
Книги / Ремонт паровых турбин. Молочек В.А.г
.pdf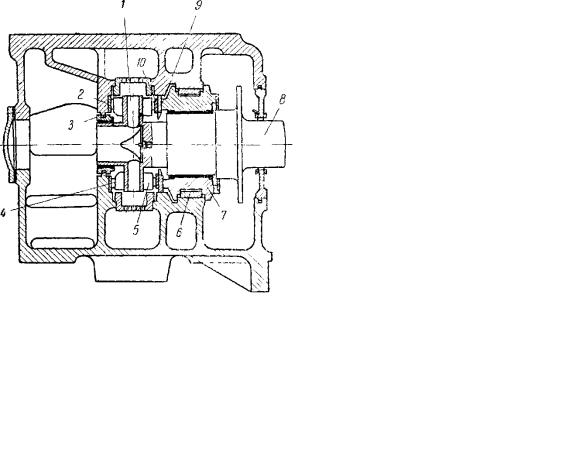
указано в § 17.4 для вкладышей опорных подшипников, с обязательными и тщательными обезжириванием, травлением и лужением. После заливки и обрубки или опиловки лишнего баббита у обеих половин вкладыша простругивается баббит у плоскости разъема и разъем пришабривается по плите и по краске при наложении обеих половинок одна на другую.
Для расточки на токарном станке обе половины вкладыша стягиваются болтами или хомутом в нормальное рабочее положение. Расточку следует вести с контролем микрометрическим нутромером (штихмасом) и по шаблону. Шаблон изготовляется из листовой стали толщиной 2—3 мм и должен точно соответствовать расположению, ширине и глубине гребней на шейке ротора; с шаблона выполняется точный контршаблон (рис. 18.5), который служит токарю для проверки правильности проточки баббита под гребни.
Рисунок 18.5. Снятие шаблона и контршаблона для расточки гребней вкладыша упорного подшипника после перезаливки.
После расточки на станке должна быть обязательно произведена пригонка рабочих поверхностей кольцевых канавок вкладыша по краске к гребням вала. Пришабровка должна производиться одновременно у обеих половин вкладыша с тем, чтобы получить равномерное прилегание опорных поверхностей подшипника по всей окружности с обеих сторон гребней и с соблюдением необходимого зазора. Шабровка должна быть закончена тогда, когда все гребни ротора одновременно касаются всех выточек во вкладыше в обоих направлениях по оси и, кроме того, разбег в упорном подшипнике достигнет величины 0,3—0,5 мм. После шабровки и окончательной пригонки вкладыша гребенчатого подшипника по осевому разбегу в нем выполняются масляные канавки, скосы и фаски по снятому до перезаливки чертежу.
Осевой разбег роторов в сегментных упорных подшипниках не должен превышать величин установленных заводом-изготовителем; для различных конструкций в роторах высокого давления он обычно находится в пределах 0,25—0,50 мм; в роторах низкого давления, имеющих упорные диски большого диаметра, величина осевого разбега доходит до 0,6—0,75 мм, а в некоторых конструкциях — даже до 1 мм. При износе упор-
ного подшипника до величины, превышающей установленный заводом максимально допустимый разбег, последний обязательно должен быть уменьшен; большой разбег может привести к задеваниям в проточной части и к ударной нагрузке на сегменты при резком изменении нагрузки турбины. Также недопустим и осевой разбег меньше нормы, так как это может вызвать зажатие сегментов и их оплавление из-за невозможности поворачиваться для создания масляного клина и жидкостного трения.
Изменение величины осевого разбега у опорно-упорных подшипников, применяемых ЛМЗ в современных конструкциях турбин высокого давления (см. рис. 18.2), производится за счет изменения толщины прокладок под разрезными полукольцами 8 и 9, состоящими из двух половин, на которые опираются рабочие 5 и устрановочные 6 сегменты подшипника.
У опорно-упорного подшипника турбины Калужского турбинного завода (рис. 18.6), в котором упорным гребнем являются боковые стенки колеса 1 центробежного масляного насоса, изменение величины осевого разбега также производится за счет увеличения или уменьшения толщины регулировочных колец 2; возможность выравнивания в небольших пределах нагрузки на отдельные упорные сегменты достигается опорой рабочих сегментов 5 на специальные упругие элементы 10.
Рисунок 18.6. Опорно-упорный подшипник турбины КТЗ. 1-упорный диск—колесо масляного насоса, 2— регулировочные кольца, 3 — уплотнение, 4— установочный сегмент, 5—рабочий сегмент, 6— опорная подушка, 7—вкладыш опорного подшипника, 8—вал турбины, 9—установочные кольца, 10 — упругие элементы.
Во всех случаях, когда осевой разбег в упорном подшипнике выходит за пределы допустимого и уменьшить его по условиям конструкции невозможно или когда вследствие износа и шабровок толщина оставшегося слоя баббита на сегментах уменьшилась до 0,8—0,9 мм (вместо
231
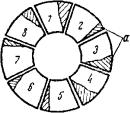
нормальной 1,5 мм), необходимо сегменты, независимо от их состояния, перезалить (§ 18.5) или заменить новыми.
Помимо проверки осевого разбега ротора, необходимо проверить правильность положения и стопорения вкладыша самого упорного подшипника в турбине, что является основным условием получения правильных осевых зазоров в лабиринтовых уплотнениях и в проточной части турбины.
Регулировка осевого положения ротора, имеющего гребенчатый подшипник типа ХТГЗ (см. рис. 18.1), у которого вкладыш состоит из двух половин и соединяется с корпусом опорного подшипника с помощью фланца, производится изменением толщины установочного кольца 3, имеющегося между фланцами вкладыша и опорного подшипника.
Осевое положение сегментного упорного подшипника может быть изменено за счет изменения толщины специальных установочных полуколец 7 и 10 (см. рис. 18.2 и 18.4), заложенных в выточках вкладышей.
Для определения места установки упорного подшипника и необходимой толщины установочных колец нужно замерить полный осевой разбег ротора при открытом цилиндре турбины без упорного подшипника. Этот разбег определяется величиной осевых зазоров на входе и выходе пара в лопаточном аппарате.
