
- •Содержание
- •ТЕПЛОВЫЕ ЭЛЕКТРОСТАНЦИИ
- •Оптимизация обмывок регенеративных воздухоподогревателей
- •Эрозионный износ твердыми частицами проточной части ЦСД-1 турбин Т-250/300-240
- •Регулирующая поворотная диафрагма с модернизированным приводом
- •ГИДРОЭЛЕКТРОСТАНЦИИ
- •К концепциям развития малой гидроэнергетики
- •ЭНЕРГОСИСТЕМЫ И ЭЛЕКТРИЧЕСКИЕ СЕТИ
- •Переходные процессы, сопровождающие включения и отключения емкостных фильтрокомпенсирующих устройств
- •Повышение эффективности удаления гололедообразований с проводов ВЛ
- •Опыт предупреждения морозного пучения свайных фундаментов опор ВЛ в северных условиях
- •Выбор промежуточной опоры для ВЛ 330 кВ “Северный транзит”
- •О выборе уставок дистанционных реле-избирателей ОАПВ ВЛ
- •ОБМЕН ПРОИЗВОДСТВЕННЫМ ОПЫТОМ
- •ЭНЕРГОХОЗЯЙСТВО ЗА РУБЕЖОМ
- •Использование газа на тепловых электростанциях США и проблемы экологии
- •По страницам зарубежных журналов
- •ХРОНИКА
- •Пресс-конференция Российского подразделения концерна АББ
- •Пресс-конференция фирмы “Оптима”

температурой 260 – 270°С и расходом 3 – 4 т ч позволяет снизить температуру корпуса ЦСД в зоне расположения каминных камер переднего концевого уплотнения и тем самым существенно ограни- чить температурные деформации обойм каминов.
Данное мероприятие в сочетании с модернизацией каминов, включающей изменение конструкции эластичного кольца и обойм, обеспечивает надежность работы переднего концевого уплотнения. При этом уменьшается износ уплотнений и исключается обводнение масла за счет снижения нерегулируемых протечек пара через уплотнения
âмашинный зал.
5.В зависимости от конкретных условий эксплуатации, наравне с примененным на Конаковской ГРЭС, могут быть использованы и другие источ- ники охлаждающего пара для подвода его в переднее концевое уплотнение ЦСД.
6.Оценка циклической прочности ротора среднего давления показывает, что прочность ротора
среднего давления в исследуемой зоне повышается, а общая повреждаемость не возрастает.
7. Результаты расчетов (рис. 7) показывают, что при подводе охлаждающего пара в зону каминных камер переднего концевого уплотнения ЦСД за счет эффекта теплового экрана несколько возрастают напряжения в роторе среднего давления в зоне первых отсосов из переднего уплотнения ЦСД.
Список литературы
1.Подгорный А. М., Гонтаровский П. П., Марченко Г. А. Решение осесимметричной задачи упругости методом конеч- ных элементов для тел сложных конструктивных форм. – Проблемы машиностроения, 1976, вып.3.
2.Плоткин Е. Р., Лейзерович А. Ш. Пусковые режимы паровых турбин энергоблоков. М.: Энергия, 1980.
3.ÐÒÌ 108.020.16-83. Расчет температурных полей роторов и корпусов паровых турбин. Л.: НПО ЦКТИ, 1985.
Эрозионный износ твердыми частицами проточной части ЦСД-1 турбин Т-250/300-240
Хаимов В. А., Качуринер Ю. Я., Воропаев Ю. А., кандидаты техн. наук
ОАО “НПО ЦКТИ” – ТЭЦ-23 Мосэнерго
Процессы эрозионного износа твердыми частицами проточной части высокого и среднего давления турбин блоков СКД, многие годы наблюдающиеся как в отечественном [1, 2], так и в зарубежном [3] энергетическом оборудовании, являются следствием формирования и последующего разрушения оксидной пленки в перегревательных трактах котлов, когда частицы пленки в виде окалины высокой твердости транспортируются паром в проточную часть и оказывают ударно-эрозион- ное и эрозионное воздействие на элементы проточной части.
На многих электростанциях срок службы лопаточного аппарата и периферийного уплотнения ча- сти среднего давления турбин Т-250/300-240 в условиях интенсивного воздействия эрозионных нагрузок сокращается до одного-трех межремонтных периодов, ухудшается экономичность, возникает опасность поломок и аварийных ситуаций, возрастают затраты на восстановление и ремонт поврежденных элементов. Согласно исследованиям [1] КПД дубль-блочной турбоустановки типа К-300-240 ХТГЗ снижается из-за эрозионного износа на 0,35% при работе с номинальной нагрузкой и на 2,16% – при работе с одним корпусом котла, а в зарубежной энергетике снижение КПД турбоустановок за каждые 5 лет достигает 0,4%.
Перевод блоков на нейтрально-кислородный водный режим [4] способствовал образованию нестойких к разрушению оксидных пленок в тракте парогенератора и повышенному износу проточной части турбин [5]. В последние годы разрабатываются мероприятия по предотвращению процессов разрушения оксидной пленки как режимного характера, так и внедрением новых аустенитных хромомарганцевых сталей типа Ди59 [6], однако проблема сохраняет актуальность и обусловливает создание средств защиты проточной части от эрозионного износа.
