
Книги / Ремонт паровых турбин. Молочек В.А.г
.pdf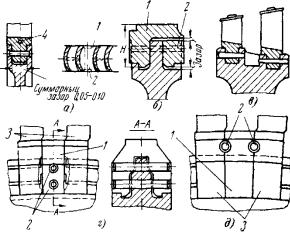
После отрегулирования места под замок производятся точные замеры расклиненного места и по ним изготовляется замковая вставка с припуском в тангенциальном направлении 0,1— 0,15 мм и зазором в осевом направлении 0,05- 0,1 мм в зависимости от размеров лопаток.
При изготовлении производится припиловка замковой вставки по профилям призамковых лопаток или промтел, снятие фасок с верхнего и нижнего торца и выполнение вырезов или канавок согласно чертежу замка. Замковая вставка после смазки тонким слоем ртутной мази устанавливается на место с усилием, в случае заеданий при установке до места замок осторожно выбивается, след заедания на металле замка пришабривается и замок полностью доводится до места на всю глубину посадки. Затем, забивается клин с расчетом полного прилегания расклиненного замка к стенкам замкового колодца, и замок расчеканивается путем начеканки на него металла с обеих половинок замковой вставки (рис. 13.19).
Рисунок 13.31. Замки с креплением хвостов лопаток заклепками. 1-замок, 2 — заклепки, крепящие замок 3
—лопатки смежные с замком, 4 — штифт.
Вконструкциях с Т-образными хвостами ЛМЗ замки крепятся заклепками (рис. 13.31,а), которые проходят через тело замка и обод диска. Такой тип замка удобен для установки и надежен
вэксплуатации. После плотной установки замковой вставки между двумя прилегающими лопатками через имеющееся в щеке диска отверстие, как по кондуктору, сверлится для заклепки отверстие в середине замковой вставки, диаметр сверла берется на 0,1—0,2 мм меньше диаметра отверстия в щеке диска для последующего доведения отверстия до необходимого диаметра разверткой.
Для проверки, действительно ли при сверлении замковой вставки отверстие пройдет через ее середину, необходимо на обод вынести риску, указывающую центр отверстия в щеке диска.
Заклепка по диаметру должна плотно входить в отверстие от легких ударов ручника. После установки на место концы заклепки с обеих сторон обода диска должны быть надежно расчеканены или, в крайнем случае, при невозможности расчеканки из-за близости расстояния между со-
седними дисками, они должны быть надежно раскернены (рис 13.20,в)
Такой же тип крепления с помощью цилиндрических штифтов или заклепок применяется
ипри установке лопаток на гребень диска (рис. 13.31,б); в этом случае отверстие в замковой лопатке или замковой вставке размечается так же, как указано выше, с обязательной и тщательной предварительной проверкой совпадения центра этого отверстия с серединой замковой лопатки или вставки.
Внекоторых конструкциях вместо цилиндрических применяются конусные штифты или заклепки (рис. 13.31,в); в этом случае конусные штифты должны изготовляться с припуском 0,02—0,025 мм на диаметр; установка и расчеканка этих штифтов производится так же, как это указано для закрепления Т-образных лопаток.
Для закрепления лопаток с грибовидными хвостами замок выполняется в виде хвоста лопатки, обработанного соответственно очертаниям обода диска в месте замкового выреза. Этот замок закрепляется на насадных дисках одной или двумя заклепками, пропускаемыми через тело замка
идиска (рис. 13.31,г), а на цельнокованных рото- рах—заклепками, пропускаемыми поверх грибка обода диска, по стыкам замка и соседних околозамковых лопаток (рис 13.31,д). Для крепления по второму способу, при котором диск не имеет сверлении, канавки под заклепки в замке и околозамковых лопаток должны быть выфрезерованы заранее с доведением их до окончательного размера по месту после установки замка.
На рис. 13.32,а показана установка замка с расклиниванием. В этой конструкции две лопатки 1 и 2, примыкающие к замку, имеют в хвостовой части выступы, которые при установке входят под хвосты соседних лопаток 3 и 4. После установки лопаток 1 и 2 и их расклинивания между ними вставляется подкладка 7, стальной клин 6 и на него загоняется подогнанная по месту замковая вставка 5, имеющая посередине в своей нижней части прорезь. Замковая вставка при ее заколачивании раздвигается клином 6, входящим в ее прорезь и заполняет всю выточку паза, расширяющуюся книзу, благодаря чему получается замок, надежно закрепляющий лопатки на диске. В случае необходимости удаление замка может быть произведено только его высверливанием и вырубкой.
Простым и надежным является замок, конструкция которого показана на рис 13.32,б; этот замок применяется в конструкциях, где реактивные лопатки и промтела заводятся в паз путем поворота вдоль паза, а не через замковый колодец. Эти лопатки удерживаются в пазе диска замком, который изготовляется из нормального промтела, разрезанного на три части. По окончании наборки лопаток и их расклинивания между двумя соседними лопатками оставляется пространство, равное ширине промтела; в это пространство вставляются две части 8 и 9 разрезанного промтела, которые входят в выточки обода и между ними плотно загоняется клин 10. Для ис-
171

ключения возможности выхода клина из паза на него производится расчеканка верхних концов вставок 8 и 9.
Для закрепления лопаток ступеней скорости на двухступенчатом диске применяется замок, состоящий из двух вставок, расширяющихся книзу (рис. 13.33,а); вставки разжимаются специальной шайбой. Замок устанавливается на место после окончательной пригонки призамковых лопаток; шайба закрепляется на диске винтом, который в свою очередь после окончательной затяжки тщательно раскернивается. Еще одной разновидностью таких замков является конструкция, изображенная на рис. 13.33,б, где закрепление замковой цельной вставки производится шайбой, накладываемой на нее и привертываемой к ободу диска винтом. Этот тип замка применяется не только для крепления лопаток в ступенях скорости, но и для крепления лопаток в ступенях давления барабанных роторов.
Рисунок 13.32. Установка замков с расклинкой.
