
Тут есть жесткость воды
.pdfуменьшение тепловых потерь за счёт эффективной теплоизоляции поверхностей аппаратуры и трубопроводов;
использование вторичных энергетических ресурсов.
2.6.ВТОРИЧНЫЕ ЭНЕРГЕТИЧЕСКИЕ РЕСУРСЫ
Степень использования тепла в химико-технологическом процессе характеризует тепловой коэффициент полезного действия. Тепловой к.п.д. показывает отношение количества тепла, использованного непосредственно на осуществление основных химических реакций, к общему количеству затраченного тепла. Тепловой к.п.д. является частным случаем коэффициента использования энергии. В химическом производстве много тепла теряется с удаляемыми из аппаратов продуктами реакции, отходящими газами и в окружающую среду. Например, в производстве негашёной извести из известняка тепло, получаемое от сгорания топлива, расходуется на испарение влаги, разложение карбонатов, теряется с отходящими газами, выгружаемой известью, через стенки печи в окружающую среду. На разложение карбонатов затрачивается лишь 65% от общего количества тепла, остальное составляют потери. Для повышения теплового к.п.д., а, следовательно, и для экономии топлива и энергии, предусматривают утилизацию тепла (использование вторичных энергетических ресурсов).
Утилизация тепла – это повторное использование тепловой энергии, выделяющейся в ходе производственного процесса и зачастую выбрасываемой в окружающую среду в виде неиспользованного отходящего тепла. Это отходящее тепло можно эффективно использовать.
Вторичные энергетические ресурсы (ВЭР) – это энергетический потенциал продукции, отходов, побочных и промежуточных продуктов, образующихся в химико-технологической системе. ВЭР могут быть частично или полностью использованы для нужд предприятий, что позволяет сократить потери энергии в окружающую среду. Так, вторичными энергоресурсами производства аммиака, наиболее энергоёмкого в химической промышленности, являются танковые и продувочные газы, физическая теплота дымовых газов трубчатых печей, конвертированного газа, синтез-газа. Танковые и продувочные газы используют в качестве топлива, физическая теплота конвертированного газа и синтез - газа применяется для получения пара в котле-утилизаторе, тепло дымовых газов используют для подогрева природного газа, парогазовой смеси и воздуха, поступающих на конверсию, и для перегрева водяного пара, вырабатываемого в котле-утилизаторе. Наибольшими тепловыми вторичными ресурсами обладают предприятия химической, нефтеперерабатывающей и нефтехимической промышленности, чёрной и цветной металлургии, промышленности строительных материалов и некоторых других отраслей экономики. Рациональное использование вторичных энергетических ресурсов является одним из крупнейших резервов экономии топлива в промышленности, способствующее снижению энергоёмкости продукции.
По виду энергии вторичные энергетические ресурсы разделяют на три группы:
горючие (топливные) ВЭР – побочные газообразные продукты технологических процессов, которые могут быть использованы в качестве топлива;
тепловые ВЭР – физическое тепло отходящих газов технологических агрегатов, горячей воды и пара, теплота химических реакций;
50
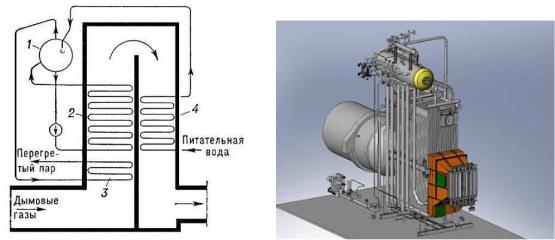
ВЭР избыточного давления – потенциальная энергия газов и жидкостей, выходящих из технологических агрегатов с избыточным давлением, которое может быть использовано.
Вторичные энергетические ресурсы могут быть использованы непосредственно как топливо, их тепло может быть использовано для получения пара, нагрева воды, материалов, поступающих в реакционные аппараты и т.д. Наиболее распространёнными утилизационными установками являются котлы-утилизаторы, водяные экономайзеры, рекуператоры и регенераторы.
Котёл-утилизатор – это агрегат, в котором тепло газообразных продуктов реакции и отходящих газов используют для производства пара. Котлы-утилизаторы обеспечивают большую экономию топлива благодаря выработке энергетического или технологического пара. Схема котла-утилизатора приведена на рис. 2.19.
