
Книги / Ремонт паровых турбин. Молочек В.А.г
.pdfриваемый металл соприкасался с основным неповрежденным металлом.
Заварка дефектов в отливках из углеродистой стали с содержанием углерода до 0,3% производится без предварительного подогрева, а заварка в отливках из легированных ста-
лей (12МХ, 15МХ, 18МХ, 12Х1МФ, 15Х1М1Ф, 12Х2МФСР) с предварительным местным подогревом до 250—450° С. В связи с тем, что снятие внутренних напряжений после сварки путем термической обработки цилиндра производить на электростанции практически не представляется возможным, необходимо сварку вести с расчетом, чтобы предупредить возможность возникновения внутренних напряжений.
Для этого наплавка производится электродами небольшого диаметра в шахматном порядке
инебольшими участками; наплавку каждого соседнего участка нужно производить после того, как ранее наплавленный участок охладился до 50—60° С, т.е. до такой степени, что к нему можно прикоснуться рукой. Порядок наплавки участками, обеспечивающий необходимые перерывы для охлаждения, показан на рис 7.11, а. В процессе сварки при нанесении каждого слоя, образующийся поверх него шлак должен быть полностью удален обрубкой, чтобы следующий слой сварочного шва наносился на чистый металл; кроме того, сам слой наплавленного металла следует прочеканивать (исключая первый слой) притупленными зубилами.
Установка в местах раковин и свищей ввертышей с их последующей расчеканкой не рекомендуется, так как надежность такого способа ремонта меньше, чем электросварки. Вообще производить подчеканку на стальных и чугунных отливках в местах просачивания воды не следует, так как расчеканка действует на небольшую глубину стенки отливки и при работы турбины обычно в этих местах вновь обнаруживается неплотность.
Устранение трещин и больших раковин в чугунных цилиндрах, при необходимости получения должной плотности и непроницаемости, производится после засверловки концов трещины
иих заделки пробками (гужонами), путем установки уплотняющих накладок толщиной 8—10 мм, как указано на рис 7.11, б. Для этого необходимо тщательно зачистить место вокруг трещины
иподогнать к этому месту накладку из стали марки Ст 3 так, что бы она плотно прилегала к стенке цилиндра. Перед установкой накладки вдоль трещины крейцмейселем разделывается паз глубиной 3—4 ми, который плотно зачеканивается проволокой из красной меди заподлицо с поверхностью стенки цилиндра.
Отверстия под болты диаметром 8—12 мм для крепления накладки должны быть сначала просверлены в накладке через каждые 150—200 мм, а затем через накладку, как по кондуктору,— в стенке цилиндра, сверление должно производиться с расчетом, чтобы рас стояние от трещины до оси отверстий было не менее трех диаметров болтов.
Накладка устанавливается на мастику с уплотняющим асбестовым шнуром и прикрепляется к телу цилиндра точно подогнанными к отверстиям болтами, проходящими через накладку и стенку цилиндра, под головки болтов и гайки должны быть поставлены шайбы из красной меди толщиной 1 мм.
В случае, если трещина проходит через разъемный фланец цилиндра, для обеспечения необходимой прочности в предварительно раз деланное гнездо ставится специальная стяжка толщиной, равной 0,3—0,5 толщины фланца, и длиной на 0,5—0,6 им меньше, чем размер гнезда. Стяжка устанавливается в горячем состоянии, после охлаждения она стягивает трещину и удерживает последнюю от распространения.
Исправление дефектов в виде сквозных раковин отверстий или свищей, имеющих диаметр до 20—25 мм, может быть произведено: 1) путем сквозного сверления и установки болтов с гайками, стальными прокладками и шайбами из красной меди, создающими не обходимую плотность (рис 7.11, в), для возможности контроля гайки ставятся с наружной стороны цилиндра; или 2) путем электродуговой сварки электродами из медной проволоки, диаметром 3—6 мм, плотно облицованной рубашкой из жести, электроды покрываются обычной меловой обмазкой (мел 70—75%, жидкое стекло 30—25%) и сушатся при температуре 15—25° С в течение 3—4 ч. Заварка производится без предварительного подогрева, но с перерывами не допускающими повышения температуры металла вблизи места заварки выше 70° С, и с проковкой после заварки.
При сварке без подогрева толстостенных конструкций для придания свариваемому шву большой прочности в процессе подготовки в основной металл по граням фаски шва ввертываются на нарезке короткие шпильки— ввертыши (рис 7.11, г). Эти ввертыши из малоуглеродистой стали, диаметром равным 0,3—0,4 толщины стенки, завертываются на глубину 1—1,5 их диаметра и оставляются выступающими на высоту 0,5—1 их диаметра, число ввертышей выбирается, исходя из того, чтобы их суммарная площадь не превышала 25% площади излома свариваемой де тали. Вначале производится обварка ввертышей, а затем заварка всего разделанного места.
7.6. РЕМОНТ ДВУХСТЕННОГО ЦИЛИНДРА ВЫСОКОГО ДАВЛЕНИЯ.
Для уменьшения перепада давления, приходящегося на стенки цилиндра высокого давления, и уменьшения толщины стенок, для облегчения условий работы фланцевых соединений горизонтальных разъемов и более быстрого обогрева цилиндра при работе на сверх высоких параметрах пара, а также для возможности применения менее дорогостоящих сталей в ряде современных турбин применяются двустенные цилиндры высокого давления (К-150-170 ЛМЗ, К-150-130 ХТГЗ, К-300-240 и др.), состоящие из внутреннего и наружного корпусов.
