
Лекции_строительные материалы и конструкции
.pdf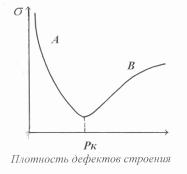
Линейные дислокации возникают под влиянием пластических и температурных деформаций и являются следствием нарушения совпадения кристаллических плоскостей. Винтовые дислокации возникают при неполном сдвиге одной части кристалла относительно другой. Дислокации подвижны внутри кристаллов и активно взаимодействуют между собой и с другими дефектами.
Поверхностные дефекты характерны для материалов, состоящих из кристаллов, различно ориентированных в пространстве и совпадают с границами зерен. Мозаичная кристаллическая структура образуется в результате сращивания отдельных кристаллических зерен под малыми углами, составляющими доли градуса. На границах зерен возникают
области скоплений дефектов структуры - дислокаций и вакансий. Зависимость прочности кристаллического тела от плотности дефектов строения представлена на рис 3. Если прочность бездефектных кристаллов исключительно высока, то повышение плотности дефектов приводит к резкому ее снижению (Рк). Дальнейшее увеличение плотности дефектов специальными методами искажения кристаллической
решетки способно повысить реальную прочность металлов. Плотность дислокаций увеличивают закалкой и пластическим деформированием.
101
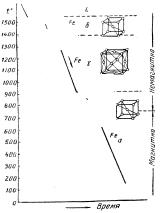
8.2. Диаграмма состояния железоуглеродистых сплавов
Свойства железоуглеродистых сплавов в значительной степени определяются содержанием углерода (рис.4). Вследствие полиморфизма железа и ограниченной растворимости углерода в железе существует
большое разнообразие фазовых и структурных |
составляющих |
||||
|
железоуглеродистых |
сплавов. |
При |
||
1539° |
охлаждении железа ниже 1539 °С про- |
||||
|
|||||
1392 ° |
исходит процесс первичной крис- |
||||
|
таллизации железа |
с образованием |
|||
|
высокотемпературной |
Feδ, имеющей |
|||
911° |
модификации |
|
кристаллическую ре- |
||
|
шетку объемно-центрированного куба. |
||||
768° |
Эта высокотемпературная форма δ- |
||||
|
|||||
|
железа может растворять до 0,1 % |
||||
|
углерода. При температуре 1392 °С |
||||
|
происходит вторичная кристаллизация |
||||
|
железа, и в интервале температур от |
||||
|
1392 °С до 911 °С железо существует в |
||||
|
форме |
γ-модификации |
с |
||
Рис.4. Кривая охлаждения |
кристаллической |
решеткой |
гране- |
||
железа |
центрированного куба. Feγ образует с |
||||
|
углеродом аустенит – твердый раствор |
внедрения, с предельной растворимостью углерода 2,14 % при температуре
1147 °С. C |
понижением температуры до 727 °С концентрация углерода |
||
уменьшается до 0,8 %. Аустенит пластичен, |
вязок, не магнитен, имеет |
||
твердость 160…200 НВ. |
|
|
|
При охлаждении ниже 911 |
°С γ-железо распадается, вновь происходит |
||
вторичная |
кристаллизация |
с образованием |
Fe с объемно- |
центрированной кубической кристаллической решеткой. При температуре 768 °С образуется Feα, обладающее магнитными свойствами.
Феррит - твердый раствор внедрения углерода в α-железе с предельной концентрацией 0,02 % при температуре 727 °С. Феррит высокопластичен и имеет относительное удлинение 40…50 %. Твердость феррита находится в пределах от 80 до 120 НВ. В холодном состоянии феррит хорошо обрабатывается давлением.
Цементит – химическое соединение Fe3C, содержащее 6,67 % углерода. Температура плавления цементита 1250 °С. Кристаллическая
102
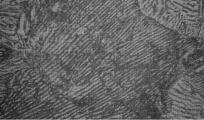
решетка сложная, ромбическая, плотноупакованная. Это самая твердая составляющая сплавов железа с углеродом, имеет условную твердость 800 НВ. Цементит ферромагнитен до температуры Кюри – 210 °С. Сплав на основе чистого цементита не используют, так как он хрупок. Различают цементит первичный, формирующийся при первичной кристаллизации и цементит вторичный, который образуется при вторичной кристаллизации. В стали вторичный цементит образуется при распаде аустенита.