Лопатки с торцовыми елочными радиусными хвостами (рис. 13.34) и осевой системой крепления в пазах диска применяются ХТГЗ для последних ступеней мощных турбин. Преимуществом этих хвостов является возможность легкой смены отдельных лопаток и высокая точность их изготовления, поэтому никаких припиловочных и пригоночных работ при переоблопачивании не требуется и не допускается. Путем осевого ввода каждая лопатка предварительно устанавливается на диск в свой паз без стопорных пластин; после расклинивания лопаток к периферии производится проверка их положения в тангенциальном и аксиальном направлениях и замеры зазоров между лопаткой и дном паза; по этим зазорам производится припиловка и шлифовка толщины стопорных пластин. После выемки лопаток и тщательной очистки хвостов лопаток и
пазов диска лопатки набираются на диск вместе со своими стопорными пластинами, концы которых затем аккуратно, во избежание появления трещин, загибаются по торцу обода диска и стопорят лопатки в осевом направлении.
Лопатки реактивных турбин с зубчиковыми хвостами крепятся на роторе с помощью промтел (рис. 13.35,а) и заводятся в паз ротора через замковый колодец, который образуется путем срезания зубчиков с одной стороны паза и обработки срезанной поверхности под клин (рис. 13.35,б). После набора всех лопаток в замковый колодец вставляется замок, состоящий из трех частей: вставки 1, имеющей зубчики соответственно зубчикам паза, вставки 2, имеющей клиновую поверхность соответственно клиновой поверхности замкового колодца и проставки 3, которая изготовляется из мягкой стали, разрезается для облегчения осадки на две-три части и вставляется между вставками 1 и 2. При забивании металл проставки 3 заполняет мелкие зубчики, выполненные на внутренних поверхностях вставок 1 и 2, и, кроме того, для исключения возможности выхода из сцепления проставки 3 на нее сверху начеканивается металл вставок 1 и 2.
Рисунок 13.33. Крепление замков винтами. 1-замковые вставки; 2 — шайбы.
После закрепления и расчеканки замка производится окончательная правка лопаток, под которой понимается исправление положения лопаток в тангенциальном и осевом направлениях; правка производится вручную с помощью специальных оправок (см. рис. 13.28).
Облопачивание цилиндра турбины.
Предварительная проверка, подготовка лопаток и других лопаточных материалов, приспособлений, а также пазов цилиндра турбины, подлежащих облопачиванию, производится аналогично указанному для рабочих лопаток.
Наборка лопаток в цилиндре производится по ходу вращения ротора после установки в паз замка (концевого тела) у плоскости разъема, к которому плотно пригоняются лопатки и промтела, устанавливаемые спинкой вверх. Выходная кромка последней лопатки, набранной в нижнюю
172
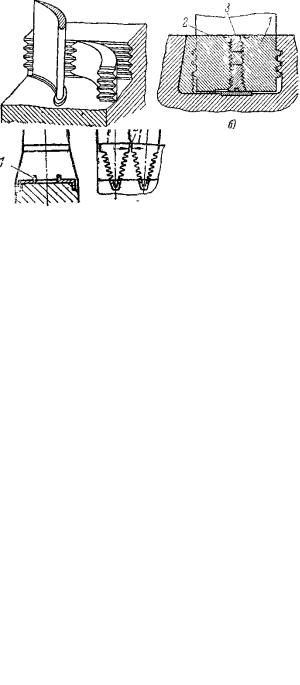
половину цилиндра, должна совпадать с плоскостью разъема цилиндра; в случае несовпадения промежуточные тела, установленные до концевой лопатки, подлежат соответствующей опиловке, с уменьшением шага не больше чем на 5%.
Наборку лопаток следует начинать с последнего ряда, т.е. с наиболее длинных лопаток, последовательно переходя к следующему ряду по окончании предыдущего; такая наборка лопаток облегчает обандаживание и пайку, которые при этом не затруднены наличием последующих рядов.
Установка лопаток контролируется в радиальном направлении шаблоном или сегментом, толщина которого равна расстоянию между переоблопачиваемым и соседним рядом лопаток и высотой, несколько превышающей высоту лопа-
ток (рис. 13.29,а).
Рисунок 13.34. Лопатки с елочным радиусным торцовым хвостом. 1-стопорная пластина, 2 — минимальный зазор 0,1 мм.
В осевом направлении проверка производится линейкой и проверочным валом. Для этой проверки линейка устанавливается на плоскость разъема поперек оси цилиндра так, чтобы ее ребро по обеим сторонам совпадало с кромками паза под концевые лопатки. Если необходимо, крайние лопатки отрихтовываются по линейке с допусками, не превышающими величин, приведенных в табл. 13.1.
После правки указатель проверочного вала, который устанавливается на подшипники, отцентровывается по выверенным концевым лопаткам; при этом должны быть приняты меры против возможного осевого смещения проверочного вала. При вращении проверочного вала в сторону выхода пара проверяется и исправляется осевое положение каждой лопатки относительно указателя вала.
Рисунок 13.35. Лопатки с зубчиковыми хвостами. а— крепление лопаток, б—замок для лопаток.
Наборка лопаток в верхней части цилиндра (в крышке) производится так же, как в нижней. Установку первого концевого тела в этой части цилиндра необходимо производить с расчетом сохранения нормального шага между концевыми лопатками обеих половин цилиндра при его закрытии.
Вторые концевые тела, после окончательной запрессовки лопаток и промтел в пазы, припаиваются к крайним к разъему лопаткам и устанавливаются в пазах верхней и нижней половин
цилиндра так, чтобы прирасклинивании |
было |
|
обеспечено плотное |
крепление всего |
ряда |
лопаток. |
|
|
Выступающие части концевых тел опиливаются заподлицо с плоскостью разъема, для зачеканки с концевых тел снимаются фаски и они зачеканиваются в пазе или стопорятся специальными планками, закрепляемыми впотай на плоскости разъема шурупами.
После окончательной правки лопаток устанавливается, разрезается по пакетам и припаивается к лопаткам бандажная проволока и устанавливается бандажная лента, если это предусмотрено конструкцией. Бандажная лента протачивается с помощью борштанги после пригонки и расклепки шипов.