71
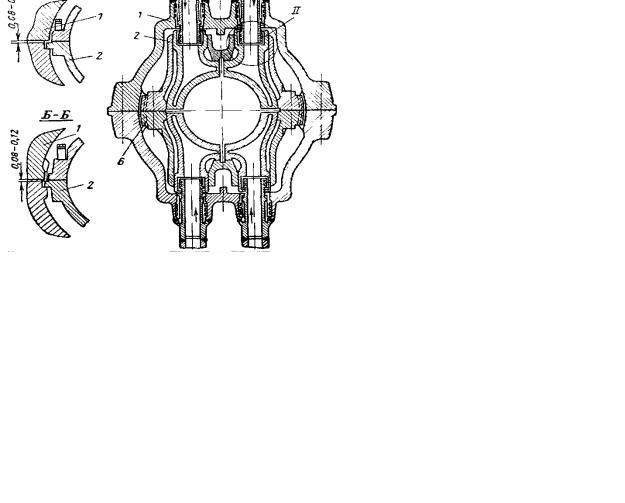
На уровне имеющегося у обоих корпусов горизонтального разъема внутренний корпус опирается лапами в пазы нижней половины наружного корпуса (рис 7.12), эти лапы одно временно выполняют роль направляющих шпонок, обеспечивающих нормальные температурные расширения во всех направлениях.
Для сохранения в работе правильного взаимного положения осей расточек наружного и внутреннего корпусов их крепление сделано с расчетом обеспечения свободы осевого и радиального расширения при расположении мертвой точки на оси клапанных коробок, такое расположение мертвой точки, связывающей внутренний и наружный корпусы, обеспечивает сохранение соосности паровпускных втулок внутреннего корпуса при расширениях обоих корпусов.
В двустенном цилиндре высокого давления турбины К-300-240 ЛМЗ, где пар к ЦВД подводится в его средней части, имеется 12 ступеней; во внутреннем корпусе расположены одна одновенечная регулирующая ступень и пять ступеней давления. Пар к сопловым коробкам внутреннего корпуса подводится через клапаны по четырем паровпускным штуцерам; после прохождения ступеней внутреннего корпуса пар делает поворот на 180° С и через паровую полость между внутренним и наружным корпусами направляется к остальным шести ступеням давления. Отработавший в ЦВД пар направляется в промежуточный пароперегреватель, после которого через за-
щитные клапаны (стопорные и отсечные) пар поступает в ЦСД.
Благодаря такой схеме движения пара наружный корпус ЦВД испытывает значительно меньшие напряжения и рассчитывается не на полное давление свежего пара, а только на давление, равное разности между давлением пара, отработавшего во внутреннем корпусе, и атмосферным давлением. Это позволило при сравнительно большом внешнем диаметре наружного корпуса уменьшить толщину его стенок, толщину фланцев разъема и уменьшить диаметр крепежа. То же самое может быть сказано и о внутреннем корпусе, так как его стенки также работают не под полным давлением свежего пара, а только под давлением разности давлений свежего и отработавшего
внем пара.
Вдвустенном цилиндре высокого давления турбины К-150-130 ХТГЗ верхняя и нижняя половины наружного корпуса состоят каждая из двух отливок, соединенных между собой вертикальным сварным швом. Передние части наружного корпуса отлиты из стали марки 20ХМФЛ, а выхлопные патрубки из углеродистой стали. Внутренний корпус, отлитый из легированной стали 15Х1М1ФЛ, также состоит из двух половин, соединенных шпильками из стали марки ЭИ723; шпильки крепежа наружного корпуса выполнены из стали марки ЭИ10. В цилиндре расположены 15 ступеней, составляющих части высокого и
среднего |
давления. |
Рисунок 7.12. Крепление внутреннего цилиндра в наружном при двухстенной конструкции ЦВД турбины К-300-240.
А-А - разрез по опорным лапам (2 шт), Б—Б—разрез по опорным лапам (4 шт), В—В—разрез по паровпускным гильзам; I—шпонка центрирующая задняя, II—установка центрирующего кольца на гильзе паровпуска, 1—наружный цилиндр, 2—внутренний цилиндр; 3 — вертикальная шпонка соединения с корпусом переднего подшипника, 4 — вертикальная шпонка соединения с корпусом среднего подшипника, 5-гильза паровпуска, 6—центрирующая расточка, 7—сегмент стопорный, 8—кольцо поршневое: 9—втулка, 10—кольцо центровочное.
72
Часть высокого давления состоит из их первых пяти ступеней, расположенных во внутреннем корпусе и двух следующих ступеней— шестой и седьмой диафрагмы, которые расположены в отдельной обойме, эта обойма вместе с диафрагмой, разделяющей цилиндр на части высокого и среднего давления, образует камеру для отвода пара на вторичный перегрев. Часть среднего давления состоит из восьми последующих ступеней, из которых восьмая ступень вместе с указанной выше разделительной диафрагмой образует камеру, куда подводится пар после вторичного перегрева.
При разборке и ремонте двустенного цилиндра высокого давления необходимо тщательно проверять: 1) зазоры, обеспечивающие расширение внутреннего корпуса в вертикальном и горизонтальном направлениях, указанных на рис. 7.12; 2) состояние шпоночных соединений, которые служат для фиксации внутреннего корпуса по отношению к наружному в вертикальной, горизонтальной и перпендикулярной к оси турбины плоскостях; 3) состояние контрольных шпилек (призонных болтов), которые устанавливаются в районе опорных латок (шпонок) для правильного и точного совпадения расточек верхней и нижней половин внутреннего корпуса, т.е. для центровки одной половины корпуса по другой; 4) правильное и плотное опирание лапок нижней половины внутреннего корпуса на соответствующие опорные места, расположенные на нижней половине наружного корпуса, при соблюдении необходимых зазоров в центрирующих шпонках; проверка правильности опирания лапок производится по краске; зазоры между верхней поверхностью опорных лапок внутреннего корпуса и крышкой наружного корпуса проверяются оттисками свинцовой проволоки, укладываемой на опорные лапки и обжимаемой крышкой ЦВД, которая обтягивается по разъему каждой третьей шпилькой; 5) состояние гильз паровпуска и насаженных на них поршневых колец, которые уплотняют и обеспечивают беспрепятственное расширение трубопроводов и патрубков, подводящих пар к 'внутреннему корпусу.
