
767_LITEJNOE_PROIZVODSTVO
.pdf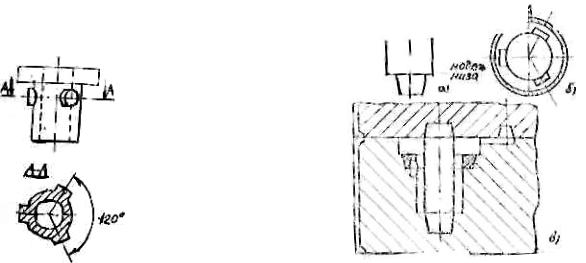
Лабораторная работа №2 «Разработка технологии изготовления отливок в разовых песчано-глинистых
формах» Цель работы: Ознакомление с технологическими принципами конструирования
литых деталей и с методикой разработки технологии отливки. Работа рассчитана на 4 часа (2 занятия по 2 часа).
2.1. Технологические принципы конструирования отливок
При разработке конструкции литой детали обычно удается проектировать ее в нескольких вариантах, равноценных с точки зрения работоспособности. Однако, эти варианты могут существенно отличаться по сложности изготовления отливки, обусловленной особенностями литейного производства.
Нерациональная конструкция литой детали увеличивает трудоемкость изготовления модели, приводит к перерасходу формовочных и стержневых смесей, усложняет процесс формовки, способствует образованию внутренних напряжений и усадочных пустот в отливке.
Наиболее существенное влияние конфигурация отливки оказывает на трудоемкость процесса формовки.
В ряда случаев изменение внешних очертаний детали, не влияют на работоспособность, позволяет упростить формовку.
Приливы, бобышки, фланцы, ребра жесткости и другие выступающие части детали желательно конструировать так, чтобы облегчить извлечение модели из формы.
На. рис. 2.1. показана деталь, имеющая бобышки, расположенные под углом 120°. Формовке такой детали может осуществляться в индивидуальном или мелкосерийном производстве по модели с отъемными частями, а в крупносерийном производстве - с внешними стержнями.
Технология формовки с внешними стержнями показана на рис. 2.2., где а - модель, б - стержень, в - разрез литейной формы в сборе. Кольцевой внешний стержень (б) устанавливается в полость, образованную в форме утолщением на модели (знаком) рис.- (2.2.-а).
На рис. 2.3. показан разрез нижней полуформы со стержнем.
Изменение формы бобышек как показано на рис. 2.4. не ухудшает работоспособности детали, но несколько увеличивает ее вес.
|
Рис. 2-2. Технология формовки с внешним стержнем, |
Рис. 2-1. Отливка |
а – модель, б – стержень, в - форма |
|
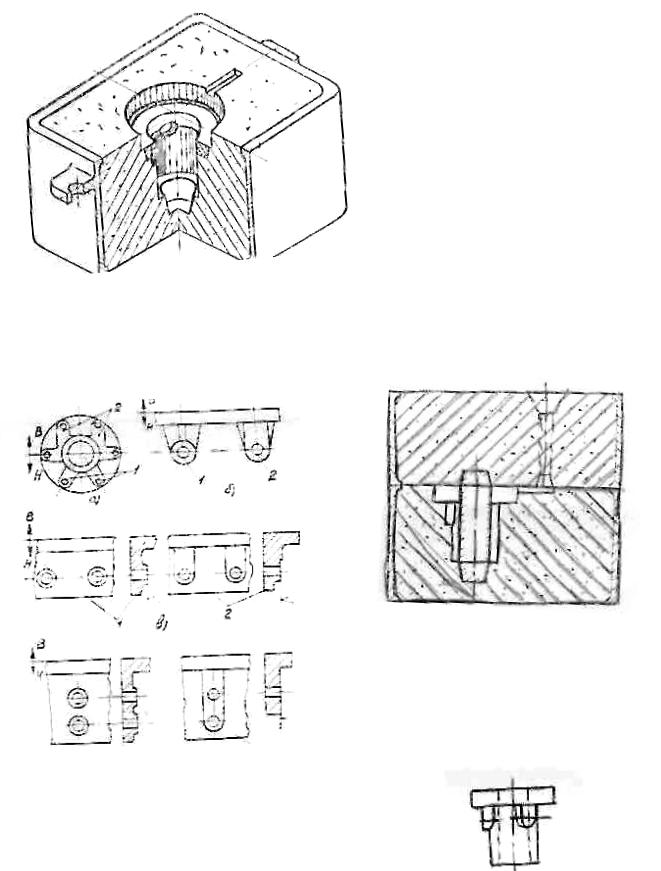
Рис. 2-3. Полуформа низа с наружным стержнем
Рис. 2-5. Разрез литейной формы для детали измененной конструкции
Рис. 2-5. Примеры оформления бобышек, 1 – нерациональная конструкция, 2 – рациональная конструкция
Рис. 2-4. Литая деталь с измененной формой бобышек
Если такое увеличение веса допустимо, то измененная конструкция предпочтительнее, потому, что формовка ее значительно проще.