После окончания работ по облопачиванию производится проверка плотности горизонтальных фланцев разъема цилиндров и, в случае необходимости, их пришабровка для устранения неплотностей, которые могли появиться вследствие раздельного производства работ по облопачиванию верхней и нижней половин цилиндров.
13.10. ПЕРЕОБЛОПАЧИВАНИЕ ЛОПАТКАМИ, ИМЕЮЩИМИ ВИЛЬЧАТЫЙ ХВОСТ.
Переоблопачивание лопатками с вильчатым хвостом для верховой посадки на гребни диска имеет много особенностей по сравнению с указанными выше, эти лопатки не имеют отдельных промежуточных вставок (изготовляются заодно целое с ними) и вместо установки общих замков крепление каждой в отдельности лопатки к гребню диска производится заклепками (рис 13.36), работающими в данном случае на срез. Преимущество этих лопаток—прочное закрепление при доступной сменяемости отдельных износившихся или поврежденных лопаток без разборки всего колеса. Недостатком этого способа крепления лопаток является ограниченное число возможных переоблопачиваний диска; это число может быть значительно увеличено, если при переоблопачиваний вести тщательный контроль за совпадением отверстий, не допуская увеличения диаметра заклепок после каждого переоблопачивания больше чем на 0,2— 0,25 мм.
После снятия лопаток (§ 13.8) и очистки гребней от грязи, ржавчины и забоин необходимо зачистить от грязи и заусениц все отверстия для
173
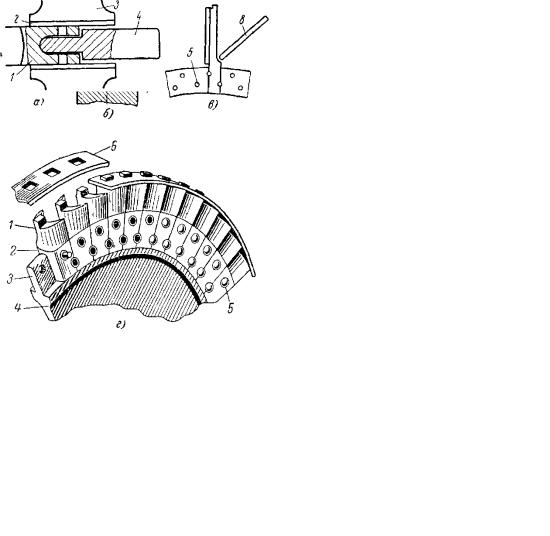
заклепок в гребнях диска. Для проверки отсутствия деформаций, гребни, на которые насаживаются лопатки, в нескольких местах по диаметру диска проверяются по толщине.
Рисунок 13.36. Посадка на диск лопаток с вильчатым хвостом. 1-лопатка, 2—седло хвостовой части, 3—гребень диска, 4 — обод диска, 5-заклепки,
6 — сегмент бандажа, 7 — штифт для крепления лопаток, 8 — оправка.
Перед облопачиванием необходимо произвести проверку посадки каждой лопатки на гребни диска по краске и щупу. Посадка новых лопаток на гребень диска должна быть тугой, при одном гребне диска лопатки должны входить на место от нажима рукой, а при трех, четырех или пяти гребнях диска—под легкими ударами через медную прокладку молотком весом соответственно 300, 500 и 800 г. Если у лопаток с вильчатым хвостом с наружной стороны гребня обнаружена слабина в посадке хвостов, эту слабину можно выбрать путем небольшой безударной осадки на соответствующей по размеру оправке, как указано на рис 13.37. Наличие зазора между щечкой хвоста лопатки и нижней частью гребня диска показывает слишком тугую посадку лопатки (рис
13.24,а).
Как уже указывалось, перед наборкой на диск лопатки должны быть распределены по пакетам с подборкой их по весу, по толщинам хвостов и плотности взаимного прилегания лопаток. Чтобы убедиться в правильности подборки, производится предварительная установка всех лопаток на диск, за исключением последней лопатки, при этом плотность прилегания хвостов лопаток проверяется с помощью щупа, проверяется совпадение отверстий в хвостах лопаток с отверстиями в диске; протяжкой через несколько пакетов лопаток бандажной проволоки проверяется также правильность выполнения отверстий в лопатках под проволоку.
При проверке совпадений отверстий под заклепки следует учитывать, что диаметр отверстий под заклепки в новых лопатках всегда на 1,5—2 мм меньше диаметра отверстий в дисках.
При этой проверке лопатки, имеющие грубые отклонения по посадке (слишком тугая или слишком слабая посадка), смещенные отверстия для заклепок по отношению к отверстиям в дисках и недостаточные по толщине хвосты (малый шаг по хвосту) подлежат замене. Лопатки, имеющие хвосты с припусками по толщине, подлежат соответствующей опиловке. Оиловка производится только по одной поверхности со стороны спинки лопатки—вне зависимости от того, будет ли хвост лопатки с прямым или полукруглым профилем. Зазоры между двумя соседними лопатками в местах соприкосновения не допускаются, поэтому припиловка производится с проверкой по краске и щупом; припиловку лопаток с прямым профилем следует производить по плите.
Пригонка и припиловка боковых отшлифованных поверхностей хвостов лопаток, являющихся базовыми, не допускается, так как при этом нарушаются размеры и чистота поверхности этих плоскостей, а также снижается качество посадки лопаток на диск и искажается качество сопряжения между поверхностями лопаток и гребнями диска. После указанной предварительной подгонки пакеты и лопатки в них нумеруются порядковыми номерами. Крайние в пакете лопатки закрепляются на диске на временных справочных конусных заклепках и между ними вставляются все остальные лопатки данного пакета.
Рисунок 13.37. Правка вильчатого хвостовика лопатки на оправке. 1-лопатка, 2-медная прокладка, 3-тиски, 4-оправка.
