
Balovnev_N_P_Raschet_rezbovyh_soedinenij_i
.pdf11
где Ψ h - отношение |
рабочей высоты |
профиля к |
шагу |
резьбы, |
равное 0,5 |
для |
|||||
трапецеидальной и прямоугольной резьбы, 0,75 |
для |
упорной, 0,54 для треугольной; |
|||||||||
Ψ H = H / d2 - |
коэффициент, равный |
1,2...2,5 (большие |
значения для |
резьб |
меньших |
||||||
диаметров); H - высота гайки. |
[p]= 10...12 (8...10) |
|
|
|
|
||||||
Допускаемое давление в резьбе |
МПа для пары закаленная |
||||||||||
(незакаленная) |
сталь по |
(незакаленной) |
стали, |
бронзе; |
[p] = 4...6 |
МПа |
для |
пары |
незакаленная сталь по чугуну. Для передач приборов допускаемое давление уменьшают в 2 - 3 раза по сравнению с передачами общего назначения.
|
|
|
|
|
Механические характеристики сталей |
|
|
|
Таблица 7 |
|||||||
|
|
|
|
|
|
|
|
|
|
|
|
|
|
|
||
|
Сталь |
|
σ В |
|
σ Т |
|
σ − 1 |
|
Сталь |
σ В |
σ Т |
|
σ − 1 |
|
||
|
|
|
|
|
МПа |
|
|
|
|
|
|
МПа |
|
|
|
|
|
Ст. 3 |
400 |
|
230 |
170 |
|
45 |
610 |
|
360 |
|
260 |
|
|||
|
Ст. 5 |
520 |
|
280 |
220 |
|
50 |
640 |
|
380 |
|
280 |
|
|||
|
А 12 |
450 |
|
300 |
230 |
|
65Г |
750 |
|
440 |
|
350 |
|
|||
|
20 |
400 |
|
240 |
170 |
|
40Х |
800 |
|
650 |
|
360 |
|
|||
|
35 |
540 |
|
320 |
230 |
|
40ХГ |
1600 |
|
1400 |
|
630 |
|
|||
|
|
|
|
Механические характеристики чугунов и бронз |
|
Таблица 8 |
||||||||||
|
|
|
|
|
|
|
|
|
|
|
|
|
|
|
||
|
Чугуны |
|
σ В |
|
Е |
|
|
Бронзы |
σ В |
|
σ Т |
|
|
Е |
|
|
|
|
|
|
МПа |
|
|
|
|
|
|
МПа |
|
|
|
|
|
|
СЧ 15 |
|
150 |
|
0,86 10 5 |
|
|
Бр010Ф1 |
260 |
|
200 |
|
1,03 10 5 |
|
||
|
СЧ 20 |
|
200 |
|
0,9 10 5 |
|
Бр06Ц6С3 |
180 |
|
90 |
|
0,93 10 5 |
|
|||
|
СЧ 30 |
|
300 |
|
1,12 10 5 |
|
БрОЦС 4-4-17 |
150 |
|
90 |
|
|
0,7 10 5 |
|
Резьбу выбирают по соответствующему стандарту при условии, что d1 ≤ d1по ГОСТ и d2 ≤ d2 по ГОСТ, с указанием основных ее параметров - диаметров наружного d ,
внутреннего d1 и среднего d2 , а также шага резьбы P . |
|
|
|
|
|
|||||||
|
Высота гайки с округлением до нормального ряда линейных размеров по табл. 9 |
|||||||||||
|
|
|
|
|
H = Ψ H d2 , мм. |
|
|
|
(12) |
|||
|
|
|
|
Ряд нормальных линейных размеров |
|
|
Таблица 9 |
|||||
|
|
|
|
|
|
|
|
|
|
|
||
6,0 |
|
9,0 |
13 |
20 |
30 |
45 |
67 |
100 |
150 |
220 |
340 |
|
6,3 |
|
9,5 |
14 |
21 |
32 |
48 |
71 |
105 |
160 |
240 |
360 |
|
6,7 |
|
10 |
15 |
22 |
34/35 |
50 |
75 |
110 |
170 |
250 |
380 |
|
7,1 |
|
10,5 |
16 |
24 |
36 |
53 |
80 |
120 |
180 |
260 |
400 |
|
7,5 |
|
11 |
17 |
25 |
38 |
56 |
85 |
125 |
190 |
280 |
420 |
|
8,0 |
|
11,5 |
18 |
26 |
40 |
60 |
90 |
130 |
200 |
300 |
450 |
|
8,5 |
|
12 |
19 |
28 |
42 |
63 |
95 |
140 |
210 |
320 |
480 |
|
|
Винты, нагруженные сжимающей осевой силой |
при lmax / d ≥ |
7 , проверяют на |
устойчивость ( lmax - наибольшая рабочая длина винта). При этом предварительно выясняют
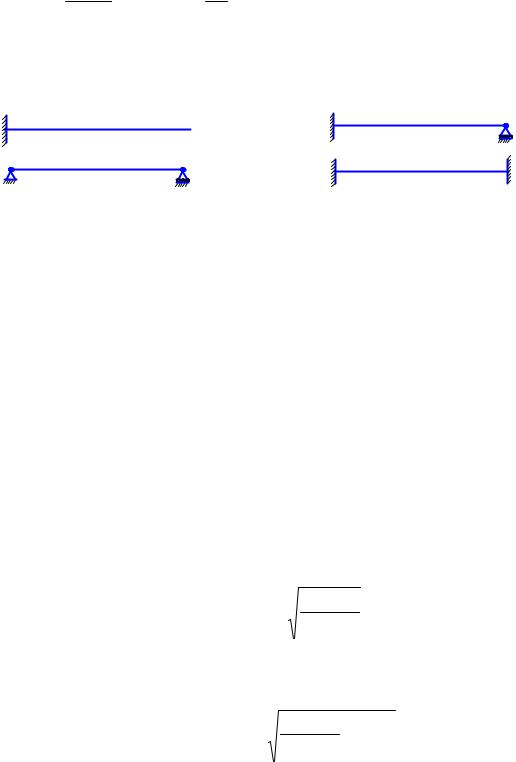
12
условия закрепления винта в опорах и его приведенную длину lпp = µ lmax , где µ -
коэффициент, зависящий от условий закрепления винта, выбираемый по рис. 2.
