
умк_кириенко_1
.pdfПроцесс изнашивания режущего инструмента протекает весьма разнообразно в зависимости от условий его работы: свойств обрабатываемого материала, геометрии и материала инструмента, скорости главного движения резания, толщины среза, смазочно-охлаждающей среды. Однако главным фактором, определяющим стойкость инструмента, является скорость главного движения резания. Обычно стойкость режущего инструмента характеризуется периодом стойкости, под которым понимают время резания новым или восстановленным режущим инструментом (лезвием) от начала резания до отказа.
Важнейшим фактором, обусловливающим снижение себестоимости изготовления деталей, является повышение производительности металлорежущего оборудовании, т.е. обеспечение минимального машинного времени (Тк, мин) при обработке деталей.
Совершенствование режущего инструмента достигается как за счет использования новых материалов (твердых сплавов, металло-керамических) и обеспечения оптимальных его форм, так и создания комбинированного инструмента и инструмента для ступенчатой обработки. Режущие инструменты из быстрорежущей стали работают при скоростях резания в 2 – 4 раза больших, чем инструменты из углеродистой стали. При оснащении инструментов пластинками из твердых сплавов скорость резания может быть увеличена еще в 3 – 5 раз. Износостойкость минералокерамического инструмента в 2 – 3 раза больше, чем инструмента из твердых сплавов. При работе инструментом со ступенчатым лезвием удельный расход мощности в 3 раза меньше, а производительность процесса в 2 раза больше, чем при обычном лезвии.
Машины, предназначенные для обработки резанием металлов, называются станками. Развитие всей машиностроительной промышленности в значительной степени зависит от уровня станкостроения.
Металлорежущие станки в зависимости от вида обработки делят на девять групп, а каждую группу на десять типов (подгрупп) в зависимости от назначения станков, их компоновки, степени автоматизации или вида применяемого инструмента. Станки подразделяются на широкоуниверсальные, универсальные (общего назначения), специализированные и специальные.
Станки токарной группы составляют до 40 % всего станочного парка механических цехов машиностроительных заводов. В эту группу входят токарно-винторезные, карусельно-токарные, токарно-револьверные, многорезцовые токарные, лобовые, токарные автоматы и полуавтоматы, свер- лильно-отрезные (при вращающейся заготовке) и специальные токарные.
Основными характеристиками токарных станков являются высота центров над станиной и наибольшее расстояние между центрами, которые соответственно определяют наибольший возможный радиус и наибольшую длину детали, подлежащей обработке на данном станке. Эти станки ис-
131
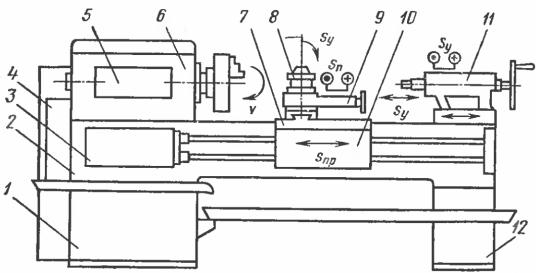
пользуют во всех производствах машиностроения, а также в отделениях сельхозтехники, в учебных и передвижных мастерских.
Токарно-винторезные станки – наиболее универсальные станки рассматриваемой группы. Их типоразмеры изменяются в широком диапазоне от настольных для обработки часовых деталей до тяжелых станков для обработки заготовок массой в несколько десятков тонн.
Токарно-винторезный станок (рис. 7.13) состоит из станины 2, закрепленной на тумбах 1 и 12, коробки подач 3, коробки сменных зубчатых колес 4, панели управления 5, передней бабки 6, продольного суппорта 7, поворотного резцедержателя 8, верхнего суппорта 9, фартука 10, задней бабки 11. В тумбе 1 установлен электродвигатель головного привода станка, в тумбе 2 – бак для смазочно-охлаждающей жидкости и насосная станция. В передней бабке 6 находится коробка скоростей станка и шпинделя, на котором закрепляют зажимные устройства для передачи вращающего момента обрабатываемой заготовке. Панель 5 предназначена для управления механизмами коробки скоростей. Продольный суппорт 7 обеспечивает движение продольной подачи резца, поперечная каретка, на которой смонтирован верхний суппорт 8, – поперечной. В задней бабке устанавливают задний центр или инструмент для обработки отверстий (сверла, зенкеры, развертки). В фартуке 10 установлены механизмы и передачи, которые преобразуют вращательное движение ходового валика или ходового винта в поступательное движение суппортов.
