
- •Содержание
- •Перспективы применения в ЕЭС России гибких (управляемых) систем электропередачи переменного тока
- •Техническое состояние основного оборудования подстанций и ВЛ и мероприятия по повышению надежности
- •Нормализация уровней напряжения и повышение надежности электрической сети
- •Технология ситуационного отображения данных текущего режима и ее реализация на диспетчерском щите ОДУ Средней Волги
- •Комплекс программ планирования суточных режимов энергообъединений ПРЭС-СУТКИ
- •Совершенствование систем и средств метрологического обеспечения измерений и учета электроэнергии при ее производстве, передаче, распределении и потреблении
- •Дефекты турбогенераторов и методы их диагностики на начальной стадии появления
- •Интеллектуальная информационно-диагностическая система и ее реализация в ОАО Тюменьэнерго
- •Опыт и перспективы применения электроприводов с регулируемой частотой на ТЭС и насосных станциях централизованного теплоснабжения
- •О концепции и практике использования геоинформационных технологий в электрических сетях
- •Учет климатических нагрузок на ВЛ
- •ХРОНИКА

Дефекты турбогенераторов и методы их диагностики на начальной стадии появления
Кузнецов Д. В., èíæ., Маслов В. В., Пикульский В. А., Поляков В. И., Поляков Ф. А., кандидаты техн. наук, Худяков А. Н., Шандыбин М. И., инженеры
ОАО “Научно-исследовательский институт электроэнергетики” (ВНИИЭ)
Как показывает статистика, надежность работы генерирующего оборудования, установленного на электростанциях нашей страны, в целом находится на высоком уровне и соответствует уровню стран с развитой электроэнергетикой. Имеющие место, хотя и редко, аварийные повреждения турбогенераторов, иногда с тяжелыми последствиями, в большинстве случаев являются следствием своевременно не выявленных развивающихся в процессе эксплуатации дефектов, многие из которых обусловлены необратимыми процессами “старения” структурных элементов турбогенераторов. Положение в настоящее время и в перспективе серьезно осложняется тем, что по состоянию на текущий год более 70% турбогенераторов мощностью более 50 МВт, составляющих основу генерирующей мощности тепловых электростанций (ТЭС) России, отработали указанные в стандартах, по которым они изготовлялись, в частности, в различных выпусках ГОСТ-533, минимальные сроки службы, т.е. могут быть существенно изношены. Все это обусловливает актуальность задач продления сроков эксплуатации и обеспечения высокой надежности работы длительно работающих турбогенераторов.
Одно из наиболее эффективных решений этой задачи – разработка и внедрение новых методов технической диагностики. Проведение диагности- ческих обследований с использованием современных методов и привлечением квалифицированных специалистов позволяет получить достоверную оценку технического состояния оборудования; выработать комплекс рекомендаций по техническому обслуживанию и эксплуатации; продлить срок службы и оптимизировать затраты на ремонт и модернизацию оборудования за счет своевременного выявления дефектов и наиболее изношенных узлов и генераторов.
Целью настоящей статьи является освещение проводимых ВНИИЭ совместно с другими организациями и энергосистемами работ для решения этих задач.
Техническое состояние турбогенератора определяется, прежде всего, техническим состоянием его основных узлов, таких как: сердечник и обмотка статора, тело, обмотка и бандажные узлы ротора. Далее приведены дефекты, возникновение и раз-
витие которых определяют надежность эксплуатации и физический ресурс перечисленных узлов.
Основными дефектами сердечника статора являются:
ослабление плотности прессовки и разрушение зубцов крайних пакетов;
повышение вибрации сердечника и разрушение системы его крепления к корпусу генератора; замыкание листов активной стали и возникно-
вение “пожаров железа”; нарушение системы вентиляции вследствие пе-
рекрытия вентиляционных каналов сердечника статора.
В настоящее время значительное число статоров турбогенераторов мощностью 165 – 300 МВт, установленных на ТЭС РАО “ЕЭС России”, имеют существенные дефекты или неудовлетворительное техническое состояние зубцовых зон крайних пакетов. Аварийные отключения вследствие разрушения зубцов крайних пакетов имели место на турбогенераторах Конаковской, Киришской, Ириклинской, Кармановской, Среднеуральской, Сургутской, Гусиноозерской, Невинномысской ТЭС и др.
Наиболее часто необратимые разрушения и аварийные отключения происходят на турбогенераторах с незапеченными крайними пакетами, работающих в маневренных режимах с потреблением реактивной мощности. Вследствие многократных ремонтов зубцовых зон путем установки распорных клиньев на этих статорах в районе “дно паза – нижний стержень” возникают аксиальные зазоры между поверхностью крайнего пакета и нажимными пальцами. В этих зонах происходят интенсивная вибрация крайних листов активной стали, их излом, повреждение изоляции обмотки статора обломками листов (ðèñ. 1).
