
- •ЭКОНОМИКА И ЭНЕРГЕТИКА
- •Методические особенности обоснования вариантов обновления объектов электроэнергетики
- •ТЕПЛОВЫЕ ЭЛЕКТРОСТАНЦИИ
- •Результаты внедрения системы автоматического пуска котлов-утилизаторов блока ПГУ-450 ЗАО “Северо-Западная ТЭЦ”
- •Способы повышения надежности топочных экранов котлов
- •Ремонт барабана котла ТГМЕ-206, поврежденного сквозными трещинами, и оценка его работоспособности
- •ЭНЕРГОСИСТЕМЫ И ЭЛЕКТРИЧЕСКИЕ СЕТИ
- •Способ автоматической ликвидации асинхронного режима
- •Применение статических компенсаторов для регулирования напряжения на подстанциях 330 и 500 кВ
- •Уравнительные токи при параллельной работе трансформаторов
- •ОБМЕН ПРОИЗВОДСТВЕННЫМ ОПЫТОМ
- •Некоторые характеристики внутритрубных отложений в барабанных котлах высокого давления
- •ХРОНИКА
- •5-я Международная выставка “Ведомственные и корпоративные сети связи 2002”
- •ЭНЕРГОХОЗЯЙСТВО ЗА РУБЕЖОМ
- •Паротурбинные энергоблоки США (итоги 2001 г.)
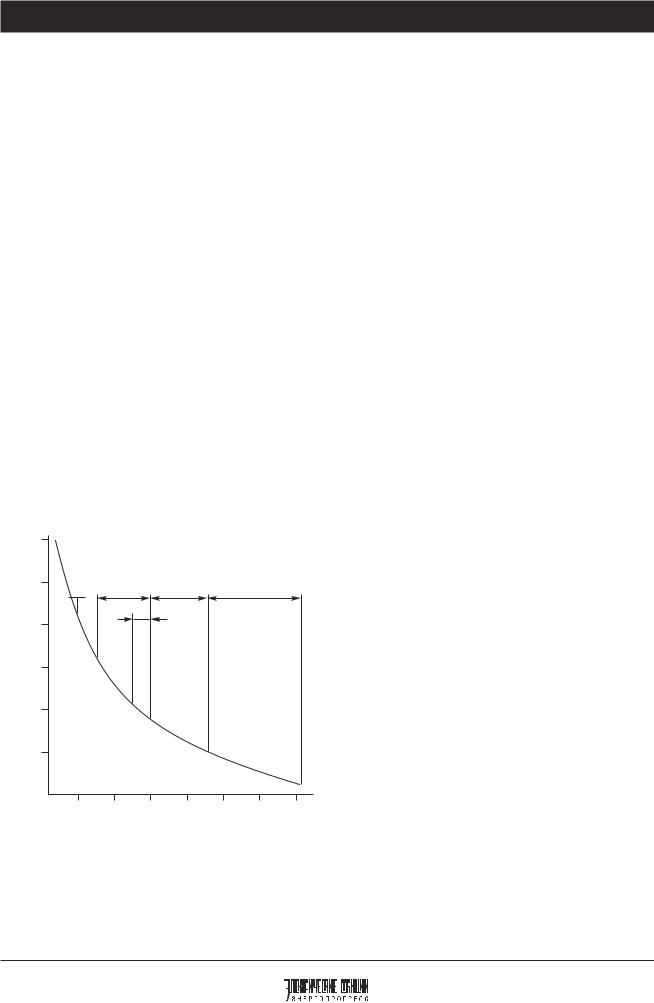
ОБМЕН ПРОИЗВОДСТВЕННЫМ ОПЫТОМ
Некоторые характеристики внутритрубных отложений в барабанных котлах высокого давления
Василенко Г. В., доктор техн. наук, Рывкин Г. Е., èíæ., Сутоцкий Г. П., êàíä. òåõí. íàóê, Мурзин М. А., èíæ.,
Семенов А. С., èíæ., Беляков И. И., Лашицкий А. П., кандидаты техн. наук, Елецкая М. С., èíæ.
