
Ахметов и др. Технология и оборудование процессов переработки нефти и газа (2006)
.pdfШлемовая линия — толстостенная труба из углеродистой стали. Кожухотрубчатый пучок конденсатора головного погона — углеродистая сталь.
Условия работы эжекторов по жесткости не уступают ускоренным коррозионным испытаниям.
Паровые сопла изготавливают из нержавеющей стали, но лучше из монеля.Горловину,котораякорродируетсильнее,изготавливаютизинконеля, монеля или нержавеющей стали, всасывающие камеры — из чугуна. Колено, соединяющее последнюю ступень эжектора с конденсатором, наиболее, подвержено износу, его выполняют из инконеля.
3.5.4.Некоторые аспекты эксплуатации и совершенствования вакуумсоздающих систем
При эксплуатации системы создания вакуума с помощью барометрических конденсаторов смешения на действующих установках АВТ с уходящей водой теряется до 0,80…0,98% на перерабатываемую нефть дизельнойигазойлевойфракции.Неконденсирующиесягазыразложения,втомчислеисероводород,выбрасываютсяватмосферу.Частичное растворениесероводородавводе,подаваемойнаконденсацию,вызывает усиленную коррозию труб (от конденсаторов смешения до барометрического колодца, коллектора и линий подачи воды в конденсаторы)
итребует создания на НПЗ изолированной третьей барометрической системы оборотного водоснабжения. Замена конденсаторов смешения конденсаторами поверхностного типа позволяет исключить большие потери нефтепродукта, загрязнение сточных вод и воздушного бассейна, поэтому осуществляемый в настоящее время на некоторых заводах переходнановуюсистемусозданиявакууманаатмосферно-вакуумных
ивакуумных установках заключается в полной замене конденсаторов смешения поверхностными конденсаторами кожухотрубчатого типа.
Сцелью обеспечения современных технологических, экологических требований к процессу вакуумной перегонки были созданы гидроэжекторные системы, применение которых позволяет сократить потребление водяного пара и объемы сточной воды на установке АВТ до минимума.
Особенностью таких систем является их оснащение жидкостногазоструйным аппаратом, в качестве рабочего тела которого выступает одна из фракций, получаемых на той же установке АВТ. Теоретические исследования и разработки наиболее системно выполнены фирмами «Техновакуум» и «Технотон», предлагающие оригинальные технологические схемы таких вакуумсоздающих систем.
461
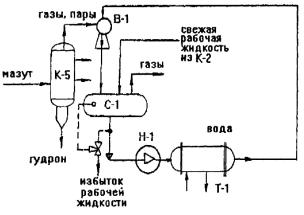
На рис. 3.30 представлена принципиальная схема гидроэжекторной вакуумной системы, разработанной фирмой «Техновакуум».
Газы разложения мазута и пары углеводородов, воды из вакуумной колонны К-5поступаютвкаче-
Рис. 3.30. Схема создания вакуума вакуумсоздающей системы стве пассивного тела
фирмы «Техновакуум» в вакуумсоздающее
устройствоВ-1, куда из сепаратораС-1насосомН-1через холодильник Т-1нагнетается рабочая жидкость (фракция дизельного топлива из ат- мосфернойколонныК-2).Врезультатеконтактаактивногоипассивного тел происходит конденсация паров, сжатие газов разложения до задан- ногодавления10…20ммрт.ст.ГазожидкостнаясмесьизВ-1разделяется
всепараторе С-1, избыток рабочего тела отводится из системы, а рабочаяжидкостьдополнительнообновляетсясвежейдизельнойфракцией. Таким образом, создается замкнутый контур рабочего тела, полностью исключаются использование водяного пара и в максимальной степени снижается объем загрязненных промышленных стоков.
Вакуумсоздаюшая система, разработанная фирмой «Технотон», принципиально отличается от приведенной выше, и это связано с применениемдвухступенчатойилитрехступенчатойгидроэжекторнойсистемы,вкоторойиспользуютсяпринципывихревогоэжектированияпарогазовых систем рабочей жидкостью. Принципиальная схема такой гидроэжекторной системы дана на рисунке 3.31.