Полный осевой разбег ротора определяется при сдвигании ротора, без проворачивания из одного крайнего положения в другое по индикатору, касающемуся какой-либо точки торцевой поверхности ротора. Разность показаний индикатора, замеренных при крайних положениях ротора, показывает полную величину разбега ротора в проточной части турбины. Для исключения ошибок в замерах связанных с недостаточно точной установкой лопаток в осевом направлении, полный разбег ротора проверяют 2—3 раза, поворачивая ротор при каждой последующей проверке на 90° по сравнению с предыдущим его положением.
Упорный подшипник закрепляется подбором толщины и укреплением установочных колец при положении ротора на расстоянии, обеспечивающем необходимые осевые зазоры на стороне входа пара на рабочие лопатки.
Уменьшение толщины установочных колец производится шабровкой по плите после замеров по месту и определения необходимой их толщины; увеличение толщины требует изготовления новых установочных колец соответствующей толщины. Установочные кольца должны заводиться в посадочные места легкими ударами молотка.
18.3. РЕМОНТ УПОРНОГО ПОДШИПНИКА.
Перед разборкой упорного подшипника необходимо произвести щупом замеры радиальных зазоров между валом турбины или втулкой упорного диска и маслозащитными баб-
битовыми поясками 12 вкладыша подшипника (рис. 18.2); ротор должен лежать только на опорном подшипнике и нигде не касаться этих поясков.
Суммарный зазор между шейкой ротора и расточкой корпуса должен находиться в пределах 0,0025—0,0035 от диаметра вала или диаметра валовой втулки в точке замера зазора. При этом внизу зазор измеряется щупом и должен быть равен 1/3, а вверху измеряется по оттиску свинцовой проволоки и должен быть равен 2/3 от суммарного; боковые зазоры устанавливаются равными с обеих сторон вала. Например, если суммарный зазор для вала диаметром 300 мм равен 300*0,003=0,9 мм, то вверху он должен равняться 0,6мм, внизу 0,3 мм и с боков (с каждой стороны) по 0,45 мм.
Больший зазор вверху требуется для учета всплывания вала на масляной пленке во время работы. Задевания в баббитовых поясках корпуса подшипника, обнаруживаемые по их натиру, могут вызывать вибрации турбины; вибрация эта обычно носит местный характер и для ее устранения необходимо вскрыть упорный подшипник, расшабрить баббитовые расточки и после сборки проверить зазор между шейкой ротора и этими расточками. При увеличенных радиальных и боковых зазорах в указанных расточках следует произвести или перезаливку маслозащитных поясков, или наплавку имеющейся заливки (§ 17.5), если не наблюдается ее отставания от основного тела.
Установочные данные, которыми являются первоначальные замеры положения вала в подшипниках и положения всего вала в осевом направлении, а также все последующие аналогичные замеры должны аккуратно, записываться в формуляры для учета характера изменений, происшедших в процессе эксплуатации, и суждения о необходимости перезаливки того или иного подшипника.
Рисунок 18.7. Зарисовка на кальке следов работы сегментов упорного подшипника. а — следы касания.
При разборке упорного подшипника необходимо убедиться в том, что все болты, сегменты и другие его части имеют точную и ясную маркировку, что имеет большое значение для правильной сборки. Во время ремонта надлежит тщательно проверить и очистить все масляные камеры и каналы корпуса и самого подшипника; частицы песка, грязи и волокон от обтирочных концов, попадая на сегменты и рабочую поверхность упорного гребня сегмнетного подшипника, могут привести к аварии.
232
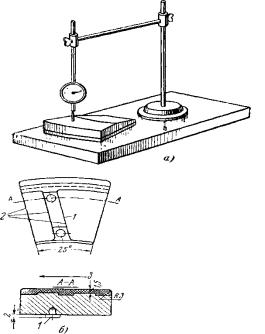
После разборки упорного подшипника необходимо произвести тщательный осмотр состояния его деталей, в особенности сегментов подшипника, упорного диска и вкладыша. Всякие риски, царапины, выбоины, трещинки, а также следы коррозии и наклепа на шлифованных поверхностях упорных дисков мешают образованию непрерывной масляной пленки между трущимися поверхностями; такие поверхности подлежат шабровке и шлифовке (см. ниже). При обнаружении у рабочих поверхностей сегментов отставания баббита от основного тела или при наличии на них посторонних включений сегменты подлежат перезаливке или замене новыми.
Для правильного суждения о работе сегментов следует зарисовать состояние их рабочей поверхности, наложив бумажную кальку на разложенные по порядку сегменты и переводя на нее следы касания и наработки на каждом сегменте (рис. 18.7). Следы работы диска на рабочей поверхности сегментов должны быть равномерными, одинаковыми и заметными только в области наиболее тонкой части масляного клина, занимая не более 20—25% от всей поверхности сегмента.
Рисунок 18.8. Проверка состояния сегмента упорного подшипника. а — проверка толщины сегмента, б— проверка линии качания и закруглений скосов сегмента.
1-ребро качания, 2 — параллельные линии, 3 — направление вращения упорного диска.
Одним из основных факторов, определяющих надежность работы упорного подшипника, является равномерное распределение нагрузки между сегментами, что определяет несущую способность упорного подшипника. Учитывая, что толщина масляной пленки между упорным диском и сегментами в самом тонком месте клина не превышает 0,01—0,015 мм, следует обратить особое внимание на толщину сегментов, которая у отдельных сегментов одного комплекта не должна разниться больше, чем на 0,01—0,02 мм.
Перегрузка отдельных сегментов, связанная с неравномерным распределением осевых усилий между ними, может вызвать их оплавление; кроме того, разная толщина сегментов может вызвать неравномерное давление на упорный диск, вследствие чего диск и вал будут воспринимать нагрузку с переменным знаком; последнее может привести к усталостным напряжениям в материале вала и, в конечном счете,—к его излому.
Проверка сегментов по толщине производится на точной проверочной плите или с помощью индикатора или таким же путем с помощью рейсмуса и щупа. При проверке сегменты кладутся стороной с баббитовой заливкой на проверочную плиту, а ножка индикатора касается сегмента так, как изображено на рис. 18.8,а. При неудовлетворительных результатах этой проверки сегменты должны быть отшабрены до получения одинаковой толщины (разница не больше 0,01 мм}; при этом сегменты должны прилегать к плите по пятнам краски всей своей рабочей поверхностью без всякого зазора с точностью шабровки двух пятен краски на 1 см2.