Рис. 2.19. Схема водотрубного котла-утилизатора. 1 – барабан-сепаратор; 2 – испарительная часть; 3 - пароперегреватель; 4 – водяной экономайзер
Вводотрубном котле-утилизаторе вода движется по трубам, а горячие дымовые газы (с температурой 800-1500 С) проходят по наружной поверхности труб. Питательная вода, пройдя экономайзер 4, попадает в барабан 1 (находится вверху котла), из которого под действием силы тяжести (в котлах с естественной циркуляцией) попадает в опускные необогреваемые трубы, а затем в подъёмные обогреваемые, где происходит парообразование (подъёмные и опускные трубы образуют циркуляционный контур). Из-за разницы температур, а, следовательно, и плотностей среды в опускных и подъёмных трубах вода поднимается обратно в барабан. В нем происходит разделение пароводяной смеси на пар и воду. Вода заново идёт в опускные трубы, а насыщенный пар уходит в пароперегреватель 3.
Вкотлах с естественной циркуляцией кратность циркуляции воды по циркуляционному контуру - от 5 до 30 раз.
Газотрубный котёл-утилизатор отличается от водотрубного тем, что горячие газы движутся по трубам, помещённым в корпусе котла, а вода находится в межтрубном пространстве.
Область применения водотрубных котлов по сравнению с газотрубными котлами значительно шире, особенно если требуется пар высокого давления.
Водяной экономайзер – это теплообменник, предназначенный для подогрева воды или за счёт тепла отходящих газов, которые для лучшего теплообмена движутся сверху вниз, а вода - снизу вверх (рис. 2.20.).
51
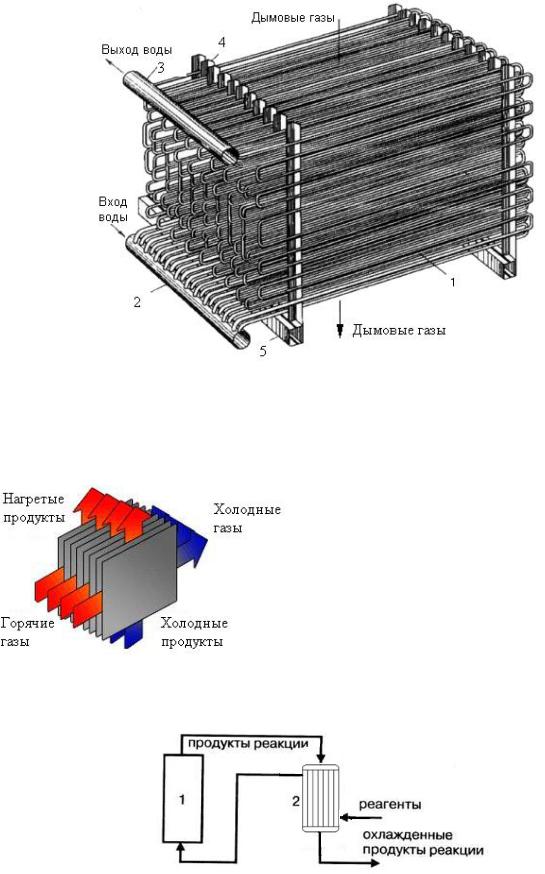
Рис. 2.20. Общий вид пакета водяного экономайзера. 1 – трубные змеевики; 2 – входной коллектор воды; 3 – выходной коллектор воды; 4 – опорные стойки; 5 – опорная балка
Область применения экономайзеров – нагрев питательной воды паровых котлов и воды систем технологического и бытового горячего водоснабжения.
Рекуператор (от лат. recuperator -
получающий обратно, возвращающий) –
это теплообменник поверхностного типа для использования теплоты отходящих газов, в котором теплообмен осуществляется непрерывно через стенку, разделяющую потоки (рис. 2.21.).
Тепло продуктов реакции или отходящих газов можно использовать для
предварительного нагрева материалов, Рис. 2.21. Схема теплообмена в рекуператоре поступающих в реакционный аппарат
(рис. 2.22.).
.
Рис. 2.22. Схема использования тепла продуктов реакции для нагрева исходных реагентов. 1
– реактор; 2 – теплообменник.