Отсутствие поднутрения между фланцем и бобышкой обеспечивает свободное извлечение модели из формы (рис. 2.5.). Формовка такой модели не требует применения внешнего стержня, а следовательно приводит к экономии на его изготовлении.
Подобные изменения обычно приходится производить при изготовлении бобышек под головки болтов и гайки, расположенные на фланцах кронштейнов, картеров и др. корпусных деталях (рис. 2.6. а, б, в, г).
в ряде случаев при наличии в отливке ребер жесткости, наклонных к плоскости разъема и препятствующих извлечению модели из формы (рис. 2.7. а), формовка может быть упрощена изменением положения ребер жесткости как показано на рис. 2.7. б, что не снижает жесткость детали и облегчает ее извлечение.
Конструкция внутренней полости отливки должна обеспечить надежное крепление стержня в форме, при этом применение жеребеек нежелательно, так как усложняет процесс сборки формы и приводит к образованию газовых раковин в местах установки жерабеек. на рис. 2-8, а показана отливка, внутренние полости которой выполняются двумя стержнями. Ст. 2 имеет только один знак, поэтому для крепления его устанавливаются жеребейки (рис. 2-8 а). Если устранение перемычки между двумя полостями не ухудшает работоспособность отливки, то желательно объединить стержни в один (рис. 2-8 б). Такой стержень имеет три знака, что обеспечивает его устойчивое положение в форме.
При конструировании литой детали желательно предусмотреть равномерную толщину стенок в отливке, так как различные по толщине части охлаждаются неравномерно, следовательно и уменьшение размеров из происходит с различной скоростью. Эта неравномерная усадка тонких и толстых частей отливки приводит к образованию внутренних напряжений, которые вызывают коробление отливок, трещины.
Так после затвердевания балки таврового сечения (рис. 2-9) тонкая стойка (1) охлаждается быстрее, чем массивная полка (2), поэтому длина стойки уменьшается быстрее. Массивная полка, находящаяся в пластичном состоянии, не препятствует усадке стойки. Когда полка в процессе охлаждения приобретает упругие свойства, длина стойки будет меньше, чем длина полки, как схематично показано на рис. 2-9 а. Дальнейшей усадке полки будет мешать жесткая стойка, поэтому в полке возникают растягивающие напряжения, а в стойке – сжимающие. Под действием этих напряжений балка изгибается, как показано на рис. 2-9,б.
Балка с равномерной толщиной стенок (рис. 2-9 в) может иметь такую же прочность и жесткость , как и показанная на рис. 2-9 а, но при охлаждении такой балки коробления не будет.
Возникновение внутренних напряжений в отливке маховика, имеющего тонкие спицы и массивный обод (рис. 2-10 а), объясняется тем, что спицы охлаждаются быстрее, чем обод, поэтому уменьшается их длина быстрее, чем диаметр обода. Однако отрыва спиц от обода не происходит так как при усадке спицы вытягивают из обода металл, который еще находится в пластичном стостоянии. Таким образом, длина спиц после охлаждения не изменяется. После
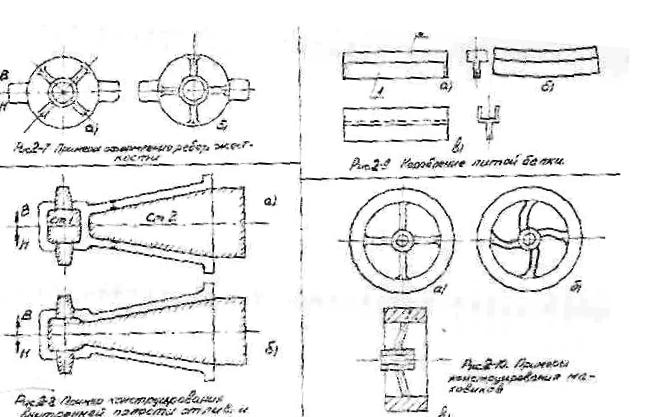
того, как в процессе охлаждения обод приобретает упругие свойства усадка его будет затруднена остывшими жесткими спицами.