Инженерно-аналитический центр АО Ленэнерго – АО “НПО ЦКТИ” – Северная ТЭЦ АО Ленэнерго
Значение удельной загрязненности труб топоч- ных экранов и химический состав отложений систематически требуются эксплуатационному персоналу электростанций для оценки необходимости проведения химической очистки котлов и выбора ее технологии. На ðèñ. 1 показаны обобщенные отечественные и зарубежные рекомендации по предельно допустимому количеству отложений [1]. Одновременно указан фактический диапазон тепловых нагрузок топочных экранов для традиционных и более теплонапряженных конструкций котлов при сжигании различных видов топлива,
|
1200 |
|
|
|
|
1000 |
|
|
Ìòí |
|
T |
Ó |
Ì |
|
2 |
|
à |
|
|
ã/ì |
|
|
|
|
800 |
|
|
|
|
загрязненность, |
|
|
|
|
600 |
|
|
|
|
|
|
|
|
|
Удельная |
400 |
|
|
|
|
|
|
|
|
|
200 |
|
|
|
|
0 |
|
|
|
|
200 |
400 |
600 |
800 |
|
|
Тепловая нагрузка, кВт/м2 |
|
+ % " , " ) % % 5 * *4 " ! % ) E F7
! 1 * * ! ! "
) % + ) " % !
% * % ! "
Ò – òîðô; Ó – уголь; Ã – ãàç; Ì – мазут; Ìòí – мазут для котлов с повышенным теплонапряжением топочных экранов
установленный на основе испытаний, выполненных НПО ЦКТИ.
Как видно из ðèñ. 1, допустимая удельная загрязненность экранных труб барабанных котлов высокого давления ограничена, а для высокофорсированных котлов она еще более снижается. Вместе с тем, представляется полезным осветить нестандартный опыт эксплуатации подобного котла при повышенной удельной загрязненности, в котором преломилось несколько практически важных аспектов формирования и удаления отложений.
На одной из электростанций котельным отделом НПО ЦКТИ проводилось исследование температурного режима топочных экранов газомазутного котла ТГМ-96Б, работающего в блоке с турбиной Т-100-130. При этом было установлено, что температура металла труб остается в допустимых пределах при возрастании удельной загрязненности до 1000 г/м2, существенно превышающей регламент [2].
Химический состав средней пробы отложений, %: SiO2 1,2, Al2O3 отсутствие, Fe2O3 56,6, CaO 7,4, MgO 6,7, CuO 8,0, ZnO 9,1, SO3 0,4, P2O5 11,1, потери при прокаливании – плюс 0,81. При этом в нижнем слое отложений содержался 31% оксидов цинка, а в верхнем слое – 31,5% металлической меди. Последнее обстоятельство в сочетании с меньшей пористостью отложений при работе на газе [3] и обусловило допустимый уровень температуры металла труб при их высокой удельной загрязненности. Указанные ингредиенты характеризуются повышенной теплопроводностью по сравнению с типовыми составляющими отложений – оксидами железа и фосфатами кальция и магния. Так, при температуре 300°С коэффициент теплопроводности магнетита равен 3,47 Вт (м К), в то время как для оксида цинка он составляет 13,1 Вт (м К), а для металлической меди коэффициенты равны 372 Вт (м К) [4].
48 |
2003, ¹ 5 |

В опытном порядке электростанциям было разрешено продолжить испытания под руководством НПО ЦКТИ при автоматическом контроле температуры металла труб топочных экранов.
Комментируя подобные случаи повышенной теплопроводности отложений, необходимо отметить, что они являются следствием интенсивной коррозии латунной трубной системы теплообменных аппаратов тракта регенерации и сетевых подогревателей.
Кроме того, надежная эксплуатация экранных труб определяется не только теплопроводностью отложений, но и гидродинамикой потока воды в трубах. Например, известен случай повреждений труб солевого отсека котла БКЗ-420-140 ПТ-2 вследствие интенсивной подшламовой коррозии при аналогичном составе отложений и характере распределения в них соединений цинка и меди [5]. Повреждения находились в районе люка, расположенного в зоне максимальных тепловых потоков и связывались с расслоением пароводяной смеси при негативном влиянии ошиповки топочных экранов.