Если приведенная длина lпр ≥ 25 d1 , то проверку винта на устойчивость проводят с
применением формулы Эйлера по условию |
π 2 E |
|
|
|
|
||||
|
|
FР |
≤ |
J |
. |
|
(13) |
||
|
|
s у lnp2 |
|
||||||
|
|
|
|
|
|
|
|
||
Здесь J = π d14 ( 0,4 + |
0,6 |
d ) |
- приведенный момент инерции сечения винта, мм4 ; |
||||||
64 |
|
d1 |
|
|
|
|
|
|
|
E - модуль упругости материала винта, МПа; s y = |
2,5 - коэффициент запаса устойчивости. |
||||||||
|
|
Схемы закрепления винта |
|
|
|||||
|
|
µ |
= |
2 |
|
|
µ |
= |
0,7 |
|
|
µ |
= |
1 |
|
|
µ |
= |
0,5 |
|
|
|
|
|
Рис. 2 |
|
|
|
|
Примечания:1. Опора с одним подшипником рассматривается как шарнирная опора; с двумя
-как жесткая заделка. 2. Гайка с опорой рассматривается как жесткая заделка.
3.Гайка или опора, перемещаемая в направляющих поддерживающая винт, рассматривается как шарнирная опора.
При lпp < 25 d1 проверку устойчивости винта проводят по условию
σ = |
4 FР |
≤ [σ |
] |
ϑ , |
(14) |
|
|||||
|
π d12 |
+ 1 |
|
|
где ϑ - коэффициент понижения допускаемого напряжения в зависимости от гибкости
стержня lпр / i ; i ≈ |
d1 / 4 -радиус инерции сечения винта. |
|
|
|
|||||||
lnp / i |
10 |
20 |
30 |
40 |
50 |
|
60 |
70 |
80 |
90 |
100 |
ϑ |
0,98 |
0,95 |
0,91 |
0,89 |
0,86 |
0,82 |
0,76 |
0,70 |
0,62 |
0,51 |
|
В случае, если условия (13) или (14) не выполняются, необходимо увеличить диаметр |
|||||||||||
резьбы с повторной проверкой устойчивости винта. |
|
|
|
|
|
|
|||||
Размеры торцовой поверхности винта, если они не заданы, определяют из расчета |
|||||||||||
на износ. |
|
|
|
|
|
|
|
|
|
|
|
Наружный диаметр при сплошном торце, мм |
|
|
|
|
|
|
|||||
|
|
|
|
D = |
4 FР |
, |
|
|
|
(15) |
|
|
|
|
|
π [p] |
|
|
|
|
|||
|
|
|
|
|
T |
|
|
|
|
|
где [p]T - допускаемое давление на торце при соответствующем материале подпятника (табл. 10), МПа.