Серьезные разрушения крайних пакетов и аварийные отключения происходят, хотя и редко, на турбогенераторах, работающих в базовых режимах, в том числе на турбогенераторах с запеченными крайними пакетами [1]. Однако в этом случае повреждения развиваются значительно медленнее.
Основными причинами повышения вибрации сердечника статора в процессе длительной эксплуатации являются недостатки конструкции и технологии его изготовления (недостаточная жесткость сердечника статора, низкая плотность сопряжения призм и сердечника, близость собственных частот
2004, ¹ 8 |
51 |
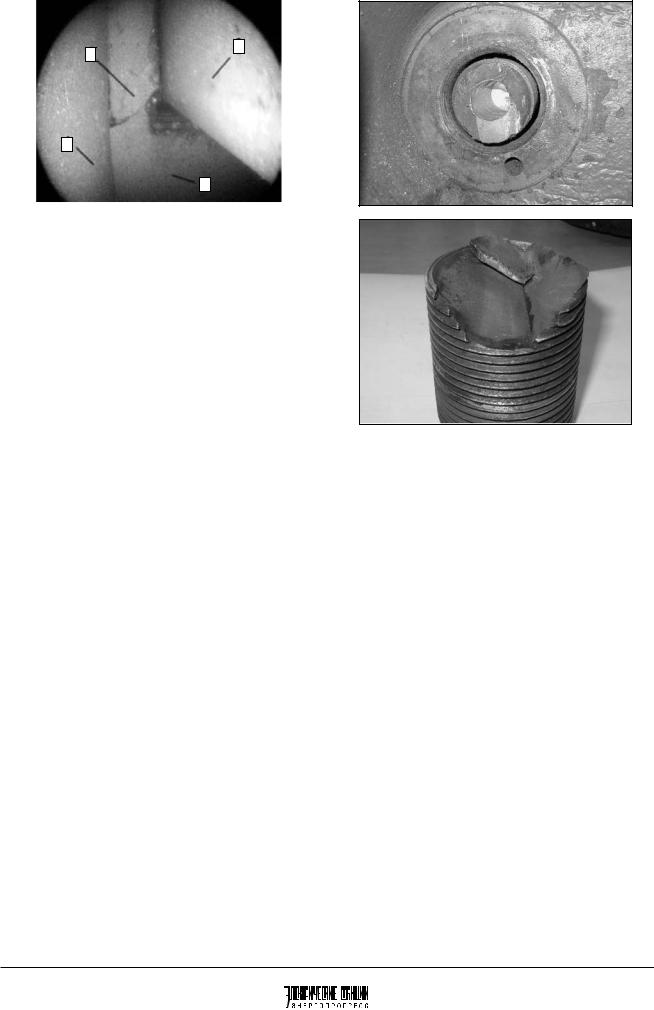
2
1
4
3
9% 7 7 * )
$ 5: .
1 – обломившийся и сместившийся фрагмент активной стали; 2 – стержень обмотки статора; 3 – крайний лист активной стали торцевого пакета; 4 – нажимной палец
конструктивных элементов к двойной оборотной частоте). Причинами развития серьезных разрушений элементов крепления активной стали, как правило, являются несвоевременное выявление и некачественное устранение дефекта на ранней стадии развития, а также работа генераторов, имеющих ослабление сопряжения сердечника с элементами его крепления к корпусу, в режимах с нагрузкой, составляющей 40 – 50% номинального значения, что обусловлено существенным снижением плотности сопряжения в таких режимах. Наиболее серьезные повреждения элементов крепления активной стали статора вследствие повышенной вибрации сердечника происходили на ряде турбогенераторов серии ТГВ мощностью 200 – 300 МВт Рефтинской, Ставропольской, Че- реповецкой, Заинской ГРЭС и др. (ðèñ. 2).
Характерным примером является турбогенератор ТГВ-300, на котором вследствие повышенной вибрации статора произошел обрыв 11 из 30 шеек стяжных призм. Часть оборванных шеек вместе с гайками упала на корзину лобовых частей обмотки статора, нажимная плита статора развернулась и провисла, вызвав опасные механические нагрузки в лобовой части обмотки статора. Быстрому развитию повреждения способствовала работа турбогенератора с нагрузкой около 120 МВт, что составляет менее 50% номинальной мощности.
Эффективным мероприятием по поддержанию удовлетворительного вибрационного состояния статоров и предотвращению разрушения элементов крепления сердечника статора является усиление его связи со стяжными призмами. В то же время на значительном числе длительно работающих генераторов типа ТГВ-300 такие мероприятия проводились уже многократно и эти возможности близки к исчерпанию. Многочисленные случаи, имевшие место в эксплуатации, показывают, что эксплуатация генераторов с неудовлетворитель-
/$* 7 "$
ным вибрационным состоянием и ослабленным сопряжением стяжных призм может в течение короткого времени приводить к необратимому разрушению подвески сердечника и повреждению изоляции обмотки статора.