Углерод может присутствовать в железоуглеродистых сплавах в свободном состоянии, в виде графита. Графит обладает низкой прочностью, это самая мягкая составляющая железоуглеродистых сплавов.
Перлит (рис.5) – эвтектоидная механическая смесь феррита и цементита, содержащая 0,8 % углерода, образующаяся при распаде аустенита при температуре 727 °С. Твердость перлита 200 НВ. У перлита высокая прочность – 800 МПа. Структура перлита состоит из чередующихся пластинок феррита и цементита.
Рис.5. Структурная составляющая |
При |
слабом |
увеличении |
||
пластинчатое |
строение перлита |
||||
железоуглеродистых сплавов: |
|||||
не различается, но полированная |
|||||
перлит |
|||||
поверхность |
имеет |
характерный |
|||
|
перламутровый блеск. Перлит при обычных условиях охлаждении образуется во всякой стали и чугуне. Сталь, содержащая 0,8 % углерода, называется эвтектоидной сталью. Под перлитным превращением понимают распад аустенита на эвтектоидную механическую смесь феррита и цементита. Сталь, содержащая углерода менее 0,8 %, называется доэвтектоидной. Она состоит из перлита и феррита. Сталь, содержащая углерода более 0,8 % называют заэвтектоидной. Заэвтектоидная сталь состоит из перлита и цементита. В заэвтектоидной стали цементит располагается в виде сетки вокруг зерен перлита.
Ледебурит - эвтектическая механическая смесь аустенита и цементита, которая формируется из расплава при первичной кристаллизации железоуглеродистого сплава, содержащего 4,3 % углерода при температуре 1147 °С. При температуре 727 °С ледебурит распадается с образование смеси цементита и перлита (превращенный
103
ледебурит). Ледебурит имеет условную твердость 700 НВ, обладает сотовым и пластинчатым строением.
Диаграмма состояния, представленная на рис.6, графически отражает в координатах «Содержание углерода»/«Температура сплава»
структуру и состояние сплавов железа с углеродом при различном содержании углерода, дает представление о температурных и концентрационных границах существования этих сплавов. Линия АВСD
– линия ликвидуса, выше которой сплав находится в жидком состоянии. Линия AНJECF – линия солидуса – геометрическое место точек конца процесса первичной кристаллизации сплава. Ниже линии солидуса сплав находится в твердом состоянии. При температуре 1147 °С при содержании углерода 4,3 % (в точке С) в системе железо-цементит происходит эвтектическое превращение: эвтектическая жидкость
кристаллизуется |
в виде |
эвтектики аустенита |
и |
цементита1 |
- |
ледебурита. Линия GSE – соответствует началу процесса вторичной |
|||||
кристаллизации |
твердого |
раствора. Линия GS |
– |
линия верхних |
критических точек (Ас3), соответствующая температуре начала процесса выделения феррита при распаде аустенита. Линия ES – линия верхних критических точек (Аcm). Она показывает температуру начала выделения вторичного цементита и соответствует предельной растворимости углерода в аустените.
104
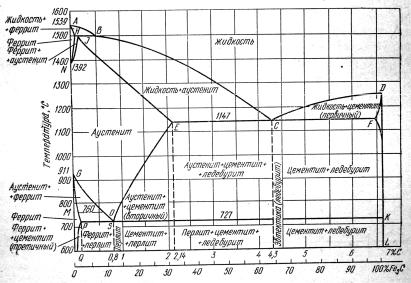
Рис. 6. Диаграмма железо-цементит
При нагреве выше верхней критической точки Аcm (линии ES) заэвтектоидные стали приобретают аустенитную структуру. Структура заэвтектоидной стали после медленного охлаждения до комнатной температуры состоит из перлита и цементитаII.