При кольцевом торце, мм |
|
4 FР |
|
|
|
D = |
|
+ |
2 |
(16) |
|
π |
[p]T |
do . |
|||
|
|
|
|

13
где |
d0 - внутренний |
диаметр |
опорной поверхности торца |
(обычно принимают |
||||
d0 = |
0,6 d ). |
|
|
|
|
|
|
|
|
|
Допускаемые давления материала подпятника |
Таблица 10 |
|||||
|
|
|
|
|
|
|
||
Материал подпятника |
|
[p]T |
|
Материал подпятника |
|
[p]T |
|
|
|
|
|
МПа |
|
|
|
МПа |
|
|
АЧС-1 |
|
9 |
|
Бр010Ф1 |
|
15 |
|
|
АЧС-4 |
|
15 |
|
БрС30 |
|
25 |
|
|
АЧС-5 |
|
30 |
|
ЦАМ10-5 |
|
20 |
|
|
АЧВ-1 |
|
12 |
|
АН-2,5 |
|
25 |
|
Незакаленная сталь |
|
5...6 |
|
Полиамид АК-7 |
|
20 |
|
|
Закаленная сталь |
|
12...15 |
|
Фенопласты |
|
42 |
|
При заданных размерах торцевой поверхности ее проверяют на износ
pT |
= |
|
4 FР |
|
≤ |
[p]T . |
(17) |
|
π ( D2 |
− |
|
||||||
|
|
do2 ) |
|
|
||||
Если условие (17) не выполняется, |
то следует увеличить размеры опорного торца, |
изменить материал подпятника (табл. 10) или применить упорный подшипник качения в паре с радиальным подшипником (качения или скольжения).
2.2. Проверочный расчет тела винта на прочность и сопротивление усталости
Этот расчет производят для опасного сечения винта, выбираемого при сопоставлении эпюр сил F и крутящих моментовT , действующих на винт. Если при этом оказывается, что максимальные значения F и T приходятся на разные сечения, то проверку производят ( при прочих равных условиях) по сечению с Fmax .
Момент в резьбе TР и на торце TT находят по формулам (5) и (6). При этом
коэффициент трения фрикционных пар берут по табл. 11.
При действии в опасном сечении осевой силы и крутящего момента условие прочности винта
|
|
|
σ |
|
= |
|
σ |
2 |
|
|
+ 3 |
τ 2 |
≤ [σ ] . |
(18) |
|
||
|
|
|
|
|
|
|
|
р( сж ) |
|
кp |
|
|
|
|
|||
Здесь σ р( сж ) = |
4 |
FР |
и τ кp |
= |
|
|
|
T |
|
- действующие в опасном сечении напряжения |
|||||||
π d12 |
|
0,2 d13 |
|||||||||||||||
|
|
|
|
|
|
|
|
МПа; T - |
|
|
|||||||
растяжения (сжатия) и кручения |
|
соответственно, |
крутящий момент в |
||||||||||||||
рассматриваемом сечении, Н.мм. |
|
|
|
|
|
|
|
|
|
|
|
|
|||||
|
|
|
Коэффициент трения фрикционных пар |
Таблица 11 |
|||||||||||||
|
|
|
|
|
|
|
|
|
|
|
|
|
|
|
|
||
Фрикционная пара |
|
|
|
|
|
|
|
|
|
Коэффициент трения |
f |
|
|||||
|
|
|
|
|
|
|
|
|
|
без смазки |
|
|
|
со смазкой |
|
||
Сталь - сталь |
|
|
|
|
|
|
|
|
|
|
0,15 |
|
|
|
0,08...0,1 |
|
|
Сталь - мягкая сталь |
|
|
|
|
|
|
|
|
|
0,2 |
|
|
|
0,1...0,2 |
|
||
Сталь - чугун |
|
|
|
|
|
|
|
|
|
|
0,18 |
|
|
|
0,1...0,15 |
|
|
Сталь - бронза |
|
|
|
|
|
|
|
|
|
|
0,1 |
|
|
|
0,07...0,1 |
|
|
Чугун - бронза |
|
|
|
|
|
|
|
|
|
0,15...0,2 |
|
|
|
0,07...0,15 |
|
||
Бронза - бронза |
|
|
|
|
|
|
|
|
|
|
0,2 |
|
|
|
0,07...0,1 |
|
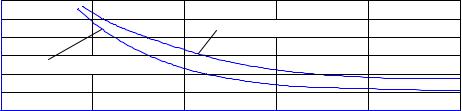
14
Условие прочности при действии только крутящего момента |
|
|
τ кp ≤ |
[τ ]кp , |
(19) |
где [τ ]кp = ( 0,5...0,6 ) [σ ] - допускаемое |
напряжение кручения, МПа; |
[σ ] = [σ ]+ 1 - |
допускаемое напряжение при расчете на статическую прочность (стр. 10), МПа.
Расчет винта на сопротивление усталости производят при механическом приводе.
