
water quality and system
.pdf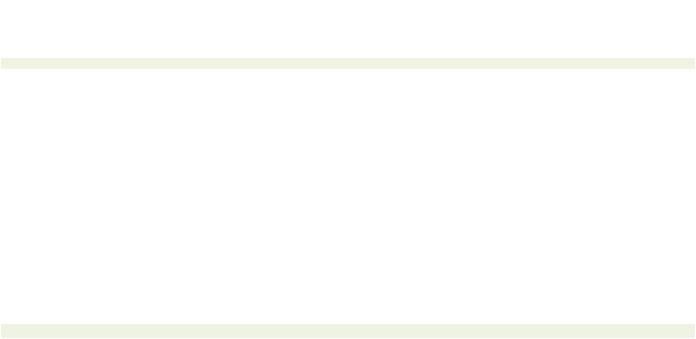
< previous page |
page_82 |
next page > |
Page 82
Conduct a Needs Assessment
The first step in the upgrade process is a needs assessment. Essential questions to be included in making an assessment as to whether to upgrade or not are listed below. In answering the questions, if the response is not known, provide a best estimate. It is possible to go back and fill in the details a little later.
1.How many maintenance work hours have been spent repairing or replacing plumbing and piping in the facility in the past year?
2.What is the total dollar value of the materials that have been installed in the past year?
3.Have there been any written complaints about the water supply? Review records of complaints.
4.How old are the plumbing fixtures in the restrooms?
5.Has the facility been contacted by the city and notified of the requirements to notify the public about health hazards in the existing water supply?
6.Any flooding or wastewater problems? What were they?
7.Has the facility staff made suggestions for improvement to the facility that would improve service?
8.Have new standards or regulations identified any potential requirements to change or modify the water supply system?
In addition, the facility manager should consider changes to the use of the space since the original water system's installation, and whether the restroom fixtures, tile and other features are pleasant and compatible with the current decor or image of the general spaces. This can be particularly critical in high-profile business such as hotels and restaurants, but corporations may consider appearance critical as well for visitors and employees alike. Additionally, if the upgrade incorporates efficient electric motors, controls, low-flow devices or water-saving methods, we must also consider potential energy and water bill savings in the selection of components and design. All of these benefits must be weighed against cost.
< previous page |
page_82 |
next page > |
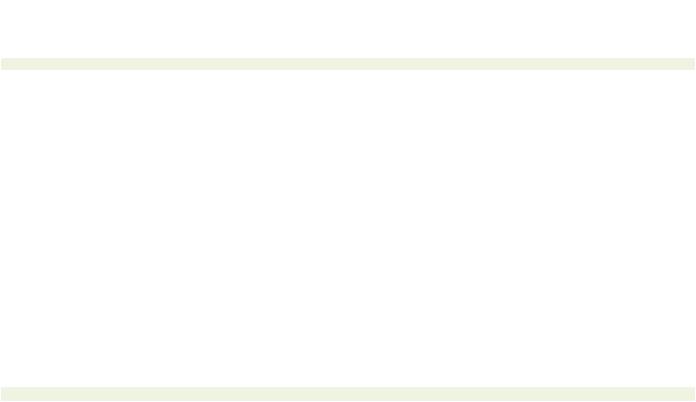
< previous page |
page_83 |
next page > |
Page 83
For a hotel, for example, the basic question would be: If we remodel these rooms, how much will we be able to increase the rental rate? If we cannot increase the rental rate, will we be able to increase occupancy? Can this formula be tested? How? It is easy to estimate costs. It is quite another problem to estimate yields, especially one that is accurate.
Conduct a Utility Survey
The next step is to conduct a survey of the water system. We want to know what types of equipment are in operation, find out how much the water system costs in energy and water, and generate a profile of water use and balance between supply and wastewater.
Is the water coming into the facility being matched by the water going out? As discussed in Chapter 1, we can construct a model of water use based on the monthly utility bills; these bills for supply water can be used as an initial guess of the water going out.
