
Технология синтеза мономеров / Основы химии и технологии мономеров Елигбаева
.pdfПеремешивание в реакторе часто является необходимым условием осуществления реакции в заданном режиме температуры и времени. Способ перемешивания зависит от агрегатного состояния реагентов. Так, для смешения газов применяют сопло, инжектор, лабиринтный и каскадный смесители. Их действия основано на перемешивании путем диффузии в смешанных потоках газа. Для перемешивания жидкостей и их смесей с твердыми телами используют механический способ с помощью мешалок различных типов (пропеллерной, турбинной, якорной и т.д.) или шнеков. Часто используется и пневматическое перемешивание с помощью воздушного подъемника или пневматического смесителя. Для перемешивания в системе газ
– жидкость применяют барботаж, а в системе газ – твердое предпочтительнее перемешивание за счет движения твердого слоя материала (движущийся слой и кипящий слой).
Теплообмен в реакторах происходит при нагревании или охлаждении реакционной смеси. Различают два основных метода теплообмена – прямой и косвенный. В случае прямого теплообмена теплота в реакторе передается по одному из следующих вариантов: 1) за счет циркуляции теплоносителя непосредственно в реакционном объеме; 2) за счет частичного или полного испарения одного их компонентов реакционной смеси или за счет эндотермической реакции; 3) теплоту получают непосредственно в реакторе за счет экзотермической реакции или электрического разряда.
Примерами могут служить различные ситуации. При сильно экзотермической реакции, чтобы отвести излишнее тепло, жидкий реагент частично испаряют, что приводит к поглощению теплоты. Образующиеся при этом пары конденсируют в наружном холодильнике и возвращают в реактор.
Для нагревания реагента его часто смешивают с водяным паром. Для охлаждения газообразного продукта экзотермической реакции его смешивают с потоком холодной жидкости.
41
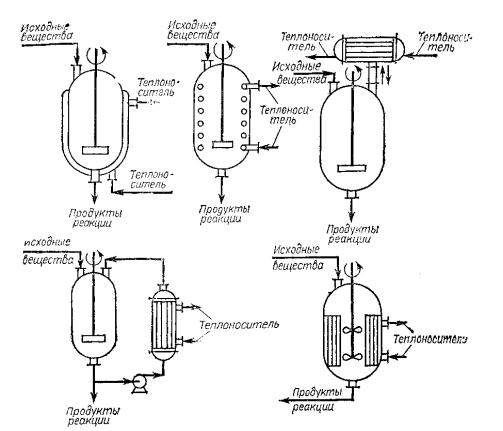
При косвенном теплообмене теплоноситель и реакционная смесь в реакторе разделены непроницаемой стенкой, через которую происходит нагрев или охлаждение. Поверхность теплообмена может иметь различную форму
(змеевик, рубашка, кольцо ит.д.) и располагаться как внутри, так и снаружи реактора. На рис. 8. приведены примеры расположения теплообменных устройств и способов обеспечения оптимальных температур в реакторах.
а |
б |
в |
|
г |
д |
|
Рисунок 8. Типы теплообменных устройств в аппаратах смешения:
а - аппарат с рубашкой; б – с внутренним змеевиком; в – с наружным дефлегматором; г – с наружным теплообменником; д – с внутренним теплообменником
42
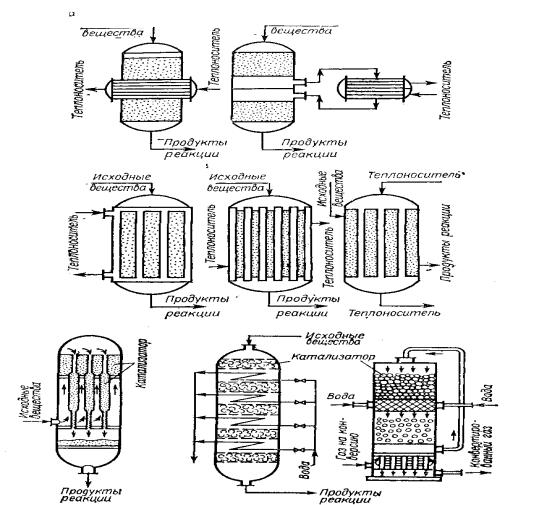
а |
исходные |
б |
исходные |
|
|
||
|
|
|
|
в |
г |
в |
|
||
|
|
е |
ж |
з |
|
Рис. 9. Типы теплообменных устройств в реакторах вытеснения:
а – реактор с внутренним теплообменником; б – с наружным теплообменником; в – с кольцевыми охлаждающими зонами; е – с катализатором в трубках; д – с катализатором в межтрубном пространстве; е
– с сочетанием полок и трубок с катализатором; ж – с полками и водяным и холодильниками между слоями катализатора; з – с впрыскиванием воды между слоями катализатора
3.2 Массообменные процессы
Массообменными называются такие процессы, сущность которых состоит
в переходе вещества из одной фазы в другую в направлении достижения
равновесия между фазами. Скорость этих процессов определяется законами
фазового равновесия.