По данным [1] размер уловленных в паре частиц составляет от 10 до 300 мкм, а их микротвердость – 700 – 750 кгс/см2, что при рабочих параметрах пара превосходит в 3,5 – 5,0 раз микротвердость лопаточных сталей и обеспечивает высокую повреждающую способность при многократных соударениях с лопатками. При упругом взаимодействии скорость частиц влияет на износ в степени не менее 2,8, а при пластическом – в степени не менее 3,5 [7]. При увеличении угла контакта контактные напряжения или деформации возрастают и могут достигать разрушающих зна- чений, а критический угол перехода от усталостного износа к микрорезанию определяется проч-
14 |
2004, ¹ 4 |
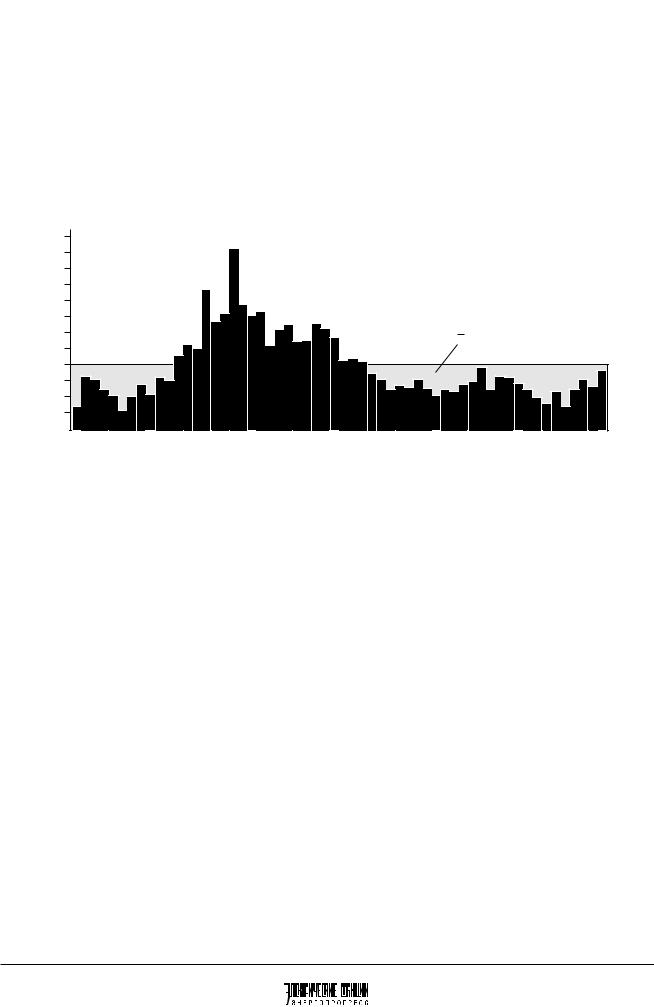
|
|
|
|
|
1 |
|
|
|
|
|
|
|
2 |
|
|
|
|
|
|
3 |
|
|
|
5 |
|
4 |
|
|
|
|
|
|
à) |
|
|
S, ìì2 |
|
|
|
|
|
|
400 |
|
|
|
|
|
|
|
|
|
|
|
S |
|
200 |
|
|
|
|
|
|
0 |
|
|
|
|
|
|
1 |
10 |
20 |
30 |
40 |
Номер лопатки |
|
|
|
|
|
á) |
|
|
<2 * . / * 2 3 0 <F& % 6 *! 2 * 2 & |
|||||
/ |
6 2' ' 5' ' %+ |
|
|
|
|
|
1 – направляющий аппарат; 2 – пароподводящий патрубок; 3 – подвижная часть регулирующего клапана; 4 – продувî÷íûé øòó- |
||||||
öåð; 5 – зона максимальной концентрации твердых частиц; S – площадь лопатки, “исчезнувшая” в результате износа; S – средняя |
||||||
площадь износа всех лопаток |
|
|
|
|
|
ностными свойствами металла лопаток, материалом частиц и скоростью соударения.
Одним из активных способов предотвращения или снижения эрозионного износа проточной части является удаление частиц оксидной пленки из парового потока. Эта задача может быть решена тремя путями.
Первый из них заключается в отделении твердых частиц от парового потока в паропроводе горячего промперегрева сепарационными устройствами, установленными на участках с изменением направления движения, например, с вертикального нисходящего в горизонтальный поток. Однако эффективность такого отделения, ограниченная естественным осаждением частиц на вогнутом участке внутренней поверхности стенки трубопровода, окажется невысокой, поскольку их значи- тельная доля будет преодолевать поворот, продолжая двигаться в парном вихре. Использование сепаратора с закрученным потоком на прямолинейном участке паропровода обусловит рост гидравлических потерь и снижение экономичности
турбоустановки, а его эффективность на переходных частичных и малых нагрузках окажется пониженной, что является неблагоприятным фактором, поскольку на таких режимах в перегревательном тракте котла происходит изменение температурной картины, способствующее интенсивному разрушению оксидной пленки.