The manager should validate if the water meters are accurately indicating the flows. If the utility readings are based on the flow meter, this is adequate for an initial assessment. Later, the facility may decide to have the flow meters calibrated to verify the accuracy of the flows.
If older bills are available in the records, a pattern can be established offering seasonal use and flows. New York City once estimated that approximately 21 percent of its water supplies is unaccounted for in utility bills.
Next, water use can be estimated based upon the types of items and number of people using water at the facility. Figure 5-1 is a form that allows the facility to collect the necessary data for finding out where the water is being used. It is desirable, in order to keep track of which worksheets go with which facilities and spaces or rooms, to use the worksheets with a floor plan, numbering each facility and room.
Constructing a Model of Water Use
Once a tally of all the devices has been completed, Table 5-1 can be used to fill out the number of gallons of use per fixture per day. By extending the numbers of fixtures times the flows per fixture a total of flows for that type of device can be calculated per day. This can be extended into a total of all flows per day.
Now that an exact count of the devices and an estimate of the
< previous page |
page_83 |
next page > |
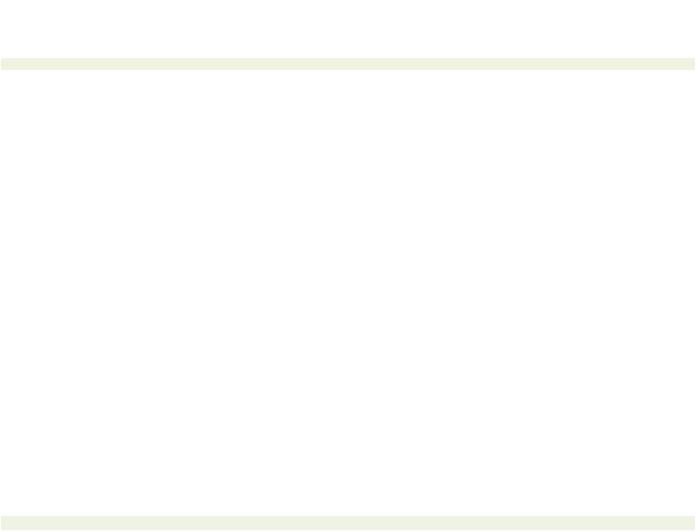
< previous page |
page_84 |
Water Survey |
Sheet ____________ |
Name of Facility __________________________ |
Location of Facility_____________ |
Name of Person Collecting Data ________________ |
Phone_______________________ |
Work address ____________________________________________________________________
Room Number or Name ____________________________________________________________
Number of Water Closets ______________ |
Manufacturer/Brand name ______________________ |
||
Number of Urinals ___________________ |
Manufacturer/Brand name ______________________ |
||
Number of Showers __________________ |
Manufacturer/Brand name ______________________ |
||
Number of Sinks ____________________ |
Manufacturer/Brand name ______________________ |
||
Are there water entertainment/recreation items at the facility? |
|
||
Swimming Pool |
____ Yes |
Size _______ |
Gallons _____________ Sq. Ft. |
|
____ No |
|
|
Fountain |
____ Yes |
Size _______ |
Gallons _____________ Sq. Ft. |
|
____ No |
|
|
Jacuzzi/Spa |
____ Yes |
Size _______ |
Gallons _____________ Sq. Ft. |
|
____ No |
|
|
Hot water boilers |
____ Yes |
____ No |
|
Steam water boilers |