При расчете на сопротивление усталости при симметричном цикле изменения напряжений, МПа
|
[σ |
]= [σ ] |
|
= σ |
− 1 K K KV Kd . |
|
|
|
|
(20) |
||||||
|
|
− 1 |
|
|
Kσ s− 1 |
|
|
|
|
|
|
|
|
|
||
|
|
|
|
|
|
|
|
|
|
Kσ |
|
|
|
|||
Здесь σ − 1 - предел выносливости материала винта, |
МПа (табл. 7); |
- |
эффективный |
|||||||||||||
коэффициент концентрации напряжений в резьбе (табл. 12); |
|
K K - |
коэффициент |
|||||||||||||
конструктивной формы: K K = 1 - |
при |
работе гайки |
на сжатие, |
K K = |
1,2...1,3 - на |
|||||||||||
растяжение; K K = 1,2 |
- для гаек с спиральными вставками или уменьшенным модулем |
|||||||||||||||
упругости (бронза, чугун); |
KV - коэффициент поверхностного |
слоя: |
KV = 1 - для |
|||||||||||||
накатанной резьбы; KV = |
0,85...0,95 |
|
- для нарезанной |
резьбы; |
Kd - |
коэффициент, |
||||||||||
учитывающий влияние абсолютных размеров (рис. 3); |
s− |
1 = |
2...2,5 |
- коэффициент запаса |
||||||||||||
по сопротивлению усталости. |
|
|
|
|
|
|
|
|
|
|
|
|
|
|
||
Эффективный коэффициент концентрации напряжений резьбе Kσ |
Таблица 12 |
|||||||||||||||
|
|
|
|
|
|
|
|
|
|
|
|
|
|
|
||
Резьба |
|
Углеродистая сталь |
|
|
|
Легированная сталь |
|
|||||||||
В соединении |
|
В свободной |
|
В соединении |
|
В свободной |
|
|||||||||
|
|
|
|
|
|
части резьбы |
|
|
|
|
|
|
части резьбы |
|
||
Метрическая и упорная |
|
3,0 |
|
|
|
1,9 |
|
|
|
3,8 |
|
|
|
|
2,3 |
|
Трапецеидальная |
|
3,5 |
|
|
|
2,1 |
|
|
|
4,4 |
|
|
|
|
3,3 |
|
|
Коэффициент, учитывающий влияние абсолютных размеров Kd |
||||
kd |
|
|
|
|
|
0,8 |
|
|
|
|
|
0,7 |
|
|
углеродистые стали |
|
|
0,6 |
|
|
|
|
|
0,5 |
легированные стали |
|
|
|
|
0,4 |
|
|
|
|
|
0,3 |
|
|
|
|
|
0 |
10 |
20 |
30 |
40 |
d, ìì |
|
|
|
Рис. 3 |
|
|
При отнулевом цикле изменения напряжений |
|
|
]− 1 |
|
|
||||
[σ ]= [σ |
] |
= |
2 [σ |
]+ 1 |
[σ |
. |
(21) |
||
[σ ] |
|
[σ |
] |
||||||
|
0 |
|
+ 1 |
+ |
|
|
|||
|
|
|
|
|
|
− 1 |
|
2.3. Коэффициент полезного действия винтового механизма
КПД винтовой пары при завинчивании

15
|
|
|
|
|
|
|
|
η p = |
|
|
|
tgψ |
|
|
|
. |
|
(22) |
||||
|
|
|
|
|
|
|
|
|
tg(ψ |
+ |
|
ϕ ′ ) |
|
|||||||||
|
КПД механизма |
|
|
|
|
|
|
|||||||||||||||
|
|
|
|
|
|
T0 |
|
|
|
|
|
|
||||||||||
|
|
|
|
|
|
|
|
|
|
|
η = |
|
, |
|
|
|
|
(23) |
||||
|
|
|
|
|
|
d2 |
|
|
|
|
T |
|
|
|
|
|
||||||
где T |
|
= F |
p |
|
tgψ - момент в резьбе, расходуемый на совершение полезной работы, |
|||||||||||||||||
|
|
|
||||||||||||||||||||
0 |
|
|
2 |
|
|
|
|
|
|
|
|
|
|
|
|
|
|
|
||||
Н.мм; |
T - суммарный момент на винте, Н.мм. |
|
|
|
|
|
|
|
|
|||||||||||||
|
|
|
|
|
|
|
|
2.4. Определение размеров воротка |
|
|||||||||||||
|
Длина воротка (или радиус маховичка), мм |
|
|
|
||||||||||||||||||
|
|
|
|
|
|
|
|
|
lB |
= |
|
T |
|
, |
|
|
(24) |
|||||
|
|
|
|
|
|
|
|
|
|
|
|
|
|
|
||||||||
|
|
|
|
|
|
|
|
|
|
|
|
|
Fpaδ |
|
|
|
||||||
где Fpaδ = |
|
150...300 Н - усилие рабочего. |
|
|
|
|
|
|
|
|
момент M , |
|||||||||||
|
Диаметр воротка определяют из расчета на изгиб, имея ввиду, что |
|||||||||||||||||||||
изгибающий вороток, равен крутящему моменту T . |
|
|
|
|||||||||||||||||||
|
|
|
|
|
|
|
|
d B |
= |
3 |
|
|
M |
|
|
|
, мм |
(25) |
||||
|
|
|
|
|
|
|
|
0,1 |
[σ |
]u |
||||||||||||
|
|
|
|
|
σ T |
|
|
|
|
|
|
|
|
|||||||||
Здесь [σ |
] |
= |
- допускаемые напряжения изгиба материала воротка, МПа; s = 2...3 - |
|||||||||||||||||||
|
||||||||||||||||||||||
|
|
u |
|
|
|
s |
|
|
|
|
|
|
|
|
|
|
|
|
|
|||
|
|
|
|
|
|
|
|
|
|
|
|
|
|
|
|
|
|
|
||||
коэффициент запаса прочности. |
|
|
|
|
|
|
|
|
|
|
|
|
|
|||||||||
|
Материал воротка и его механические характеристики берут по табл. 7. |
|
||||||||||||||||||||
|
|
|
|
|
|
|
|
3. РАСЧЕТ КРЕПЕЖНЫХ РЕЗЬБ |
|
|||||||||||||