52
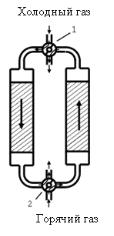
Рекуперация позволяет использовать высоко- и низкотемпературные вторичные энергетические ресурсы.
Для использования тепла газообразных продуктов реакции или отходящих газов кроме рекуператоров применяют и так называемые регенераторы.
Регенераторы – периодически действующие камеры, заполненные насадкой. Обычно насадкой являются решётки из кирпича, керамические или металлические шары и др. Теплота горячих газов сначала аккумулируется в теплоёмкой насадке, а затем передаётся нагреваемому газу (например, воздуху). Схема регенератора с неподвижной насадкой приведена на рис. 2.23. Непрерывный процесс теплопередачи между теплоносителями по этой схеме осуществляется с помощью двух регенераторов: когда в одном из них происходит охлаждение горячего теплоносителя, в другом нагревается холодный теплоноситель. Затем аппараты переключаются с помощью клапанов 1 и 2, после чего в каждом из них процесс
Рис. 2.23. Схема работы теплопередачи протекает в обратном направлении. регенераторов.
Использование вторичных энергетических ресурсов позволит получить большую экономию топлива, снизить выброс вредных веществ, уменьшить тепловое загрязнение окружающей среды.
2.6.1. Энерготехнологические установки
Одним из наиболее действенных средств повышения эффективности топлива является переход к энерготехнологическим процессам.
Энерготехнологической установкой называют химико-технологическую систему, состоящую из технологических и энергетических агрегатов, тесно связанных между собой. В таких установках тепло химических реакций, продуктов реакций, отходящих газов и т.п. используется для производства энергии, которая расходуется внутри данного процесса, а также выдаётся на сторону. Энерготехнология имеет два главных практических направления. Первое направление связано с поиском путей повышения эффективности использования органической и минеральной части топлива, применяемого на электростанциях и в промышленной энергетике. Второе направление – создание энерготехнологических методов производства важнейших видов промышленной продукции (химической, строительных материалов и т.п.).
Основным назначением энерготехнологических установок является повышение коэффициента использования энергии и тем самым снижение стоимости получаемой продукции. Приведём несколько примеров энерготехнологических систем.
Энерготехнологические системы использования топлива. Сущность энерготехнологического использования топлив заключается в том, что топливо перед сжиганием в котельной топке подвергается в определённых условиях термической переработке с получением высококалорийного газа и ценных твёрдых и жидких продуктов. Такие схемы служат для получения жидких смол и газового бензина, содержащих ценные виды химического сырья, высококалорийного газа, цементного клинкера и других строительных материалов. Эти схемы применимы при потреблении большинства твёрдых, жидких и газообразных видов топлива, однако их назначение зависит от конкретных условий.
53
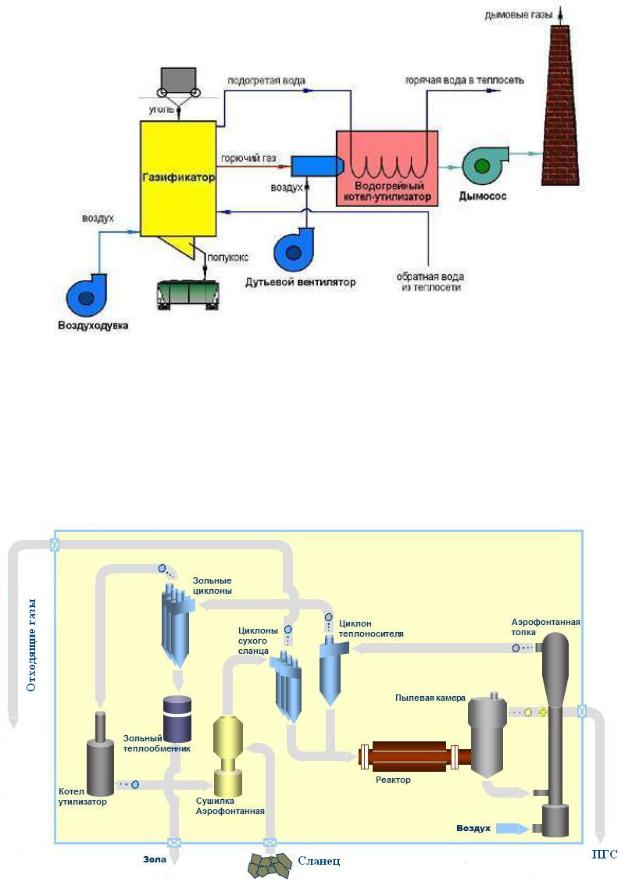
Рис. 2.24. Энерготехнологическая схема газификации угля
Для энерготехнологического использования наиболее перспективны твёрдые топлива с большим выходом летучих веществ. К ним относятся бурые угли, горючие сланцы, торф. На рис. 2.24. приведена простейшая энерготехнологическая схема использования угля.