Рис. 7.13. Схема токарно-винторезного станка
Токарные работы включают точение и растачивание цилиндрических, конических и фасонных поверхностей, подрезание торцевых поверхностей; отрезание; нарезание резьб; сверление; зенкерование и развертывание отверстий и др.
132
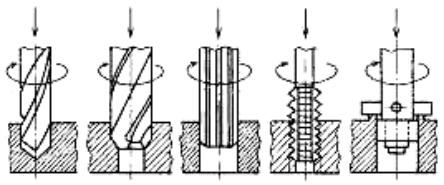
При выполнении отверстий на токарных станках применяют сверла, зенкеры, развертки, закрепляемые (вместо центра) в задней бабке; в этом случае продольная подача осуществляется инструментом, а заготовка, закрепленная в патроне, получает вращательное движение.
Сверление – широко распространенный метод получения отверстий резанием. Главное движение при сверлении – вращательное, а движение подачи – поступательное. Оба движения при сверлении отверстий на сверлильных станках сообщаются инструменту – сверлу.
Процесс сверления характеризуют следующими элементами резания: скоростью резания, подачей, глубиной резания, площадью поперечного сечения среза, машинным временем.
Сверлильные и расточные станки служат для обработки отверстий различными способами. Основными технологическими операциями, связанными с обработкой отверстий, являются сверление, зенкерование, рассверливание, нарезание резьбы и др. Операции обработки отверстий представлены на рис. 7.14.
Рис. 7.14. Схема обработки отверстий: сверление; зенкерование; развертывание; нарезание резьбы метчиком; зенкование
Все эти операции производятся на станках сверлами, зенкерами, развертками, метчиками (на расточных станках применяются резцы). Основным инструментом является спиральное сверло. Однако при сверлении (даже в несколько проходов) отверстие получается небольшой точности, с шероховатой поверхностью. Поэтому предварительно просверленные отверстия обрабатывают зенкером (зенкерование) и разверткой (развертывание). Зенкерование в основном применяют для увеличения диаметра и в отдельных случаях для повышения точности отверстия и уменьшения шероховатости его поверхности.
Зенкеры имеют три-четыре режущие кромки, резание производят боковыми зубьями. При работе зенкерами обеспечивается точность обработки по 4 – 5 квалитетам. Для получения более точных отверстий используют развертки, имеющие значительное число режущих кромок.
133
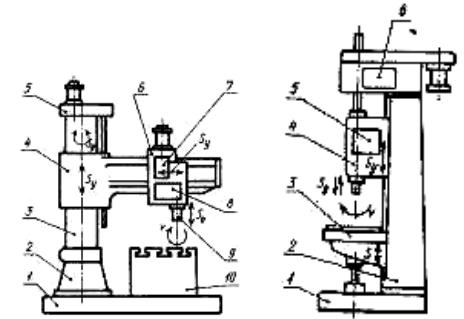
При развертывании снимаются малые слои металла и обеспечивается высокая точность (1 – 3-й квалитеты) и шероховатость обработки отверстия.
Существуют сверлильные станки различных типов: вертикально-
сверлильные, горизонтально-сверлильные, радиально-сверлильные, расточные, координатно-расточные и специальные. Станки сверлильной группы бывают одношпиндельные и многошпиндельные. Вертикальносверлильные станки применяют в инструментальных и ремонтных цехах, а также в условиях мелкосерийного производства при обработке отверстий в небольших деталях.
Одношпиндельный вертикально-сверлильный станок представлен на рис. 7.15, б.
а) |
б) |
Рис. 7.15. Схемы сверлильных станков: а – радиально-сверлильный станок; б – вертикально-сверлильный станок
Вертикально-сверлильный станок (см. рис. 7.15, б) монтируют на фундаментной плите 1. Он состоит из колонны 2, стола 3, кронштейна 4, на котором установлена коробка подач 5, и коробки скоростей 6. На этих станках выполняют такие операции, как сверление, зенкерование, цекование, зенкование, нарезание резьбы и др.
В целях повышения производительности труда применяют многошпиндельные вертикально-сверлильные станки, на которых выполняют одновременно обработку нескольких отверстий.
Для обработки различных отверстий в тяжелых деталях больших размеров применяют радиально-сверлильные станки. Станок (см. рис. 7.15, а)
134
монтируется на фундаментной плите 1. Он состоит из неподвижной колонны 2 с поворотной гильзой 3, траверсы 4, механизма 5, шпиндельной головки 6, в которой расположены коробка скоростей 7 и коробка подач 8, шпинделя 9 и стола 10. Шпиндель с инструментом имеет главное вращательное движение и движение вертикальной подачи. Для обработки заготовку закрепляют на столе 10 или на фундаментной плите 1. В рабочее положение инструмент устанавливают поворотом траверсы вместе с гильзой и перемещением шпиндельной головки по направляющим траверсы.