Лопатки должны плотно прилегать одна к другой в тангенциальном направлении и правильно без какой бы то ни было слабины посажены на гребни диска; лопатки должны иметь строго радиальное направление и не должны выступать по оси диска. Качество пригонки лопаток на гребне проверяется щупом; в верхней точке седла хвостовой части (рис. 13.36,а) зазора не должно быть, а зазор между хвостом и выступом диска должен быть выдержан в пределах 0,1— 0,15 мм. Такая пригонка дает уверенность в полной посадке лопаток на гребень диска, а не на его обод. Наличие выступающих лопаток по оси проверяется линейкой, прикладываемой к входной и выходной кромкам лопаток.
При наборке лопаток, хвост которых закрыт гребнями диска, в начале облопачивания на гребень диска с помощью старых заклепок закрепляются две старые лопатки, имеющие по толщине хвосты с меньшим шагом; у первой лопатки
174
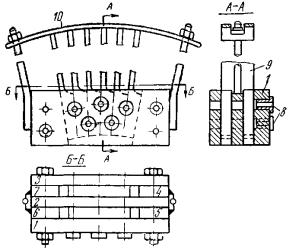
заклепка забивается легкими ударами ручника в верхнее отверстие, а между лопатками — в нижнее отверстие.
После выверки шаблоном тангенциального положения этих лопаток набираются несколько пакетов новых лопаток в соответствии с их порядковой нумерацией, установленной при предварительной проверке. При наборке лопаток производится одновременно контроль за плотным прилеганием хвостов соседних лопаток, за правильным радиальным и осевым положением лопаток, за концентричным положением отверстий в лопатках и диске и в случае необходимости производится соответствующая их подгонка.
Для обеспечения необходимого натяга между лопатками в тангенциальном направлении через каждые пять-шесть лопаток одна набираемая лопатка подгоняется так, чтобы она сидела на гребне диска с зазором 0,5 мм по отношению к вершине гребня. В дальнейшем по окончании наборки при полной осадке этих выступающих лопаток выбирается указанный зазор и уплотняется прилегание хвостов соседних лопаток.
По окончании проверки посадки лопаток в осевом и тангенциальном направлениях острой чертилкой по отверстию в диске намечаются риски на двух соседних лопатках, показывающие перекрытие их замковых отверстий. После снятия этих лопаток отверстия в них распиливаются круглым напильником по отметкам от чертилки и лопатки снова устанавливаются на диск для проверки концентричности отверстий под заклепки в диске и в лопатках. По достижении этого между лопатками в верхнее отверстие устанавливается временная заклепка.
Указанным путем производится наборка лопаток по всему диску с установкой через каждые восемь-десять лопаток временных заклепок. В конце наборки две старые лопатки, установленные первыми, удаляются и вместо них подгоняются последними две новые лопатки с установкой временной заклепки в верхнее отверстие.
Убедившись, что лопатки набраны правильно, производят разметку отверстий во всех лопатках для их рассверловки концентрично отверстиям в диске Рассверловка отверстий в лопатках, набранных на отдельном снятом диске, может производиться электродрелью, а их доведение до надлежащих размеров—разверткой с воротком.
Рассверловка отверстий в лопатках, набранных на дисках собранного ротора, по характеру самой работы и по необходимой точности представляет большие трудности, особенно учитывая, что полное отверстие образуется из двух полуотверстий на двух смежных лопатках
Разделка отверстий в хвостах лопаток производится по нанесенным отметкам круглыми напильниками вручную или для повышения точности и ускорения производства работ разметкой и рассверловкой по кондуктору, что позволяет рассверливать отверстия в лопатках пакетами.
Имеется значительное количество различных конструкций кондукторов для сверловки ука-
занных отверстий. Одной из таких конструкций является кондуктор, который служит для сверления отверстий в пакете лопаток с расположением хвостов снаружи гребня (рис 13.39). Этот кондуктор состоит из двух основных планок, одной промежуточной планки и четырех концевых планок; концевые планки имеют скосы и заклинивают вставляемый пакет. В зависимости от количества гребней количество промежуточных планок соответственно увеличивается. Основная планка 1 точно фиксируется в кондукторе и имеет отверстия с направляющими втулками для сверла, эти отверстия, имеющие диаметр на 0,2 мм меньше отверстий в гребне диска, должны быть расположены в полном соответствии с расположением отверстий для заклепок в диске.
При сверловке отверстий по их разметке планка с направляющими втулками в кондукторе должна соответственно перемещаться; такая сверловка дает более надежные результаты, так как во многих случаях шаг отверстий для заклепок на диске неодинаков. Вообще в связи с тем, что расположение отверстий и диаметры дисков для различных ступеней не совпадают, обычно кондуктор пригоден для сверления отверстий в хвостах лопаток одной какой-либо ступени. Поэтому, необходимо изготовлять кондукторы на месте в соответствии с расположением отверстий в гребнях диска. Использование кондукторов для сверления значительно упрощает разделку отверстий, особенно в лопатках с полукруглым хвостом, требующим точного сочленения хвостов соседних лопаток.
По окончании разделки отверстий, при которой должна быть достигнута их концентричность с отверстиями в диске, лопатки вновь набираются с полной посадкой на гребень диска для окончательного развертывания отверстий и крепления лопаток постоянными заклепками. Для этой цели вначале проходят набором разверток верхние отверстия двух пар лопаток, являющихся крайними лопатками пакета и расположенных между временными заклепками.
Рисунок 13.39. Кондуктор для пакета лопаток. 1, 3— основные планки, 2 — промежуточная планка,
4 5, 6, 7 — концевые планки, 8 — планка с направляю-
175
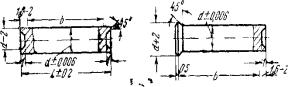
щими втулками для сверла, 9 — лопатка, 10 — хомут для крепления лопаток.
Для развертывания отверстий необходимо заранее подготовить такой набор разверток, который давал бы возможность развертывать отверстия с постепенным увеличением диаметра развертки через 0,1 мм. Если, например, требуется развернуть отверстие с диаметром 10,0 мм до диаметра 10,5 мм, то необходимо иметь развертки с диаметром 10,0; 10,1; 10,2; 10,3; 10,4 и 10,5 мм.