Уголь сначала подвергают термической переработке с получением высококалорийного газа и ценного продукта – полукокса. Газ далее сжигают в топке котла-утилизатора, а полукокс идёт на использование (например, как топливо в металлургии, для производства карбида кальция и др.).
Рис. 2.25. Энерготехнологическая схема переработки горючих сланцев.
54
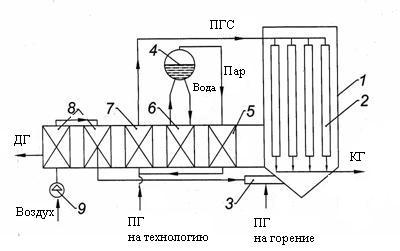
Энерготехнологическая схема переработки горючих сланцев с получением жидких и газообразных продуктов, а также зольного остатка реализована на установках с твёрдым теплоносителем УТТ (процесс Galoter). Газ и жидкие сланцевые продукты используют в качестве энергетического и технологического топлива, а зольный остаток может быть использован в промышленности строительных материалов.
В основу энерготехнологической схемы использования горючих сланцев положен метод термической переработки мелкозернистого сланца с твёрдым зольным теплоносителем (рис. 2.25.). Метод основан на применении сланцевой золы в качестве теплоносителя, смешиваемого во вращающемся реакторе барабанного типа с перерабатываемым, предварительно высушенным сланцем. Охладившийся теплоноситель вновь нагревается за счёт тепла сжигаемого твёрдого остатка, образующегося при термическом разложении сланцевого полукокса.
Энерготехнологические системы использования природного газа предусматривают его глубокую переработку с получением газовой серы, этилена, ацетилена и других ценных компонентов.
Энерготехнологические системы использования теплоты химических реакций. В
современной химической технологии большое значение имеет создание энерготехнологических процессов и систем, в которых использовалась бы теплота химических реакций. Классическими примерами являются производство аммиака, разбавленной азотной кислоты, карбамида.
Рассмотрим принцип создания энерготехнологической схемы на примере получения водорода паровой конверсией природного газа в производстве аммиака (рис. 2.26.). Основным технологическим звеном энерготехнологической установки получения водорода является трубчатая печь-реактор 1, где происходит паровая конверсия метана:
CH4 + H2O ↔ 3H2 + CO; ∆Н = 206,4 кДж/моль.
Рис. 2.26. Энерготехнологическая схема получения водорода конверсией природного газа. ПГ – природный газ; ПГС – парогазовая смесь; КГ – конвертированный газ; ДГ – дымовые газы; 1 – трубчатая печь; 2 – трубы с катализатором; 3 – горелка; 4 – барабан; 5 – пароперегреватель; 6 – испаритель котла-утилизатора; 7 – подогреватель парогазовой смеси; 8 – воздухоподогреватель; 9 – воздуходувка.