Второй путь решения задачи, реализованный ЦКТИ и ТЭЦ-23 [8], заключается в организации процесса отделения частиц от пара непосредственно в отсечном или регулирующем клапане. При этом практически не увеличиваются гидравличе- ские потери при удовлетворительной эффективности сепарации, не снижается надежность отсечного клапана, так как не нарушается целостность его основных элементов и наружной стенки, а затраты на изготовление и установку сепарирующего устройства во много раз меньше, чем при установке сепаратора непосредственно в паропроводе.
Третий путь решения задачи предусматривает отвод сконцентрированных в проточной части ЦСД потоков частиц вместе с паровой продувкой
2004, ¹ 4 |
15 |
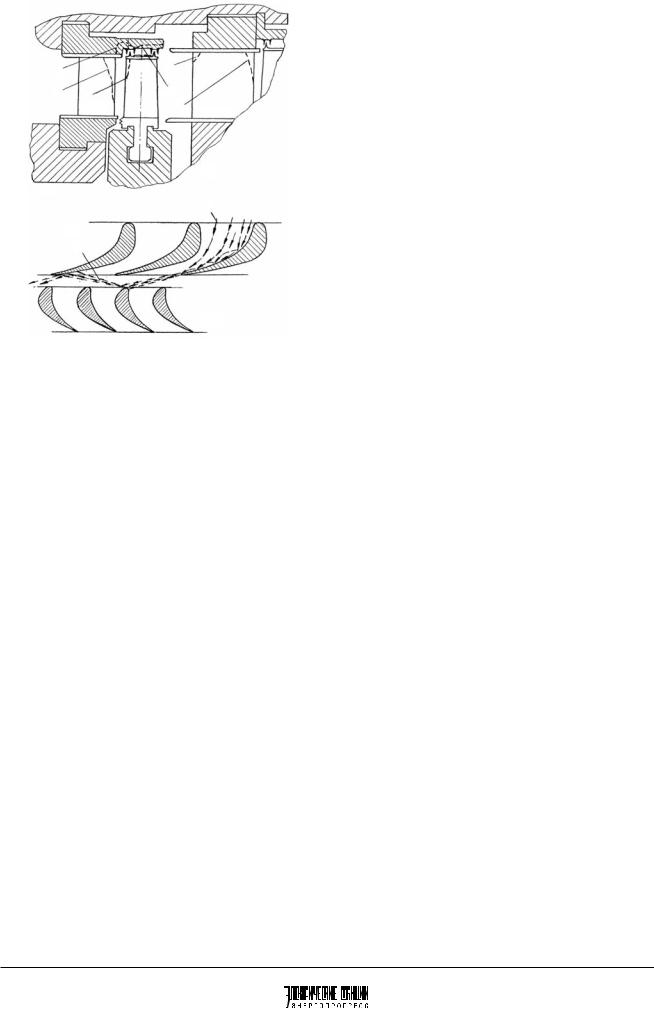
2 |
|
5 |
1 |
3 |
4 |
|
13 ступень |
6 |
|
14 ступень |
||
|
à)
7
8
á)
, ? 3 ) 3 <F& % 2 &
* ) / * 2 3 0 2 * &
/ 6 2' ' 5' ' %+
1 – 6 – зоны износа; 7, 8 – паровые потоки
во внешний сепарационный контур, отделении ча- стиц от паровой среды и сбросе пара в следующий по проточной части отбор [9]. Поскольку при этом используется формирующаяся естественным образом газодинамическая картина двухфазного потока в проточной части, высокая эффективность достигается при незначительных экономических затратах. Более того, если учитывать потери экономичности от эрозионного износа лопаток и надбандажных уплотнений, применение такого решения приводит, в конечном счете, к значительному экономическому выигрышу и сохранению надежности элементов проточной части. Впервые этот путь был реализован ТМЗ при модернизации 13 ступени турбины Т-250/300-240 за счет открытия межвенечного зазора для вывода частиц из проточной части, что осуществлено переносом места крепления козырька надбандажного уплотнения с направляющего аппарата 13 ступени на диафрагму 14 ступени. Эксплуатация турбин с модернизированной 13 ступенью подтвердила уменьшение износа козырька и надбандажного уплотнения, однако износ направляющих лопаток оставался значи- тельным из-за ограниченных размеров накопительной камеры и отсутствия дренажа частиц из нее.
Для оптимального решения задачи необходима общая картина движения частиц и эрозионного износа проточной части. Согласно исследованиям ЦКТИ и ТЭЦ-23 на турбинах Т-250/300-240 характер износа определяется, в первую очередь, трактом подвода пара к камере паровпуска ЦСД-1: пар
из паропровода промперегрева поступает в отсеч- ной клапан, а из него – в регулирующий клапан, подвижная часть которого расположена у нижней стенки подводящего патрубка камеры паровпуска (ðèñ. 1). (Íà ðèñ. 1 номера лопаток указаны по вращению от правой стороны горизонтального разъема, а изношенная площадь каждой из лопаток определена компьютерной обработкой рельефа выходной кромки). Благодаря этому возникает сильная неравномерность распределения частиц в камере паровпуска с высокой концентрацией в нижней зоне на входе в направляющий аппарат.