“Пожары железа”, приводившие к аварийным отключениям и заменам статоров, в последние годы происходили на турбогенераторах ТГВ-300 и ТВМ-500 Рефтинской ГРЭС, ТВВ-320-2 Каширской ГРЭС, ТГВ-200М Нерюнгринской ГРЭС, ТГВ-300 Криворожской ГРЭС. Опасные замыкания в глубине зубцов активной стали выявлены на турбогенераторах ТВВ-200-2А Сургутской ГРЭС-1, ТГВ-200 Заинской ГРЭС, ТВС-63 Волгоградской ТЭЦ-2, резервном статоре турбогенератора типа ТВВ-320-2. В ряде случаев “пожары” железа из-за деградации изоляционных лаковых пленок листов активной стали происходили после 25 – 30 лет эксплуатации генераторов.
Наиболее опасным является повреждение изоляции листов в глубине зубцовой зоны (в районе основания зубца, дна паза или в ярме сердечника), поскольку выявить такой дефект при проведении традиционных испытаний стали статора кольцевым потоком с индукцией 1,0 или 1,4 Тл трудно даже при использовании тепловизионной техники.
Нарушение вентиляции сердечника приводит к ухудшению технического состояния и сокращению срока службы генератора вследствие опасных
52 |
2004, ¹ 8 |

перегревов конструктивных элементов статора и из-за теплового старения изоляции обмотки статора и ротора. В эксплуатации наблюдались случаи нарушения вентиляции из-за некачественного изготовления статоров и несоблюдения правил эксплуатации. Особую опасность нарушение вентиляции представляет для турбогенераторов с воздушным охлаждением, имеющих высокую тепловую нагрузку активных и конструктивных элементов.
Показательным случаем дефекта системы вентиляции статора из-за несоблюдения правил эксплуатации является возникновение обширной коррозии активной стали на спинке сердечника статора ряда турбогенераторов типа ТВВ-320 из-за высокой влажности водорода и низкой температуры технической воды в газоохладителях. Продукты коррозии практически полностью перекрыли вентиляционные каналы сердечника в торцевых частях зон холодного газа (15 – 20 пакетов с каждой стороны сердечника).
Основными дефектами обмоток статоров с длительным сроком службы, определяющими снижение надежности эксплуатации и исчерпание физического ресурса, являются следующие:
для генераторов с косвенным охлаждением
(имеющих в большинстве термопластичную изоляцию обмотки статора):
расслоение и распухание микалентной изоляции;
растворение и вымывание битумной пропитки микалентной изоляции в результате попадания в корпус генератора масла из системы уплотнения вала;
ослабление крепления лобовых частей, их повышенная вибрация и истирание изоляции;
ухудшение вентиляции лобовых частей обмотки из-за распухания микалентной изоляции;
нарушение паяных соединений; перегревы вследствие нарушений в системе ох-
лаждения;
для генераторов с форсированным охлаждением (имеющих в большинстве термореактивную изоляцию обмотки статора):
истирание изоляции, усталостные изломы элементарных проводников, повреждение паяных и гидравлических соединений из-за повышенной вибрации, вызванной ослаблением системы крепления обмотки статора;
перегревы обмотки статора, вызванные закупоркой полых элементарных проводников и гидравлического тракта обмотки;
увлажнение изоляции вследствие течи полых проводников;
тепловые и механические повреждения изоляции из-за разрушения зубцовых зон крайних пакетов.
Чрезвычайно опасным дефектом длительно работающих турбогенераторов является зарождение и развитие усталостных трещин в металле роторов. Можно выделить следующие основные де-
& 4 % 3
фекты, приводящие к разрушению металла ротора, и основные причины, их вызвавшие:
разрушение шеек вала вследствие подкала металла при потере маслоснабжения подшипников;
разрушение по галтельным переходам и кольцевым маслоотбойным канавкам вследствие коррозионного изъязвления металла;
разрушение бочки ротора вследствие подкала металла токами обратной последовательности при длительной работе в недопустимых несимметрич- ных режимах;
разрушение в районе установки центрирующего кольца вследствие наличия концентраторов напряжения и воздействия фреттинг-коррозии.
Усталостные трещины выявлялись на роторах турбогенераторов типа ТВВ мощностью 200, 300, 500 и 1200 МВт, типа ТГВ мощностью 25 и 300 МВт, типа ТВ-60, ТВФ-63, ТВ2-150, ТВМ-300.
Во многих случаях усталостные трещины роторов выявлялись при аварийных остановах, вызванных нарастанием вибраций на генераторных подшипниках. При этом роторы турбогенераторов восстановлению не подлежали. Кроме того, существовала опасность развития повреждения вследствие высоких резонансных вибраций на выбеге турбоагрегата во время останова при прохождении критических оборотов.