Разработка и заедания в шпоночных соединениях, предназначенных для обеспечения свободного расширения внутреннего корпуса без нарушения его сопряжения с подводящими паропроводами и наружным цилиндром, могут приводить к значительным напряжениям при тепловых деформациях и к нарушениям зазоров проточной части ЦВД.
Проверка плотности горизонтального разъема внутреннего цилиндра, а также его шабровка производятся аналогично проверке и подгонке фланцев наружного корпуса.
После выполнения всех работ по внутреннему и наружному корпусам производится полная сборка цилиндра, как указано ниже.
7.7. ЗАКРЫТИЕ ЦИЛИНДРА ТУРБИНЫ.
Закрытие цилиндра при сборке турбины производится немедленно после окончательной укладки ротора на место, что необходимо для предотвращения попадания в цилиндр посторонних предметов и мусора.
Крышка поднимается большим крюком крана так же, как это делалось при разборке. Подвеска крышки тщательно выверяется так, чтобы положение фланца разъема крышки в горизонтальной плоскости в осевом и поперечном направлениях строго соответствовало положению фланца разъема нижней половины цилиндра (параллельность фланцев); проверка горизонтальности производится по рамочному уровню, приложенному к плоскости фланца разъема крышки.
Перед поднятием крышки необходимо убедиться в хорошем закреплении в ней обойм, диафрагм и уплотнений. После поднятия крышки на 1—1,5 м от уровня пола необходимо протереть поверхности фланцев чистой тряпкой и тщательно обдуть крышку сжатым воздухом
Фланцы нижней части цилиндра после протирки сухой тряпкой равномерно намазываются слоем мастики толщиной не более 0,3— 0,5 мм (§ 2.5), с проверкой, чтобы в мастике не было крупинок; наложение мастики более толстым слоем может привести к короблению фланца или пробою стыка.
Необходимо тщательно проверять равномерность слоя и наложения мастики в надлежащих местах с тем, чтобы при затяжке фланца разъема и ее выдавливания она не попала внутрь цилиндра турбины. Иногда предпочитают намазывать мастику тогда, когда крышка уже наполовину опущена на направляющие колонки, что предохраняет от попадания сора на мастику; однако этот способ не может быть рекомендован, так как намазывание приходится производить под висящей над головой крышкой.
Применение для уплотнения горизонтальных разъемов ЦВД турбин с повышенными параметрами пара даже только тонкого слоя мастики из чистого вареного масла в ряде случаев оказалось непригодным; наблюдавшиеся размыв мастики и образование в процессе эксплуатации сквозных свищей приводили к необходимости остановки турбины для вскрытия ЦВД. При состоянии горизонтального разъема, обеспечивающем хорошую плотность, от применения мастики можно отказаться, ограничившись тщательным протиранием фланцев разъема крышки и нижней части цилиндра сухим чешуйчатым графитом.
После окончания подготовки разъема положение крышки вновь проверяется рамочным уровнем; после точной установки крана с крышкой над нижней частью цилиндра крышка опускается по направляющим колонкам, смазанным тонким слоем турбинного масла, с теми же мерами против перекосов, какие применяются при ее подъеме.
При опускании обязательна тщательная проверка хода крышки, необходимо предупредить перекосы и заедания, помимо проверки уровнем или замерами метром расстояний четырех угловых точек плоскости разъема цилиндра от крышки, необходимо, покачивая крышку поперек ее оси в пределах зазоров в направляющих колонках, прослушивать отсутствие задеваний в лопаточном аппарате.
Крышка опускается до тех пор, пока она не дойдет почти вплотную (3—5 мм) до мастики, после чего устанавливаются контрольные шпильки (призонные болты). Установка контрольных шпилек до полного опускания крышки необходима, чтобы избежать несовпадения установки обеих половин цилиндра вследствие имеющихся зазоров в отверстиях крышки под направляющие колонки. Такое несовпадение может привести к тому, что после опускания крышки контрольные шпильки не будут входить на свои места и выправление крышки потребует ее нового поднятия отжимными болтами и подъемным приспособлением, что вызовет непроизводительную потерю времени.
Окончательно опустив крышку и заколотив свинцовыми или медными кувалдами контрольные шпильки, снимают стропы, подъемные приспособления и направляющие колонки.
До закрепления крышки болтами желательно собрать упорный подшипник и провернуть ротор за муфту (при тяжелых роторах— краном), чтобы убедиться на слух в отсутствии задеваний в лопаточных аппаратах и лабиринтовых уплотнениях.
После установки гаек на болты и шпильки согласно имеющейся на них маркировке производится крепление цилиндра (см ниже).
Во избежание заеданий и облегчения снятия гаек при последующем закрытии цилиндра после длительного периода работы в условиях высоких температур нарезка шпилек, болтов и гаек, а также торцы гаек и места их упора во фланцы (подрезки) должны быть предварительно после полной очистки натерты одним из указанных в § 2.5 составов с оставлением минимального слоя.
Затяжку гаек на шпильках и болтах следует начинать с обеих сторон середины цилиндра. Правильное направление и последовательность крепления болтов с обеих сторон, устраняющие деформации цилиндра и перекос крышки, показаны цифрами и стрелками на рис 7.8.
После затяжки крепежа фланцевого разъема цилиндра до отказа следует повторно при собранном упорном подшипнике провернугь ротор и прослушать цилиндр, после чего производить сборку остальных деталей турбины.
7.8. КРЕПЛЕНИЕ ФЛАНЦЕВ ГОРИЗОНТАЛЬНОГО РАЗЪЕМА ЦИЛИНДРОВ.
При сборке турбины приходится прибегать к усиленному креплению фланцев горизонтального разъема цилиндров, работающих на вы-
соких и сверхвысоких параметрах пара и имеющих большие диаметры шпилек и болтов, которые изготовляются из легированных сталей, отличающихся высокой релаксационной стойкостью.