Газы разложения мазута, пара углеводородов, воды из вакуумной колонны К-5 поступают в струйный или вихревой эжектор В-1 и далее во вихревой эжектор В-2. Рабочим телом этих эжекторов является дизельная фракция (или вакуумный газойль), откачиваемая из сепаратора С-1 насосом Н-1 через фильтры Ф-1, Ф-2 в оба эжектора одновременно. Поток рабочей жидкости после эжектора В-2 подается
вциклонный газоотделитель Ц-1 и далее охлаждается в Т-1 и возвращается в сепаратор С-1. Потоки газов, выводимые из Ц-1, также подаются в сепаратор С-1 для отделения растворенных газов и далее отводятся в печь для дожига. Как и в предыдущем случае, осущест-
462
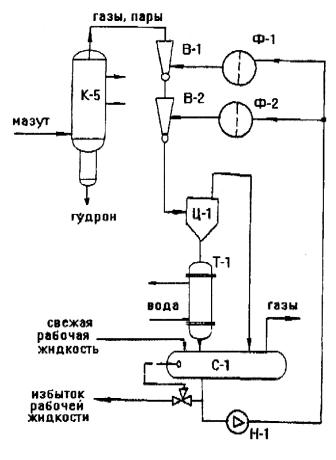
вляется вывод избытка рабочей жидкости и подача свежей дизельной фракции(иливакуумногогазойля).Втабл.3.12приведенысравнительные характеристики двух вакуумсоздающих систем – пароэжекторной и гидроэжекторной.
Сопоставлениеэксплуатационныхпараметровпоказываетбезусловные преимущества гидроэжекторной системы, которые заключаются всниженииостаточногодавлениянаверхуколонныдо15…30мм.рт.ст., увеличении выхода вакуумного газойля в 1,5 раза, сокращении потребления водяного пара до минимума, снижении объемов и загрязненности сточных вод. Вместе с тем гидроэжекторные системы отличаются от пароэжекторных намного большим потреблением электроэнергии и необходимостью использования высоконапорных насосов.
Рис. 3.31. Принципиальная схема двухступенчатой гидроэжекторной системы «Технотон»
463
Таблица 3.12 — Характеристика систем
Параметры |
Пароэжекторная |
Гидроэжек- |
система |
торная |
|
|
система |
|
|
|
|
Расход мазута, м3/ч |
255…270 |
264…282 |
Остаточное давление на верху К-5, ммрт.ст. |
40…60 |
15…30 |
|
|
|
Температура,°С: |
|
|
низа колонны |
350…355 |
350…360 |
верха колонны |
150…170 |
110…120 |
Отбор вакуумного газойля, т/сут |
1221 |
1815 |
|
|
|
Содержание в гудроне фракций до 500°С,% |
25 |
18 |
|
|
|
Расход водяного пара на эжектор, т/год |
4814 |
— |
|
|
|
Содержание H2S в стоках , мг/л |
150 |
5 |
|
|
|
Реализация возможностей снижения вакуума в ректификационной колонне должна сочетаться с необходимостью такого оформления технологии. Часто на НПЗ вслед за модернизацией вакуумсоздающих систем следует полная замена массообменных элементов (тарелок на насадочные устройства), в результате достигается максимальный эффект в виде улучшения качества масляных фракций (сужение пределов выкипания до 40…50°С) либо осуществляется производство остаточных дорожных битумов, получаемых без процесса окисления, т.е. непосредственно в вакуумной колонне в виде кубового продукта.
Вакуумсоздающие системы на установках АВТ являются важными узлами, от эффективной работы которых зависит глубина переработки мазутов и качество получаемых продуктов.
464

Глава 4
ТЕОРЕТИЧЕСКИЕ ОСНОВЫ И ТЕХНОЛОГИЯ ПРОИЗВОДСТВА СМАЗОЧНЫХ МАСЕЛ
Введение
Назначение,классификация,основныепоказатели,сорта,требования к качеству смазочных масел изложены в п. 1.3.6.
Практически любое смазочное масло представляет собой масляную основу — базовое масло, в которое вводят присадки разного функционального назначения.