При накоплении повышенного количества отложений возникает необходимость решения и сопутствующей проблемы – выбор технологии химической очистки котла. В свое время в Ленэнерго при содействии Уралтехэнерго была внедрена и достаточно эффективно использовалась при нормальной и близкой к ней удельной загрязненности очистка барабанных котлов высокого давления раствором серной кислоты по методу “травления”. В новой ситуации при высоком уровне загрязненности требовалось уточнение числа стадий кислотной очистки и исходной концентрации кислоты.
Решение этой проблемы осложняется существенно более низкой константой диссоциации серной кислоты по сравнению с соляной и необходимостью учета сульфатно-кальциевого отношения в рабочем растворе в процессе очистки.
Ранее, в 50-х годах, применение серной кислоты для очистки котлов не рекомендовалось [6] в связи с возможностью образования малорастворимого соединения – сернокислого кальция, препятствующего дальнейшему взаимодействию кислоты с накипью. В настоящее время накоплен определенный положительный опыт проведения эксплуатационных химических очисток барабанных котлов серной кислотой. Однако в связи с отсутствием обобщающих нормативных материалов для барабанных котлов некоторые рекомендации по удалению повышенного количества отложений могут быть почерпнуты из соответствующего руководящего документа [7], разработанного для водогрейных котлов.
Согласно [7] при удельной загрязненности топочных экранов до 1000 г м2 допускается одностадийная очистка котла 5%- или 10%-ным раствором серной кислоты при использовании соответственно методов циркуляции или “травления”. Принципиально важно отметить при этом, что в
поверхностинеотмытой |
100 |
|
|
|
|
|
|
|
|
|
образца,% |
|
|
|
|
|
|
|
|
|
|
|
80 |
|
|
|
|
|
|
|
|
|
|
60 |
|
|
|
|
1 |
|
|
|
|
|
|
|
|
|
|
|
|
|
|
|
|
40 |
|
|
2 |
|
|
|
|
|
|
Äîëÿ |
20 |
|
|
|
|
|
|
|
|
|
0 |
|
|
|
|
|
|
|
|
|
|
|
|
|
|
|
|
|
|
|
|
|
|
0 |
1 |
2 |
3 |
4 |
5 |
6 |
7 |
8 |
9 |
|
|
|
|
Продолжительность очистки, ч |
|
|
$ 2++ , * %& * * * ! ! " " G H % " # , 1
) !
концентрация кислоты 10%, температура раствора 55 5°С; 1 – исходная удельная загрязненность образцов 1000 г м2; 2 – òî æå 1600 ã ì2
обоих случаях содержание кальция в отложениях ограничивается 10%.
Для обоснования требуемой концентрации серной кислоты, к сожалению, не представляется возможным использовать термодинамический подход вследствие высокой ионной силы промывочного раствора. Например, уже при расчете растворимости сернокислого кальция в воде [8] полученное теоретическое значение оказывается заниженным в несколько раз по сравнению с экспериментальным. Кроме того, известную неопределенность вносит различие состава отложений в барабанных и водогрейных котлах. Поэтому наиболее надежные сравнительные данные могут быть получены при проведении лабораторных опытов по очистке образцов труб, вырезанных из барабанного котла.
Некоторые результаты экспериментальной проверки рекомендаций [7] показаны на ðèñ. 2. Было установлено, что регламентируемая для водогрейных котлов концентрация серной кислоты до 10% и в данном случае не встречает препятствий для эффективного удаления отложений. Следует отметить при этом важность правильного выбора ингибитора коррозии для используемой кислоты [9].
Полученные положительные результаты лабораторных опытов согласуются с данными по химическому составу отложений в барабанных котлах высокого давления, свидетельствующими, что содержание кальция, как правило, не превышает указанного в [7] порогового значения 10% (таблица).