|
Витки крепежных резьб рассчитывают на срез и смятие. |
|
||||||||||||||||||||
|
Условие прочности витков резьбы на срез |
|
|
|
||||||||||||||||||
|
|
|
|
|
|
|
|
τ cp = |
|
|
|
|
|
FР |
|
|
|
|
≤ [τ ]cp , |
(26) |
||
|
|
|
|
|
|
|
|
π d( 1 ) |
|
|
|
|
|
|
||||||||
|
|
|
|
|
|
|
|
|
ξ H km |
|
где ξ - коэффициент полноты резьбы, равный 0,87 для треугольной резьбы, 0,75 для упорной, 0,65 для трапецеидальной и 0,5 для прямоугольной; km = 0,55...0,75 - коэффициент, учитывающий распределения нагрузки по виткам резьбы (большие значения для резьб с крупным шагом, когда материал болта прочнее материала гайки); -
внутренний диаметр резьбы d1 , если материалы болта и гайки одинаковы, или наружный
диаметр резьбы d , если материал гайки менее прочен (в последнем случае следует проверить на срез витки резьбы болта и гайки); [τ ]cp - допускаемое напряжение среза.
Обычно для стальных деталей принимают [τ ]cp = ( 0,2...0,3 ) σ T . Для деталей из хрупких материалов - [τ ]cp = ( 0,1...0,15 ) σ B .
В проектном расчете определяют длину свинчивания в мм

16
|
lсв = |
|
|
FР |
|
. |
(27) |
|
||
|
|
|
|
|
|
|||||
|
|
|
π d( 1 ) ξ km [τ ]cp |
|
|
|
||||
Условие прочности на смятие |
4 |
FР P |
|
|
|
|
|
|||
|
σ см = |
|
|
≤ [σ ]см . |
(28) |
|
||||
|
|
|
|
|
|
|||||
|
π ( d 2 − d12 ) km H |
материалов [σ ]см |
|
|
|
|||||
Допускаемое напряжение смятия для пластичных |
принимают |
|||||||||
равным допускаемому |
напряжению |
[σ |
]+ 1 (стр. 10), |
а при частом завинчивании и |
||||||
отвинчивании: σ см = |
( 0,5...0,6 ) [σ |
]+ 1. |
Коэффициент |
запаса прочности |
s |
обычно |
|
|||
|
выбирают в пределах 1,5...2,5. Меньшие значения принимают при контролируемой затяжке и |
||||||
d >16 мм. Для хрупких материалов [σ ]см = 0,25 σ |
В . |
|
|
|
||
Необходимую длину свинчивания из условия отсутствия смятия поверхности витков в |
||||||
мм находят по формуле |
|
|
|
|
|
|
lсв = |
4 FР P |
|
. |
(29) |
||
π ( d 2 − d 2 ) k |
m |
[σ ] |
||||
1 |
|
см |
|
|
||
Если хотябы одна из свинчиваемых деталей является стандартной (болт, винт, |
||||||
шпилька или гайка), то минимальное значение [σ ]T |
материала этой детали находят по |
|||||
классу их прочности (см. раздел 1.5). |
|
|
|
|
|
4. РАСЧЕТ НЕЗАТЯНУТЫХ И ЗАТЯНУТЫХ БОЛТОВ
Параметры резьбы стандартных крепежных изделий подобраны таким образом, что наиболее слабым элементом является тело болта (винта, шпильки).
Незатянутые болты работают только на растяжение или сжатие.
Расчетный внутренний диаметр резьбы незатянутого болта находят по формуле
d1 |
= |
|
4 FР |
, мм |
|
(30) |
π |
[σ ]P |
|
||||
|
|
|
|
|
||
где FP - внешняя сила, растягивающая или сжимающая болт, |
Н; [σ |
]P -допускаемые |
||||
напряжения, МПа (для болтов из углеродистых сталей [σ |
]р = |
(0,5...0,6) σ T , |
||||
легированных - [σ ]р = (0,4...0,55) σ |
T ). |
|
|
|
|
|
Затянутые болты, помимо растяжения или сжатия, работают на кручение, поэтому
расчетный внутренний диаметр их резьбы находят по формуле (10). При неконтролируемой |
|||||||
затяжке допускаемые напряжения [σ ]р |
для затянутых болтов находят по таблице 13 в |
||||||
зависимости от диаметра резьбы и предела текучести материала болта σ |
T . Для стандартных |
||||||
болтов σ T определяют согласно разделу 1.5. |
|
|
|
|
|||
Допускаемые напряжения в долях от предела текучести ([σ ]р / σ |
T ) |
||||||
|
|
|
|
|
|
Таблица 13 |
|
Сталь |
Постоянная нагрузка |
Переменная нагрузка |
|
||||
|
М6...М16 |
|
М16...М30 |
М6...М16 |
|
М16...М30 |
|
Углеродистая |
0,20...0,25 |
|
0,25...0,40 |
0,08...0,12 |
|
0,12 |
|
Легированная |
0,15...0,20 |
|
0,20...0,30 |
0,10...0,15 |
|
0,15 |
|
17
При контролируемой затяжке для болтов из углеродистых сталей [σ ]р = 0,6 σ T ,
легированных - [σ ]р = 0,5 σ T .