Установленные на парозапорной, парорегулирующей арматуре и фланцах разъема некоторых турбин, работающих с повышенными параметрами пара (565—570° С), шпильки из сталей марок ЭИ10 (25Х1МФ) и ЭИ723 (25Х2М1Ф) обладают недостаточными жаропрочными свойствами, релаксационной стойкостью и склонны к хрупкому разрушению. Такие шпильки при капитальных ремонтах следует заменять шпильками из жаропрочных сталей марок ЭП182 (20Х1М1Ф1ТР) или ЭП44 (20ХМФБР), обладающих более высокой релаксационной стойкостью при температурах до 580° С и менее чувствительных к надрезам и концентрации напряжений, гайки к этим шпилькам изготовляются из сталей ЭИ723 и ЭИ10. Шпильки из стали ЭИ723 могут применяться для работы при температурах пара не выше 540° С и из стали ЭИ10— не выше
510° С.
Усиленное крепление фланцев разъемов осуществляется затяжкой болтов и шпилек в нагретом состоянии (термическая затяжка), после остывания шпильки укорачиваются и в них создаются напряжения, достаточные для обеспечения плотности фланцевого соединения без пропаривания по разъему до следующей остановки турбины на плановый капитальный ремонт. Начальные напряжения в шпильках, обеспечивающие такую плотность фланцев разъемов цилиндров современных турбин, достигают 3 000 к/см2.
Способ нагрева шпилек до удлинения их на величину заданного натяга является по существу единственным приемлемым способом затяжки гаек на шпильках М120 и выше, при котором удается избавиться от напряжении кручения.
Механическая затяжка требует приложения очень больших сил, для затяжки гаек М165 при необходимости создания усилия затяжки около 3000 кг/см2 требуется приложение крутящего момента величиной около 5000 кГ, получить такой крутящий момент в условиях электростанции весьма трудно. Применение ударного способа затяжки приводит к большим контактным напряжениям, к пластической деформации резьбы шпилек (болтов) и гаек, к вытягиванию волокон металла в одном направлении и к образованию спаек металла по контактной поверхности резьбы. При разболчивании образующиеся на контактных поверхностях резьбы спайки создают надиры, вызывают заедания гаек и при водят к необходимости срезания гайки, а иногда и шпильки.
Следует также учесть, что при ударном способе затяжки невозможно обеспечить равномерную и правильную затяжку крепежа с достижением одинаковых напряжений во всех шпильках. Такая неравномерность затяжки сильно нагруженных шпилек (болтов) приводит к чрезмерно большим напряжениям отдельных
74
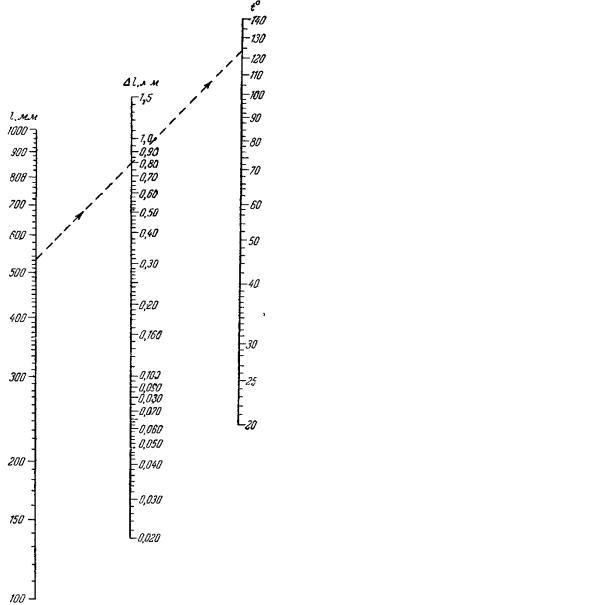
шпилек, к сокращению срока службы и к их по- |
щине обоих фланцев разъема, а рабочий размер |
|||||
ломке. |
|
шпильки l—длине свободного конца шпильки. |
||||
Термическая затяжка выполняется следую- |
Величина дуги К, на которую необходимо |
|||||
щим образом. Перед нагревом резьба шпилек и |
довернуть гайку после нагрева, зависит от диа- |
|||||
гаек натирается легким слоем смазки, которая |
метра шпильки, шага резьбы и рабочей длины |
|||||
предохраняет нарезку |
крепежа от задирания |
шпильки |
и |
определяется |
по |
формуле: |
(§ 2.5). После смазки производится предваритель- |
K=γ(σзат*l*π*Dнг)/SF. |
|
|
|||
ная обтяжка до отказа всего крепежа с одинако- |
На основании этой формулы составлена |
|||||
вым усилием вручную (без нагрева) накидным |
номограмма 1 (рис. 7.14). Эта номограмма ЛМЗ |
|||||
ключом с рычагом (трубой), длина которого вы- |
дает возможность графически определить длину |
|||||
бирается в зависимости от диаметра крепежа; на- |
дуги поворота гайки К и величину необходимого |
|||||
пример, при затяжке гаек М165 усилием двух че- |
удлинения l шпильки при нагревании на осно- |
|||||
ловек длина рычага составляет 2 м, а гаек М76 |
вании известных величин длины свободного кон- |
|||||
усилием одного человека — длина 1 м. |
ца шпильки l, принятого напряжения затяга σзат, |
|||||
При холодной |
предварительной затяжке |
шага резьбовой пары S, подлежащей затяжке, |
||||
выбираются все зазоры, имеющиеся во флан- |
наружного |
диаметра колпачковой |
гайки Dнг, |
|||
цевом соединении, и из него выдавливается из- |
γ-коэффициент пластической деформации, рав- |
|||||
лишняя мастика. Положение колпачковой гайки, |
ный 1,5. |
|
|
|
|
достигнутое при этой затяжке, фиксируется вертикальной риской, нанесенной мелом на ее цилиндрической поверхности (внешний контур гайки), и горизонтальной риской т, являющейся продолжением вертикальной риски на горизонтальную поверхность фланца (рис 7-13).