После развертывания отверстий до диаметра, равного диаметру новой заклепки, в них устанавливаются постоянные заклепки; затем производится развертывание верхних отверстий и установка постоянных заклепок в средних лопатках, расположенных между лопатками уже укрепленными постоянными заклепками. После укрепления всех лопаток между этими постоянными заклепками приступают к креплению следующего пакета лопаток, отделенных одна от другой временными заклепками. Установку скрепляющей проволоки следует производить после установки каждого пакета.
После окончания развертки и установки постоянных заклепок в верхних отверстиях описанным путем производится развертывание отверстий и установка постоянных заклепок в нижнем ряду отверстий.
Развертывание отверстий в лопатках, хвост которых располагается с наружной стороны гребня диска, должно заканчиваться зенкованием с обеих сторон под головку заклепки на глубину 1 мм. При развертывании необходимо следить за тем, чтобы лопатку не выжимало с гребня диска, что обычно происходит при некотором несовпадении отверстий диска и лопатки.
Для обеспечения плотного прилегания хвостов соседних лопаток и предупреждения выжимания лопаток производится крепление лопаток специально изготовленным охватывающим хомутом, после установки хомута лопатки, в которых производится развертывание отверстий, расклиниваются клиньями, забиваемыми между ними и хомутом. Во многих случаях, вместо указанного, можно ограничиться при надлежащем контроле периодической осадкой лопаток на диск медной выколоткой.
Рисунок 13.40. Заклепки (b—ширина обода диска).
В заклепочных отверстиях после их развертки не должно быть задиров и чернот. Черноту в отверстиях разрешается выводить развертками только до диаметра заклепок, допускаемого заводом для каждого диска. Проверку правильности обработки отверстий производят путем тщательного осмотра с применением зеркальца.
Перед установкой на место заклепки следует смазывать ртутной мазью. Постоянные заклепки должны входить в отверстия плотно, под легкими ударами ручника весом не более 500 г с одинаковым усилием по всей длине отверстия, при этом ни слабые заклепки, ни слишком тугие применять не следует. Чтобы добиться такого сопряжения, при котором заклепки работают только на срез, не допуская ни их смятия, ни изгиба, приходится сортировать заклепки по размерным группам в пределах разницы в диаметрах от 0,01 мм и подбора на каждую группу соответствующей развертки. Допуски на изготовление заклепок приведены на рис 13.40.
Перед установкой на место заклепки должны быть проверены по длине, чтобы после клепки не оставалось большой головки, что может привести к задеваниям за диафрагмы, вместе с тем недостаточная длина заклепок не позволит надежно их заклепать. Нормально концы заклепок должны выступать на 1,5— 2 мм.
После установки заклепку расклепывают ударами ручника для образования головки, придерживая с другой стороны домкратиком, упирающимся в соседний диск или с помощью бойка и рычага типа, оказанного на рис. 13.20 Головка заклепки не должна иметь заусениц, надрывов и пр.
13.11. УСТАНОВКА И ПАЙКА ПРОВОЛОЧНЫХ БАНДАЖЕЙ.
Проволочные бандажи диаметром 6—12мм изготовляются из холоднотянутой проволоки и применяются в термически обработанном состоянии для скрепления лопаток проволокой в один, два, три и более рядов в зависимости от длины лопатки. Установка бандажных проволок производится для отстройки лопаток от резонансных колебаний и уменьшения усталостных напряжений от вибраций.
Для повышения стойкости проволоки, работающей при переменных нагрузках, необходимо уделять особое внимание чистоте ее поверхности, поверхность проволоки должна быть светлой и не иметь рисок, царапин, волосовин, следов коррозии, вмятин, забоин и других концентраторов напряжений.
Проволока должна быть подобрана такого диаметра, чтобы зазор между проволокой и отверстием лопатки не превышал 0,1—0,4 мм, так как увеличение этого зазора приводит к повышенному расходу серебряного припоя. При заправке в отверстия проволока должна проходить свободно, для устранения заедания проволоки при протаскивании ее через отверстия лопаток следует запилить торцы проволоки, тщательно выправить и отполировать ее тонкой наждачной шкуркой, чтобы она имела гладкую поверхность, и выгнуть по дуге, соответствующей расположению отверстий в лопатках.
В процессе окончательной наборки лопаток на диск проволочные бандажи устанавливаются отдельными сегментами, соразмерными пакетам лопаток (обычно шесть — десять лопаток),
176
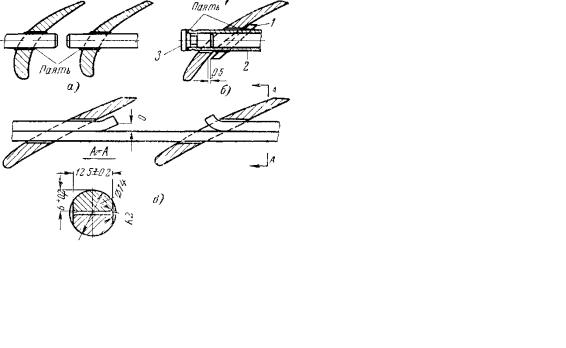
заправка сегментов проволоки производится в сторону вогнутой части лопаток со стороны неустановленных пакетов, откуда они прогоняются до места их установки. Последние перед замком пакеты лопаток надеваются на проволочный бандаж, после чего устанавливаются на место и замок закрепляется. Такой способ протаскивания требует, чтобы лопатки были отрихтованы до установки замка.
В некоторых случаях протаскивание проволоки производится после временного отгибания оправкой нескольких лопаток по обе стороны от установленного замка, после установки проволок на месте отогнутые лопатки должны быть вновь выправлены.
Пропущенную через все лопатки проволоку разрезают ножовкой между отдельными пакетами лопаток, оставляя свисающими концы проволоки в пределах 0,2—0,25 шага лопаток, после чего производится пайка проволочного бандажа к лопаткам серебряным припоем (рис 13.41,а).