При значительном истирании рабочей поверхности, недостаточной толщине заливки баббита или при отставании баббита от тела сегмента сегменты подлежат перезаливке или замене новыми.
При использовании на подшипниках новых запасных сегментов, кроме проверки качесгва поверхности, толщины и закруглений входных кромок, необходимых, чтобы избежать нарушений в масляном слое, следует производить проверку одинакового расположения линий качания и направления скосов (рис. 18.8,б). Обычно линии качания сегмента располагаются радиально и делят тыльную (не рабочую) сторону сегмента на участки с отношением 2/5 : 3/5 (рис. 18.3) и с расположением более длинной части со стороны входа масла на сегмент.
В настоящее время в ряде конструкций подшипников такое расположение изменено, так как оно не дает одинакового зазора по длине выходной кромки при работе турбины. При большом числе сегментов и расположении сегментов на большом диаметре, где имеют место большие скорости масла, линия качания располагается не радиально, а параллельно выходной кромке сегмента (рис. 18.8,б), чтобы наибольший щелевой зазор получался у этой кромки на большем радиусе сегмента; такое расположение линии качания обеспечивает более равномерное распределение давления масла, что в свою очередь создает условия для более правильной работы масляного клина и для повышения несущей способности упорного подшипника.
После проверки толщины сегмента на плите необходимо проверить на полностью собранном подшипнике все ли сегменты равномерно касаются упорного диска. Для этого ротор с предварительно наложенным на упорный диск тонким слоем краски (синька, разведенная на керосине) или даже с насухо вытертым упорным диском и
233
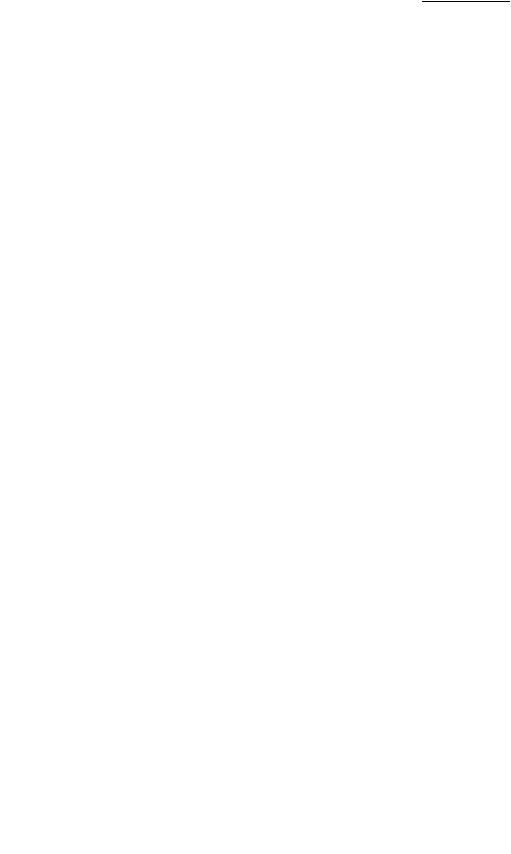
сегментами (краска может искажать результаты), проворачивается с помощью крана или вручную на три—пять оборотов по направлению нормального вращения и с сильным нажатием по оси до упора сначала в направлении хода пара и затем против хода пара. После разборки подшипника по следам краски или натиров судят о равномерности прилегания рабочих и нерабочих сегментов к упорному диску.
При недостаточно равномерном прилегании исправление производится путем шабровки поверхности баббита сегментов. Сегменты должны прилегать к поверхности диска не менее 3/4 поверхности их баббитовой заливки.
Шабровка сегментов может вызвать увеличение осевого разбега ротора, поэтому одновременно с обеспечением равномерного прилегания сегментов необходимо обеспечить осевой разбег ротора в пределах допуска.
Неправильная установка вкладыша, его установка с перекосом могут привести к тому, что, несмотря на одинаковую толщину сегментов, будет наблюдается их различная приработка.
В опорно-упорных подшипниках ЛМЗ с опорной шаровой поверхностью (см. рис. 18.2) необходимо проверять величину затяжки пружины амортизатора 10, установленного под свисающей частью подшипника и предназначенного для восприятия веса консольной упорной части вкладыша; натяжение пружины, регулируется так, чтобы разъемы вкладыша 1 и обоймы 2 были параллельны между собой; необходимо также проверять прилегание шейки вала по всей длине ее опорной части.
18.4. СНЯТИЕ И ПОСАДКА УПОРНЫХ ДИСКОВ.
Упорные диски и гребенки, если они не выполнены заодно целое с валом, насаживаются на роторы в горячем виде с небольшим натягом— до 0,06—0,08 мм. От вращения в подшипниках, типа приведенного на рис. 18.2, они фиксируются шпонками, от осевого перемещения с одной сто- роны—буртом 14, а с противоположной— разрезным кольцом (из двух половин) 15, которое закладывается в паз вала и предохраняется от выпадения под действие центробежных сил охватывающим его с натягом 0,1 мм цельным стопорным кольцом 11.
Рисунок 18.9. Проверка упорного диска. а—проверка индикаторами правильности насадки диска, б— проверка диска на плоскостность с помощью линейки и щупа, I и II — индикаторы, III — положение линейки.
Таблица 18.1. Записи показаний индикаторов при проверке осевого биения торца упорного диска.
Места отсчетов |
Показания |
Алгеб- |
Биение |
||
по индикаторам |
индикаторов, |
раи- |
|||
ческая |
диска, |
||||
(рис. 189) |
0,01 мм |
разность |
0,01 мм |
||
|
|
|
|
||
|
|
|
|
пока- |
|
I |
II |
I |
II |
заний, |
|
|
|
|
|
0,01 мм |
|
1 |
5 |
0 |
0 |
0 |
0 |
|
|
|
|
|
|
2 |
6 |
+2 |
-2 |
±4 |
2 |
3 |
7 |
+4 |
-4 |
±8 |
4 |
4 |
8 |
+6 |
-6 |
±12 |
6 |
5 |
1 |
+8 |
-8 |
±16 |
8 |
6 |
2 |
+16 |
+4 |
+12 |
6 |
7 |
3 |
+14 |
+6 |
±8 |
4 |
8 |
4 |
+12 |
+8 |
±4 |
2 |
1 |
5 |
+10 |
+10 |
0 |
0 |
Снятие упорных дисков и гребенок производится после их нагрева паяльными лампами или газовой горелкой равномерно по всей окружности до температуры 120—150° С. Нагрев для обратной посадки производится погружением в кипящую воду или в горячее масло.