Исходное сырье (природный газ) под давлением прокачивают вместе с паром через подогреватель 7, а оттуда в подогретом состоянии ПГС поступает в печь-реактор 1 для конвертирования. Необходимый для конверсии водяной пар требуемых давления и
55
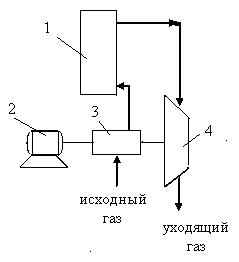
температуры подается из парового котла, работающего на отходящих продуктах сгорания, поступающих из реактора. Котловая вода из барабана 4 поступает в испарительную часть котла 6. Отсепарированный пар из барабана 4 направляется в пароперегреватель 5, оттуда пар вместе с природным газом поступает в подогреватель 7, а затем в реактор для участия в процессе конверсии. Так как реакция конверсии природного газа водяным паром эндотермическая, реакционные трубы 2 обогревают снаружи дымовыми газами, образующимися при сжигании топливного природного газа в горелках 3. Воздух для горения вентилятором 9 подается в воздухоподогреватель 8, а затем в горелки трубчатой печи. Отходящие от реактора 1 продукты сгорания с температурой свыше 900°С последовательно проходят газоходы пароперегревателя 5, испарителя 6, подогревателя сырья 7, воздухоподогревателей 8 и дымососом выбрасываются в дымовую трубу. Конвертированный газ на выходе из реактора имеет температуру 750-850°С и направляется для дальнейшего технологического использования.
Количество пара, вырабатываемого в данной энерготехнологической установке, превышает потребность для целей конверсии. Избыток пара поступает в заводскую сеть для нужд производства.
Врезультате использования энерготехнологических систем в производстве аммиака расход электроэнергии снизился почти в 8 раз; в установках производства карбамида на 40% сократился расход пара, получаемого со стороны.
Вхимико-технологических системах имеются возможности и для сбережения электроэнергии. Особенно это актуально для электротермических (например, электрометаллургия) и электрохимических процессов (электролиз). Экономию электроэнергии можно получить за счёт увеличения единичной мощности аппаратов, усовершенствования их конструкций, уменьшения электрического сопротивления электродов и электролитов. В процессах, протекающих при высоких давлениях, целесообразно использовать избыточную энергию давления газов и жидкостей для сжатия и перемещения веществ, направляемых в процесс. Для этого используют агрегаты мотор - компрессор – турбина (рис. 2.27) и мотор – насос – турбина.
Рис. 2.27. Схема агрегата мотор – компрессор – турбина. 1 – реактор; 2 – электромотор; 3 – компрессор; 4 – турбина.
Газ, поступающий в реактор 1, сжимают в компрессоре 3, который находится на одном валу с турбиной 4 и электромотором 2. Выходящий из реактора газ под давлением расширяется в турбине 4, которая вращает компрессор 3, повышающий давление подаваемого в реактор 1
56
газа. Потери энергии компенсирует электродвигатель 2. Таким образом, можно сэкономить до 50% энергии, расходуемой на сжатие газа. Подобные агрегаты целесообразно использовать в производстве аммиака и других химических производствах, где используют высокие давления.
Использование вторичных энергетических ресурсов является особенно актуальным на предприятиях с большим расходом топлива, тепловой и электрической энергии. При правильном использовании вторичных энергоресурсов, образовавшихся в виде тепла отходящих газов технологических агрегатов, тепла основной и побочной продукции, тепла химических реакций достигается значительная экономия топлива.
Использование вторичных энергетических ресурсов не ограничивается лишь энергетическим эффектом - это и охрана окружающей среды, в том числе воздушного бассейна, уменьшение количества выбросов вредных веществ. Некоторые из этих выбросов могут давать дополнительную продукцию, например, диоксид серы, выбрасываемый с отходящими газами, можно улавливать и направлять на выпуск газовой серы или серной кислоты.
57
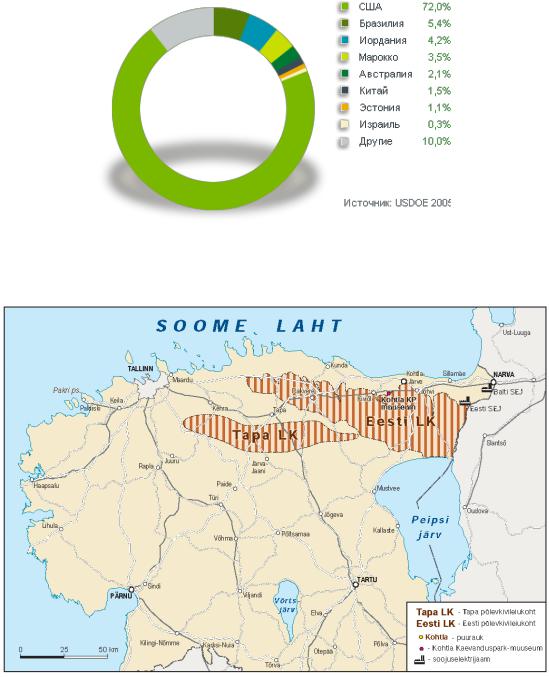
2.7.СЫРЬЕВЫЕ И ЭНЕРГЕТИЧЕСКИЕ РЕСУРСЫ ЭСТОНИИ
2.7.1. Горючий сланец
Из полезных ископаемых наибольшее значение для Эстонии имеет горючий сланец - кукерсит. Сланцы есть во многих частях мира, известно более 600 месторождений на всех материках. Крупнейшие запасы сланца расположены в США, Бразилии, Иордании, России и Мексике. В Америке, оценочно, находится 72% мировых запасов сланца (рис. 2.28.).