Поскольку скорость частиц относительно направляющих лопаток 13 ступени невысокая и углы их контактирования малы, заметного износа входной и средней частей профиля лопаток не происходит (ðèñ. 2). Эрозионный продукт транспортируется паровым потоком по межлопаточным каналам, частично соприкасаясь преимущественно с входной кромкой и вогнутой поверхностью направляющих лопаток и образуя вблизи этой поверхности область повышенной концентрации (поток 7, ðèñ. 2, á ).
Так как скорость частиц в межвенечном зазоре остается существенно меньше скорости пара, они встречаются с рабочими лопатками под отрицательными углами. При этом скорость контакта оказывается недостаточно высокой, чтобы создать опасный уровень эрозионных нагрузок на входные кромки рабочих лопаток, хотя при этом происходят определенные изменения механических свойств в поверхностном слое металла. Обследование рабочих лопаток подтверждает незначительный износ входных кромок в виде узкого участка периферии непосредственно у бандажа, где возникает повышенная концентрация частиц в паровом потоке (зона 3, ðèñ. 2, à ).
При встрече с рабочими лопатками частицы отражаются от них с высокой скоростью и движутся под углом в сторону направляющих лопаток (поток 8, ðèñ. 2, á ). Пересекая межвенечный зазор в обратном направлении, частицы встречаются с выпуклой поверхностью выходных кромок направляющих лопаток и вызывают эрозионный износ поверхности лопаток (зона 1, ðèñ. 2, à ). После удара скорость частиц гаснет, они подхватываются паром и снова перемещаются к рабочим лопаткам – процесс эрозионного разрушения металла повторяется.
Изложенные особенности движения частиц определяют распределение износа направляющих лопаток в окружном направлении (ðèñ. 1, á): в нижней части камеры паровпуска образуется максимальная концентрация частиц и, поскольку наибольшую опасность несут первые удары, когда ча- стицы имеют максимальные размеры и обладают максимальной энергией разрушения, зона интенсивного износа смещается с учетом вращения ко-
16 |
2004, ¹ 4 |
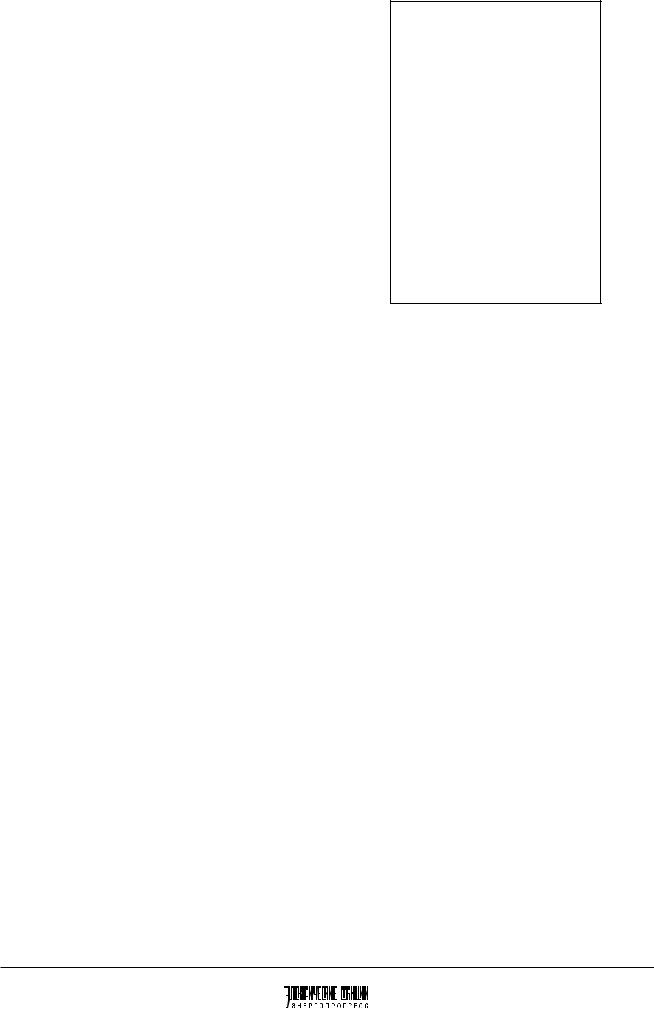
леса в левую нижнюю и частично верхнюю четверти дуги направляющего аппарата.
Исследованный механизм движения частиц объясняет и характерную картину износа выходных кромок, нарастающего к периферии лопаток (зона 1, ðèñ. 2, à ). После контактирования с рабо- чими лопатками частицы отражаются от них по касательной и, следовательно, встречаются с направляющими лопатками на большем диаметре по сравнению с тем, по какому они двигались к рабо- чим лопаткам. При каждом последующем контакте частицы будут перемещаться к периферии направляющих лопаток, где происходит нарастание числа соударений, обусловливающее увеличение износа до максимальной величины у периферии. Таким образом, если в корневой зоне контактирование направляющих лопаток совершается только с теми частицами, которые попадают туда под действием парового потока из камеры паровпуска, то на периферии с направляющими лопатками контактирует большинство частиц, поступивших в направляющий аппарат и не попавших в межлопаточные каналы рабочего колеса.