____ Yes |
____ No |
|
Natural gas boilers |
____ Yes |
____ No |
|
What kind of fuel is used for heat? |
|
|
|
Natural gas |
Cost: __________________ |
|
|
Fuel oil |
Cost: __________________ |
|
|
LPG gas |
Cost: __________________ |
|
|
How much does water cost for the facility? |
$ _______ per ________________ |
||
Figure 5-2. |
|
|
|
Form for performing a water utility study. |
|
|
|
< previous page |
|
|
page_84 |
next page >
Page 84
next page >
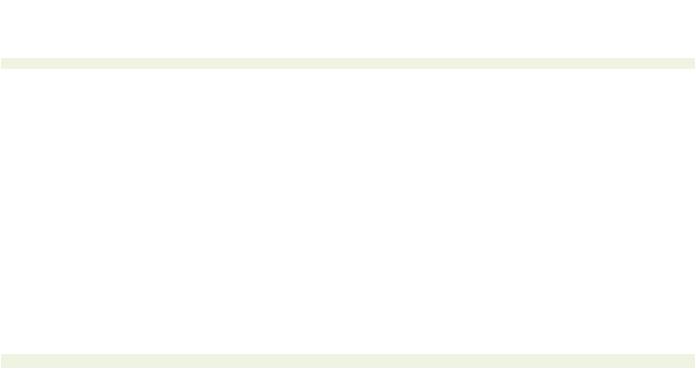
< previous page |
|
page_85 |
Are there water treatment systems such as water |
____ Yes |
____ No |
softeners? |
|
|
Make ____________________________ |
Model _____________________________ |
|
Water used per cycle ___________ Gallons* |
No. cycles per day ____________________ |
|
Is there are a laundry? |
____ Yes |
____ No |
Number of washing machines _____________ |
|
|
Make _______________________________ |
Model ______________________________ |
|
Water used per cycle ___________ Gallons* |
No. cycles per day ____________________ |
|
Are there any other items consuming water? |
____ Yes |
____ No |
What? ______________________________ |
|
|
Make ______________________________ |
Model ______________________________ |
|
Water used per cycle ___________ Gallons* |
No. cycles per day _____________________ |
*Hint: Check the operations and maintenance manual if you have one; if not, get the make and model and call a local vendor and ask him.
Figure 5-2.
Form for performing a water utility study.
< previous page page_85
next page >
Page 85
next page >
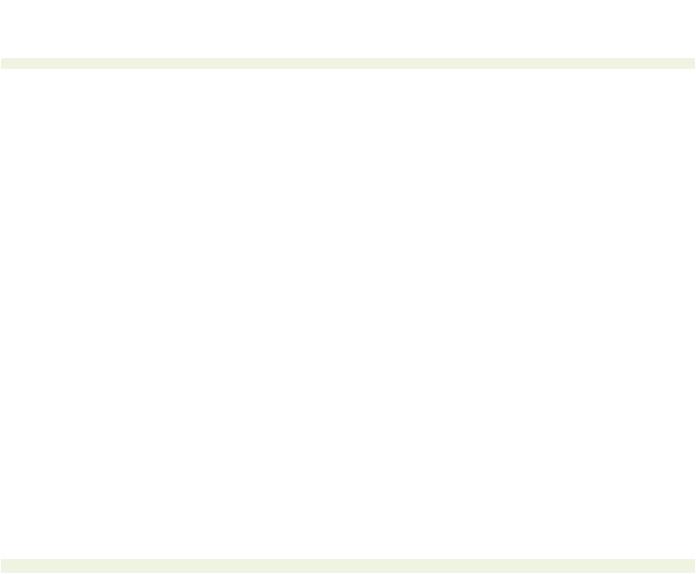
< previous page |
page_86 |
next page > |
Page 86
flows is known it is possible to check the calculated totals from fixture use against utility bills and to note any significant differences. Managers who are familiar with spreadsheet formulas on personal computers will find this type of information lends itself quite readily to a spreadsheet analysis.
The number of fixtures and total flows calculated from extending the fixtures times the flows is called a "water use model."
Adjusting the Model To Meet the Flows
Once built, the model should be adjusted for actual versus calculated totals. This process is called reconciliation. Using the known information from the utility bills, the estimated flows from the model are compared to the actual utility meter readings. This allows the manager to verify the accuracy of the model. If flows calculated are within 15 percent of the amount indicated on the utility bills, the results of the model can be considered fairly accurate.
