
Ахметов и др. Технология и оборудование процессов переработки нефти и газа (2006)
.pdfполя высокого напряжения. После охлаждения в теплообменниках обессоленная и обезвоженная нефть отводится в резервуары подготовленной нефти, а на секции ЭЛОУ комбинированных установок она без охлаждения подается на установки первичной перегонки нефти.
3.1.3. Подготовка горючих газов к переработке
Под горючими газами обычно подразумевают смеси газообразных горючих веществ: низкомолекулярных углеводородов (алканов и алкенов С1–C4), водорода, окиси углерода и сероводорода, разбавленных такими негорючими газами, как диоксид углерода, азот, аргон, гелий и пары воды.
Горючие газы принято подразделять (классифицировать) в зависимости от происхождения на следующие группы:
1)природные (сухие), состоящие преимущественно из метана, добываемые из чисто газовых месторождений;
2)нефтяные(жирные),состоящиеизметанаиегонизкомолекулярных гомологов (С1–С5), добываемые попутно с нефтью;
3)газоконденсатные, по составу аналогичные нефтяным, добываемые из газоконденсатных месторождений;
4)искусственные, к которым относятся:
—нефтезаводские, получаемые при переработке нефти;
—газы переработки твердых топлив (коксовый, генераторный, доменный и др.).
Посодержаниюсеросодержащихкомпонентовгорючиегазыделятся:
—на слабосернистые с содержанием сероводорода и тиоловой серы менее 20 и 36 мг/м3 соответственно (то есть ниже допустимых норм поотраслевомустандартуОСТ51.40—83«Газыгорючиеприродные, подаваемые в магистральные газопроводы»), которые не подвергаются специальной сероочистке;
—сернистые (условно подразделяемые на малосернистые, сернистые и высокосернистые), содержащие сероводород и тиоловую серу более20и36мг/м3 соответственно,подлежащиеобязательнойочистке от сернистых соединений и переработке последних в газовую серу (только при переработке малосернистых газов допускается сжигание газов регенерации на факелах).
Сероводород и диоксид углерода являются кислыми коррозионноагрессивнымикомпонентамигорючихгазов,которыевовлажнойсреде способствуют внутренней коррозии труб и оборудования и приводят к ухудшению топливных качеств газа. Поэтому эти примеси следует удалять перед транспортировкой и переработкой горючих газов.
391
Влага, содержащаяся в газе, вызывает различные осложнения в работе газовой аппаратуры. Пары воды в условиях промысловой подготовки и при транспортировании способны конденсироваться и, что особенно опасно, образовывать твердые кристаллогидраты, которые приводят к возникновению аварийных ситуаций. По этой причине горючие природные газы подлежат, кроме очистки от кислых компонентов, обязательной осушке до допустимых норм (табл. 3.3). На практике о влагосодержании горючих газов судят по их точке росы, понимая под этимтерминомтемпературу,нижекоторойводянойпарконденсируется (выпадает в виде «росы»).
Таблица 3.3 — |
Требования к качеству природных горючих газов, |
||||
|
подаваемых в магистральные газопроводы |
|
|||
|
(ОСТ 51.40.—83) |
|
|
|
|
|
|
|
|
|
|
|
|
Климатический район |
|||
|
Показатель |
умеренный |
холодный |
||
|
|
|
|
|
|
|
|
I* |
II* |
I |
II |
|
|
|
|
|
|
Точка росы газа, °С, не выше: |
|
|
|
|
|
|
|
|
|
|
|
по влаге |
|
0 |
–5 |
–10 |
–20 |
по углеводородам |
0 |
0 |
–5 |
–10 |
|
Содержание, г/м3, не более: |
|
|
|
|
|
механических примесей |
0,003 |
0,003 |
0,003 |
0,003 |
|
сероводорода |
|
0,02 |
0,02 |
0,02 |
0,02 |
тиоловой серы |
|
0,036 |
0,036 |
0,036 |
0,036 |
Объемная доля кислорода, %, не более |
1 |
1 |
1 |
1 |
*I – с 01.05. по 30.09; II – с 01.10 по 30.04.