Характерный пример выявления опасной трещины в районе установки центрирующего кольца представлен на ðèñ. 3.
За последние 30 лет на ТЭС СССР и России произошло 25 аварийных отключений, обусловленных разрушениями элементов бандажных узлов роторов турбогенераторов. Основными причи- нами, вызывающими повреждения и разрушения бандажных колец роторов турбогенераторов, являются:
2004, ¹ 8 |
53 |
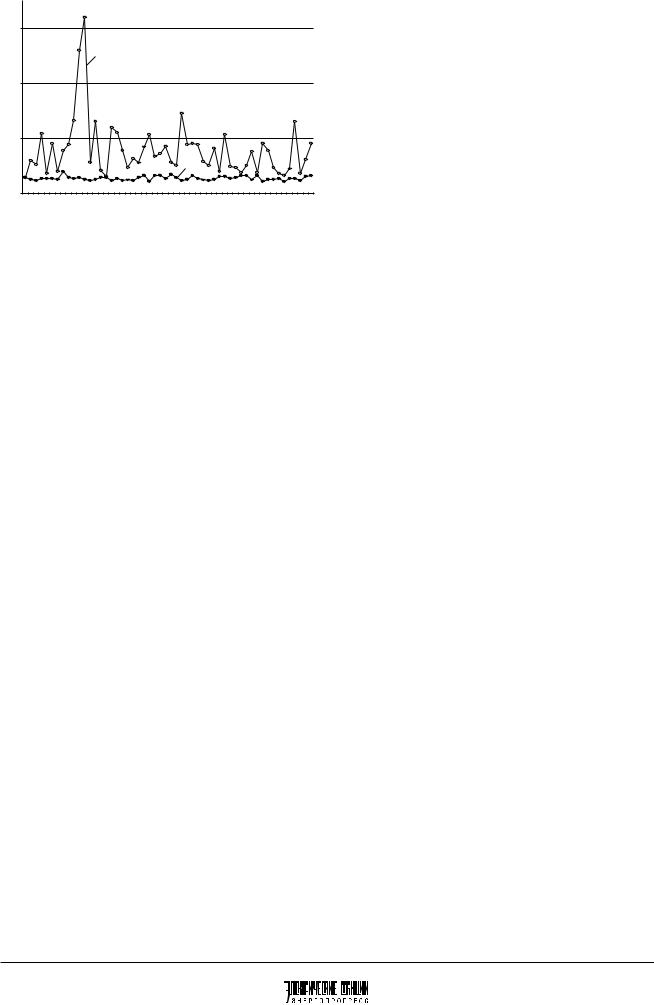
, ìêñ |
|
|
|
|
|
300 |
|
|
|
|
|
|
|
1 |
|
|
|
200 |
|
|
|
|
|
100 |
|
|
|
|
|
|
|
|
|
2 |
|
0 |
|
|
|
|
|
1 |
5 |
15 |
25 |
35 |
45 |
|
|
|
|
|
Номер зубца |
* ! 5 ) " !$ % 7 t "!%: 7 )
7 .
1 – предаварийное состояние зубцов перед проведением ремонта; 2 – состояние зубцов через 4 года после проведения ремонта с использованием УЗК
коррозионное растрескивание под действием влажности, нагревов и механических нагрузок;
подкалы бандажных колец, возникающие в несимметричных режимах работы турбогенераторов;
знакопеременные механические нагрузки, обусловленные вращением ротора, имеющего естественный прогиб от собственного веса.
Из 25 аварийных отключений в 18 случаях происходил разрыв бандажных колец, приводивший к полному разрушению обмоток статора и ротора, диффузора, вентилятора, торцевых щитов и повреждениям сердечника и корпуса статора. Во всех этих случаях турбогенератор не подлежал восстановлению или требовал большого объема ремонтных работ. Во многих случаях разрушения бандажных колец сопровождались выбросом водорода, его взрывом и возгоранием. В отдельных случаях имело место разрушение машинного зала.
Практически все аварийные отключения происходили на турбогенераторах, имеющих бандажные кольца из коррозионно-нестойких марок стали и двухпосадочную конструкцию бандажных узлов, для которых характерен повышенный уровень знакопеременных механических нагрузок.
Обмотка ротора работает под сравнительно низким электрическим напряжением, поэтому основное разрушающее воздействие на нее оказывают механические напряжения, перегревы, загрязнение и увлажнение. Вследствие термомеханических напряжений происходят повреждение витковой изоляции и укорочение витков. Перегревы, загрязнение и увлажнение снижают электри- ческую прочность корпусной и витковой изоляции. Имеется много примеров, когда перечисленные дефекты приводили к аварийным отключениям и серьезным повреждениям роторов. В то же
время, как показывает практика ВНИИЭ, эти дефекты сравнительно легко выявляются в процессе обследования роторов.