Рисунок 7.13. Горячая затяжка шпилек и болтов фланцев разъема цилиндра.
m-риска на фланце, n-вертикальная риска на цилиндрической поверхности колпачковой гайки, Dнг-наружный диаметр гайки, l-рабочий размер болта и шпильки, 1-положение гайки до поворота, 2 — положение гайки после поворота по дуге К.
В направлении, обратном завертыванию гаек от вертикальной риски по окружности на расстоянии длины дуги К, на гайке наносится вторая вертикальная риска n, указывающая, на какой угол нужно довернуть гайку после надлежащего удлинения шпильки (болта). После нагрева шпильки и ее удлинения на величину l между торцом гайки и фланцем образуется зазор, обеспечивающий свободный поворот гайки ключом на заданный угол, т.е. до совпадения второй вертикальной риски n с горизонтальной риской m на фланце. После остывания в шпильках возникнут заданные начальные напряжения, которые обеспечат необходимую плотность фланцевого соединения.
Нагрев болта (шпильки) должен производиться до такой температуры, при которой получается увеличение его рабочей длины l, позволяющее легко повернуть гайку дополнительно на заранее установленную величину дуги К. Рабочий размер болта l принимается равным тол-
Рисунок 7.15. Номограмма 2. Расшифровочный ключ l→Δl→to.
75
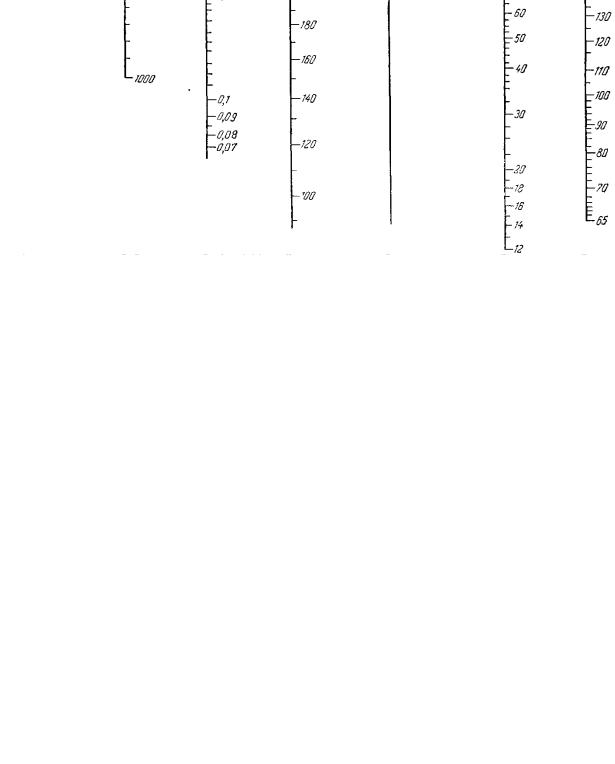
Рисунок 7.14. Номограмма 1. Расшифровочный ключ 1) l→Δl→σзат; 2) S→Δl→O; 3) O→K→Dнг.
Для определения расчетных величин температур нагрева шпилек при затяжке служит номограмма 2 (рис. 7.15).
Затяжка шпилек после нагрева на расчетную дугу поворота гайки является наиболее простым по выполнению способом термической затяжки, однако серьезным дефектом такой затяжки является отсутствие гарантии в равномерности напряжений затяжки крепежа одного и того же фланцевого соединения (разброс напряжений), так как расчет дуги поворота производится без
достаточно надежного учета податливости гаек, шайб и в целом резьбовых соединений.
Для обеспечения надежности сборки, постоянства начальных напряжении натяга и при наличии измерительных приборов для соответствующих измерений целесообразно после по ворота гаек и полного остывания шпилек проверять полученные в них напряжения, определяя их по удлинению шпилек.
Для этого индикатором с удлинителем (рис 4.5, в) конструкции ЦРМЗ Мосэнерго, специаль-
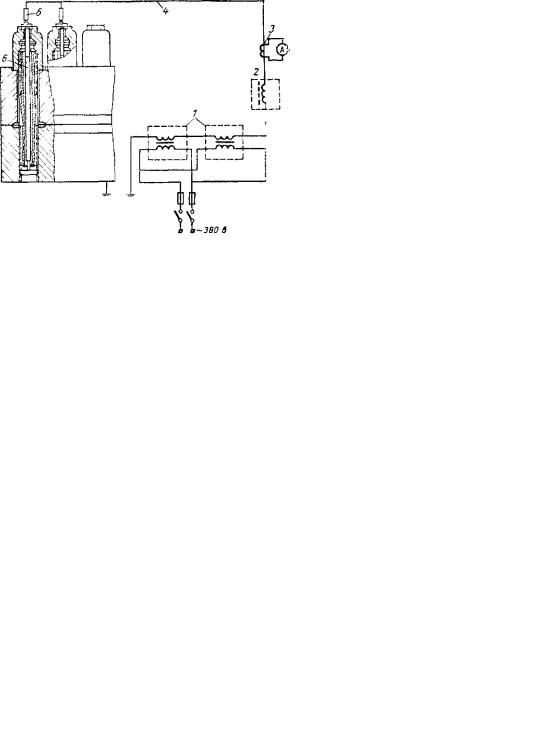
ным штангенциркулем (рис 7.16) или цанговым инструментом (рис. 7.17) конструкции Ленэнергоремонта производятся измерения с точностью до 0,01 мм длины каждой пронумерованной шпильки в холодном ее состоянии до затяжки и длины шпильки после нагрева и затяжки на расчетную дугу поворота и остывания.
Рисунок 7.16. Схема штангенциркуля для измерения длины шпильки. 1-индикатор, 2-губки штангенциркуля.