43
Процессы массообмена используются в химической технологии для разделения реакционной смеси, выделения и очистки целевого продукта,
предварительной подготовки исходного реагента, извлечения ценных или вредных веществ из газовых выбросов и других операций.
К массообменным процессам относятся: абсорбция, дистилляция и ректификация, экстракция, адсорбция, растворение и кристаллизация, сушка.
Все эти технологические операции особенно важны в производстве мономеров,
к чистоте которых предъявляются повышенные требования, поскольку наличие малейших примесей (иногда > 0,01 %) существенно снижает в ходе дальнейшей переработки качество полимеров и материалов на их основе.
В процессах массообмена между двумя фазами принимает участие три компонента. Два из них являются основой двух различных фаз (жидкость – газ,
или твердое – жидкость, или две несмешивающиеся жидкости). Третий компонент – это извлекаемое вещество, переходящее из одной фазы в другую до достижения равновесия. Движущей силой массообмена является разница
(градиент) концентраций распределяемого вещества между фазами:
с = с – сp
где с – фактическая концентрация вещества в данной фазе;
сp – равновесная концентрация его.
Процесс массопередачи выражается основным уравнением ее для единицы времени:
Δm = k cf
где Δm - количество вещества, перешедшее из одной фазы в другую;
f - поверхность раздела фаз; c - движущая сила процесса массообмена.
Таким образом, скорость массопередачи определяется перепадом
(градиентом) концентрации между фазами и величиной поверхности их
44
раздела. Создание максимальной поверхности соприкосновения фаз является одной из главных задач в технологических процессах массообмена.
3.2.1 Абсорбция
Абсорбция - это процесс избирательного поглощения газов или паров из газовой смеси жидким поглотителем (абсорбентом). При физической абсорбции поглощаемый компонент не взаимодействует химически с поглотителем и поэтому процесс обратим. На этом основан обратный процесс десорбции, т.е. выделение поглощенного газа из его раствора в абсорбенте.
Если же поглощенный компонент образует с абсорбентом химическое соединение, то процесс называют хемосорбцией.
В основе процесса абсорбции лежат законы Генри и Рауля. Согласно закону Генри количество газа, растворяющегося в жидкости, прямо пропорционально парциальному давлению газа над ней:
P* = k·x
где P* - парциальное давление растворенного газа; x - содержание газа в мольных долях;
k - коэффициент Генри, зависимый от температуры и свойств газа и жидкости.
По закону Рауля парциальное давление компонента над раствором равно давлению пара чистого компонента (p), умноженному на его мольную долю в растворе:
P* = p·x
Из рассмотрения законов Рауля и Генри следует, что растворимость газов в жидкости увеличивается с повышением давления и понижением температуры, а
также зависит от физических и химических свойств газов и жидкостей. Кроме того, при повышении температуры абсорбента (т.е. уменьшении растворимости газа) или понижении давления происходит десорбция поглощенного газа.