Для демпфирования колебаний тяжелонагруженных лопаток последних и предпоследних ступеней мощных турбин (например, К-100-90, К-150-130, К-300-240) применяются «демпферные» бандажные связи, представляющие собой бандажи из полых трубок (рис 13.41,б), или составные бандажи из двух проволок, каждая из которых имеет в сечении полукруг (рис. 13.41,в). Трубчатые и составные проволочные бандажи свободно проходят сквозь отверстия в лопатках, к лопаткам не припаиваются для возможности их трения о лопатки и между собой.
Рисунок 13.41. Проволочные и трубчатые бандажи.
а— проволочные бандажи с припайкой к лопаткам,
б— трубчатые бандажи фиксированные шайбами. 1-шайба, 2—трубка 3 — пробка, в — проволочный составной из двух половин бандаж
без припайки к лопаткам.
Такая связь не уменьшает частоты колебаний пакета лопаток, но благодаря трению бандажей в отверстиях лопаток и связыванию составной проволокой лопаток в одну систему передает на весь пакет в целом усилие, действующее на каждую лопатку, благодаря этому образующийся единый пакет, замкнутый по окружности, препятствует появлению танген-
циальных колебаний с амплитудами большой величины, установка второго ряда таких проволок дополнительно снижает уровень тангенциальных колебаний, практически устраняя условия для их возникновения.
Трубчатые бандажи, применение которых уменьшает также действие на лопатки центробежных сил от массы бандажа, изготовляются из трубок диаметров 10—14 мм с толщиной стенки 1,5—2 мм. Фиксация этих трубок относительно лопаток производится шайбами, которые надеваются на концы трубок и припаиваются к ним серебряным припоем, для устранения попадания внутрь трубок пара или влаги концы трубчатых бандажей закрываются пробками, которые припаиваются к трубкам серебряным припоем.
При ремонте необходимо контролировать, чтобы свисающий конец трубок был меньше длины пробок, так как иначе под действием центробежной силы пробки, возможна поломка трубчатого бандажа в месте его стыка с лопаткой; необходимо также проверять плотность закрытия трубки пробкой и качество ее пайки, так как попадание влаги в трубку может привести к коррозии ее внутренней поверхности и к появлению дополнительных центробежных сил.
Рисунок 13.42. Пайка бандажной проволоки се-
ребряным припоем. 1-сторона входа пара; 2 — автогенная горелка, 3 — флюс, 4 — припой, 5 — правильная пайка.
В ступенях со свободными проволочными бандажами расположение в межлопаточных каналах концов половинок проволок (свесов), фиксирующих их относительно лопаток, должно соответствовать указаниям на рис. 13.41,в; при диаметрах проволоки 6,5 и 8 мм размер О, показывающий величину отгиба проволоки, должен быть равен 2—2,5 мм, а при диаметрах 10 и 12 мм 3—4 мм. Значительное увеличение указанных размеров может приводить к отгибу и отрыву концов проволоки, выступающей из лопаток.
Пайка бандажной проволоки к лопат-
кам производится серебряным припоем марки ПСр-45 (ОСТ 2982). Состав этого припоя: серебро 45%, медь 30%, цинк 25% и примесей не более 0,5%. Этот припой выпускается промышленностью в виде прутков, полос или небольших листов (примерно 150х200х2 мм), которые для пайки бандажей нарезаются в виде узких лент шириной 3-5 мм и длиной 150—200 мм. Серебряный припой ПСр-45 имеет температуру плавления 710— 720° С, т.е. наиболее низкую температуру из всех
177
серебряных припоев, благодаря чему пайка не должна влиять на структуру материала лопаток. Это имеет большое значение для пайки, особенно хромистой нержавеющей стали, так как сталь при нагреве в процессе пайки может закалиться и в ней в зоне пайки образуются трещины.
Внекоторых случаях для увеличения жесткости соединения в местах предусмотренных чертежом, или когда это требуется по условиям отстройки, серебряным припоем производится пайка к лопаткам также и ленточного бандажа.
Вкачестве специального флюса, который покрывает место пайки и предохраняет его от окисления, для лопаток из нержавеющей и никелевой стали применяется состав: 43 % безводного фтористого калия и 57% борной кислоты (по весу). Для получения однородного флюса указанная смесь размельчается, затем расплавляется
втигле при температуре 800— 850° С. После остывания сплав выливается на мраморную доску и толчется в стальной ступе Полученный белый порошок флюса должен храниться в герметически закрытой банке, так как он поглощает влагу из воздуха.
Применение буры в качестве флюса (борнокислый натрий, разведенный перед пайкой в теплой воде) может быть рекомендовано только для пайки лопаток из латуни; для расплавления такого флюса требуется повышение температуры места пайки до 780—790° С, что вредно для стальных лопаток, так как при этой температуре начинаются структурные изменения материала лопаток и явления закалки.
Сама пайка производится ацетиленкислородным пламенем при горизонтальном положении лопатки вогнутой стороной вверх (рис. 13.42,а). Место пайки предварительно тщательно очищается от ржавчины и обезжиривается, что обеспечивает последующую качественную пайку. Место пайки прогревается пламенем автогенной горелки № 1 или 2 до температуры, немного выше температуры плавления серебряного припоя (730—750° С—темно-красное каление). Когда флюс, нанесенный на подогретое место, растечется и покроет место пайки сплошной тонкой пленкой, палочка серебряного припоя, прижатая к месту пайки, проводится кругом бандажной проволоки.
Серебряный припой должен заполнить весь цилиндрический зазор между лопаткой и проволокой и свободно протечь с одной стороны лопатки на другую, тем самым пропаивается весь стык проволоки с лопаткой (рис. 13.42,б). Для покрытия равномерным слоем всей поверхности проволоки у лопатки и у отверстия, а также для образования вокруг отверстия вогнутой галтели серебряный припой при пайке не должен целиком расплавляться в пламени и не должен капать на место пайки. Поэтому, как только температура места пайки дойдет до температуры плавления припоя, необходимо прекратить нагрев автогеном.
Быстрое расплавление припоя и светлокрасный цвет места нагрева указывают на недо-
пустимо высокую температуру пайки; вместе с тем температура ниже 720° С не обеспечивает хорошей пропайки. Отсюда ясно, что проведение пайки в небольших пределах температур (720— 750° С), при которых не происходит структурных изменений металла лопаток, следует поручать только квалифицированному сварщику.