Затянутые и незатянутые болты подбирают по условию d1 ≤ d1 по ГОСТ с
указанием d , d1, d2 и Р (табл. 1).
В ответственных случаях проводят проверку в соответствии с разделом 2.2., принимая приведенный коэффициент трения резьбы f ′ и коэффициент трения фрикционной пары торца f по таблице 5.
При контролируемой затяжке момент «на ключе» находят по формуле (9).
5. РАСЧЕТ ЗАТЯНУТЫХ БОЛТОВ, НАГРУЖЕННЫХ ВНЕШНЕЙ ОСЕВОЙ СИЛОЙ
Такими болтами выполняют соединения, для которых необходимо кроме прочности болтов обеспечить нераскрытие стыка, во избежание нарушения взаимного расположения соединяемых деталей, контактной коррозии и пониженной контактной жесткости, или
герметичность соединения.
Нераскрытие стыка обеспечивается, если в любой момент времени в любой точке стыка напряжение больше нуля (под стыком понимают площадь контакта соединяемых деталей).
Герметичность обеспечивается, если напряжение на стыке больше рабочего давления среды p р .
Сила затяжки болта, обеспечивающая нераскрытие стыка, Н
|
FЗ = kЗ FB (1− χ) , |
(31) |
|
где FB - |
внешняя сила, действующая на болт, |
Н; kЗ - |
коэффициент запаса начальной |
затяжки: |
при статической нагрузке kЗ = |
1,5...2,0 ; |
при переменной нагрузке |
kЗ = 2,5...4 ; χ - коэффициент внешней нагрузки.
Вприближенных расчетах для соединений из стальных и чугунных деталей принимают χ= 0,2...0,3 ; для соединений с упругими прокладками (паронит, резина и т.д.)
χ= 0,4...0,5 .
При уточненных расчетах
|
|
|
|
χ= |
|
|
λд |
|
. |
|
|
|
|
(32) |
|||
|
|
|
|
|
λ + |
λ |
|
|
|
|
|||||||
|
|
4 |
lб |
|
|
|
|
б |
|
д |
|
|
|
|
|
||
Здесь λб |
= |
- податливость болта, |
мм/Н; |
lб - |
длина растягиваемого участка |
||||||||||||
Eб π d 2 |
|||||||||||||||||
|
|
|
|
|
|
|
|
|
|
|
|
|
|
|
|||
болта, мм; Eб - |
модуль упругости материала болта, |
МПа; |
λд - суммарная податливость |
||||||||||||||
сжимаемых деталей, мм/Н. |
|
|
|
|
|
|
|
|
|
|
|
||||||
Суммарную податливость деталей находят по формуле |
|
||||||||||||||||
|
|
|
|
|
λд = |
n |
λдi |
|
|
|
|
|
|||||
|
|
|
|
|
∑ |
, |
|
|
|
(33) |
|||||||
|
|
|
|
|
|
|
|
i = |
1 |
|
|
|
|
|
|
||
где λдi |
- податливость i-й детали; n - число сжимаемых деталей. |
||||||||||||||||
Податливость сжимаемой детали, мм/Н |
4 |
li |
|
|
|
|
|
||||||||||
|
|
|
|
λдi = |
|
|
|
|
|
|
|
, |
(34) |
||||
|
|
|
|
E |
дi |
π |
(d 2 |
− |
d 2 ) |
||||||||
|
|
|
|
|
|
|
|||||||||||
|
|
|
|
|
|
|
|
ср |
|
0 |
|
|
|
18
Здесь Eдi - модуль упругости i - й детали, МПа ( для стали E = 2,1 105 МПа, чугуна и бронзы по табл. 8, других материалов по табл. 14); dср - средний внешний диаметр конуса
давления, мм; d0 - диаметр отверстия под болт, мм; li - толщина i-й детали, мм. Средний внешний диаметр конуса давления в мм находят по формуле
|
S - размер «под ключ», |
dср = 2 S + li tgγ |
, |
|
S = 1,5 d ); γ |
(35) |
||||
где |
мм (ориентировочно можно принять |
- угол |
||||||||
конуса давления (для стали γ = |
22...270 ). |
|
|
|
|
|
|
|||
|
Уплотняющая сила, обеспечивающая герметичность , Н |
|
|
|||||||
|
A = k0 A0 |
|
Fуп = |
q0 A , |
|
|
|
|
(36) |
|
где |
- площадь |
поверхности |
прокладки |
с учетом |
отверстий под |
болты, |
||||
мм 2 ; k0 = |
0,7...0,8 - коэффициент, учитывающий уменьшение площади прокладки за счет |
|||||||||
отверстий |
под болты; q0 = k уп p p ≥ q0 min - давление на контактных поверхностях |
|||||||||
прокладки, МПа; |
k уп - коэффициент запаса уплотнения (табл. 14); |
q0 min - минимальное |
||||||||
давление уплотнения (табл. 14), МПа. |
|
|
|
|
|
|
||||
|
Сила затяжки болта, обеспечивающая герметичность, Н |
|
|
|||||||
|
|
|
|
FЗ = FB (1− χ) + |
Fуп |
, |
|
(37) |
||
|
|
|
|
z |
|
|
||||
|
|
|
|
|
|
|
|
|
|
где z - количество болтов.