Рисунок 7.17. Схема цангового измерителя абсолютного удлинения шпильки от плоскости разъема. 1- индикатор, 2-центральный стержень прибора, 3- пружинная цанга.
Для равномерного нагрева шпильки (болты) и колпачковые гайки имеют центральные (осевые) сквозные отверстия диаметром 18-30 мм, зависящие от диаметра, длины и металла шпильки. Нагрев шпилек (болтов) через осевые отверстия производится с помощью болтонагревателей различного типа. Производить нагрев открытым пламенем газовой горелки, направленным непосредственно в центральное отверстие болта (со стороны его головки) или в отверстие колпачковой гайки для нагрева шпильки, не допускается. Высокая температура ацетиленокислородного пламени может приводить к местным пережогам металла, к оплавлению кранов отверстия шпилек вблизи торцов, к нарушениям структуры металла с недопустимым падением механических свойств и образованием микротрещин, к заеданиям и, в конечном счете, к сокращению срока службы и обрывам шпилек и болтов.
Хорошо зарекомендовавшими себя в ремонтной практике для нагрева крепежа являются карборундовые электронагреватели ЛМЗ типа
КНМВ-25 и некоторые конструкции газовых нагревателей. Карборундовый электродвигатель ЛМЗ (рис. 7.18) состоит из карборундового стержня 6 диаметром 25 мм и верхнего контакта 5, который проводом 4 присоединяется к двум последовательно соединенным сварочным трансформаторам 1. Стержень 6 помещается в осевое отверстие шпильки диаметром 35 мм, после того, как произведены холодная затяжка колпачковой гайки и разметка расчетной дуги поворота гайки К. При опускании нагревателя в отверстие шпильки особое внимание следует обращать на правильность установки его верхней части; эта установка должна обеспечить равномерный кольцевой зазор между карборундом и отверстием в шпильке; касание карборунда с металлом может вызвать замыкание и повреждение карборунда. Карборундовый стержень должен быть опущен в осевое отверстие шпильки так, чтобы его греющая часть приходилась по длине на ненарезанную часть шпильки. Это вертикальное положение стержня фиксируется с помощью установочного кольца.
Включение карборундовых нагревателей на питание током от сварочных трансформаторов по схеме, приведенной на рис. 7.18, производится после того, как на нагреватели одеты верхние контакты. Сила тока, подаваемая на нагреватели, регулируется дросселем 2 и по амперметру, включенному через трансформатор тока 3, должна быть равна 70 А на один нагреватель.
Температура рабочей части карборундового стержня достигает 1200° С. За счет радиации тепла от раскаленного стержня достигается равномерный по всей длине шпильки нагрев ее внутренней поверхности до температуры 550° С, что обеспечивает необходимое удлинение шпильки; такое падение температуры объясняется термическим сопротивлением воздушного зазора между стержнем и шпилькой.
Рисунок 7.18. Схема подключения карборундовых нагревателей ЛМЗ.
По мере нагрева и удлинения шпильки поворот гайки производится обычным ключом вручную на размеченную ранее величину дуги К. После поворота гайки на заданную величину питание нагревателя отключается; снятие верхнего
77
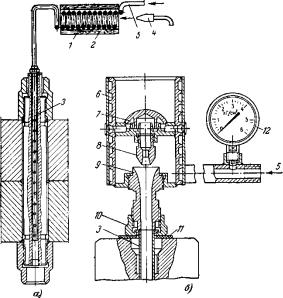
контакта и перенос нагревателя в отверстие следующей шпильки производятся после проверки прибором отсутствия тока в цепи нагревателя.
По данным ЛМЗ нагрев шпильки М120 при силе тока 70 А, напряжении 90 в и мощности 6,3 кВт выполняется за 12—15 мин, шпильки М140—за 20—25 мин и шпильки М165—за 25— 30 мин. При этих условиях, работая двумя: нагревателями, затяг крепежа цилиндра высокого давления турбины К-200-130 может быть произведен не более чем за 3—4 ч.
Для обеспечения требований техники безопасности при пользовании карборундовыми электронагревателями должны соблюдаться следующие условия: 1) хорошее заземление шпилек и корпуса цилиндра турбины; 2) надежная изоляция провода и верхнего контакта, подводящих электропитание к нагревателю (сопротивление изоляции должно быть не менее 150 кОм; 3) соответствующие организационные меры, обеспечивающие безопасносгь в связи с производством работ при напряжении 90—110 В и высокотемпературном нагреве нагревателя и шпилек.
Все операции по вводу стержней в отверстия шпилек, по выемке и переносу их в отверстия других шпилек, подлежащих затяжке, должны производиться очень осторожно, так как карборундовые стержни отличаются большой хрупкостью и совершенно не выдерживают ударов, изгибающих нагрузок и т.д.
Рисунок 7.19. Схемы нагрева шпильки; а - газовым змеевиковым нагревателем ХТГЗ; б - газовым нагревателем эжекторного типа; 1-змеевиковый нагреватель, 2-кожух с изоляцией, 3-распределительная трубка нагревателя, 4-автогенная горелка, 5-подвод сжатого воздуха, 6-корпус нагре вателя, 7-подогреватель, 8-сопло,
9-смеситель (диффузор), 10-гайка накидная, 11-прокладка, 12-манометр.
Для нагрева крепежа применяются также газовые нагреватели, одним из которых является змеевиковый нагреватель ХТГЗ, схема действия этого нагревателя приведена на рис 7-19,а. В
обогреваемый пламенем автогенных горелок змеевик, который изготовляется из 8—10 витков (диаметр витка 120—150мм) стальной трубки диаметром 15—20 мм, подается воздух под давлением 3—4 ат. Змеевик помещается в камеру из листового железа, выложенную внутри асбестом. После нагрева горячий воздух с температурой 250—300°С поступает через наконечник в распределительную трубку с равномерно расположенными по длине и окружности отверстиями, вставленную в осевое отверстие шпильки. Нагрев шпильки диаметром 120 мм при использовании такого нагревателя до необходимой для затяжки температуры достигается за 12—15 мин. Недостатком нагревателей этого типа является быстрое прогорание их змеевиковой части, вызываемое действием пламени высокой температуры.