Масляная основа нефтяных смазочных масел представляет собой сложную смесь высококипящих углеводородов с числом углеродных атомов 20…60 (молекулярной массы 300…750), выкипающих в интервале 300…650°С. Сырьем для их производства является мазут, а главным процессом — вакуумная перегонка, в результате которой получают узкие масляные фракции (от 1 до 4) и гудрон. В этих фракциях содержатся: парафиновые углеводороды (алканы нормального и изостроения); нафтеновые углеводороды (цикланы), содержащие пяти-
ишестичленныекольцаспарафиновымицепямиразнойдлины;ароматические углеводороды (арены моно- и полициклические); гибридные углеводороды,атакжесмолисто-асфальтеновыевеществаисеро-,азот-
икислородсодержащие гетероорганические соединения. В исходных масляных фракциях нефти содержатся компоненты, составляющие основу базовых масел, и так называемые нежелательные компоненты, ухудшающиефизико-химическиеиэксплуатационныесвойстватовар- ных масел, такие как смолисто-асфальтеновые, полициклические ароматические и высокомолекулярные парафиновые углеводороды. Поэтомутехнологияпроизводствабазовойосновысмазочныхмаселосновананаизбирательномудаленииизмасляныхфракцийнежелательных углеводородовпримаксимальновозможномсохранениикомпонентов, обеспечивающих требуемые физико-химические и эксплуатационные свойства конечных товарных масел.
Методыудалениянежелательныхкомпонентов,тоестьочисткимасляных фракций, делятся на химические и физические.
При химической очистке используют реагенты (щелочь, кислоту, водород), химически взаимодействующие с удаляемыми компонента-
465
ми. Наиболее старыми, но до сих пор используемыми методами являются сернокислотная и щелочная очистки. В процессе сернокислотной очисткиизисходногосырьяудаляютсяпреимущественносмолисто-ас- фальтеновые вещества и полициклические ароматические углеводороды. Кислые вещества, остающиеся в очищенном масле после удаления кислого гудрона, удаляют обработкой водным раствором щелочи или контактированием с отбеливающими землями. При гидрогенизационных методах очистки требуемое качество масел достигается химическим преобразованием нежелательных компонентов сырья в углеводороды нужной структуры.
Физические методы очистки масел предусматривают разделение масляной фракции на две части без изменения химического строения углеводородов исходного сырья.
Измассообменныхпроцессовфракционированиямногокомпонентных смесей в производствах смазочных масел наибольшее распростра-
нениеполучилиэкстракционныепроцессы,основанныенаиспользовании различной растворимости углеводородов в растворителях.
Вэтихпроцессахфракционированиемасляногосырьяосуществляется не по температурным пределам кипения, а по химическому углеводородномусоставу.Однигрупповыехимическиекомпонентысырьяхорошо растворяются в выбранном для данного экстракционного процесса растворителе, а другие, наоборот, плохо или совсем не растворяются.
В последние годы в технологии производства базовых масел все более широкое применение находят гидрокаталитические процессы, такиекакгидроочистка,гидрокрекинг,гидроизомеризация,гидродепарафинизация. В этих процессах улучшение качества смазочных масел достигается не удалением нежелательных компонентов, а химическим преобразованием их в высокоиндексные низкозастывающие углеводороды с низким содержанием гетероатомов под действием водорода икатализаторовприповышенныхтемпературахидавлениях(см.гл.8).
4.1.Основные понятия и определения экстракционных процессов
Целевое назначение экстракционных процессов масляных производств – удаление из исходного сырья низкоиндексных и коксогенных компонентов, таких как смолисто-асфальтеновые и полициклические углеводороды, а также высокоплавких парафинов, ухудшающих низкотемпературные свойства товарных масел. В производстве нефтяных смазочных масел применяются следующие 3 типа экстракционных процессов: деасфальтизация гудронов, селективная очистка деасфаль-
466
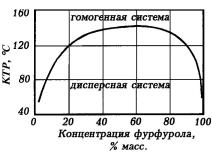
тизированных гудронов и масляных дистиллятов и депарафинизация экстрактивной кристаллизацией.