Впрактике эксплуатации после облопачивання наблюдались случаи обрыва проволочных связей в непосредственной близости от мест пайки; причиной таких обрывов являются трещины, которые появляются в проволоке в процессе пайки под действием напряжений от изгиба проволоки при несоосности отверстий в лопатках, напряжений, возникающих в проволоке из-за местного характера нагрева при пайке, и термических напряжений, вызываемых высокой температурой и местной закалкой при пайке.
Во избежание неблагоприятного влияния высокой температуры на качество пайки и на материал лопаток следует производить пайку не всех лопаток подряд, а, пройдя первый круг, пропаивать все первые лопатки всех пакетов; далее, пройдя второй круг, пропаять все вторые лопатки всех пакетов и т.д. Такой порядок дает возможность вести пайку холодных лопаток, так как лопатки, с которых начата пайка, успевают остыть за время обхода.
Вслучае необходимости пайки лопаток, имеющих несколько рядов бандажной проволоки, сначала следует начинать паять с нижнего ряда, ближнего к хвосту. После пайки и проверки тангенциального положения и в необходимых случаях выправки лопаток производится пайка следующего ряда проволоки и т.д.
По окончании пайки следует убедиться в том, что пропаяны все лопатки без пропусков, а затем тщательно смыть с мест пайки флюс горячей водой с температурой 80—90° С или струёй насыщенного пара в 1,5—2 ат. Промывка должна производиться тотчас же по окончании пайки всех лопаток этой ступени; оставленный на непродолжительное время флюс затвердевает и его последующее механическое удаление, необходимое для проведения контроля качество пайки, требует значительной затраты труда; кроме того, применение скребков может вызвать появление рисок и царапин на полированной поверхности лопаток.
Контроль за качеством проведенной пайки должен быть тщательным для своевременного обнаружения ее дефектов и устранения их соответствующей подпайкой или повторной пайкой.
При пайке бандажной проволоки в цилиндре турбины приходится иметь дело с пайкой лопаток, которые находятся не только в горизонтальном, но и в вертикальном и наклонном положениях. Пайка лопаток, находящихся в горизонтальном положении, производится, как указано выше. Наложение флюса и серебряного припоя на лопатки, находящиеся в вертикальном и наклонном положениях, должно производиться при возможно низкой температуре с внутренней стороны профиля лопатки, нагреваемой несколько
178
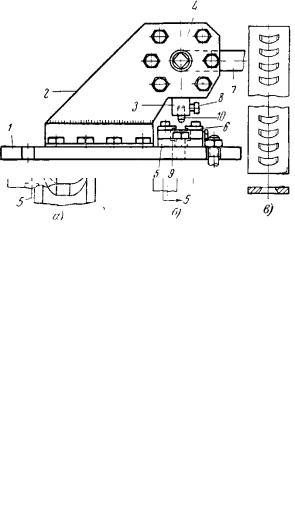
выше бандажной проволоки. Для выравнивания температуры вокруг бандажной проволоки с обеих сторон лопатки пламя автогенной горелки переносится на противоположную сторону лопатки; этот перенос пламени с одной стороны лопатки на другую необходим для того, чтобы не допустить перегрева припоя, отекания припоя вниз по лопатке, и производится до тех пор, пока серебряный припой не растечется равномерно вокруг проволоки с обеих сторон лопатки.
13.12. УСТАНОВКА ЛЕНТОЧНЫХ БАНДАЖЕЙ.
Установка ленточных бандажей на шипы головок лопаток для пакетной связи лопаток с числом от 6 до 20 в пакете производится после окончательной установки лопаток, их закрепления на диске и соответствующей правки.
Установка бандажных лент на пакеты лопаток придает им необходимую жесткость против вибраций и вместе с тем, ограничивая по высоте лопаток каналы для прохода пара, создает условия для лучшей организации парового потока и уменьшения его протечек.
Для качественной установки бандажных лент на пакеты лопаток и расклепки шипов необходимо обеспечить правильное положение бандажа относительно оси симметрии шипов всех лопаток, плотное прилегание и жесткое соединение бандажа с торцами соединяемых им лопаток. Правильность прилегания бандажей к лопаткам проверяется предварительно при помощи шаблона по отсутствию зазоров между торцами лопаток и бандажом; при обнаружении зазоров опиловка торцов производится так, чтобы сохранить переходные радиусы у корня шипов.
Шаг отверстий под шипы определяется для каждого отрезка бандажа путем его разметки на облопаченном ряду с помощью шаблона (рис. 13.43,а, б). Пробивать отверстия в ленточных бандажах заранее нельзя; для правильной и плотной насадки бандажной ленты на шипы лопаток пробивка отверстий в них должна производиться на расстояниях, соответствующих фактическому шагу шипов набранных лопаток, получившемуся после рихтовки и с учетом необходимости расположения замковой лопатки или вставки против середины бандажного сегмента.
Для разметки на каждом сегменте бандажной ленты проводится центровая линия; бандажная лента выгибается по дуге расположения шипов и прикладывается сбоку шипов пакета лопаток, на который намечена ее насадка; чертилкой с помощью шаблона или угольника на бандажную ленту наносятся риски, которые определяют шаг шипов. В некоторых случаях разметка отверстий для круглых шипов производится с помощью картонного шаблона; оттиски отверстий размечаются или путем обстукивания молотком шаблона, наложенного на шипы, или путем наложения шаблона на головки шипов, предварительно окрашенные лазурью; с шаблона разметка отверстий переносится на бандажную ленту.
Для обеспечения плотной посадки бандажа на лопатки разметку отверстий следует производить с внутренней стороны бандажной ленты; с этой же стороны после выправки согнутых бандажей производится пробивка отверстий по произведенной разметке, благодаря чему заусеницы выходят наружу, а края отверстий получают некоторый прогиб внутрь, в виде раззенковки, способствующей лучшему прилеганию бандажа к лопаткам (рис. 13.43,в).