Линия PSK – линия эвтектоидного превращения, соответствующая завершению процесса вторичной кристаллизации при температуре 727оС (Ас1). При изотермическом распаде аустенита структуры перлитного типа (феррит + цементитII) образуются в интервале температур 727-500 °С.
Сплав, содержащий до 2,14 % углерода, кристаллизующийся с образованием первичной структуры аустенит, называют сталью. Сплав, с содержанием углерода более 2,14 %, кристаллизующийся с образованием первичной структуры ледебурит, называют чугуном.
Чугун, содержащий 4,3 % углерода, называют эвтектическим; менее 4,3 % С – доэвтектическим и более 4,3 % - заэвтектическим. Структура чугуна может включать перлит, феррит, цементит, графит. Механическими характеристиками чугуна можно управлять, влияя на изменение формы углеродной составляющей. Углерод в чугуне может находиться в химически связанном состоянии в цементите и в свободном состоянии в виде графита (рис.7). В белом чугуне углерод
105
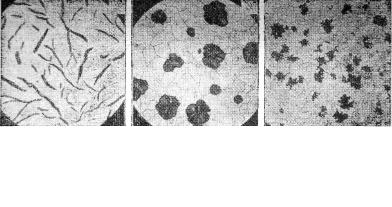
находится в химически связанном состоянии в цементите. Серый чугун характеризуется наличием графитной фазы.
а |
б |
в |
Рис. 7. Структура серых чугунов: а – обычного с пластинчатым графитом ; б – высокопрочного с шаровидным графитом ; в – ковкого с хлопьевидным графитом
Форма углерода в чугуне зависит от скорости охлаждения, содержания примесей и последующей обработки. Белые чугуны не содержат свободного графита, в них углерод находится в составе цементита. Цементит придает излому чугуна белый цвет. Получению белого чугуна способствует присутствие марганца, хрома, молибдена, вольфрама. Белый чугун имеет высокую твердость, хрупок, практически не поддается обработке резанием.
Для получения обычного серого чугуна требуется медленное охлаждение расплава. В этих условиях при высоких температурах происходит графитизация - цементит распадается с выделением пластинчатого графита. Графитизации чугуна способствует также наличие примесей кремния, алюминия, никеля и меди. В серых чугунах содержится обычно от 1,5 до 3,5 % кремния. По составу различают обычные серые чугуны с перлитной, ферритной и ферритно-перлитной основой. Свойства металлической матрицы серых чугунов аналогичны свойствам сталей.
Пластинчатый графит снижает прочность чугуна при растяжении и уменьшает пластичность сплава, так как графитовые включения по сути представляют собой микродефекты. На прочность при сжатии и твердость графит не оказывает существенного влияния. Графит, образуя смазочные пленки, снижает коэффициент трения, повышает износостойкость чугуна и улучшает обрабатываемость резанием.
106
Ферритные и ферритно-перлитные серые чугуны применяют для строительных конструкций. Перлитные чугуны используют для изготовления износостойких деталей.
В высокопрочном сером чугуне графит присутствует в виде включений шаровидной (глобулярной) формы. По механическим свойствам он превосходит и обычный серый, и ковкий чугуны. При таком строении графитовых включений металлическая матрица наименее ослаблена. Основа металлической матрицы высокопрочного чугуна такая же, как и в обычных серых чугунах. Для получения графитовых включений шаровидной формы в жидкий чугун вводят 0,03…0,07 % щелочных или щелочноземельных металлов. Высокопрочные чугуны, имея хорошие литейные свойства и износостойкость, по механическим свойствам соответствуют литой углеродистой стали и могут обрабатываться резанием. Применяются для изготовления ответственных деталей в тяжелом машиностроении – валов прокатных станов, траверс прессов.
Ковкий серый чугун получают из белого чугуна ступенчатым отжигом. Для получения ковкого чугуна белый чугун, содержащий приблизительно 2,5 % углерода, выплавленный в электропечи, нагревают в нейтральной атмосфере до 900...950 °С, а затем медленно охлаждают со скоростью 5 град/час. Структура серого ковкого чугуна характеризуется наличием графитовых включений хлопьевидной формы. Металлическая основа ковкого чугуна может быть ферритной или перлитной.
