
Учебники и учебные пособия / Конструирование и расчет элементов колонных аппаратов. Учебное пособие
.pdf Рис. 2.5. Тарельчатый аппарат с прямоточными контактными устройствами: 1—стакан, 2—тарелки, 3—труба, 4—переливная труба, 5— перегородки.
Газ поступает в кольцевой зазор между трубой 3 и стаканом 1;
захватывая жидкость, вытекающую из этого стакана, газ движется вверх по
кольцевому зазору между трубами 3 и 4, а жидкость поднимается в виде пленки
по наружной поверхности переливной трубы 4. Газо-жидкостной поток по выходе из зазора между трубами 3 и 4 ударяется в дно вышележащей тарелки и поворачивает вниз; при этом капли жидкости отделяются от газа.
Жидкость по переливной трубе стекает на нижележащую тарелку, а газ поступает в трубу 3, закрепленную на вышележащей тарелке. Перегородка 5 препятствует попаданию капель жидкости на поверхность трубы 3, откуда они могли бы быть унесены потоком газа [24].
3 КОЛОННЫ С ПОВЕРХНОСТЬЮ, ОБРАЗУЕМОЙ В ПРОЦЕССЕ ДВИЖЕНИЯ ФАЗ
3.1 КОНСТРУКЦИЯ РАСПЫЛИТЕЛЬНЫХ КОЛОНН
На рис. 3.1 показаны некоторые типы распыливающих аппаратов, выполненных в виде полых колонн [24]. Газ в них движется обычно снизу вверх, а жидкость подается через расположенные в верхней части колонны распылители с направлением факела распыла сверху вниз (рис. 3.1,а) или под некоторым углом к горизонтальной плоскости (рис. 3.1,б).
Во многих случаях, особенно при большой высоте колонны, распылители
располагают в несколько ярусов. При этом факелы распыла направляют сверху
вниз или под углом к горизонтальной плоскости (см. рис. 3.1,б), либо снизу
вверх. Применяют также комбинированную установку распылителей: часть факелом вверх, а часть — факелом вниз.
11
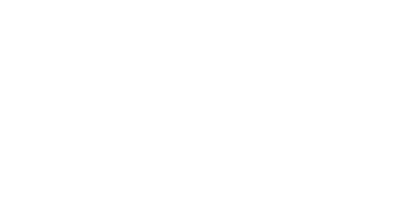
Рис. 3.1. Полые распиливающие аппараты: а — факел распыла направлен вниз, б
—факел распыла направлен под углом (двухрядное расположение форсунок), в - с пережимом в нижней части.
Вполом аппарате, где распылители с направлением факела распыла
сверху вниз расположены в один ярус в верхней части аппарата, теоретически
осуществляется противоток (при движении газа снизу вверх). Однако
вследствие циркуляции и перемешивания газа такие аппараты по характеру контакта газа и жидкости ближе к аппарату с полным перемешиванием газа и эффективная движущая сила в них ниже, чем при противотоке.
Вмногоярусных полых аппаратах (при вводе в распылители каждого яруса свежей жидкости), а также в аппаратах с направленным вверх факелом распыла противоток отсутствует; однако при этом эффективная движущая сила примерно такая же, как и в противоточпых аппаратах с одним ярусом распылителей. В то же время наличие нескольких ярусов распыления ведет к повышению эффективности аппарата.
Врассмотренных типах полых аппаратов газ распределяется неравномерно, что снижает их эффективность. Предложено несколько
конструкций, позволяющих улучшить распределение газа. На рис. 3.1,в
изображен аппарат с пережимом в нижней части. Через отверстие в пережиме газ проходит со сравнительно большой скоростью (до 6—10 м/с), что способствует более равномерному распределению его вследствие добавочного сопротивления в пережиме. Добавочное сопротивление может быть создано также тонким слоем насадки, отделяющим входящую струю газа от основного
объема аппарата.
Полые распыливающие аппараты отличаются простотой конструкции и низкой стоимостью; они обладают малым гидравлическим сопротивлением и могут применяться при сильно загрязненных газах. При использовании
форсунок соответствующей конструкции полые аппараты могут работать и в случае загрязненных жидкостей.
Основной недостаток полых аппаратов — невысокая эффективность,
обусловленная перемешиванием газа и плохим заполнением объема факелом распыленной жидкости. В результате объемный коэффициент массопередачи и число единиц переноса в этих аппаратах невелики; скорость газа в них должна быть низкой (до 1 м/с) во избежание уноса распыленной жидкости с газом.