Возникающие при этом напряжения могут привести к образованию в отливке трещин.
Для уменьшения диаметра приведет к дополнительному изгибу спицы. При этом изгибающие напряжения в изогнутой спице будут незначительными по сравнению с сжимающими напряжениями в прямой спице.
Уменьшению внутренних напряжений способствуют также наклонные спицы или диски в шкивах и маховиках (рис. 2.10 в).
Конструкция детали оказывает существенное влияние на образование усадочных пустот. Затвердевание отливки начинается с образования корочки металла на ее поверхности, температура этой корочки ниже, чем температура расплава, находящегося внутри ее.
После полного охлаждения отливки объем жидкости, заключенной в первоначальной твердой оболочке, уменьшится больше, чем объем самой оболочки, в результате чего внутри отливки образуются полости, незаполненные металлом. Поскольку давление внутри усадочной раковины равно нулю, атмосферное давление деформируют корку, и на поверхности отливки образуется утяжина. Схема образования усадочной раковины в отливках из чистых металлов показана на рис.2- 11.
В отличие от чистых металлов, характеризующихся точкой плавления и затвердевания, большинство реальных сплавов затвердевает в интервале температур. Это усложняет картину затвердевания отливки и приводит к образованию в ней наряду с усадочной раковиной рассеянной усадочной пористости (рыхлости).
Если в отливке имеются разные по толщине части (рис. 2-12 а), то затвердевание начинается с самой тонкой. Образующаяся в ней пустота заполняется жидки металлом из средней части, которая охлаждается медленнее. Объемная усадка средней части компенсируется жидким металлом из самой массивной части, затвердевающей в последнюю очередь. В этой части и концентрируется усадочная раковина, объем которой равен сумме объемов усадочных раковин всех трех частей отливки.
Для крупных отливок, изготовляемых из сплавов, имеющих большую объемную усадку предусматривают при изготовлении формы место для прибыли (рис. 2-12 б). Прибыли располагают на самых толстых частях отливки. Размеры и форму прибыли подбирают так, чтобы она затвердевала в последнюю очередь, поэтому прибыль должна быть массивнее самой толстой части отливки.
При производстве сравнительно небольших по сечению отливок образуются незначительные по размерам усадочные раковины, которые не оказывают существенного влияния на прочность отливки. Однако в местах скопления металла будут образовываться концентрированные усадочные раковины и рыхлости. Такие скопления металла образуются обычно при неправильном сопряжении стенок корпусных деталей. Равномерность толщины стенки и скопления металла можно определить диаметром вписанной в сечение отливки окружности. На рис. 2-13 показаны способы устранения скоплений металла, образующихся в местах сопряжения стенок отливки.
2.2. Разработка чертежа модели по чертежу детали
2.2.1. Выбор положения отливки в форме и плоскости разъема. Разработка технологии изготовления литой детали начинается с выбора
положения ее в форме на основе анализа конструкции отливки.
Элементы этой конструкции, неоправданно усложняющие технологию изготовления отливки изменяют в соответствий с рекомендациями, изложенными в разделе 1. Кроме того, учитывают, что мелкие отверстия, выемки и пазы целесообразнее выполнять на литьем, а последующей механической обработкой. Такие изменения ("напуски") изображаются крестообразной штриховкой рис. 2.-14.
При выборе положения отливки в форма наиболее ответственные, подвергающиеся механической обработке поверхности отливки, располагают внизу ила вертикально, так как при заливке металла в форму шлаковые и неметаллические включения всплывают вверх.