45
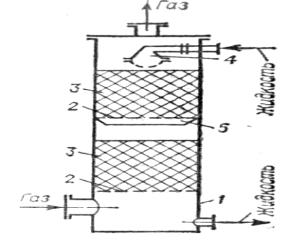
В промышленности процесс абсорбции обычно сочетают с десорбцией, что позволяет многократно использовать абсорбент. Примерами промышленного использования абсорбции могут служить процессы разделения углеводородных газов на нефтеперерабатывающих установках, очистка газовых выбросов от ядовитых примесей, выделение ценных компонентов из газовых фракций крекинга и пиролиза, отделение реакционных газовых смесей от аммиака,
углекислого газа, сероводорода и т.п.
Процесс абсорбции проводится в аппаратах колонного типа, где реализуется противоток абсорбента и разделяемой газовой (паровой) смеси.
Как и другие процессы массопередачи, абсорбция протекает на границе раздела фаз, поэтому конструкция абсорбционного аппарата должна обеспечивать максимальную поверхность соприкосновения между жидкостью и газом. По способу образования этой поверхности абсорберы подразделяются на следующие группы: насадочные, барботажные (тарельчатые) и
распылительные.
Насадочные адсорберы являются наиболее распространенными. Они представляют собой колонный аппарат, заполненный насадкой (рис. 10.).
Рисунок 10. Насадочный абсорбер:
1 – корпус;
2 - решетка;
3 - насадка;
4 - брызгалка;
5 – направляющий конус.
Насадка может иметь различную форму (кольца Рашига, куски труб,
шары) и выполняется из различных материалов (керамика, стекло, дерево,
46
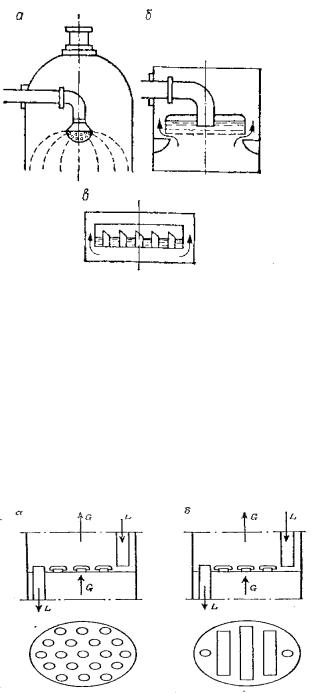
металл и пр.) Она может заполнять либо весь объем, либо укладываться слоями на разделительных решетках. Для орошения используют различные устройства:
брызгалки, открытые сита, распределительные тарелки с трубками (рис. 11.).
Рисунок 11. Оросительные устройства: .
а – брызгалка; б – открытое сито; в– распределительная тарелка с трубами.
Барботажные абсорберы представляют собой тарельчатые колонны.
Чаще всего применяются тарельчатые колонны с колпачками круглого или туннельного сечения (рис. 12). Наряду с колпачковыми имеются и другие виды тарелок: ситчатые, клапанные, струйные.
Рисунок 12. Колпачковая тарелка:
а – с круглым колпачком; б – с туннельным колпачком
Во всех случаях на тарелках поддерживаются слои жидкого абсорбента,
через который барботирует восходящий поток газа, распределяясь в нем
47
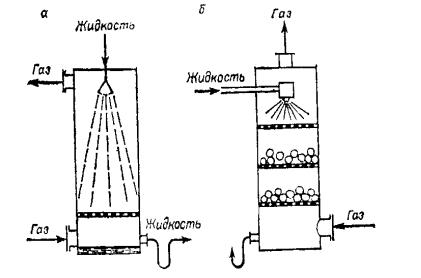
пузырьками и струйками. Газ последовательно проходит через слои жидкого абсорбента на тарелках, расположенных в колонне на определенном расстоянии друг от друга. Жидкость непрерывно перетекает с верхних тарелок на нижние,
обогащаясь постепенно тем компонентом газовой смеси, который хорошо растворим в абсорбенте.
Газовая смесь, попадая в межтарелочное пространство, отделяется от унесенных капель и брызг жидкости. Контакт между поднимающимся газом и
жидкостью осуществляется непрерывно. Абсорбционная колонна может
работать при атмосферном или избыточном давлении газа.