Частицы, достигшие после многократного контактирования периферийной области, концентрируются у козырька, оказывая на него высокое локальное эрозионное воздействие. Движение частиц в зоне 2 (ðèñ. 2, à ) ограничено торцом направляющего аппарата и надбандажным уплотнением, что повышает их концентрацию, а периодическое контактирование с рабочим колесом обеспечивает им высокую скорость движения, а значит, и разрушительную силу. Это, в конечном итоге, обусловливает быстрый износ козырька в узкой ограни- ченной зоне (зона 2, ðèñ. 2, à ). Причем, в наибольшей степени износ проявляется от той массы частиц, которая поступает в направляющий аппарат из нижней части камеры паровпуска. Именно здесь, как отражено на ðèñ. 1, á, происходит наиболее глубокий износ и отрыв части козырька с последующим разрушением бандажа и повреждением рабочих лопаток (ðèñ. 3). Доля частиц, достигшая в межвенечном зазоре козырька, под действием протечек проникает в надбандажное уплотнение и производит износ уплотнительных гребней и шипов рабочих лопаток (зона 4, ðèñ. 2, à ).
Если размеры частиц достаточно малы, они проходят межлопаточные каналы рабочего колеса 13 ступени и поступают в диафрагму 14 ступени, где процессы эрозионного характера повторяются, но уже с меньшей интенсивностью. Износ на направляющих лопатках этой ступени формируется в двух зонах (ðèñ. 2, à ): в зоне 5 – под воздействием частиц, покидающих рабочие лопатки 13 ступени и имеющих высокую окружную составляющую скорости движения, и в зоне 6, где износ выходных кромок является следствием отражения частиц от входных кромок рабочих лопаток 14 ступени.
5 1 * . .* & 2 * 2 3 2 5 !
$ ! * * .$ /
3 '# 3' ' ' &,94 544&,84' &,5
С учетом изложенной картины в 13 и 14 ступенях ЦКТИ была разработана и испытана в 1994 г. на турбине Т-250 300-240 ТЭЦ-23 экспериментальная система отвода частиц из проточной части. Она предусматривала вывод пробы через накопительные камеры из периферийной области межвенечных зазоров 13 и 14 ступеней, где имеется максимальная концентрация эрозионного продукта, во внешний сепарационный контур, отделение ча- стиц от пара и возвращение очищенного пара в ближайший отбор ЦСД-1. Система содержала также электронное устройство непрерывного контроля интенсивности поступления частиц оксидной пленки в сепараторы. Несмотря на то, что включе- ние системы имело непродолжительный характер, ее влияние оказалось заметным: средний износ направляющих лопаток был на 17%, а минимальный и максимальный износы в 1,7 – 1,9 раза меньше, чем лопаток других турбин. В связи с перестройкой потока в межвенечном зазоре 13 ступени снижение износа направляющих лопаток происходило, прежде всего, за счет уменьшения длины повреждения выходных кромок.
Для установления количественных характеристик движения твердых частиц в прямом и отраженном потоках 13 ступени на номинальном режиме выполнен расчет по программам [10], в которых газодинамика в направляющем аппарате и межвенечном зазоре рассчитывается методом установления для стационарного сжимаемого совершенного газа с учетом периодичности потока, а траекторные параметры продуктов разрушения оксидной пленки – методом меченых частиц с оптимальным выбором наиболее представительных
2004, ¹ 4 |
17 |
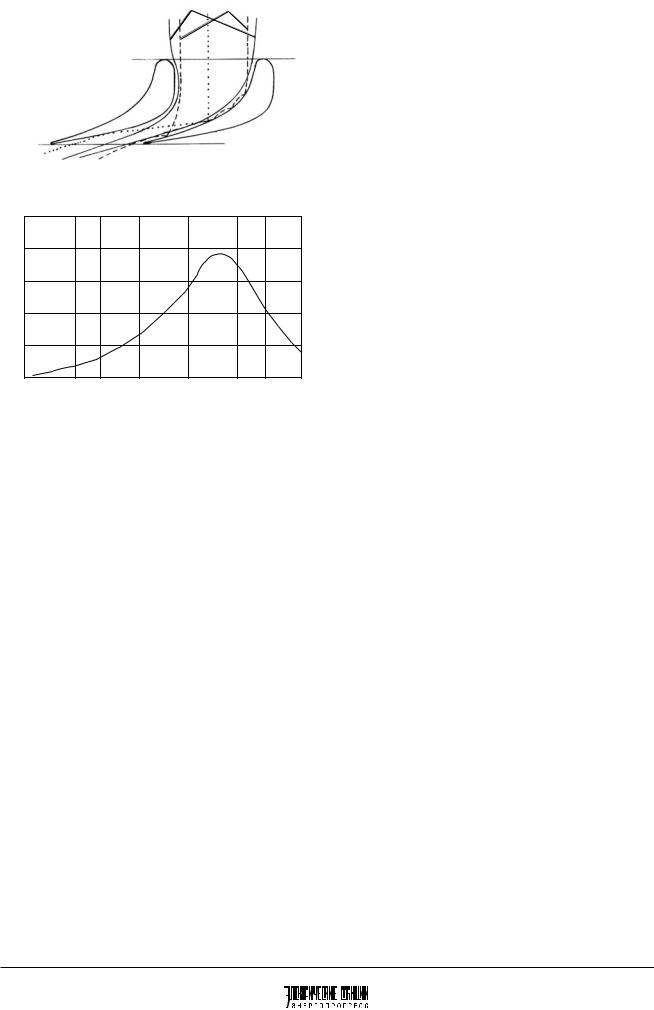
1 3 2
à)
vini [106], ìêì3
160
120
80
40
10 |
20 30 |
40 |
100 |
200 300 di, ìêì |
|
|
|
á) |
|
8 3 0 / 6 5
' %' ' 2'B 0 )' ' %+
1 – 3 – размер частицы соответственно 10; 50 и 500 мкм; vi è ni
– объем и число частиц размером di
их размеров (ðèñ. 4, à ). Коэффициент аэродинами- ческого сопротивления принят по опытным данным [11], учитывающим отклонение от стандартной кривой сопротивления для сферы при различ- ной форме твердых частиц, а отражение частиц от входных кромок рабочих лопаток определено с учетом экспериментальных исследований [12].