Рис. 2.28. Мировые запасы сланца.
Эстонское месторождение горючих сланцев (рис. 2.29.) является частью Прибалтийского бассейна, к которому относятся также Тапаское и Ленинградское (Россия) месторождения.
Рис. 2.29. Месторождения сланца в Эстонии. Eesti LK – Эстонское месторождение; Tapa LK
– Тапаское месторождение.
Горючие сланцы Прибалтийского бассейна известны с 18 века. Глубина залегания сланцев на Эстонском месторождении до 75 м, на Тапаском и Ленинградском – до 170 м. Мощность
58
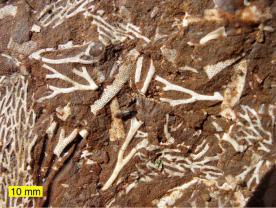
сланцевого пласта в Эстонском месторождении составляет 2,5 – 3,0 м, причём слои сланца чередуются со слоями известняка. Малая мощность сланцевых пластов является невыгодной отличительной чертой Прибалтийского месторождения. Весь запас эстонского сланца оценивается в 4,7 млрд. тонн. Промышленное освоение Эстонского месторождения ведётся с 1916 года. В Эстонском месторождении представлены и другие виды полезных ископаемых. В западной части бассейна помимо известняка находятся диктионемовый сланец и фосфориты.
Сланец – осадочная порода, образовавшаяся 400-500 миллионов лет назад на дне водоемов. Образовавшиеся из донных отложений доисторических морей и озер горючие сланцы, как правило, старше каменных углей. А диктионемовые сланцы, открытые под пластами кукерсита, еще на десятки миллионов лет старше. Сланец состоит из органических веществ, образовавшихся из одноклеточных организмов, бактерий, водорослей озер и морей и биомассы фито- и зоопланктона.
Кукерсит (англ. kukersite) - горючий сланец коричневато-бурого цвета, залегающий в Прибалтийском сланцевом бассейне (рис. 2.29.). Название сланца произошло от немецкого названия эстонского селения Кукрузе (Kukruse). Главными компонентами кукерсита являются кероген (органическое вещество) и карбонат кальция.
Источником органического вещества были сине-зелёные водоросли (цианобактерии). Известковая минеральная составляющая образована преимущественно известковыми раковинами морских организмов и их обломками. Кукерсит является одним из лучших в мире горючих сланцев. Эстонские сланцы содержат 20-60% керогена, 20-60% карбонатов и 15-50% обломочного материала, теплота сгорания составляет 8-11 МДж/кг.
Рис. 2.30.Кукерсит
Вхимический состав органического вещества сланца входят следующие основные элементы: углерод C, водород H, кислород О, азот N, сера S (табл. 8). Углерод - основной элемент, определяющий теплоту сгорания горючих ископаемых. Водород - второй по важности теплотворный элемент. Он играет существенную роль в энергетическом потенциале керогена, поскольку его теплота сгорания (129,8 МДж/кг) почти в 4 раза выше, чем у углерода (34 МДж/кг).
Всоставе минеральной части горючих сланцев чаще всего встречаются кальцит, доломит, кварц, полевые шпаты, пирит и глинистые минералы.
Горючие сланцы — сложное по составу полезное ископаемое. По сравнению с другими горючими ископаемыми они содержат меньше органического вещества и, следовательно, дают меньше тепла, выделяемого при сжигании (табл.2.9.). По этому показателю они в 2 раза уступают каменному углю и в 4 раза нефти. Вот почему важно максимально использовать
59