Распылительные абсорберы, показанные на рис. 13, отличаются тем, что в них поверхность взаимодействия между газом и жидким абсорбентом образуется каплями жидкости, полученными с помощью форсунок,
распылителей, сеток и т.п. Распылители подразделяются |
на три группы: |
гидравлические, работающие под давлением жидкости; |
пневматические, в |
которых распыление достигается сжатым газом или паром; центробежные, где распыление осуществляется быстро вращающимся диском, на который подается жидкий абсорбент.
Рисунок 13. Распылительный абсорбер:
а – полый; б – с шаровой насадкой.
48
Сепараторы для разделения газожидкостных потоков используются для отделения жидкости, унесённой газом, поскольку газ, выходящий из абсорбера, все еще содержит в своем потоке мелкие капли и брызги жидкого абсорбента. Сепараторы устанавливают сразу после абсорбционной колонны
или их монтируют вместе с колонной перед выходом газа.
В насадочных абсорберах самым простым сепарационным устройством может служить дополнительный слой насадки высотой около 30см из мелких колец. Существуют также сепарационные устройства больших размеров,
работающие на различных принципах воздействия на жидкую фазу при
разделении газожидкостной смеси: гравитационные, центробежные, вихревые.
После отделения в сепараторе остатков жидкой фазы газ, очищенный в процессе абсорбции от одного из компонентов, может быть выброшен в атмосферу или отправлен на дальнейшие выделение (в зависимости от технологических целей). Вся собранная жидкая фаза (т.е. раствор одного из компонентов первичной газовой смеси в жидком абсорбенте) отправляется на
десорбцию.
Десорбция представляет собой обратный процесс удаления растворенного газа из раствора с целью регенерации отработанного жидкого абсорбента и выделения поглощенного газа. Способом десорбции в зависимости от свойств
обрабатываемой системы может быть отгонка или ректификация с
десорбирующим агентом (водяной пар, инертный газ) или без него, а также повышение температуры абсорбента или понижение его давления, которые приводят к снижению растворимости газа. Процесс десорбции осуществляется в таких же аппаратах, как и абсорбции, чаще всего в колоннах тарельчатого типа.
На рис. 14. показана схема абсорбционно–десорбционной установки. Газ,
содержащий извлекаемый компонент проходит через абсорбер 1 снизу вверх, а
жидкость стекает сверху вниз. При этом уходящий из абсорбера газ встречается со свежим абсорбентом, что обеспечивает более полное его извлечение.
49
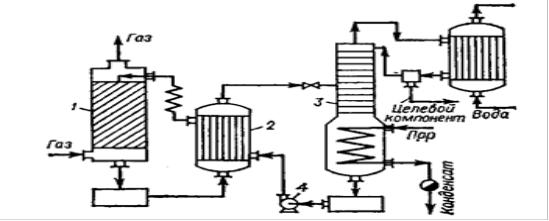
Абсорбер – это колонна, заполненная насадкой, уложенной на опорные решетки, имеющие отверстия для прохождения газа и стока жидкости. Жидкая фаза, выходящая из абсорбера, проходит теплообменник 2, где она подогревается и затем поступает на десорбцию в ректификационную колонну 3.
В десорбере 3 абсорбент освобождается от поглощенного газа и насосом 4
подается в теплообменник 2, где охлаждается и возвращается в абсорбер.
3.2.2 Дистилляция и ректификация
Дистилляция и ректификация – это процессы разделения жидких смесей,
основанные на неравенстве составов жидкости и пара, образующегося над ней при испарении. Они широко применяются в химической технологии при разделении бинарных или многокомпонентных смесей жидкостей и очистке органических растворителей.
Дистилляция или перегонка - это процесс частичного испарения жидкой смеси с образованием пара, конденсация которого приводит к образованию жидкости нового состава (дистиллята), который содержит больше летучего компонента, чем исходная смесь.
Рисунок 14. Схема абсорбционно-десорбционной установки непрерывного
действия: 1 - абсорбер (насадочная колонна); 2 – теплообменник;
3 – десорбер (ректификационная колонна); 4 – насос.
50