При ремонте, особенно в случаях, если производилось снятие с вала упорного диска или гребенки, необходимо произвести проверку строгой перпендикулярности рабочей поверхности диска или гребенок по отношению к оси вала; перекос и отклонения от плоскостной формы (конусность) вызывают неравномерное распределение нагрузки между отдельными сегментами упорного подшипника или выточками во вкладыше подшипника гребенчатого типа и значительно снижают несущую способность подшипника.
Проверка производится установкой двух индикаторов, закрепленных на плоскости разъема у упорного подшипника с двух диаметрально противоположных сторон его на одинаковом радиусе от оси вала (рис. 18.9,а). Ножки индикаторов должны быть перпендикулярны к поверхности и должны касаться рабочей торцевой поверхности упорного диска или гребенки на уровне плоскости разъема.
В табл. 18.1 приведен пример записи показаний индикаторов при проворачивании ротора и совпадении ножек индикаторов с каждым из восьми отверстий под болты соединительной муфты, что обеспечивает получение сравнимых данных в течение ряда лет. Данные таблицы позволяют найти алгебраические разности показаний обоих индикаторов по каждой паре измерений и после приведения к нулю по наибольшему их значению определить величину и направление перекоса торца упорного диска.
Если при проворачивании ротора показания индикаторов совпадают или наибольшая разница в их показаниях не превышает 0,03 мм, то насадка упорного диска или гребенки считается удовлетворительной. Превышение этой разницы при хорошем состоянии поверхности упорного
234
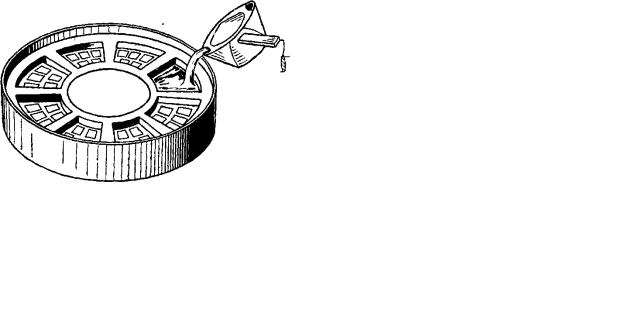
диска или гребенки указывает на насадку с перекосом. Для устранения перекоса необходимо снять диск или гребенку, проверить, имеется ли необходимый натяг (разница в диаметрах расточки диска и шейки вала в месте посадки), проверить состояние шпонки и шпоночной канавки, после чего произвести повторную посадку диска.
При небольшой разнице, указываемой индикаторами, при наличии небольшой конусности, что проверяется по величине зазора между линейкой и поверхностью упорного диска (рис 18.9,б), а также при наличии на упорном диске рисок и неглубоких забоин можно ограничиться шабровкой и шлифовкой рабочей поверхности диска, не снимая его с вала.
Шабровку производят по краске с шабровочной плитой (чугунный притир), выполненной в виде кольца толщиной 15—20 мм с вырезом в его нижней части; внешний диаметр притира должен быть больше диаметра упорного диска, а его внутренний диаметр выполняется по диаметру втулки упорного подшипника (рис. 18.10), которая является базой для притира. Шабровка упорного диска ведется по следам краски до получения равномерного распределения краски по всей торцевой поверхности диска и получения осевого биения (биение торца диска) не более 0,02 мм, которое проверяется двумя индикаторами.
Рисунок 18.10. Чугунный притир для шабровки и шлифовки упорного диска. 1-упорный диск, 2—притир, 3—рукоятки для вращения притира, 4- рычаги для прижатия притира к диску.
По окончании шабровки рабочая поверхность притира покрывается тонким слоем наждачного порошка (№ 250—300), порошка карбида бора № 180—200, или пасты ГОИ, разведенной на керосине. После прижатия притира к упорному диску притир поворачивается на 30— 50° в ту и другую сторону; в процессе шлифования периодически ротор поворачивается на 90°, 180° и т.д., что обеспечивает равномерность шлифовки всей поверхности диска. Шлифовка заканчивается после получения чистой и гладкой поверхности упорного диска.
При наличии глубоких рисок, шероховатости и осевого биения, превышающего 0,07— 0,08 мм, необходимо предварительно проточить диск, а затем шабрить его и шлифовать. Для проточки ротор, лежащий на опорных подшипниках, распирается против осевых перемещений, после чего при его вращении производится проточка и последующая шлифовка упорного диска или гребенок.
18.5. ПЕРЕЗАЛИВКА СЕГМЕНТОВ УПОРНОГО ПОДШИПНИКА.
Толщина слоя заливки баббита на сегментах должна быть меньше минимального осевого зазора между рабочими и направляющими лопатками; благодаря этому в случае выплавления баббита из сегментов во время работы турбины упорный диск вала упрется в основное тело сегмента (бронза или сталь) и соприкосновения в лопаточном аппарате при этом не произойдет. Если толщина баббитовой заливки будет больше, то выплавление баббита на сегментах вызовет задевание в проточной части и поломку лопаточного аппарата турбины. Исходя из указанного толщина баббитовой заливки сегментов, определяемая допустимым сдвигом ротора в осевом направлении, составляет примерно 1,5 мм.
При необходимости перезаливки старый баббит должен быть полностью выплавлен из сегментов без оставления его остатков в выточках и углублениях.
Перезаливка сегментов должна производиться при соблюдении всех условий, указанных для перезаливки вкладышей опорных подшипников. Успех перезаливки целиком зависит от правильной подготовки поверхности сегментов (очистка, обезжиривание, протравление и лужение), от соблюдения правильных температур заливаемого сегмента и расплавленного баббита, а также и от качества заливки.
Заливка производится после укладки сегментов в форму, выполненную из кровельного железа (рис. 18.11), с высотой, определяемой толщиной тела сегмента, плюс необходимая толщина заливки сегмента и плюс припуск на обработку и на отсутствие усадочных раковин. Этот припуск для сегментов должен быть не меньше
12—15 мм.