Необходимый для расчета фракционный состав продуктов разрушения оксидной пленки, содержащих представительную совокупность из 45 тыс. частиц и отобранных из камеры паровпуска ЦСД-1 турбины Т-250 300-240, установлен измерением размеров частиц с погрешностью, не превышающей 3 мкм. Согласно ðèñ. 4, á модальный по массе размер частиц составляет примерно 140 мкм, а максимальный – 500 мкм, хотя в пробе встречались и немногочисленные конгломераты частиц с размерами до 1500 – 2000 мкм.
Расчетом установлено, что частицы, размер которых не превышает 10 мкм, проходят через направляющий аппарат 13 ступени, не контактируя с лопатками. С увеличением размеров наблюдается рост числа частиц, ударяющих по вогнутой поверхности лопаток, и перемещение точки удара к входной кромке лопаток; одновременно изменяется и скорость соударения от 10 до 80 м с. В этой области с лопатками контактируют все частицы,
размер которых превышает 30 – 50 мкм. Некоторые частицы, отражаясь от поверхности лопатки, снова попадают на нее, и скачут по ней до выходной кромки или, отражаясь от поверхности, возвращаются в паровой поток и уносятся в межвенечный зазор.
Наиболее крупные частицы (массовая доля примерно 2 – 3%), отражаясь от вогнутой поверхности лопаток, пересекают межлопаточный канал и ударяют со скоростью 40 – 80 м с по выпуклой поверхности соседней лопатки в области косого среза решетки, внося свой вклад в износ этой поверхности. В эту же область могут попадать и частицы с размером менее 10 мкм, движущиеся вблизи периферийного обвода направляющего аппарата и сносимые вторичными течениями пара. Хотя ударная составляющая скорости их и невелика, они могут в некоторой степени интенсифицировать износ лопаток, поскольку, двигаясь с периферийного обвода по спинке лопатки к выходной кромке со скоростью 15 – 20 м с, способны оказывать абразивное воздействие на поверхность металла.
В зависимости от характера движения частиц в межлопаточном канале скорость и угол выхода их из направляющего аппарата изменяются в широких пределах даже для частиц одного размера. Поэтому скорость и место встречи с рабочими лопатками и траектории отражения частиц от лопаток оказываются существенно различными (ðèñ. 2, á). Масса отраженных от рабочих лопаток и движущихся к направляющим лопаткам под углом относительно парового потока частиц составляет 30 – 40%, а их скорость достигает 70 – 140 м с. Отраженные частицы, размеры которых превышают 60 мкм, достигают выходной части выпуклой поверхности направляющих лопаток и воздействуют на них со скоростью 50 – 140 м с в зоне контакта 20 – 25 мм.
При увеличении межвенечного зазора в 2 раза число отраженных от рабочих лопаток и достигающих направляющих лопаток частиц, а также область их соударения с направляющими лопатками существенно уменьшаются. Для частиц с размерами более 100 мкм, обладающих наиболее высокой эрозионной способностью, кратность этого уменьшения достигает 3 – 5 при одновременном некотором снижении скорости и сужении области контакта.
