубы:
диаметр, мм ……………………………………….. 10 – 50; длина, мм ………………………………………… 50 – 250; вместимость, см3 ………………………………….3,5 – 300;
Питание: переменный ток:
частотой, Гц …………………………………………… 50; напряжением, В …………..………………………. 380/220;
сжатый воздух под давлением, мПа…………………. 0, 5; Потребляемая мощность, кВт, не более ..………………………… 1,3; Расход сжатого воздуха, дм3/мин, не более………………………. 100; Габаритные размеры, мм:
длина ………………………………………………......1800, ширина ……………………………………………...... 1300, высота …………………………………………………2350;
Масса, кг………………………………………………………….. 1550.
По приведенной схеме выполняются и другие тубонаполнительные автоматы, например фирмы «NORDEN UVA» (Швеция), такие как:
модели «НОРДЕНМАТИК NM 600-M» производительностью 60 туб/мин.;
модели «НОРДЕНМАТИК NM 1000-M» производительностью 100 туб/мин.;
модели «НОРДЕНМАТИК NM 2000-M» производительностью 200 туб/мин.
идругие.
Автомат для наполнения пластмассовых и ламинатных туб фирмы
«CO. MA. DI. S» (Италия), в свою очередь, содержит установленные на станине 1 (рис.17.6) следующие функциональные устройства и механизмы:
карусельный стол 2 с гнездами 3 для туб 4, периодически поворачивающийся с заданным ритмом;
питатель с кассетой 5, из которой тубы механизмом 6 поштучно забираются
ивставляются в гнезда 3 карусельного стола;
устройство 7 довинчивания колпачка, а также ориентирования тубы в требуемое положение, контролируемое фотодатчиком 8 по нанесенной на ее конце метке, с фиксацией в гнезде;
дозатор 9, осуществляющий фасование в тубу требуемого объема продукта по команде датчика, контролирующего наличие тубы;
15

устройство 10, обеспечивающее нагрев до пластичного состояния конца тубы на высоту 8 – 10 мм горячим воздухом с температурой около 340 оС;
Рис.17.6. Схема карусельного автомата для наполнения ламинатных туб
прессовый механизм 11, обжимающий плоскими губками разогретый конец тубы, при этом ее кромки свариваются и частично охлаждаются;
устройство 12, наносящее маркировку с помощью клише на закрывающий сварной шов тубы;
устройство 13, обеспечивающее охлаждение закрывающего шва тубы проточной водой;
механизм 14, подрезающий верхнюю неровную кромку закрывающего шва тубы, для придания упаковке товарного внешнего вида;
механизм 15, извлекающий упаковочные единицы из гнезд 3 карусельного стола и выводящий их через счетное устройство 16 из автомата.
Цикловые дискретные повороты карусельного стола 2, а также работа установленных вокруг него с адекватным шагом функциональных устройств и механизмов автомата осуществляется от общего электродвигателя, связанного
сними механическими системами передачи движений. Микропроцессорная же система управления этого автомата обеспечивает взаимосвязанную работу всех его устройств и механизмов по параллельно-последовательной схеме действия, а также вывод на дисплей информации с индикаторов неполадок, датчиков контроля технологических режимов работы и счетного устройства. По приведенной схеме выполняются и другие тубонаполнительные автоматы, например фирмы «NORDEN UVA» (Швеция), такие как:
модели «НОРДЕНМАТИК NM 600-Р» производительностью 50 туб/мин.;
модели «НОРДЕНМАТИК NM 1000-Р» производительностью 75 туб/мин.;
модели «НОРДЕНМАТИК NM 2000-Р» производительностью 150 туб/мин. Созданы также комплексно-автоматизированные линии, например,
модели «KOMBIS» (рис.17.7), которые в едином цикле обеспечивают изготовление ламинатных туб, а также их наполнение продуктом, закрытие и поштучное упаковывание в пачки. Модульный принцип конструктивного
16
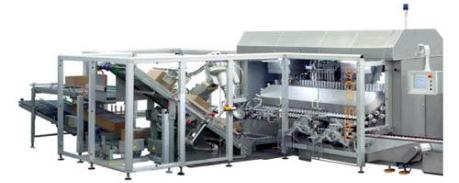
исполнения этих линий позволяет с соответствующей переналадкой производить на них ламинатные тубы в широком диапазоне типоразмеров корпуса, с различными формами плеч головки и укупоривающих колпачков, а также герметично закрывать отверстие в горловине тубы алюминиевой защитной мембраной.
Рис.17.7. Комплексно-автоматизированная линия ламинатных туб модели «KOMBIS»
В настоящее время это одно из наиболее интересных предложений на рынке технологического оборудования этого класса. Несколько десятков таких линий стоимостью от 800 тысяч евро уже закуплены и эксплуатируются компанией «Unilever».