Рисунок 18.11. Заливка сегментов упорных подшипников баббитом.
Форма заполняется смесью из 80% обыкновенной тонкоразмолотой печной глины (по весу) и 20% волокнистого асбеста, разведенной водой до тестообразного состояния. В эту массу вдавливаются сегменты, после чего форма тщательно просушивается и перед заливкой баббитом подогревается до 300—350° С.
После заливки баббитом имеющим температуру 400—420° С, целесообразно для удаления газов и уплотнения баббита встряхнуть несколько
235
раз форму и, накрыв ее сверху асбестовым листом, охлаждать снизу.
После остывания баббит должен плотно пристать к телу сегмента, что является основным условием его удовлетворительной работы. Проверка плотности приставания баббитовой заливки к телу сегмента может быть произведена способами, указанными в § 17.2 или, что более надежно, ультразвуком (§ 17.4).
Качество заливки должно проверяться также после механической обработки, производимой после установки сегментов на станке по индикатору в специально изготовленную оправку. После обработки, производимой по чертежным размерам с припуском на шабровку 0,05—0,06 мм, на поверхности баббитовой заливки не должно быть посторонних включений, раковин и пористости; заливка должна иметь тусклосеребристый цвет без желтизны и желтых пятен, и излом—однородное и мелкозернистое строение.
После шабровки сегментов, производимой по плите и краске с проверкой индикатором для обеспечения их одинаковой толщины, равномерного прилегания к упорному диску и создания необходимого осевого разбега производится закругление кромок баббита. Закругление особенно необходимо со стороны входа масла на сегмент, так как острые кромки создают затруднения для прохода масла между трущимися поверхностями; обычно радиус округления на входе масла выдерживается в пределах 2—4 мм.
18.6. СБОРКА УПОРНОГО ПОДШИПНИКА.
При сборке необходимо обратить внимание на маркировку сегментов, чтобы обеспечить правильное положение сегментов по отношению к направлению вращения упорного диска и правильную сборку сегментов правого и левого вращения, в особенности, когда они имеют одинаковые размеры и отличаются только положением скосов и линий качания.
При полностью собранном упорном подшипнике и насухо вытертых упорном диске и сегментах необходимо, как это указано в § 18.3, проверить по натирам совместное прилегание рабочих поверхностей упорного диска и сегментов при вращении диска и его отжатии как по ходу пара, так и в противоположную сторону. Только такая тщательная проверка может обеспечить безусловное и полное прилегание упорных
сегментов к упорному диску, что необходимо для равномерного распределения осевых усилий по всей рабочей поверхности сегментов; несоблюдение этого условия вызовет во время работы турбины перегрузку отдельных сегментов, выплавление баббита и аварию турбины, связанную со сдвигом ротора.
Необходимо проверить состояние и плотность пригонки контрольных шпилек, обеспечивающих точность взаимного соединения верхней крышки или вкладыша с корпусом подшипника; при свободном входе шпилек в свои отверстия, что может привести к перемещению крышки или вкладыша во время работы турбины, шпильки подлежат замене. Одновременно с этой проверкой производится проверка плотности прилегания разъема верхней крышки к корпусу подшипника. При свободной укладке крышки или вкладыша на свое место с установленными контрольными шпильками и легкой затяжке болтами никаких зазоров в их разъеме, проверяемом щупом, быть не должно.
При сборке необходимо соблюдать меры предосторожности против загрязнений, проверять все детали, масляные каналы и отверстия в отсутствии каких-либо повреждений, обеспечить установку всех деталей в соответствии с их маркировкой и принимать необходимые меры против самоотвинчивания и изменения их положения в процессе работы турбоагрегата.
При первом пуске турбины после ремонта должно быть установлено тщательное наблюдение за работой упорного подшипника. Это наблюдение должно вестись прослушиванием, наощупь, по температуре рабочей поверхности упорных сегментов. Контроль за температурой баббитового слоя выходной кромки каждого упорного сегмента, замеряемой термопарами или термометрами сопротивления, предусмотрен почти на всех современных турбинах (К-100-190,
К-150-130, К-200-130 и др.).
После небольшого периода работы (8-10 ч) желательно, а после перезаливки сегментов обязательно турбину остановить, вскрыть упорный подшипник, проверить его состояние и, в случае надобности, подшабрить сегменты.
При ненормальной работе упорного подшипника (нагрев, вибрация и пр.) следует остановить турбину для вскрытия и осмотра упорного подшипника.
19. РЕГУЛИРОВАНИЕ.
19.1. ТРЕБОВАНИЯ, ПРЕДЪЯВЛЯЕМЫЕ К СИСТЕМЕ РЕГУЛИРОВАНИЯ.
Система регулирования в основном служит для автоматического поддержания соответствия между мощностью, развиваемой паром в турбине, и мощностью, отдаваемой электрическим генератором в сеть, при постоянном числе оборотов. В турбинах различных назначений и конструкций к
числу регулируемых параметров относятся также: давление отбираемого пара (конденсационные турбины с отбором), давление отработанного пара (турбины с противодавлением) и др.
От четкого и правильного процесса регулирования зависит надежность и экономичность работы турбины. В практике эксплуатации нередки случаи, когда разладка и дефекты в системе регулирования, вызванные небрежно проведенным ремонтом, приводили к тяжелым авариям с
236
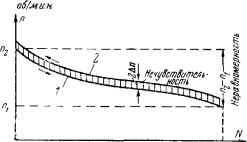
турбоагрегатами вплоть до их полного выхода из строя.
Важнейшими требованиями, которым должны удовлетворять системы регулирования, являются: быстродействие, устойчивое поддержание числа оборотов при изменениях режима от холостого хода до полной нагрузки и удержание оборотов при мгновенных и полных сбросах нагрузки; вызываемое сбросами нагрузки кратковременное повышение числа оборотов не должно вызывать срабатывания предохранительного выключателя турбины.