Одним из наиболее часто повреждающихся узлов турбогенераторов является щеточно-контакт- ный аппарат (ЩКА). Основные дефекты, которые приводят к отказу ЩКА, это – неравномерное распределение тока по щеткам, биения колец, перегревы и ускоренный износ щеток и контактных колец. Предусмотренные инструкцией по эксплуатации регулярные ревизии ЩКА не гарантируют его безотказной работы, поскольку некоторые дефекты развиваются очень быстро и могут привести к его аварийному повреждению в промежутках между осмотрами. Анализ развития дефектов ЩКА показывает, что практически все опасные дефекты в конечном итоге приводят к повышенному искрению и затем к “круговому огню”, поэтому необходим непрерывный аппаратурный контроль уровня искрения ЩКА. Такая аппаратура успешно применяется за рубежом. ВНИИЭ также имеет возможность оснащать турбогенераторы аппаратурой контроля искрения ЩКА [8], однако внедрение ее на электростанциях идет недостаточными темпами.
Обобщение эксплуатационных данных и опыта проведения обследования показывает, что при выявлении дефектов на ранней стадии развития, своевременном и качественном их устранении, а также при адекватных техническому состоянию режимах работы и ремонтном обслуживании в подавляющем большинстве случаев турбогенераторы могут эксплуатироваться без снижения надежности в течение времени, существенно превышающего минимальные сроки службы. Необходимо отметить, что методы контроля, проведение которых регламентировано нормативными документами, как правило, позволяют выявлять дефекты в такой стадии их развития, что не всегда может обеспечить безаварийную работу генераторов.
Начиная с 1990 г. ВНИИЭ активно проводит работы по диагностическому обследованию турбогенераторов с использованием новых методов диагностики, ориентированных на выявление наиболее значимых дефектов турбогенераторов, в том числе на ранней стадии их появления и развития:
электромагнитный метод выявления замыканий листов активной стали статора при кольцевом намагничивании сердечника с низкой индукцией (0,02 – 0,05 Тл) [3, 6];
ультразвуковой метод контроля плотности прессовки и выявления ослабленных зубцов активной стали сердечника статора [4];
метод контроля вибрационного состояния генератора на основе анализа виброперемещений, виброскоростей и виброускорений, а также их гармонических составляющих в диапазоне 10 – 1000 Гц на корпусе статора, подшипниках ротора и фундаменте при работе генератора;
54 |
2004, ¹ 8 |
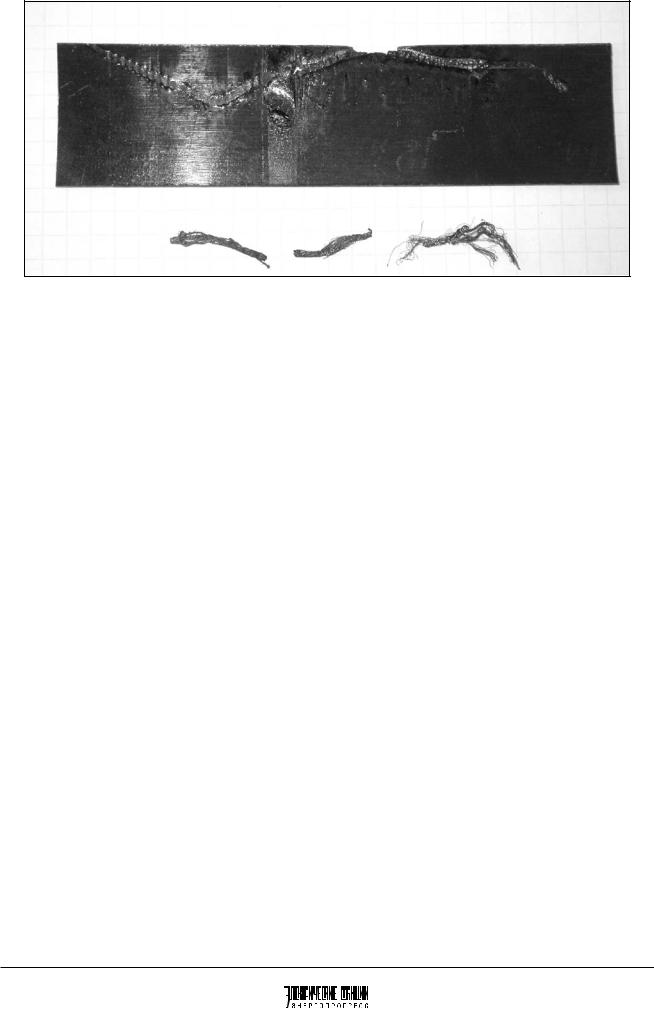
/ * * * * A " 3$ * " * 3)
" ! % 4 56
метод оценки технического состояния сердеч- ника статора на основе эндоскопического осмотра; метод оценки технического состояния обмотки статора на основе контроля частичных разрядов,
импульсных напряжений в нейтрали [7]; метод контроля проходимости каналов водяного
охлаждения и герметичности водяного тракта [9]; метод оценки технического состояния обмоток
статора и ротора по результатам эндоскопического обследования;
метод оперативного контроля исправности ще- точно-контактного аппарата [8] и др.