Table 5-1. Minimum flow and pressure required by typical water-using devices, used for estimating flow and constructing a model of facility water use. Source: U.S. EPA, Manual of Individual Water Supply Systems, 1975.
|
Flow Pressure* |
Flow Rate |
||
|
(psi) |
(kPa) |
(gpm) |
(L/s) |
Ordinary basin faucet |
8 |
55 |
2.0 |
0.13 |
Self-losing basin faucet |
8 |
55 |
2.5 |
0.16 |
Sink faucet, 3/8-in. (9.5 mm) |
8 |
55 |
4.5 |
0.28 |
Sink faucet, 1/2-in. (12.7 mm) |
8 |
55 |
4.5 |
0.28 |
Bathtub faucet |
8 |
55 |
6.0 |
0.38 |
Laundry tub faucet, 1/2-in. (12.7 mm) |
8 |
55 |
5.0 |
0.32 |
Shower |
8 |
55 |
5.0 |
0.32 |
Ball-cock for closet |
8 |
55 |
3.0 |
0.19 |
Flush valve for closet |
15 |
103 |
15-40** 0.95-2.52** |
|
Flushometer valve for urinal |
15 |
103 |
15.0 |
0.95 |
Garden hose (50 ft., ¾-in., sill cock)(15 m, 19 mm) |
30 |
207 |
5.0 |
0.32 |
Garden hose (50 ft., 5/8-in. outlet)(15 m, 16 mm) |
15 |
103 |
3.33 |
0.21 |
Drinking fountains |
15 |
103 |
0.75 |
0.05 |
Fire hose 1.5-in. (38 mm), 1/2-in nozzle(12.7 mm) |
30 |
207 |
40.0 |
2.52 |
*Flow pressure is the pressure in the supply near the faucet or water outlet while faucet or water outlet is wide open and flowing.
**Wide range due to variation in design and type of closet flush valves.
< previous page |
page_86 |
next page > |
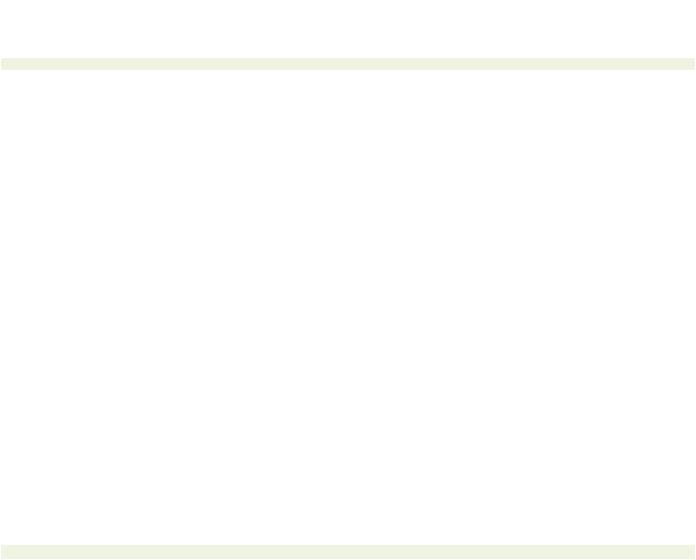
< previous page |
page_87 |
next page > |
Page 87
If the differences are greater than 15 percent, the model can be "ratioed." (see Figure 5-2). By ratioing, the model can be made to correlate with the utility bills.
The adjustment in the ratio is usually a result of a facility pressure different from the values assumed in Table 5-1. If, in Table 5-1, the flow was estimated at 20 gallons of water per day and the pressure at the facility is less than 60 pounds per square inch (psi), then perhaps the flow at that facility is only 15 gallons per day (gpd). If, on the other hand, the pressure is 120 psi, then the flow is going to be 30 gpd. So ratioing is not an uncommon method for adjusting models.
Next, the facility manager should locate a map of the utility piping. This map will show where the water lines are and it may be possible to isolate portions of the facility and measure flows to that area. If each building is submetered in addition to a meter for the entire complex, the individual meters can be used to total the flows for the entire complex. Do the flows total the same?
