
Методичка по Материаловедению Теперь и в ПДФ
.pdf103
металлокерамические твердые сплавы с более высокой твердостью, чем инструментальные стали (твердые сплавы группы ВК с содержанием кобальта не менее 15%).
Стали для штампов горячего деформирования. К инструмен-
ту, деформирующему металл в горячем состоянии, относятся штампы для кузнечного производства, которые деформируют металл, предварительно нагретый до высоких температур (1000º...1150°С). В процессе работы штампы подвергаются воздействию сложных напряжений (сжатию, растяжению, изгибу) и истирающему действию горячего металла. Кроме того, при пластической деформации рабочая часть штампа значительно нагревается. Поэтому сталь для изготовления кузнечных штампов должна иметь высокие механические свойства (прочность, вязкость, износостойкость), не только при обычных, но и при повышенных температурах, т.е. быть теплостойкой.
Теплостойкие стали применяют для изготовления тяжелонагруженного прессового инструмента, а также штампов для горизон- тально-ковочных машин. Из них также изготовляют детали пресс-форм для литья под давлением магниевых, алюминиевых и медных сплавов.
При кратковременном воздействии горячего металла на штамп используют стали 5ХГМ, 5ХНМ, 5ХНВ, 5ХНВС и др. Все стали содержат одинаковое количество углерода 0,5-0,6%, что дает возможность получить требуемую твердость и прочность при достаточной вязкости.
Из этих сталей изготавливают молотовые штампы, для которых характерны большие размеры и работающие со значительными ударными нагрузками при умеренном разогреве рабочих поверхностей (примерно до 400°С).
Долговременное воздействие ударных нагрузок выдерживают стали 4Х2В5ФМ, 4ХЗВФ2М2, ЗХ2В8Ф и др.
Твердые сплавы. Для изготовления твердых сплавов используют метод порошковой металлургии. Для этого порошки карбидов вольфрама (WC), титана (ТС) и тантала (ТаС) смешивают с кобальтом (Со), прессуют в формы и затем запекают при
1500...2000°С.
Применение твердых сплавов позволяет не только увеличить скорость обработки, но и значительно повысить износостойкость обрабатывающего и штампового инструмента. Износостойкость твердых металлокерамических сплавов увеличивается с ростом твердости и в 10 - 15 раз превышает значения, характерные для
104
быстрорежущей стали. Сохраняется она до 800...1000°С.
Твердые сплавы делятся на три группы: одно-, двух- и трехкарбидные.
Однокарбидные твердые сплавы, которые содержат карбиды вольфрама, называют вольфрамокобальтовыми (группа ВК). В марках ВК2, ВК4, ВК6, ВК10 цифра показывает процентное содержание кобальта, остальное - карбид вольфрама. Сплавы этой группы наиболее прочные, с увеличением содержания кобальта сплавы повышают сопротивление ударным нагрузкам, одновременно снижается износостойкость.
Сплавы ВК4, ВК6 рекомендуются для чернового точения, фрезерования, рассверливания, зенкерования при обработке чугуна, жаропрочных сплавов, цветных металлов и неметаллических материалов.
Сплав ВК8 применяют для чернового точения и других видов черновой обработки, а также для волочения и калибровки труб, прутков и проволоки.
Сплав ВК10 предназначается для изготовления быстроизнашивающихся деталей. Этот сплав характеризуется высокой эксплуатационной прочностью, но сравнительно низкой износостойкостью.
Двухкарбидные твердые сплавы помимо группы ВК содержат еще карбиды титана, поэтому их называют титановольфрамокобальтовыми (группа ТВК). В марках Т5К10, Т15К6, Т30К4 цифры после буквы Т показывают процентное содержание карбидов титана, после К – содержание металлического кобальта, остальное
-карбиды вольфрама. Эти сплавы менее прочны и более износостойки, чем сплавы первой группы.
Титановольфрамовые сплавы применяют для чистового (Т30К4) и чернового (Т15К6, Т5К10) точения, фрезерования и строгания стали.
Трехкарбидные твердые сплавы содержат еще и карбиды тантала и поэтому называются титанотанталовольфрамокобальтовыми (группа ТТК). В марках ТТ7К12, ТТ8К6, ТТ20К9 цифра перед К показывает суммарное процентное содержание карбидов титана и тантала, после К
-содержание металлического кобальта, остальное - карбиды вольфрама. Сплавы обладают повышенной прочностью, износостойкостью и вязкостью.
Состав (массовая доля основных компонентов, %) и твердость HRA некоторых твердых сплавов даны в табл. 13 .