Количество разъемов формы должно быть минимальным, поверхности – разъемов – по возможности плоскими. Желательно располагать всю отливку в одной полуформе, так как наличие зазоров между штырями и втулками опок обычно приводит к смещению полуформ, а следовательно к смещению верхней части отливки относительно нижней (перекосу). При формовке всей отливки в одной опоке перекоса не будет.
Плоскость разъема выбирается так, чтобы части модели свободно извлекались из формы после уплотнения смеси. При невозможности обеспечения этого условия поднутрения (выемки) отливки оформляются внешними стержнями.
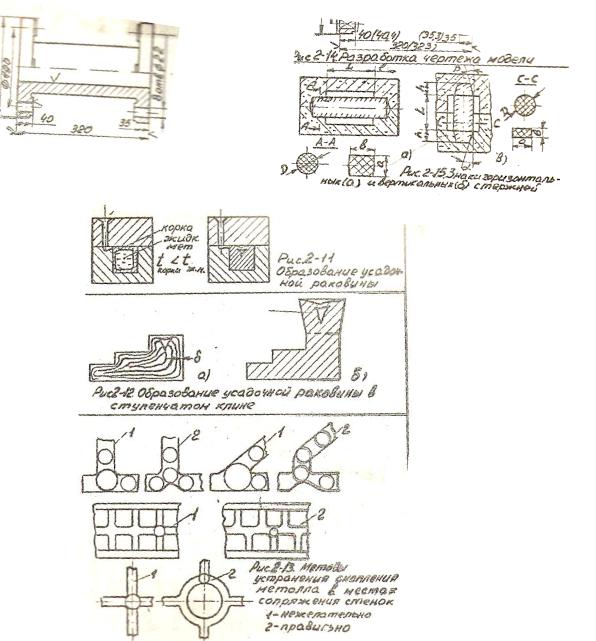
Поверхность разъема полуформ показывается на чертеже отрезком прямой ли ломаной сплошной основной линией, у которой ставится буквенное обозначение разъема – МФ (рис. 2-14). Количество стержней должно быть минимальным. Стержни устанавливаются преимущественно в нижней полуформе: в ней же должны располагаться основные (опорные) знаки.
2.2.2. Назначение припусков на механическую обработку Припуски на механическую обработку даются на все обрабатываемые
поверхности отливки. Величина их зависит от размера и материала отливки, степени
еесложности, положения данной поверхности при заливке, характера производства.
Всоответствии с ГОСТ 2789-73 шероховатость поверхности изделий как до, так и после механической обработки оценивается высотой неровностей поверхности
Rz в мкм. Чем чище и ровнее поверхность, тем меньше высота неровностей. Поверхность отливок, изготавливаемых в обычных песчаных формах,
характеризуется относительно большой высотой неровностей (от 320 до 1000 мкм, а иногда и больше). Механическая обработка обеспечивает получение более чистой поверхности со значительно меньшей величиной шероховатостей.
Предусматривается 3 класса точности размеров отливок и соответственно 3 класса припусков на механическую обработку.
Втаблицах 2.2-1 и 2.2-2 приведены припуски на механическую обработку для остальных и чугунных отливок, а в табл. 2.2-3 для отливок из цветных сплавов.
Отливки наиболее высокого 1 класса точности получают в крупносерийном и массовом производстве с использованием машинной формовки по металлическим моделям.
Наибольшую величину припусков назначают на отливки 3 класса точности, получаемые при ручной формовке по деревянным моделям.
Таблица 2.2-1 Величина припуска на механическую обработку для стальных отливок (ГОСТ
2009-55)
Наибольший |
Класс |
Номинальный размер |
|
|
|
|
|
||
габратиный |
точности |
до 120 |
|
120-160 |
|
260-500 |
500-800 |
||
размер, мм |
|
верх |
низ. бок |
верх |
низ.бок |
верх |
низ. бок |
верх |
низ. бок |
до 120 |
1 |
3,5 |
3 |
|
|
|
|
|
|
|
2 |
4 |
4 |
|
|
|
|
|
|
|
3 |
5 |
4 |
|
|
|
|
|
|
120-160 |
1 |
4 |
3 |
5 |
3,5 |
|
|
|
|
|
2 |
5 |
4 |
6 |
4 |
|
|
|
|
|
3 |
5 |
4 |
6 |
5 |
|
|
|
|
260-500 |
1 |
5 |
3 |
7 |
4 |
6 |
4 |
|
|
|
2 |
6 |
5 |
7 |
4 |
7 |
6 |
|
|
|
3 |
6 |
5 |
8 |
6 |
9 |
6 |
|
|
2 классу точности соответствуют отливки, получаемые машинной формовкой по деревянным моделям или ручной формовкой по металлическим моделям.