Высокая эффективность диагностических обследований, проводимых ВНИИЭ, может быть проиллюстрирована следующими данными.
За указанный период времени обследовано более 150 турбогенераторов различных типов и мощностей, эксплуатирующихся в различных режимах работы. В частности, профилактическими комплексными обследованиями охвачены практически все крупные турбогенераторы в Мосэнерго, на Костромской, Кармановской, Ириклинской, Невинномысской, Череповецкой ГРЭС и ряда других. При этом необходимо отметить положительную роль персонала электроцехов, оказывающего всестороннее содействие внедрению новых методов диагностики в эксплуатационную практику.
Благодаря широкому использованию методов контроля сердечников статоров при проведении капремонтов число аварийных отключений из-за разрушения зубцовых зон крайних пакетов и прорезания изоляции обмотки статора обломками листов активной стали сократилось с 3 – 4 случаев в 1993 – 1994 гг. до 1 – 2 случаев в 1995 – 1996 гг. Начиная с 1997 г. по этой причине, несмотря на старение генераторного парка, происходит примерно одно аварийное отключение в 2 года. При- чем все аварийные отключения имели место на
турбогенераторах, не прошедших обследование. Проведенные обследования позволили предотвратить аварии по рассматриваемой причине на турбогенераторах Сургутской, Костромской, Кармановской, Ириклинской ГРЭС, Краснодарской ТЭЦ, ТЭЦ-22, -23, -26 Мосэнерго и ряда других станций.
На основании проведенных обследований разрабатывались рекомендации по восстановлению зубцовых зон крайних пакетов, замене статоров турбогенераторов, вводились необходимые ограничения на работу в режимах потребления реактивной мощности, корректировались сроки выполнения ремонтов с выводом ротора на турбогенераторах Костромской, Ириклинской, Невинномысской ГРЭС, Краснодарской ТЭС и др.
Характерные результаты, иллюстрирующие эффективность мероприятий, выполненных по результатам обследований с использованием современных методов контроля и, в частности, ультразвукового метода контроля плотности прессовки активной стали (УЗК), представлены на ðèñ. 4.
На рассматриваемом турбогенераторе мощностью 300 МВт, находящемся в эксплуатации 17 лет, при выводе в ремонт было выявлено предаварийное состояние торцевых зон активной стали (массовое нарушение запечки зубцов двух крайних пакетов со стороны “КК” и “Т”, ослабление прессовки практически всех зубцов третьего пакета со стороны “КК” и “Т”, опасные выкрашивания примерно 10% запеченных зубцов крайних пакетов, поверхностные повреждения изоляции шести стержней обмотки статора обломками листов активной стали). Использование ультразвукового метода контроля состояния зубцов в процессе ремонта позволило восстановить плотность прессовки и обеспечить ее стабильность.
2004, ¹ 8 |
55 |

Благодаря проведенным обследованиям своевременно выявлялись и устранялись опасные повреждения системы крепления сердечников статоров Гусиноозерской и Новочеркасской ГРЭС, а также замыкания листов активной стали статоров турбогенераторов Сургутской, Невинномысской, Заинской, Ириклинской ГРЭС и Краснодарской ТЭЦ. Причем в двух последних случаях предотвращены тяжелые аварии из-за “пожара” железа.
Традиционные испытания стали статора методом кольцевого намагничивания при индукции 1,0 или 1,4 Тл не обеспечивают полного выявления замыканий листов активной стали даже при использовании тепловизионной техники. Применение при проведении комплексных обследований электромагнитного метода выявления замыкания листов при кольцевом намагничивании с низкой индукцией (0,02 – 0,05 Тл) позволяет надежно контролировать состояние изоляции листов активной стали, а также проводить контроль полноты устранения дефекта непосредственно при проведении ремонтных работ.
Так, благодаря применению электромагнитного метода начальная стадия “пожара железа” в глубине зубца активной стали и недопустимое повреждение корпусной изоляции прилегающего к дефекту стержня обмотки статора были выявлены на турбогенераторе мощностью 165 МВт. На резервном статоре турбогенератора мощностью 320 МВт, прошедшем полную замену обмотки, перед его монтажом на дне паза были выявлены обширные замыкания (ðèñ. 5), которые не были обнаружены при неоднократном проведении традиционных испытаний. В обоих случаях были предотвращены тяжелые аварии турбогенераторов.