Титанотанталовольфрамокобальтовые сплавы применяют при черновой и чистовой обработке труднообрабатываемых материалов, в том
105
числе жаропрочных сплавов и сталей.
Разработаны твёрдые сплавы, не содержащиеся дефицитного вольфрама. Безвольфрамовые твердые сплавы на основе Ti + Ni + Mo – сплав ТН-20 (цифра показывает суммарное содержание Ni и Mo) и на основе карбонитрида титана Ti(NC) + Ni + Mo – KHT16. Никель и молибден образуют связывающую матрицу, применяются при получистовом и чистовом точении и фрезеровании сталей и цветных металлов.
|
|
|
|
|
|
|
|
|
|
|
Таблица 13 |
|
|
|
Состав и твердость твердых сплавов |
||||||||||
|
|
|
|
|
|
|
|
|
|
|
|
|
Сплав |
|
WC |
|
|
TiC |
|
ТаС |
|
Со |
|
Твердость HRA, не |
|
|
|
|
|
|
|
|
|
|
|
|
менее |
|
|
|
|
|
|
|
|
|
|
|
|
|
|
|
|
|
Вольфрамокобальтовая группа (ВК) |
|
|
|
||||||
ВК3 |
|
97 |
|
|
- |
|
- |
|
3 |
|
89,5 |
|
|
|
|
|
|
|
|||||||
ВК4 |
|
96 |
|
|
- |
|
- |
|
4 |
|
89,5 |
|
|
|
|
|
|
|
|
|
|
|
|
|
|
ВК6 |
|
94 |
|
|
- |
|
- |
|
6 |
|
88,5 |
|
|
|
|
|
|
|
|
|
|
|
|
|
|
ВК8 |
|
92 |
|
|
- |
|
- |
|
8 |
|
87,5 |
|
|
|
|
|
|
|
|
|
|
|
|
|
|
ВК10 |
|
90 |
|
|
- |
|
- |
|
10 |
|
87,0 |
|
|
|
|
|
|
|
|
|
|
|
|
|
|
|
|
|
|
|
|
|
|
|
|
|
|
|
|
|
|
|
|
|
|
|
|
|
|
|
|
|
|
|
Титановольфрамокобальтовая группа ( ТВК) |
|
||||||||
|
|
|
|
|
|
|
||||||
Т30К4 |
|
66 |
|
|
30 |
|
- |
|
4 |
|
92.0 |
|
Т15К6 |
|
79 |
|
|
15 |
|
- |
|
6 |
|
90,0 |
|
Т5К10 |
|
85 |
|
|
5 |
|
- |
|
10 |
|
88,5 |
|
|
|
|
|
|
|
|
|
|
|
|
|
|
|
|
Титанотанталовольфрамокобальтовая группа (ТТК) |
|
|||||||||
|
|
|
|
|
|
|
||||||
ТТ7К12 |
|
81 |
|
|
4 |
|
3 |
|
12 |
|
87 |
|
|
|
|
|
|
|
|||||||
ТТ8К6 |
|
86 |
|
|
6 |
|
2 |
|
6 |
|
90,5 |
|
ТТ20К9 |
|
71 |
|
|
8 |
|
12 |
|
9 |
|
89,0 |
|
|
|
|
|
|
|
|
|
|
|
|
|
|
Порядок выполнения работы
1. Изучить виды инструментальных материалов.
106
2.Указать режимы термической обработки и проанализировать изменение структуры и механических свойств.
3.Привести примеры маркировки и области применения инструментальных материалов, используя коллекцию металлорежущих инструментов.
Контрольные вопросы и задания
1.Каковы достоинства и недостатки углеродистых инструментальных сталей?
2.Назовите преимущества легированных сталей для режущего инструмента по сравнению с углеродистыми.
3.Укажите марки быстрорежущих сталей.
4.Каким образом достигается упрочнение быстрорежущих сталей?
5.Каким требованиям должна отвечать сталь для штампов деформирования в холодном состоянии? Приведите примеры марок сталей.
6.Укажите стали для штампов горячего деформирования.
7.Что собой представляют твердые сплавы?
8.Назовите классификацию и назначение твердых сплавов.
9.Какие Вы знаете безвольфрамовые твердые сплавы?
Работа № 10
Медные и антифрикционные сплавы
107
Цель работы: изучение структуры, свойств, маркировки медных и антифрикционных сплавов и области их применения.
Приборы и оборудование: коллекция изделий из медных и антифрикционных сплавов.