Таблица 2.2-2 Величина припуска на механическую обработку для чугунных отливок
(ГОСТ 1855-55)
Наибольший |
Класс |
|
|
|
Номинальный размер, мм |
|
|
|
||||
габаритный |
точности |
до 50 |
50-120 |
120-260 |
260-500 |
500-600 |
||||||
размер, мм |
|
верх |
низ. |
верх |
низ. |
верх |
низ. |
верх |
|
низ. |
верх |
низ. |
|
|
|
бок |
|
бок |
|
бок |
|
|
бок |
|
бок |
до 120 |
1 |
2,5 |
2,0 |
0,5 |
2,0 |
|
|
|
|
|
|
|
|
2 |
3,5 |
2,5 |
4,0 |
3,0 |
|
|
|
|
|
|
|
|
3 |
|
|
4,5 |
4,5 |
|
|
|
|
|
|
|
120-260 |
1 |
2,5 |
2,0 |
3,0 |
2,5 |
|
|
|
|
|
|
|
|
2 |
4,0 |
3,0 |
4,5 |
8,5 |
5,0 |
4,0 |
|
|
|
|
|
|
3 |
|
|
5 |
4 |
5,5 |
4,5 |
|
|
|
|
|
260-500 |
1 |
8,5 |
2,5 |
3,5 |
3,0 |
4,0 |
3,5 |
4,5 |
|
3,5 |
|
|
|
2 |
4,5 |
3,5 |
5,0 |
4,0 |
6,0 |
4,5 |
6,5 |
|
5,0 |
|
|
|
3 |
|
|
6,0 |
4,5 |
7,0 |
5,0 |
7,0 |
|
6,0 |
|
|
Примечание: Номинальным размером для установления припусков на механическую обработку является наибольшее расстояние между противоположными обрабатываемыми поверхностями или расстояние от базовой поверхности или оси до обрабатываемой поверхности.
Таблица 2.2-3 Величина припусков на механическую обработку отливок из цветных сплавов
Наибольши |
Полож. |
|
|
|
Номинальный размер, мм |
|
|
||||
й |
поверхн. |
до 120 |
|
120-260 |
|
260-500 |
500-800 |
||||
габаритный |
|
М |
|
Р |
М |
Р |
М |
|
Р |
М |
Р |
размер, мм |
|
|
|
|
|
|
|
|
|
|
|
до 120 |
Верх |
3 |
|
4 |
|
|
|
|
|
|
|
|
Низ. бок |
2 |
|
3 |
|
|
|
|
|
|
|
120-260 |
Верх |
3 |
|
4 |
3 |
4 |
|
|
|
|
|
|
Низ. бок |
2 |
|
3 |
2 |
3 |
|
|
|
|
|
260-500 |
Верх |
4 |
|
5 |
4 |
5 |
5 |
|
6 |
|
|
|
Низ. бок |
3 |
|
4 |
3 |
4 |
4 |
|
5 |
|
|
500-800 |
Верх |
4 |
|
5 |
4,5 |
5 |
5 |
|
6 |
5,5 |
6 |
|
Низ. бок |
3 |
|
4 |
3,5 |
4 |
4 |
|
5 |
4,5 |
5 |
Примечание: М – машинная формовка, Р – ручная формовка.
На тех частях отливки, которые при заливке формы обращены вверх, припуск дается больший, чем на боковых и нижних поверхностях, так как наверху обычно собираются неметаллические, шлаковые и газонные включения.
2.2.3. Литейные уклоны Для облегчения извлечения модели из формы стенки модели,
перпендикулярные плоскости разъема, делают с уклоном в сторону разъема формы. Аналогиченые уклоны даются на стенках стержневых ящиков, переендикулярных его плосткости разъема.
Величины формовочных уклонов зависят от способа изготовления форм, материала моделей и стержневых ящиков и от высоты поверхности, на которую назначаются уклоны.