Из технологических параметров экстракционных процессов наибольшее значение имеют температура экстракции, соотношение растворитель : сырье (кратность растворителя) и являющаяся функцией этих параметров критическая температура растворения.
Критическая температура растворения (KTP). При смешении сырьясрастворителемприпостояннойтемпературевначалепроисходит полноерастворениерастворителявсырье.Придальнейшемувеличении кратностирастворителяобразуетсядисперсная(гетерогенная)система, состоящаяиздвухфаз:однаизних–дисперсионнаясреда,представляю- щая собой растворитель с растворенными компонентами, а другая — дисперсная фаза — нерастворенные компоненты с растворителем. При значительной кратности растворителя может происходить полная растворимость сырья.
Принеизменнойкратностирастворителясповышениемтемпературы увеличивается содержание растворенных компонентов сырья и при достиженииопределеннойтемпературы,называемойКТР,ивышеэтой температуры сырье полностью смешивается с растворителем, образуя гомогенную, то есть однофазную систему. Кривая растворимости масляного сырья в растворителях можетбытьразличнойвзависимости от качества сырья и типа растворителя. На рис. 4.1 представлена в качестве примера типичная кривая растворимости масляного дистиллята парафинистой нефти в фурфуроле: внутри этой кривой находится область существования двух фаз, вне ее — область полной взаимной растворимости.
Разделениеисходногосырьянагрупповыехимическиекомпоненты при помощи экстракции может быть осуществлено лишь при условии образования дисперсной системы, что обеспечивается соответствующим выбором температуры экстракции и кратности растворителя.
Разделениеобразующихсяфазосуществляетсяпоразностиихплотностей в экстрактных аппаратах (преимущественно в противоточных колоннахтарельчатого,насадочногоилироторноготипа)ипутемфильтрации.
467
В масляных производствах после отгонки растворителей из обеих фаз получают полупродукты под следующими названиями:
|
Из дисперсионной среды |
Из дисперсной фазы |
Деасфальтизация |
деасфальтизат |
асфальтит |
Селективная |
|
|
очистка |
экстракт |
рафинат |
Депарафинизация |
|
|
кристаллизацией |
депарафинизат |
гач или петролатум |
Растворяющаяспособностьиизбирательностьрастворителя—
дваосновныхэксплуатационныхсвойства,которыеявляютсярешающими привыбореэффективногорастворителядляэкстракционныхпроцессов.
Растворяющая способность — показатель, характеризующий абсолютную растворимость компонентов масляных фракций в определенномколичестверастворителя.Общепринятойединойметодикидля определениярастворяющейспособностирастворителейдосихпорнет. Принято этот показатель оценивать:
1)по выходу растворенного компонента сырья при одинаковой кратности растворителя;
2)по значению КТР при одинаковой кратности растворителя;
3)количеством растворителя, необходимым для извлечения одного
и того же растворенного компонента сырья.
Изприведенныхнижевкачествепримерасопоставительныхданных видно,чтоиздвухрастворителейбольшейрастворяющейспособностью обладаетнитробензол,имеющийприпостоянномрасходерастворителя меньшую КТР и обеспечивающий больший выход растворенного компонента, а также одинаковый выход растворенных компонентов при в 4,5 раза меньшем расходе растворителя по сравнению с анилином.
|
Расход |
|
|
Выход |
|
|
|
|
растворенных |
||
Растворитель |
растворителя, |
КТР, |
°С |
||
компонентов, |
|||||
|
% мас. |
|
|
||
|
|
|
% мас. |
||
|
|
|
|
||
|
|
|
|
|
|
Анилин |
200 |
56 |
|
20,8 |
|
|
200 |
34 |
|
48,8 |
|
|
|
|
|
|
|
Анилин |
200 |
|
|
15 |
|
Нитробензол |
45 |
|
|
15 |
|
|
|
|
|
|
Избирательность (селективность) характеризует способность растворителя растворять только компоненты определенной структу-
468
ры сырья, что позволяет четко разделять исходное сырье на отдельные групповые химические компоненты.