Ферритный ковкий чугун получают из белого чугуна следующего химического состава: С – 2,4…2,8 %, Si – 0,8…1,4 %, Mn – 0,3…0,4 %.
Отливки белого чугуна сначала отжигают, нагревая до 850…1000 оС в течение 20…25 часов и выдерживая при этой температуре 10…15 ч . При этом распадается первичный и частично вторичный цементит. Вторая стадия отжига протекает при 720…740 °С в течение 25…35 ч . При этом распадается цементит перлита. Излом ферритного ковкого чугуна имеет темный матовый цвет. Детали из него получают литьем с последующим отжигом.
Перлитный ковкий чугун получают из белого чугуна следующего состава: С- 2,8…3,4 %, Si – 0,5…0,8 %, Mn – 0,4…0,5 %. Отжиг производят в окислительной среде, засыпая отливки измельченной рудой, нагревом их до 1000 оС и выдержкой при этой температуре в течение 51…57 ч. Затем медленно охлаждают на воздухе. При этом значительная часть углерода в поверхностном слое выгорает.
107
Диаграмму Fe-Fe3C применяют для назначения температурных интервалов термической обработки, обработки давлением, литейного производства. Состав и количество фаз в двухфазных областях диаграммы определяют по правилу отрезков.
8.3. Влияние примесей на свойства железоуглеродистых сплавов
В состав обычных углеродистых сталей кроме железа и углерода входят в небольшом количестве примеси кремния, марганца, фосфора, серы, кислорода, азота. Их присутствие вызывается условиями получения стали. В обычных углеродистых сталях содержание кремния не превышает 0,35 % и марганца 0,9 %. В таких количествах они не оказывают существенного влияния на механические свойства сталей.
Фосфор относится к числу вредных примесей. Образуя с α-железом твердый раствор замещения, фосфор сильно искажает кристаллическую решетку феррита, в связи с чем повышаются его твердость и хрупкость. Наличие фосфора в количестве более 0,045 % делает сталь хрупкой при низких температурах. Фосфор является сильно ликвирующим элементом, поэтому содержание его в сталях не должно превышать 0,07 %. Фосфор способствует росту зерен, что ухудшает механические свойства стали. В присутствии меди добавки фосфора могут улучшать обрабатываемость и повышать коррозионную стойкость сплава.
Сера, так же как и фосфор, - вредная примесь. Сера находится в стали в виде химического соединения FеS, образуя с железом легкоплавкую эвтектику с температурой затвердевания около 985 °С. Затвердевая в последнюю очередь, она располагается по границам зерен, разобщая их хрупкой и непрочной оболочкой. При нагреве стали до красного каления эти оболочки частично расплавляются, и прочная связь между зернами нарушается. Поэтому сталь с повышенным содержанием серы становится хрупкой при горячей механической обработке. Кроме того, сера понижает коррозионную стойкость и ухудшает свариваемость стали. Содержание серы в стали не должно превышать 0,06 %.
Повышенным содержанием кислорода характеризуются плохо раскисленные стали. Кислород находится в стали преимущественно в виде хрупких оксидов: FеО, SiO2, Al2O3. FеО растворяется в железе, но при охлаждении растворимость его снижается и закись железа выделяется в виде хрупких шлаковых прослоек на поверхности зерен
108
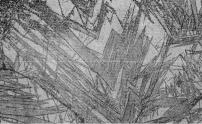
металла, способствуя повышению хрупкости и понижению ударной вязкости. В спокойной стали 0,002…0,001 % кислорода, в кипящей —
0,03…0,08 %.
Азот присутствует в стали в виде нитрида Fe4N или в свободном виде, располагаясь в дефектах кристаллов, трещинах, повышая хрупкость. Повышенное содержание азота снижает пластичность стали.