Основные свойства меди. Медь – металл красного (светло – розового) цвета с плотностью 8,94 г/см3, имеющий кристаллическую решётку ГЦК, без полиморфных превращений и температурой плавления
1083º С.
Широкое применение меди обусловлено рядом её ценных свойств и прежде всего высокой электро- и теплопроводностью. Медь принято считать эталоном электрической проводимости и теплопроводности по отношению к другим металлам. Медь обладает высокой пластичностью, хорошей коррозионной стойкостью, удовлетворительной жидкотекучестью.
Медь и её сплавы хорошо обрабатываются давлением, свариваются всеми видами сварки и легко поддаются пайке. На поверхности меди образуется плотная оксидная плёнка, поэтому медь имеет высокую коррозионную стойкость в пресной и морской воде, в атмосферных условиях и различных химических средах (органических кислотах, едких щелочах). Однако медь не противостоит воздействию азотной и соляной кислот, концентрированной серной кислоты, аммиака. Недостатком меди является сравнительно плохая обрабатываемость резанием.
Электрическая проводимость меди зависит от содержания примесей. При наличии даже небольшого количества примесей проводимость резко падает. При ГОСТ 859-78 в зависимости от содержания примесей различают следующие марки меди: М00 (99,99% Cu), М0 (99,97% Cu), М1 ( 99,9% Cu), М2 ( 99,7% Cu), М3 ( 99,5% Cu).
Наиболее чистую медь марок М00, М0, М1, содержащую не более 0,1% примесей, применяют для проводников тока различных теплообменников. Медь остальных марок, более загрязнённая примесями, пригодна только для производства сплавов различного состава и качества (М3, М4).
Наиболее часто встречающиеся в меди элементы подразделяют на две группы:
1. Растворимые в меди элементы алюминий (Аl), железо (Fe), никель (Ni), стронций (Sr), цинк (Zn), серебро (Ag) повышают прочность и твердость меди и используются для легирования сплавов на медной основе.
Нерастворимые элементы свинец (Pb), висмут (Bi) ухудшают ме-
108
ханические свойства меди. Висмут и свинец даже в тысячных долях процентов резко ухудшают способность меди обрабатываться путём прокатки или волочения. С этими элементами медь образует легкоплавкие эвтектики, которые располагаясь по граница зёрен, при нагреве расплавляются и вызывают красноломкость меди, т. е. приводят к разрушению металла при горячей деформации. Висмут, будучи хрупким металлом охрупчивает медь и её сплавы. Свинец, обладая низкой прочностью, снижает прочность медных сплавов, однако вследствие хорошей пластичности не вызывает их охрупчивание. Кроме того, свинец улучшает антифрикционные свойства и обрабатываемость резанием медных сплавов, поэтому его применяют для легирования.
Механические свойства меди в большей степени зависят от её состояния и в меньшей от содержания примесей. В отожженном виде медь весьма пластична (δ = 50%, HB 50, σВ = 240 МПа). В деформированном состоянии (при наклёпке) пластичность меди понижается, но прочность повышается (δ = 2-5%, HB 120, σВ = 500 МПа). Исходные свойства меди восстанавливают путём отжига при температуре
600…700ºС.
Общая характеристика и классификация медных сплавов. Для повышения прочностных свойств медь легируют цинком, оловом, алюминием, марганцем, железом, кремнием, никелем. Повышая прочность медных сплавов, легирующие элементы практически не снижают, а некоторые из них (цинк, алюминий) увеличивают пластичность. Высокая пластичность – отличительная особенность медных сплавов. По прочности медные сплавы уступают сталям. Сплавы меди устойчивы против коррозии, обладают хорошими антифрикционными, технологическими и механическими свойствами и широко используются в качестве конструкционных материалов.
По технологическим свойствам медные сплавы подразделяют на деформируемые (обрабатываемые давлением) и литейные. Из деформируемых медных сплавов изготавливают трубы, листы, ленту, проволоку, из литейных путем литья различные фасонные детали.
По способности упрочняться с помощью термической обработки медные сплавы делятся на упрочняемые и неупрочняемые термической обработкой.
По химическому составу медные сплавы подразделяют на две ос-
109
новные группы: латуни и бронзы.
Медные сплавы маркируют по химическому составу, используя буквы для обозначения элементов и числа для указания их массовых долей. В медных сплавах буквенные обозначения отличаются от обозначений, принятых для сталей. Алюминий в них обозначают буквой А, бериллий – Б, железо – Ж, кремний – К, магний – Мг, марганец – Мц, медь – М, мышьяк – Мш, никель – Н, олово – О, свинец – С, серебро – Ср, сурьма – Су, фосфор – Ф, цинк – Ц, цирконий – Цр, хром – Х.