Обращает на себя внимание, однако, то обстоятельство, что содержание кальция в отложениях близко или равно содержанию магния. Принимая во внимание соотношение этих элементов в исходной воде водоисточника (3 : 1), можно ожидать в первом приближении, что до 30% ионов кальция, поступающих с питательной водой, осаждаются в котле. Этот вывод является достаточно неожиданным, учитывая, что режим фосфатирования при-
2003, ¹ 5 |
49 |

( : " * ! # * * ! ! "
|
|
|
Котел |
|
|
|
Параметр |
|
|
|
|
|
|
ÁÊÇ-320-140 |
ÒÏ-84 |
|
ÒÃÌ-96Á |
|||
|
|
|||||
|
|
|
|
|
|
|
Топочный экран |
Левый боковой |
Левый боковой |
Задний |
|
Фронтовой |
Левый боковой |
|
|
|
|
|
|
|
Отсек |
Чистый |
Солевой |
Чистый |
|
Чистый |
Чистый |
|
|
|
|
|
|
|
Фактическое содержание, %: |
|
|
|
|
|
|
CaO |
12,1 |
8,2 |
7,3 |
|
8,7 |
7,4 |
MgO |
10,3 |
11,7 |
14,0 |
|
13,7 |
6,7 |
P2O5 |
16,2 |
19,8 |
16,2 |
|
17,6 |
11,1 |
Теоретически необходимое коли- |
|
|
|
|
|
|
чество P2O5, % [суммарно для |
22,3 |
20,6 |
22,5 |
|
23,4 |
13,5 |
Ña3(PO4)2 è Mg3(PO4)2] |
|
|
|
|
|
|
Äîëÿ P2O5, которой не хватает до |
27,4 |
3,9 |
28,0 |
|
24,9 |
17,7 |
теоретически необходимогоколи- |
|
|||||
чества, % |
|
|
|
|
|
|
|
|
|
|
|
|
|
зван предупреждать кальциевое накипеобразование. При этом pH котловой воды в чистом отсеке целесообразно поддерживать равным 9,6 – 9,8 для формирования гидроксилапатита кальция.
Подобная картина наблюдается в котлах всех электростанций энергосистемы, что дает основание полагать недостаточно совершенным процесс перемешивания поступающей питательной воды с раствором тринатрийфосфата. Об этом свидетельствует также соотношение в составе отложений кальция, магния и фосфора.
Учитывая существенно более высокую растворимость фосфата кальция по сравнению с гидроксилапатитом кальция [4] и условия образования серпентина [10], можно предполагать, что кальций и магний присутствуют в отложениях в виде ортофосфатов. В этом случае для чистого отсека фиксируется недостаток P2O5 до теоретически необходимого значения по сумме CaO и MgO, достигающий 20% и более (таблица). Следовательно, кальций в отложениях частично не связан с фосфатионом. Это явление характерно для всех барабанных котлов высокого давления и не может быть объяснено только наличием присосов охлаждающей и сетевой воды.
О возможности протекания рассматриваемых процессов свидетельствует и конструктивное исполнение внутрикотловых устройств. В частности, следует учитывать, что через определенный период времени торцевые участки коллектора фосфатирования оказываются полностью забитыми отложениями, суммарно до 20 – 25% длины (60% оксидов железа и 10% P2O5), что приводит к нарушению распределения фосфатов по длине барабана.
В связи с изложенным авторами предложены соответствующие технические решения по повышению эффективности внутрикотловой обработки воды.
Выводы
1.Нормативные рекомендации по предельно допустимому количеству отложений в топочных экранах котлов базируются на опыте эксплуатации при типовом составе отложений, имеющих достаточно низкую теплопроводность. Случаи повышенной теплопроводности отложений связаны с интенсивной коррозией латунных трубных систем теплообменных аппаратов докотлового тракта и, как следствие, присутствием в составе отложений повышенного количества продуктов коррозии – соединений цинка и меди.
2.Необходимо обобщение данных по составу отложений в барабанных котлах высокого давления и технологии их химической очистки раствором серной кислоты с разработкой соответствующего нормативного документа.
Список литературы
1.Василенко Г. В., Сутоцкий Г. П. Предельно допустимая внутренняя загрязненность топочных экранов барабанных котлов высокого давления. – Теплоэнергетика, 1985,
¹5.
2.ÐÄ 34.37.306-87. Методические указания по контролю состояния основного оборудования электрических станций, определению качества и химического состава отложений.