Существенное влияние на свойства чугуна оказывает форма углеродной составляющей. При медленном охлаждении чугуна цементит распадается с образованием графита. Кремний способствует графитизации чугуна. Марганец в количестве 0,5…1,4 % препятствует графитизации. Фосфор не оказывает существенного влияния на процесс графитизации. Сера, являясь вредной примесью, ухудшает литейные свойства чугуна, увеличивает его усадку, повышает склонность к трещинообразованию, снижает температуру хрупкости. Чтобы устранить вредное влияние серы, в состав чугуна вводят марганец. Марганец образует с серой тугоплавкое соединение MnS – пластичный сульфид марганца, с температурой плавления 1620 °С.
8.4. Термическая обработка стали
Термическая обработка стали производится с целью придать ей ту или иную структуру для изменения соответствующим образом ее свойств, поскольку последние определяются структурой металла. При этом под термином “термическая обработка” понимают лишь такие приемы изменения внутреннего строения стали при которых как действующим фактором пользуются исключительно только теплом, не прибегая к другим воздействиям. Основой процессов термической
|
обработки |
|
|
|
является |
||
|
полиморфизм |
железа |
и |
его |
|||
|
твердых |
|
|
растворов |
|||
|
определяющих структуру стали. |
||||||
|
Термическая |
|
обработка |
||||
|
заключается |
в |
нагреве |
сплавов |
|||
|
до определенных температур, |
||||||
|
выдержке |
их |
|
при |
|
этих |
|
|
температурах |
и |
последующем |
||||
Рис. 8. Микроструктура мартенсита |
охлаждением |
с |
различной |
||||
скоростью. |
Различают |
три |
|||||
|
|||||||
|
основных |
вида |
термической |
109
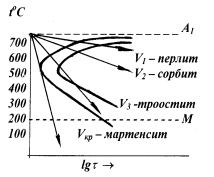
обработки стали: закалку, отпуск и отжиг.
При медленном охлаждении стали происходит полный распад аустенита с образованием равновесной структуры, представленной ферритом и цементитом. В процессе закалки получают сталь неравновесной структуры повышенной твердости. Под закалкой понимают термическую обработку, состо-ящую в нагреве стали до температуры выше критической точки Ас1 (линия РSK, рис.7) или Ас3 (линия GS на диаграмме состояния железо – цементит), выдержке и последующем быстром охлаждении. Различают два вида превращений в стали при закалке: закалка на мартенсит и закалка на ферритноцементитную смесь. При скорости охлаждения стали ≥ Vкр происходит бездиффузионное превращение аустенита в мартенсит (рис.9). При этом имеет место перестройка кубической гранецентрированной решетки аустенита в тетрагональную объемно-центрированную решетку мартенсита. Мартенсит представляет собой пересыщенный твердый раствор внедрения углерода в -железе. Таким образом, главным фактором закаливаемости является содержание углерода.
В практике термической обработки при регулировании скорости охлаждения аустенита с целью получения требуемой структуры стали пользуются С-образными кривыми, получаемыми для каждой марки стали опытным путем (рис. 10). По оси ординат показана температура переохлаждения аустенита, а по оси абсцисс – логарифм времени. Линия А1 - нижняя критическая точка, соответствующая 727 °С. Первая С-образная кривая лежащая ближе к оси ординат показывает начало, а вторая С-образная кривая соответственно окончание превращения аустенита в ферритно-цементитную смесь.
|
Мартенсит |
отличается |
|||
|
высокой |
|
твердостью |
||
|
(600…650 НВ) и хрупкостью. |
||||
|
Критическая |
|
|
скорость |
|
|
охлаждения |
при |
закалке это |
||
|
минимальная |
|
|
скорость |
|
|
охлаждения |
для |
|
получения |
|
|
мартенситной |
структуры. |
|||
|
Регулируя |
|
|
скорость |
|
|
охлаждения |
Vкр, |
ниже |
||
|
критической |
можно |
|||
|
получать |
|
|
структуры |
|
Рис. 9. Различные скорости |
пониженной твердости в виде |
||||
смесей связанных между собой |
|||||
охлаждения, нанесенные на |
|||||
диаграмму изотермического |
частиц феррита и |
цементита: |
превращения аустенита
110