Следует также отметить, что в эксплуатации имеют место не только случаи пропуска дефекта при проведении испытаний на потери и нагрев, но и случаи ложного выявления дефекта. Так, на статоре турбогенератора мощностью 60 МВт при проведении традиционных испытаний с использованием тепловизионной техники ошибочно диагностировалась непригодность к дальнейшей эксплуатации сердечника статора из-за паразитных сигналов, которые интерпретировались как интенсивные, мигрирующие по расточке очаги замыканий листов активной стали и не поддавались устранению. Возникновение паразитных сигналов было обусловлено, по-видимому, сильным загрязнением поверхности расточки активной стали. Выполненное обследование с использованием электромагнитного метода выявило отсутствие замыканий и удовлетворительное состояние сердеч- ника статора.
Накопленный ВНИИЭ опыт в проведении вибрационных обследований турбогенераторов позволяет проводить всестороннюю оценку технического состояния статора и ротора, выявлять дефекты системы крепления сердечника к корпусу генера-
тора, крепления генератора к фундаменту, определять причины повышенных вибраций подшипников генератора, а также разрабатывать пути устранения выявленных дефектов.
Эффективным средством контроля технического состояния обмотки статора является техниче- ский осмотр с использованием эндоскопов в комплексе с измерением частичных разрядов в изоляции обмотки статора, что позволяет оценить внутреннюю структуру изоляции, т.е. качество ее изготовления и степень старения, а также выявлять все основные дефекты изоляции обмотки статора на ранней стадии развития. Метод имеет положительный опыт применения как за рубежом, так и в нашей стране. ВНИИЭ с успехом применяет его на ТЭС Мосэнерго, Пермьэнерго, Черепетской, Кармановской, Костромской ГРЭС и др.
Для эффективного выявления закупорок и разгерметизации полых проводников во ВНИИЭ разработаны и применяются аналитический метод тепловой диагностики проходимости каналов водяного охлаждения и метод ранней диагностики герметичности на основе измерения концентрации растворенного в дистилляте водорода [9, 10, 11].
При проведении обследований турбогенераторов с использованием указанных методов обнаружено и устранено более 15 случаев засорения каналов водяного охлаждения [12]. Из них как минимум в трех случаях дефекты проходимости имели уровень, близкий к критическому, и с большой степенью вероятности привели бы к повреждению генераторов при дальнейшей эксплуатации. Предотвращен пробой изоляции обмотки статора турбогенератора ТВВ-320-2 ТЭЦ-26 Мосэнерго из-за ее увлажнения при работе с незначительной разгерметизацией каналов водяного охлаждения.
Например, на двух генераторах типа ТВВ-320-2, установленных на разных электростанциях, в соединениях “шар – конус” фторопластового шланга и фланца водяного коллектора по данным диагностики были обнаружены две дополнительные, не предусмотренные конструкцией уплотняющие прокладки конической формы из пластиката (ðèñ. 6). Допущенное установкой прокладки сужение сечения канала в 9 раз привело к сокращению расхода дистиллята на 25%, что еще не является критическим состоянием для генератора типа ТВВ-320-2. Однако в этом случае существенно возрастает вероятность полной блокировки охлаждения стержня из-за попадания в этот канал мелких посторонних включений, достаточно часто встречающихся в потоке охлаждающего дистиллята (ðèñ. 6).
Накопленный ВНИИЭ опыт диагностических обследований положен в основу действующих эксплуатационных циркуляров и информационных писем Ц-01-91(э), Ц-03-94(э), Ц-06-96, ИП-13-97(э), Ц-03-97(э), Ц-03-98(э), ИП-03-99(э).
56 |
2004, ¹ 8 |
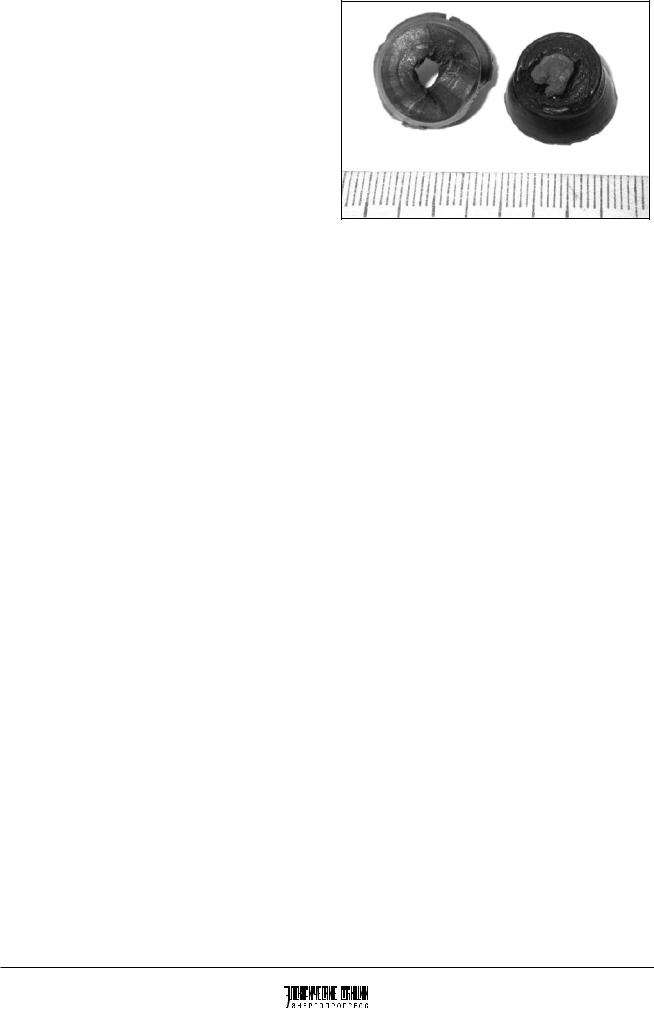
Выполненные комплексные обследования позволили за счет своевременного выявления и каче- ственного устранения дефектов предотвратить аварийные отключения на 14 турбогенераторах, избежать необратимого снижения технического состояния 18 генераторов. В ряде случаев за счет своевременного введения ограничений на допустимые режимы работы и корректировки сроков проведения ремонтов удалось поддержать до замены в работоспособном состоянии 8 статоров.