Число болтов для обеспечения равномерной затяжки стыка выбирают
кратным четырем. Расстояние между осями болтов (шаг болтов t ) при малых давлениях
( pP ≤ 1 МПа) t = ( 5...7 ) d ; при больших давлениях ( pP ≥ |
3 МПа) t = |
|
( 2,5...4 ) d . |
||||
Коэффициенты запаса уплотнения k уп , минимальные давления уплотнения q0 min и |
|||||||
модули упругости Е |
|
|
|
Таблица 14 |
|||
|
|
|
|
|
|
||
Материал прокладки |
|
k уп |
|
q0 min |
|
Е |
|
|
|
|
|
|
|
МПа |
|
Резина |
|
1,2 |
|
2,5 |
|
400 |
|
Паронит или пересованный асбест |
|
1,6 |
|
10 |
|
3000 |
|
Фторопласт - 4 |
|
1,4 |
|
4,0 |
|
2000 |
|
Фибра |
|
1,4 |
|
40 |
|
7000 |
|
Асбест, армированный проволочной сеткой |
|
1,4 |
|
10 |
|
3000 |
|
Мягкий алюминий |
|
2,0 |
|
50 |
|
70000 |
|
Мягкая медь |
|
2,4 |
|
70 |
|
110000 |
|
Мягкая сталь |
|
2,7 |
|
80 |
|
210000 |
|
Примечание. При уплотнении воздуха или пара значения k уп и q0 min увеличивают в 1,8 |
|
||||||
раза; а газов с высокой проникающей способностью (водород, гелий и т.д.) - в 2,5 раза. |
|
||||||
Расчетная сила в болте, |
|
|
|
|
|
|
|
FP = FЗ C + |
χ FВ , |
|
|
(38) |
где C = 1,2...1,4 - коэффициент, учитывающий напряжения кручения.

19
Расчетный внутренний диаметр болта, мм
|
|
|
|
|
|
d1 = |
4 FР |
. |
|
(39) |
|||
|
|
|
|
|
|
π [σ ] |
|
||||||
|
|
|
|
|
|
|
|
|
|
р |
|
|
|
Допускаемые напряжения [σ ]р находят в соответствии с разделом 4. |
|
|
|||||||||||
Момент на ключе для контроля затяжки находят по формуле (9). |
|
|
|||||||||||
При |
переменных нагрузках |
|
болты |
проверяют на сопротивление |
усталости |
по |
|||||||
амплитудному напряжению, МПа |
|
|
|
|
χ FB |
|
|
|
|||||
|
|
|
|
|
|
|
σ |
а = |
, |
|
(40) |
||
|
|
d12 |
|
|
|
|
|
|
|
2 A |
|
|
|
где A = |
π |
|
|
|
|
|
|
|
|
2 |
|
|
|
|
|
- площадь поперечного сечения болта, мм . |
|
|
|||||||||
|
4 |
|
|
||||||||||
|
|
|
|
|
|
|
|
|
|
|
|
|
|
Предельная амплитуда цикла напряжений для резьбовых соединений типа болт - |
|||||||||||||
гайка, МПа |
|
|
|
σ |
|
|
|
|
|
|
|
||
|
|
|
|
σ |
п = |
− 1 р |
|
K K KV Kd . |
(41) |
||||
|
|
|
|
|
Kσ |
||||||||
Здесь σ − 1р = |
( 0,8...0,9 ) σ − |
|
|
|
|
|
|
||||||
1 - предел выносливости материала болта при растяжении - |
|||||||||||||
сжатии, МПа; σ |
− 1 - предел выносливости по табл. 7, МПа; коэффициенты Kσ , K K , |
KV |
|||||||||||
и Kd те же, что и в формуле (20). |
|
|
|
|
|
|
|
|
|||||
Запас по сопротивлению усталости резьбовых соединений |
|
|
|||||||||||
|
|
|
|
|
sа = |
|
σ |
п = |
2,5...4 . |
(42) |
|||
|
|
|
|
|
|
|
σ |
а |
|
|
|
|
|
Высокие значения |
sа объясняются возможными погрешностями при определении |
||||||||||||
коэффициентов |
основной |
нагрузки |
|
χ и |
рассеянием величины σ п в |
зависимости от |
технологических факторов.