Actual Use (From Water Bills) ÷ Calculated Use (From Model) = Ratio*
Calculated Use |
Ratioed Use |
Ratio x Sinks |
= Sinks Use |
Ratio x Building A |
= Building A Use |
Ratio x Lawns |
= Lawns Use |
Calculated Use Total |
= Actual Use |
Example: Water Billed |
= 28,265 gallons (Actual Use) |
Calculated Use |
= 25,200 gallons |
28,265 + 25,200 |
= 1.12 |
1.12 × Sink Use |
= Sinks Use |
1.12 × Building A Use |
= Building A Use |
1.12 × Lawns Use |
= Lawns Use |
Total |
= Actual Use (28,265 gallons) |
*The ratio should not be more than 1.25. If it is, the model has likely missed a major user not yet identified. Check the facility to make sure that all water use has been accounted for. Some places where water use is missed is in mechanical rooms or boiler rooms where water is used for cooling. In addition, a leak could be present in the lines at some point.
Figure 5-2.
Ratioing the water use model, a technique used to reconcile known metered water use based on utility bills with the facility's water use model if a difference in
flows greater than 15 percent exists.
< previous page |
page_87 |
next page > |
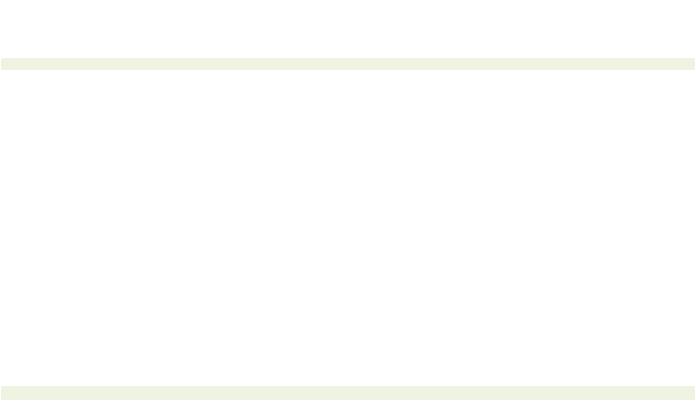
< previous page |
page_88 |
next page > |
Page 88
Remember water is not terribly expensive, so a little difference between the totals is not going to matter. Small leaks, drips or the gardener using a hose to wash down the sidewalk should not be enough to cause concern.
Another way to measure flows is to allow the device to flow into a known volume and measure the time it takes to fill the volume. For example, if it takes two minutes to fill a 5-gallon pail, then the flow can be estimated at 5 gallons ÷ 2 minutes = 2.5 gallons in one minute, or 2.5 gpm.
Analyze the Model
Once the flows are complete, the model's results can be analyzed to see where the flows are going.
Where is most of the use? Is it in the restrooms? the water heating? Is water being needlessly wasted?
By studying the water use model, the facility can determine how to save both water and money. In addition, hot water and boilers for utility processes and for facility heating can be analyzed and estimates for energy costs established as well.
Compare Alternatives and Decide
Just by knowing where the water is going is effective at showing the facility manager what his present water costs are. Once the facility has a model and the manager is confident that it is representative of actual water use in the facility, economic comparisons of alternative water uses are made.
Use Low-Flow Fixtures And Components - Water closets, urinals and water faucets can be improved to use less water.
Water conservation can be accomplished when upgrading by installing low-flow shower heads, aerators on sinks and lavatories, low-flow or ultra- low-flow toilets, low-flow urinals and other water-saving equipment.
Heating systems can be changed to more direct methods that reduce energy costs. For example, a direct natural-gas-fired water heater can be cheaper to operate than a steam water heater because of the energy lost in the steam system between the steam boiler and the hot water heater.
By taking the number of fixtures in the model and applying use factors from water conservation measures, a new scenario of water use can be generated. This can then be totaled against the utility bills to show the dollar value of the savings.