Втабл. 3.4 приведен состав природных горючих газов некоторых газовых, газоконденсатных и нефтяных месторождений бывшего
СССР.
Осушка горючих газов. В газовой промышленности для осушки природных газов наиболее широко используют абсорбционный процесс с применением преимущественно в качестве абсорбента высококонцентрированных растворов гликолей — диэтиленгликоля (ДЭГ) и триэтиленгликоля (ТЭГ). В последнее время применяют также пропиленгликоль (ПГ). По таким показателям, как летучесть, следовательно, и расход абсорбента, осушительная способность, склонность к пенообразованию, устойчивость к окислению и термическому раз-
392
ложению, коррозионная активность и некоторым другим, ДЭГ и ТЭГ более предпочтительны и потому находят в абсорбционных процессах осушки газов преимущественное применение по сравнению с моноэтиленгликолем. Процесс осушки газов включает 2 стадии: абсорбцию идесорбциювлаги–иосуществляетсясоответственновдвухаппаратах колонного типа с тарелками (или насадками) — абсорбере и десорбере. Абсорбция проводится при температуре около 20°С и повышенном давлении — 2…6МПа, а десорбция – при пониженном давлении и повышенной температуре 160…190°С. Принципиальная схема установки осушки газов гликолями представлена на рис. 3.4.
Таблица 3.4 — Примерный состав газа некоторых газовых,
газоконденсатных и нефтяных месторождений бывшего СССР,% об.
|
СН4 |
С2Н6 |
С3Н8 |
С4Н10 |
С15Н12 |
СО2 |
H2S |
N2 |
Месторождение |
и |
|||||||
|
|
|
|
|
выше |
|
|
|
|
|
|
|
|
|
|
|
|
|
|
Газовое |
|
|
|
|
|
|
|
|
|
|
|
|
|
|
|
Уренгойское |
96,00 |
0,09 |
0,01 |
0,00 |
0,01 |
0,49 |
— |
3,40 |
Медвежье |
99,20 |
0,08 |
0,01 |
0,07 |
0,02 |
0,06 |
— |
0,57 |
Ямбургское |
95,20 |
0,04 |
0,01 |
0,00 |
0,01 |
0,30 |
— |
4,00 |
|
|
|
|
|
|
|
|
|
Ставропольское |
98,80 |
0,30 |
0,20 |
0,10 |
— |
0,20 |
— |
0,40 |
|
|
|
|
|
|
|
|
|
Газлинское |
92,70 |
3,20 |
0,90 |
0,47 |
0,13 |
0,10 |
— |
2,50 |
|
|
|
|
|
|
|
|
|
|
Газоконденсатное |
|
|
|
|
|||
|
|
|
|
|
|
|
|
|
Астраханское |
54,15 |
5,54 |
1,68 |
0,93 |
1,57 |
21,55 |
12,60 |
1,98 |
|
|
|
|
|
|
|
|
|
Оренбургское |
81,70 |
4,50 |
1,80 |
1,00 |
3,55 |
2,35 |
4,00 |
1,10 |
Карачаганакское |
75,31 |
5,45 |
2,62 |
1,37 |
5,98 |
4,79 |
3,69 |
0,79 |
Вуктыльское |
75,00 |
9,00 |
3,90 |
1,80 |
5,20 |
0,10 |
— |
5,00 |
|
|
|
|
|
|
|
|
|
Шатлыкское |
95,70 |
1,70 |
0,23 |
0,04 |
0,02 |
1,24 |
— |
1,40 |
|
|
|
|
|
|
|
|
|
|
|
Нефтяное |
|
|
|
|
|
|
|
|
|
|
|
|
|
|
|
Ромашкинское |
39,00 |
20,00 |
18,50 |
6,20 |
4,70 |
0,10 |
— |
11,50 |
|
|
|
|
|
|
|
|
|
Туймазинское |
41,00 |
21,00 |
17,40 |
6,80 |
4,60 |
0,10 |
2,00 |
7,10 |
|
|
|
|
|
|
|
|
|
Ишимбайское |
42,40 |
12,00 |
20,50 |
7,20 |
3,10 |
1,00 |
2,80 |
11,00 |
|
|
|
|
|
|
|
|
|
Шкаповское |
47,00 |
14,10 |
27,20 |
9,50 |
5,20 |
— |
— |
— |
Жирновское |
82,00 |
6,00 |
3,00 |
3,50 |
1,00 |
5,00 |
— |
1,50 |
Мухановское |
30,10 |
20,20 |
23,60 |
10,60 |
4,80 |
1,50 |
2,40 |
6,80 |
|
|
|
|
|
|
|
|
|
Небит—Дагское |
85,70 |
4,00 |
3,50 |
2,00 |
1,40 |
2,09 |
0,01 |
1,30 |
|
|
|
|
|
|
|
|
|
393
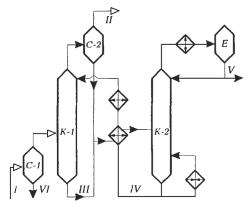