Латуни. Сплавы меди с цинком, а иногда с добавками небольшого количества других элементов называют латунями. Из цветных сплавов латуни являются самыми распространенными.
По назначению и технологическим признакам латуни подразделяются на деформируемые и литейные.
Латуни маркируются буквой Л. В деформируемых латунях, не со-
держащих кроме меди и цинка других элементов, за буквой Л ставить-
ся число, показывающее среднее содержание меди. В многокомпо-
нентных латунях после Л ставятся буквы – символы элементов, а затем числа, указывающие содержание меди и каждого легирующего эле-
мента. Например, латунь марки Л68 содержит 68% меди, остальное цинк. Латунь ЛЖМц 59-1-1 содержит 59% меди, 1% железа, 1% мар-
ганца, остальное – цинк. В марках литейных латуней указывается со-
держание цинка, а количество каждого легирующего элемента ста-
виться непосредственно за буквой, обозначающей его. Например, ла-
тунь ЛЦ40Мц3А содержит 40% цинка, 3% марганца, 1% алюминия,
остальное – медь.
Цвет (от красноватого до светло-желтого) и механические свой-
ства латуни изменяются при увеличении содержания в них цинка.
Структура латуней зависит от их состава и может быть установлена по известной диаграмме состояния системы медь – цинк (Cu - Zn). В системе Cu – Zn образуется шесть твердых растворов: α, β, γ, δ, σ, η, но практическое применение имеют латуни, содержащие до 45% цинка.
Левая часть диаграммы состояния Cu – Zn, включающая область однофазных (α) и двухфазных (α + β) латуней, приведена на рис. 46.
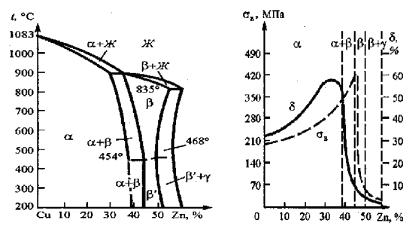
110
Однофазная α–латунь представляет собой твердый раствор цинка в меди с решеткой ГЦК и может содержать до 39% цинка. Однофазная α–латунь характеризуется высокой пластичностью. При содержании более 39% цинка в структуре появляется хрупкая β-фаза. β-фаза – это электронное соединение CuZn с решеткой ОЦК.
Рис. 46. Левая часть диаграммы |
Рис. 47. Влияние цинка на меха- |
состояния Cu-Zn |
нические свойства латуней |
Существуют две модификации β-фазы: выше 454…486°С устойчива пластичная β-фаза, имеющая неупорядоченное расположение атомов. Ниже этих температур – более твердая и хрупкая β´-фаза, которая характеризуется упорядоченным расположением атомов меди и атомов цинка.
Двухфазные (α + β´)–латуни могут содержать до 45% цинка.
В соответствии с изменением структуры меняются механические свойства латуней. Влияние цинка на механические свойства латуней приведены на рис. 47.
β´-фаза появляется в структуре латуней при содержании цинка около 30%. Поэтому в сплавах, содержащих менее 30% цинка, увеличение его концентрации повышает и прочность, и пластичность. Затем пластичность начинает уменьшаться, а после появления в структуре
111
значительных качеств β´-фазы происходит резкое падение пластичности. Прочность продолжает повышаться при увеличении цинка до 45%, пока латунь находиться в двухфазном состоянии, а потом также резко снижается. Сплавы с большим содержанием цинка отличаются высокой хрупкостью.
Химический состав некоторых промышленных латуней (ГОСТ 15527-70, ГОСТ 1774-93) и их механические свойства приведены в табл. 14, 15.