Для обработки крупногабаритных заготовок с большим числом отверстий применяют сверлильные станки с ЧПУ.
Строгание выполняется при прямолинейном возвратно-поступа- тельном движении резца или заготовки; это движение является главным. После каждого двойного хода заготовка или резец перемещаются в поперечном направлении, совершая тем самым движение поперечной подачи.
Основными элементами резания при строгании являются: скорость резания, подача и глубина резания.
Скорость резания при строгании – отношение пути перемещения режущей кромки резца относительно обрабатываемой поверхности ко времени обработки. При строгании на поперечно-строгальном станке и долблении скорость резания равна средней скорости перемещения резца или долбяка.
Прямолинейное относительное перемещение обрабатываемой детали и инструмента при строгании имеет как преимущества, так и недостатки. Недостатком является то, что при работе на строгальных и долбежных станках резание осуществляется только во время рабочего хода. Во время обратного хода резец не снимает стружку, и это приводит к значительным потерям времени. Однако он успевает несколько остыть, и в связи с этим принудительное его охлаждение при строгальных и долбежных работах не требуется. Вследствие прерывистости работы в начале каждого рабочего хода врезание резца в обрабатываемый материал сопровождается ударом. Удары, а также значительное усилие, необходимое для снятия стружки при строгании, являются причиной того, что строгальные резцы делают обычно большего сечения, чем токарные, с изогнутым стержнем. При встрече с твердыми шлаковыми включениями и при ударах резец отгибается без повреждения обработанной поверхности.
На строгальных станках обрабатывают в основном различные по расположению плоскости: горизонтальные, вертикальные, параллельные, перпендикулярные и наклонные; Т-образные, прямоугольные и другие пазы и канавки; фасонные поверхности.
Строгание горизонтальных, вертикальных, параллельных и перпендикулярных плоскостей на поперечно- и продольно-строгальных станках производится с помощью проходных резцов – чистовых и черновых. Чис-
135
товые проходные резцы применяются для сравнительно точной обработки. Они бывают нормальные, предназначенные для строгания с малыми подачами, и широкие – для строгания с большими поперечными подачами, доходящими до 30 мм за один рабочий ход. Глубина резания при работе чистовых резцов составляет 0,5 – 1,5 мм. Черновые проходные резцы предназначаются для грубой обработки.
Строгание наклонных плоскостей выполняют на поперечно- и про- дольно-строгальных станках проходными резцами при установке суппорта под необходимым углом, что обеспечивает его подачу параллельно наклонной плоскости, для обработки узких (10 – 30 мм) наклонных плоскостей применяют специальные широкие резцы.
Для строгания прямоугольных, Т-образных пазов, канавок, выемок используются прорезные пазовые резцы. Ширина строгального пазового резца при узких пазах выбирается равной ширине паза, благодаря чему снижается время на его выполнение. Широкие и Т-образные пазы выполняют последовательно за несколько проходов. Внутренние шпоночные канавки выполняют особыми изогнутыми резцами.
Строгание фасонных поверхностей на поперечно- и продольнострогальных станках производится фасонными резцами вогнутыми, выпуклыми и других форм – с использованием поворотных и специальных копировальных устройств.
Долбежные работы и резцы для них мало отличаются от строгальных. Резец совершает прямолинейное возвратно-поступательное движение по вертикали. Долбежные резцы делятся на проходные, прорезные и для выполнения шпоночных пазов. Проходными резцами обрабатывают вертикальные и всевозможные криволинейные поверхности, прорезными – пазы, канавки, выемки, плоскости с уступами и разрезание.
Процесс резания фрезой имеет много общего с процессом резания резцом. Стружкообразование в этом случае сопровождается теми же физическими явлениями: упругой и пластической деформацией металла, тепловыделением, наклепом и др.
Каждый зуб фрезы, являющейся многолезвийным инструментом, имеет такие же режущие элементы, как и резец. Весь припуск с заготовок последовательно срезается зубьями фрезы.
По сравнению с процессом точения процесс фрезерования имеет следующие особенности. В работе одновременно участвуют несколько лезвий, поэтому фрезерование является более производительным способом обработки, чем точение, каждый зуб фрезы работает периодически, а корпус ее большей частью имеет значительную массу, что способствует лучшему охлаждению лезвий; толщина стружки изменяется до некоторого максимума по вполне определенному закону, вследствие чего силы резания имеют переменные значения.