Полые аппараты неудовлетворительно работают при низких плотностях
12

орошения, а количество подаваемой жидкости трудно поддается
регулированию. Кроме того, расход энергии на распыление жидкости довольно высок (0,3—1 квт*ч на 1 т распыляемой жидкости).
Из-за указанных недостатков полые аппараты имеют довольно
ограниченное применение.
Из многочисленных типов форсунок, используемых для распыления жидкости, в полых аппаратах применяют главным образом механические центробежные и ударные форсунки. Эти форсунки производят распыление за счет энергии жидкости, подаваемой под избыточным давлением 0.2—0.3 МПа. В центробежных форсунках распыление происходит под действием
центробежной силы, развиваемой при вращении жидкости, вызванном либо ее
тангенциальным вводом (рис. 3.2,а), либо движением по спиральным каналам (рис. 3.2,б). В ударных форсунках распыление происходит или в результате удара струи жидкости о препятствие (рис.3.2,в), или при взаимном ударе двух
жидких струй (рис. 3.2,г).
Рис. 3.2. Форсунки: а — центробежная с тангенциальным вводом жидкости; б — с винтовым вкладышем; в — ударная; г — с взаимным ударом двух струй.
В полых распыливающих аппаратах скорость газа нельзя значительно повысить, так как это вызвало бы унос с ним большей части распыленной
жидкости. В случае прямотока газа и жидкости процесс проводят при больших
скоростях газа (20—30 м/сек и выше), причем вся жидкость уносится с газом и отделяется от него в отдельном сепарационном устройстве.
3.2 КОНСТРУКЦИЯ ИНЖЕКТОРНЫХ (СКОРОСТНЫХ ПРЯМОТОЧНЫХ) КОЛОНН
Рабочий объем скоростных прямоточных распыливающих аппаратов
обычно имеет форму трубы Вентури (поэтому такие аппараты часто называют аппаратами Вентури) [24]. Этот объем состоит (рис. 3.3) из сужающейся части
(конфузора), узкой части (горловины) и расширяющейся части (диффузора). Жидкость подают в горловину или в конфузор. Пройдя с большой скоростью
через горловину, газ поступает в диффузор; здесь скорость газа постепенно
снижается, после чего он направляется в сепарационное устройство. В
диффузоре кинетическая энергия газа переходит в энергию давления с
минимальными потерями.
На рис. 3.3 показаны некоторые типы аппаратов Вентури. В аппарате, изображенном на рис. 3.3,а, жидкость подается в горловину 1 через
расположенные по ее периферии отверстия и отделяется от газа в циклоне 2. На рисунке изображена труба Вентури прямоугольного сечения; применяют
13

аппараты такого же типа и с круглыми трубами. В аппарате, приведенном на
рис. 3.3,б, осуществляется центральный ввод жидкости через сопло 3. Сепарационным устройством является бак 4, на крышке которого установлена труба Вентури. Аппараты Вентури, показанные на рис. 3.3, называют
форсуночными, поскольку жидкость вводят в них через форсунки (сопла).
Такие аппараты могут иметь вертикально или горизонтально расположенные трубы Вентури.
Рис. 3.3. Форсуночные аппараты Вентури: а — с периферийным вводом жидкости; б — с центральным вводом жидкости; 1 — горловина с отверстиями, 2 — циклон, 3 — сопло; 4 — бак.
Рис. 3.4. Бесфорсуночные аппараты Вентури: а — с эжекцией жидкости; б — с пленочным орошением; 1 — бак; 2 — сепаратор; 3 — циркуляционная труба; 4 — затвор.
При вертикальном расположении трубы Вентури возможны и другие способы ввода жидкости. На рис. 3.4,а показан бесфорсуночный аппарат Вентури, в котором жидкость эжектируется в конфузор поступающим в него газом. Количество засасываемой газом жидкости определяется ее уровнем в
баке 1. Жидкость, отделенная от газа в сепараторе 2, возвращается в бак по циркуляционной трубе 3. Из бака жидкость удаляется через затвор 4, при помощи которого и поддерживается необходимый уровень жидкости в баке. Бесфорсуночные аппараты Вентури могут работать и без циркуляции жидкости. В аппарате показанном на рис. 3.4.б жидкость поступает в конфузор,
14

переливаясь через его верхний обрез. Далее жидкость стекает по конфузору в
виде пленки и распыливается газом при прохождении через горловину.