3.Сутоцкий Г. П. Вода – причина аварий в энергетике. 130 случаев из практики. Санкт-Петербург: АО Ленэнерго, 2001.
4.Василенко Г. В. Фазовый состав и надежность эксплуатации барабанных котлов. – Электрические станции, 1990,
¹9.
5.Сутоцкий Г. П., Верич В. Ф., Межевич Н. Е. О причинах повреждений экранных труб солевых отсеков котлов ÁÊÇ-420-140 ÏÒ-2. – Электрические станции, 1991, ¹ 11.
6.Шапкин И. Ф. Водоподготовка на тепловых электростанциях. М. – Л.: Госэнергоиздат, 1954.
7.ÐÄ 34.37.402–96. Типовая инструкция по эксплуатационным химическим очисткам водогрейных котлов.
8.Справочник химика-энергетика, т. 1. М.: Энергия, 1972.
9.Василенко Г. В., Мурзин М. А. Ингибиторы коррозии для химических очисток котлов. – Электрические станции, 2000, ¹ 7.
10.Сутоцкий Г. П., Рабкина М. Б., Цветков А. В. Кремнемагниевые отложения в пиковых подогревателях сетевой воды. – Теплоэнергетика, 1991, ¹ 10.
50 |
2003, ¹ 5 |
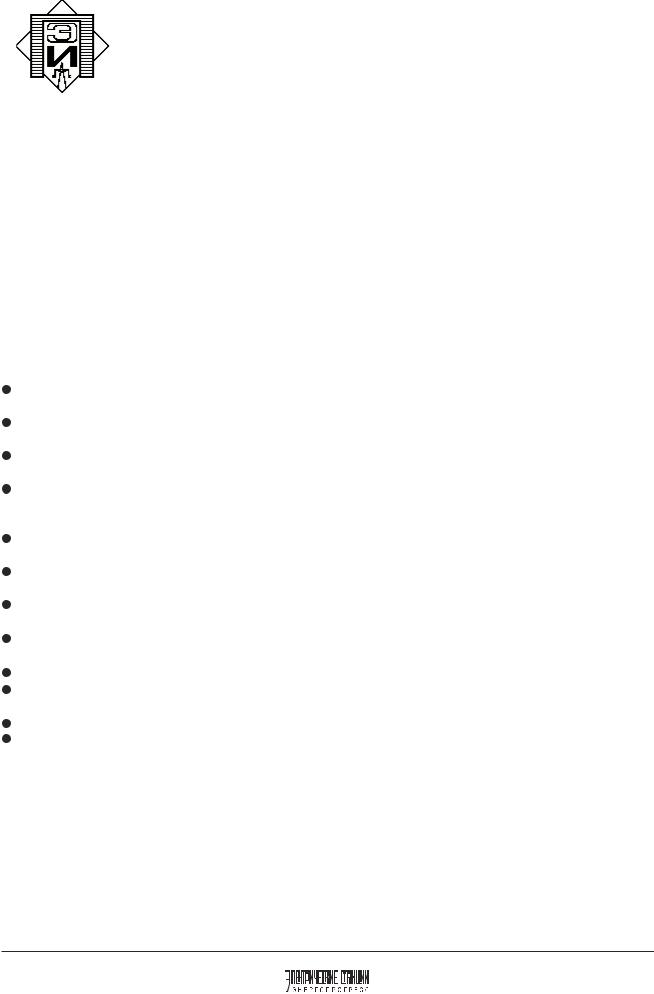
ПЭИПК
Государственное образовательное учреждение
дополнительного профессионального образования
ПЕТЕРБУРГСКИЙ ЭНЕРГЕТИЧЕСКИЙ ИНСТИТУТ
повышения квалификации руководящих работников и специалистов
Министерства энергетики Российской Федерации
ПЭИпк – базовое образовательное учреждение Министерства энергетик и Российской Федерации. Институт аккредитован и действует на основании государственной лицензии Министерства образования России. Начало его деятельности совпадает с началом реализации плана ГОЭЛРО. Работа института, прерванная войной, была восстановлена решением Правительства СССР в 1952 году.