< previous page |
page_88 |
next page > |
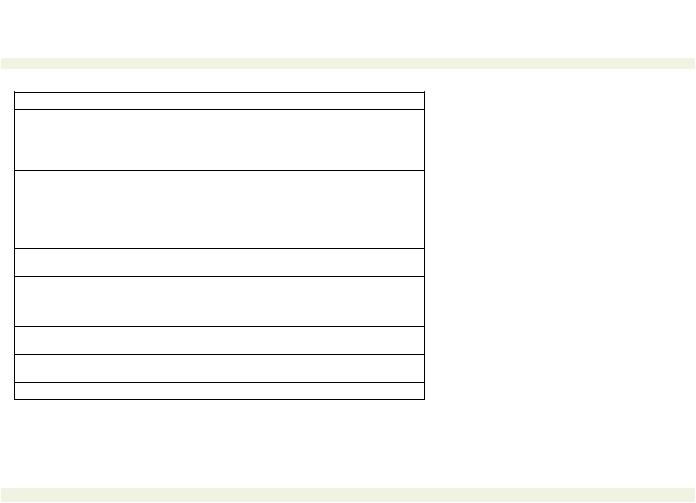
< previous page |
page_89 |
next page > |
Page 89
The U.S. EPA's WAVE SAVER Program
The U.S. EPA has formed Water Alliances to Save Energy (WAVE) to help the hotel/motel industry economize on water and energy use. A membership in WAVE entitles partners, supporters and endorsers to utilize the U.S. EPA's promotional material and the WAVEsaver. WAVEsaver is a computer modeling program like the ones discussed in this chapter.
By joining WAVE, facilities in the hotel/motel industry can request the program and use it for modeling and tuning water use.
WAVEsaver program materials include on instruction manual, guideline forms and floppy disks or CD-ROM to install the system on an IBM-compatible 486SX or higher-capacity computer. The program requires about 8 megabytes of RAM and 15 megabytes of space available on the hard drive. The system operates in DOS 6.0 and Windows 3.1.
The WAVEsaver program also comes with the necessary forms for conducting the utility field survey which is entered into the computer program before analysis is run.
WAVEsaver calculates the true incremental cost of water, creates budget projections based on historical utility rates and occupancy patterns. The program contains hundreds of databases that enable the facility to conduct cost-efficiency options and to select and customize property-specific studies. Forms are available from U.S. EPA.
The CD-ROM version provides interactive video and sound to analyze high-efficiency system upgrades
The WAVEsaver program was developed in conjunction with water use experts and jointly sponsored by the U.S. EPA and the Metropolitan Water District of Southern California.
For more information, call the U.S. EPA at (202) 260-7388.
A good model will reveal where water can be saved, how much can be saved and total the value of the savings. In addition, the facility can capitalize upon the marketing value of being a good water conservation steward which helps with marketing the facilities' public image.
The savings from use of low-flow water fixtures and from implementing water savings measures can be used to off-set the costs of remodeling and may even repay the total costs of the improvements.
< previous page |
page_89 |
next page > |
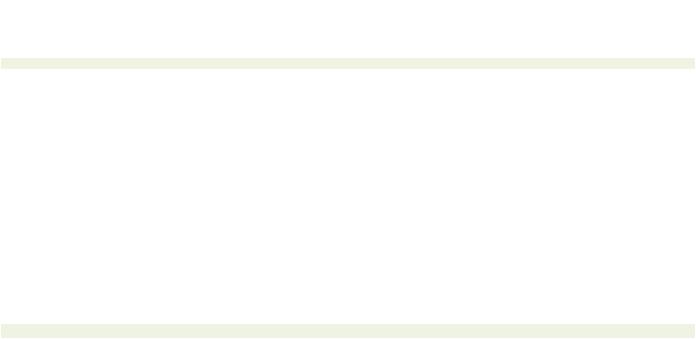
< previous page |
page_91 |
next page > |
Page 91
Chapter 6
Hot Water Systems
Every facility manager wants to provide hot water effectively and at low cost. In most facilities, the absence of hot water for a short period, while inconvenient, is not disastrous. Hospitals are, of course, another matter since the hot water is necessary for patient bathing and controlling sanitary conditions. Proper design, planning, and a good understanding of the system provides hot water that meets the facility needs economically.