Рис. 3.5. Аппарат распыливающего типа (APT): а — с одним центральным конусом, б
— с несколькими конусами; в — с двумя ступенями распыления.
Разновидностью скоростных прямоточных распыливающих аппаратов является аппарат распыливающего типа (APT). Этот аппарат (рис. 3.5,а)
действует аналогично изображенному на рис. 3.4,б, но не имеет диффузора.
При больших производительностях в верхней плите устанавливают несколько конусов (конфузоров), как показано на рис. 3.5,б. Из-за отсутствия диффузора аппарат APT обладает более высоким гидравлическим сопротивлением, чем
аппараты с трубами Вентури. В аппаратах APT можно осуществить несколько
ступеней распыления, устанавливая два или более конуса (рис. 3.5,в).
Другой разновидностью скоростных прямоточных аппаратов является ударно-распылительный аппарат (рис. 3.6), выполненный в виде колонного аппарата с многоступенчатым контактом.
Рис. 3.6. Ударно-распылительный аппарат: 1 —перегородка; 2—гидравлический затвор; 3 —порог перелива.
Скоростные прямоточные распыливающие аппараты — высоко интенсивные аппараты и поэтому весьма перспективны для процессов, не требующих противотока или позволяющих обойтись небольшим числом ступеней. Однако эти аппараты изучены пока еще недостаточно и опыт
промышленной эксплуатации их невелик. Поэтому трудно дать рекомендации
по выбору типа указанных аппаратов и режиму в них.
15
Если требуется иметь небольшое гидравлическое сопротивление, целесообразно применять невысокие скорости газа (20 — 30 м/с), устанавливая
в случае необходимости лишнюю ступень. Наименьшим сопротивлением обладают форсуночные аппараты Вентури. Сопротивление бесфорсуночных аппаратов и аппаратов APT выше. В то же время бесфорсуночный аппарат
Вентури может работать без циркуляции жидкости посредством насоса, что обычно требуется в форсуночных аппаратах Вентури и APT; поэтому общий
расход энергии для бесфорсуночного аппарата в ряде случаев меньше.
3.3 КОНСТРУКЦИИ НАСАДОЧНЫХ КОЛОНН
Конструкции насадочных колонн описаны многими авторами
[1,4,15,20,24,31]. Такие аппараты представляют собой колонны, загруженные насадкой из тел различной формы (кольца, кусковой материал, деревянные решетки и т.д.) [24]. Соприкосновение газа с жидкостью происходит в основном
на смоченной поверхности насадки, по которой стекает орошающая жидкость. Поверхность насадки в единице объема аппарата может быть довольно
большой и поэтому в сравнительно небольших объемах можно создать значительные поверхности массопередачи. Однако в ряде случаев активная
поверхность контакта меньше геометрической поверхности.
Насадочные колонны применяются главным образом при перегонке
высокоагрессивных или вязких продуктов, при необходимости иметь небольшой перепад давления или малый запас жидкости в колонне. Новые типы высокоэффективной насадки применяются также для разделения компонентов, имеющих близкие температуры кипения.
Применение насадочных колонн в настоящее время ограничено
сравнительно небольшими их диаметрами (порядка 0,8—1,0 м). Подобное положение в основном объясняется тем, что в колоннах большого диаметра жидкость и газ могут двигаться через различные сечения колонны, не взаимодействуя друг с другом, и эффективность разделения при этом будет
резко падать.
Насадочные колонны с высокоэффективной и сравнительно недорогой насадкой при правильной организации в них гидродинамического режима во
многих случаях могут оказаться даже значительно более экономичными
аппаратами, чем тарельчатые колонны [1].
Течение жидкости по насадке носит в основном пленочный характер,
вследствие чего насадочные аппараты можно рассматривать как разновидность пленочных. В то же время между насадочными и пленочными
аппаратами, в том числе аппаратами с листовой насадкой, имеются различия. В пленочных аппаратах пленочное течение жидкости происходит по всей высоте аппарата, тогда как в насадочном — лишь по высоте элемента насадки.
При перетекании жидкости с одного элемента насадки |
на |
другой |
пленка |
жидкости разрушается и на нижележащем элементе |
образуется |
новая |
|
пленка. Некоторая часть жидкости при этом проваливается |
в виде |
капель |
|
через расположенные ниже слои насадки. |
|
|
|
16

При определенных условиях пленочное течение жидкости в
насадочных аппаратах нарушается и контакт между газом и жидкостью осуществляется в режиме барботажа.