Пробивка отверстий в ленте производится на специальном ручном прессе—штампе (рис. 13.44), устанавливаемом на верстаке вблизи от места переоблопачивания. В прессе закрепляется пуансон и матрица с размерами, соответствующими размеру шипов лопаток; неудовлетворительная взаимная подгонка матрицы и пуансона и плохая их заточка в процессе пробивки отверстий под шипы могут приводить к смятию и трещинам. Суммарный зазор А между матрицей и пуансоном (рис. 13.45) не должен превышать: 0,07 мм для бандажного сегмента толщиной 1 мм; 0,12 мм— для 1,5 мм; 0,16—для 2 мм и 0,24 мм для бандажа толщиной 3 мм.
Рисунок 13.43. Разметка отверстий в бандаже с помощью шаблонов. а — для лопаток с прямоугольными шипами; б — для лопаток с круглыми шипами; в — пробивка отверстий по разметке, 1—лопатка, 2— бандажная лента, 3—шаблон, 4—риска, нанесенная с помощью шаблона, 5 — центровая риска.
Рисунок 13.44. Ручной пресс для пробивки отверстий в бандажной ленте под шипы лопаток. 1-опорная плита, 2 — боковые листы, 3 — держатель пуансона, 4—валик приводный, 5— держатель матрицы,
6— накладка держатель бандажной ленты, 7—рычаг, 8 — болт 10 мм, 9— матрица, 10 — пуансон.
179
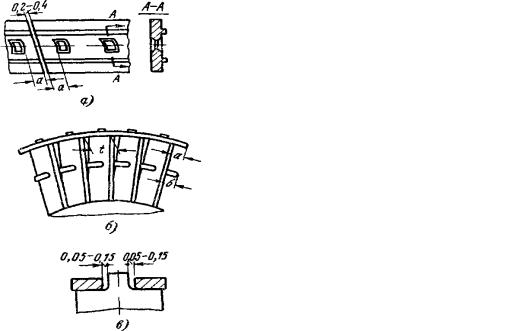
Для лопаток с круглыми шипами изготовление специальных пуансонов и матриц не требуется, так как отверстия в бандаже в этих случаях сверлятся сверлами соответствующих размеров.
После пробивки отверстий бандажи следует тщательно проверять травлением на отсутствие трещин и надрывов у краев отверстий, в особенности у отверстий под шипы с острыми углами, так как в этих местах могут образоваться тончайшие трещинки, приводящие в эксплуатации к разрыву бандажа.
Перед посадкой бандажной ленты на шипы надлежит удалить опиловкой все заусеницы на бандаже и у оснований шипов на лопатках, так как заусеницы могут помешать плотному прижатию бандажа к лопаткам; для этой же цели круглые отверстия в бандажах следует зенковать, а в прямоугольных отверстиях запиливать фаски размером 1х1,5 мм под углом 45° с обеих сторон по толщине бандажа (рис. 13.46,а).
может создать дополнительное напряжение в хвостах лопаток и привести к их изгибу в тангенциальном и осевом направлениях. Посадка на шипах не должна быть напряженной, но шипы не должны заходить в отверстия в бандаже с зазором больше 0,05—0,15 мм на сторону в зависимости от толщины бандажа (рис. 13.46,в).
При расклепке шипов прижатие бандажа к торцам лопаток должно быть равномерным и одинаковым по всей площади касания; только убедившись в правильности положения бандажа, можно приступать к расклепке шипов лопаток.
Если шипы лопаток и бандажи изготовлены из недостаточно вязкого материала, в них при расклепке могут появиться трещины; трещины, не обнаруженные при расклепке, могут послужить причиной аварии в эксплуатации из-за обрыва бандажа.
Рисунок 13.45. Матрица (а) и пуансон (б).
В целях устранения коробления при температурных расширениях необходимо разметить, обрезать и запилить скосы концов бандажных сегментов, связывающих лопатки в пакеты так, чтобы между их стыками по окружности были получены зазоры в соответствии с чертежом облопачивания или с зазорами до облопачивания. Обычно эти зазоры в стыках бандажных сегментов выполняются в пределах от 0,75 до 1,5 мм. Для лопаток, имеющих бандажи с уплотнительными усиками, зазоры по окружности между стыками сегментов бандажей (рис. 13.46,а) должны быть 0,2—0,4 мм. Нельзя оставлять недостаточные зазоры в стыках, но вместе с тем не следует выполнять эти зазоры больше необходимых
Длина свисающих концов бандажной ленты у пакетов—размер а (рис. 13.46, а и б) должен быть равен половине шага лопаток t минус половина зазора между торцами двух соседних сегментов бандажной ленты, разница в длине свесов соседних сегментов не должна быть больше 1 мм. При длинных лопатках, в связи с большим шагом лопаток, длина свисающей части бандажной ленты уменьшается, температурный зазор при этом соответственно увеличивается; такое укорочение необходимо для снижения высоких изгибающих напряжений, возникающих в шипах крайних лопаток при длинных свисающих концах бандажа.
Отдельные сегменты бандажной ленты, предварительно выгнутые соответственно дуге расположения шипов, должны надеваться без всякого натяга отдельных лопаток, так как это
Рисунок 13.46. Установка бандажной ленты.
а— сегменты бандажей с уплотчительными усиками,
б— «свес» бандажной ленты между пакетами лопаток,
в— зазоры между шипом и бандажной лентой.
Для ослабления наклепа, предупреждения повышения жесткости и хрупкости шипа и для уменьшения внутренних напряжений расклепывание должно производиться особо тщательно. Расклепка шипов должна производиться на всех лопатках одинаково, в определенной последовательности и при одинаковой силе ударов; сначала легкими ударами молотка (в зависимости от сечения шипа лопатки вес молотка 300—400 г) по шипам, расположенным по краям сегмента бандажа, а затем окончательная чеканка — специальной оправкой для получения головки шипа заданной формы и хорошего внешнего вида (рис. 13.47).
После чеканки производится проверка плотности прилегания бандажей к торцам лопаток (щуп толщиной 0,05 мм нигде проходить не должен) и тщательный осмотр под лупой бандажей и расчеканенных шипов на отсутствие тре-
180