Формовочные уклоны обозначаются тонкими линиями, как показано на рис.2.1.4.
Величина формовочных уклонов приведена в табл.
таблица
Для стержневых ящиков формовочные уклоны выполняются такими же, как и уклоны моделей.
Если в форме имеются выступы, расположенные между двумя вертикальными стенками модели (земляные болваны), то формовочные уклоны на эти стенки увеличивают в 1,5 – 2 раза, чтобы уменьшить опасность отрыва их при извлечении модели из формы.
2.2.4. Галтели (округления вершин углов на моделях и стержневых ящиках)
предупреждают ссыпание формовочной смеси и скалывание острых вершин моделей при набивке форм.
Радиус галтели R (рис. 2-14) рассчитывается по формуле
R = (1/3 – 1/5) * (а+b)/2,
где a и b – толщины сопрягающихся стенок отливки, 1/3 – принимается в случае, когда (а+b)/2 < 50 мм, а 1/5 – когда (а+b)/2 > 50 мм.
Нормальный ряд радиусов: 1, 2, 3, 5, 8, 10, 15, 20, 30, 40 (радиусы 1, 2, 3 мм применяются только для металлических моделей).
Чертеж детали с нанесенными на него напусками, припусками на механическую обработку, литейными уклонами и радиусами представляет собой чертеж будущей отливки.
2.2.5. Припуск на усадку Залитый в форму металл при затвердевании и охлаждении уменьшается в
размерах, т.е. дает усадку. В следствие этого модель должна быть несколько больших размеров, чем будущая отливка.
Припуски на усадку даются в зависимости от величины линейной усадки сплава, измеряемой в процентах.
Величина усадки принимается одинаковой по всем направлениям отливки, хотя сопротивление формы и стержней затрудняет усадку и изменяет ее величину.
Линейная усадка зависит от типа сплава и составляет: для чугуна – 1%, стали
– 2%, для большинства цветных металлов – 1,5-2%.
2.2.6. Внешний контур и размеры стержня Стержневые знаки в зависимости от их положения при сборке формы
подразделяются на горизонтальные (рис. 2-15а) и вертикальные (рис. 2-15б). Размеры и элементы стержневых знаков регламентируются ГОСТ 3606-57 и выбираются по таблицам.
таблица
Таблица 2.6-2 Высота нижних вертикальных знаков
(а+b)/2 или Д |
Высота стержня h (не более) при длине стержня L |
|
|||
|
|
до 50 |
свыше 50 до 150 |
|
свыше 150 до 300 |
до 25 |
|
20 |
25 |
|
- |
свыше 25 |
до 50 |
20 |
40 |
|
60 |
свыше 50 |
до 100 |
25 |
35 |
|
50 |
свыше 100 до 200 |
30 |
30 |
|
40 |
Примечание: При отсутствии верхнего знака высота нижнего может быть увеличена до 50% против величины, взятой по таблице.
Таблица 2.6-3 Высота верхних вертикальных знаков
Высота нижнего знака, мм |
20 |
25 |
30 |
35 |
40 |
50 |
60 |
Высота верхнего знака, мм |
15 |
15 |
20 |
20 |
25 |
30 |
35 |
Знаки стержней для удобства сборки выполняются с уклонами и к плоскости разъема.
Стержневые знаки показываются на чертеже детали тонкими линиями. По контуру стержня наносится штриховка (рис. 2.15).
Наружный контур чертежа отливки, увеличенной на величину линейной усадки, вместе с нанесенными на него стержневыми знаками представляет собой чертеж модели.
2.2.7. Литниково-питающая система Назначение и устройство литниковой системы рассмотрены в методических
указаниях к лабораторной работе №1. Расчет элементов литниковой системы является сложной инженерной задачей, представляющей интерес для специалистовлитейщиков, поэтому в данной работе не производится. При выполнении работы, необходимо выбрать схему подвода металла к отливке и нанести ее на чертеж разреза литейной формы по размерам, указанным преподавателем.
2.3.Порядок выполнения работы
1.Изучить чертеж детали в полученном варианте задания, наметить положение отливки в форме, плоскость разъема, необходимые изменения конструкции детали.
2.Обсудить с преподавателем выбранный способ формовки детали.
3.Рассмотреть способы формовки, предложенные в других вариантах заданий.