Рис. 3.4. Принципиальная схема установки осушки природного газа гликолями:
I — сырой газ; II — осушенный газ; III — насыщенный гликоль; IV — регенерированный гликоль; V — конденсат воды; VI — конденсат углеводородов и воды; К-1 — абсорбер; К-2 — десорбер; С-1иС-2—сепараторы-каплеотбойники;Е—ем- кость – сборник конденсата
Очистка горючих газов от сероводорода и диоксида углерода.
Для очистки горючих газов от кислых компонентов или одного из них промышленное применение в настоящее время нашли следующие основные процессы:
—абсорбционные, основанные на использовании жидких поглотителей – физических или химических абсорбентов или их смесей(комбинированных абсорбентов);
—адсорбционные, с использованием твердых поглотителей (активированных углей, природных или синтетических цеолитов и др.);
—окислительные, основанные на химическом превращении сернистых соединений (сероводорода и меркаптанов) в элементарную серу (Джиаммарко – Ветрокок-, Стретфорд-процессы) или комбинированном использовании процессов щелочной очистки газов и каталитической окислительной регенерации щелочного раствора (типа Мерокс-процесса).
В физических абсорбционных процессах в качестве абсорбентов применяютдиметиловыйэфирполиэтиленгликоля(селексол-процесс), N-метилпирролидон, пропиленкарбонат (флюор-процесс) трибутилфосфат, ацетон, метанол и др. В качестве химических абсорбентов (хемосорбентов) широко используют амины, щелочь, аммиак, карбонат калия и др. Из комбинированных абсорбционных процессов, использующих в качестве поглотителя смесь физических и химических поглотителей,наиболееширокоепрактическоераспространениеполучил процесс «Сульфинол» с использованием сульфолана и диизопропаноламина. В отечественной газовой промышленности и нефтепереработке преобладающее применение получили процессы этаноламиновой очистки горючих газов. Из аминов преобладающее применение нашли
394

в нашей стране моноэтаноламин (МЭА), за рубежом — диэтаноламин (ДЭА). Среди аминов МЭА наиболее дешевый и имеет такие преимущества, как высокая реакционная способность, стабильность, высокая поглотительная емкость, легкость регенерации. Однако ДЭА превосходит МЭА по таким показателям, как избирательность, упругость паров, потери от уноса и химических необратимых взаимодействий, энергоемкость стадии регенерации и некоторым другим.
Процесс моноэтаноламиновой очистки газов от H2S и СО2 основан на хемосорбционном их взаимодействии с образованием легко разлагаемых при нагревании солей:
2RNH2+H2S(RNH3)2S;
(RNH3)2S+H2S2RNH3HS;
2RNH2+CO2+H2O(RNH3)2CO2;
(RNH3)2CO3+CO2+H2O2RNH3HCO3,
где R — группа ОН–СН2–СН2–.
Согласно принципу Ле-Шателье, понижение температуры и повышение давления способствуют протеканию реакций в прямом направлении, а повышение температуры и понижение давления — в обратном направлении. Это положение является определяющим при выборе режимов очистки газа и регенерации насыщенного абсорбента. Обычно стадию абсорбции кислых газов проводят при давлении около 1,5МПа
итемпературе 25…40°С, а регенерацию – пpи температуре ≈ 130°С
идавлении 0,15…0,2МПа. Концентрация МЭА составляет 15…20%.