Высокопроизводительное оборудование для наполнения туб производят, например, такие известные зарубежные фирмы, как «NORDEN» (Швеция),
«AXOMATIC» и «CO.MA.DI.S» (Италия), «OYSTAR» и «TGM Tecnomachines»
(Германия), «UNIKO» и «SIGMA» (Чехия). Заказчиками для них выступают такие международные концерны, как «Procter & Gamble», «Colgate», «Johnson & Johnson», «Henkel» и другие. Оборудование этих производителей соответствует фармацевтическим стандартам качества GMP, а по своим эксплуатационным показателям и надежности в работе удовлетворяет самым высоким требованиям. В нем применяются высококачественные электронные системы управления и другие комплектующие известных фирм, а также разнообразные ноу-хау. Например, на автоматах фирмы «NORDEN» (Швеция) в неподвижном овальном столе движется транспортирующая лента с наполняемыми тубами, вместо традиционно применяемого для этого карусельного стола. Применяются также разнообразные устройства нагрева конца тубы до пластичного состояния перед его сваркой, противокаплевые механизмы дозаторов, механизмы для разнообразных форм подрезки кромки закрывающего сварного шва тубы и высечки в нем отверстия для ее подвешивания, а также устройства для загрузки туб нетрадиционных форм – овальных, кубических, призматических и т. д. Стоимость такого оборудования, обеспечивающего не высокую производительность, начинается от 60 тысяч евро, а стоимость многопоточного автомата, работающего, например, с производительностью 500 туб в минуту, может достигать и одного миллиона евро. Тубонаполнительное оборудование производится также в России (ЗАО «Ленпродмаш» и Ногинский завод «ФНПЦ Прибор»), Болгарии (фирма «Problend»), КНР, Израиле и других странах. Наиболее же дешевым является оборудование производства НПП «Интермаш» (г. Киев).
17
18. ПРОИЗВОДСТВО КАРТОННОЙ ТАРЫ 18.1. Характеристика картонной тары
Для упаковывания товарной продукции широко применяются картонные пачки, коробки, ящики и лотки. Из картона изготовляют также банки, стаканы, пеналы, папки, ведра, барабаны, гильзы, катушки, шпули, разнообразные укладочные средства, амортизирующие и другие элементы упаковки.
Достоинства картонной упаковки заключаются в невысокой стоимости материала, малом удельном весе тары, технологичности ее производства, хорошей газопроницаемости и низкой светопроницаемости, хорошем воспроизведении полиграфического оформления. К недостаткам же следует отнести невысокую прочность, которая резко снижается при намокании картона, высокую влагопроницаемость, легковозгораемость, а также ее подверженность разрушению микроорганизмами и насекомыми. Перечисленные недостатки частично устраняются у тары, выполненной из композиционных и многослойных материалов на основе картона, получаемых ламинированием картона полимерными пленками, кашированием (склеиванием) картона с алюминиевой фольгой, а так же его пропиткой соответствующими веществами.
По конструктивным особенностям и способу изготовления картонная тара и другие элементы упаковки подразделяются на цельные и сборные, а также складные и нескладные.
Цельные картонные изделия изготовляются без применения сборочных операций, например, штамповкой и прессованием из одной заготовки, формованием из бумажной гидромассы, а также навивкой и механической обработкой.
Сборная картонная тара изготовляется из одной или нескольких деталей путем образования между сопрягающимися элементами клеевых, сварных паяных, сшивных, фальцевых или замковых соединений, а также с использованием крепежных и соединительных деталей, таких как скобы, заклепки, гвозди, шурупы, винты, гайки, шайбы, петли, ушки, угольники, планки, крючки и другие.
Складную картонную тару можно без повреждений складывать из объемной в плоскую, хранить и транспортировать в таком виде, а затем снова приводить в объемное рабочее состояние непосредственно при упаковывании продукции.
Нескладная картонная тара после изготовления не может быть сложена без повреждений, а затем снова раскрыта. Как в порожнем, так и в заполненном состоянии она всегда занимает одинаковый объем. Нескладными, например, являются все виды цельных лотков и подарочных коробок, картонные банки, стаканы, пеналы, ведра, барабаны, гильзы, катушки, шпули, а также многие исполнения сборных коробок, выполненных на клеевых, паяных, сварных, фальцевых и других неразъемных соединениях.
По форме картонная тара выполняется квадратной, прямоугольной, шестигранной, цилиндрической, овальной, конусообразной, а также в виде
других простых и комбинированных объемных фигур. |
Многие |
виды |
картонной тары получают в результате соединения |
между |
собой |
18
разнообразных по исполнению составляющих их конструктивных элементов, таких как стенки, обечайки, дно, крышки (затворы), клапаны, плинтусы и других.
18.2. Формование изделий из бумажной гидромассы
Упаковка, формованная из бумажной гидромассы, появилась в начале 20го столетия в США в виде ячеисто-бугорчатых лотков, предназначенных для упаковывания яиц. Постепенно такие лотки стали самым массовым и практически монопольным средством для упаковывания этой продукции во всем мире. В настоящее время этим методом изготовляют также ячеистобугорчатые коробки, в которые укладывают от 4 до 20 штук яиц, а также футляры разнообразных форм и размеров, в которые упаковывают фрукты, бутылки, электроприборы, косметику. Этим методом изготовляют также лотки и стаканы для посадки рассады, амортизирующие прокладки и многие другие упаковочные изделия.