При параллельной работе турбоагрегата на общую сеть дефекты в работе регулирования в течение длительного времени могут не ощущаться вследствие того, что частота сети, определяющая число оборотов агрегата, поддерживает их на нормальном уровне. Эти дефекты сказываются: при холостом ходе турбины, когда регулирование не держит нормальных оборотов турбины; при сбросах нагрузки, когда надежность работы турбины обеспечивается только исправным действием предохранительного выключателя; в эксплуатации, когда ненормальности в работе регулирования приводят к колебаниям нагрузки, к потерям, связанным с вредным дросселированием, и др.
Сказанное определяет необходимость тщательного осмотра, ремонта, сборки и наладки высококвалифицированным персоналом системы регулирования при каждом ее ремонте.
Для наладки и эксплуатации системы регулирования большое практическое значение имеют специальные испытания, производимые до и после капитального ремонта, для получения данных и построения статической характеристики регулирования. Если капитальные ремонты турбин производятся не ежегодно, снятие статических характеристик регулирования должно производиться не менее одного раза в год во время текущих ремонтов.
Статическая характеристика изображается в виде двух параллельных кривых 1 и 2 (рис. 19.1), которые показывают, как при нормальных условиях работы турбоагрегата на самостоятельную электрическую сеть (номинальные параметры пара и нормальная тепловая схема) и при неизменном положении синхронизатора изменяется число оборотов при плавном изменении нагрузки.
Рисунок 19.1. Статическая характеристика регулирования скорости. 1-уменьшение числа оборотов при увеличении нагрузки, 2 — повышение числа оборотов при снижении нагрузки.
Устойчивая работа регулирования во всем диапазоне изменения нагрузки обеспечивается, если статическая характеристика имеет общий постоянный уклон, не имеет горизонтальных участков и каждому числу оборотов отвечает только одна возможная нагрузка. Наличие на статической характеристике горизонтального участка вызовет неустойчивую работу турбины, так как нагрузка такой турбины при малейшем изменении часто ты в сети будет произвольно меняться на величину, соответствующую длине горизонтального участка характеристики. Из этих кривых видно, что максимальной нагрузке турбины, при которой имеет место максимальный пропуск пара (наибольшее открытие паровпускных клапанов), соответствует наименьшее число оборотов n1 и, наоборот, наибольшее число оборотов n2 соответствует холостому ходу.
Разность между наибольшим и наименьшим числом оборотов, отнесенная к номинальному числу оборотов nном и выраженная в процентах, называется степенью неравномерности системы регулирования: δ=(n2-n1)/nном.
В современных турбинах неравномерность регулирования должна быть в пределах 4±1%. Уменьшение неравномерности ниже 3% ведет к уменьшению разгона турбоагрегата при сбросе нагрузки, но вызывает неустойчивую работу системы регулирования; повышение неравномерности выше 5% ведет к увеличению динамического заброса оборотов при сбросе полной нагрузки.
Кривые 1 и 2 (рис. 19.1) снимаются при одних и тех же условиях работы турбоагрегата, но кривая 1 снимается при уменьшении оборотов, а кривая 2—при повышении. При снятии кривых необходимо следить, чтобы изменение числа оборотов происходило в одном направлении, так как даже кратковременное увеличение оборотов при снятии кривой 1 или уменьшение оборотов при снятии кривой 2, не даст возможности правильно построить эти кривые.
Несовпадение кривой, снятой при уменьшении оборотов, с кривой, снятой при повышении оборотов, определяет степень нечувствительности регулирования ε=2 n/n.
Процесс регулирования протекает удовлетворительно, если степень нечувствительности для систем регулирования скорости с рычажными связями не превышает 0,5% от номинального числа оборотов; для систем гидродинамического регулирования степень нечувствительности должна быть не более 0,3%.
Увеличение нечувствительности ухудшает качество работы регулирования, так как вызывает отставание действия регулирования (опоздание перемещения сервомоторов и регулирующих клапанов при изменении числа оборотов); это отставание вызывается наличием трения, заедания, износа, перекосов и искривлений в деталях регулирования (в сервомоторах, золотниках, штоках, передаточно-рычажных соединениях и др.) и возникновением связанных с этими дефектами слабины, игры и мертвых ходов.
237
Внекоторых случаях большая нечувствительность может при работе на общую сеть приводить к качаниям (сбросам или набросам) нагрузки, а при работе на изолированную сеть к колебаниям числа оборотов. Причину плохого подчинения турбоагрегата управлению синхронизатором также в первую очередь следует искать
вувеличении нечувствительности, которая может накапливаться в процессе эксплуатации в результате заеданий, износа и слабины шарнирных соединений регулятора, рычажной передачи от регулятора к золотнику, искривления штоков клапанов, коробления втулок штоков, попадания окалины и т.д.
Таким образом, если по полученной при указанных испытаниях статической характеристике регулирования будет установлена неравномерность выше 5% или ниже 3% и нечувствительность выше 0,5%, необходимо произвести ремонт и наладочные работы по системе регулирования.
Ремонт и настройка регулирования имеет целью обеспечить такое взаимодействие всех его элементов, при котором турбоагрегат может работать нормально как на изолированную электросеть, так и при параллельной работе с другими турбоагрегатами на общую электросеть при любом режиме нагрузки, задаваемом эксплуатацией и предусмотренном заводом-изготовителем.
Всистему регулирования входят: регулятор скорости, сервомоторы, золотники, обратная связь, передаточные устройства регулятора скорости, золотников, сервомоторов и регулирующих клапанов.
Вместо систем регулирования с механическими рычажными связями, шарнирными соединениями и главным объемным масляным насосом (шестеренчатым или винтовым), связанным червячной или зубчатой передачей с передним концом вала турбины, в современных турбоагрегатах применяются главным образом системы гидродинамического регулирования.
Вместо механических рычажных связей эти системы имеют гидравлические связи, а вместо объемных масляных насосов—центробежные масляные насосы, непосредственно насаженные на передний конец вала турбины или на отдельный вал, соединенный с передним концом вала турбины гибкой муфтой или шлицевым валиком; при этом применяется или один центробежный масляный насос, который, наряду с подачей масла в систему смазки подшипников, выполняет роль импульсного органа по изменению числа оборотов гидродинамического регулятора скорости, или два центробежных насоса, из которых один обеспечивает систему смазки, а другой является только импульсным датчиком системы регулирования.
Большое разнообразие систем регулирования у турбин различных заводов и различных назначений требует индивидуального подхода в решении вопросов ремонта и проверки отдельных деталей каждой системы регулирования.