Этаноламиновая очистка горючих газов ведется на установках (рис. 3.5), состоящих из абсорбера и десорбера колонного типа (оборудованного соответственно ≈ 20 и 15 тарелками) и вспомогательного оборудования. В низ абсорбера К-1 поступает исходный газ, противотоком контактирует с нисходящим потоком раствора МЭА. С верха К-1 через каплеотбойник уходит очищенный газ, а снизу – насыщенный раствор МЭА, который нагревается в теплообменнике (и при необходимости пароподогревателе ) до температуры 80…90°С и поступает в верхнюю часть десорбера К-2. Из К-2 сверху уходят H2S и СО2, снизу — регенирированный раствор МЭА. Часть этого раствора подогревается в паровом кипятильнике и возвращается в десорбер для подвода тепла, а остальное количество охлаждается в теплообменнике ихолодильникеиподаетсянаверхабсорбера.Наверхдесорбераподается водный конденсат из сепаратора С-2, выводимый с верха К-2вместе с кислыми газами после конденсации в конденсаторе-холодильнике.
395
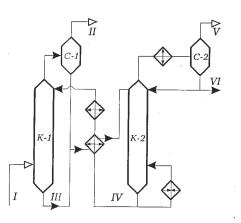
Рис. 3.5. Принципиальная схема установки этаноламиновой очистки горючих газов:
I — сырьевой газ; II — очищенный газ; III — насыщенный расвор амина; IV — регенерированный раствор амина; V — кислые газы; VI — водный конденсат; К-1—абсорбер;К-2—десорбер;С-1—каплеотбойник; С-2 — сепаратор
3.2.Теоретические основы процессов перегонки нефти и газов
Сосновными закономерностями процессов физической переработки нефти и газов, в частности перегонки и ректификации, а также конструкцией и принципами работы их аппаратов студенты ознакомились в курсе «Процессы и аппараты нефтепереработки». В этой связи ниже будут изложены лишь обобщающие сведения по теоретическим основампроцессов,получившихвнефтепереработкенаименованиепервичной (прямой) перегонки (переработки), подразумевая, что продукты этих головных на НПЗ процессов будут подвергаться далее вторичной (физическойилихимической)переработкесполучениемтоварныхнефтепродуктов или их компонентов.
3.2.1. Общие сведения о перегонке и ректификации нефти и газов
Перегонка (дистилляция) — это процесс физического разделения нефти и газов на фракции (компоненты), отличающиеся друг от друга и от исходной смеси по температурным пределам (или температуре) кипения. По способу проведения процесса различают простую и сложную перегонку.
Простая перегонка осуществляется постепенным, однократным или многократным испарением.
Перегонка с постепенным испарением состоит в постепенном на-
греваниинефтиотначальнойдоконечнойтемпературыснепрерывным отводом и конденсацией образующихся паров. Этот способ перегонки нефти и нефтепродуктов в основном применяют в лабораторной практике при определении их фракционного состава.
396
При однократной перегонке жидкость (нефть) нагревается до заданной температуры, образовавшиеся и достигшие равновесия пары однократно отделяются от жидкой фазы — остатка. Этот способ, по сравнению с перегонкой с постепенным испарением, обеспечивает при одинаковыхтемпературеидавлениибольшуюдолюотгона.Этоважное его достоинство используют в практике нефтеперегонки для достижения максимального отбора паров при ограниченной температуре нагрева во избежание крекинга нефти.
Перегонка с многократным испарением заключается в последо-
вательном повторении процесса однократной перегонки при более высоких температурах или низких давлениях по отношению к остатку предыдущего процесса.
Из процессов сложной перегонки различают перегонку с дефлегмацией и перегонку с ректификацией.
При перегонке с дефлегмацией образующиеся пары конденсируют и часть конденсата в виде флегмы подают навстречу потоку пара. В результате однократного контактирования парового и жидкого потоков уходящие из системы пары дополнительно обогащаются низкокипящими компонентами, тем самым несколько повышается четкость разделения смесей.