Выводы
1.Одной из основных причин аварийных отключений и необратимого снижения технического состояния турбогенераторов является несвоевременное выявление и устранение дефектов.
2.Обобщение накопленного опыта позволяет рекомендовать проведение профилактических обследований по методике ВНИИЭ с использованием современных методов диагностики в процессе выполнения капитальных ремонтов как эффективное мероприятие по повышению надежности и уровня эксплуатации, продлению срока службы статоров турбогенераторов, а также оптимизации затрат на ремонт, модернизацию и техперевооружение.
3.Проведение обследований наиболее эффективно на статорах турбогенераторов мощностью 160 МВт и выше, отработавших минимальный установленный срок эксплуатации; на турбогенераторах, систематически работающих в маневренных режимах с потреблением реактивной мощности; на статорах турбогенераторов, подлежащих замене обмотки; а также при принятии решений об очередности и сроках проведения замен или заводских ремонтов статоров турбогенераторов ТЭС.
Список литературы
1. Повреждаемость и контроль зубцовых зон запеченных крайних пакетов стали сердечников статоров турбогенераторов / Бутов А. В., Мамиконянц Л. Г., Пикульский В. А. и др. – Электрические станции, 2001, ¹ 5.
2.Проведение ремонтов турбогенераторов ТЭЦ-22 АО “Мосэнерго” с использованием современных методов диагностики сердечников статоров / Бутов А. В., Каплин В. Н.,
<$ ! 64 * A % !)
$ * ;< > ! + *
* 7 % A )
$
Крылов М. П., Пикульский В. А. – Электрические станции, 2000, ¹ 11.
3. Электромагнитный метод выявления замыканий листов активной стали статора турбогенератора / Бутов А. В., Пикульский В. А., Поляков Ф. А., Шандыбин М. И. – Электрические станции, 1998, ¹ 11.
4.Пикульский В. А., Бутов А. В. Ультразвуковой метод оценки состояния плотности прессовки активной стали статора турбогенератора. – Электрические станции, 1993, ¹ 3.
5.Пикульский В. А., Чистиков А. А., Лившиц А. Л. Стабилизация давления прессования сердечников статоров турбогенераторов. – Электротехника, 1987, ¹ 7.
6.Поляков Ф. А. Выявление замыканий листов активной стали турбогенераторов электромагнитным методом. – Электрические станции, 2002, ¹ 9.
7.Маслов В. В. Контроль состояния изоляции и токоведущих частей вращающихся электрических машин методом измерения частичных разрядов. – Вестник ВНИИЭ-2003.
8.Брауде Л. И., Борозинец Б. В., Маслов В. В. Оперативный контроль исправности щеточно-контактных аппаратов турбогенераторов. – Электрические станции, 1988, ¹ 1.
9.Поляков В. И., Цветков В. А. Тепловая диагностика обмоток статоров мощных генераторов с водяным охлаждением. – Вестник ВНИИЭ-1996.
10.Поляков В. И. Метод и прибор для обнаружения нарушений герметичности системы водяного охлаждения обмотки статора работающего турбогенератора. – Вестник ВНИИЭ-1997.
11.Ненормативные методы контроля технического состояния турбогенераторов / Аникин Ю. М., Колодезев В. Л., Сафонов Н. Н. и др. – Энергетик, 2001, ¹ 8.
12.Поляков В. И. Диагностика технического состояния каналов водяного охлаждения и креплений стержней обмоток мощных турбогенераторов для продления срока их службы. – Электрические станции, 2001, ¹ 10.
2004, ¹ 8 |
57 |