Ежегодно в институте и его филиалах повышают квалификацию более 2,5 тысяч специа- листов-энергетиков топливно-энергетического комплекса, промышленности, строительства, транспорта, сельского и жилищно-коммунального хозяйства. Более подробную информацию можно найти в сети Internet: www.peipk.spb.ru
ПО РЕЗУЛЬТАТАМ ОБУЧЕНИЯ СЛУШАТЕЛЯМ ВЫДАЮТСЯ ДОКУМЕНТЫ ГОСУДАРСТВЕННОГО ОБРАЗЦА
ПОДРАЗДЕЛЕНИЯ ПЕТЕРБУРГСКОГО ЭНЕРГЕТИЧЕСКОГО ИНСТИТУТА ПОВЫШЕНИЯ КВАЛИФИЦАЦИИ РУКОВОДЯЩИХ РАБОТНИКОВ И СПЕЦИАЛИСТОВ
Кафедра «Электроэнергетического оборудования электрических станций, подстанций и промышленных предприятий» (ЭЭСП), т. (812) 371-83-50, факс 373-90-24. E-mail: eesp@peipk.spb.ru Кафедра «Эксплуатации тепломеханического оборудования» (ЭТМО), т. (812) 373-20-43, 373-90-25, факс 373-22-61. E-mail: etmo@peipk.spb.ru
Кафедра "Диагностики энергетического оборудования" (ДЭО), т. (812) 371-83-52, 373-90-20, факс 373-90-21. E-mail: iec@peipk.spb.ru
Кафедра «Диспетчерского управления электрическими станциями, сетями и системами» (ДУЭС), т. (812) 279-42-29, АТС ОАО «Ленэнерго» 50-27. E-mail: dues@peipk.energo.ru;
Internet: www.dues.spb.ru
Кафедра «Релейной защиты и автоматики электрических станций, сетей и энергосистем» (РЗИА), т. (812) 277-50-33, т/факс 277-13-37. E-mail: rza@peipk.energo.ru
Кафедра «Систем связи топливно-энергетического комплекса» (ССТЭК), т. (812) 151-23-32, т/факс 151-31-91, E-mail: sstek@peterlink.ru
Кафедра «Экономики и организации управления в энергетике» (ЭОУЭ), т. (812) 145-96-24, 145-73-09, т/факс 151-25-52. E-mail: peipk-econ@peterlink.ru
Кафедра «Энергетического надзора и энергосберегающих технологий» (ЭНЭТ), т. (812) 373-90-27, 373-90-28, т/факс 373-21-43, E-mail: peipk-enet@peterlink.ru Факультет целевого обучения (ФЦО), т. (812) 373-18-26, 373-19-26, 373-90-29
Камский филиал. 423803, Татарстан, г. Набережные Челны, Челнинский пр., 7, т. (8552) 46-71-11, 33-00-96, ò/ôàêñ (8552) 46-68-37, 33-00-96 Челябинский филиал. 454084, г. Челябинск, ул. Набережная, 5, т. (3512) 35-35-84, ò/ôàêñ 35-46-71
Новосибирский филиал. 630007, г. Новосибирск, Пристанский пер., 4, т. (3832) 23-95-12, т/факс 23-96-77. E-mail: nfpaipk@online.sinor.ru; Internet: www.sinor.ru/nfpaipk
ИНСТИТУТ ИМЕЕТ СОБСТВЕННЫЕ КОРПУСА ДЛЯ ОБУЧЕНИЯ И ПРОЖИВАНИЯ СЛУШАТЕЛЕЙ
Наш адрес: 196135, Санкт-Петербург, Авиационная ул., 23 ПЕТЕРБУРГСКИЙ ЭНЕРГЕТИЧЕСКИЙ ИНСТИТУТ ПОВЫШЕНИЯ КВАЛИФИКАЦИИ (ПЭИпк)
Планово-договорная служба: тел. (812) 373-61-74, т/факс (812) 371-83-53, факс (812) 108-39-50. E-mail: pdo@peipk.spb.ru. Internet: www.peipk.spb.ru тел. администрации гостиницы «Энергетик» (812) 151-25-59.
2003, ¹ 5 |
51 |