Перегонкасректификацией—наиболеераспространенныйвхими- ческойинефтегазовойтехнологиимассообменныйпроцесс,осуществля- емыйваппаратах—ректификационныхколоннах—путеммногократно- гопротивоточногоконтактированияпаровижидкости.Контактирование потоковпараижидкостиможетпроизводитьсялибонепрерывно(внасадочных колоннах), либо ступенчато (в тарельчатых ректификационных колоннах). При взаимодействии встречных потоков пара и жидкости на каждой ступени контактирования (тарелке или слое насадки) между нимипроисходиттепло-имассообмен,обусловленныестремлениемсис- темы к состоянию равновесия. В результате каждого контакта компоненты перераспределяются между фазами: пар несколько обогащается низкокипящими, а жидкость — высококипящими компонентами. При достаточнодлительномконтактеивысокойэффективностиконтактного устройствапарижидкость,уходящиеизтарелкиилислоянасадки,могут достичьсостоянияравновесия,тоестьтемпературыпотоковстанутодинаковымииприэтомихсоставыбудутсвязаныуравнениямиравновесия. Такойконтактжидкостиипара,завершающийсядостижениемфазового равновесия,принятоназыватьравновеснойступенью,илитеоретической тарелкой. Подбирая число контактных ступеней и параметры процесса (температурный режим, давление, соотношение потоков, флегмовое
397
число и др.), можно обеспечить любую требуемую четкость фракционирования нефтяных смесей.
Место ввода в ректификационную колонну нагретого перегоняемого сырья называют питательной секцией (зоной), где осуществляется однократное испарение. Часть колонны, расположенная выше питательной секции, служит для ректификации парового потока и называется концентрационной (укрепляющей), а другая — нижняя часть,
вкоторой осуществляется ректификация жидкого потока, — отгонной, или исчерпывающей, секцией.
Различают простые и сложные колонны.
Простые колонны обеспечивают разделение исходной смеси (сырья) на два продукта: ректификат (дистиллят), выводимый с верха ко- лоннывпарообразномсостоянии,иостаток—нижнийжидкийпродукт ректификации.
Сложныеректификационныеколонныразделяютисходнуюсмесь болеечемнадвапродукта.Различаютсложныеколоннысотборомдополнительныхфракцийнепосредственноизколонныввидебоковыхпогонов иколонны,укоторыхдополнительныепродуктыотбираютизспециальныхотпарныхколонн,именуемыхстриппингами.Последнийтипколонн нашелширокоеприменениенаустановкахпервичнойперегонкинефти.
Для разделения бинарных или многокомпонентных смесей на 2 компонента достаточно одной простой колонны (если не предъявляются сверхвысокие требования к чистоте продукта). Для разделения же многокомпонентных непрерывных или дискретных смесей на более чем2компонента(фракции)можетприменятьсяоднасложнаяколонна либо система простых или сложных колонн, соединенных между собой
вопределенной последовательности прямыми или обратными паровыми или (и) жидкими потоками. Выбор конкретной схемы и рабочих параметров процессов перегонки определяется технико-экономичес- кими и технологическими расчетами с учетом заданных требований по ассортименту и четкости разделения, термостабильности сырья и продуктов, возможности использования доступных и дешевых хладоагентов, теплоносителей и т.п.
Четкостьпогоноразделения—основнойпоказательэффективнос- тиработы ректификационных колонн– характеризует их разделительную способность. Она может быть выражена в случае бинарных смесей концентрациейцелевогокомпонентавпродукте.Применительнокректификации нефтяных смесей она обычно характеризуется групповой чистотой отбираемых фракций, то есть долей компонентов, выкипающих по кривой ИТК до заданной температурной границы деления сме-
398
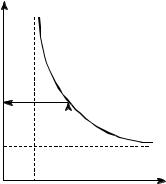
си в отобранных фракциях (дистиллятах или остатке), атакже отбором фракцийотпотенциала.Каккосвенныйпоказательчеткости(чистоты) разделениянапрактикечастоиспользуюттакуюхарактеристику,какналегание температур кипения соседних фракций в продукте. В промышленной практике обычно не предъявляют сверхвысоких требований по отношению к четкости погоноразделения, поскольку для получения сверхчистых компонентов или сверхузких фракций потребуются соответственно сверхбольшие капитальные и эксплуатационные затраты. В нефтепереработке, например, в качестве критерия достаточно высокой разделительной способности колонн перегонки нефти на топливные фракции считается налегание температур кипения соседних фракций в пределах 10…30°С.