Газовый нагреватель ЛМЗ отличается от указанного тем, что нагрев воздуха производится
взмеевике не ацетиленовыми горелками, а электрическим током. В данном случае змеевик используется как сопротивление, подключенное к сварочному трансформатору, являющемуся источником тока.
Газовый нагреватель эжекторного типа Свердловского турбомоторного завода (рис 7.19,б), представляющий собой поверхностносмешивающий теплообменник, является одной из удачных конструкций для нагрева шпилек. Сжатый воздух с давлением 5—6 ат сначала нагревается газовой горелкой в корпусе 6, затем после дополнительного нагрева в подогревателе 7 наиболее горячей частью пламени горелки поступает
всопло 8.
Из сопла горячий воздух вытекает с высокой скоростью и, захватывая продукты сгорания, поступает в смеситель 9, где происходит смешение воздуха с продуктами сгорания, отсюда газовоздушная смесь с температурой 550—650° С поступает через специальный наконечник в отверстие шпильки. Время нагрева шпилек этим нагревателем, по данным завода, ориентировочно составляет от 3-4 мин для шпилек М64 до 8—11 мин для шпилек М140.
Применение карборундовых и других болтонагревателей, не портящих резьбовых соединений, повышает производительность труда и долговечность фланцевого соединения; под долговечностью в данном случае понимается время между двумя перезатяжками шпилек, производимыми из-за ослабления затяжек шпилек вследствие релаксации напряжений, это время должно быть не меньше, чем время между двумя остановками турбоагрегата на плановый капитальный ремонт, т.е. по крайней мере не менее двух лет.
7.9. ТЕПЛОВЫЕ РАСШИРЕНИЯ.
Проверке правильности тепловых расширений турбин в целом и отдельных ее деталей, подвергающихся в эксплуатации действию высоких температур, следует при ремонте турбины уделять серьезное внимание.
78
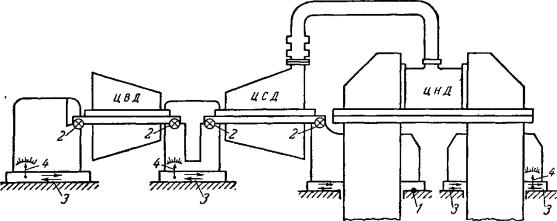
Рисунок 7.20. Схема тепловых расширений турбины К-200-130 ЛМЗ. 1-мертвая точка, 2-поперечные шпонки, 3-скользящие опоры, 4-указатели расширения.
Вэксплуатации, особенно в периоды пусков и изменений режимов нагрузки турбины, должно быть обеспечено систематическое наблюдение за беспрепятственностью продольных и поперечных тепловых расширений цилиндров и роторов, за сохранением постоянства взаимного положения осей расточек цилиндров и корпусов подшипников.
Особенно большое значение это имеет для турбин с повышенными начальными параметрами пара и мощностями, так как тепловые расширения этих турбин достигают 50 мм.
На рис. 7.20 показана схема тепловых расширений турбины К-200-130 ЛМЗ. Турбина имеет на средней раме обратного потока ЦНД мертвую точку, которая образована системой продольных
ипоперечных направляющих шпонок. Наблюдающиеся тепловые расширения вдоль оси турбины достигают при нормальной нагрузке величин: до 30 мм по указателю на переднем скользящем подшипнике ЦВД, до 12 мм—на среднем подшипнике между ЦВД и ЦСД и до 3 мм расширение ЦНД в сторону генератора.
При таких величинах расширений цилиндров турбины, естественно, что любые ненормальности и нарушения тепловых расширений вызывают перекосы, дефекты в направляющих шпоночных соединениях и защемления в скользящих опорах цилиндров; такие нарушения работы могут приводить к вибрации агрегата, к задеваниям в лабиринтовых уплотнениях и лопаточных аппаратах, к прогибам валов и пр.
Вбольшинстве конструкций турбин корпус переднего подшипника выполняется подвижным, скользящим по фундаментной раме вдоль оси турбины по двум продольным шпонкам; шпонки обеспечивают перемещение корпуса подшипника при тепловых расширениях цилиндра турбины, опирающегося на этот корпус. Чтобы избежать заеданий при перемещении, продольные шпонки должны быть пригнаны к гнездам в опорной поверхности корпуса подшипника с боковым зазором 0,04—0,05 мм, к фундаментной раме с боковым зазором 0,01—0,02 мм и по отношению к корпусу подшипника с верхним зазором в 2—3 мм (рис. 7.21, а). Шпонки привертываются к раме
впотай, сами же опорные поверхности корпуса и рамы должны быть тщательно пришабрены одна к другой и смазаны ртутной мазью.
Крепление корпуса подшипника к фундаментной раме производится болтами, шпильками и угловыми шпонками, не препятствующими перемещению подшипника (рис. 7.21, г, д, е). Для обеспечения такого крепления необходимо:
1)пришабрить поверхность, прилегающую к шайбам, подложенным под болты или шпильки;
2)подогнать гайки или головки шпилек и болтов так, чтобы при довернутом до отказа состоянии зазор между ними и шайбой равнялся 0,05—0,06 мм; 3) проверить зазор между стенкой отверстия в корпусе подшипника и телом болта или шпильки, который должен соответствовать величине максимального перемещения корпуса; этот зазор со стороны цилиндра в корпусе подшипника двухцилиндровых турбин берется равным 12—20 мм (размер х); 4) установить зазоры в угловых шпонках по обе стороны корпуса подшипника, равными 0,05—0,06 мм; эти шпонки - «диванчики» предназначены для предотвращения отставания корпуса подшипника от рамы под действием момента сил, который может появиться вследствие заедания и значительного трения при скольжении
корпуса подшипника по фундаментной раме; 5) смазать все скользящие поверхности ртутной мазью для устранения заедании и уменьшения трения.