Introduction
For existing facilities, the hot water system, if it has been designed correctly, will be adequate. In an older facility, the manager may be concerned about the status of the system. This concern may stem from observations of water and rust-colored stains on the floor and piping in the hot water tank room. Another area of concern may be customer calls about the temperature of the water.
The callers usually say the water is not warm enough, but there may be the occasional call that the water is too hot. Perhaps a simple thermostat adjustment will solve the problem for now. Unfortunately, in today's busy and often hectic world of facility management, hot water system issues are given low priority. Once the facility manager obtains a little breathing room on other issues he can look into hot water supply problems or, if he can obtain the necessary funds, he can contact an engineering firm to perform a short study to address hot water needs. Figure 6-1 lists a series of quick assessment questions that allow a facility manager to determine the status of
< previous page |
page_91 |
next page > |
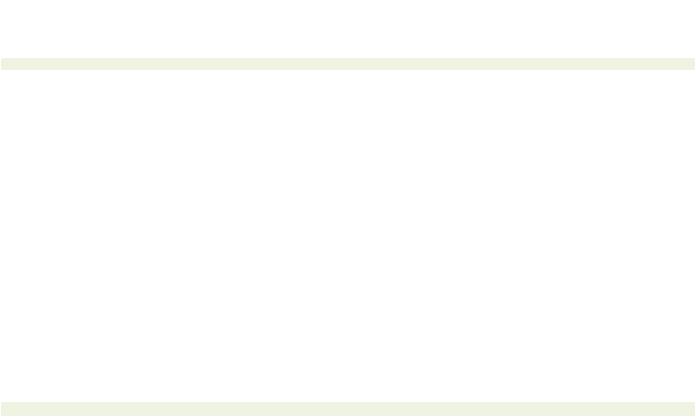
< previous page |
page_92 |
next page > |
Page 92
his hot water system. Armed with this information, the facility manager can decide whether to expend his resources on his hot water system immediately or wait a few weeks or months if the situation is sufficiently under control.
To adequately meet facility needs, the hot water system must be sized correctly and the water should be the right temperatures to provide enough hot water for the needs of the users.
The system uses energy to heat the water, either a fuel or electricity, and the tanks and pipes will be insulated to conserve energy once the water has been heated. The system must meet certain codes and standards for the safety of the building occupants and for the operators and maintenance people who work on the system.
Options Available to the Facility
Does the system supply enough of the right temperature of water to meet the facility needs? That is the question.
Hot water system design is a function of four basic elements that are interrelated, including 1) size of the tank, 2) its volume or dimensions, 3) flow of hot water in the pipes to the point where it is used and 4) the temperature of the heated water. Another variable that must be addressed by a facility manager is the energy source used for heating the water.
Most of the systems in the United States are hot water storage systems. In a domestic hot water storage system, a sufficient volume of water is heated in a tank where it waits until needed.
Turning on the hot water tap, or starting the washer or dishwasher, are typical uses for hot water. In a storage system, hot water flows out of the tank until either the user has enough hot water and valves are closed, or the water heater runs out of hot water.
As a facility grows, more and more users draw more hot water from the tank until finally there is not enough hot water to go around. The first thing the maintenance staff does is raise the tank's thermostat. Now the hot water in the tank is hotter so more users can draw bath and shower water because they will turn down the hot water faucet a little. However, if the water is too hot, careless users can be scalded.
The facility manager's objective is to meet the needs of the facility users as effectively as possible. Effective means costand energy efficient. The facility could have a large tank that heats water slowly, or a small tank that heats water quickly. The tradeoffs are
< previous page |
page_92 |
next page > |