Согласно ПТЭ система регулирования турбины должна удовлетворять следующим требованиям:
1)устойчиво удерживать турбину на холостом ходу при полностью открытых запорных задвижках;
2)обеспечивать при изменении нагрузки плавное (без толчков) перемещение регулирующих клапанов;
3)обеспечивать плотное закрытие клапанов автоматического затвора (стопорных клапанов свежего пара); у турбин с давлением пара 90 ат и выше плотность закрытия этих клапанов может быть признана удовлетворительной, если при их полном закрытии установившаяся скорость вращения ротора не превышает 50% от номинального значения.
19.2. РЕГУЛЯТОР СКОРОСТИ.
В турбинах, где в качестве регуляторов скорости применяются центробежные регуляторы, каждому положению муфты регулятора, определяющему открытие паровпускных клапанов и соответственно нагрузку турбины, соответствует определенное число оборотов.
При разборке регулятора скорости необходимо обратить внимание на удаление вала регулятора из корпуса до вывода из зацепления червячной передачи, так как нередко небрежное удаление приводит к повреждениям отдельных частей и деталей регулирования.
Обычными неисправностями регулятора скорости являются: заедание или разработка в шарнирных соединениях и рычажных передачах от грузов к муфте регулятора, заедание грузов, заедание и ослабление главных пружин грузов регулятора и дополнительных пружин синхронизатора, разработка, и изгиб шпинделя, стягивающего грузы регулятора, разработка в направляющих и опорных катках, пластинках, призмах и опорных ножах грузов регулятора, излом опорных призм и ножей, недостаточная смазка деталей регулятора и др. Такого же рода дефекты в виде разработки шарнирных соединений и деформации тяг наблюдаются и в передаточнорычажных устройствах между муфтой регулятора скорости, золотником, шайбой обратной связи, сервомоторами и регулирующими клапанами.
Наличие заеданий, задеваний, разработки, перекосов и изломов в отдельных деталях регулятора скорости обычно нетрудно обнаружить по следам касаний, натиров и выработок и при тщательном осмотре регулятора после разборки и замерах для определения величины и характера дефекта. Эти дефекты должны устраняться правильной выверкой зазоров в соприкасающихся между собой и взаимно перемещающихся деталях, а также пригонкой или заменой соответствующих деталей; последнее главным образом, относится к шпинделям шарнирных соединений, к шпинделю стягивающему грузы регулятора, к каткам, опорным пластинкам, призмам и опорным ножам грузов.
238
Шарнирные соединения должны быть подогнаны без какой-либо игры, но недопустима и слишком плотная пригонка, так как это приведет к недопустимому значительному повышению трения. Искривления тяг должны быть устранены правкой или, при значительной деформации, тяги должны быть заменены новыми.
При устранении задеваний пружин центробежного регулятора и пружины синхронизатора необходимо учитывать, что диаметр пружин регулятора при их растяжении уменьшается, а диаметр пружины синхронизатора при ее сжатии увеличивается; кроме того, при работе пружин могут иметь место их искривления; в связи с указанным зазоры между пружинами и деталями, с которыми они могут соприкасаться в работе, должны быть установлены не менее 1 мм.
При сборке регулятора и всей системы регулирования все детали следует собирать в последовательности, обратной тому порядку, который принят при разборке, пользуясь для этого маркировкой деталей. Для предотвращения самоотвинчивания и обеспечения надежности соединении и крепления деталей особое внимание должно уделяться установке контргаек, стопорных шайб, шплинтов и других средств крепления и стопорения. Не следует производить перемену местами даже одинаковых деталей, так как это может вызвать ухудшение работы; например, перемена местами грузов может вызвать разбалансировку и вибрацию регулятора.
Между муфтой и валом регулятора должно быть проверено наличие зазора 0,05—0,1 мм на диаметр; зазор в подшипнике регуляторного вала, принимаемый в пределах 0,0012-0,0018 от диаметра вала, должен обеспечивать свободное проворачивание вала.
Отсутствие мертвых ходов и заеданий проверяется при сборке регулятора, до установки главных пружин, путем передвижения вручную различных частей одной относительно другой в нужном направлении и наблюдения за свободным их перемещением из любого положения без игры.
При сборке обязательно должны быть проверены: отсутствие кривизны вала центробежного регулятора и правильность его центровки с валом масляного насоса (неточность центровки не должна превышать 0,02 мм), величина осевого разбега вала регулятора, которая не должна превышать 0,15—0,25 мм, правильное перекрытие золотниками окон втулок (перекрыша золотников), надлежащее крепление стяжек между пружинами регулятора и др.
Сборка регулятора и передаточнорычажных соединений может считаться удовлетворительной, если при неизменном положении муфты регулятора мертвый ход сервомотора не превышает 3% от максимального его хода. Это перемещение 'проверяется на стоящей собранной после ремонта турбине при пущенном вспомогательном масляном насосе простым поднятием вручную золотника, что вызовет перемещение сервомотора на величину имеющегося мертвого хода. При сборке необходимо проверить все мас-
ляные каналы и тщательно продуть трубки подвода и спуска масла для обеспечения хорошей смазки деталей регулятора.
Установка и затяжка главных пружин регулятора должна быть произведена по размеру, замеренному до ремонта, с проверкой возможности полного рабочего хода муфты регулятора. Если в процессе длительной эксплуатации из-за ослабления пружины требуют затяжки, значительно превышающей первоначальную, их необходимо заменить новыми с предварительной проверкой их характеристик (§ 4/4).
При замене пружин следует иметь в виду, что жесткие пружины могут вызвать повышение степени неравномерности регулирования. Слишком слабые пружины могут потребовать такой затяжки, при которой витки пружины сомкнутся, что недопустимо, так как это вызовет ограничение рабочего хода муфты при нормальном разбеге грузов; по этим же соображениям не рекомендуется подкладывать шайбы под пружины для увеличения их натяга. Недопустимость взаимного касания витков в равной степени относится и к дополнительной пружине синхронизатора, так как это также может повести к ограничению хода муфты регулятора.
После сборки должен быть проверен максимальный ход муфты регулятора, зависящий от положения ограничительных упоров перемещения муфты или грузов регулятора. Этот ход регулятора должен быть больше рабочего, необходимого для принятия турбиной нагрузки от холостого хода до полной.