136
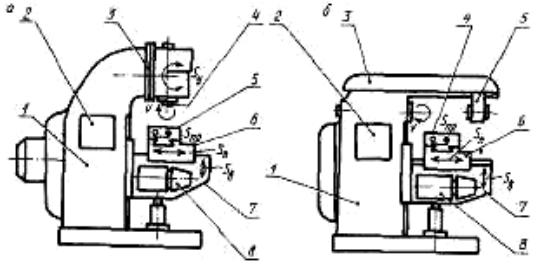
Фрезе сообщается вращательное (главное) движение, а обрабатываемая деталь получает поступательное движение (движение подачи). Различают два способа фрезерования: встречное – направления вращения и движения подачи противоположны; попутное – направления вращения и движения подачи совпадают. При встречном фрезеровании происходит постепенное возрастание нагрузки на зуб по мере его врезания в обрабатываемый материал, что обеспечивает более плавную работу и меньшую скорость изнашивания зубьев, чем при попутном фрезеровании, однако чистота обрабатываемой поверхности при этом уменьшается.
Для процессов фрезерования применяют горизонтальные и вертикальные фрезерные станки.
Основными узлами вертикально-фрезерного станка (рис. 7.16, а)
являются: станина 1, коробка скоростей 2, поворотная шпиндельная головка 3, шпиндель 4, стол 5, салазки 6, консоль 7, коробка подач 8. Шпиндель имеет главное вращательное движение. При обработке заготовка получает движение подачи в трех направлениях: продольном, поперечном и вертикальном.
а) |
б) |
Рис. 7.16. Схема фрезерных станков: а – вертикально-фрезерный станок; б – горизонтально-фрезерный станок
Горизонтально-фрезерный станок (см. рис. 7.16, б) состоит из ста-
нины 1, коробки скоростей 2, размещенной в станине, хобота 3 для подвески 5, стола 4, салазок 6, консоли 7, коробки подач 8, которая размещена в консоли. Для обработки заготовка (устанавливается на столе в тисках или приспособлениях) получает подачу в трех направлениях: продольном, поперечном и вертикальном. Продольное направление заготовки осуществляется за счет перемещения стола по направляющим салазок, поперечное – салазок по направляющим консоли и вертикальное – консоли по направляющим станины. Главным движением является вращение шпинделя.
137
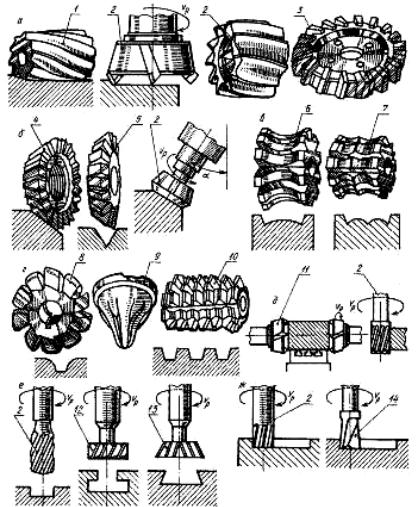
Точность фрезерования зависит от многих факторов: типа станка, вида фрез, режимарезанияидр. Можнополучитьточность3 – 4-гоквалитетов.
Основные работы, выполняемые на фрезерных станках, – фрезе-
рование плоскостей, пазов, сложных поверхностей, шпоночных канавок и зубьев шестерен.
Фрезерование горизонтальных плоскостей (рис. 7.17, а) осуществляется на горизонтально- и вертикально-фрезерных станках цилиндрическими 1, торцевыми 2, дисковыми 3 фрезами. Для обработки наклонных плоскостей (см. рис. 7.17, б) на горизонтально-фрезерных станках используют одноугловые 4 и двуугловые 5 фрезы, а на вертикально-фрезерном станке со шпинделем, установленным под требуемым углом, – торцевые фрезы 2.
Рис. 7.17. Основные виды фрезерных работ и инструмент для фрезерования
Фрезерование сложных и фасонных поверхностей (см. рис. 7.17, в) производят фасонными фрезами 6 и 7 соответствующего профиля на гори- зонтально-фрезерных станках. Для этих же целей используют продольнофрезерные станки, на которых суппорт можно устанавливать наклонно, а также специальные копировально-фрезерные станки.
138
Прямоугольные, Т-образные, типа ласточкина хвоста и другие пазы (см. рис. 7.17, е) выполняют с помощью соответствующих фрез 2, 12 и 13 на вертикально-фрезерном станке.