Насадочный аппарат (рис. 3.7) состоит из колонны, в которой помещена
поддерживающая решетка 1 на этой решетке уложен слой насадки 2.
Орошающая жидкость подается на насадку при помощи распределительного устройства 3. В показанном на рис. 3.7,а аппарате насадка уложена сплошным слоем по всей высоте. Иногда насадку укладывают несколькими слоями, устанавливая под каждым слоем отдельные поддерживающие решетки (рис. 3.7,б). В некоторых случаях при послойной укладке насадки между отдельными
слоями устанавливают устройства 4 для перераспределения жидкости.
Движение газа и жидкости в насадочных аппаратах обычно осуществляется противотоком, как показано на рис. 3.7. Прямоток применяют довольно редко. Однако в последнее время большое внимание уделяют
созданию прямоточных насадочных аппаратов, работающих с большими
скоростями газа (до 10 м/сек). При таких скоростях, которые в случае противотока недостижимы из-за наступления захлебывания, интенсифицируется процесс и уменьшаются габариты аппарата;
гидравлическое сопротивление при прямотоке значительно ниже, чем при
противотоке. Применение таких аппаратов целесообразно в тех случаях, когда
направление движения фаз не влияет заметно на движущую силу.
Рис. 3.7. Насадочные аппараты: а - сo сплошной загрузкой насадки; б - с послойной загрузкой насадки; 1 — поддерживающие решетки, 2 —насадка, 3 — устройство для распределения жидкости, 4 — перераспределитель, 5 — труба.
Описаны аппараты с плавающей насадкой, в которых легкие насадочные тела (полые пластмассовые шары) поддерживаются током газа во взвешенном
(псевдоожиженном) состоянии.
Положение слоя шаров фиксируется нижней (опорной) и верхней
(ограничивающей) решетками. В больших аппаратах пространство между
решетками разделено вертикальными перегородками на квадратные или
прямоугольные отсеки. Такие аппараты рекомендуются при обработке
загрязненных газов и жидкостей, так как в них забивания насадки не происходит. Описаны установки с аппаратами, имевшими характеристики:
17
диаметры 3 и 3,5 м; высота насадки (в неподвижном состоянии) около 0,3 м, приведенная скорость газа примерно 2,5 м/сек; сопротивление 1200—1300 Па.
Недостаток насадочных аппаратов — трудность отвода тепла в процессе
абсорбции. Обычно применяют циркуляционный отвод тепла, используя выносные холодильники. Предложенные конструкции аппаратов с внутренним
отводом тепла при помощи помещенных в насадку охлаждающих элементов не получили распространения [24].
3.3.1 РАСПРЕДЕЛИТЕЛЬНЫЕ УСТРОЙСТВА ДЛЯ ПОДАЧИ ЖИДКОСТИ
Наиболее полное смачивание насадки и наибольшая эффективность аппарата достигаются при равномерном распределении жидкости по
поперечному сечению колонны. Для равномерной подачи орошающей жидкости применяют различные распределительные устройства [1,12,15,24], которые
можно подразделить на две группы:
•устройства, подающие жидкость отдельными струями (струйчатые оросители);
•устройства, в которых подаваемая на насадку жидкость разбивается на капли (разбрызгивающие оросители).
Кструйчатым оросителям относятся распределительные плиты, желоба, «пауки», дырчатые трубы, брызгалки и оросители типа сегнерова колеса; к разбрызгивающим — тарельчатые, многоконусные и вращающиеся
центробежные оросители.
Распределительные плиты применяют двух видов: с затопленными отверстиями и свободным сливом жидкости. Плита с затопленными отверстиями (рис. 3.8,а и б) представляет собой горизонтальную решетку 1, в
которой закреплены патрубки 2, нижние концы патрубков опущены в насадку
или доходят до ее торца. Диаметр и количество патрубков выбирают так, что уровень жидкости устанавливается выше их верхнего обреза, и они заполнены текущей жидкостью. Газ отводится через патрубки 3, выступающие выше уровня жидкости (рис. 3.8,б). Иногда отвод газа располагают ниже плиты (рис.
3.8,а); в этом случае пространство над плитой может быть открытым (если
орошающая жидкость не выделяет газов и паров), что удобно для наблюдения за орошением и для прочистки патрубков. Чтобы предотвратить быстрое засорение, патрубки применяют диаметром не менее 15 мм. Длину патрубков следует брать не менее чем в 2,5—3 раза больше их диаметра, причем во избежание прорыва газа через патрубки уровень жидкости должен быть выше их верхнего обреза не менее чем на 120—150 мм.