Между положением муфты, при котором достигается полное закрытие клапанов, и верхним ограничителем хода муфты должен оставаться запас, который должен составлять 0,25-0,3 рабочего хода муфты; такой запас необходим для того, чтобы в случае сброса нагрузки муфта имела возможность подняться выше положения, которое соответствует полному закрытию сервомотора; это будет способствовать ускорению закрытия регулирующих клапанов, а, следовательно, уменьшит заброс оборотов турбины.
Если при проверке перемещения сервомотора при положении синхронизатора, соответствующем максимальному числу оборотов, окажется, что сервомотор полностью закроет клапаны в момент, когда муфта регулятора почти достигнет верхнего ограничителя, это покажет, что запас хода муфты меньше 0,25 рабочего хода; в этом случае следует изменить длину подвески золотника или длину передаточно-рычажной тяги так, чтобы сервомотор закрыл клапаны при более низком положении муфты регулятора, что и дает необходимый запас хода муфты.
В гидродинамических системах регулирования, не имеющих центробежных регуляторов и большого количества сложных подвижных элементов, износ и неправильная выверка которых приводят к пульсациям и аварийным простоям турбин, также возможны пульсации, вызывающие неустойчивую работу золотников и связанных с ними сервомоторов. Эти пульсации могут вызы-
239
ваться скоплением воздуха в сервомоторе, пульсирующим давлением масла, создаваемым центробежным масляным насосом в случае значительного содержания воздуха в масле, и др. Наряду с мероприятиями по эффективному удалению воздуха из масла и обеспечением устойчивого давления масла, создаваемого центробежным насосом, необходимо в этих случаях проверить правильность перекрыш у золотников.
19.3. КЛАПАНЫ АВТОМАТИЧЕСКОГО ЗАТВОРА, РЕГУЛИРУЮЩИЕ И ЗАЩИТНЫЕ КЛАПАНЫ.
Назначение клапанов автоматического затвора (стопорных клапанов)—в аварийных случаях при ручном или автоматическом воздействии предохранительных выключателей мгновенно прекращать доступ пара в турбину путем отключения паропроводов свежего пара.
Назначение защитных клапанов—в аварийных случаях при ручном или автоматическом воздействии предохранительных выключателей и закрытии клапанов автоматического затвора, отключать паропроводы промежуточного перегрева для закрытия доступа пара в цилиндр среднего давления и предотвращения тем самым разгона турбины паром из промперегрева.
Назначение регулирующих клапанов — включать и отключать группы сопл и дросселировать пар при изменениях нагрузки.
Ко всем указанным клапанам предъявляются следующие требования: 1) быстродействие и высокая плотность; в закрытом положении клапан должен надежно закрывать доступ пара в турбину; 2) наименьшие потери от дросселирования при полностью открытом клапане; 3) механическая надежность клапана, которая обеспечивает работу деталей без износа и тем более без поломок.
Впроцессе разборки колонок, регулирующих клапанов, кулачкового pacnpеделительного устройства, рычагов, вертикальных тяг, соединяющих колонки боковых регулирующих клапанов ЦВД и ЦСД с кулачковым распределительным устройством, и всех других элементов парораспределения (рис 19.2) должны быть зафиксированы состояние, взаимное положение, зазоры, размеры и нанесены, при отсутствии, метки, необходимые для обеспечения после ремонта быстрой и правильной сборки деталей. Эти данные необходимы также для правильной установки парораспределения, при котором поворот кулачкового вала ведет к правильной последовательности открытия клапанов с соответствующей перекрышей открытия последующего клапана по отношению к полному открытию предыдущего клапана,
Вэксплуатации нарушения плотности клапанов вызываются такими дефектами, как разъедание клапанов паром, раковины на седлах и уплотняющих кромках клапанов, заедание клапанов
на седлах и штоков во втулках, коробление клапанов и др. Нарушение правильности открытия и закрытия клапанов может быть вызвано неправильностью регулировки тяг (в турбине К-200-130 зазор между роликом и окружностью наименьшего радиуса кулака при холодном состоянии и закрытых клапанах должен быть равен 5±0,2 мм) и соединения штока клапана с колонкой (зазор в этом соединении между шайбой и прижимным кольцом должен быть равен
0,05 мм).
Нарушение правильной работы клапанов может быть вызвано также неправильным методом ремонта или неопытностью персонала, применяющего, например, для увеличения радиальных зазоров, необходимых для предупреждения заедания клапанов на седлах, расточку клапанов выше допускаемой. Такое увеличение радиальных зазоров между посадочными поверхностями клапанов и седел, при наличии свободы перемещений клапана на штоке, вызывает боковые смещения клапанов, вследствие чего происходит неправильная их посадка на седла.
Достижение плотности клапанов, особенно двухседельных, является достаточно трудной задачей; на решение этой задачи при ремонте следует обратить самое серьезное внимание, так как плотность клапанов имеет решающее значение для быстрой остановки турбины при аварийных режимах. Из-за дефектов регулирующих клапанов и недержания турбиной холостого хода наблюдались неоднократные случаи разгона и разрушения турбин.
Преимуществом двухседельного клапана является значительное уменьшение паровых усилий, действующих на его шток, но сделать двухседельный клапан достаточно плотным в рабо- те—затруднительно; объясняется это сложностью обеспечить одновременное закрытие обеих кромок клапана и надлежащее контактное напряжение, достигаемая притиркой плотность в холодном состоянии нарушается при его нагреве.
В односедельных клапанах не удается осуществить достаточно полное уравновешивание паровых усилий, но, учитывая возможность достижения и поддержания в эксплуатации большой паровой плотности, в турбинах среднего и особенно высокого давления применяются исключительно односедельные регулирующие клапаны.
Плотность клапанов при ремонте достигается притиркой клапанов к седлам, производимой самым мелким наждачным порошком с маслом и пастой ГОИ. Притирку следует производить при установке на место крышек паровых коробок, что обеспечивает большую плотность прилегания посадочных поверхностей клапанов к седлам. Вращение клапанов при притирке обычно производится с помощью хомута, укрепляемого на штоке (рис. 19.3,а); этим хомутом можно производить также и подъем клапана вместо подъема с помощью рыма и восьмерки (рис. 19.3,б).
240