Крепление цилиндров высокого давления с корпусами подшипников осуществляется с помощью опорных лап или полуфланцев.
Наиболее распространенной является конструкция крепления, в которой цилиндр высокого давления с помощью двух опорных лап, являющихся продолжением фланца горизонтального разъема нижней половины, опирается на корпус переднего подшипника (рис 7.22, а).
Лапы цилиндра 1 опираются на две поперечные шпонки 2; зазоры в шпоночных соединениях выдерживаются в пределах 0,04-0,07 мм. Эти шпонки, конструкции которых приведены на рис. 7.21,б, фиксируют правильность положения цилиндра по отношению к корпусу подшипника в осевом направлении и одновременно
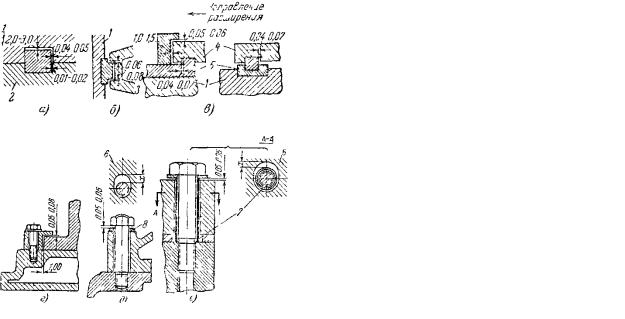
являются направляющими в поперечном направ- |
относительно оси подшипника в вертикальном |
лении. |
направлении вверх. Это является дефектом кон- |
Для обеспечения правильного направления |
струкции, так как такое, хотя и незначительное, |
расширения цилиндра относительно корпуса |
смещение при дефектах скольжения подшипника |
подшипника в вертикальном направлении внизу |
по фундаментной раме приводит к тому, что при |
между цилиндром и корпусом подшипника уста- |
расширении в осевом направлении цилиндр стре- |
новлена одна вертикальная шпонка, прикреплен- |
мится прижать корпус подшипника к фундамент- |
ная к корпусу подшипника или к цилиндру. Если |
ной раме, а при сокращении возникает опрокиды- |
шпонка крепится к цилиндру, то шпоночный паз |
вающий момент от усилий, передаваемых лапами |
выполняется в корпусе подшипника и зазор в |
ЦВД на поперечные шпонки; при этом цилиндр |
этом случае предусматривается в шпоночном со- |
стремится наклонить подшипник к себе, поэтому |
единении в пределах 0,1—0,18 мм (в зависимости |
опорная поверхность корпуса подшипника спере- |
от величины нагрева шпонок); при шпонках, рас- |
ди приподнимается, а сзади прижимается к фун- |
положенных на подшипнике (рис. 7-21, 6), зазор |
даментной раме. В наличии подъема опоры под- |
выполняется в пределах 0,06—0,08 мм. Во избе- |
шипника спереди при уменьшении нагрузки тур- |
жание заклинивания в пазу при нагреве цилиндра |
бины, снижении температуры свежего пара и пр., |
в большинстве конструкций шпоночный паз вы- |
когда цилиндр охлаждается и перемещает корпус |
полняется на цилиндре, а шпонка крепится вин- |
подшипника по направлению к генератору, не- |
тами к корпусу подшипника, являющемуся более |
трудно убедиться, замерив зазор а щупом |
холодной частью, чем цилиндр. |
(рис. 7.22, а). |
Рисунок 7.21. Крепление подвижного корпуса подшипника и зазоры в шпонках; а – продольная шпонка, б – вертикальная шпонка, в – поперечные консольные шпонки, г – угловая шпонка-«диванчик», д – шпилька с дистанционной шайбой, е – шпилька с дистанционной
втулкой. 1-корпус подшипника, 2-рама, 3-цилиндр, 4-лапа цилиндра, 5-шпонка, 6-сторона цилиндра, 7-дистанционная втулка, 8-дистанционная шайба.
Таким образом, боковым перемещениям цилиндров относительно корпусов подшипников препятствуют вертикальные шпонки, а сохранению постоянного осевого расстояния между цилиндрами и подшипниками—поперечные шпонки под лапами цилиндров. Благодаря наличию указанных шпонок оси цилиндров и подшипников практически не имеют взаимного смещения, несмотря на значительные тепловые расширения цилиндров.
В этой конструкции поверхности скольжения лап цилиндра лежат несколько ниже оси турбины, вследствие чего при тепловом расширении лап может возникнуть смещение оси цилиндра
Рисунок 7.22. «Опрокидывание» корпуса переднего подшипника; а - при креплении ЦВД на лапах, б - при креплении ЦВД на полуфланцах.
Это явление приводит к некоторой расцентровке цилиндра и корпуса подшипника и может вызывать вибрации передней части турбины, наклеп на опорной поверхности фундаментной рамы, корпуса подшипника и на продольных шпонках и при наличии червячной передачи регулятора может приводить к срабатыванию ее зубьев вследствие изменений в зацеплении.
Для устранения подобных дефектов необходимо во время ремонта освободить соединительные и крепежные болты корпуса подшипника, несколько приподнять его мостовым краном
иочистить от грязи и ржавчины фундаментную раму, опорную поверхность корпуса подшипника, шпонки и гнезда, после чего все скользящие поверхности смазать ртутной мазью или протереть серебристым чешуйчатым графитом.
Подъем корпуса подшипника, а также, в случае необходимости, его удаление с фундаментной рамы являются исключительно ответственными операциями и могут производиться только под руководством опытного персонала.
Если при проверке во время ремонта обнаружен износ шпоночных соединений, исправление этих соединений хотя и является очень трудоемкой работой, но должно быть обязательно проведено. Эта работа заключается в припиловке
ивыравнивании боковых поверхностей шпоноч-
80