Установлено, что на разделительную способность ректификационных колонн значительное влияние оказывают число контактных ступеней и соотношение потоков жидкой и паровой фаз. Для получения продуктов, отвечающих заданным требованиям, необходимо, наряду с другими параметрами ректификационнойколонны (давление, температура,местовводасырьяит.д.),иметьдостаточноечислотарелок(или высоту насадки) и соответствующее флегмовое и паровое числа.
Флегмовое число (R) характеризует соотношение жидкого и парового потоков в концентрационной части колонны и рассчитывается как R=L/D,где Lи D— количества соответственно флегмы и ректификата.
Паровоечисло(П) характеризует соотношение контактирующихся потоков пара и жидкости в отгонной секции колонны, рассчитываемое как П=G/W,где Gи W— количества соответственно паров и кубового
продукта. |
|
|
Число тарелок (N) колонны |
|
|
(или высота насадки) определяет- |
|
|
ся числом теоретических тарелок |
|
|
(NТ), обеспечивающим заданную |
|
|
четкость разделения при приня- |
|
|
том флегмовом (и паровом) числе, |
|
|
а также эффективностью контакт- |
|
|
ных устройств (обычно КПД реаль- |
||
|
||
ных тарелок или удельной высотой |
MIN |
|
насадки, соответствующей 1 теоре- |
||
тическойтарелке).Зависимостьчис- |
|
|
латеоретическихтарелокотфлегмо- |
MIN |
|
вогочислаколонныможновыразить |
||
|
||
ввидеграфика,какэтопредставлено |
Рис.3.6.Зависимостьчислатеоретическихта- |
|
на рис. 3.6. |
релок NТв колонне от флегмового числа Rпри |
|
заданной четкости разделения смеси |
399
Анализ графика позволяет выявить следующую закономерность, обусловливающая граничные пределы нормального функционирования ректификационных колонн: заданная четкость разделения смесей может быть обеспечена (достигнута) лишь при одновременном выполнении ограничений по флегмовому числу и числу теоретических тарелок:
Rмин <R<∞, ∞ >NТ >NТмин,
где – Rмин и NТмин — минимальные значения соответственно флегмового числа и числа теоретических тарелок.
Любая точка на кривой (рис. 3.6) может быть выбрана в качестве рабочей. Это означает, что заданная четкость разделения смеси может быть достигнута бесконечным множеством пар чисел NТ и R. Как следует из рисунка, флегмовое число, следовательно, и количество орошения в колонне изменяется от минимального значения до бесконечно большой величины; при этом необходимое для обеспечения заданной четкостиразделениячислотарелокбудетизменятьсясоответственноот бесконечно большой величины до некоторой минимальной. Очевидно, при увеличении количества орошения будут расти эксплуатационные затраты(связанныесрасходомэнергиинаперекачку,теплавкипятильнике и холода в конденсаторах), а капитальные затраты вначале будут существенноуменьшатьсяврезультатеснижениявысоты,азатемрасти из-за увеличения диаметра колонны. Из опыта эксплуатации колонн установлено,чтооптимальноезначениефлегмовогочисла,соответствующее минимуму общих затрат на ректификацию (рис. 3.7), не намного превышает минимально необходимое Rмин:
Rопт =βRмин ,
где β — коэффициент избытка флегмы (в пределах 1,0…1,3).
Фактическое число тарелок Nф определяется либо аналитическим расчетом (на ЭВМ с использованием уравнений равновесия фаз, материального и теплового балансов потоков), либо исходя из опытных данных с учетом эффективного КПД тарелки ηТ:
Nф = NТ/ηТ .
В зависимости от конструкции и места расположения в колонне ηТ изменяется в пределах 0,3…0,9. На технико-экономические показатели ичеткостьпогоноразделенияректификационнойколонны,кромеееразделительной способности, в значительной степени влияют физические свойства (молекулярная масса, плотность, температура кипения, лету-
400