При увеличении межвенечного зазора, во-пер- вых, возрастает путь отраженных от рабочих лопаток частиц окалины в сторону направляющего аппарата. Паровой поток, воздействуя на эти частицы под углом, затормаживает их скорость и снижает или вовсе предотвращает удар по выходным кромкам направляющих лопаток. Одновременно увеличенный межвенечный зазор способствует более быстрому перемещению отраженных от рабочих лопаток частиц в периферийную область за-
18 |
2004, ¹ 4 |
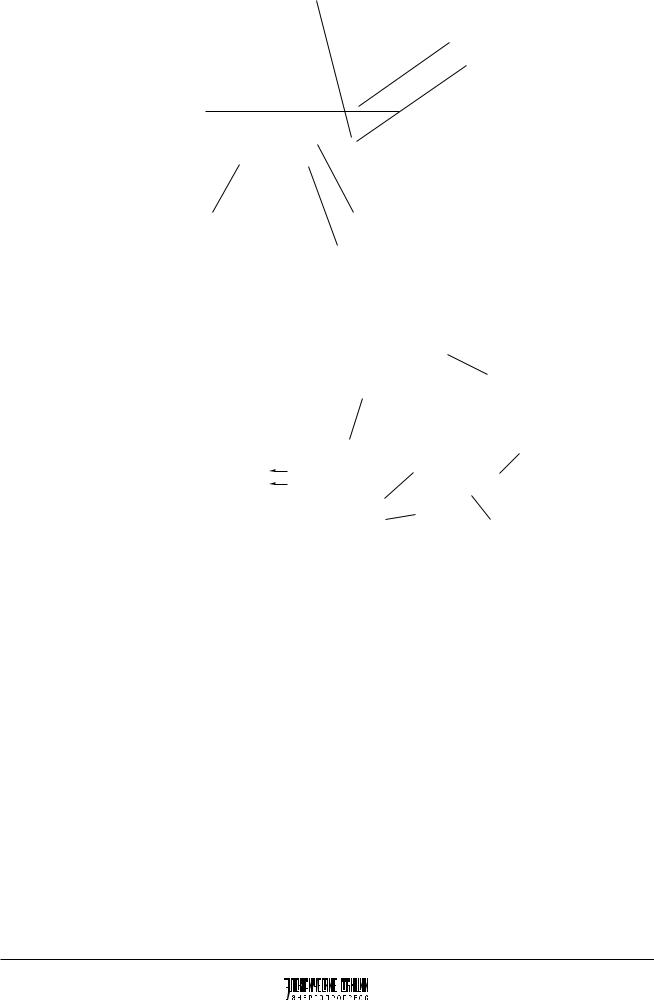
8
5
9
7
6
10
1
11
2
4
3
2
3
9 < 6 G$ 3 ) 3 <F& &,94 544&,84 &,5 > G$
зора, откуда они вместе с паровой продувкой могут быть выведены из проточной части в сепаратор. Во-вторых, увеличенный межвенечный зазор способствует разгону паром твердых частиц до более высокой скорости, и частицы, проникая глубже в межлопаточные каналы рабочих лопаток, соударяются с их входными кромками под меньшими отрицательными углами, а значит, и отражаются под меньшими углами, что изменяет траекторию отлета окалины и увеличивает путь до направляющих лопаток, предотвращая или ослабляя контакт их с выходными кромками лопаток.
Таким образом, расчетный и физический анализ показывает целесообразность увеличения межвенечного зазора для снижения эрозионных нагрузок на направляющие лопатки при наличии в паре твердых частиц.
На базе выполненных многолетних исследований ЦКТИ разработана система защиты ЦСД-1 от эрозионного износа с двумя продувочными контурами (ðèñ. 5). Первый контур отводит с паровой
продувкой частицы окалины из зоны их наибольшей концентрации в камере паровпуска через штуцер дренажа 1 в сепаратор 2, откуда очищенный пар сбрасывается по линии 4 в третий отбор (отбор ПТН). Внутренняя часть второго контура включает увеличенный межвенечный зазор 5, дренажную камеру 10 в корпусе ЦСД-1 под козырьком 6 и диафрагмой 7 14 ступени и внутренний канал от дренажной камеры до штуцера 11 в стенке корпуса. Внешняя часть контура содержит трубу подвода двухфазного потока к сепаратору 2 и линию 4 отвода от него очищенного пара в третий отбор. В нижней части сепараторов 2 предусмотрены накопительные камеры 3 с большим объемом, что обеспечивает непрерывную длительную эксплуатацию продувочных контуров.
Выбор оптимальной величины межвенечного зазора 13 ступени определяется следующим обстоятельством. Согласно исследованиям [13] при увеличении относительного зазора до z* = 1, ãäå z* = z (t1 sin b1), ãäå z – расстояние от выходных
2004, ¹ 4 |
19 |

кромок направляющих лопаток до входных кромок рабочих лопаток вдоль оси турбины; t1 – шаг направляющих лопаток; b1 – угол выхода парового потока из направляющего аппарата. КПД ступени растет в связи с выравниванием скоростей в кромочном следе и улучшением обтекания рабочих лопаток, а потом, при z* > 1, из-за роста потерь трения на ограничивающих поверхностях постепенно падает. Для уменьшения эрозионного износа элементов проточной части межвенечный зазор 13 ступени целесообразно увеличивать (в зависимости от конструкции надбандажного уплотнения и высоты лопаток) до z* = 1,5 2,5, за пределами которого снижение экономичности ступени в результате аэродинамических потерь значительно возрастает.
С учетом особенностей конструкции ЦСД-1 турбины Т-250 300-240 оптимальным для системы защиты (ðèñ. 5) выбран вариант с двукратным увеличением межвенечного зазора 13 ступени. При этом снижение КПД ступени, согласно [13], не превышает 0,2%. Влияние снижения КПД ступени на КПД ЦСД-1 будет еще меньше из-за возврата тепла потерь в последующих ступенях.