На рис. 3.8, в показана плита со свободным сливом жидкости. В этой конструкции патрубки имеют сравнительно большой диаметр (30—100 мм),
причем газ и жидкость проходят через одни и те же патрубки. В выступающих частях патрубков иногда выполняют прорези для стекания через них жидкости.
18

Рис. 3.8. Распределительные плиты: а, б — с затопленными отверстиями; в— со свободным сливом; 1 — решетка, 2 — патрубки для жидкости, 3 - патрубки для газа.
Для хорошего распределения жидкости плиты, особенно со свободным
сливом жидкости, должны быть установлены так, чтобы верхние обрезы патрубков были расположены в одной строго горизонтальной плоскости. Точная установка плит представляет большие трудности, особенно в аппаратах больших диаметров (свыше 2—3 м). В таких аппаратах часто изготавливают
плиту из нескольких частей, причем каждая из частей подвешивается к крышке
аппарата посредством тяг, что дает возможность регулировать положение каждой из частей; при этом газ проходит через зазоры между частями плит.
Рис. 3.9. Распределительные желоба со свободным сливом.
Желоба по принципу работы близки к распределительным плитам. В желобах со свободным сливом (рис. 3.9) жидкость стекает через прорези в боковых стенках. Верхние обрезы труб (в желобах с затопленными отверстиями) или нижние края прорезей (в желобах со свободным сливом)
должны лежать в одной горизонтальной плоскости. Кроме того, для
обеспечения равномерного орошения уровень жидкости по всей длине желоба
должен быть одинаковым. Для достижения этого жидкость обычно подводят к
желобу посредине или в нескольких местах по его длине; скорость жидкости в желобе не должна быть выше 0,3 м/сек.
«Пауки» (рис. 3.10) представляют собой простейшего типа распределительные плиты. Жидкость подается в распределитель 1 и далее
поступает в колонну по проходящим через ее крышку трубам 2. Во избежание прорыва газа трубы перекрыты колпачками 3, образующими гидравлический
19

затвор. «Пауки» являются простым и надежным устройством для
распределения орошения и широко применяются в колоннах небольшого диаметра.
Рис. |
3.10. Ороситель |
«паук»: 1 — распределитель, 2 — труба, 3—колпачок. |
Рис. |
3.11. Ороситель |
из дырчатых труб: 1 — кольцо, 2 — поперечины, 3 — |
|
патрубки для ввода жидкости. |
Дырчатые трубы выполняют в виде системы труб, укладываемых на насадку или подвешиваемых над ней. В нижней части 1 трубы имеют отверстия
диаметром 3—6 мм для выхода жидкости. Для равномерного распределения жидкости по всем отверстиям рекомендуется выполнять ороситель в виде кольца 1 (рис. 3.11) с вваренными по хордам поперечинами 2 и двумя патрубками 3 для ввода жидкости. Ороситель из дырчатых труб прост в изготовлении; его недостаток — легкость засорения отверстий.
Брызгалки представляют собой цилиндрический стакан (рис. 3.12,а) или
чашу полушаровой формы (рис. 3.12,б), которые размещают в центре колонны на высоте 0,7 — 1 м (и более) над насадкой. Жидкость вытекает через отверстия диаметром 3 — 15 мм, просверленные в стенках брызгалки. Соответствующим размещением отверстий на поверхности брызгалки можно осуществить требуемое распределение струй по сечению колонны. Жидкость подается в брызгалку под напором, создаваемым насосом или напорным баком.
Брызгалки удовлетворительно работают при постоянном расходе
орошающей жидкости. При изменении расхода, а также при колебаниях напора изменяются радиусы орошения (радиус, на котором струя достигает насадки), в
результате чего не будет орошаться весь торец насадки или, наоборот, часть
жидкости будет попадать на стенки колонны. Брызгалки — простое и дешевое устройство, пригодное для орошения колонн большого диаметра (до 9 м). Недостатком брызгалок является засоряемость отверстий, особенно при малом
их диаметре.
Щелевая брызгалка (рис. 3.12,в) имеет небольшое число прорезей (6—8) прямоугольной формы. Щелевые брызгалки создают сравнительно небольшой радиус орошения, и в колоннах больших диаметров устанавливают несколько
таких брызгалок.
20