Фрезерование шпоночных канавок прямоугольного сечения ведут на го- ризонтально-фрезерных станках дисковой фрезой, на вертикально-фрезерных – концевой2 илиспециальной шпоночнойфрезой14 (см. рис. 7.17, ж).
В массовом и серийном производстве фрезерование зубьев шестерен выполняют на специальных зубофрезерных станках, а в индивидуальном – на горизонтально- и вертикально-фрезерных станках. Для фрезерования зубьев (см. рис. 7.17, г) используют модульные дисковые 8, пальцевые 9 или червячные 10 фрезы. Каждая модульная фреза пригодна для получения зубьев только данного модуля и только в определенном интервале количества зубьев (например, от 17 до 20), поэтому фрезы обычно изготовляются комплектами. Червячная фреза имеет зубья трапецеидальной формы. Нарезание ею зубьев производится методом обкатки, при этом точность более высокая, чем при использовании для этих же целей модульных фрез. Нужный профиль получается автоматически в зависимости от обкатываемого диаметра. Червячные фрезы применяются также для резьбонарезания, фрезерования шлицев и т.д. Основное технологическое время, определяющее в значительной мере производительность процесса при фрезеровании, рассчитывается по той же формуле, что и при точении.
Процесс шлифования по сравнению с рассмотренными процессами точения, сверления и фрезерования имеет следующие особенности:
1.Шлифовальный круг состоит из абразивных зерен (алмаз, кремнезем, корунд, карбид и др.), связанных цементирующим веществом (керамическим, силикатным, вулканитовым, бакелитовым и др.) в одно целое, и является многолезвийным режущим инструментом. В работе участвует одновременно значительное количество зерен, представляющих собой многогранники неправильной формы, работающие с невыгодными углами резания.
2.В отличие от работы однолезвийным режущим инструментом, когда процессом резания можно управлять, изменяя режим резания и геометрию инструмента, при шлифовании управлять процессом труднее.
3.Шлифование осуществляется при больших скоростях резания. Температура в рабочей зоне достигает 1500 °С. Обработка шлифованием в большинстве случаев является чистовой и отделочной операцией, обеспечивающей высокое качество обработанной поверхности и точность обработки (1 – 2-й квалитеты). В некоторых случаях шлифование применяют для предварительной обработки (очистки) заготовок, обдирки при снятии слоя до 6 мм.
Процесс шлифования обычно осуществляется при помощи трех движений: вращения шлифовального круга, вращения или возвратно-
139
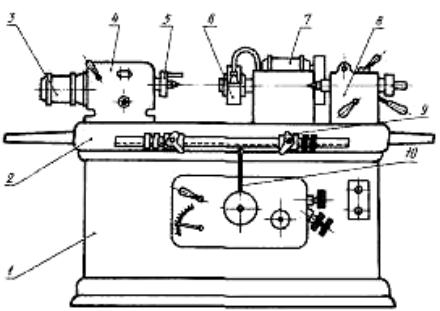
поступательного перемещения обрабатываемой детали и движений подачи, осуществляемых кругом или обрабатываемой деталью.
Основными элементами режима резания при шлифовании являются скорость и глубина резания, продольная подача, скорость вращения обрабатываемой детали и др.
В группу шлифовальных станков входят круглошлифовальные, внутришлифовальные, обдирочно-шлифовальные, специализированные (зубошлифовальные, бесцентрово-шлифовальные, копировальные и др.), заточные станки для режущих инструментов, притирочные и полировальные.
Схема круглошлифовального станка представлена на рис. 7.18.
Рис. 7.18. Общий вид круглошлифовального станка
По направляющим станины 1 круглошлифовального станка совершает продольное возвратно-поступательное перемещение стол 2 с передней 4 и задней 8 бабками. Причем последняя неподвижна. Стол имеет только поперечную периодическую подачу. Вращение круга 6 осуществляется электродвигателем 7 через ременную передачу. Электродвигатель 3 через коробку скоростей, расположенную в передней бабке 4, приводит во вращение поводковую планшайбу 5, которая обеспечивает вращение шлифуемой детали. Возвратно-поступательное движение стола 2 осуществляется гидравлическим приводом, а управление столом – с помощью специальных упоров 9, устанавливаемых на различном расстоянии в зависимости от длины шлифуемой детали и воздействующих на рукоятку 10.
Шлифование наружных поверхностей цилиндрических, кониче-
ских, фасонных тел вращения и их торцевых поверхностей (рис. 7.19, а – в) производят на круглошлифовальных станках с использованием плоских 1,
140