Для сравнения: оценка по [14] снижения КПД 13 ступени от повреждения износом периферийного уплотнения дает величину 5%, к которой следует добавить значительные потери от износа лопаток и изменения профиля межлопаточного канала направляющего аппарата, а также потери от дополнительного дросселирования в регулирующем клапане, обусловленные повышенной пропускной способностью первой ступени ЦСД-1.
Для эффективного вывода эрозионного продукта из межвенечного зазора 13 ступени открытый осевой зазор 9 (ðèñ. 5) выполнен не менее двух пятых межвенечного зазора. Повышение экономичности 13 ступени обеспечивается также за счет сокращения протечек пара через осевой зазор между торцом кольца 8 и входной кромкой бандажа рабочих лопаток, который устанавливается равным проектной величине. При этом одновременно повышается надежность надбандажного уплотнения, поскольку уменьшается количество поступающих в него частиц. В нижней зоне кольца 9 предусмотрены щели для возврата в межвенечный зазор 10 под воздействием центробежных сил проникшего в уплотнительную щель эрозионного продукта.
Система защиты (ðèñ. 5) смонтирована на турбине Т-250 300-240 ТЭЦ-23 в период капремонта 2001 г., где она проходит опытно-промышленную эксплуатацию. В период ближайших капремонтов на этой турбине и другой, которая эксплуатируется в аналогичных условиях без системы защиты, будут проведены измерения с применением специальных средств. Это позволит выполнить сравните-
льный анализ состояния проточных частей ЦСД-1 и сделать заключение об эффективности защиты.
Выводы
1.Первые ступени ЦСД-1 турбин Т-250 300-240 подвергаются интенсивному эрозионному износу продуктами распада оксидной пленки тракта пароперегревателя котла, что ведет к снижению экономичности и сокращению срока службы лопаточного аппарата и надбандажных уплотнений до одного – трех межремонтных периодов.
2.Для уменьшения отрицательных последствий эрозионного износа разработана и внедрена на
турбине Т-250 300-240 ТЭЦ-23 система удаления частиц оксидной пленки из камеры паровпуска и первой ступени ЦСД-1.
Список литературы
1.Школьник Г. Т., Дегтев О. Н. Внутреннее окалинообразование в трубах пароперегревателей и эрозионный износ лопаток первых ступеней ЦВД и ЦСД паровых турбин. – Теплоэнергетика, 1970, ¹ 4.
2.Школьник Г. Т., Лужнов М. И., Зеленский В. Г. Пути предотвращения эрозионного износа лопаточного аппарата первых ступеней ЦВД и ЦСД турбин энергоблоков. – Теплоэнергетика, 1972, ¹ 6.
3.Трояновский Б. М. Совершенствование проточных частей паровых турбин. – Теплоэнергетика, 1996, ¹ 1.
4.Паули В. К. Некоторые проблемы организации нейтраль- но-кислородного водного режима котлоагрегатов ТЭС. – Электрические станции, 1996, ¹ 12.
5.Паули В. К. О влиянии режимных факторов прямоточных котлоагргатов на скорость износа элементов проточной части турбин. – Электрические станции, 1996, ¹ 12.
6.Резинских В. Ф., Школьникова Б. Э., Урусова Г. А. Перспективные стали для пароперегревателей котлов СКД. – Теплоэнергетика, 2000, ¹ 10.
7.Крагельский И. В., Добычин М. Н., Комбасов В. С. Основы расчетов на трение и износ. М.: Машиностроение, 1977.
8.À.ñ. 1612167 (СССР). Отсечной клапан паровой турбины
Хаимов В. А., Бакурадзе М. В., Камнев В. И., Воропаев Ю. А. Опубл. в Б. И., 1990, ¹ 45.
9. Ïàò. ¹ 2208682 (РФ). Цилиндр среднего давления паровой турбины Хаимов В. А., Бакурадзе М. В., Кокин В. Н. и др. Опубл. в Б. И., 2003, ¹ 20.
10.Качуринер Ю. Я. Опыт использования программ ППП
“Влажный пар” при проектировании и отладке энергети- ческого оборудования. – Тр. ЦКТИ, 1997, ¹ 281.
11.Вахрушев Н. А. Обобщенное уравнение для коэффициента лобового сопротивления частиц различной формы при относительном движении в безграничной среде. – Химиче- ская промышленность, 1965, ¹ 8.
12.Табаков В., Малак М. Измерение лазером характеристик отскакивания частиц от твердой поверхности для расчета их движения в турбомашинах. – Энергетические машины и установки, 1988, ¹ 4.
13.Аэродинамика проточной части паровых и газовых турбин Кириллов И. И., Яблоник Р. М., Карцев Л. В. и др. М.: Машгиз, 1958.
14.ÐÒÌ 108.020.33-86. Уплотнения лабиринтные стационарных паровых и газовых турбин и компрессоров. Проектирование и расчет.
20 |
2004, ¹ 4 |