Дляоценкиизбирательнойспособностирастворителейвнастоящее время также нет единой методики. Об избирательности растворителя можно судить по разности (градиенту) таких показателей, как плотность, индекс вязкости, коэффициент преломления или анилиновая точка.
Применительно к процессам селективной очистки масел пользуются коэффициентом распределения К, определяемым из соотношения объемных концентраций извлекаемых компонентов в экстракте (Сэкс)
и рафинате (Сраф) : К = Сэкс / Сраф.
Для характеристики избирательности растворителя для этого же процесса можно пользоваться уравнением А. З. Биккулова:
Избирательность = (Аэкс – Браф) / (Араф – Бэкс),
где Аэкс, Араф и Бэкс, Браф — содержание в экстракте и рафинате соответственно ароматических и парафино-нафтеновых углеводородов.
Показатели избирательности могут быть использованы только для сравнения растворителей при их выборе для тех или иных целей, но непригодны при расчетах экстракционных процессов.
Как правило, растворяющая и избирательная способности растворителей антибатны, и обычно рост одного показателя ведет к снижениюдругого.Поэтомупривыборерастворителяприходитсяпринимать компромиссные решения.
Растворяющая способность и избирательность для каждого растворителя не являются постоянными и зависят как от технологических условийэкстракционныхпроцессов,такиотхимическогосоставасырья.
Требования к растворителям. В качестве избирательных растворителей предложено большое количество различных органических и неорганических соединений, однако сложный комплекс требований, предъявляемых к экстрагентам, ограничивает возможность использования многих из них для промышленных экстракционных процессов.
Промышленныеэкстрагентыдолжныобладатьпреждевсегоследующими эксплуатационными свойствами:
—оптимальной растворяющей способностью и высокой избирательностьювдостаточноширокоминтервалетемператур(этипоказатели обусловливают выход и качество целевых продуктов);
—низкимитеплотойиспаренияитемпературойкипенияпосравнению с сырьем, что позволяет уменьшить энергетические затраты на регенерацию растворителей;
469
—достаточновысокойразностьюплотностейсисходнымсырьеминизкой вязкостью для облегчения процесса разделения гетерогенных фаз образующейся дисперсной системы.
Кроме того, они должны быть дешевыми и недефицитными, а также удовлетворять следующим экологическим требованиям:
—иметь высокие химическую и термическую стабильности;
—быть нетоксичными, взрыво- и пожаробезопасными;
—не вызывать коррозии аппаратуры.
Растворителямотдельныхэкстракционныхпроцессовпредъявляется дополнительно ряд специфических требований. Так, растворители процессов депарафинизации кристаллизацией должны:
—иметь низкую температуру застывания, чтобы не кристаллизоваться при температуре депарафинизации и не забивать фильтровальную ткань;
—обеспечивать минимальную разность между температурами застывания депарафинизата и конечного охлаждения смеси растворителя с сырьем;
—способствовать образованию крупных кристаллов твердых парафинов, обеспечивающих хорошее фильтрование.
Растворители процессов деасфальтизации должны:
—обладать хорошей коагулирующей способностью;
—иметьнеслишкомнизкуютемпературукипениядляпроведенияпроцесса экстракции при пониженных давлениях;
—не растворять или плохо растворять смолисто-асфальтеновые углеводороды нефтяных остатков.
Определенноезначениеимеюттакжеповерхностноенатяжение,теп-
лоемкость, критические температура и давление и другие показатели растворителей.
Из анализа вышеприведенных требований к качеству экстрагентов можно констатировать, что практически невозможно рекомендовать универсальный растворитель для всех видов сырья и для всех экстракционных процессов. В этой связи приходится довольствоваться узким ассортиментом растворителей для отдельных экстракционных процессов. Так, в процессах деасфальтизации гудронов широко применялись
иприменяются низкомолекулярные алканы, такие как этан, пропан, бутан, пентан и легкий бензин, являющиеся слабыми растворителями, плохорастворяющимисмолисто-асфальтеновыесоединениянефтяных остатков. В процессах селективной очистки масляных дистиллятов
идеасфальтизатов применялись сернистый ангидрид, анилин, нитробензол, хлорекс, фенол, фурфурол, крезол и N-метилпирролидон.
470