Для производства формованных изделий используется макулатура с малым содержанием инородных тел (полимерных пленок, песка, металлических скоб) и других включений. Это использованный картон, гофрокартон и их обрезки, газетная, книжная и писчая бумага, а также другая утилизированная макулатура. За счет такого производства уменьшаются объемы выбрасываемой в мусор макулатуры и, в результате, снижается загрязнение окружающей среды, а высоким содержанием целлюлозы в таком сырье гарантируется хорошее качество изготовляемых изделий. Соотношение бумаги и картона для приготовления гидромассы должно быть следующее: 20
– 30 % бумажной макулатуры и 70 – 80 % картона и гофрокартона. Технологический процесс производства формованной тары включает в
себя следующие основные стадии:
приготовление гидромассы из макулатуры;
вакуумное формование изделий;
сушку изделий до необходимой влажности;
окончательную механическую обработку изделий.
Начинается процесс с загрузки макулатуры и подачи воды в гидроразбиватель (пульпер) 1 (рис.18.1). Далее макулатура в пульпере разволокняется в потоках жидкости, которые создаются центробежным ротором и специальной армировкой его корпуса. Затем приготовленная гидромасса (пульпа) перекачивается насосом через гидрогрохот 2 в промежуточную емкость 3. В гидрогрохоте при этом обеспечивается отделение из пульпы крупных минеральных и других посторонних включений, которые направляются в отходы, а также сортировка по размерам содержащихся в пульпе волокон, крупные из которых направляются обратно в пульпер на повторное разволокнение, а остальная прошедшая через гидрогрохот пульпа в промежуточной емкости 3 доводится до требуемой концентрации. Далее из емкости 3 приготовленная гидромасса дозирующим насосом постепенно перекачивается в бак 4 формовочной машины. Здесь при формовании изделий в пульпу бака 4 периодически погружается всасывающее-фильтрующая полуформа 5, формирующая внутреннюю полость изготовляемого изделия. Ее формообразующая часть выполнена из мелкоячеистой сетки, закрепленной на
19
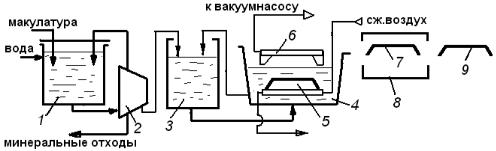
камере, через которую при погружении всасывающим насосом прокачивается находящаяся в баке пульпа. При этом вода отфильтровывается, а волокна осаждаются на сетке, формируя картонную заготовку.
Рис. 18.1. Схема производства изделий формованием из бумажной гидромассы
После получения требуемой толщины слоя полуформа 5 поднимается над пульпой и сопрягается с расположенной над ней передающей полуформой 6, формирующей наружную поверхность изделия. При этом в полуформу 5 подается избыточное давление, а в камере полуформы 6 над перфорированной мелкими отверстиями сопрягающейся поверхностью создается вакуум. Под действием перепада давлений сформованная масса притягивается к поверхности передающей полуформы 6 и принимает ее очертания. После этого нижняя полуформа 5 снова опускается в пульпу, а верхняя полуформа 6 перемещает удерживаемую заготовку 7 в зону работы транспортера сушильной камеры 8. Здесь в камеру полуформы 6 подается избыточное давление воздуха, обеспечивающее отделение от ее поверхности заготовки 7 с укладкой на транспортер. Далее подача сжатого воздуха прекращается и полуформа 6 возвращается в исходное положение, а заготовка 7, содержащая влаги 70 – 75%, транспортером перемещается в сушильную камеру 8, где конвективным методом высушивается до необходимой остаточной влажности. После сушки обычные отформованные изделия 9 подаются на окончательную механическую обработку (при необходимости) или сразу укладываются в транспортную тару для доставки потребителям.
При производстве же высококачественных изделий их отформованные заготовки высушиваются в камере 8 при заданной температуре только до определенной степени влажности, а затем на формовочной машине (подпрессовщике) из этих заготовок горячим прессованием в смыкающейся форме, имеющей адекватную конфигурацию рабочей полости, получают готовые изделия с более привлекательным внешним видом, гладкими поверхностями стенок и улучшенными эксплуатационными свойствами.
На приведенном принципе действия работают установки формования, выполненные в разнообразных конструктивных исполнениях, начиная с небольших полуавтоматов с производительностью 360 изделий в час и заканчивая комплексно автоматизированными линиями, работающими с производительностью более 10 тысяч изделий в час. Фирма «Колеус», (г. Москва) производит, например, малогабаритные установки для формования изделий из бумажной гидромассы с ручным управлением и некоторыми элементами автоматики. Современный же высокопроизводительный комплекс фирмы «НОRTMANN» (Дания) состоит из роторного формовочного автомата, сушильной камеры туннельного типа, а также системы использования оборотной
20