Таблица 14
Химический состав и механические свойства деформируемых латуней после отжига (ГОСТ 15527-70)
Марка латуни |
Содержание, мас. % |
σв, |
σ0,2, |
δ, |
Ψ, |
KCU, |
HB |
||
|
|
||||||||
Cu |
Прочих |
МПа |
МПа |
% |
% |
МДж/м2 |
|||
|
|
элементов |
|
|
|
|
|
|
|
Л90 |
88-91 |
- |
260 |
120 |
45 |
80 |
1,76 |
53 |
|
Л68 |
67-70 |
- |
320 |
90 |
55 |
70 |
1,68 |
55 |
|
Л63 |
62-65 |
- |
330 |
110 |
50 |
66 |
1,37 |
56 |
|
Л60 |
59-62 |
- |
380 |
160 |
25 |
62 |
0,78 |
77 |
|
ЛА77-2 |
76-79 |
1,75-2,5 Al |
400 |
140 |
55 |
58 |
- |
60 |
|
ЛАН59 - 3 - 2 |
57-60 |
2,5-3,5 Al |
380 |
300 |
50 |
- |
0,5 |
75 |
|
2-3 Ni |
|||||||||
|
|
|
|
|
|
|
|
||
ЛН65 - 5 |
64-67 |
5-6,5 Ni |
400 |
170 |
65 |
- |
- |
60 |
|
|
|
0,1-0,4 Al |
|
|
|
|
|
|
|
ЛЖМц59-1-1 |
57-60 |
0,6-1,2 Fe |
450 |
170 |
50 |
58 |
1,18 |
88 |
|
0,5-0,8 Mn |
|||||||||
|
|
|
|
|
|
|
|
||
|
|
0,3-0,7 SN |
|
|
|
|
|
|
|
ЛМц58 - 2 |
57-60 |
1-2 Mn |
400 |
160 |
40 |
52, |
- |
85 |
|
5 |
|||||||||
|
|
|
|
|
|
|
|
||
ЛО7О - 1 |
69-71 |
1-1,5 Sn |
350 |
100 |
0 |
70 |
0,6 |
60 |
|
ЛК80 - 3 |
79-81 |
2,5-4 Si |
340 |
200 |
58 |
55 |
0,4 |
100 |
|
|
|
|
|
Таблица 15 |
|
Механические свойства и область применения |
||||
|
|
литейных латуней (ГОСТ 17711-93) |
|||
|
|
|
|
|
|
Марка латуни |
|
σв, МПа |
δ, % |
HB |
Область применения |
|
|
|
|
|
|
ЛЦ40С |
|
|
|
|
Арматура, втулки, сепарато- |
|
215 |
12-20 |
70-80 |
ры для подшипников качения |
|
|
|
||||
ЛЦ40Мц3Ж |
|
|
|
|
Несложные детали ответст- |
112
|
|
|
|
венного назначения, гребные |
|
|
390-490 |
10-18 |
90-100 |
винты и лопасти, судовая |
|
|
|
|
|
арматура, работающая при |
|
|
|
|
|
температуре до 300°С |
|
|
|
|
|
Антифрикционные втулки, |
|
ЛЦ38Мц2С2 |
245-340 |
10-15 |
80-85 |
вкладыши, ползуны, судовая |
|
|
|
|
|
арматура |
|
ЛЦ30А3 |
290-390 |
12-15 |
80-90 |
Коррозионно-стойкие детали |
|
|
|
|
|
Детали ответственного на- |
|
ЛЦ23А6Ж3Мц2 |
|
|
|
значения, нажимные винты и |
|
700 |
7 |
160-165 |
гайки прокатных станов, |
||
|
|||||
|
|
|
|
венцы червячных колес |
|
|
|
|
|
Сложные по конфигурации |
|
ЛЦ16К4 |
290-340 |
15 |
100-110 |
детали, работающие при |
|
|
|
|
|
температуре до 250°С |
|
ЛЦ14К3С3 |
245-290 |
7-15 |
90-100 |
Подшипники, втулки |
Латуни обычно хорошо обрабатываются давлением. Наибольшую пластичность имеют однофазные α–латуни (содержание цинка до 39%) и они хорошо поддаются холодной пластической деформации, которая значительно повышает их прочность и твердость.
Вдвухфазных α+β´–латунях пластичность резко снижена, поэтому они удовлетворительно деформируются в горячем состоянии. Обычно их деформируют при температуре несколько выше 700°С.
Повышение содержания цинка удешевляет латуни, улучшает их обрабатываемость резанием, способность прирабатываться и противостоять износу. Вместе с тем уменьшаются теплопроводность и электрическая проводимость, которые составляют 20-50% от характеристик меди.
Примеси повышают твердость и снижают пластичность латуней. Особенно неблагоприятно действуют свинец и висмут, которые в однофазных латунях вызывают красноломкость. Поэтому однофазные латуни в основном выпускают в виде холоднокатаных полуфабрикатов: полос, лент, проволоки, листов, из которых изготовляют детали методом глубокой вытяжки (радиаторные трубки, снарядные гильзы, сильфоны, трубопроводы), а также детали, требующие по условиям эксплуатации низкую твердость (шайбы, втулки, уплотнительные кольца и др.).
Вдвухфазные латуни иногда добавляют свинец для улучшения обрабатываемости резанием и повышения антифрикционных свойств.