6. РАСЧЕТ ГРУППОВОГО БОЛТОВОГО СОЕДИНЕНИЯ, НАГРУЖЕННОГО В ПЛОСКОСТИ СТЫКА
В отверстия соединяемых деталей болты устанавливают: с диаметральным зазором (черные болты) и без зазора с небольшим натягом (чистые болты). В общем случае такие
соединения могут быть нагружены сдвигающими силами Fi и моментами Ti . Для расчета все силы и моменты приводят к центру масс стыка методом плоско - параллельного переноса и находят их равнодействующие FB и T . Стыком считают плоскую фигуру,
ограниченную центрами отверстий под болты.
При расчете и конструировании таких соединений следует обращать внимание на наличие или возможность применения центрирующих буртов, штифтов или упоров, препятствующих сдвигу деталей, а, следовательно, разгружающих болты.
6.1. Соединения болтами, установленными с зазором
Сдвигу деталей препятствуют силы трения на стыках деталей, создаваемые силами затяжки болтов. При этом условно принимают, что силы трения сосредоточены под болтами. Сила затяжки болтов - одинакова.
Необходимая сила затяжки болта, обеспечивающая несдвигаемость детали, Н
|
|
|
|
20 |
|
|
|
|
|
|
|
|
|
|
|
|
|
|
|
|
|
|
|
|
|
|
|
|
FB |
|
|
|
|
|
|
|
|
|
FЗ = |
k |
|
+ |
1000 T |
, |
(43) |
||||||
|
|
|
|
|
|
|
|
|
||||
f m |
z |
|
n r |
|
|
|||||||
|
|
|
|
z |
|
|
|
|
||||
|
|
|
|
|
|
∑ |
i |
|
i |
|
|
|
|
|
|
|
|
|
i = |
1 |
|
|
|
|
|
где k = 1,2...2,0 - коэффициент запаса сцепления; m - число стыков деталей; f - коэффициент трения на стыке деталей ( табл. 15); z - общее количество болтов; zi -
количество болтов, расположенных на расстоянии ri от центра масс стыка; T - сдвигающий |
|||||||||||||||
момент, Н м. |
|
|
|
|
|
|
|
|
|
|
|
|
|
|
|
Коэффициент трения |
f на стыке стальных (чугунных) деталей |
|
|||||||||||||
|
|
|
|
|
|
|
|
|
|
|
|
|
|
|
Таблица 15 |
Обработка стыка |
|
|
|
|
f |
|
|
|
|
|
|
Окраска стыка |
|
f |
|
Без обработки |
|
|
|
0,3 |
|
|
|
Алюминиевым порошком |
|
0,15 |
|||||
Пескоструйная |
|
|
|
0,5 |
|
|
|
Антикоррозионная краска |
|
0,1 |
|||||
Газовой горелкой |
|
|
|
0,4 |
|
|
|
Свинцовым суриком |
|
0,06 |
|||||
Резанием |
|
|
|
0,12 |
|
|
|
|
|
|
|
|
|
||
В частном случае при кольцевой форме стыка, Н |
|
|
|||||||||||||
|
|
|
|
|
|
|
|
|
|
|
|
|
|||
F |
З |
= |
|
|
k |
|
F |
B |
+ |
2000 T |
. |
(44) |
|||
|
z |
|
D |
||||||||||||
|
|
|
|
f m |
|
|
|
|
|||||||
|
|
|
|
|
|
|
|
|
|
б |
|
|
Здесь Dб - диаметр окружности осей болтов, мм.
Далее болты рассчитывают как затянутые в соответствии с разделом 4.
6.2. Соединения болтами, установленными без зазора
Отказ такого соединения наступает в результате среза болтов и смятия боковой поверхности болтов или деталей.
Срезающая сила от внешней силы FF , Н
FF = |
FB |
, |
(45) |
|
z |
||||
|
|
|
где z - полное количество болтов.
Срезающая сила от внешнего момента T , Н |
|
||||
F |
= |
1000 T l1 |
, |
(46) |
|
|
|||||
T |
|
n |
l 2 |
|
|
|
|
∑ |
|
||
|
|
i = 1 |
i |
|
где l1 и li - расстояние от центра масс стыка до наиболее нагруженного болта и до каждого из них соответственно, мм (наиболее нагруженным является болт, расположенный ближе
всех к линии действия силы). |
|
|
|
|
|
При кольцевой форме стыка |
|
2000 T |
|
|
|
F |
= |
. |
(47) |
||
|
|||||
T |
|
z Dб |
|
||
|
|
|
Расчетная сила при одновременном действии силы и момента, Н